焊接技术标准规范.docx
《焊接技术标准规范.docx》由会员分享,可在线阅读,更多相关《焊接技术标准规范.docx(19页珍藏版)》请在冰豆网上搜索。
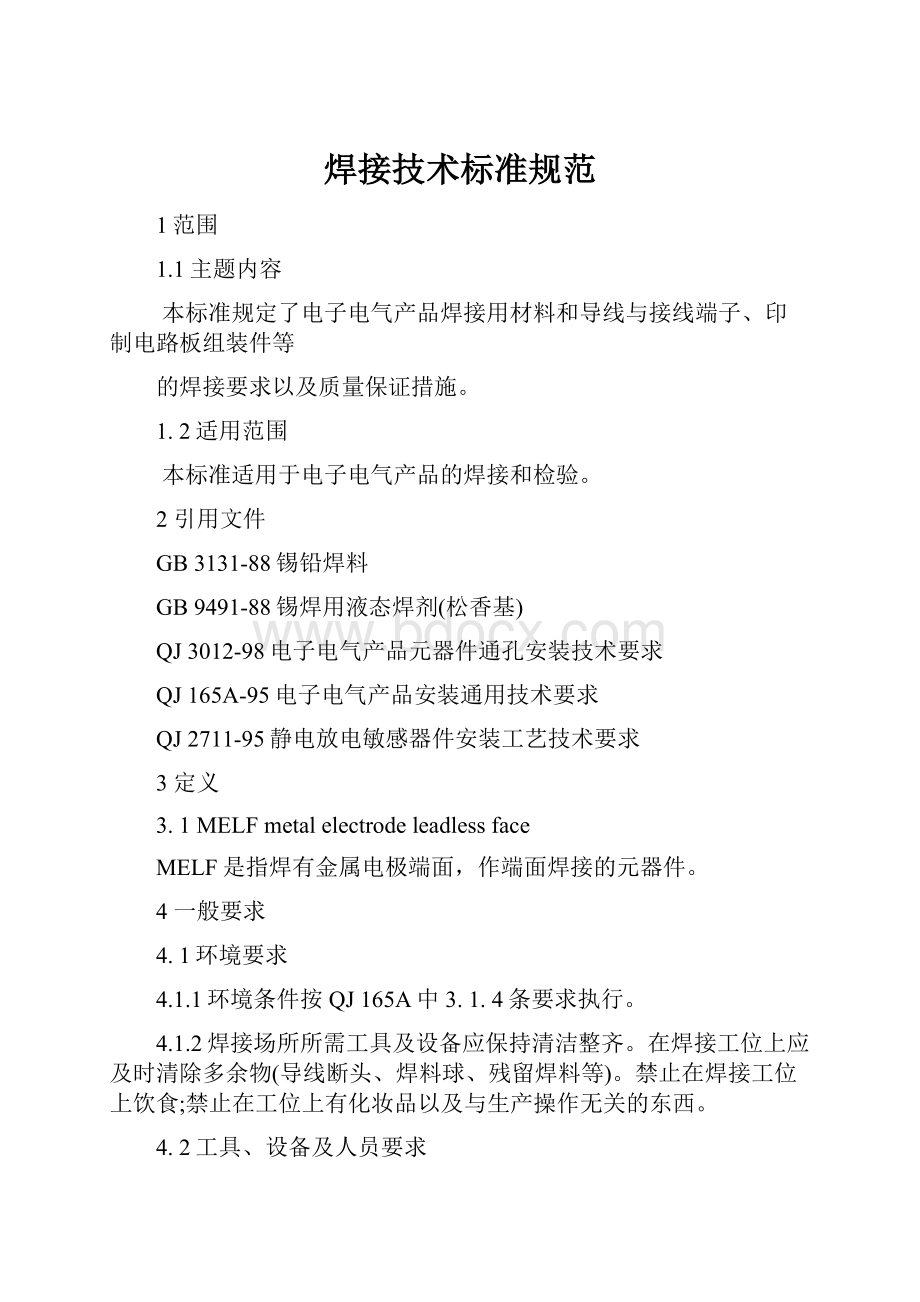
焊接技术标准规范
1范围
1.1主题内容
本标准规定了电子电气产品焊接用材料和导线与接线端子、印制电路板组装件等
的焊接要求以及质量保证措施。
1.2适用范围
本标准适用于电子电气产品的焊接和检验。
2引用文件
GB3131-88锡铅焊料
GB9491-88锡焊用液态焊剂(松香基)
QJ3012-98电子电气产品元器件通孔安装技术要求
QJ165A-95电子电气产品安装通用技术要求
QJ2711-95静电放电敏感器件安装工艺技术要求
3定义
3.1MELFmetalelectrodeleadlessface
MELF是指焊有金属电极端面,作端面焊接的元器件。
4一般要求
4.1环境要求
4.1.1环境条件按QJ165A中3.1.4条要求执行。
4.1.2焊接场所所需工具及设备应保持清洁整齐。
在焊接工位上应及时清除多余物(导线断头、焊料球、残留焊料等)。
禁止在焊接工位上饮食;禁止在工位上有化妆品以及与生产操作无关的东西。
4.2工具、设备及人员要求
4.2.1工具
电烙铁应为温控型的,烙铁头空焊温度应保持在预选温度的士5.5℃之内,烙铁头的形状应符合焊接空间要求,并保证良好的接地。
4.2.2设备
4.2.2.1波峰焊设备
波峰焊设备(包括焊剂装置、预热装置、焊槽)焊接前应能将印制板组装件预热到120℃以内,在整个焊接过程中,焊料槽焊接温度的控制精度应维持在士5.5℃,并具有排气系统。
4.2.2.2再流焊设备
再流焊设备应可将焊接表面迅速加热,并能在连续焊接操作时,迅速加热到预定温度的士6℃范围内。
加热源不应引起印制电路板或元器件的损坏,也不应在加热源与被焊金属直接接触时污染焊料。
再流焊设备包括采用平行等距电阻加热、短路棒电阻加热、热风加热、红外线加热、激光加热装置或非电烙铁热传导焊接的设备。
4.2.3人员
操作人员应经过专业技术培训,熟悉本标准及相关工艺的规定,具有判别焊点合格或不合格的能力,并经考核合格上岗。
4.3焊点
4.3.1外观
4.3.1.1焊点表面应无气孔、非晶态,以及有连续良好的润湿。
焊点不应露出基底金属、不应有锐边、拉尖、焊剂残渣以及夹杂。
与邻近导电通路之间焊料不应出现拉丝、桥接等现象。
4.3.1.2当存在下列情况时焊点外表呈暗灰色是允许的。
a.焊点焊接采用的不是HLSn60Pb焊料;
b.焊接部件为镀金或镀银;
c.焊点冷却速度缓慢(例如:
热容量大的组装件经波峰焊或汽相焊之后),但不应有过热、过冷或受扰动的焊点。
4.3.2裂纹和气泡
焊点的焊料与焊接部位间不应有裂纹、裂缝、裂口或隙缝。
气泡或气孔若与最小允许焊料量同时发生,则为不合格。
4.3.3润湿及焊缝
焊料应润湿全部焊接部位的表面,并围绕焊点四周形成焊缝。
