新编钣金工艺指导书LP.docx
《新编钣金工艺指导书LP.docx》由会员分享,可在线阅读,更多相关《新编钣金工艺指导书LP.docx(23页珍藏版)》请在冰豆网上搜索。
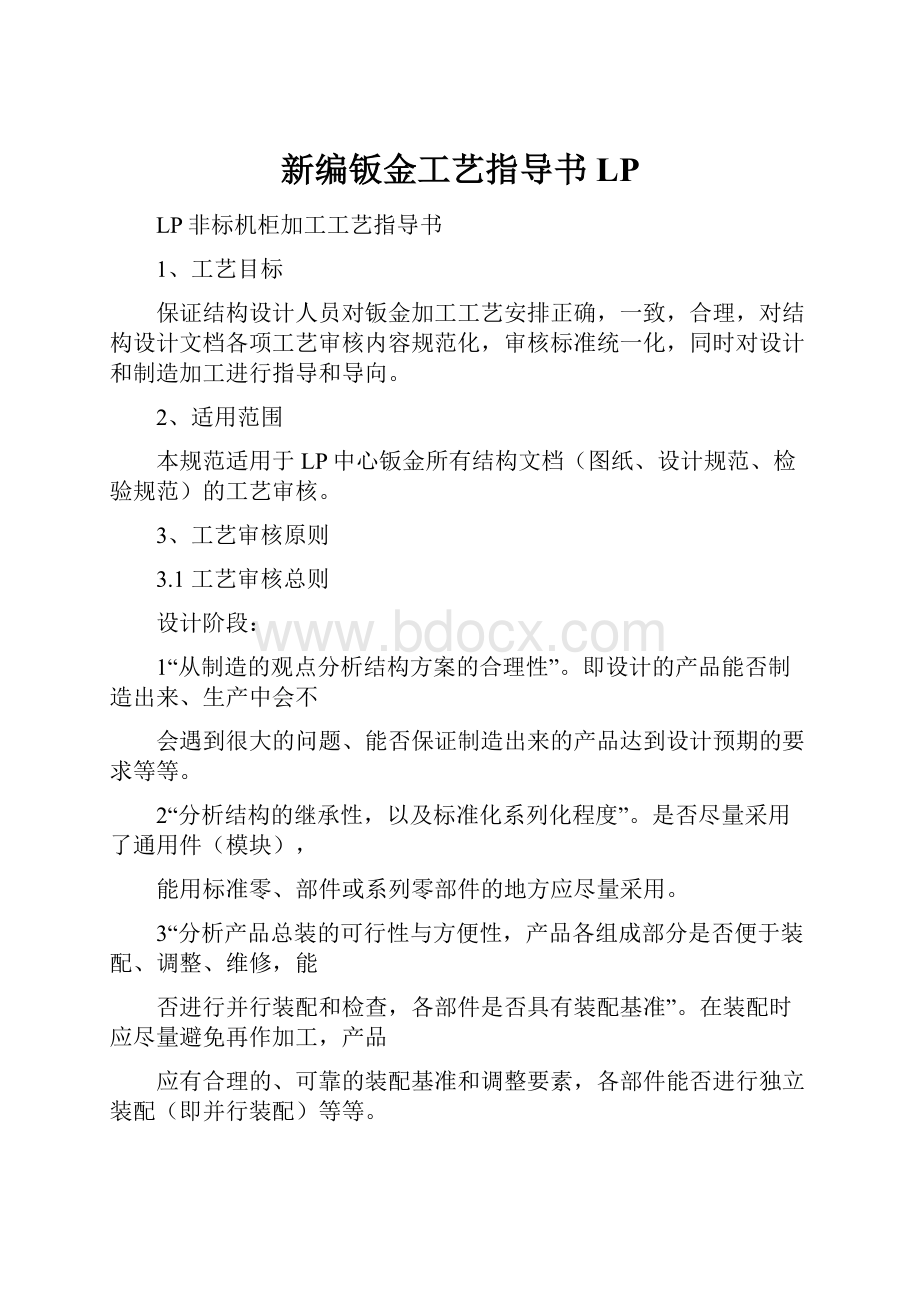
新编钣金工艺指导书LP
LP非标机柜加工工艺指导书
1、工艺目标
保证结构设计人员对钣金加工工艺安排正确,一致,合理,对结构设计文档各项工艺审核内容规范化,审核标准统一化,同时对设计和制造加工进行指导和导向。
2、适用范围
本规范适用于LP中心钣金所有结构文档(图纸、设计规范、检验规范)的工艺审核。
3、工艺审核原则
3.1工艺审核总则
设计阶段:
1“从制造的观点分析结构方案的合理性”。
即设计的产品能否制造出来、生产中会不
会遇到很大的问题、能否保证制造出来的产品达到设计预期的要求等等。
2“分析结构的继承性,以及标准化系列化程度”。
是否尽量采用了通用件(模块),
能用标准零、部件或系列零部件的地方应尽量采用。
3“分析产品总装的可行性与方便性,产品各组成部分是否便于装配、调整、维修,能
否进行并行装配和检查,各部件是否具有装配基准”。
在装配时应尽量避免再作加工,产品
应有合理的、可靠的装配基准和调整要素,各部件能否进行独立装配(即并行装配)等等。
4“分析主要材料选用是否合理”。
尽量不用或少用难加工的、难购买的材料和稀有、
贵重的材料。
5“分析产品零件在本企业或外协加工的可能性”。
如果一个产品的主要零件无法加
工,或加工后不能达到设计要求,这种结构显然是不好的。
6“分析高精度、复杂零件能否在现有生产条件下加工出来,主要的精度参数的可检查
性和装配精度的合理性”。
不能加工出来的,是否可以另想办法替代,加工、装配时无法进
行检查的精度要求,是不和理的,超过使用要求的过高精度要求也是不合理的。
7“审查各有关零件的工艺性”。
(钣金、机加工、焊接、喷涂、电镀等等)。
8“审核三维模型,要求钣金零件必须能够展开”。
3.2图面规范性
图面表达按照制图规范进行。
3.3尺寸和公差
1.重要尺寸应完整、正确、清晰;
2.尺寸基准选择既要考虑设计要求、又要考虑加工定位和测量检验的要求;
3.有装配要求的两个零件的配合尺寸应有公差要求;
4.配合选择应合理,优先选用基孔制,尽量选用优先配合和常用配合;
5.公差等级选择应适当;
6.形位公差选择应合理、适当;
7.未注尺寸公差和未注形位公差的使用按信息平台/设计规范/技术规范中“未注尺寸公
差技术规范”和“未注形位公差技术规范”执行。
3.4装配图
1.各零件组装是否方便,安装方法是否过于复杂,可否有更简便的结构实现同样功能的
装配;
2.装配中的运动部件应运动自如,在运动时不得与其它零部件产生干涉;
3.必要的尺寸标注必须完整。
装配图中必须标注的尺寸包括外形尺寸、装配尺寸、安装
