数控加工工艺及编程技术考试笔记.docx
《数控加工工艺及编程技术考试笔记.docx》由会员分享,可在线阅读,更多相关《数控加工工艺及编程技术考试笔记.docx(15页珍藏版)》请在冰豆网上搜索。
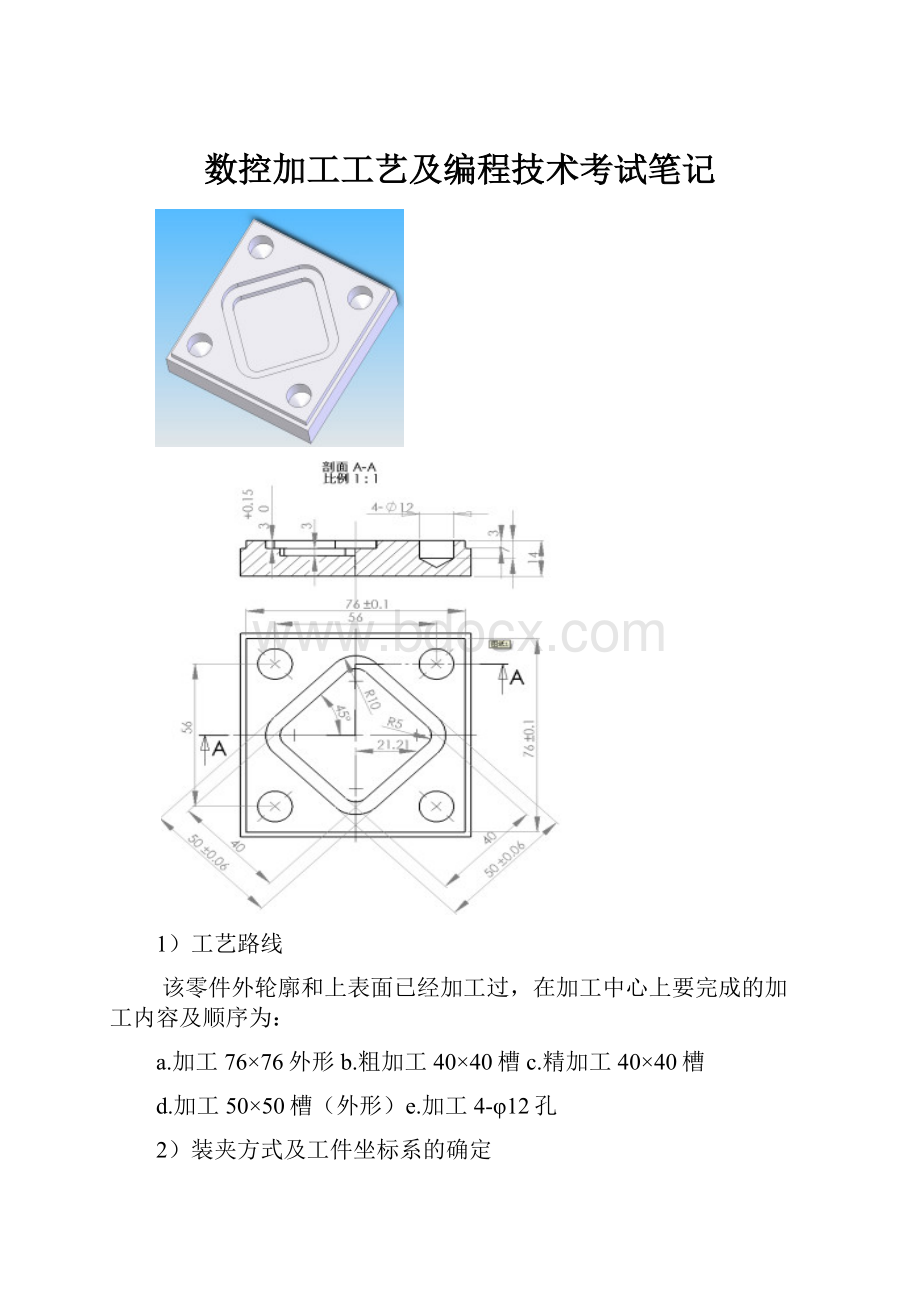
数控加工工艺及编程技术考试笔记
1)工艺路线
该零件外轮廓和上表面已经加工过,在加工中心上要完成的加工内容及顺序为:
a.加工76×76外形b.粗加工40×40槽c.精加工40×40槽
d.加工50×50槽(外形)e.加工4-φ12孔
2)装夹方式及工件坐标系的确定
工件使用平口钳或其他夹具装夹,注意留出6-8mm高度
选择上表面中心为工件坐标系原点
3)数学处理根据编程需要,待加工表面的点的坐标计算
二、走刀路线确定
(1)原则:
①根据工件表面形状和精度要求确定工序和工步,并由此确定各表面加工进给路线的顺序。
②在保证工件轮廓表面加工后精度和粗糙度要求的前提下,寻求最短进给路线(包括空行程路线和切削路线),减少走刀时间以提高加工效率,尽量减少程序段数。
③对横截面积小的细长零件或薄壁零件应采用分几次进给加工的方式,防止切削深度过大,造成切削力过大,工件变形。
④刀具的进、退刀点应避免在轮廓处,避免因停刀而在工件表面留下刀痕,也要避免在工件轮廓面上垂直下刀而划伤工件。
三、
四、
O5005
G50X200Z50T0300;
G96S150M03;
G00X14Z6T0303;
G01Z0F0.25;
X30;
G03X40Z-5R5;
G01Z-20;
X60Z-30;
G02U21.214W-10.607R15;
G01X110;
G00X200Z50;
M05;
M30;
五、
刀尖位置编码:
3
O1000;
N10G50X200Z175T0101;
N20M03S1500;
N30G00G42X58Z10M08;
N40G96S200;
N50G01Z0F1.5;
N60X70F0.2;
N70X78Z-4;
N80X83;
N90X85Z-5;
N100G02X91Z-18R3F0.15;
N110G01X94;
N120X97Z-19.5;
N130X100;
N140G00G40G97X200Z175S1000;
N150M30;
六、
1)依据图样要求,确定加工路线
用三爪卡盘夹持工件Ø36外圆,根据先主后次的原则,确定其加工路线为:
先自右向左切削工件的外轮廓面,然后用切槽;切削完成后返回参考点。
2)选择刀具
根据加工要求,选用外圆车刀(1号刀)和3mm宽切槽刀(2号刀)。
对刀时先以1号刀为基准刀进行对刀,并将01号刀具补偿的R参数设置为1号刀的刀尖圆弧半径值,如0.4,T参数设置为假想刀尖方位号3,X、Z参数均设为0.0;然后通过对刀操作测得2号刀相对于基准1号刀具在径向和轴向的位置偏差值ΔX、ΔZ,分别输入对应的02号刀具补偿的X、Z参数中,R、T参数均不设置或均设为0。
3)选择切削用量
根据工件材料、刀具材料和机床等因素来考虑。
本例中精车外轮廓时主轴转速为600r/min,进给量为0.15mm/r;切槽时主轴转速为300r/min,进给量为0.1mm/r。
4)编写加工程序
工件坐标系原点设在工件右端面与回转轴线的交点O1上,选A点作为起刀点(程序起点),也同时作为换刀点。
加工程序如后
N10G50X100.0Z80.0;工件坐标系设定
N20T0101;调用1号刀,同时选用1号刀具补偿值
N30G42G00X10.0Z3.0S600M03;快速进刀,且刀尖圆弧半径右补偿
