我国甲醇产业发展研究.docx
《我国甲醇产业发展研究.docx》由会员分享,可在线阅读,更多相关《我国甲醇产业发展研究.docx(13页珍藏版)》请在冰豆网上搜索。
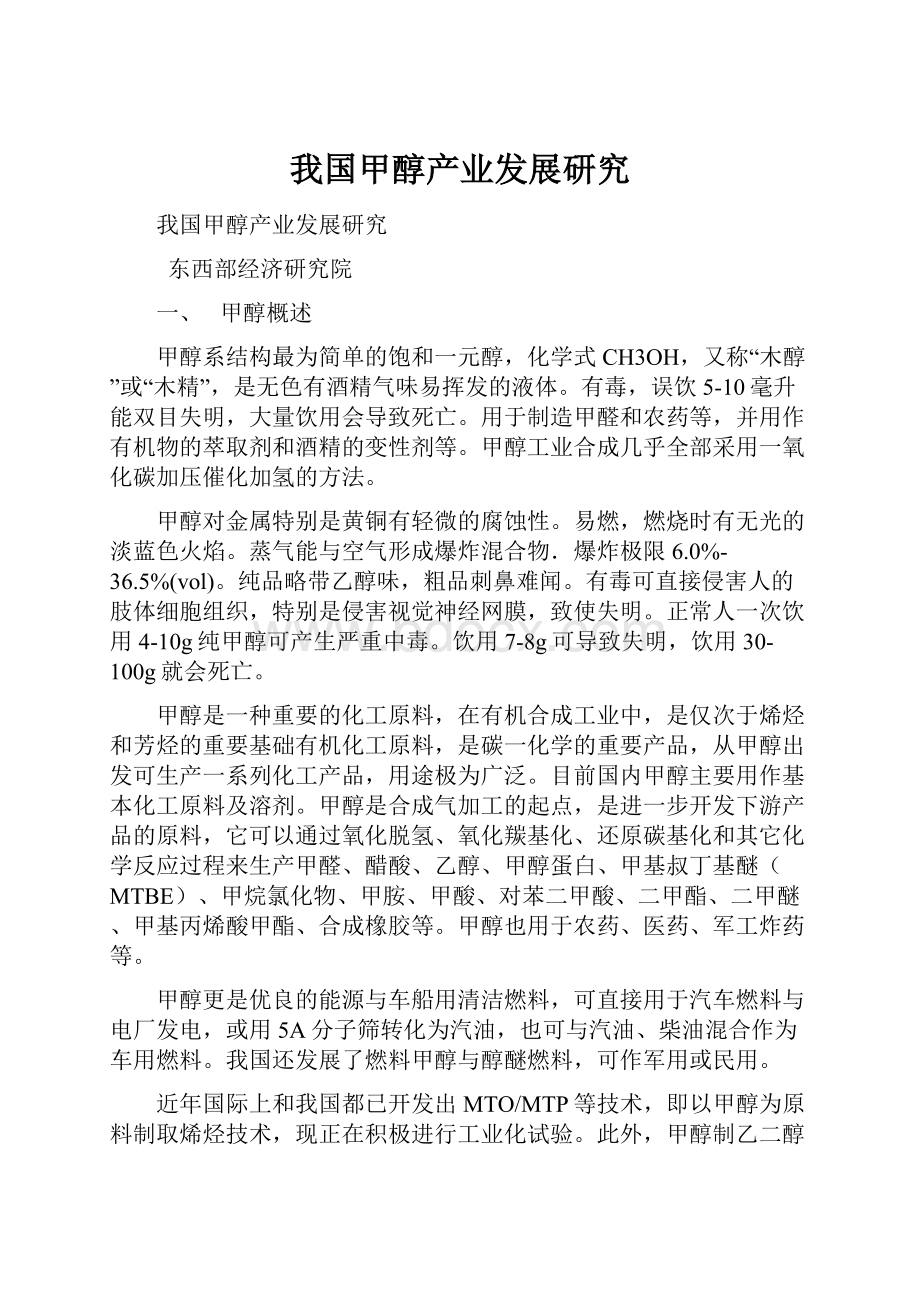
我国甲醇产业发展研究
我国甲醇产业发展研究
东西部经济研究院
一、 甲醇概述
甲醇系结构最为简单的饱和一元醇,化学式CH3OH,又称“木醇”或“木精”,是无色有酒精气味易挥发的液体。
有毒,误饮5-10毫升能双目失明,大量饮用会导致死亡。
用于制造甲醛和农药等,并用作有机物的萃取剂和酒精的变性剂等。
甲醇工业合成几乎全部采用一氧化碳加压催化加氢的方法。
甲醇对金属特别是黄铜有轻微的腐蚀性。
易燃,燃烧时有无光的淡蓝色火焰。
蒸气能与空气形成爆炸混合物.爆炸极限6.0%-36.5%(vol)。
纯品略带乙醇味,粗品刺鼻难闻。
有毒可直接侵害人的肢体细胞组织,特别是侵害视觉神经网膜,致使失明。
正常人一次饮用4-10g纯甲醇可产生严重中毒。
饮用7-8g可导致失明,饮用30-100g就会死亡。
甲醇是一种重要的化工原料,在有机合成工业中,是仅次于烯烃和芳烃的重要基础有机化工原料,是碳一化学的重要产品,从甲醇出发可生产一系列化工产品,用途极为广泛。
目前国内甲醇主要用作基本化工原料及溶剂。
甲醇是合成气加工的起点,是进一步开发下游产品的原料,它可以通过氧化脱氢、氧化羰基化、还原碳基化和其它化学反应过程来生产甲醛、醋酸、乙醇、甲醇蛋白、甲基叔丁基醚(MTBE)、甲烷氯化物、甲胺、甲酸、对苯二甲酸、二甲酯、二甲醚、甲基丙烯酸甲酯、合成橡胶等。
甲醇也用于农药、医药、军工炸药等。
甲醇更是优良的能源与车船用清洁燃料,可直接用于汽车燃料与电厂发电,或用5A分子筛转化为汽油,也可与汽油、柴油混合作为车用燃料。
我国还发展了燃料甲醇与醇醚燃料,可作军用或民用。
近年国际上和我国都已开发出MTO/MTP等技术,即以甲醇为原料制取烯烃技术,现正在积极进行工业化试验。
此外,甲醇制乙二醇、乙醛、甲苯、二甲苯以及未来高科技产品燃料电池等都在快速进展中。
总之,甲醇用途十分广泛,在国民经济中几乎找不到另外一种有机产品有甲醇如此广阔的应用范围。
而且随着科学技术的不断发展与进步,甲醇的应用领域仍在不断扩大,已突破了其传统的应用范围,未来的潜在开发前景十分看好。
二、甲醇主要生产工艺
现行的工业化甲醇合成工艺以气相合成法为主。
从上世纪60年代至今,除了在反应器的放大上及催化剂的研究方面有些进展外,其合成工艺基本上没有大的突破。
鉴于气相合成存在的一系列问题,从70年代起人们把甲醇合成工艺研究开发的重点转移到液相合成法,并且初步实现了工业化的生产。
(一)气相甲醇合成工艺
现在世界许多公司都以天然气、煤或重油为原料来生产甲醇。
其中以天然气居多,约占90%以上。
根据操作压力可分为高压法、中压法和低压法。
高压法因技术经济指标落后而淘汰。