尺寸、性能规格尺寸和运动部件的极限尺寸等。
尺寸标注的基准尽量考虑便于检验。
4.装配时需特别注意的事项应在技术要求中注明。
3.5钣金加工工艺
3.5.1钣金加工基本流程及主要加工工艺
3.5.2钣金加工工序
3.5.2.1冲裁与下料
1.冲裁件的形状尽可能设计成对称、简单和减少废料;
2.冲裁件的外形和内孔应避免尖角,在各直线或曲线的连接处应有适宜的圆角相连。
一
般情况下圆角半径R应大于或等于板厚t,即R≥t;特殊情况下采用激光切割最小R0.5。
3.冲孔优先选用圆形孔,冲孔的最小尺寸与孔的形状、材料机械性能和材料厚度有关。
自由凸模冲孔的直径d或边宽a按下表确定:
4.冲裁件上应避免窄长的悬臂和凹槽(见图2)。
一般凸出或凹入部分的宽度B应大于
或等于板厚t的一倍半,即B≥1.5t。
对高碳钢、合金钢等较硬材料B值应再乘以系数
K=1.3~1.5;对黄铜、铝等材料B值应再乘以系数K=0.75~0.8。
有特殊要求的零件可采用激光
切割,最小B值为0.38,但设计时B值尽可能不要小于0.5。
5.孔边距和孔间距均应大于或等于板厚t的二倍,即:
A≥2t;B≥1.5t(见图3)。
3.5.2.2折弯
1.一般原则:
(1)折弯件在弯曲变形区截面会产生变化,折弯半径与板厚之比越小,截面形状变化
越大;
(2)折弯件的弯曲线最好垂直于轧纹方向,最好将毛坯的光亮面作为弯曲件的外表
面,以减少外层拉裂;
(3)折弯成形时会产生回弹现象,折弯半径与板厚之比越大,回弹就越大。
2.折弯件的折弯半径应选择适当,不宜过大或过小,最小折弯半径只有在结构上必要时
才选用。
其数值见下表:
另外,特殊情况下必须选用0.5以下的折弯半径时,可采用折弯前压线的工艺方法。
3.折弯件的直边高度应选择适当,折弯件的最小直边高度按下表确定。
4.工艺孔和工艺缺口应明确标注,工艺孔和工艺缺口的尺寸根据图5所示选取。
5.折弯件上的孔边缘离弯曲变形区应有一定距离,以免孔的形状因弯曲而产生变形。
孔
边缘离弯曲圆弧中心的距离L应大于或等于板厚t的二倍,即:
L≥2t(见图6)。
6.折弯件的弯曲线应避开尺寸突变的位置,离变形区的距离L应大于弯曲半径r,即:
L
≥r(见图7)。
7.带斜边的折弯边应避开变形区(见图8)。
3.5.2.3拉伸与成型
<1>拉伸变形
1.拉伸件的底与壁之间最小圆角半径应大于板厚,即r1>t,为了使拉伸进行得更顺利,
一般取r1=(3~5)t,最大圆角半径应小于或等于板厚的8倍,即r1≤8t。
(参见图9)
2.拉伸件凸缘与壁之间的圆角半径应大于板厚的二倍,即r2>2t,为了使拉伸进行得更
顺利,一般取r2=(5~10)t,最大凸缘半径应小于或等于板厚的8倍,即r2≤8t。
(参见图9)
3.圆形拉伸件的内腔直径应取D≥d+12t,以便在拉伸时压板压紧不致起皱。
(参见图
9)