焊料润湿不良或润湿不完全,不应超出焊点四周10%焊料不应收缩成融滴或融球。
4.3.4焊料覆盖面
焊料量应覆盖全部焊接部位,但焊料中导线的轮廓应可辨认。
4.3.5热缩焊焊点
热缩焊装置形成的焊点其焊缝及焊接部件应清晰可见,焊料环应熔融,焊料沿引线流动,外部套管可以变色,但应可见焊区套管外的导线绝缘层,除轻微变色外,不应受损。
4.4印制电路板组装件
4.4.1导电体脱离基板
焊接后,从印制电路板面至焊盘外侧下部边缘最大允许上翘距离,应为焊区或焊盘的厚度(高度)。
4.4.2组装件的清洁
组装件焊接后应清除杂质(焊剂残渣、绝缘层残渣等)。
4.5热膨胀系数失配补偿
元器件安装工艺或印制电路板设计,应能补偿元器件与印制电路板之间的热膨胀系数失配,安装工艺的补偿应限于元器件引线、元器件的特殊安装以及常规焊点。
禁止设计特殊的焊点外形作部分热膨胀系数失配补偿之用。
无引线元器件不应在槽形而和焊盘之间使用多余的内连线连接,无引线芯片载体仅底部端接时最小焊点高度一般为0.2mm。
4.6互连线的焊接点
组装件间的互连线,应焊接在金属化孔或接线端上。
不应采用另加绝缘套管的镀锡裸线。
4.7表面安装的焊接
手工焊接表面贴装多引线元器件时,应使用对角线方法依次焊接引线,最小焊接长度为1~2mm。
4.8焊接温度、时间
4.8.1手工焊接温度一般应设定在260~300℃范围之内,焊接时间一般不大于水,对热敏元器件、片状元器件不超过2s,若在规定时间未完成焊接,应待焊点冷却后再复焊,非修复性复焊不得超过2次。
4.8.2波峰焊机焊槽内温度应控制在250士5℃范围,焊接时间为3~3.5s。
4.8.3再流焊焊接温度、时间按有关文件规定。
4.9通孔充填焊料的要求
对有引线或导线擂入的金属化孔充填焊料时,焊料只能从焊接面一侧流入小孔内的另一侧。
5详细要求
5.1焊接准备
5.1.1被焊导电体表面在焊接操作前应进行清洁处理。
5.1.2导线、引线与接线端子在焊接前,应使用机械方法将其固定,防止导线、引线在端
子上移动。
5.1.3对镀金的元器件应经搪锡处理(高频器件、微电路除外)。
5.1.4元器件安装应按QJ3012要求执行。
5.2焊接材料
5.2.1焊料
应采用符合GB3131的焊料制品HLSn60Pb或HLSn63Pb,焊料外形任选,带芯焊料的焊剂应为R型或RMA型。
5.2.2膏状焊料
选用时应考虑焊料粉的颗粒形状、粘性、印刷性能、分解温度等技术指标,对焊料粉的氧化物应有控制。
5.2.3焊剂
应采用符合GB9491的R型或RMA型松脂剂液体焊剂。
导线电缆焊接不应使用RA型焊剂,其它场合使用RA型焊剂时应得到有关部门批准。
5.3焊接
5.3.1导线、引线与接线端子的焊接
5.3.1.1导线、引线与接线端的缠绕
导线、引线在接线端子上缠绕最少为3/4圈,但不得超过一圈。
如图1所示。
对于直径小于0.3mm的导线,最多可缠绕3圈。
5.3.1.2导线、引线最大截面积
导线、引线与接线端连接部位的截面积,不应超过接线端子接线孔的截面积。
