焊接机器人的应用与发展.docx
《焊接机器人的应用与发展.docx》由会员分享,可在线阅读,更多相关《焊接机器人的应用与发展.docx(30页珍藏版)》请在冰豆网上搜索。
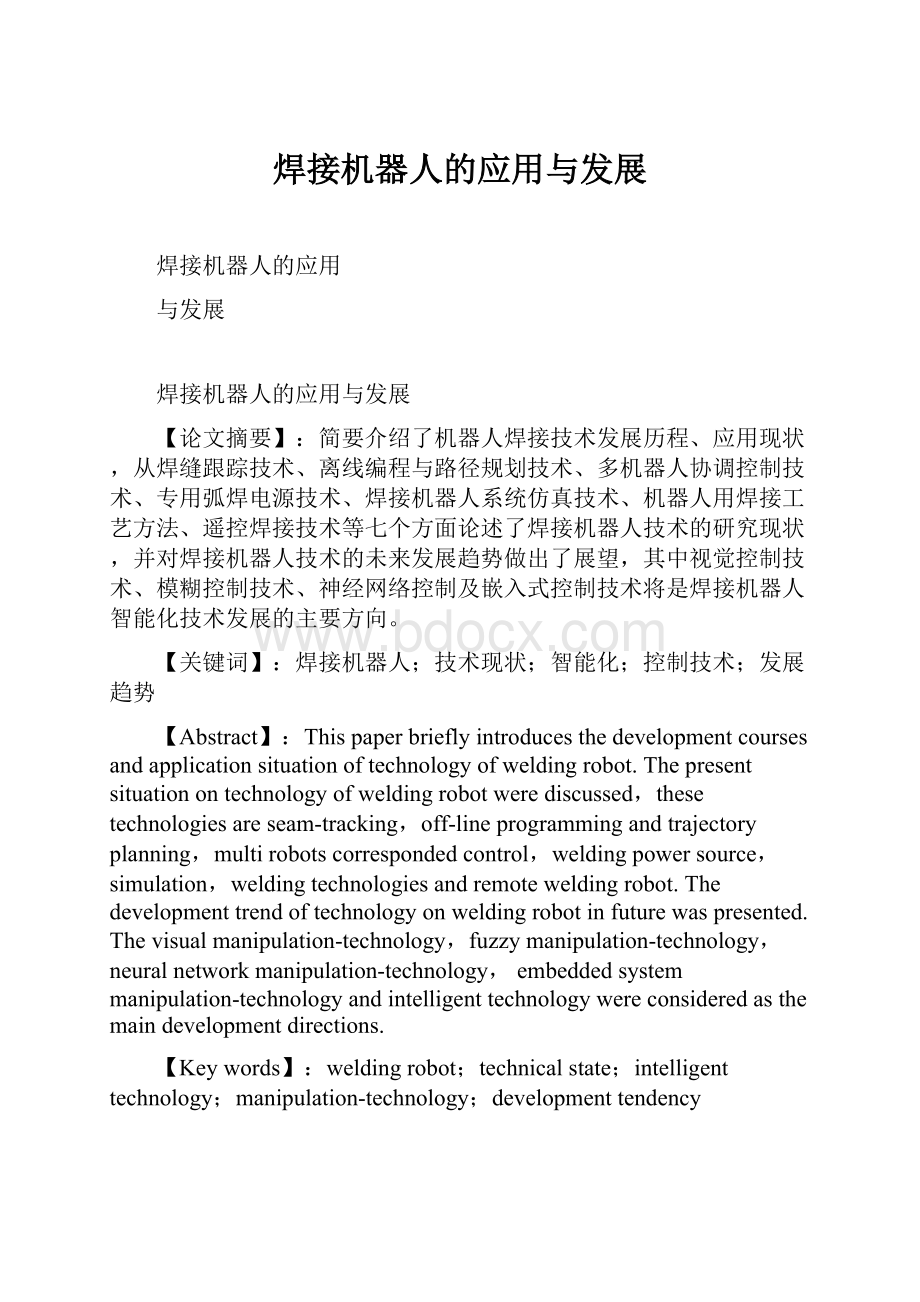
焊接机器人的应用与发展
焊接机器人的应用
与发展
焊接机器人的应用与发展
【论文摘要】:
简要介绍了机器人焊接技术发展历程、应用现状,从焊缝跟踪技术、离线编程与路径规划技术、多机器人协调控制技术、专用弧焊电源技术、焊接机器人系统仿真技术、机器人用焊接工艺方法、遥控焊接技术等七个方面论述了焊接机器人技术的研究现状,并对焊接机器人技术的未来发展趋势做出了展望,其中视觉控制技术、模糊控制技术、神经网络控制及嵌入式控制技术将是焊接机器人智能化技术发展的主要方向。
【关键词】:
焊接机器人;技术现状;智能化;控制技术;发展趋势
【Abstract】:
Thispaperbrieflyintroducesthedevelopmentcoursesandapplicationsituationoftechnologyofweldingrobot.Thepresentsituationontechnologyofweldingrobotwerediscussed,thesetechnologiesareseam-tracking,off-lineprogrammingandtrajectoryplanning,multirobotscorrespondedcontrol,weldingpowersource,simulation,weldingtechnologiesandremoteweldingrobot.Thedevelopmenttrendoftechnologyonweldingrobotinfuturewaspresented.Thevisualmanipulation-technology,fuzzymanipulation-technology,neuralnetworkmanipulation-technology,embeddedsystemmanipulation-technologyandintelligenttechnologywereconsideredasthemaindevelopmentdirections.
【Keywords】:
weldingrobot;technicalstate;intelligenttechnology;manipulation-technology;developmenttendency
目录
摘要……………………………………………………………………………………2
前言……………………………………………………………………………………4
1、焊接机器人的发展历程………………………………………………4
2、焊接机器人国内外应用现状…………………………………………4
3、焊接机器人的发展趋势………………………………………………4
一、焊接基础知识…………………………………………………………………6
1.2、焊接的定义及其本质…………………………………………………6
1.3、焊接工艺的发展历史…………………………………………………6
1.4、概述焊接方法的分类及特点…………………………………………7