4.矩形拉伸件相邻两壁间的圆角半径应取r3≥3t,为了减少拉伸次数应尽可能取r3≥
1/5H,以便一次拉出来。
(参见图10)
5.拉伸件由于各处所受应力大小各不相同,使拉伸后的材料厚度发生变化。
一般来说,
底部中央保持原来的厚度,底部圆角处材料变薄,顶部靠近凸缘处材料变厚,矩形拉伸件四
周圆角处材料变厚。
在设计拉伸产品时,对产品图上的尺寸应明确注明必须保证外部尺寸或
内部尺寸,不能同时标注内外尺寸。
6.拉伸件之材料厚度,一般都考虑工艺变形中的规律有上下壁厚不相等的现象(即上厚
下薄)。
7.圆形无凸缘拉伸件一次成形时,高度H和直径d之比应小于或等于0.4,即H/d≤0.4
(见图11)。
<2>局部成型
1.加强筋。
在板状金属零件上压筋,有助于增加结构刚性,加强筋结构及其尺寸选择参
见图12。
2.百叶窗。
百叶窗通常用于各种罩壳或机壳上起通风散热作用,其成型方法是借凸模的
一边刃口将材料切开,而凸模的其余部分将材料同时作拉伸变形,形成一边开口的起伏形
状。
百叶窗的结构及其尺寸选择参见图13。
3.打凸的工艺尺寸。
(1)在板状金属材料上打凸须参照以下数据。
(2)打凸间距和凸边距的极限尺寸按下表选取。
4.翻边攻丝主要用于薄板攻丝,在薄板上翻边后攻丝以保证螺纹深度(一般板厚为
0.8~1.5mm)。
翻边攻丝的结构尺寸按下表选取:
3.5.2.4压铆与涨铆
1.铆螺母、铆螺柱、铆螺钉和铆松不脱螺钉参照信息平台/通用结构/紧固件所列规格选
择;
2.零件上用于压铆(涨铆)的开孔直径及中心距弯边或外边缘的尺寸参照信息平台/通
用结构/紧固件规格书中所列选取;
3.如果从折弯件内部压铆螺母,铆螺母中心到弯边内侧的距离L应大于外圆柱半径与4倍
折弯半径之和,即L>D/2+4r(见图14);如果在折弯处开工艺孔,可防止压铆底孔变形,最
小L值为,L>D/2+2r。
4.各种压铆松不脱螺钉适用的最小板厚及压铆底孔参照下表选取。
3.5.2.5攻丝(直接攻丝)
1.攻丝对于材质硬度、板厚及底孔大小均有严格要求。
最小板厚及攻丝底孔的选择按照
下表确定。
2.为保证螺纹质量一般不提倡在铝板上直接攻丝,如必须在铝材上攻丝则需要保证足够
的螺纹深度(一般要求在3mm以上)。
3.注意:
在板材上直接攻丝的零件避免用激光切割,以免由于切割处加热而提高材质硬
度,导致攻丝困难。
3.5.2.6螺钉及铆钉过孔与沉孔
1.螺钉和螺栓的过孔结构尺寸按下表选取。
2.沉头螺钉及沉头铆钉的过孔及沉头大小尺寸按下表选取。
从下表中可以看出来,M2.5以上沉头螺钉的螺钉头高度h均在1.5mm以上,所以厚度
在1.5mm以下的板材不适宜打M2.5以上的国标号为GB819-85的沉头螺钉。
请注意以下带括号
的螺钉在相应板厚使用时,螺钉头会突出到板料外。
因此,尽可能选用特制螺钉头高度与螺
钉头大小的螺钉。