N40G01Z0.0F0.15;到达轮廓切削起点位置
N50X16.0W-20.0;加工圆锥面
N60W-10.0;加工Ø16圆柱面
N70G02X32.0W-8.0R8.0;加工R8顺圆弧面
N80G01W-10.0;加工Ø32圆柱面
N90X38.0;加工Ø36端面
N100G40G00X100.0Z80.0;取消刀尖圆弧半径补偿,并退到换刀点
N110T0100M05;取消01号刀刀具补偿,且主轴停转
N120T0202;调用2号刀,同时选用2号刀具补偿值
N130G00X20.0Z-27.0S300M03;到准备切槽位置,且主轴正转
N140G01X13.0F0.1;切槽
N150G04U2.0;暂停2s进行光整
N160G01X20.0;横向退刀
N170G00X100.0Z80.0;退到换刀点
N180T0200;取消02号刀刀具补偿
N190G28U0.0W0.0;直接返回到参考点
N200M30;程序结束
(2)O5010
G00X100Z80T0100;
T0101;
M03S600;
G00X38Z5;
G71U3R1;
G71P30Q40U1W1F0.2;
N30G00X10;
G01X16Z-20;
Z-30;
G02U16W-8R8;
G01W-10;
N40X40;
G40G00X100Z80;
T0100;
G00X100Z80;
M05;
M30;
七、
典型零件程序编制
●通过本例掌握数控车削编程过程步骤与方法,养成良好的工作习惯。
●1.根据零件图样要求、毛坯情况,确定工艺方案及加工路线
1)对细长轴类零件,轴心线为工艺基准,用三爪自定心卡盘夹持φ58㎜外圆一头,使工件伸出卡盘175㎜,用顶尖顶持另一头,一次装夹完成粗精加工(注:
切断时将顶尖退出)
2)工步顺序
①粗车外圆。
基本采用阶梯切削路线,粗车φ56㎜、SφS50㎜、φ36㎜、M30㎜各外圆段以及锥长为10㎜的圆锥段,留1㎜的余量。
②自右向左精车各外圆面:
螺纹段右倒角→切削螺纹段外圆φ30㎜→车锥长10㎜的圆锥→车φ36㎜圆柱段→车φ56㎜圆柱段。
③车5㎜×φ26㎜螺纹退刀槽,倒螺纹段左倒角,车锥长10㎜的圆锥以及车5㎜×φ34㎜的槽。
④车螺纹。
⑤自右向左粗车R15㎜、R25㎜、Sφ50㎜、R15㎜各圆弧面及30°的圆锥面。
⑥自右向左精车R15㎜、R25㎜、Sφ50㎜、R15㎜各圆弧面及30°的圆锥面。
⑦切断
2.选择机床设备
根据零件图样要求,选用经济型数控车床即可达到要求。
故选用CK0630型数控卧式车床。
3.选择刀具
根据加工要求,选用三把刀具,T01为粗加工刀,选90°外圆车刀,T03为切槽刀,刀宽为3㎜,T05为螺纹刀。
同时把三把刀在自动换刀刀架上安装好,且都对好刀,把它们的刀偏值输入相应的刀具参数中。
4.确定切削用量
切削用量的具体数值应根据该机床性能、相关的手册并结合实际经验确定,详见加工程序。
5.确定工件坐标系、对刀点和换刀点
确定以工件左端面与轴心线的交点O为工件原点,建立XOZ工件坐标系。
采用手动试切对刀方法(操作与上面数控车床的对刀方法相同)把点O作为对刀点。
换刀点设置在工件坐标系下X70、Z30处。
6.编写程序
按该机床规定的指令代码和程序段格式,把加工零件的全部工艺过程编写成程序清单。
O1000
N0010G59X0Z195
N0020G90
N0030G92X70Z30
N0040M03S450
N0050M06T01
N0060G00X57Z1
N0070G01X57Z-170F80