包括中压法在内的低压法主要以ICI(帝国化学)和Lurgi(鲁奇)两公司技术为代表。
所用的催化剂基本上是以铜和氧化锌为主加入铝或铬的氧化物。
工艺设计大同小异,差异之处是在反应器的设计和操作单元的组合上。
气相法工艺流程主要有以下几种。
1、ICI低压甲醇合成流程
由H2、CO、CO2及少量CH4组成的合成气经过变换反应以调节CO/CO2比例,然后用离心压缩机升压到5MPa,送入温度为270℃冷激式反应器,反应后的气体进行冷却分离出甲醇,未反应的气体经压缩升压与新鲜原料气混合再次进入反应器,反应中所积累的甲烷气作为驰放气返回转化炉制取合成气。
该生产工艺生产的甲醇浓度低,合成气循环量大,能耗高。
该工艺生产的甲醇中含有少量水、二甲醚、乙醚、丙酮、高碳醇等杂质,需要蒸馏分离才能得到精甲醇。
2、Lurgi低压甲醇合成工艺
Lurgi低压甲醇合成工艺与ICI的最大区别是,它采用列管式反应器,CuO/ZnO基催化剂装填在列管式固定床中,反应热供给壳程中的循环水以产生高压蒸汽,反应温度由控制反应器壳程中沸水的压力来调节,操作温度和压力分别为250~260℃和5~6MPa。
合成气由甲烷、石脑油用蒸汽转化法或部分氧化法制取,它与循环气一起压缩,预热后进入反应器。
Lurgi工艺可以利用反应热副产一部分蒸汽,能较好地回收能量,其经济性和操作可靠程度要好一些。
3、TEC的新型反应器
上世纪90年代TEC(东芝)公司才开发了MRF-Z新型反应器,其基本结构是反应器为圆筒状,有上下两个端盖,下端盖可以拆卸以方便催化剂装填和内部设施检修;反应器内装有一直径较小的内胆用以改变物料流向;反应器的中心轴向安装一带外壳的列管式换热器,换热器的外壳上开有直径小于催化剂颗粒的小孔,换热器内管束间设有等距离的折流挡板,以使原料气体在管间均匀分布。
由于该工艺的特殊设计,甲醇生成的浓度和速度可大幅度提高,反应温度容易控制,催化剂用量减少,反应器的结构紧凑。
该装置易于从现在的2500~2800吨/日放大到5000吨/日。
但是,此项工艺的反应器内部结构复杂,零部件较多,工艺的稳定性还需进一步完善。
4、紧凑式转化器的甲醇新工艺
Kvaemer公司组合BP阿莫科Kvaemer紧凑式转化器与低压甲醇合成的甲醇新工艺于2004年工业化。
BP阿莫科将紧凑式转化器的验证试验装置建于阿拉斯加,2002年投运。
应用于3000吨/日装置的新甲醇工艺,投资费用比常规蒸汽转化的装置节约3000万美元。
紧凑式转化器采用模块化管式反应器设计,它将一侧的燃烧与另一侧的催化蒸汽转化紧密地组合在一起。
由于有大的内部热循环,紧凑式转化器的热效率超过90%,而常规装置为60%—65%。
5、鲁奇和Synetix公司的LCM工艺
LCM工艺的目标之一是要完全取消蒸汽发生系统,工艺用蒸汽用一个饱和器回路来回收低等级热发生蒸汽。
在LCM甲醇工艺中,饱和器回路的30%—40%热源来自甲醇合成系统。
因此,LCM工艺的另一个特点是易于启动和停工。