沉头螺钉过孔及沉孔σ=90°
3.5.2.7钣金焊接
1.选择合适的焊接方法(如碰焊、CO2焊、氩弧焊、埋弧焊等),
电阻焊:
点焊、碰焊.
点焊又分为双面点焊、单面点焊、多点点焊
适用在t≤6mm的低碳钢、低合金钢板上,t≤4mm的铝板上.
优点:
焊接质量好,生产效率高,生产成本低,操作简单.
电弧焊:
CO2焊:
具有生产效率高,能耗少,成本低,抗锈能力强.
Ar焊:
1)熔深浅,熔整速度小,生产率低.
2)生产成本比手弧,埋弧焊,CO焊成本均高,且有夹钨缺陷.
2
3)具有焊接质量较好的优点,可焊接有色金属如铝,镁等合二.
2.正确选择焊缝型式和焊缝代号(含基本符号、辅助符号、引出线及焊缝尺寸符号等
);
3.焊接区域空间足够,便于操作;
4.焊接后的结构不应造成喷涂上的困难;
5.尽量减小焊缝长度,减少焊接变形。
6.钣金焊接常见的缺陷,
电弧焊(CO2焊、Ar焊):
焊接变形、咬边、烧穿、气孔、未焊透、夹杂、裂纹
电阻焊(碰焊):
电极过热及压痕过大、飞溅、未焊透、焊点核心不对称、缩孔
3.6开模件
开模件(主要包括塑料件和压铸件)的设计应符合信息平台/设计规范/“塑料件技术规
范”和“压铸件技术规范”。
在此特别注意:
1.各处壁厚尽量均匀,不能相差太大;
2.两壁相交处应平缓过渡(应留有大于R0.5的圆角);
3.开模结构应易于充型,避免出现充型发生困难的死角;
4.垂直于分型面的表面应留有拔模斜度(一般应大于0.5°);
5.开模件尽量避免或减少采用抽芯;
6.尽量避免或减少后续加工量,需要加工的面应力求在同一平面上(不要成台阶面)。
7.塑料件的表面粗糙度图纸上可不标注,但必要的表面处理方法(如蚀纹或抛光)应该
注明。
3.7表面处理
3.7.1几种常见的表面处理
1.电镀
电镀锌工艺流程:
电镀光亮镍工艺流程:
电镀常见的缺陷形式:
起泡、花斑、挂印、黑点、晶粒粗大、露白、手印、水印、焊缝夹溶腐蚀等。
2.皮膜
磷化皮膜工艺流程:
铬化皮膜工艺流程:
皮膜常见的缺陷形式:
露白、针孔、麻点、花斑、水印、残液留痕、深划伤、变形、哑淡等。
3.7.2表面处理注意事项
1.所有电化学处理都应在零件状态下进行,因为处理过程中的化学溶液会被截留在组合
件的缝隙之中而引起腐蚀;
2.点焊的零件可进行化学处理,但不能进行电化学处理(包括电镀、阳极化);
3.铝合金铸件不能进行硫酸阳极氧化处理;
4.细而长的管形(其长度大于2倍直径)零件一般不宜进行电化学处理,因为其内表面
将没有膜层;(特殊情况下可采取特别措施来满足要求)
5.有较深凹槽或细孔(一般指深度大于2倍直径或开口宽度,但优良的工艺可不受此
限)的零件电镀后,其内表面将不能完全覆盖镀层;
6.钢铁件喷涂前最好先进行磷化处理,以增加涂层的附着力;
7.镀亮镍的钢件为提高其耐蚀性,可先镀铜或镀暗镍打底;