1.5、焊接在现代工业中的地位……………………………………………8
二、焊接机器人的发展…………………………………………………………9
2.1、焊接机器人国内外应用现状…………………………………………9
2.2、焊接机器人在焊接生产中的应用……………………………………10
2.3、焊接机器人的编程方法………………………………………………11
2.4、焊接机器人技术的研究现状…………………………………………11
2.5、焊接机器人最新进展…………………………………………………13
三、焊接机器人的发展趋势………………………………………………………15
3.1、焊接机器人的发展趋势…………………………………………………15
3.2、焊接机器人的技术展望…………………………………………………16
3.3、焊接机器人未来研究的热点及发展方向………………………………18
结论挑战与对策……………………………………………………………………19
参考文献………………………………………………………………………………20
致谢词…………………………………………………………………………………21
附录焊接技术发展方向…………………………………………………………22
前言
1、焊接机器人的发展历程
自从世界上第一台工业机器人UNIMATE于1959年在美国诞生以来,机器人的应用和技术发展经历了三个阶段:
第一代是示教再现型机器人。
这类机器人操作简单,不具备外界信息的反馈能力,难以适应工作环境的变化,在现代化工业生产中的应用受到很大限制。
第二代是具有感知能力的机器人。
这类机器人对外界环境有一定的感知能力,具备如听觉、视觉、触觉等功能,工作时借助传感器获得的信息,灵活调整工作状态,保证在适应环境的情况下完成工作。
第三代是智能型机器人。
这类机器人不但具有感觉能力,而且具有独立判断、行动、记忆、推理和决策的能力,能适应外部对象、环境协调地工作,能完成更加复杂的动作,智能机器人还具备故障自我诊断及修复能力。
焊接机器人就是在焊接生产领域代替焊工从事焊接任务的工业机器人。
早期的焊接机器人缺乏“柔性”,焊接路径和焊接参数须根据实际作业条件预先设置,工作时存在明显的缺点。
随着计算机控制技术、人工智能技术以及网络控制技术的发展,焊接机器人也由单一的单机示教再现型向以智能化为核心的多传感、智能化的柔性加工单元(系统)方向发展。
2、焊接机器人国内外应用现状
焊接机器人具有焊接质量稳定、改善工人劳动条件、提高劳动生产率等特点,广泛应用于汽车、工程机械、通用机械、金属结构和兵器工业等行业。
据不完全统计,全世界在役的工业机器人中大约有一半用于各种形式的焊接加工领域。
截止2005年全世界在役工业机器人约为91.4万套,其中日本装备的工业机器人总量达到了50万台以上,成为“机器人王国”,其次是美国和德国;在亚洲,日本、韩国和新加坡的制造业中每万名雇员占有的工业机器人数量居世界前三位。
近几年,全球机器人的数量在迅速增加,仅2005年就达12.1万台。
我国自上个世纪70年代末开始进行工业机器人的研究,经过二十多年的发展,在技术和应用方面均取得了长足的发展,对国民经济尤其是制造业的发展起到了重要的推动作用。
据不完全统计,最近几年我国工业机器人呈现出快速增长势头,平均每年的增长率都超过40%,焊接机器人的增长率超过了60%;2004年国产工业机器人数量突破1400台,进口机器人数量超过9000台,这其中的绝大多数都应用于焊接领域;2005年我国新增机器人数量超过了5000台,但仅占亚洲新增数量的6%,远小于韩国所占的15%,更远小于日本所占的69%。
这样的增长速度相对于我国的经济发展速度以及经济总量来说显然是不匹配的,这说明我国制造业的自动化程度有待进一步提高,另一方面也反映了我国劳动力成本的低廉,制造业自动化水平以及工业机器人应用程度的提高受到限制。
当前焊接机器人的应用迎来了难得的发展机遇。
一方面,随着技术的发展,焊接机器人的价格不断下降,性能不断提升;另一方面,劳动力成本不断上升,我国经济的发展,由制造大国向制造强国迈进,需要提升加工手段,提高产品质量和增加企业竞争力,这一切预示着机器人应用及发展前景空间巨大。
3、焊接机器人的发展趋势
焊接机器人在高质量、高效率的焊接生产中,发挥了极其重要的作用。
工业机器人技术的研究、发展与应用,有力地推动了世界工业技术的进步。
近年来,焊接机器人技术的研究与应用在焊缝跟踪、信息传感、离线编程与路径规划、智能控制、电源技术、仿真技术、焊接工艺方法、遥控焊接技术等方面取得了许多突出的成果。
随着计算机技术、网络技术、智能控制技术、人工智能理论以及工业生产系统的不断发展,焊接机器人技术领域还有很多亟待我们去认真研究的问题,特别是焊接机器人的视觉控制技术、模糊控制技术、智能化控制技术、嵌入式控制技术、虚拟现实技术、网络控制技术等方面将是未来研究的主要方向。
一、焊接基础知识
1.1、焊接的定义及其本质
焊接是通过加热、加压,或两者并用,并且用或不用填充材料,使两个分离的物体产生原子(分子)间结合的一种方法被结合的两个物体可以是各种同类或不同类的金属、非金属(石墨、陶瓷、塑料等),也可以是一种金属与一种非金属。
金属等固体之所以能保持固定的形状是因为其内部原子间距(晶格距离)十分小,原子之间形成牢固的结合力。
要把两个分离的金属焊件连接在一起,从物理本质上来看就是要使这两个焊件连接表面上的原子拉近到金属晶格距离(即0.3~0.5nm或3~5Å)。
然而,在一般情况下材料表面总是不平整的,即使经过精密磨削加工,其表面平面度仍比晶格距离大得多(约几十微米);另外,金属表面总难免存在着氧化膜和其他污物,阻碍着两分离焊件表面原子间的接近。
因此,焊接过程的本质就是通过适当的物理化学过程克服这两个困难,使两个分离焊件表面的原子接近到晶格距离而形成结合力。
这些物理化学过程,归结起来不外乎是用各种能量加热和用各种方法加压两类。
1.2、焊接工艺的发展历史
焊接技术是随着金属的应用而出现的,古代的焊接方法主要是铸焊、钎焊和锻焊。
中国商朝制造的铁刃铜钺,就是铁与铜的铸焊件,其表面铁与铜的熔合线蜿蜒曲折,结合良好。
春秋战国时期曾侯乙墓中的建古铜座上有许多盘龙,是分段钎焊连接而成的。
经分析,所用的与现代钎料成分相近。
战国时期制造的刀剑,刀刃为钢,刀背为熟铁,一般是经过加热锻焊而成的。
据明朝宋应星所著《天工开物》一书记载:
中国古代将铜与铁一起入炉加热,经锻打制造刀、斧;用黄泥或筛细的陈久壁土撒在接口上,分段锻造大型船锚。
到公元7世纪唐代时,已应用锡钎焊和银钎焊来焊接了这比欧洲国家要早10个世纪。
古代焊接技术长期停留在铸焊、锻焊和钎焊的水平上,使用的热源都是炉火,温度低、能量不集中,无法用于大截面、长焊缝工件的焊接,只能用以制作装饰品、简单的工具和武器。
