发生炉煤气站设计规范.docx
《发生炉煤气站设计规范.docx》由会员分享,可在线阅读,更多相关《发生炉煤气站设计规范.docx(35页珍藏版)》请在冰豆网上搜索。
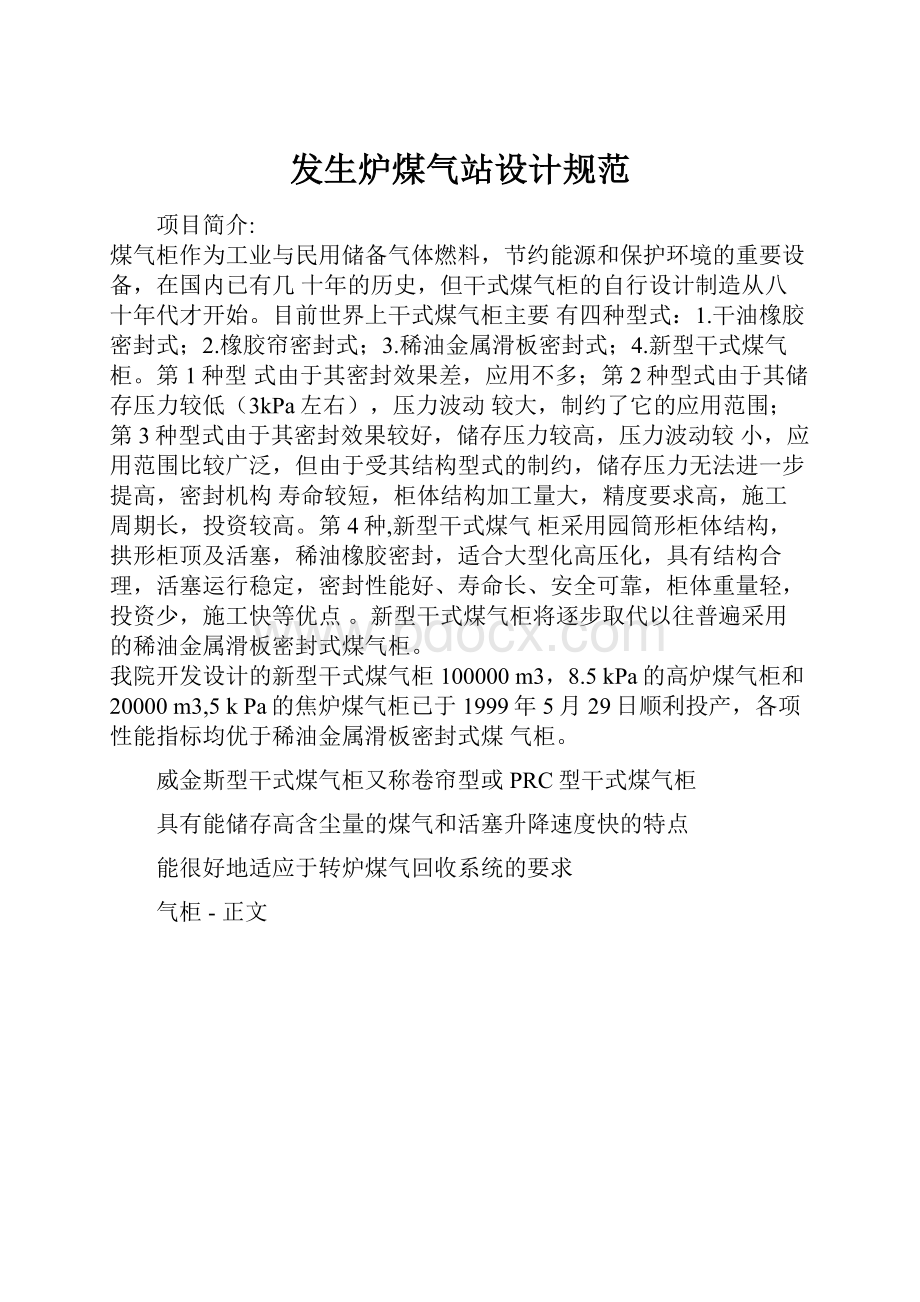
发生炉煤气站设计规范
项目简介:
煤气柜作为工业与民用储备气体燃料,节约能源和保护环境的重要设备,在国内已有几十年的历史,但干式煤气柜的自行设计制造从八十年代才开始。
目前世界上干式煤气柜主要有四种型式:
1.干油橡胶密封式;2.橡胶帘密封式;3.稀油金属滑板密封式;4.新型干式煤气柜。
第1种型式由于其密封效果差,应用不多;第2种型式由于其储存压力较低(3kPa左右),压力波动较大,制约了它的应用范围;第3种型式由于其密封效果较好,储存压力较高,压力波动较小,应用范围比较广泛,但由于受其结构型式的制约,储存压力无法进一步提高,密封机构寿命较短,柜体结构加工量大,精度要求高,施工周期长,投资较高。
第4种,新型干式煤气柜采用园筒形柜体结构,拱形柜顶及活塞,稀油橡胶密封,适合大型化高压化,具有结构合理,活塞运行稳定,密封性能好、寿命长、安全可靠,柜体重量轻,投资少,施工快等优点。
新型干式煤气柜将逐步取代以往普遍采用的稀油金属滑板密封式煤气柜。
我院开发设计的新型干式煤气柜100000m3,8.5kPa的高炉煤气柜和20000m3,5kPa的焦炉煤气柜已于1999年5月29日顺利投产,各项性能指标均优于稀油金属滑板密封式煤气柜。
威金斯型干式煤气柜又称卷帘型或PRC型干式煤气柜
具有能储存高含尘量的煤气和活塞升降速度快的特点
能很好地适应于转炉煤气回收系统的要求
气柜-正文
用于贮存各种工业气体,同时也用于平衡气体需用量的不均匀性的一种钢制容器设备。
可以分为低压气柜和高压气柜两大类。
前者又有湿式与干式两种结构。
湿式低压气柜 是最简单常见的一种气柜。
通常用于煤气贮存,它由水封槽和钟罩两部分组成。
钟罩是没有底的、可以上下活动的圆筒形容器(图1a)。
如果贮气量大时,钟罩可以由单层改成多层套筒式,各节之间以水封环形槽密封(图1b)。
寒冷地区为防冬季水封槽结冰,必须用蒸汽加热槽中的水。
湿式气柜构造简单,易于施工,但是其煤气压力波动大,土建基础费用高,冬季耗能大,检修时产生大量污水,寿命只有约10年。
大容量贮气柜用此型不经济。
此类气柜中国已有系列生产,其容量(103m3)为5、10、20、30、50、100、150、200等系列。