5.3.1.3接线端最多焊点数
每个接线端子一般不应有三个以上的焊点。
5.3.1.4绝缘层间隙
焊点焊料与导线的绝缘层间隙:
a.最小间隙:
绝缘层可紧靠焊料,但不能嵌入焊料,绝缘层不能熔融,烧焦或缩直
径;
b.最大间隙:
为两倍导线直径或1.6mm。
5.3.1.5导线、引线与接线端子的焊接
焊料应在导线与接线端接触部分形成焊缝,焊料不应掩盖导线的轮廓,对槽形接线端,焊料可以充满焊槽。
如图2所示。
5.3.1.6导线、引线与焊杯的焊接
不应有超过=根的导线插人焊杯,多股芯线保持整齐,不应折断,并全部插入焊杯的底部,焊缝沿接触表面形成,焊料应润湿焊杯整个内侧,并至少充满杯口的75%,如图3、4所示。
5.3.2印制电路板组装件的焊接
5.3.2.1通孔焊接
5.3.2.1.1引线或导线插装用孔
对有引线或导线插入的金属化孔,通孔应充填焊料.焊料应从印制电路板一侧连续流到另一侧的元器件面,并覆盖焊盘面积的90%以上,焊料允许凹缩进孔内,凹缩量如图5所示。
5.3.2.1.2引线弯曲半径部位的焊料
正常的润湿,焊料应在元器件引线弯曲成形部位,但弯曲半径应暴露,焊料沿引线润湿如图6所示。
5.3.2.1.3导线界面连接
作为界面连接的单股镀锡铜线穿过通孔弯钩,弯钩要求应符合元器件引线弯钩要求,
并与印制电路板两面的焊盘焊接。
如图7所示。
5.3.2.1.4非支承孔合格焊点
焊料与被焊表面应有小于90°的接触角。
5.3.2.1.5无引线或导线插装的金属化孔
这种通孔可不填充焊料。
当需填充焊料时焊料塞应满足图5所示的要求。
5.3.2.2表面安装焊接
5.3.2.2.1片状元器件的焊缝
芯片在焊盘上面应75%以上的金属端帽覆盖,并有一条焊缝,焊缝向元器件端面上方延伸,高度为25%或1.0mm。
侧面不需要焊缝,焊料对元器件和焊料对焊盘的润湿角都应小于90°焊料不能把元器件本体上的非金属化部位包住。
如图8、9、10、11所示。
5.3.2.2.2MELF的焊点外形
MELF在焊盘上面应有75%以上的金属端帽的宽度和长度覆盖,如图12所示。
焊点应形成一条焊缝,焊缝向MELF侧面上方延伸高度为0.1mm或25%D(金属端帽直径),如图13所示。
5.3.2.2.3无引线槽形元器件上的焊缝
无引线芯片载体在焊盘上面应有75%以上的金属化槽面宽度覆盖,并有一条焊缝,焊料垂直上升到外侧槽面的下部边缘,焊料对元器件和焊盘的润湿角都应小于90°,当无引线芯片载体仅有底部端接时,最小的焊点高度一般为0.2mm,如图14所示。
5.3.2.2.4无引线元器件平行度
元器件每个端部下面的焊料厚度差异不大于0.4mm,如图15所示。
5.3.2.2.5引线弯曲部位的外形
引线的弯曲不应向元器件本体引线封口处延伸,弯曲引线到焊盘的角度大于45°,小于90°。
;如图16所示。
5.3.2.2.6引线和焊盘的接触
最小的接触长度,扁平引线为引线宽度,圆形引线为两倍直径,如图17所示。
侧向外伸趾端外伸应如图17、18所示范围内。
总的外伸量要保持在最小的接触长度,根部不应伸出焊盘,如图19所示。
5.3.2.2.7引线离开焊盘的高度
引线最小安装面翘离焊盘表面的最大值,圆形引线为引线直径(D)的一半,扁平或带状引线为引线厚度(T)两倍或0.5mm,最小安装面内各点均应在直径一半或两倍引线高度这个最大间隙内,如图20所示。
最小安装面范围取决于引线接触长度以及引线直径或厚度。
5.3.2.2.8最小焊料覆盖面
圆形或扁圆形引线上的最小焊缝高度应为引线直径的25%,扁平引线上的最小焊缝高度处应有一条清晰可见的焊缝,该焊缝至少要从焊盘上升到引线侧面50%高处,焊料与引线焊盘等长,引线轮廓在焊料中应可见,如图21所示。
5.3.2.2.9引线根部焊缝
焊料应向引线上弯部延伸,但不能与元器件本体或引线封口接触,根部焊缝在引线根部和焊盘之间应连续不断,并延伸超出弯曲半径,根部不能伸出焊盘。
5.3.2.2.10J形和V形引线的焊缝
焊盘上应有75%以上的引线宽度覆盖并有一条焊缝,焊缝应向引线侧面上方延伸到引线内表面的高度,焊料不能与元器件封装的底部接触。
焊料沿“J”或“V”的圆弧处形成的焊缝应有一个引线宽度,如图22所示。
5.3.2.2.11J形和V形元器件安装的平行度
焊接后,元器件与印制电路板之间的间隙不应超过2.5mm,如图23所示。
5.4质量保证措施
5.4.1潜在失效的预防
5.4.1.1静电放电
焊接时为防止元器件及电子部件的静电损伤,应按QJ2711规定执行。
5.4.1.2元器件安装、焊接
当根据设计要求安装和焊接的元器件经受不住后续工艺施加应力,应采取单独的操作,将这些元器件安装并焊接到组装件上。
5.4.1.3冷却
焊点应在室温下自然冷却,在焊料固化期间,焊点不应经受移动及应力,不应采用液体冷却焊点。
5.4.1.4引脚的剪断
引脚不应采用产生内应力的剪切工具剪断。
5.4.1.5焊后引线剪断
焊接后剪断元器件引线或导线,焊点应重熔。
5.4.1.6表面安装元器件的单点焊接
初次焊接时,一般不宜采用单点焊接表面安装((SMT)元器件,允许进行单点返修操作的条件是不同时重熔邻近的焊点。
5.4.2检验
焊接质量应在清洗后检验。
5.4.2.1焊点的检验
焊点应百分之百目测检验(可以借助于3~5倍放大镜),焊点的外观应按4.3条规定。
各焊缝的要求,应按5.3条规定。
对返工后的焊点均应重新检验,并应符合4.3条、5.3条规定。
5.4.2.2绝缘体的检验
焊接后,绝缘体不应出现热损伤,裂痕、烧焦,分解等现象(过热变色是允许的)。
5.4.2.3检验用的放大装置
对有争议的焊点或目测拒收的产品,仲裁应提高放大倍数来检验。
焊盘宽度仲裁用
>0.5mm10X
0.25---0.5mm20X
G0.25mm30X
5.4.2.4焊料纯度的检验
对重复使用的焊料应保持其纯度,在焊接前应清除出现在焊料接触面上所有浮渣,并定期按GB3131进行化学光谱分析,若不合格应全部更新焊料。