然而,目前工业生产中广泛应用的焊接方法却是19世纪末和20世纪初现代科学技术发展的产物。
特别是冶金学、金属学以及电工学的发展,奠定了焊接工艺及设备的理论基础;而冶金工业、电力工业和电子工业的进步,则为焊接技术的长远发展提供了有利的物质和技术条件。
19世纪初,英国的戴维斯发现电弧和氧乙炔焰两种能局部熔化金属的高温热源;1885~1887年,俄国的别纳尔多斯发明碳极电弧焊钳;1900年又出现了铝热焊。
20世纪初,碳极电弧焊和气焊得到应用,同时还出现了薄药皮焊条电弧焊,电弧比较稳定,焊接熔池受到熔渣保护,焊接质量得到提高,使手工电弧焊进入实用阶段,电弧焊从20年代起成为一种重要的焊接方法。
在此期间,美国的诺布尔利用电弧电压控制焊条送给速度,制成自动电弧焊机,从而成为焊接机械化、自动化的开端。
1930年美国的罗宾诺夫发明使用焊丝和焊剂的埋弧焊,焊接机械化得到进一步发展。
40年代,为适应铝、镁合金和合金钢焊接的需要,钨极和熔化极惰性气体保护焊相继问世。
1951年苏联的巴顿电焊研究所创造了电渣焊,成为大厚度工件的高效焊接法。
1953年,苏联的柳巴夫斯基等人发明了二氧化碳气体保护焊,促进了气体保护电弧焊的应用和发展,如出现了混合气体保护焊、药芯焊丝气渣联合保护焊和自保护电弧焊等。
1957年美国的盖奇发明了等离子弧焊;40年代德国和法国发明的电子束焊,也在50年代得到了实用和进一步的发展;60年代又出现激光焊。
等离子弧焊、电子束焊和激光焊等焊接方法的出现,标志着高能量高密度熔焊的新发展,大大改善了材料的焊接性,使许多难以用其他方法焊接的材料和结构得以焊接。
其他的焊接技术还有,1887年美国的汤普森发明电阻焊,并发明用于薄板的点焊和缝焊;缝焊是压焊中最早的半机械化焊接方法,随着缝焊过程的进行,工件被两滚轮推送前进;20世纪20年代开始使用闪光对焊方法焊接棒材和链条。
至此电阻焊进入实用阶段。
1956年,美国的琼斯发明了超声波焊;苏联的丘季科夫发明了摩擦焊;1959年,美国斯坦福研究所研究成功爆炸焊;50年代末苏联又制成真空扩散焊设备
1.3、概述焊接方法的分类及特点
目前,在工业生产中应用的焊接方法已达百余种。
根据它们的焊接过程特点可将其分为熔焊、压焊和钎焊三大类,每大类又可按不同的方法细分为若干小类,如图所示。
------
(1)熔焊将待焊处的母材金属熔化以形成焊缝的焊接方法称为熔焊。
实现熔焊的关键是要有一个能量集中、温度足够高的局部热源。
若温度不够高,则无法使材料熔化;而能量集中程度不够,则会加大热作用区的范围,徒然增加能量损耗。
按所使用热源的不同,熔焊可分为以下一些基本方法:
电弧焊(以气体导电时产生的电弧热为热源,以电极是否熔化为特征分为熔化极电弧焊和非熔化极电弧焊两大类)、气焊(以乙炔或其他可燃气体在氧中燃烧的火焰为热源)、铝热焊(以铝热剂的放热反应产生的热为热源)、电渣焊(以熔渣导电时产生的电阻热为热源)、电子束焊(以高速运动的电子流撞击焊件表面所产生的热为热源)、激光焊(以激光束照射到焊件表面而产生的热为热源)等若干种。
在熔焊时,为了避免焊接区的高温金属与空气相互作用而使性能恶化,在焊接区要实施保护。
保护的方法通常有造渣、通以保护气和抽真空三种。
因此,保护形式常常是区分熔焊方法的另一种特征。