Methanex公司将在新西兰的莫图努伊建一座材料验证装置,用全尺寸转化器管进行各种材料试验,以用于甲醇生产或天然气炼油。
此装置于2001年第4季度投产,初期试验计划在18个月内完成。
2006年LCM工艺用于6500吨/日装置。
此外,鲁奇公司开发了采用气冷反应器和水冷反应器的联合转化合成工艺,水冷反应器催化剂用量可减少50%,可省去原料预热器并可减少其他设备,合成部分的投资可节省40%。
(二)液相法甲醇合成工艺
目前在液相甲醇合成方面,采用最多的主要是浆态床和滴流床。
1、浆态反应器在甲醇合成中应用
在浆态床反应器中,催化剂粉末悬浮在液体中形成浆液,气体在搅拌桨或是气流的搅动作用下形成分散的细小气泡在反应器内运动。
原美国化学系统公司在1975年提出开发液相法甲醇合成工艺的新概念,并于上世纪90年代与美国空气与化学产品公司一起开发出使用液升式浆态反应器的LPMEOHTM工艺(液相法甲醇工艺)。
早期在美国能源部(DOE)的Texas州Laporte工厂做过小试,与现行的甲醇合成方法相比,催化剂在高热容的矿物油中形成料浆,反应所产生热量被惰性液体介质所吸收,因而反应能够在等温下进行。
由于细颗粒催化剂的利用率很高,出口气中甲醇含量可以从传统的气固相催化工艺的5%提高到15%。
这种反应器可以在很宽的H2/(CO+CO2)比例范围内操作,并且在低H2/(CO+CO2)比例下催化活性不会降低,因而特别适用于用煤造气的低H2/(CO+CO2)比原料气。
但是这种料浆反应器催化剂的装填量有一定的限度,所以操作中空速不能太大。
2、滴流床反应器在甲醇合成中应用
滴流床反应器与传统的固定床反应器的结构类似,由颗粒较大的催化剂组成固定层,液体以液滴方式自上而下流动,气体一般也是自上而下流动,气体和液体在催化剂颗粒间分布。
滴流床兼有浆态床和固定床的优点,与固定床相类似。
它的催化剂装填量大且无磨蚀,床层中的物料流动接近于活塞流且无返混现象存在,同时它又具备浆态床高转化率等温反应的优点,更适合于低氢碳比的合成气。
从工业角度来看,滴流床中的液相流体中所含的催化剂粉末很少,输送设备易于密封且磨损小,长时间运行将更为可靠。
三、我国甲醇产业发展现状
我国甲醇工业起步于上世纪50年代,70年代自主开发了合成氨联产甲醇生产工艺,90年代精脱硫工艺的成功研发和推广应用,届时甲醇产业进入以联醇工艺生产为主的第一个快速发展期;“十一五”期间,随着市场需求增加和对新兴下游应用的预期,以及大型甲醇装置设计和制造技术的日臻完善,出现了以单醇工艺生产为主的第二个快速发展期。
(一)产能、产量、表观消费量现状
“十一五”期间,我国甲醇产能、产量有很大增长。
据中国氮肥工业协会甲醇专业委员会统计,到2010年底,我国甲醇行业共有企业291家,产能达到3840万吨,比“十一五”初期增长三倍,年均增长率达到32%;2010年产量为1752万吨,比“十一五”初期增长169%,年均增长率约为22%。
2010年甲醇行业产能发挥率仅为46%,2011年也仅仅提高到约50%。
