地下连续墙施工专项方案.docx
《地下连续墙施工专项方案.docx》由会员分享,可在线阅读,更多相关《地下连续墙施工专项方案.docx(18页珍藏版)》请在冰豆网上搜索。
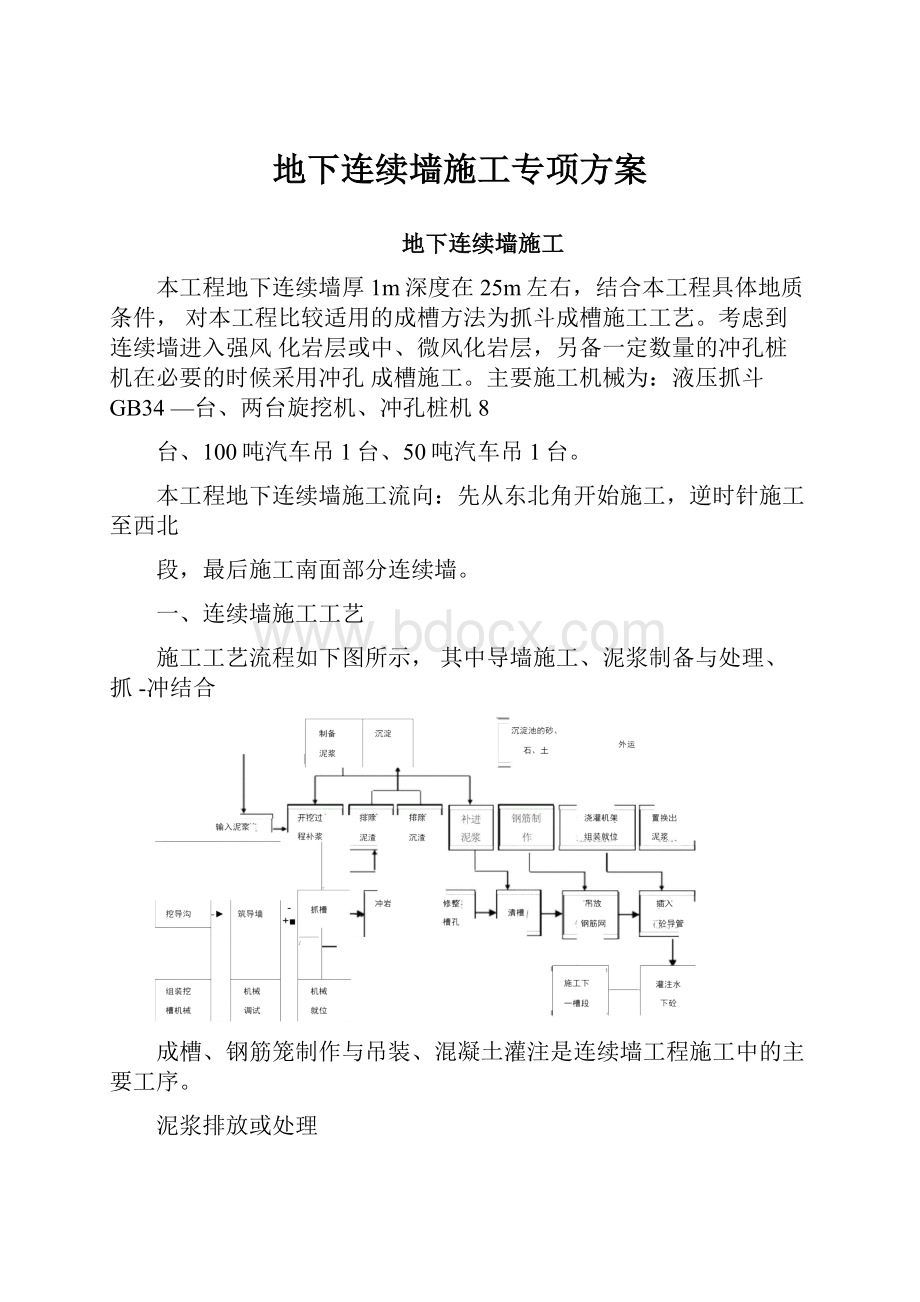
地下连续墙施工专项方案
地下连续墙施工
本工程地下连续墙厚1m深度在25m左右,结合本工程具体地质条件,对本工程比较适用的成槽方法为抓斗成槽施工工艺。
考虑到连续墙进入强风化岩层或中、微风化岩层,另备一定数量的冲孔桩机在必要的时候采用冲孔成槽施工。
主要施工机械为:
液压抓斗GB34—台、两台旋挖机、冲孔桩机8
台、100吨汽车吊1台、50吨汽车吊1台。
本工程地下连续墙施工流向:
先从东北角开始施工,逆时针施工至西北
段,最后施工南面部分连续墙。
一、连续墙施工工艺
施工工艺流程如下图所示,其中导墙施工、泥浆制备与处理、抓-冲结合
成槽、钢筋笼制作与吊装、混凝土灌注是连续墙工程施工中的主要工序。
泥浆排放或处理
连续墙施工工艺流程图
二、连续墙施工方法
(1)导墙施工
控制标高,控制槽段,钢筋网定位,防止槽口坍塌及承重。
导墙施工顺序为:
平整场地T测量定位一挖槽一浇注垫层一绑扎钢筋一
支模板一浇筑混凝土一拆模并设置横撑一导墙外侧回填粘土压实。
(2)泥浆配置和使用
泥浆的正确使用是成槽的关键。
结合本工程的地质特点和施工条件,采
用膨润土和优质粘土进行泥浆制备。
a、泥浆池及泥浆沟设置
在基坑内的设置2个三级泥浆池,包括沉淀池、循环池、储浆池,尺寸
为20m^6m,深度2m,采用C20混凝土浇筑,墙厚200mm泥浆池平面布置见下图。
泥浆池构造示意图
沿基坑外侧1.2m处设置400mm<400mm砖砌泥浆沟,地下连续墙施工完
成后作排水沟使用。
泥浆沟与泥浆池相连,同时通过预埋©400PVC管与连续
墙沟槽连接。
泥浆池构造见下图。
泥浆沟构造示意图
b、泥浆的配制:
拌制泥浆前,应根据地质条件、成槽方法等进行泥浆配
合比的初定,合格后方可使用。
优质粘土在使用前需经取样,进行泥浆配比
试验和物理分析。
将选定的优质粘土放入泥浆搅拌机中进行搅拌,制作泥浆。
新制备的泥浆必须在泥浆池存放24小时以上,使粘土充分水化后,才能使用。
泥浆主要成分为优质粘土和水,泥浆初步定的配比(占水的百分比)如下表:
泥浆配合比
水
膨润土
甲基纤维素
烧碱
1
10%
0.05%亠0.1%
0~0.3%
b、泥浆的性能:
泥浆性能指标应符合表6-2的规定,每天检查两次,对
不合格的泥浆应及时采取有效措施,进行处理。
其对于再生利用的泥浆,要适当掺入一定量的甲基纤维素和烧碱,并经检验合格。
泥浆的性能指标
项次
项目
性能指标
检验方法
备注
制
备
时
1
比重
1.1〜1.15
泥浆比重计
2
粘度
10〜25s