(2)压焊焊接过程中,必须焊件施加压力(加热或不加热),以完成焊接的方法称为压焊。
为了降低加压时材料的变形抗力,增加材料的塑性,压焊时在加压的同时常伴随加热措施。
按所施加焊接能量的不同,压焊的基本方法可分为:
电阻焊(包括点焊、缝焊、凸焊、对焊)、摩擦焊、超声波焊、扩散焊、冷压焊、爆炸焊和锻焊等。
(3)钎焊采用比母材熔点低的金属材料作钎料,将焊件和钎料加热到高于钎料熔点,低于母材熔化温度,利用液态钎料润湿母材,填充接头间隙并与母材相互扩散实现连接焊件的焊接方法称为钎焊。
钎焊时,通常要清洁焊件表面污物,增加钎料的润湿性,这就需要采用钎剂。
钎焊时也必须加热熔化钎料(但焊件不熔化)。
按热源的不同可分为火焰钎焊(以乙炔在氧中燃烧的火焰为热源)、感应钎焊(以高频感应电流流过焊件产生的电阻热为热源)、电阻钎焊(以电阻辐射热为热源)、盐浴钎焊(以高温盐溶液为热源)和电子束钎焊等。
也可按钎料的熔点不同分为硬钎焊(熔点450℃以上)和软钎焊(熔点在450℃以下)两类。
钎焊时通常要进行保护,如抽真空、通保护气体和使用钎剂等。
1.4、焊接在现代工业中的地位
在现在工业中,金属是不可缺少的重要材料。
高速行驶的汽车、火车、载重万吨至几十万吨的轮船、耐腐耐压的化工设备以至宇宙飞行器等都离不开金属材料。
在这些工业产品的制造过程中,需要把各种各样加工好的零件按设计要求连接起来制成产品,焊接就是将这些零件连接起来的一种加工方法。
据不完全统计,,目前全世界年产量45%的钢和大量有色金属,都是通过焊接加工形成产品的。
特别是焊接技术发展到今天,几乎所有部门(如机械制造、石油化工、交通能源、冶金、电子、航空航天等)都离不开焊接技术。
因此可以这样说,焊接技术的发展水平是衡量一个国家科学技术先进程度的重要标志之一,没有现代焊接技术的发展,就不会有现代工业和科学技术的今天。
随着工业生产的发展,对焊接技术提出了多种多样的要求。
如对焊接产品的使用方面,提出了动载、强韧、高压、高温、低温和耐蚀等项要求;从焊接产品结构形式上,提出了焊接厚壁零件到精密零件的要求;从焊接材料的选择上,提出了焊接各种黑色金属和有色金属的要求。
二、焊接机器人的发展
据不完全统计,全世界在役的工业机器人中大约有将近一半的工业机器人用于各种形式的焊接加工领域,焊接机器人应用中最普遍的主要有两种方式,即点焊和电弧焊。
我们所说的焊接机器人其实就是在焊接生产领域代替焊工从事焊接任务的工业机器人。
这些焊接机器人中有的是为某种焊接方式专门设计的,而大多数的焊接机器人其实就是通用的工业机器人装上某种焊接工具而构成的。
在多任务环境中,一台机器人甚至可以完成包括焊接在内的抓物、搬运、安装、焊接、卸料等多种任务,机器人可以根据程序要求和任务性质,自动更换机器人手腕上的工具,完成相应的任务。
因此,从某种意义上来说,工业机器人的发展历史就是焊接机器人的发展历史。
2.1、焊接机器人国内外应用现状
从机器人诞生到本世纪80年代初,机器人技术经历了一个长期缓慢的发展过程。
到了90年代,随着计算机技术、微电子技术、网络技术等的快速发展,机器人技术也得到了飞速发展。
工业机器人的制造水平、控制速度和控制精度、可靠性等不断提高,而机器人的制造成本和价格却不断下降。
在西方社会,和机器人价格相反的是,人的劳动力成本有不断增长的趋势。