干式低压气柜 是内部设有活塞的圆筒形或多边形立式气柜(图2)。
活塞直径约等于外筒内径,其间隙靠稀油或干油气密填封,随贮气量增减,活塞上下移动。
多用于贮存煤气。
干式低压气柜的基础费用低,占地少,运行管理和维修方便,维修费用低,无大量污水产生,煤气压力稳定,寿命可长达30年。
大容量干式气柜在技术与经济两方面均优于湿式气柜。
中国已有容量(103m3)为20、50、100、150等系列。
气柜
高压气柜 贮存压力最大约16MPa,有球形和卧式圆筒形两种。
高压气柜没有内部活动部件,结构简单。
按其贮存压力变化而改变其贮存量。
多用于贮存液化石油气、烯烃、液化天然气、液化的氢气等。
容量大于120m3者常选用球形,小于120m3则多用卧式圆筒形。
转炉煤气回收气柜系统的若干安全问题钱红辉(武钢能源总厂 武汉 430083) 【摘 要】 简述了武钢一炼钢厂转炉煤气回收气柜系统的工艺及特点,分析了该系统工艺及设备在安全性方面存在的问题,并对完善安全性措施提出了建议。
【关键词】 转炉煤气回收 安全问题 分析SafetyProblemsofRecoveryGas-HolderSystemofConverterGasQianHonghui(EnergySourcesGeneralPlant,WuhanIron&SteelCo.,Wuhan 430083)【Abstract】 Abriefintroductionwasmadeonprocessandcharacteristicsofrecoverygas2holdersystemforconvertergasofNo.1SteelMillofWuhanIron&SteelCompany.Problemsinsafetyoftheprocessandequipmentofthesystemwereanalyzedandmeasuresofimprovingthesafetywereproposed.【Keywords】 recoveryofconvertergas,safetyproblem,analysis1 前言 1999年5月18日,武钢一炼钢“平改转”工程转炉煤气回收气柜系统正式建成投产,标志着武钢转炉煤气将实现全部回收利用。
该系统投资少、建设工期短、工艺水平较高,达到国内同类技术先进水平,但经过近两个月的生产调试,发现还存在一些问题,为了确保安全,实现连续稳定达产,现就这些问题作一些探讨,并提出改善的措施。
2 工艺简介2.1 工艺流程该系统由一炼钢引风机房后三通切换阀出口总管来的转炉煤气经á1820×8管道送至50000m3威金斯气柜,由柜后电除尘净化及鼓风机加压后,再经煤气混合站调好热值并入二混系统。
2.2 主要技术特点
(1)在柜前设置有O2分析仪表,当O2含量≥2%时,由PLC联锁控制关柜前2#蝶阀,阻止危险性气体进柜,并同时打开1#蝶阀放散。
(2)气柜采用威金斯干式煤气柜,综合性能明显优于其他类型煤气柜。
(3)加压机前设置有SDB22-1型湿法卧式电除尘,为国内首批设计制造投产的湿法卧式电除尘,并考虑有泄爆阀和氧高报警联锁。
(4)加压机选用单吸悬臂式离心机,叶轮带有喷水装置,防止积灰,轴封设置有油脂密封、N2密封、轴封抽吸装置三道防线以防止煤气泄漏。
(5)设置了引射式双蝶阀混合站,由热值仪控制掺入焦炉煤气的比例,混合压力与热值能够自动控制。
(6)采用可编程控制器和显示监控设备,对煤气加压机、电除尘、气柜及各管道阀门进行联锁控制并适时显示各电控设备的工作状态及故障情况。
(7)设置有固定式CO检测报警装置,能在气柜、电除尘、加压站及周边有煤气泄漏时,及时发现而采取措施保证安全。
3 有关问题的讨论3.1 系统进空气发生爆炸的危险性分析转炉煤气回收生产中,极有可能发生回收系统进空气的异常情况,本系统在2000年7月1日的试回收过程中,就出现了一次误进空气的操作,致使柜前混合气体氧含量高达14%,其原因是炼钢烟气回收系统在大水封逆止水层仅100mm的情况下,试验三通联锁蝶阀,而风机高速运行,这时,气柜系统正处“同意回收”的状态;依据二、三炼钢回收系统的操作经验,也曾多次发生过此类情况。
煤气系统进了空气,往往会形成爆炸性的混合气体。
且系统存在可能的点火源:
较长时间运行后,系统存积有含S、P元素的转炉灰,有氧的情况下,·22·冶金动力METALLURGICALPOWER 2001年第2期 总第84期 会产生自燃。
在二炼钢煤气系统检修时,清扫出裸露在大气中的转炉灰经常自燃冒烟,并伴有较浓的硫磺燃烧气味,可以证实自燃的可能。
对这个问题设计中已采取了措施,但对能否可靠阻挡含氧的混合气体进柜显然是考虑不周的。
3.1.1 转炉煤气中危险氧含量的确定煤气与空气混合后其氧含量在多大范围内是安全的,可以由可燃气体在空气中爆炸极限的计算方法进行估算。
我们取近期一炼钢回收的较典型的转炉煤气(忽略微量的H2)进行分析。
按Lechatelier公式,下文式
(1),转炉煤气可以视为混入惰性气体的两种可燃气体混合物,其爆炸极限由图1可得。
Lm=100V1L1+V2L2+?
?
VnLn
(1)式中:
Lm——混合气体的爆炸极限 % L1、L2、Ln——混合气中各组分爆炸极限 % V1、V2、Vn——各组分在混合气中的浓度 %图1 氢、一氧化碳、甲烷和氮、二氧化碳混合气的爆炸极限计算过程如下。
(1)有关参数:
a.煤气组分:
CO211.6%,O20.8%,CO61.6%,N226%b.CO在空气中的爆炸极限(体积分量):
爆炸下限12.5%,爆炸上限75%
(2)计算数据:
a.气体分类:
①空气:
0.8%O2+3%N2=3.8%②CO+惰性气体:
61.6%CO+23%N2+11.6%CO2=96.2%b.燃料转换:
①11.6%CO2+11.6%CO=23.2%(CO+CO2)②23%N2+50%CO=73%(N2+CO)c.各组分爆炸极限:
①一组,由惰性气体?
可燃气体:
11.6%?
11.6%=1,查图1,确定该组分爆炸极限为:
(30,65)②二组,由惰性气体?
可燃气体:
23%?
50%=0.46,查图1,确定该组分爆炸极限为:
(20,72.5)d.转炉煤气爆炸极限的确定:
将数据代入公式计算:
①爆炸上限:
1上=96.223.2?
65+73?
72.5=70.54②爆炸下限:
1下=96.223.2?
30+73?
20=21.75e.煤气中氧含量的确定:
①爆炸上限时O2含量:
(100%-70.54%)×0.21=6.19%②爆炸下限时O2含量:
(100%-21.75%)×0.21=16.43%即转炉煤气处危险状态的氧含量范围是6.19%~16.43%。
由上述计算结果可以看出,理论上转炉煤气中氧含量达到6.19%以上、16.43%以下时,处于能爆炸的浓度,是危险的混合气体;实际中考虑到温度、压力、容器、其他杂质及点火能源等复杂因素的影响,应该与理论计算有一些偏差,必须要有足够的保险余量。
3.1.2 危险空气量及柜位的估算由上面分析的结果,氧含量大于6.19%时,混合气体中空气的体积分量达29.46%以上,危险是绝对的;氧含量小于2%时,此时煤气中的空气量在2%?
0.21=9.52%以下,肯定是安全的;混合气体中空气的体积在9.52%~29.46%之间时,可以把它指认为是亚危险状态。
下面,就回收系统由于氧分析仪表滞后、管程短及阀门有动作时间等因素,对发生以上分析的误操作导致进入气柜的空气量进行估算。
该系统氧气分析仪取样点距离联锁的2#蝶阀只有约30m;样气流经磁氧分析仪取样管道再加上仪表自身的滞后时间为30~32s,计算取30s,2#蝶阀由全开到全关耗时约53s,考虑到阀门动作过程要使煤气流量减少,其延时时间取30s;气体状态按40℃、2.3kPa;气体流量取一台风机的设计流量。
估算当发生氧高报警时,由于滞后等因素未能阻止进柜的空气量估算如下:
·23· 2001年第2期 总第84期 冶金动力METALLURGICALPOWER
(1)基础数据:
a.气体流量:
6×104m3?
hb.管内径:
1.804mc.阀门动作滞后计算时间:
30sd.氧分析表滞后计算时间:
30se.O2取样点到2#阀距离:
30mf.气体温度:
40℃g.气体压力:
2340Pa
(2)计算过程:
a.管道截面积:
S=3.1415×(1.804?
2)=2.56m2b.工况时气体流量:
Q=〔101330?
(101330+2340)〕×〔(273+40)?
273〕×6×10000=67238m3?
hc.气体流速:
V=67238?