8.锌基合金一般采用电镀层作防护装饰,为提高其镀层的结合力,一般需先预镀铜或
镍;
9.因多数有机气体对锌有腐蚀作用,故在设计中应谨慎选用镀锌层与有机材料接触或组
装在同一密闭体内;
10.对有铆接要求的电镀(氧化)件,其加工工序必须是先电镀(或氧化)、然后再铆
接。
3.8丝印
为保证公司产品整体形象的统一,所有公司产品的丝印设计需按以下原则进行:
1.系列产品的丝印形式必须保持一致;
2.同一产品的不同模块的丝印形式必须保持一致;
3.丝印内容(文字或标记)的排列,根据功能和具体结构形式,结合平面设计的美学法
则进行组织,在视觉上达到美观,整齐一致;
4、丝印内容的定位一般以零件外边缘作为基准,为了丝印时更换基准的方便,丝印图
最好将外形尺寸标上;
5、用于指示某一器件功能的丝印内容可位于该器件的上、下、左或右适当位置,位于
器件上或下时丝印内容以中心定位,位于器件左边时丝印内容以右边定位,位于器件右边时
丝印内容以左边定位。
3.9钣金材料介绍
常用钣金材料及性能参数:
注:
板材厚度一般公差为+0,-0.08,即板厚为2.0mm的材料,实际厚度可能只有
1.92mm。
材料选择的一般原则:
1.根据零件所需的机械性能、化学性能和电性能正确选择材料的种类;
2.材料选择应同时兼顾性能要求和经济性,在能够满足性能要求的前提下尽量选用较便
宜的材料;
3.机加工材料的规格(如板材厚度、棒料直径)选取既要考虑有足够的加工余量又要考
虑节省材料。
板材厚度或棒料直径太小会造成加工余量紧张,加工困难;板材厚度或棒料直
径太大会浪费材料,提高成本。
4.钣金材料应在保证强度和刚性的前提下,尽量选用较薄的规格。
有时为了提高钣金件
的强度或刚性,可在钣金件上打出凸筋或凸苞。
4.0主要钣金加工设备简介
1.数控冲床工作原理:
上下模固定,工作台移动带动板材移动来冲切板材,加工出所需
要的工件形状。
在冲切过程中,板材的截面大致可分以下四层,R角(5%)光滑面(60%)撕裂面
(30%)毛刺面(5%),可切板厚最厚达4MM.。
特点:
精度高,加工灵活.。
缺点:
受模具限
制。
2.镭射切割机的工作厚理:
利用凹凸镜焦集激光发生器中光子的能量熔化金属材料,
再利用高压保护气体N2或O2等辅助气体吹除熔解部分来加工。
最大板厚可加工到20mm,特点:
精度高,加工灵活,不受模具限制。
缺点:
效率较低,加工成本高,尽可能不用于加
工铝板以避免因反光而烧毁镭射探头。
3.剪冲床下料:
剪床下料只能切工件的最大外形,必须配合冲床,才能加工出所需工件
之形状。
剪冲下料的特点:
效率高适合大批量生产之产品。
4.折床折弯成型工作原理:
将上、下模分别固定于折床的上、下工作台,利用伺服马
达(液压)传输驱动工作台的相对运动,结合上、下模的形状,从而实现对板材的折弯成形。
5.镭射切割机、数控冲床、折床的加工范围及加工精度见下表: