井巷工程课程设计资料收集.docx
《井巷工程课程设计资料收集.docx》由会员分享,可在线阅读,更多相关《井巷工程课程设计资料收集.docx(50页珍藏版)》请在冰豆网上搜索。
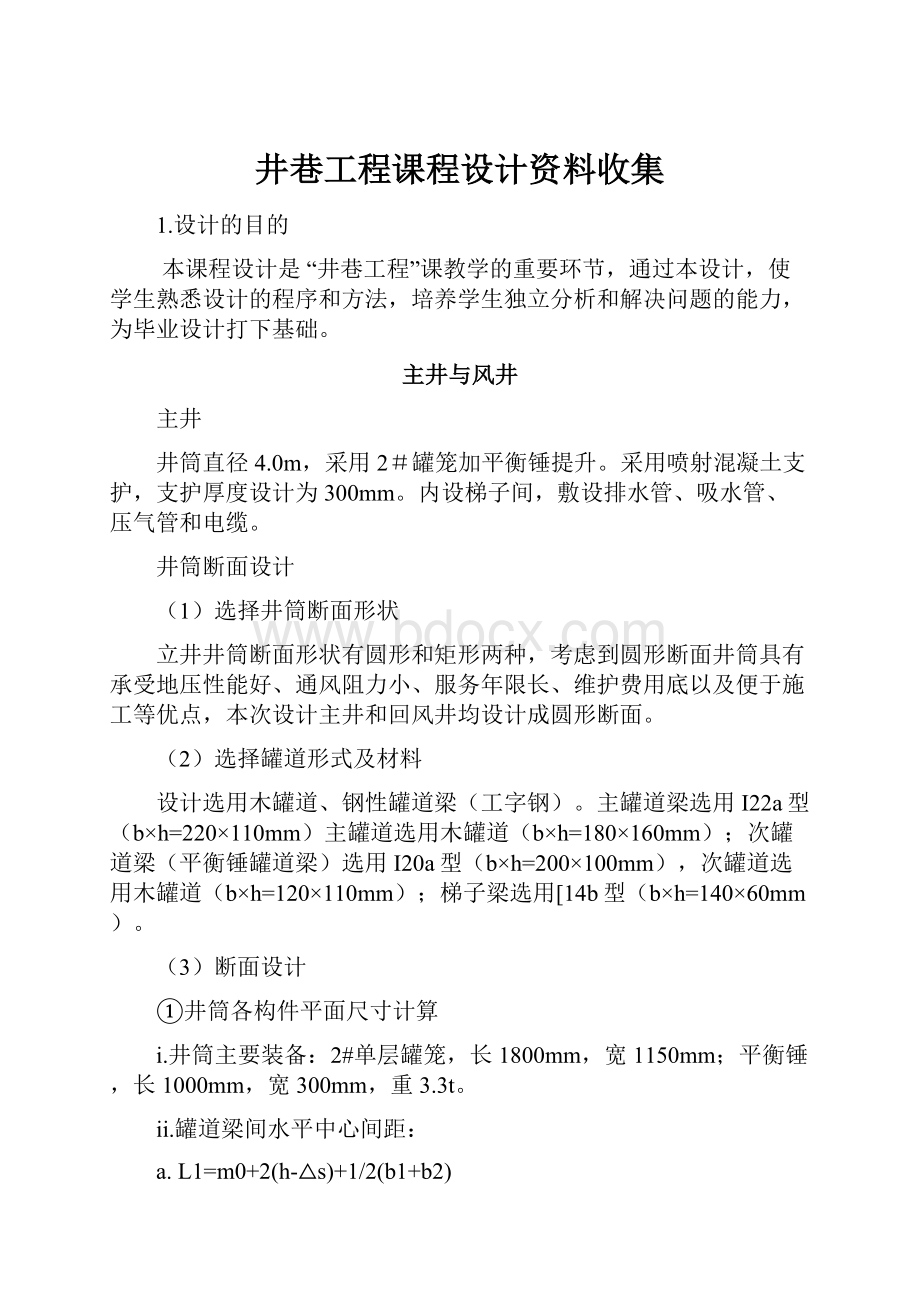
井巷工程课程设计资料收集
1.设计的目的
本课程设计是“井巷工程”课教学的重要环节,通过本设计,使学生熟悉设计的程序和方法,培养学生独立分析和解决问题的能力,为毕业设计打下基础。
主井与风井
主井
井筒直径4.0m,采用2#罐笼加平衡锤提升。
采用喷射混凝土支护,支护厚度设计为300mm。
内设梯子间,敷设排水管、吸水管、压气管和电缆。
井筒断面设计
(1)选择井筒断面形状
立井井筒断面形状有圆形和矩形两种,考虑到圆形断面井筒具有承受地压性能好、通风阻力小、服务年限长、维护费用底以及便于施工等优点,本次设计主井和回风井均设计成圆形断面。
(2)选择罐道形式及材料
设计选用木罐道、钢性罐道梁(工字钢)。
主罐道梁选用I22a型(b×h=220×110mm)主罐道选用木罐道(b×h=180×160mm);次罐道梁(平衡锤罐道梁)选用I20a型(b×h=200×100mm),次罐道选用木罐道(b×h=120×110mm);梯子梁选用[14b型(b×h=140×60mm)。
(3)断面设计
①井筒各构件平面尺寸计算
i.井筒主要装备:
2#单层罐笼,长1800mm,宽1150mm;平衡锤,长1000mm,宽300mm,重3.3t。
ii.罐道梁间水平中心间距:
a.L1=m0+2(h-△s)+1/2(b1+b2)
式中、L1—两相邻主罐道梁水平中心距离,mm;
M0—提升容器要求的罐道之间的水平净间距,由罐笼型号确定,mm;
h—罐道高度,mm;
△s—连接处木罐道卡入钢罐梁的深度,取10mm;
b1、b2—罐道梁的宽度,mm。
故
L1=m0+2(h-△s)+1/2(b1+b2)=1190+2×(160-10)+0.5×(110+110)
=1600mm
b.L2=m0+2(h-△s)+1/2(b1+b3)
式中、L2—两相邻平衡锤罐道梁水平中心距离,mm;
M0—提升容器要求的罐道之间的水平净间距,由平衡锤型号确定,mm;
h—罐道高度,mm;
△s—连接处木罐道卡入钢罐梁的深度,取10mm;
b1、b3—次罐道梁的宽度,mm。
故
L2=m0+2(h-△s)+1/2(b1+b2)=1040+2×(110-10)+0.5×(100+100)
=1340mm
c.梯子间尺寸计算
M=1200+m+b3/2
S=H-d
式中、M—梯子间短边梁中心线与井壁的交点至梯子主梁中心线间距,mm;
m—梯子间安全隔栏的厚度,取100mm;
b3—梯子主梁或罐道梁的宽度,mm;
H—梯子间的两外边次梁中心线间距,即梯子间长度,取1400mm;
S—梯子间短边次梁中心线至井筒中心线的距离,mm;
d—梯子间另一侧短边次梁中心线至井筒中心线的距离,考虑方便安装,应不小于300mm。
M=1200+m+b3/2=1200+100+110/2=1355mm;
S=H-d=1400-400=1000mm。
②利用图解法确定井筒直径
经绘图量取井筒直径近似为3865mm,按500mm模数进级,确定主井井筒断面直径为4.0m。
③支护厚度选用
参照《井巷工程》表10-4,选取井筒支护厚度为300mm。
故井筒的掘进直径为4.6m。
④管缆布置
按照管缆布置的原则,结合该井条件,管缆布置见井筒断面图。
⑤工程量及材料消耗
井筒净断面积:
S净=πD净2/4=π×4.02/4=12.56m2;
井筒掘进断面积:
S掘=πD掘2/4=π×4.62/4=16.6m2;
每米井筒混凝土量:
V壁=(S掘-S净)×1=(16.6-12.56)×1=4.04m3;
⑥罐道梁、梯子梁长度
罐道梁长度按下式计算:
式中、R—井筒净直径;C—每根罐道梁至井筒中心线的距离。
故
图5-1主井井筒断面图
在保证罐道梁埋入井壁的长度须合乎要求的前提下,取长度10的整数倍,则各罐道梁长度分别为:
L1=3860mm;
L2=3400mm;
L3=3780mm。
梯子梁长度:
Lt1=1063mm;Lt2=1374mm;Lt3=1366mm。
根据实际情况,取值如下:
Lt1=1070mm;Lt2=1380mm;Lt3=1380mm。
风井
设计回风井井筒断面净直径2.5m,采用喷射混凝土支护,支护厚度设计为200mm。
内设梯子间,兼作第二安全出口。
详见图5-2回风井井筒断面图。
回风井井筒断面图
矿井通风方式的选择
矿井通风系统主要包括通风方式(即进风井和回风井的布置方式)、通风方法(即矿井通风机的工作方法)以及由若干通风巷道和交汇点构成的通风网络。
矿井通风方式
中央并列式
进风井和回风井大致并列于井田中央,由主井兼作回风井或专设中央风井。
这种方式具有初期工程量少,建井期短,便于管理等优点。
其主要缺点是进回风井之间漏风大,矿井的中后期通风线路长,通风阻力大,工业场地噪音大。
这种通风方式适合于矿层倾角大,走向长度小于4公里的低瓦斯矿井。
中央分列式
进风井位于井田中央,回风井位于井田上部边界中央。
这种方式具有通风阻力小、漏风小、安全性能好、工业场地噪音小等优点,且便于从回风井敷设防尘洒水管路,适合于矿层倾角较小、埋藏较浅、瓦斯和矿层自燃发火比较严重的矿井,走向长度较大的中型矿井,投产初期多用这种方式。
两翼对角式
进风井位于井田中央,回风井井田两翼各一个,分别为井田一翼服务。
适用于高瓦斯矿井、自燃发火和热害比较严重或有矿和瓦斯突出的矿井。
分区对角式
进风井位于井田中央,两翼各有两个或两个以上回风井为所在的附近采区服务。
它适用于矿层距离地表较浅且高低起伏大、第一水平无法开凿总回风道的情况,也适用于矿和瓦斯突出危险的矿井或高瓦斯矿井。
此外,各分区有独立的进回风系统,具有建井期短、安全性能好、便于管理等优点,但因风井多、占地大、风机管理分散等原因,多适用于分区分散开拓、分期投产的特大型矿井。
混合式
主要是指以上几种方式的组合。
这种通风方式适用于井田走向长度大或矿井改扩建和开拓延伸矿井,或多矿层多井筒,或井田面积较大,产量大且分散开拓的矿井。
经分析以上几种风井布置方式,根据本井田矿层赋存状况,结合矿井开拓布置情况,采用中央边界式。
2)矿井通风方式的选择
根据本矿井矿层瓦斯含量高,矿层埋藏较深和赋存状态复杂,冲积层厚,矿与瓦斯具有突出危险,矿层自然发火性等综合考虑后结合压入式、抽出式和抽压混合式三种通风方式的适用条件和优缺点分析后确定本矿井采用的通风方式为:
抽出式。
各种通风方式的适用条件和优缺点分析见下表3-1:
表3-1通风方式分类表
通风方式
适用条件和优缺点
抽出式
是当前通风方式中的主要形式,适应性较广泛,尤其对高瓦斯矿井,更有利于对瓦斯的管理,也适用于矿井走向长,开采面积大的矿井
优点:
①井下风流处于负压状态,当主扇因故障停止运行时,井下的风流压力提高可能使采空区瓦斯涌出量减少,比较安全;②漏风量小,通风管理较简单;③与压入式比,不存在过度到下水平时期通风系统和风量变化的困难
缺点:
当地面有小窑塌陷区并和采区沟通时,抽出式会把小窑积存的有害气体抽到井下使矿井有效风量减小。
压入式
低瓦斯矿井的第一水平,矿井地面地形复杂、高差起伏,无法在高山上设置通风机。
总回风巷无法连通或维护困难的条件下
优缺点:
①压出式的优缺点与抽出式相反;②进风路线漏风大,管理困难;③风阻大、风量调节困难;④由第一水平的压入式过渡到深部水平的抽出式有一定的困难;⑤通风机时井下风流处于正压状态,当通风机停止运转时,风流压力降低,有可能使采空区瓦斯涌出量增加。
抽压联合式一、二水平过渡
可产生较大的通风压力,能适应大阻力矿井需要,但通风管理困难,一般新建矿井和高瓦斯矿井不宜采用,只是个别用于老井延深或改建的低瓦斯矿井。
采区通风系统选择
1)采区通风系统选择的依据
本设计在选择采区通风系统时遵守《矿矿安全规程》的以下相关规定:
(1)每一个生产水平和每一个采区,都必须布置回风道,实行分区通风;
(2)回采工作面和掘进工作面都应采用独立通风;
(3)矿层倾角大于12°的回采工作面都应采用上行通风。
如果采用下行通风时,必须报矿总工程师批准,并遵守下列规定:
①回采工作面风速不得低于1m/s;
②机电设备设在回风道时,回采工作面回风道风流中瓦斯浓度不得超过1%,并应装有瓦斯自动检测报警断电装置;
③应有能够控制逆转风流、防止火灾气体涌入进风流的安全措施。
在有矿(岩)与瓦斯(二氧化碳)突出危险的、倾角大于12°的矿层中,严禁回采工作面采用下行通风。
(4)开采有矿尘爆炸危险矿层的矿井,在矿井的两翼、相邻的采区和相邻的矿层,都必须用水棚隔开;在所有运输巷道和回风巷道中,必须散布岩粉或冲洗巷道。
此外,在确定采区通风系统时还考虑满足以下要求:
在采区通风系统中,保证风流流动的稳定性,尽可能避免对角风路,尽量减少采区漏风量,并有利于采空区瓦斯的合理排放及防止采空区浮矿自然,使新鲜风流在其流动路线上被加热与污染的程度最小。
对于薄及中厚缓倾斜矿层,我国广泛采用走向长壁采矿法。
厚矿层则多采用倾斜分层走向长壁采矿法或放顶矿开采,开掘采区上山联系回风大巷及运输大巷。
上山至少要两条,即输送机上山和轨道上山,对生产能力大的采区可以有三条或四条上山。
采区上山通风系统主要有以下三种,如表3-2。
表3-2采区上山通风系统
通风系统
上山数目
适用条件及优缺点
输送机上山进风,轨道上山回风
2
1、运输机上山进风,其风流与运矿路线相同而方向相反,所以风门较少,比较容易控制风流;
2、由于风流方向与运矿方向相反,风流与矿的相对速度增加,造成大量的矿尘飞扬;同时,矿在运输过程中不断涌出瓦斯,使风流中矿尘与瓦斯浓度增加;
3、输送机上山电气设备散热,使进风流温度升高;4、轨道上山下部车场需要安设风门,不易管理。
轨道上山进风,输送机上山回风
2
1、轨道上山的下部车场可不设风门、车辆通过方便;2、上山绞车房便于得到新鲜风流;
3、进风风流不受上山运矿和瓦斯污染,含矿尘较小;
4、当采用矿层双巷布置时,作为回风、运料用的各区段中部车场、上山上部车场内均需设置风门,不易管理,漏风大。
输送机上山、轨道上山进风,回风上山回风
3
采区生产能力大,所需风量多,瓦斯涌出量大,上下阶段同时生产等,是目前大、中型矿井普遍采用的采区通风系统。
避免了上述两种系统的缺点,同时具备两者的优点,但需增加一条上山,工程量较大。
本矿井设计为大型矿井,根据以上规定及要求,通过分析对比确定本矿井采用轨道上山进风、回风上山和输送机上山回风相组合的三上山采区通风系统。
2)采工作面通风系统的选择
回采工作面和掘进工作面都有独立的通风;并尽量保证回采工作面的调节设施可靠、风流稳定,还要尽量减小回采工作面的内部和外部漏风,特别注意避免从外部向回采工作面的漏风。
由于本矿井的矿(岩)与瓦斯(二氧化碳)具有突出危险,矿层还具有自然发火性,且矿层倾角平均大于10°,按照规程只能采用上行通风。
目前,国内采矿工作面通风方式有“U”型、“Y”型、“W”型、“E”型、“Z”型等,其中“U”型应用最为广泛。
各类回采工作面通风系统适用条件和优缺点
表3-3回采工作面通风系统分类
通风系统分类
适用条件和优缺点
“U”型通风系统
优点:
工作面采用后退式回采。
上、下顺槽在矿体中维护容易。
有利于了解矿层赋存状况,有利于掌握瓦斯与矿层自然的发生及发展规律,特别是对采空区实行均压防灭火、控制瓦斯比较方便,更有利于抑制采空区浮矿的自然。
这种通风方式也不需要维护采空区的巷道
缺点:
工作面上偶角附近容易积存瓦斯,特别是瓦斯涌出量增大时,常造成回风巷道瓦斯超限。
“Y”型通风系统
优点:
工作面采用后退式回采。
上、下顺槽同时进风,改善了回风巷的气象条件,
缺点:
回风巷维护在采空区内,维护困难且工作面漏风大,易引起采空区自然发火。
“Z”型通风系统
优点:
工作面采用前进式后沿倾斜方向回采。
回风巷在前方矿体维护,须预先挖掘,上、下顺槽同时进风,在相同风速下,风量可增加一倍,
缺点:
进风巷在采空区内,维护困难,密闭不好,漏风量大。
“W”型通风系统
优点:
工作面后退式回采。
进、回风巷均在矿体中维护,工作面通风量大,有利于工作面降温和排除瓦斯。
本矿井是矿层容易自然矿井,为了减少漏风,有利于防灭火管理工作,本设计采用工作面“U”型通风系统,偶角附近容易积存瓦斯问题主要通过瓦斯抽放来解决。
3.1.5风流路线
1)风流路线
(1)新鲜风路线:
副井→轨道大巷→采区下部车场→轨道上山→下顺槽→工作面
(2)乏风路线:
工作面→上顺槽→回风上山→回风大巷→风井
3.2矿井风量计算及风量分配
3.2.1矿井总风量的计算
1)风量计算原则
设计根据《矿矿安全规程》有关规定,以本矿井的瓦斯资料为基础,按采矿、掘进硐室及其它特点实际需要风量的总和计算矿井总风量。
2)风量计算依据
矿井设计能力为2.40Mt/a,矿井风量设计以矿井开拓部署与配采安排,以及预测的瓦斯涌出量为依据,同时考虑回采与掘进工作面具有良好的气象环境。
3)矿井风量计算
矿井采用边界式通风系统,按下列要求计算,并且必须取其中最大值。
根据《矿矿安全规程》第110条规定,矿井总风量按下列要求分别计算,并取其中最大值。
(1)按井下同时工作最多人数计算,每人每分钟供给风量不得少于4m3;
Q=4×N×K(3-1)
式中Q---矿井总进风量,m3/min;
N---矿井井下同时工作的最多人数;(取750人);
K---矿井通风系数,包括矿井内部漏风和配风不均匀等因素,采用边界式通风时,可取1.10—1.15,上述备用系数在矿井产量T≥90×10
t/a时取最小值,本矿井设计容易时期取1.1(困难时期取1.15)。
(2)按采矿工作面、掘进工作面、硐室及其他地点实际需要风量的总和计算:
Q=(ΣQ采+ΣQ掘+ΣQ硐+ΣQ其)×K(3-2)
式中ΣQ采---采矿工作面实际需要风量的总和,m3/min;
ΣQ掘---掘进工作面实际需要风量的总和,m3/min;
ΣQ硐---硐室实际需要风量的总和,m3/min;
ΣQ其—矿井其他井巷需要进行通风风量的总和,m3/min;
K----矿井通风系数,边界式取1.1。
3.2.2矿井容易时期需风量计算及风量分配
1)容易时期需风量计算
采矿工作面实际需要风量
每个采矿工作面实际需要的风量,应按瓦斯、二氧化碳涌出量和爆破后的有害气体产生量以及工作面气温、风速和人数等规定要求分别进行计算,必须取其中最大值。
(1) 工作面需风量计算
按瓦斯涌出量计算
Q采i=100×QCH4·采i×Ki(3-4)
式中Q采i---第I个采矿工作面需要的风量,m3/min;
QCH4采i---第I个采矿工作面的瓦斯绝对涌出量,QCH4采i=10m3/min;
Ki---第i个采矿工作面因瓦斯涌出不均匀的备用风量系数,它是该工作面瓦斯绝对涌出量的最大值与最小值之比。
生产矿井可根据各个工作面正常生产条件时,至少进行5昼夜的观测,得出5个比值,取其最大值。
通常机采工作面取1.2~1.6;炮采工作面取1.4~2.0;水采工作面取2.0~3.0。
K=1.6。
Q采i=100×10×1.6=1600m3/min
按工作面进风流温度计算
采矿工作面应有良好的劳动气候条件,其温度和风速应符合表3-1的要求:
表3-4工作面空气温度与风速对应表
工作面空气温度(℃)
工作面风速(m/s)
<15
0.3~0.5
15~18
0.5~0.8
18~20
0.8~1.0
20~23
1.0~1.5
23~26
1.5~1.8
A长壁工作面实际需要风量,按下式计算:
Q采i=60×V采i×S采i×Ki(3-5)
式中V采i---第i个采矿工作面的风速,按其进风流温度从表3-1中选取,m/s;
本设计取V采i=1.0;
S采i---第i个采矿工作面的有效通风断面,取最大和最小控顶时有效断面的平均值,工作面的断面积取9m2;
Ki------第i个采矿工作面的长度系数,本设计取1.4。
则Q采=60×1.0×9×1.4=756m3/min
③按工作人员数计算:
Q采i=4×Ni(3-6)
式中4---每人每分钟应供给的最低风量,m3/min;
Ni---第i个采矿工作面同时工作的最多人数,取50人;
Q采=4×50=200
按风速进行计算:
按最低风速验算,每个工作面的最低风量:
Q采i≥0.25×60×S采i(3-7)
式中S采i---工作面平均断面积,取13m2
Q采≥0.25×60×9=135m3/min;
按最高风速验算,每个工作面的最高风量:
Q采i≤4×60×S采i
Q采≤2160m3/min
所以采矿工作面的风量应在195-2160m3/min之间,
因此工作面的实际需风量为:
Q采=1600m3/min
(2)掘进工作面实际需要风量
①按瓦斯涌出量计算:
Q掘进=100×QCH4掘进×ki(3-8)
QCH4掘进---该掘进面瓦斯绝对涌出量,QCH4矿巷掘进=2m3/min
Ki---掘进面瓦斯涌出不均匀和备用风量系数,一般可取1.5~2.0本设计矿巷掘进时取K=1.8。
Q矿巷掘进=100×2×1.8=360m3/min
②按该掘进面最多的工作人数计算:
Q掘回=4×N(3-9)
式中N---掘进面同时工作的人数N=40人
Q掘进=4×40=160m3/min
③按实际吸风量计算:
掘进面配备一台28kW的JBT—62风机,其实际风量为:
Q矿巷掘进=300×1.2=360m
/min
④按风速进行计算:
a按最小风速进行验算:
Q矿巷掘进≧60×0.25×S
S---该掘进面平均断面积,取S矿巷=9m3/min
Q矿巷掘进=60×0.25×9=135m3/min
b按最大风速进行验算:
Q掘进=60×4×S=60×4×9=2160m3/min
经过验算矿巷掘进面的需风量为360m3/min;则ΣQ矿巷掘进=360×4=1440m3/min
ΣQ矿巷掘进=360×4=1440m3/min
(3)硐室需风量
按矿井各个独立通风硐室实际需要风量的总和计算,即:
Q硐=∑Q硐i(i=1,2,…,N)(3-10)
式中Q硐i---第i个独立通风的硐室实际需要的风量,m3/min
每个硐室实际需要风量应根据不同类型的硐室分别进行计算。
a机电硐室
发热量大的机电硐室,按硐室中运行的机电设备发热量进行计算:
Qri=3600×∑N×θ/(ρ×Cp×Δt)(3-11)
式中Qri---第i个机电硐室的需风量,m3/min;
θ---机电硐室的发热系数,可根据实际考察由机电硐室内机械设备运转时的实际热量转换为相当于电器设备容量做无用功的系数确定;
∑N----机电硐室中运转的电动机总功率,kw;
ρ----空气密度,一般取1.2kj/m2;
Cp----空气的定压比热,一般可取1kj/kg·k;
Δt----机电硐室进、回风流的温度差,℃;
采区变电所及变电硐室,可按经验植确定需风量:
Qri=60~80m3/min
b爆破材料库实际需要风量
按每小时4次换气量计算,即:
Qr=4×V/60(3-12)
式中Qr---爆破材料库所需的风量,m3/min;
V---包括联络巷在内的爆破材料库的空间总体积,m3/min;
也可按经验值给风量:
大型爆破材料库大于100m3/min;中小型爆破材料库给60~100m3/min。
c各硐室按经验配风量:
见表3-5
表3-5各硐室按经验配风量
硐室
风量(m3/min)
炸药库
240
采区绞车房
60
采区变电所
60
(4)矿井实际总体需风量:
按采矿、备用面、硐室,其它地点实际需风量的总和计算:
Q前期一=(ΣQ采+ΣQ掘+ΣQ硐)×K漏(3-13)
式中ΣQ采---采矿工作面风量之和,m3/min;
ΣQ硐---各个硐室风量之和,m3/min;
K漏---矿井漏风系数,,取1.15;
Q=5754m3/min
容易时期风量分配表
用风地点
计算风量m3/min
实际风量m3/min
风速m/s
断面面积m2
允许风速m/s
6111工作面
1602
1842
3.41
9
0.25—4
6112工作面
1602
1842
3.41
9
0.25—4
6113风巷掘进面
360
420
0.78
9
0.15—4
6114风巷掘进面
360
420
0.78
9
0.15—4
6113轨道掘进面
360
420
0.78
9
0.15—4
6114轨道掘进面
360
420
0.78
9.
0.15—4
变电所
60
60
绞车房
60
60
爆破材料库
240
240
合计
5004
5754
3.2.3矿井困难时期需风量计算及风量分配
1)困难时期需风量计算
同理根据以上计算计算公式及原则计算可得:
ΣQ采=3740m3/minΣQ掘=1848m3/min
ΣQ硐=400m3/min
Q=5988m3/min
表3-8困难时期风量分配
用风地点
计算风量m3/min
实际风量m3/min
风速m/s
断面面积m2
允许风速m/s
6121工作面
1603
1870
3.47
9
0.25-4
6122工作面
1603
1870
3.47
9
0.15-4
6123掘进头风巷
420
462
0.86
9
0.15-4
6124掘进头风巷
420
462
0.86
9
0.15-4
6123掘进头轨道巷
420
462
0.86
9
0.15-4
6124掘进头轨道巷
420
462
0.86
9
0.15-4
变电所
80
80
绞车房
80
80
爆破材料库
240
240
合计
5206
5988
3.3通风阻力计算及风速校核
3.3.1风速校核
为了保证所设计的井巷、硐室的风量、风速符合《规程》要求(见表3-7),不致发生风速超限,必须进行风速校核。
由各采区通风阻力计算表中数值可知,各个巷道风速均满足要求,说明风量分配合理。
表3-10井巷中风流风速
井巷名称
允许风速(m/s)
最低
最高
无提升设备的风井和风硐
—
15
专为升降物料的井筒
—
12
风桥
—
10
升降人员和物料的井筒
—
8
主要进回风巷
—
8
续表3-10
井巷名称
允许风速(m/s)
最低
最高
架线电机车巷道
1.0
8
运输机巷、采区进回风巷
0.25
6
回采工作面、掘进中的矿巷、半矿岩巷
0.25