输油管道施工方案完整版.docx
《输油管道施工方案完整版.docx》由会员分享,可在线阅读,更多相关《输油管道施工方案完整版.docx(21页珍藏版)》请在冰豆网上搜索。
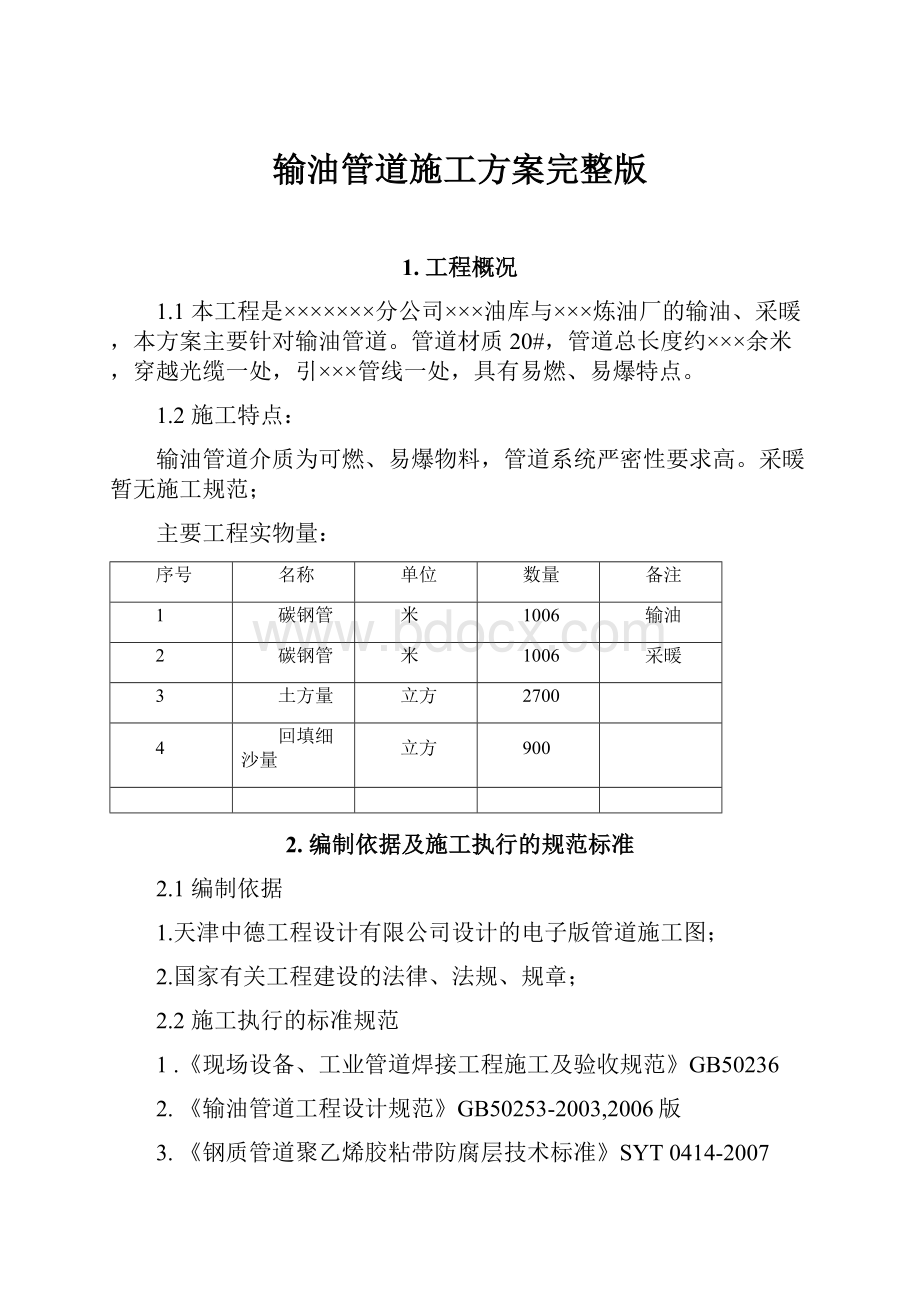
输油管道施工方案完整版
1.工程概况
1.1本工程是×××××××分公司×××油库与×××炼油厂的输油、采暖,本方案主要针对输油管道。
管道材质20#,管道总长度约×××余米,穿越光缆一处,引×××管线一处,具有易燃、易爆特点。
1.2施工特点:
输油管道介质为可燃、易爆物料,管道系统严密性要求高。
采暖暂无施工规范;
主要工程实物量:
序号
名称
单位
数量
备注
1
碳钢管
米
1006
输油
2
碳钢管
米
1006
采暖
3
土方量
立方
2700
4
回填细沙量
立方
900
2.编制依据及施工执行的规范标准
2.1编制依据
1.天津中德工程设计有限公司设计的电子版管道施工图;
2.国家有关工程建设的法律、法规、规章;
2.2施工执行的标准规范
1.《现场设备、工业管道焊接工程施工及验收规范》GB50236
2.《输油管道工程设计规范》GB50253-2003,2006版
3.《钢质管道聚乙烯胶粘带防腐层技术标准》SYT0414-2007
4.《涂装前钢材表面锈蚀等级和除锈等级》GB8923-88
3.施工原则
3.1施工步骤:
首先进行打砂防腐,检验合格后进入现场组对施工,首先采用先放线开管沟;然后就地在坑边将管道(即从库区围墙到***炼厂围墙)根据实际地下障碍物情况分段组对焊接、探伤;最后由两台挖沟机相互配合将管道依次吊入垫好细沙的沟中并按图调整好位置,将固定口焊接、进行100%探伤后,打压、防腐保温然后进行回填;对穿越引松管线、围墙及进入装置区的焊缝进行100%探伤。
3.2管道工程技术准备、过程控制及交工资料收集原则
1.在收到施工图纸后、组织管道施工人员熟悉图纸,全面地了解整个装置的管道布置情况、特点、重点、难点所在、了解设计的意图,参加设计交底及答疑,将发现的问题尽量在施工之前解决掉。
2.打砂防腐:
2.1.喷砂前,喷砂除锈用的砂,要求颗粒坚硬、干燥、无泥土及杂质的粗河砂,砂料粒径以0.5~1.5mm为宜,筛选前须晒干或明火烘干,存储于棚内、室内,筛孔大小为:
粗筛40~48孔/cm2。
2.2.喷砂操作时,空压机气压为0.6MP以下,喷砂前应检查压力容器是否有合格证、喷砂工必须佩戴好防护工具、并检查是否安全可靠,当喷嘴孔口直径增大25%时宜更换。
2.3.工艺控制施工时除应环境保护和注意防尘,还必须每日检测施工现场环境温度、湿度和金属表面的温度,做好施工记录。
当空气相对湿度大于85%、金属表面温度低于露点以上3℃时不得施工。
喷砂用的压缩空气必须经冷却装置及油水分离器处理,以保证干燥、无油;喷嘴到钢管表面距离以300~500mm为宜,喷砂前对非喷砂部位应遮蔽保护。
喷射方向与钢管表面法线夹角以15°~30°为宜。
2.4.质量控制
喷砂完成后首先应对喷砂除锈部位进行全面检查,其次要对基体钢材表面进行清洁度和粗糙度检查。