2010年甲醇表观消费量2270万t,同比增加37%,约为世界总消费量45%。
国产甲醇占总消费量比例77.2%,进口甲醇占22.9%。
其中,甲醛占35.5%,二甲醚16.5%,甲醇燃料(包括甲醇汽油)占16.3%,醋酸占8.4%,MTBE占6.0%,DMF占3.5%。
(二)企业布局现状
我国甲醇生产企业主要分布在原料资源地和重点消费地区,近年来向原料资源地发展的趋势明显。
以煤为原料的企业主要集中在山东、河南、内蒙古、河北、山西、陕西等省;以天然气为原料的企业主要集中在西南、西北,其中内蒙古、海南、陕西、重庆产能最大;以焦炉气为原料的企业主要集中在山西、河北、内蒙古、山东等省。
2010年山东、内蒙古、河南、陕西、山西和河北6省的甲醇产能占到全国总产能的65%。
华东、华中及华南地区为甲醇主要调入地区。
(三)原料结构现状
我国是缺油少气、煤炭资源相对丰富的国家。
因此,甲醇生产以煤为主、天然气为辅的原料路线适合我国国情。
“十一五”期间,随着国家原料政策调整和技术进步,新建装置主要以煤为原料,特别是以非无烟煤为原料的装置发展很快;天然气受气源紧张的影响,产能降低;焦炉气制甲醇作为资源综合利用得到重视,产能增加。
2010年我国甲醇产能中以煤为原料占66%,以天然气为原料占23%,以焦炉气为原料占11%。
(四)企业规模现状
“十一五”期间联醇企业甲醇产能伴随着合成氨的发展而增加,大型单醇装置快速发展,装置规模大幅提高。
到2010年底已形成神华、兖矿、中海油、内蒙古远兴能源等4家百万吨级超大型企业;上海焦化、平煤蓝天、榆林天然气、新奥能源、神木化工、联盟化工、龙宇煤化工等10家50-100万吨级企业;年甲醇产能在30万吨以上的大型企业36家。
但企业规模在10万吨以下的小型甲醇企业还有175家,其中大部分是合成氨、炼焦联产甲醇装置。
(五)技术水平现状
近年来,我国成功研发了一批具有自主知识产权的先进工艺技术与装备:
多喷嘴对置式水煤浆气化技术、粉煤加压气化技术、经济型气流床分级气化技术、甲醇低压合成技术及装置、精脱硫技术;醇烃化技术、醇氨联产技术、新型低温甲醇合成催化剂、超滤甲醇分离技术;甲醇精馏技术以及自动化、信息化管理技术等的开发应用,使甲醇生产技术水平进一步提高。
特别是以煤、天然气、焦炉气为原料的甲醇装置的大型化,提升了我国甲醇工业整体水平,部分装置已经接近或达到世界先进水平。
四、甲醇产业发展存在的问题
(一)投资过热,产能明显过剩
“十一五”期间,特别是“十一五”后期,随着我国国民经济的快速发展、工业需求的拉动以及对下游应用的过度乐观,甲醇行业出现盲目投资现象,造成甲醇产能大幅增加,产能过剩情况已经十分严重。
据中国氮肥工业协会甲醇专业委员会的统计,在2011年正式投产的产能和目前在建、计划2013年前建成的产能1800万吨。
如不能尽快淘汰落后产能、突破下游产品应用瓶颈,产能过剩的矛盾将更为突出。
(二)产业结构不尽合理
1、原料结构方面:
天然气供应紧张、无烟煤价格上涨。
近几年,占产能总量23%的以天然气为原料的甲醇企业面临着气源供应无法保证、价格继续上调的压力;占产能总量约43%的以无烟煤为原料的固定床甲醇企业也同样面临原料调整压力。
2、企业结构方面:
集中度较低,部分单醇装置产能规模偏小。
合成氨和炼焦生产中联产甲醇属于综合利用项目,由于受到合成氨和炼焦规模的制约,装置规模较小。
近十年,随着大型单醇装置的陆续投产,单醇装置平均规模有较大增加,但产量在10万吨及以下的单醇企业还有约20家,这些企业规模偏小,技术落后,产品竞争力不强。
3、产品结构方面:
产品品种单一,综合盈利和抵御风险能力低。
我国甲醇企业产品结构上的单一化、同质化现象严重,大部分企业将甲醇作为终端产品进行销售,产品的单一化导致企业严重依赖甲醇市场,抵御风险和综合盈利能力低。
(三)节能减排和环保治理压力大,企业自我改造能力弱
甲醇工业是能源密集型行业和耗水大户,尤其是以煤为原料的企业,在节能、节水和污染物减排方面的任务很重。
目前甲醇行业已经有一批先进的节能、环保技术成果,但近年来由于全行业亏损严重,多数企业在新技术改造时,受到资金紧张的困扰。
(四)面临水资源、二氧化碳排放制约
我国煤炭资源和水资源一般都呈现“逆向分布”,即富煤地区缺水。
煤基甲醇项目耗水量较大,吨甲醇产品耗水量在10t以上,水资源成为限制煤基甲醇发展的“瓶颈”;同时,煤制甲醇过程中排放大量的二氧化碳,每产一吨甲醇,排放的二氧化碳约两吨,目前对于二氧化碳的排放还缺乏有效的处理措施,一般采取直接放空形式进行排放。
目前国际社会对二氧化碳等温室气体减排问题日益重视,通过制定《京都议定书》等协议来限制二氧化碳排放量,在可预计的将来,二氧化碳排放将成为影响煤基甲醇产业发展的又一主要限制因素。
五、甲醇下游产业市场前景分析
(一)甲醇下游产业链介绍
甲醇是重要的有机化工原料,而且是能源的一种替代品。
甲醇经过加工、转化可生成多种化工原料,如甲醛、醋酸、二甲醚、甲烷氯化物、聚乙烯醇、甲胺、甲酸甲酯、甲基叔丁基醚、DMF等。
(二)下游重点产品市场前景预测
1、甲醛
我国甲醛主要用于生产木材加工黏合剂,其次是酚醛树脂等。
近年来,我国甲醛产量保持快速增长的势头,年均增长高达19%。
2009年至2010年,房地产市场的异常活跃带动了国内房屋装修市场,也促进了木材加工黏合剂的消费,进而导致国内甲醛产量的猛增。
未来几年,国内甲醛仍将有较好的发展势头。
一方面,用于木材加工、室内装饰装修的三醛胶仍是甲醛最大的消费领域,其对于甲醛的需求量将稳步增长。
另一方面,聚甲醛(POM)作为重要的工程塑料,市场需求量将会逐年增长。
按照GDP增长率为7%(《中华人民共和国国民经济和社会发展第十二个五年规划纲要》确定的国内生产总值年均增长率)估算,2015年国内甲醛的需求量将达到2380万吨。
按生产1吨甲醛需要0.47吨甲醇计算,届时生产甲醛大约需要消耗甲醇1100万吨/年。
2、醋酸
2010年我国醋酸表观消费量为368万吨,主要应用于醋酸酯,占醋酸总消费量的25.2%;其次是醋酸乙烯、PTA(精对苯二甲酸)和醋酸酐,分别占醋酸总消费量的17%、15.8%和9.4%。
醋酸酯类替代苯类做溶剂,有利于环境保护,将在涂料等行业中有较好发展空间。
与此同时,受聚酯和涤纶工业快速发展的带动,PTA需求将有较大幅度的增长,其对醋酸的需求也会同步增长。
同样按照GDP增长率为7%估算,2015年国内醋酸需求量为516万吨。
若按生产1吨醋酸需要0.6吨甲醇计算,则需要消耗甲醇300万吨/年左右。
3、甲基叔丁基醚(MTBE)
尽管美国禁用MTBE以及欧洲国家以乙基叔丁基醚代替MTBE,但我国改善空气质量的压力远大于MTBE对水源的污染,所以未来几年MTBE仍将是我国提高汽油辛烷值的重要调和组分。
随着我国油品产量的不断增加和质量的不断升级,汽油调和组分的使用量势必会增加,预计到2015年我国MTBE的需求量将会有很大的增长。
4、甲醇汽油
《车用燃料甲醇》和《车用甲醇汽油(M85)》国家标准的颁布实施,使甲醇汽油的推广有了政策依据。
我国已在陕西、山西等地实施了甲醇汽油的封闭销售,拥有了一定的推广经验。
另外,我国自主开发了新型甲醇燃料GQME(汽油)和GPFME(柴油),在不添加任何添加剂的情况下,解决了甲醇汽油涉及的腐蚀和溶胀等主要问题,在2010年建成10万吨/年GQME示范装置后,已分别在山东、宁夏、安徽、江苏新建了100万吨/年工业化装置。
该技术是将甲醇按40%60%的比例分别与汽油和柴油混合,在常温、常压条件下通过化学反应,将甲醇转化为一种与汽油外表特征、物理性能相类似的改性甲醇制品,其性能基本达到欧Ⅳ汽油标准,且不需清洗车辆油箱,实现与现有汽油的任意比例混合。
由于GQME和GPFME甲醇燃料目前仅处于工业化阶段,大规模推广尚需时日,若在山东、宁夏、安徽、江苏新建的100万吨/年装置能够满负荷生产,并按照40%的掺混比例计,需要160万吨左右的甲醇。
如果按照GDP年均增长率7%计算,2015年国内汽油消费需求量约为1亿吨,甲醇按照15%(M15)的掺比计,需要1500万吨的甲醇。
总体来说,到2015年,在甲醇汽油方面预计消耗甲醇约1660万吨/年。
5、二甲醚
二甲醚是甲醇的下游产品,是理想的柴油和液化石油气的替代燃料。
二甲醚与液化石油气的物理性质很相似,具有惰性、无腐蚀性、无致癌性、几乎无毒的特性。
据预测,“十二五”期间,我国每年柴油缺口在3000万t以上,每年液化石油气缺口在1100万t以上,以煤制甲醇为基础,延伸醇———醚———氢产业链,填补巨大的燃料市场,是重要的战略举措。
推广使用甲醇汽车与甲醇燃料,可以带动二甲醚替代柴油及液化石油气的技术开发和应用。
6、烯烃
近年来,随着国民经济的快速发展,我国对石油资源的需求日益增长,已经成为石油生产大国和消费大国。
2010年我国原油对境外石油的依存度超过50%。