500ml/700ml漏斗法
3
含砂率
V6%
4
胶体率
>95%
重杯法
5
失水量
V30ml/30min
失水量仪
6
泥皮厚度
1〜3mm/30min
失水量仪
7
静切力
1min20〜30mg/cm2
静切力计
10min50〜
100mg/cm2
8
稳定性
v0.03g/cm2
9
PH值
7〜9
PH试纸
清槽后底部
1
比重
<1.15
泥浆比重计
泥浆取样在
槽底20〜
50cm处
2
粘度
<28
500ml/700ml漏斗法
3
含砂率
<8%
含砂量法
4
胶体率
>95%
重杯法
5
失水量
<30ml/30min
失水量仪
6
PH值
7〜9
PH试纸
c、泥浆的使用:
施工期间,槽内泥浆液面必须高于地下水位1.0m以上,
在砂层施工时,为避免槽壁塌方,应适当提高泥浆比重和粘度,增加泥浆储备量,备有堵漏材料。
d、泥浆处理:
采用机械处理和重力沉浆处理相结合的方法。
从槽段中置
换出来的泥浆经过机械处理后流入沉淀池,经重力沉淀16小时稳定后,用水
泵抽走表面清稀部分浆水到过滤池,并通过滤网过滤,将废水排除,余下的浆体再重新利用。
废弃的泥浆和残渣不得随意排放,按广州市余泥渣土排放管理规定执行。
(3)成槽工艺
a.接头施工
地下连续墙槽段间接头采用“工字钢”接头形式,这种接头具有加强槽段间整体性及传递剪力、减小渗漏、施工简单的特点。
为保证钢筋笼定位准确及便于二期槽段准确对位,工字钢需长至导墙内。
工字钢接头是根据设计钢筋网的外尺寸作为工字钢接头的净宽,以腹板为界线,二期槽段侧长度为25cm,—期槽段为15cm工字钢采用钢板场外加工而成,场内与I期槽段钢筋网拼接而成。
槽段工字钢平面示意图
由于工字钢与端孔间有一定的空隙,为避免浇注混凝土时,混凝土绕过空隙充填U期槽段空位,造成U期槽段施工困难。
因此,在接头处采用接头钢套箱止浆。
b.成槽的顺序
地下连续墙采用跳槽施工,一期浇注完成后达到70%虽度后方能进行相
邻的二期槽段施工。
c.成槽方法
成槽是地下连续墙施工关键工序之一,既控制工期又影响质量,根据地质情况及结合以往施工经验,我司采用液压抓斗和冲孔桩机配合施工。
采用两冲一抓,即使用冲孔桩机先冲端头孔,严格控制其垂直度,然后液压抓斗挖掘岩层(强风化)以上部分,强、中及微风化岩层换用冲孔桩机成槽。
岩层成槽时,先施工圆形主孔,后施工副孔,最后方锤修孔。
液压抓斗沿导墙壁挖土,通过液压抓斗导向杆调整抓斗的垂直度,以控制成槽精度,挖至岩面时,应尽量修平槽底,以减小冲孔桩机成孔偏差。
d.槽深的鉴定
当冲、抓至设计深度时,应汇同监理、设计、地质勘察单位及业主代表进行现场确认,确定终槽深度。
(4)钢筋网制安
根据设计图纸制作钢筋网,为保证钢筋网制作平直规整,钢筋网加工在场内的钢筋加工场进行,工字形接头型钢在场外加工,运往场内与钢筋网焊接,并严格控制加工尺寸精度。
钢筋笼吊放主要采用一台100t履带式起重机按“退吊”方式起吊,履带吊边退边提钩,必要时采用一台履带式起重机配合进行。
钢筋网吊点布置和起吊方式要防止起吊时引起钢筋网不可恢复变形。
由水平瞬删主髀鮭亶辭滋|妁时据如蛀號翱耶
地下连续墙钢筋网起吊示意图
a.钢筋笼制作
钢筋笼根据地下连续墙墙体配筋图来制作,按单元槽段做成一个整体,不分段制作。
根据设计要求,主筋保护层厚度迎土面为7cm,背土面为5cm,采用4mm
钢板制作定位块焊接在竖向桁架上。
制作钢筋笼时,要预先确定浇筑混凝土的导管位置,使该位置上下贯通。
钢筋笼在制作平台上一次成型。
钢筋网骨架及四边各交叉点全部采用点
焊,其余各纵横交叉点采用50%梅花形点焊,50%绑扎。
竖向钢筋桁架的布置应满足间距不大于1.5m,且布置应均匀,使钢筋笼
吊装保持平衡。
钢筋笼底端距离槽底面20cm,顶端伸出墙顶84cm=
连续墙钢筋笼上的预埋件,必须严格按设计要求进行施工。
钢筋笼制作应符合表5-3的规定。
钢筋笼制作允许偏差
项目
允许偏差
检查方法
检验方法
(mm)
范围
点数
长度(深度方向)
±50
每片钢筋网
3
宽度(段长方向)
±20
3
尺量
0
4
厚度(槽宽方向)
-10
主筋间距
±10
4
在任一断面连续量钢筋间距,取
分布筋间距
±20
4
其平均值作为一点
预埋件中心位置
±10
4
尺量
同一截面受拉钢筋接头数
<50%或按
量占钢筋总数量的比例
设计规定
b.钢筋笼吊放
钢筋笼采用100t履带式起重机吊装,必要时采用50t履带式起重机配合吊装,以防止起吊时钢筋笼变形。
起吊时不能使钢筋笼下端在地面上拖引,以防造成下端钢筋弯曲变形。
为防止钢筋笼吊起后在空中摆动,在钢筋笼下端系上拽引绳以人力操纵。
下放钢筋笼时,钢筋笼对准槽段中心,垂直又准确地插入槽内,钢筋笼进入槽内时,吊点中心对准槽段中心,徐徐下降,防止碰撞槽壁。
钢筋笼插入槽内后,检查其顶端高度是否符合设计要求,然后将其搁置在导墙上。
(5)清槽
清槽工作分2个阶段进行。
第1阶段:
成槽过程中清渣
1、在成槽过程中清渣,采用泥浆循环法,将输浆管通向孔底泵进新泥浆,使已冲开的泥渣上浮;
2、在成槽过程中,对于含砂率大,沉渣厚的槽孔需采用空气吸泥法进行清底,从皮管内压入空气通向槽底的吸泥装置,泥砂吸上,并同时补充新鲜泥浆,保持泥浆液面标高的相对稳定和槽壁稳定;
第2阶段:
最终清孔
最后清孔时,采用空气吸泥反循环清槽,与第一阶段
(2)相同,确保清
槽后槽底沉渣厚度满足设计要求。
空气吸泥法是用4寸管从管下压入6〜8Mpa
空气,空气上行产生压力差(负压)吸取泥渣。
操作是沿槽段口在槽底缓慢移动,抽吸槽底沉渣,在面上不间断地补充新泥浆,控制槽内的泥浆液面不低于导墙顶的0.5mo
在清槽后及灌注混凝土前,槽底沉碴厚度不大于100mm清槽后,槽底
以上0.2〜0.5m处的泥浆比重应小于1.15,含砂率小于8%粘度小于28s。
(6)水下混凝土浇注
地下连续墙混凝土按水下混凝土的要求配制及浇注。
浇注混凝土前须清
孔,并应将工字钢接缝面的泥土杂物冲刷干净。
1、按照混凝土的设计指标及施工工艺要求进行混凝土的配合比试验,确定混凝土的配合比。
2、钢筋笼验收合格后,会同建设、监理、设计单位和质检部门对该槽段进行隐蔽工程验收,合格后及时灌注水下混凝土。
钢筋笼在入槽后至浇注混凝土总停滞时间不应超过4个小时。
3、一个槽段内一般同时使用两根导管灌注,其间距不大于3m导管距
槽段接头端不大于1.5m。
两根导管同时开塞灌注混凝土,并保证两导管处的
混凝土表面高差不大于0.3m。
浇注导管埋入混凝土深度宜为2〜4m
4、每一槽段灌注混凝土前,混凝土漏斗及集料斗内应准备好足够的预
备混凝土,以便确保开塞后能达到_0.5m的埋管深度,并连续浇灌。
5、隔水栓用预制混凝土塞,开始灌注时,隔水栓吊放的位置应临近泥
浆面,导管底端到孔底的距离应以能顺利排出隔水栓为准,一般为0.3〜
0.5m。
6、在混凝土顶面存在一层浮浆层,需要凿去,因此混凝土需要超浇
50cm,以使在混凝土硬化后查明强度情况,将设计标高以上部分用风镐凿去。
7、地下连续墙的施工允许偏差和质量要求应符合下列规定:
槽底沉碴厚度不应大于100mm;
墙身垂直度:
土0.5%;
墙顶中心线偏差:
w30mm
(7)地下连续墙的凿除
凿除方法采用凿岩机、风镐结合人工的方法进行。
连续墙顶的浮渣层凿除后,按有关部门指定的槽段进行检测,验收合格后方进行下一工序施工。
凿除墙顶浮渣层前,墙顶以上的土体采用临时钢板桩支护,完成冠梁和挡墙施工后拔除钢板桩。
三、地下连续墙施工技术措施
1、连续墙的成孔和清孔应符合的要求
(1)导墙中心线与槽段中心线的偏差不得超出规范的要求,保证成槽位置的准确。
(2)制备泥浆的比重应控制在1.113;施工过程中应经常测定泥浆比
重和粘度。
(3)施工时要经常检查抓斗的垂直度,并随时调整,尤其是地面至地下
10m左右的初始挖槽精度,对以后的整个槽壁精度影响很大,必须慢速均匀掘进,保证成槽垂直度满足要求。
2、防止槽壁坍方的措施
(1)根据地质情况选择泥浆配合比,保证泥浆在安全液位以上,在施工期间如发现有漏浆或跑浆现象,应及时堵漏和补浆。
(2)减少地面荷载。
(3)防止附近的车辆和机械对地层产生振动。
(4)当挖槽出现坍塌迹象时,迅速补浆,提高泥浆液面和回填黄泥,待槽壁稳定后再重新开挖。
3、钢筋网的制作、安装措施
(1)钢筋笼制作时,主筋的焊接接头应错开。
(2)钢筋笼安装时,钢筋笼外侧需设置定位钢板,以确保钢筋笼保护层
的厚度;钢筋笼下沉到设计位置后,应立即固定,防止移动。
钢筋笼安装完毕时,应会同设计单位和监理人员进行隐蔽工程验收,合格后应及时灌注水下混凝土。
4、导管内卡混凝土处理
导管内卡混凝土产生的原因有:
(1)导管口离槽底的距离过小。
(2)混凝土的塌落度过小。
(3)石子粒径过大,砂率过小。
(4)浇灌间歇时间过长。
预防措施如下:
(1)保持导管口离孔底的距离不小于30cm=
(2)按设计要求制定混凝土的配合比,选用1〜3cm石,加强操作管理,尽量保持连续浇筑。
(3)浇筑间歇时,上下小幅度提动导管。
(4)选用非早强型的水泥,掺入减水剂和缓凝剂。
已堵管时,敲击、抖动、振动或提动导管(高度在30cm以内),或用长
杆对导管内混凝土进行疏通。
如无效,在顶层混凝土未初凝时,将导管拔出,改用带密封活底盖的导管插入混凝土内,二次开塞,重新浇筑混凝土。
5、斜孔
当遇到较大的块石或孤石时或在有倾斜度的软硬地层交界岩面倾斜处,容易造成斜孔。
斜孔现象在连续墙成槽中经常遇到,当前一槽段斜孔时不进行修正,在下放钢筋笼时将很难就位,还会引起下一槽段的施工困难。
解决办法是遇到斜孔时,填充优质的粘土块和石块,将斜孔部分填平,用液压抓斗慢抓或改换冲孔桩冲孔,低锤密击,往复扫孔纠正。
6、钢筋笼难以放入槽孔内或上浮
造成钢筋笼难以放入槽内或上浮的原因有:
(1)槽壁凹凸不平或弯曲。
(2)斜孔。
(3)钢筋笼尺寸不准。
(4)纵向接头处弯曲。
(5)钢筋笼重量太轻。
(6)槽底沉渣过多。
(7)钢筋笼刚度不够,吊放时产生变形。
(8)定位块位置突出。
(9)导管埋入深度过大,或混凝土浇灌速度过慢。
采取的措施如下:
(1)成孔要保持槽壁面平整。
(2)严格控制钢筋笼外尺寸,按设计图纸制作钢筋笼。
(3)如因槽壁弯曲钢筋笼不能放入,应修整后再放钢筋笼。
(4)钢筋笼上浮时,在导墙上设置锚固点固定钢筋笼,清除槽底沉渣,
加快浇灌速度,控制导管的最大埋深不要超过6m
7、混凝土浇注
水下混凝土必须具有良好的和易性,其配合比应通过试验确定,坍落度宜为180220mm(以孔口检验的指标为准)。
钢筋笼安放完毕后,应及时灌注水下混凝土,其间歇时间不得超过4小
时,灌注前应复测沉碴厚度。
混凝土浇注时,导管的埋管深度保持在24m,
相邻两导管的混凝土高差不应大0.3m,严禁将导管底端提出混凝土面。
每槽
段的留置试块不得少于一组。
在灌注混凝土过程中,若发现导管漏水、堵塞或混凝土内混入泥浆,应
立即停灌并进行处理。
四、连续墙特殊槽段的施工技术措施
根据槽段划分平面图,连续墙有为“L”型等槽段。
与“一”字型槽段相
比,特殊槽段在施工中需采取相应措施保证其施工质量要求:
1、导墙施工时,对于“L”型槽段,拐角处应向外放出50cm,满足抓土要求和保证转角处地下连续墙断面的完整。
2、根据以往施工经验,特殊槽段比“一”字型槽段在成槽过程中易发生槽壁坍方,所以在特殊型槽段长度划分上尺寸不宜过大,满足抓斗机取土尺寸即可,施工中要加快成槽进度,尽量缩短成槽时间,禁止重型机械在该处的来回移动,以保护槽壁稳定,防止坍方。
&成槽垂直度的控制
地下连续墙成槽工艺主要采用抓斗式成槽机和“二钻一抓”成槽的施工工艺。
抓斗式成槽机成槽的施工方法速度较快,成槽垂直度控制在1/300以内;“二钻一抓”成槽施工工艺成槽速度相对较慢,垂直度能控制在1/300以内;铣槽机可达1/600。
机械配备上可满足本工程设计要求。
工程中采用的成槽机和铣槽机均具有自动纠偏装置,可以实时监测偏斜情况,并且可以自动调整。
施工时按照设计槽孔偏差控制斗体和液压铣铣头下放位置,将斗体和液压铣铣头中心线对正槽孔中心线,缓慢下放斗体和液压铣铣头施
工成槽。
抓斗每抓2〜3斗即旋转斗体180度,每抓2m检测中心钢丝绳偏移距离,做到随时监控槽孔偏斜,以此保证槽孔垂直。
每一抓到底后(到砂层),用超声波
测井仪检测成槽情况,如果抓斗在抓取上部黏土层过程中出现孔斜偏大的情况,可用液压铣吊放自上而下慢铣修正孔形,但槽孔偏斜关键在抓斗抓取过程中控制。
地下连续墙成槽自动纠偏装置
五、地下连续墙施工平面布置
I1X
nnr
HF
b
训区
机
料
即左%却J
丫:
:
7*仲T
TTvi'''■■匸
1丄.
£■—nin-g—g
2号肌
.——=
mix
3号机
I.
顺
{区
5号机
尺、
L也
-t:
>*2
临HJ腿11道邯
泥;尺“
賈池r:
20*
6*2
临时施工道路
训区?
号机
El
地卜连续墙施工平面布置图
说壮】*陀挨墙肯1:
核方位划井为四牛itI:
区域.扎牛施「,鬼甚中束面为皿“氐;南闻为51~5】£;西面沖ll-H0dt®^NlM12hlTftK>-6冲由帖札曲工方式为爾「冲=具体喷序如丘
乐加E代3-E5-E2-E4E6;
北區3号机:
Kl-NT-N5-N2-PH-N6h2^H:
K7-N9-Kn4i8-N10-M2;
丙近:
帝和I:
肌⑷-乔和-巩弓机:
阶時卅O昭毗
WBi跨#USH3-S5-S2-S4,?
^札海眇$10£>59』号弘$H-S15-$l5-Sl2-SU-$]6.8台冲击怙机址城进斯「毎台负贵1个槽段的施工;成槽施工親一台就屋抓斗删°
2>慨氏5牛竊驗分划侯朋、D07*讯仏DQ7>«8>修业为松hM|7-h«7-2>DQ7-3.«8-L
六、施工人员
项目管理机构主要施工人员名单,职务及职称见下表
姓名
职务
职称
在本工程中拟担任工作
蔡敬义
组长
高级工程师
连续墙班组组长
周火锋
技术负责
工程师
技术负责人
钱海权
副组长
连续墙班组副组长
陈燕峰
安全员
安全员
梁准
施工员
施工员
王学华
施工员
助理工程师
施工员
陈友兴
施工员
施工员
黄家辉
测量员
助理工程师
测量员
卢剑文
试验员
试验员