N0080G00X58Z1
N0090G00X51Z1
N0100G01X51Z-113F80
N0110G00X52Z1
N0120G91
N0130G81P3
N0140G00X-5Z0
N0150G01X0Z-63F80
N0160G00X0Z63
N0170G80
N0180G81P2
N0190G00X-3Z0
N0200G01X0Z-25F80
N0210G00X0Z25
N0220G80
N0230G90
N0240G00X31Z-25
N0250G01X37Z-35F80
N0260G00X37Z1
N0270G00X23Z-72.5
N0280G00X26Z1
N0290G01X30Z-2F60
N0300G01X30Z-25F60
N0310G01X36Z-35F60
N0320G01X36Z-63F60
N0330G00X56Z-63
N0340G01X56Z-170F60
N0350G28
N0360G29
N0370M06T03
N0380M03S400
N0390G00X31Z-25
N0400G01X26Z-25F40
N0410G00X31Z-23
N0420G01X26Z-23F40
N0430G00X30Z-21
N0440G01X26Z-23F40
N0450G00X36Z-35
N0460G01X26Z-25F40
N0470G00X57Z-113
N0480G01X34.5Z-113F40
N0490G00X57Z-111
N0500G01X34.5Z-111F40
N0510G28
N0520G29
N0530M06T05
N0540G00X30Z2
N0550G91
N0560G33D30I27.8X0.1P3Q0
N0570G01X0Z1.5
N0580G33D30I27.8X0.1P3Q0
N0590G90
N0600G00X38Z-45
N0610G03X32Z-54I60K-54F40
N0620G02X42Z-69I80K-54F40
N0630G03X42Z-99I0K-84F40
N0640G03X36Z-108I64K-108F40
N0650G00X48Z-113
N0660G01X56Z-135.4F60
N0670G00X56Z-113
N0680G00X40Z-113
N0690G01X56Z-135.4F60
N0700G00X50Z-113
N0710G00X36Z-113
N0720G01X56Z-108F60
N0730G00X36Z-45
N0740G00X36Z-45
N0750M03S800
N0760G03X30Z-54I60K-54F40
N0770G03X40Z-69I80K-54F40
N0780G02X40Z-99I0K-84F40
N0790G03X34Z-108I64K-108F40
N0800G01X34Z-113F40
N0810G01X56Z-135.4F40
N0820G28
N0830G29
N0840M06T03
N0850M03S400
N0860G00X57Z-168
N0870G01X0Z-168F40
N0880G28
N0890G29
N0900M05
N0910M02
滚珠丝杠副的精度等级分为1、2、3、4、5、7、10七个等级,1级精度最高,依次递减,数控机床主要采用1-4级。
直线电动机是一种将电能直接转换成直线运动机械能的电力传动装置,它可以看成是一台旋转电机按径向剖开,并展成平面而成。
直线电机进给驱动的主要特点
速度特性好。
速度偏差可达
(1)0.01%以下。
加速度大。
直线电机最大加速度可达30g,目前加工中心的进给加速度已达3.24g,激光加工机的进给加速度已达5g,而传统机床进给加速度在1g以下,一般为0.3g。
定位精度高进给速度范围宽。
可从1
(1)m/s到20m/min以上,目前加工中心的快进速度已达208m/min,而传统机床快进速度<60m/min,一般为20~30m/min。
。
采用光栅闭环控制,定位精度可达0.1~0.01
(1)m。
应用前馈控制的直线电机驱动系统可减少跟踪误差200倍以上。
由于运动部件的动态特性好,响应灵敏,加上插补控制的精细化,可实现纳米级控制。
行程不受限制。
传统的丝杠传动受丝杠制造工艺限制,一般4~6m,更长的行程需要接长丝杠,无论从制造工艺还是在性能上都不理想。
而采用直线电机驱动,定子可无限加长,且制造工艺简单,已有大型高速加工中心X轴长达40m以上。
结构简单、运动平稳、噪声小,运动部件摩擦小、磨损小、使用寿命长、安全可靠。
进给系统齿轮侧隙调整
在数控机床上常见的齿轮间隙消除方法有刚性消除方法和柔性消除方法两种。
1.刚性调整方法
刚性调整法是指调整后齿侧间隙不能自动补偿的调整方法。
它要求严格地控制齿轮的齿厚及齿距的误差,用这种方法调整的齿轮传动有较好的传动精度,结构也比较简单。
2.柔性调整方法
柔性调整法是指调整后齿侧间隙可以自动补偿的调整方法。
即使齿轮齿厚和周节有差异的情况下,仍可以保证无齿隙的啮合。
1)偏心套调整法
2)锥度齿轮轴向垫片调整法
3)双片薄齿轮错齿调整法
4)斜齿轮轴向垫片调整法
5)斜齿轮轴向压簧错齿调整法
按工艺用途分类
切削加工类:
如数控铣床、数控车床、数控磨床、加工中心、数控齿轮加工机床、FMC等。
成型加工类:
数控折弯机、数控弯管机等。
特种加工类:
数控线切割机、电火花加工机、激光加工机等。
其它类型:
数控装配机、数控测量机、机器人等。
按数控系统的进给伺服子系统有无位置测量装置可分为开环数控系统和闭环数控系统,在闭环数控系统中根据位置测量装置安装的位置又可分为全闭环和半闭环两种。
开环数控系统
没有位置测量装置,信号流是单向的(数控装置到进给系统),故系统稳定性好
无位置反馈,精度相对闭环系统来讲不高,其精度主要取决于伺服驱动系统和机械传动机构的性能和精度。
一般以功率步进电机作为伺服驱动元件。
这类系统具有结构简单、工作稳定、调试方便、维修简单、价格低廉等优点,在精度和速度要求不高、驱动力矩不大的场合得到广泛应用。
一般用于经济型数控机床。
半闭环数控系统
半闭环数控系统的位置采样点如图所示,是从驱动装置(常用伺服电机)或丝杠引出,采样旋转角度进行检测,不是直接检测运动部件的实际位置
半闭环环路内不包括或只包括少量机械传动环节,因此可获得稳定的控制性能,其系统的稳定性虽不如开环系统,但比闭环要好。
由于丝杠的螺距误差和齿轮间隙引起的运动误差难以消除。
因此,其精度较闭环差,较开环好。
但可对这类误差进行补偿,因而仍可获得满意的精度。
半闭环数控系统结构简单、调试方便、精度也较高,因而在现代CNC机床中得到了广泛应用。
全闭环数控系统
全闭环数控系统的位置采样点如图的虚线所示,直接对运动部件的实际位置进行检测。
从理论上讲,可以消除整个驱动和传动环节的误差、间隙和失动量。
具有很高的位置控制精度。
由于位置环内的许多机械传动环节的摩擦特性、刚性和间隙都是非线性的,故很容易造成系统的不稳定,使闭环系统的设计、安装和调试都相当困难。
该系统主要用于精度要求很高的镗铣床、超精车床、超精磨床以及较大型的数控机床等。