我国石油缺口逐年增大已是不可回避的严峻现实,并对能源的安全供应、国民经济的平稳运行以及全社会的可持续发展构成了严重威胁。
就我国煤炭和石油的储量对比关系来看,用煤炭为原料替代石油发展化工,可以扬长避短,能够满足未来相当长时间内的原料需求,同时可提高资源的合理、有效利用程度,在资源的有效利用方面具有明显的优势。
随着现代煤化工技术的发展,以煤为原料经适当的工艺路线来生产聚乙烯和聚丙烯产品已经成为可能,因此,利用我国丰富的煤炭资源,采用先进的煤化工技术,大力发展煤制烯烃产业,在我国拥有广阔的市场前景。
六、甲醇产业关注重点
未来一段时期内,我国甲醇行业要把握好当前和长远的关系,大力推进结构调整和技术进步;严格控制甲醇产能的盲目扩张,淘汰落后产能;加快新技术、新产品的市场研发,延长产品链条,积极拓展下游应用,实现甲醇行业持续、稳定、健康发展,促进由甲醇大国向甲醇强国的转变。
关注的重点将在以下方面。
(一)合理调控甲醇总量,加快淘汰落后产能
从提高能源转化效率、优化产业布局、严格准入条件三个方面,加强对产业发展的引导。
严格新建项目的审批,提高准入门槛,遏制盲目建设。
建立健全市场机制,加强市场机制对于淘汰落后产能和促进产业结构调整的作用。
通过先进产能替代落后产能,实现总量平衡和产业布局的合理调整。
(二)提高产业集中程度,优化产业空间布局
鼓励强强联合、兼并重组。
支持业内龙头企业、能源企业,通过兼并重组,整合生产要素,优化资源配置,实现优势互补,形成大型化和集约化的企业集团,提高产业集中度。
按照园区化、集约化模式和发展循环经济、保护生态环境的要求,进一步优化产业布局,推进产能向资源地集中。
促进我国甲醇下游产业链的发展,提高甲醇产品的就地消化率,减少低值液态产品运输。
(三)加快原料结构调整,提高资源综合利用效率
完善和提高水煤浆气化、加压粉煤气化(17.50,0.51,3.00%)等技术的研发和应用水平。
在总量控制的前提下,具备资金、资源条件的企业进行原料结构调整,减少对天然气和晋城无烟煤的过度依赖。
积极发展以焦炉气为原料生产甲醇,促进焦炉气资源的有效利用。
(四)积极推进产品结构调整,提高企业经济效益
转变发展方式,鼓励企业向延长产品链、产品多元化方向发展,实现产品的高性能化、专用化和高附加值化。
改变目前甲醇基本作为商品出售、附加值低、抗风险能力弱的状况。
鼓励甲醇企业发挥自身技术、经济优势及所在地资源优势,在现有产品的基础上,重点发展化工新材料、精细化工、新能源等领域中的高技术含量、有市场需求、附加值高的延伸产品,优先选择发展资源综合利用型产品。
加快甲醇制烯烃示范项目的完善、评估及成熟技术的适时、适度推广,积极推动甲醇燃料及甲醇下游新产品、新技术的市场研发。
(五)坚持自主创新引领行业,淘汰落后技术和装备
加强前沿技术、核心技术装备的开发研究。
重点开发进一步大型化和提高气化压力的国产化干煤粉气化技术,高效率的大型国产化压缩机技术,高效、低压、大型化甲醇合成技术。
推进煤的洁净利用,提高高灰、高硫、低热值劣质煤的综合利用水平,推广褐煤高效洁净综合利用技术。
推进百万吨级以上的大型甲醇装置的国产化。
推广连续加压煤气化、低压法甲醇合成、精脱硫、中低压甲醇合成催化剂等先进技术,提高装置技术水平;淘汰和限制落后的工艺和设备,改善企业装备状况。
(六)开发应用清洁节能技术,建设环境友好型企业
统筹兼顾产业发展与生态环境保护,着力推动清洁生产、节能减排。
加快新型节能技术推广应用,充分利用生产过程余热、余压,实现能量梯级利用,降低原材料及动力消耗。
加大清洁生产和环境保护的投入,全面推广废气废固资源化利用、循环冷却水超低排放、氨法锅炉烟气脱硫等技术,搞好三废的资源化利用。
七、甲醇产业发展建议
(一)进一步加强规划引导
按照国家煤化工产业发展政策,对已规划的区域加强指导,在园区详规中按一体化的原则合理布局项目。
在项目实施中,要严格对规模、节能减排、环保、技术水平等方面进行审核,凡未纳入规划、建设规模达不到国家产业政策标准的不予核准或备案。
同时,近几年来,在甲醇直接掺烧汽油尚未得到国家许可和甲醇制烯烃未形成规模的情况下,甲醇市场将出现供过于求,须慎重对待。
建议国家有关部门牵头,组织甲醇汽油的应用试验,建议尽快出台法规、标准等规范性文件。
(二)加快水源、交通等基础配套建设
建设等大型水源工程,适时启动实施引水工程。
加快铁路、公路、机场等交通建设,为甲醇化工产业发展提供安全可靠的运输条件。
加强重点工业园区基础设施和城镇配套建设,促进甲醇化工项目顺利实施。
(三)推进资源节约和有效利用
加快资源税费制度改革步伐,推行煤炭资源储量管理。
强化对各类开发主体的监管,提高煤炭资源回采率。
对规划布局的项目进行水资源合理配置,尽快确定节水工艺、技术的产业标准,大力提倡采用污水处理、中水回用等节水措施,不断提高循环水浓缩倍数和水资源重复利用率,最大限度减低水资源消耗,发展节水型甲醇化工产业。
(四)加强生态环境保护和治理
以煤头路线为主,酸性气体和灰渣排放量较大,主要项目规划在生态脆弱、环境容量有限、产业密集的区域,必须防范由甲醇生产造成的环境污染风险,依法开展规划、区域和建设项目环境影响评价;在项目建设中,遵循循环经济的理念,积极采用先进技术工艺,推进“三废”等污染物的减量化、无害化和资源化综合利用,加强二氧化碳气体减排和综合利用工作,建设环保处理设施,采用洁净煤等减污技术,力争达到少排放、零排放或无害化处理的目标,确保不损坏或少损坏环境,促进全社会的和谐发展和甲醇化工产业的健康发展。
(五)加强技术和装备国产化研究
引进国外的技术和设备投资高昂,不仅采购供货周期长、专利技术使用费用昂贵,而且投产后存在运行、维修、保养成本过高等问题,导致项目投入产出比过小。
我国一些甲醇生产技术及生产设备已经处于国际先进水平,因此,应积极发挥科研优势,坚持自主创新,进一步加强国产化技术和装备研究,深入挖掘国内科研技术成果,鼓励具有我国自主知识产权的甲醇生产技术与国产化装备的应用,促进我省甲醇化工产业健康快速发展。
(六)推动甲醇