(2.56×3600)=7.296m?
sd.60s通过管径:
L=7.296×60=437.75me.进柜气量:
Q=(437.75-30)×2.56=1043.8m3由此可以看出,误操作可能导致1043.8m3空气进入气柜,假设混合均匀,则达到的危险程度与当时柜内的煤气容量有关,可以确定(取前面计算数据):
安全煤气容量:
Va=1043.8×(100-9.52)9.52-3.8=16511m3危险柜位范围:
Vs=1043.8×(100-29.46)29.46-3.8=2869.4m3Vx=1043.8×(100-78.25)78.25-3.8=304.9m3即柜位保持16511m3以上,是安全的;柜位在2869.4~16511m3处亚危险状态;柜位保持在304.9~2869.4m3是非常危险的;而柜位在304.9m3以下又较安全。
3.2 柜前管道存在负压情况的分析生产操作中,对柜前管可能会出现负压感到不安,负压存在的危险是系统会吸入空气,按两种情况分析:
一种情况是发生氧高报警、PLC联锁动作时,柜前管处2#阀关、1#阀开的状况,此时,三通阀由于联锁处于放散状态,与柜前管隔断,则可能在管内形成一定的负压值,其负压值由公式
(2)确定。
P=h×(r空气-r煤气)
(2)式中:
r空气——放散管周围大气的平均重度 r煤气——煤气的平均重度 h——放散管的高度,取40m取:
煤气温度t煤气=60℃,大气温度t空气=30℃。
转炉煤气的成分为:
11.6%CO2,0.8%O2,61.6%CO,26%N2则比重r0煤气=11.6%×1.976+0.8%×1.429+61.6%×1.25+26%×2.151=1.336kg?
m3空气的比重r0空气=1.293有负压值P=40×(273273+30×1.293-273273+60×1.336) =27.44Pa的确,放散压力平衡的瞬间,可能会出现微负压的状况,如果迅速组织处理,危险性不大。
第二种情况是系统较长时间停止运行时,一炼钢大水封处高水位,气柜入口水封或水封逆止阀关,由于管道及1#蝶阀可能存在泄漏,管内压力即可降至为零,在昼夜温差的作用下,管内压力处正负交替变化,空气则可能慢慢进入管道内部,逐渐积累成为危险性气体,这种情况要引起注意。
3.3 电除尘安全运行问题电除尘在运行时,必然会出现可以引起混合燃气爆炸的火源,防
高炉煤气综合利用技术的探讨
摘要 阐述了有效利用高炉煤气的重要性。
对目前钢铁行业普遍采用的锅炉-蒸汽轮机、燃气—蒸汽联合循环两种发电利用技术进行热效率比较,分析了在节能、环保、经济效益方面燃气—蒸汽联合循环发电技术的优势及发展前景。
关键词 高炉煤气 锅炉-蒸汽轮机发电 燃气—蒸汽联合循环发电
1引言
大力发展循环经济是实现钢铁工业可持续发展的必由之路。
它的实质就是以尽可能少的资源消耗、尽可能小的环境代价实现最大的经济和社会效益。
目前,我国的钢铁工业仍然是依靠资源的高消耗来推动增长的,因此必须以循环经济的发展理念为指导原则,充分挖掘能源等方面的潜力,提高资源的利用效率,最大限度的减少污染物的排放。
钢铁企业的节能降耗,高炉煤气能量综合利用是提高效益的突破口。
由于高炉煤气的热值较低,一般在3125~3542kJ/Nm3左右,为低热值气体燃料,属于二次能源。
因此如何高效的利用低热值的高炉煤气一直是钢铁企业所广泛关注的问题。
2高炉煤气综合利用技术
高炉煤气除满足炼铁工艺自身需求外,尚有大量的富余,如不能回收利用则只能放空排放,造成能源浪费和环境污染。
为了充分利用这部分富余的高炉煤气,目前国内钢铁企业主要采用以下两种发电技术:
(1)锅炉-蒸汽轮机发电
把高炉煤气作为锅炉的燃料,产生高中压过热蒸汽(通常参数为3.82~16.7MPa,450~550℃)在汽轮机中作功转换为机械能,从而驱动汽轮机发电,其抽汽或背压用于供热和制冷。
(2)燃气—蒸汽联合循环发电
由燃气轮机发电系统和锅炉蒸汽轮机发电系统所组成,采用全烧高炉煤气的燃气轮机。
高炉煤气经除尘加压后进入燃气轮机燃烧器燃烧,而后进入燃气轮机启动涡轮机做功从而带动发电机发电,做完功后的烟气(温度~540℃,压力~5000~6000Pa)进入余热锅炉生产中压或次高压蒸汽(通常参数为3.82~5.9MPa,450~550℃),并使蒸汽在汽轮机中继续作功发电,其抽汽或背压排汽用于供热和制冷。
——图2中各点所对应的焓值,kJ/kg。
(2)布雷顿循环[1]
燃气轮机装置的基本循环为布雷顿循环,其工作原理图和温熵图如下:
图4工作原理图 图5 T—S图
工质的吸热量为:
(5)
放热量为:
(6)
其循环热效率为:
(7)
——图4中各点所对应的焓值,kJ/kg。
3.2热效率比较
(1) 锅炉-蒸汽轮机发电机组是利用汽轮机组的朗肯循环来完成作功发电的。
煤气燃烧产生的高温高压烟气只用于锅炉燃烧,产生蒸汽,然后利用蒸汽朗肯循环作功发电。
因此,若不考虑热量损失情况,则锅炉-蒸汽轮机发电机组的热效率即为朗肯循环的热效率。
(2)燃气—蒸汽联合循环发电机组是由燃气轮机组的布雷顿循环以及汽轮机的朗肯循环所组成。
在煤气的布雷顿热力循环中,煤气燃烧产生的高温压力烟气在状态变化时作功发电。
而煤气布雷顿循环排出的较高温度烟气作为余热锅炉热源能量,产生蒸汽驱动汽轮机发电,组成朗肯循环。
这样,煤气的热能既参与了燃气轮机的布雷顿循环又参与了蒸汽轮机和锅炉组成的朗肯循环,既利用了烟气的作功能力发电,又利用了蒸汽的作功能力发电。
因此,若不考虑能量损失情况,粗估整套燃气—蒸汽联合循环发电机组的热效率为:
通过以上分析结果,从(8)、(9)两式可以得知,燃气—蒸汽联合循环发电机组要远大于锅炉-蒸汽轮机发电机组的热效率,整个能源利用水平也有了明显提高。
一般来说,以高炉煤气作为锅炉燃料产生蒸汽来驱动汽轮机发电的蒸汽轮机发电机组热效率仅能达到25%左右,而燃气—蒸汽联合循环发电机组在不外供热的情况下热效率可高达40%~45%。
并且,随着航太技术的融入和冷却技术的研发改善,促使燃气轮机的发展一日千里,近600℃以上的高温排气以及气机进气温度的不断提高,将进一步提高燃气—蒸汽联合循环发电机组的热效率。
4燃气—蒸汽联合循环发电在钢铁行业的应用
在钢铁行业,第一台燃用高炉煤气的煤气—蒸汽联合循环发电机组于1956年投产,安装在卢森堡布尔巴赫—埃希联合公司钢铁厂内,其主要用于发电。
至今,世界发达国家主要钢铁厂均装有燃用高炉煤气的燃气—蒸汽联合循环发电机组。
上海宝山钢铁股份有限公司于1997年投产的两台145MW机组是钢铁行业目前最大的煤气—蒸汽联合循环发电机组。
该机组100%全烧高炉煤气,煤气热值为3276kJ/m3,按宝股目前运行的情况,每台机组小时耗高炉煤气33~36万立方米,机组输出功率145MW,并可供应蒸汽180t/h,热效率达46.52%,投产后年发电量11亿kW.h。
除宝股外,国内钢铁企业已经投入运行的燃气—蒸汽联合循环发电机组还有济钢的65MW和通钢的56MW机组,均取得了不错的环保和经济效益。
同时,太钢、沙钢等很多钢铁企业也正在建设或有意应用此项技术。
5燃气—蒸汽联合循环发电机组工艺特点及技术要求
燃气—蒸汽联合循环发电机组将不易稳定燃烧、通常被排放的低热值高炉煤气加以回收利用,合理、高效、无污染地利用钢铁厂剩余的低热值高炉煤气发电和供热,达到节能和环保的双重效果。
并且,由于燃气—蒸汽联合循环发电先进的技术和设备以及优化系统,使其热效率及发电效率远高于常规锅炉—蒸汽轮机发电,并且具有运行灵活、适于各种不同运转模式的优良性能。
也应当看到,燃气—蒸汽联合循环发电的建设与运行要求较高的技术水平。
首先,其建设前提必须具有充足、稳定的燃料供应,且对燃料的热值、压力等指标有较严格的要求。
同时,与常规燃气轮机相比,燃气—蒸汽联合循环发电系统增加了压缩机、除尘器等设备,因而其调节系统比较复杂,调节的参数多,调节的精度要求高,维修费用也远高于常规发电系统。
6结论
(1)钢铁企业在炼铁过程中,要产生大量的副产品——高炉煤气。
如何高效利用低热值高炉煤气,实现合理利用资源,减少环境污染是钢铁行业所普遍关注的问题。
(2)提高高炉煤气的回收率,增加低附加值高炉煤气向高附加值能源形式电能的转换,有着重要的意义。
目前,国内钢铁企业主要采用常规锅炉—蒸汽轮机发电以及燃气—蒸汽联合循环发电两种技术。
与常规的锅炉—蒸汽轮机发电相比,燃气—蒸汽联合循环发电具有高效率、提高能源利用率及环保等方面的优越性。
(3)国家新出台的钢铁行业产业技术政策中也明确鼓励企业应根据自身发展循环经济的要求,采用燃气—蒸汽联合循环发电等能源、资源回收再利用技术。
总之,燃气—蒸汽联合循环发电技术较常规锅炉—蒸汽轮机发电技术在高效、节能、环保方面均具有较大的优势,而且从发展的眼光看,其具有广阔的发展前景。
随着相关技术的日趋成熟,在高炉煤气的综合利用方面,这项技术将得到更充分的发展。
高炉煤气洗涤废水的处理技术
高炉炼铁过程产生的大量炉气中含有一定量的一氧化碳气体(CO>20%),故称高炉煤气。
高炉煤气中含有大量的可燃性成分并夹杂有大量的灰尘,温度通常为150~400℃。
从炉顶排出的废气一般先经重力除尘器后,再进行洗涤处理和深度除尘。
洗涤处理是通过在洗涤塔或文氏管中的气、水对流接触实现煤气的洗涤和冷却。
洗涤冷却后的水就是高炉煤气洗涤废水。
这种废水水温高达60℃以上,主要杂质是固体悬浮物、尘泥(瓦斯泥)、氧化物、焦炭粉等。
除此之外,还含有一部分无机盐及酚、氰、重金属等有毒物质,由于该废水水量大、污染重,必须进行处理,并尽可能循环使用[1]。
1治理现状
目前大、中型高炉煤气洗涤废水的沉淀处理可分为自然沉淀和混凝沉淀。
1.1自然沉淀法
首都钢铁公司、攀枝花钢铁公司、湘潭钢铁公司、上海第一钢铁厂等的高炉煤气洗涤废水均采用自然沉淀为主的处理方法。
莱芜钢铁厂高炉煤气洗涤废水过去靠两个D=12m的浓缩池处理,未达到工业用水及排放标准,后来改用平流式沉淀池进行自然沉淀,沉淀效率达90%左右,出水悬浮物含量小于100mg/L,冷却以后水温约40℃,水的循环率达90%,除个别指标(如Pb、酚)有时超标外,处理后的废水基本可达标排放。
国外高炉煤气洗涤废水的处理大多数采用自然沉淀方法[2],特点是废水靠重力排入沉淀池或浓缩池,处理后经冷却塔冷却后循环使用,出水悬浮物SS<85mg/L,循环率达96%。
整个系统设计成闭路循环,运行期间没有排污。
自然沉淀法的优点是节省药剂费用,节约能源;缺点是水力停留时间长,占地面积大,对用地紧张的企业不宜采用;另外,当瓦斯泥颗粒过细时,自然沉淀后的水中悬浮物含量偏高,输水管道、水泵吸水井积泥较多