把1990年的机器人价格指数和劳动力成本指数都作为参考值100,至2000年,劳动力成本指数为140,增长了40%;而机器人在考虑质量因素的情况下价格指数低于20,降低了80%,在不考虑质量因素的情况下,机器人的价格指数约为40,降低了60%.这里,不考虑质量因素的机器人价格是指现在的机器人实际价格与过去相比较;而考虑质量因素是指由于机器人制造工艺技术水平的提高,机器人的制造质量和性能即使在同等价格的条件下也要比以前高,因此,如果按过去的机器人同等质量和性能考虑,机器人的价格指数应该更低。
由此可以看出,在西方国家,由于劳动力成本的提高为企业带来了不小的压力,而机器人价格指数的降低又恰巧为其进一步推广应用带来了契机。
减少员工与增加机器人的设备投资,在两者费用达到某一平衡点的时候,采用机器人的利显然要比采用人工所带来的利大,它一方面可大大提高生产设备的自动化水平,从而提高劳动生产率,同时又可提升企业的产品质量,提高企业的整体竞争力。
虽然机器人一次性投资比较大,但它的日常维护和消耗相对于它的产出远比完成同样任务所消耗的人工费用小。
因此,从长远看,产品的生产成本还会大大降低。
而机器人价格的降低使一些中小企业投资购买机器人变得轻而易举。
因此,工业机器人的应用在各行各业得到飞速发展。
根据UNECE的统计,2001年全世界有75万台工业机器人用于工业制造领域,其中38.9万在日本、19.8万在欧盟、9万在北美,7.3万在其余国家。
至2004年底全世界在役的工业机器人至少有约100万。
我国的工业机器人从80年代“七五”科技攻关开始起步,目前已基本掌握了机器人操作机的设计国的工业机制造技术、控制系统硬件和软件设计技术、运动学和轨迹规划技术,生产了部分机器人关键元器件,开发出喷漆、弧焊、点焊、装配、搬运等机器人;弧焊机器人已应用在汽车制造厂的焊装线上。
但总的来看,我器人技术及其工程应用的水平和国外比还有一定的距离,如:
可靠性低于国外产品;机器人应用工程起步较晚,应用领域窄,生产线系统技术与国外比有差距;应用规模小,没有形成机器人产业。
当前我国的机器人生产都是应用户的要求,单户单次重新设计,品种规格多、批量小、零部件通用化程度低、供货周期长、成本也不低,而且质量、可靠性不稳定。
因此迫切需要解决产业化前期的关键技术,对产品进行全面规划,搞好系列化、通用化、模块化设计,积极推进产业化进程。
2.2、焊接机器人在焊接生产中的应用
众所周知,焊接加工一方面要求焊工要有熟练的操作技能、丰富的实践经验、稳定的焊接水平;另一方面,焊接又是一种劳动条件差、烟尘多、热辐射大、危险性高的工作。
工业机器人的出现使人们自然而然首先想到用它代替人的手工焊接,减轻焊工的劳动强度,同时也可以保证焊接质量和提高焊接效率。
然而,焊接又与其它工业加工过程不一样,比如,电弧焊过程中,被焊工件由于局部加热熔化和冷却产生变形,焊缝的轨迹会因此而发生变化。
手工焊时有经验的焊工可以根据眼睛所观察到的实际焊缝位置适时地调整焊枪的位置、姿态和行走的速度,以适应焊缝轨迹的变化。
然而机器人要适应这种变化,必须首先像人一样要“看”到这种变化,然后采取相应的措施调整焊枪的位置和状态,实现对焊缝的实时跟踪。
由于电弧焊接过程中有强烈弧光、电弧噪音、烟尘、熔滴过渡不稳定引起的焊丝短路、大电流强磁场等复杂的环境因素的存在,机器人要检测和识别焊缝所需要的信号特征的提取并不像工业制造中其它加工过程的检测那么容易,因此,焊接机器人的应用并不是一开始就用于电弧焊过程的。