对钢管表面进行清洁度和粗糙度检查时,一是严禁用手触摸;二是应在良好的散射日光下或照度相当的人工照明条件下进行,以免漏检。
注:
若不易喷射的部位,可手工或动力工具除锈并达到St3级要求。
除锈后,对可能刺伤防腐层的尖锐部分应进行打磨。
并将附着在金属表面的磨料和灰尘清除干净。
喷砂除锈后,金属结构表面清洁度应达到Sa2.5级,应对照《涂装前钢材表面锈蚀等级和除锈等级》中提供的照片进行比较,比较时至少每2平方米有一个比较点。
2.5.防腐工艺:
2.5.1.在喷砂除锈合格后进行防腐工序前,应检查钢管表面是否因室内与室外温度差产生湿气,若有必须用干燥的压缩空气吹干表面水分并检查金属表面露点温度达到3℃以上时可以涂刷厂家配套的丁基橡胶底漆一遍,在风沙较大、雨雪天气时,没有可靠的防护措施,不应进行现场施工。
底漆涂敷时应充分搅拌均匀,按照制造商提供的底漆说明书的要求涂刷底漆。
底漆应涂刷均匀,不得有漏涂、凝块,和流挂等缺陷。
待底漆表干后再缠绕胶粘带,期间应防止表面污染。
2.5.2.胶粘带解卷的最低温度不应低于产品说明书规定的最低温度,在过低温度下解卷会造成胶粘带的损坏,胶带缠绕方法:
宜使用专用缠绕机或手动缠绕机进行缠绕。
缠绕过程中,应保持胶粘带始终如一的缠绕张力,以保证胶粘带的搭接量、平行度,避免防腐层产生皱褶。
在缠绕胶带时,如焊缝两侧可能产生空隙,应采用胶粘带制造商配套供应的填充材料填充焊缝两侧。
在涂好底漆的钢管上按照搭接要求缠绕胶粘带,胶粘带始末端搭接长度应不小于1/4管子周长,且不少于100mm。
两次缠绕搭接缝应相互错开。
搭接宽度遵照设计规定,但不应低于25mm。
缠绕时胶粘带搭接缝应平行,不得扭曲皱褶,带端应压贴,使其不翘起。
管端应有150mm±10mm的焊接预留段。
2.5.3.防腐管的堆放层数以不损伤防腐层为原则,在防腐管层间及底部垫上软质垫层。
运输时应采取相应的防护措施防止损伤防腐层。
防腐管吊装应采用宽尼龙带或专用吊具,不能用损伤防腐层的吊具。
采用合理的吊装方法,轻吊轻放,严禁损伤防腐层。
2.5.4.补伤及补口
修补时先修整损伤部位,并清理干净,涂上底漆。
使用与管体相同的胶粘带修补时,采用缠绕法;也可使用专用胶粘带采用贴补法修补。
补口带与原防腐层搭接宽度应不小于100mm。
补口处防腐等级应不低于管体防腐层。
缠绕和贴补宽度应超出损伤边缘至少50mm。
2.5.5.表面预处理质量检验:
预处理后的钢管表面应进行表面预处理质量检验。
用《涂装前钢材表面锈蚀等级和除锈等级》GB/T8923中相应的照片进行100%目视比较。
2.5.6.防腐层外观检验:
应对防腐层进行100%目测检查,防腐层表面应平整、搭接均匀、无永久性气泡、无皱褶和破损。
2.5.7.厚度检验:
每20根防腐管随机抽查一根,每根测三个部位,每个部位测量沿圆周方向均匀分布的四点的防腐层厚度。
每个补口、补伤随机抽查一个部位。
厚度不合格时,应加倍抽查,仍不合格,则判为不合格。
不合格的部分应进行修复。
2.5.8.电火花检漏:
现场涂敷的防腐层应进行全线电火花检漏,补口、补伤逐个检查。
发现漏点及时修补。
检漏时,探头移动速度不大于0.3m/s;检漏电压按下列公式计算确定:
当Tc≥1.2mm时,V=7843
=7843*1.1=8627(V)
Tc式中V—检漏电压;Tc—防腐层厚度(mm)
2.5.9.剥离强度检验:
剥离强度测试应在缠好胶粘带24h后进行。
用刀环向划开10mm宽、长度大于100mm的胶粘带层,直至管体。
然后用弹簧秤与管壁成90º角拉开,拉开速度应不大于300mm/min。
测试时的温度宜为20℃~30℃。
现场涂敷时,每千米防腐管至少应测试三处;补口、补伤抽查1%。
剥离强度值应不低于20N/cm。
若一处不合格,应加倍抽查,仍不合格,全部返修。
3.管道施工员按设计施工图绘制单线图,并对焊口按管道号进行编号,附焊接记录表-并交于施工班组。
施工人员将焊缝编号、焊接日期、焊工代号、无损检验结果等施工记录入焊接记录中。
4.对于管道施工中形成的施工记录(如隐蔽工程记录、管道试压记录、管道的预拉伸记录等)应及时办理各方的签字确认。
格式采用SH3503-J201/J202/J115/J117;
3.3现场预制、安装施工原则
3.3.1.管道的焊接采用手工氩弧焊打底,手工电弧焊盖面。
管道的焊材选用如下表所示:
序号
母材材质
焊条牌号
焊丝
备注
1
碳钢+碳钢
E4303
ER50-4
3.3.2.管道对接一般焊缝检测采用100%超声(Ⅰ级合格)加15%X射线(Ⅱ级合格),合格等级及检验级别符合《GB50253-2003,2006版》表中规定。
3.3.3.工艺管线采用工艺卡进行管理,在施工过程中将管线焊接工序与无损检验统一起来管理,做到每一个焊口都有记录。
4.施工程序
管线施工程序见下页图
5.施工方法及技术要求
5.1输油管线施工准备
5.1.1技术准备:
在管线施工开工前,要仔细审阅施工图,编制输油管线施工方案,在正式施工前对所有参加管线施工的人员进行技术交底。
5.1.2施工机具的准备:
根据施工方案的要求配备足够的处于完好状态的机具设备(包括各种焊机、探伤机、试压泵等)。
5.1.3材料的准备:
在施工之前,提出管线的材料领用计划,并根据施工进度安排陆续进料,保证管线能连续施工。
5.1.4施工现场的准备:
合理布置管道的预制场地,管道半成品的存放场地。
5.1.5考试试件类别及位置:
焊接方法分类
焊接方法分类
代号
手工电弧焊
D
钨极氩弧焊
Ws
试件、焊缝类别及位置分类代号
试件及焊缝类别
代号
位置分类
代号
对接焊缝性质
管状坡口对接焊缝试件(TG)
TG
管立焊/水平固定
F/V/A
全焊透
考试试件为:
DN200,厚度6.5,材质20#钢管,管状坡口对接焊缝试件。
5.1.6.管状坡口对接焊缝试件,应进行外观检验、射线(Ⅱ合格)检验,
应在焊接作业指导书规定的范围内,在保证焊透和熔合良好的条件下,采用小电流、短电弧、快焊速和多层多道焊工艺,并应控制层间温度。
见附页焊接作业指导书
焊接作业指导书
(第页共页)
单位名称中石化吉林石油分公司农安油库外网输油管道
编制人批准人签字
焊接作业指导书编号日期焊接工艺评定报告编号
焊接方法机械化程度手工半自动自动
焊接接头:
坡口图:
坡口形式
母材:
20#
类别号组别号与类别号组别号相焊
或标准号牌号与标准号牌号相焊
厚度范围:
管材直径、壁厚范围:
对接焊缝Φ219*6.5mm
焊接材料:
焊条类别其它
焊条标准
填充金属尺寸
焊丝、焊剂牌号
焊条、焊丝填充金属化学成分(%):
C
Si
Mn
P
S
Cr
Ni
Mo
V
Ti
焊接位置:
对接焊缝的位置
焊接方向:
向上向下
角焊缝位置
焊后热处理:
保温方式冷却方式
预热:
最低的预热温度
最高的层间温度
保持预热时间
加热时间
保护气体
尾部保护气流量
背面保护气流量
电特性:
电流种类极性
焊接电流范围(A)电压范围(V)
接前页
焊缝层次
焊接方法
焊条、焊丝
焊接电流
电弧电压范围(V)
焊接速度(cm/min)
线能量
牌号
直径
极性
电流(A)
钨极规格及类型:
钍钨极或铈钨极
熔化极气体保护焊溶滴过渡形式:
喷射过渡短路过渡
焊丝送进速度范围
技术措施:
摆动焊或不摆动焊摆动方式
喷嘴尺寸
焊前清理或层间清理
背面清根方法
导电嘴至工件距离
多道焊或单道焊
单丝焊
锤击有无
环境温度相对湿度
当焊件露点温度低于0℃时,焊缝应在始焊处100mm范围内预热到15℃以上。
若露点温度过低,焊后可酌情进行岩棉保温缓冷15分钟。
5.2材料的检验与管理
5.1材料检验
1.聚乙烯胶粘带和底漆出厂时应有产品说明书、合格证、质量检验报告、安全数据表等技术资料并包装完好,包装上应注明产品型号、批号、制造商名称、生产日期和储存有效期。
按照制造商提供的说明书要求储存底漆和聚乙烯胶粘带。
2.管道组成件必须具有质量证明文件,无质量证明文件不得使用。
3.管道组成件在使用前应进行外观检查,其表面质量应符合相应产品标准规定,不合格者不得使用。
a.钢管的表面质量应符合下列规定:
—钢管内、外表面不得有裂纹、折叠、发纹、扎折、离层、结疤等缺陷;
—钢管表面的锈蚀、凹陷、划痕及其他机械损伤的深度,不应超过相应产品标准允许的壁厚负偏差;
—钢管端部、坡口的加工精度及粗糙度应达到设计文件或制造标准的要求;
—有符合产品标准规定的标识。
b.管件的表面不得有裂纹,外观应光滑、无氧化皮,表面的其他缺陷不得超过产品标准规定的允许深度。
坡口、螺纹加工精度及粗糙度应符合产品标准的要求。
焊接管件的焊缝应成型良好,且与母材圆滑过渡,不得有裂纹、未熔合、未焊透、咬边等缺陷。
C.阀门的外观不得有裂纹、氧化皮、粘砂、疏松等影响强度的缺陷。
4.凡按规定作抽样检查或检验的样品中,若有一件不合格,必须按原规定数加倍抽检,若仍有不合格,则该批管道组成件不得使用,并作好标识和隔离。
5.所有阀门根据要求进行压力试验,有上密封结构的进行上密封实验,试验合格的阀门做上标识并作好记录,未经检验的阀门不得运至现场安装。
5.2材料管理
1.材料应由专职材料管理人员进行管理。
2.材料按品种、材质、规格、批次划区存放,并作好标识。
3.室外存放的管材、管件应下垫、上盖,防止防腐层受损。
4.材料发放时,核对材质、规格、型号、数量,防止错发。
5.焊材严格按焊材管理发放制度执行。
5.3管道的预制
5.3.1管线下料
1.预制管段要将内部清理干净,管内不得有砂土、铁屑及其他杂物,用塑料管帽或用盖板封好管口,防止异物进入管内。
2.每一预制段都应标明区号、管号、焊口号、焊工号。
3.管子下料尺寸应根据管段图对照总的管道施工平面及竖面图来确定。
4.在计算下料尺寸时,同时要考虑对口间隙、切割余量和焊接收缩量。
5.3.2管线切割及坡口加工
6.按图纸要求的几何形状及尺寸加工坡口,坡口端面要与管子轴线垂直,坡口要用磨光机打磨出金属光泽。
8.管子坡口加工型式如下图,图中L≥4(S1-S2)。
5.3.3管线组对
1.对照图纸核对下料尺寸,不得有误。
2.看清图纸,弄清管件的组对方位。
3.检查坡口几何形状及尺寸是否正确,坡口内外20mm范围打磨清洁。
4.管子管件组对时其内壁应做到平齐,内壁错边量不得超出相应规范要求。
5.3.4管道的点焊
1.管道焊口定位焊的焊接工艺要求与正式焊接相同,并应由同一焊工施焊。
2.定位焊焊肉的长度、高度及点数,按下表要求执行。
管壁厚度Smm
<3
3≤S<5
5≤S<12
≥12
定位焊长度mm
6—9
9—13
12—17
14—20
定位焊高度mm
2
2.5
3—5
≤6
点数
2
2—4
3—5
4—6
3.定位焊的焊肉不得有裂纹及其他缺陷,否则应立即去除缺陷,重新进行定位焊。
4.定位焊焊肉两端应磨成缓坡形。
5.4管线的焊接
5.4.1施焊前根据焊接工艺评定编制焊接工艺指导书,在焊接过程中必须严格按焊接工艺进行控制,以确保其焊接质量。
5.4.2焊材的烘烤、保管、发放、使用正确。
焊条应按焊接工艺卡的要求进行烘烤,并在使用过程中保持干燥。
焊条应存放在焊条保温筒内,焊条保温筒内不可存放不同牌号的焊条,当日未用完的焊条应应回收并做好记录。
5.4.3管道焊接时,焊接参数严格按焊接工艺卡执行,焊接坡口表面两侧各20mm范围内清除掉油漆、毛刺、锈斑、氧化皮、水分和其它对焊接有害的物资。
并应采取措施防止管内成为风道,必要时应封闭管道两端。
5.4.4焊口正式焊接的起焊点,必须选在两定位焊焊肉之间,禁止在定位焊处起焊。
不准在母材上引弧,引弧时要在坡口面内或引弧板上进行。
在焊接中应确保起弧与收弧的质量,收弧时应将弧坑填满。
多层焊的层间接头应相互错开。
在焊接时应确保起弧与收弧处的质量,收弧应将弧坑填满。
多层焊的层间接头应相互错开。
焊接过程中要仔细施焊,避免咬边、气孔、夹渣、弧坑及未焊透等缺陷,如发现这些缺陷,应停止继续施焊,及时处理缺陷。
5.4.5多层焊接时层间应用砂轮机或钢丝刷仔细清除焊渣、残留凝固了的焊珠和飞溅物等,要根据母材材质分别准备砂轮片和钢丝刷。
5.4.6除工艺有特殊要求外,每道焊缝均应一次连续焊完。
5.4.7每道焊道应做好施工记录,记下焊工号、焊口号及焊接日期。
格式采用SH3503-J123/J124;
5.4.8管道的施焊环境如出现下列情况之一时,应采取防护措施,否则不得施焊。
1.风速大于或等于8m/s,(气体保护焊为2m/s);相对湿度大于90%;
2.下雨或下雪;
3.环境温度低于0℃。
5.4.12焊后外观检查不得有咬边、夹渣、余高过高、过度氧化、未焊透、未熔合、内凹等,一旦有这类缺陷,令焊工对其进行返修,直至外观检查合格。
5.6半成品的存放、保护及运输
5.6.1在管道预制场设吊车及卡车,用于管道材料及管道预制件的装卸及运输用。
5.6.2预制完的管道应在管段的醒目处做上标识,注明该管段的安装区号、管号、预制人、安装位置。
5.6.3预制完的管段所有的开口处均应进行封堵,防止脏、杂物进入管内。
5.7管道的安装
5.7.1管道安装具备的条件
1.与管道有关的土建工程已施工完毕,并经土建与安装单位人员共同检查合格。
2.管材、管件、阀门等已经检验合格。
3.预制管段内已清理干净,不留污物或杂物。
5.7.2管道的安装要求
1.管道安装必须符合施工图纸要求,包括管材管件的材质、规格、型号、管线走向、管件阀门安装顺序及坡度等符合要求。
2.安装时应将法兰面清理干净,并检查法兰密封面上不得有影响密封性能的划痕、锈斑等缺陷。
3.法兰连接的阀门在安装过程中应处于关闭状态,焊接法门在安装时应处于开启状态。
4.垫片在安装前应进行外观检查,不得有影响密封性能的缺陷;
5.当管道安装工作有间断时,应及时封闭敞开的管口,重新开始安装时,应检查管内是否有异常情况。
14.管道安装尺寸偏差不应超过下表要求:
管道安装尺寸允许偏差一览表
项目
允许偏差(mm)
坐标
架空及地沟
室外
25
室内
15
标高
架空及地沟
室外
±20
室内
±15
水平管道弯曲度
DN≤100
2L‰,最大50
DN>100
3L‰,最大80
立管铅垂度
5L‰,最大30
成排管道的间距
15
交叉管的外壁或绝热层间距
20
6.管道系统试压、清洗
6.1管线试压、清洗方案另外编写详细的方案,其主要原则如下:
1.管道系统全部施工完毕,符合设计要求和相关规范要求。
3.焊接无损检验工作都已完成,检验合格。
4.焊缝及其它应检查部位不得涂漆或设绝热层。
5.试验用临时加固措施符合要求,标记清晰,安全可靠。
6.试验用的检测仪表符合要求,压力表应经校验合格,精度不低于1.5级,量程为最大被测压力的1.5-2倍,表数不少于两块。
试压露点温度应在5℃以上。
7.有完善的试压方案,并经批准,对试压人员进行技术交底。
6.2液压试验准备
1.试验介质用洁净水,水中不得含有沙粒、铁锈等异物。
2.确定试验压力为设计压力的1.5倍。
6.3管道水压试验
1.水压试验应缓慢升压,待达到试验压力后,稳压10分钟,再降压至设计压力,停压30分钟,检查以无降压、无泄漏、无变形为合格。
2.降压时,排放地点应选在室外合适地点。
3.当最高点压力降至表压为零时,应及时打开进气阀,严禁系统造成负压。
4.管道系统试压完毕,应及时拆除所用的临时盲板。
5.试压合格,管道除锈防腐检测按照施工蓝图工艺说明第三项执行。
6.4水压试验注意事项
1.对位差较大管道,应将试验介质的静压计入试验压力中,液体管道的试验压力应以最高点的压力为准,但最低点的压力不得超过管道组成件的承受力。
2.试验前,注水时要打开排气口,排尽空气。
3.当试验过程中发现泄漏时,不得带压处理。
消除缺陷后,重新进行试验。
4.在系统试压前被拆除不与系统一起试压的短管段应单独试压,合格后恢复到原来位置。
5.压力试验过程中,作好压力试验记录,经业主、监理等几方共同检查合格后,及时办理签字确认。
6.5若冬季严寒不能水压试压则需设计同意改为气压,强度试验压力为设计压力的1.15倍,稳压时间4小时,不破裂、不渗漏合格;严密性试验压力为设计压力的1.1倍,稳压时间4小时,以压降不大于1%试验压力值为合格。
气压试压时不宜上升过快,应缓慢上升0.3到0.6倍强度试验压力时稳压30min,管道无异常可继续试验压力,试压区域内严禁非试压人员进入,试压人员应与试压管道保持6米以上距离,距试压设备及试压管段50米内为试压区域。
6.6管道系统吹洗:
格式采用SH3503-J410
1.吹洗方法应根据对管道的使用要求、工作介质及管道内表面的脏污程度确定。
公称直径<600mm的液体管道宜采用水冲洗;
2.冲洗管道应使用洁净水时,水中氯离子含量不得超过25ppm。
水冲洗应连续进行,以排出口的水色和透明度与入口水目测一致为合格。
6.7.管道下沟与回填:
在前面工序合格管道下沟前,应复查管沟尺寸,清楚杂物,并用电火花检测仪检查管道防腐层,若有破损必须修补检测合格,按图纸要求垫好200mm细砂;两台钩机以12米间距设两个吊点轮流作业,由专业司索指挥将管道吊入沟内按图纸尺寸调整好位置;若沟内有积水需排除,回填600mm细砂,然后将地表耕作土回填于最上层。
9.质量控制措施
9.1严格按设计要求、图纸施工。
9.2实行岗位资格制,焊工施焊必须持证上岗,合格证项目与施焊项目相同,且在有效期内。
9.3认真作好工序检验交接工作,上道工序检验合格方可进行下道工序施工;执行“三检制”,设置质量控制点,以设计规范有关验收质量标准作检验验收依据,按控制点等级检验、报检、确认,质量控制点分三级,即A、B、C:
A级——为停检点,由业主或监理方验收的控制点。
B级——为由施工单位质检员验收的控制点。
C级——为一般控制点,由施工班组验证,施工员确认的控制点。
执行SH-3503作为交工资料依据,由参加验证各方签字确认,作为质量控制点检验状态记录标识,并保证其具有可追溯性。
质量控制点的设置见下表:
中国化学工程第
九建设公司
管道安装工程质量控制点
第1页
共1页
检验依据
GB50235-97,GB50236-1998,GB50252-94,GB50184-93,GBJ126-89,SH-3503
序号
控制点名称
检验内容
控制等级
备注
1
保证资料核查
管道组成件合格证明书或复验报告,方案,安全阀检验与标定
A
2
阀门检验
阀门试压,试压结果
B
3
组对焊接
坡口形式,角度,间隙,错边量,预热
C
4
管线安装
水平和垂直方向偏差,预拉伸量,支吊架,管托
C
5
阀门,管件安装
阀门,管件的压力等级,规格型号,法兰面平行偏差,管件清洁
C
6
焊接检验
焊缝外观质量,高度,宽度
B
7
隐蔽工程
基槽,管线敷设坐标,标高,坡度,防腐质量
A
SH3503-J201/J202/J115/J117
8
试验条件审查
施工记录,焊接记录
B
9
资料审查
焊工合格证、焊缝探伤比例、探伤记录
A
SH3503-J116/
J123/J124
10
强度,气密性试验
按设计规定进行试验,升降压速度,试验值,时间确认
A
SH3503-J410