实际上,工业机器人在焊接领域的应用最早是从汽车装配生产线上的电阻点焊开始的。
原因在于电阻点焊的过程相对比较简单,控制方便,且不需要焊缝轨迹跟踪,对机器人的精度和重复精度的控制要求比较低。
。
点焊机器人在汽车装配生产线上的大量应用大大提高了汽车装配焊接的生产率和焊接质量,同时又具有柔性焊接的特点,即只要改变程序,就可在同一条生产线上对不同的车型进行装配焊接。
工业机器人的结构形式很多,常用的有直角坐标式、柱面坐标式、球面坐标式、多关节坐标式、伸缩式、爬行式等等,根据不同的用途还在不断发展之中。
焊接机器人根据不同的应用场合可采取不同的结构形式,但目前用得最多的是模仿人的手臂功能的多关节式的机器人,这是因为多关节式机器人的手臂灵活性最大,可以使焊枪的空间位置和姿态调至任意状态,以满足焊接需要。
理论上讲,机器人的关节愈多,自由度也愈多,关节冗余度愈大,灵活性愈好;但同时也给机器人逆运动学的坐标变换和各关节位置的控制带来复杂性。
因为焊接过程中往往需要把以空间直角坐标表示的工件上的焊缝位置转换为焊枪端部的空间位置和姿态,再通过机器人逆运动学计算转换为对机器人每个关节角度位置的控制,而这一变换过程的解往往不是唯一的,冗余度愈大,解愈多。
如何选取最合适的解对机器人焊接过程中运动的平稳性很重要。
不同的机器人控制系统对这一问题的处理方式不尽相同。
一般来讲,具有6个关节的机器人基本上能满足焊枪的位置和空间姿态的控制要求,其中3个自由度(XYZ)用于控制焊枪端部的空间位置,另外3个自由度(ABC)用于控制焊枪的空间姿态。
因此,目前的焊接机器人多数为6关节式的。
对于有些焊接场合,工件由于过大或空间几何形状过于复杂,使焊接机器人的焊枪无法到达指定的焊缝位置或焊枪姿态,这时必须通过增加1~3个外部轴的办法增加机器人的自由度。
通常有两种做法:
一是把机器人装于可以移动的轨道小车或龙门架上,扩大机器人本身的作业空间;二是让工件移动或转动,使工件上的焊接部位进入机器人的作业空间。
也有的同时采用上述两种办法,让工件的焊接部位和机器人都处于最佳焊接位置。
由于机器人控制速度和精度的提高,尤其是电弧传感器的开发并在机器人焊接中得到应用,使机器人电弧焊的焊缝轨迹跟踪和控制问题在一定程度上得到很好解决,机器人焊接在汽车制造中的应用从原来比较单一的汽车装配点焊很快发展为汽车零部件和装配过程中的电弧焊。
机器人电弧焊的最大的特点是柔性,即可通过编程随时改变焊接轨迹和焊接顺序,因此最适用于被焊工件品种变化大、焊缝短而多、形状复杂的产品。
这正好又符合汽车制造的特点。
尤其是现代社会汽车款式的更新速度非常快,采用机器人装备的汽车生产线能够很好地适应这种变化。
另外,机器人电弧焊不仅用于汽车制造业,更可以用于涉及电弧焊的其它制造业,如造船、机车车辆、锅炉、重型机械等等。
因此,机器人电弧焊的应用范围日趋广泛,在数量上大有超过机器人点焊之势。
2.3、焊接机器人的编程方法
焊接机器人的编程方法目前还是以在线示教方式(Teach-in)为主,但编程器的界面比过去有了不少改进,尤其是液晶图形显示屏的采用使新的焊接机器人的编程界面更趋友好、操作更加易。
然而机器人编程时焊缝轨迹上的关键点坐标位置仍必须通过示教方式获取,然后存入程序的运动指令中。
这对于一些复杂形状的焊缝轨迹来说,必须花费大量的时间示教,从而