高炉控制系统工程设计.docx
《高炉控制系统工程设计.docx》由会员分享,可在线阅读,更多相关《高炉控制系统工程设计.docx(30页珍藏版)》请在冰豆网上搜索。
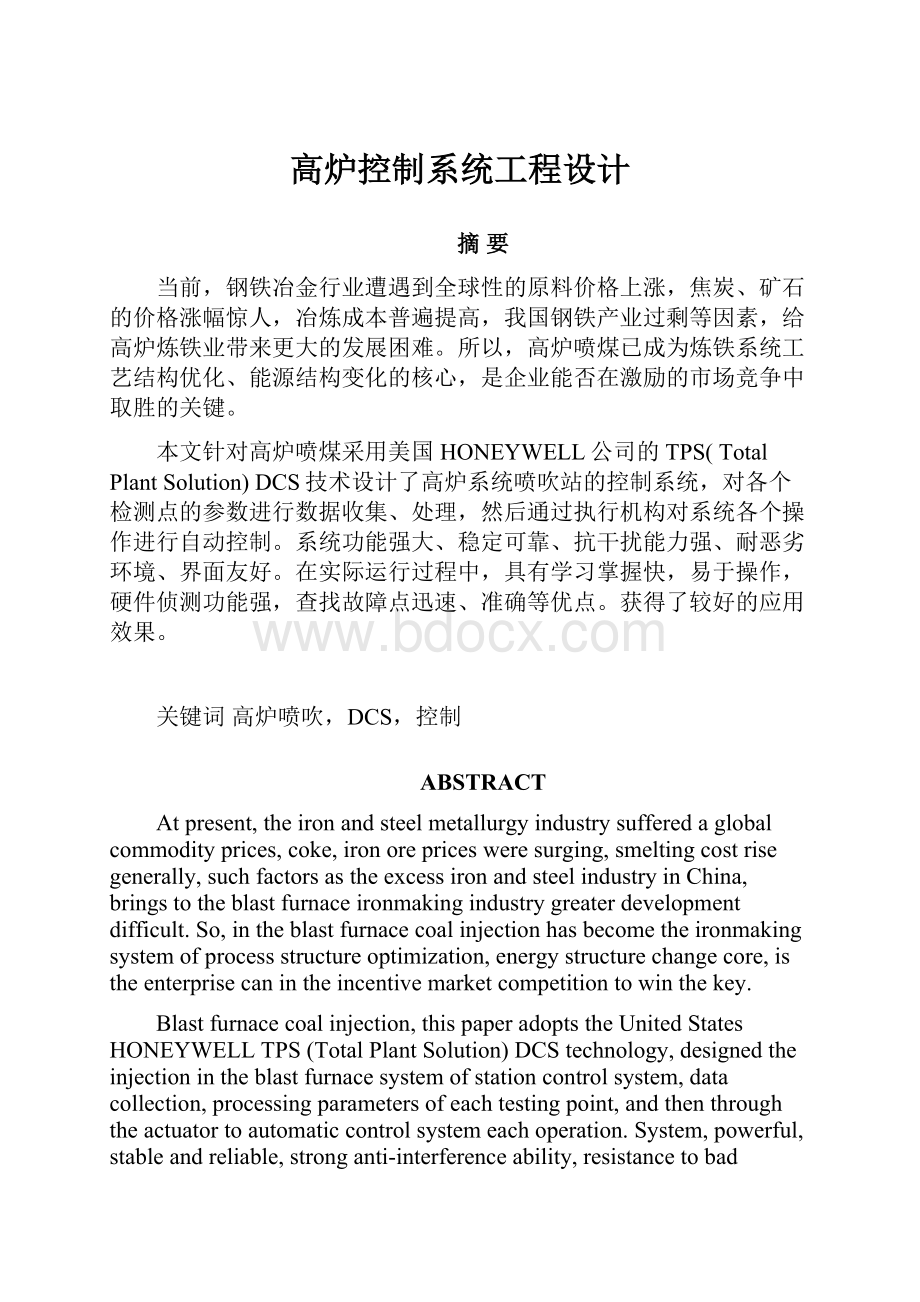
高炉控制系统工程设计
摘要
当前,钢铁冶金行业遭遇到全球性的原料价格上涨,焦炭、矿石的价格涨幅惊人,冶炼成本普遍提高,我国钢铁产业过剩等因素,给高炉炼铁业带来更大的发展困难。
所以,高炉喷煤已成为炼铁系统工艺结构优化、能源结构变化的核心,是企业能否在激励的市场竞争中取胜的关键。
本文针对高炉喷煤采用美国HONEYWELL公司的TPS(TotalPlantSolution)DCS技术设计了高炉系统喷吹站的控制系统,对各个检测点的参数进行数据收集、处理,然后通过执行机构对系统各个操作进行自动控制。
系统功能强大、稳定可靠、抗干扰能力强、耐恶劣环境、界面友好。
在实际运行过程中,具有学习掌握快,易于操作,硬件侦测功能强,查找故障点迅速、准确等优点。
获得了较好的应用效果。
关键词高炉喷吹,DCS,控制
ABSTRACT
Atpresent,theironandsteelmetallurgyindustrysufferedaglobalcommodityprices,coke,ironorepricesweresurging,smeltingcostrisegenerally,suchfactorsastheexcessironandsteelindustryinChina,bringstotheblastfurnaceironmakingindustrygreaterdevelopmentdifficult.So,intheblastfurnacecoalinjectionhasbecometheironmakingsystemofprocessstructureoptimization,energystructurechangecore,istheenterprisecanintheincentivemarketcompetitiontowinthekey.
Blastfurnacecoalinjection,thispaperadoptstheUnitedStatesHONEYWELLTPS(TotalPlantSolution)DCStechnology,designedtheinjectionintheblastfurnacesystemofstationcontrolsystem,datacollection,processingparametersofeachtestingpoint,andthenthroughtheactuatortoautomaticcontrolsystemeachoperation.System,powerful,stableandreliable,stronganti-interferenceability,resistancetobadenvironment,friendlyinterface.Intheactualoperationprocess,learningtomasterquickly,easytooperate,stronghardwaredetectionfunction,findthefaultpointquicklyandaccurately,etc.Obtainedthegoodapplicationeffect.
KeywordsInjectionintheblastfurnace,DCS,control
1绪论
1.1高炉炼铁的介绍
高炉炼铁技术经济指标良好,工艺简单,生产量大,劳动生产效率高,能耗低等优点,所以这种经济的方法生产的铁占世界铁总产量的绝大部分。
高炉炼铁的任务是用还原剂(焦炭、煤等)在高温下降铁矿石或贴原料还原成液态生铁的过程。
高炉生产要求以最小的投入获得最大的产出,即做到高产、优质、低耗,有良好的经济效益。
高炉生产是借助高炉本体和其他辅助设备来完成的。
高炉本体是冶炼生铁的主体设备。
高炉是一个竖式的圆筒形炉子,起本体包括炉基、炉壳、炉衬、冷却设备和炉顶装料设备等。
高炉的内部空间称为炉型,从上到下分为五段,即炉喉、炉身、炉腰、炉腹、炉缸。
整个冶炼过程是高炉内完成的。
高炉炉炉型如图1.1所示。
1.炉基:
高炉基础有上下两部分组成。
上面部分用耐热混凝土制成,称为基墩;下面用钢筋混凝土制成,称为基座。
2.炉壳:
炉壳是用钢板焊接而成的,它起着承受负荷、强固炉体、密封炉墙等作用。
3.冷却设备:
在炉壳与炉衬之间,带走高炉散出的热量,起着保护炉衬、炉壳及延长高炉寿命的作用。
冷却介质多采用水,冷却形式较多。
4.炉衬:
是用耐火砖砌筑而成,他在高温下工作,主要作用是维持高炉合理的内型,为高炉的冶炼创造条件。
图1.2高炉炼铁工艺
高炉炼铁生产系统包括高炉本体工程之外还有其他附属系统相辅助,只有高炉本体工程不能完成高炉炼铁生产。
高炉炼铁的工艺生产流程如图1.2所示。
1.供料系统:
由贮矿槽、称量、筛分、贮焦槽等一个系列设备组成,供料系统的任务是将高炉所需的原料稳定有效地通过上料系统装入高炉炉顶布料设备。
2.送风系统:
由鼓风机、热风炉、和相互联通的管道和阀门等组成,送风系统的任务是将高炉炼铁所需的热风连续可靠的供给高炉。
3.煤气除尘系统:
由重力除尘器、洗涤塔、文氏管、脱水器煤气管道一系列饿设备组成,煤气除尘系统的任务是将高炉炼铁所需的煤气,经过一系列的净化处理使其含尘量降至10mg/m3以下,使煤气能够满足用户对其质量的要求。
4.渣铁处理系统:
由出铁场、炉前吊车、开铁口机、堵渣口机、炉前吊车、铁水罐车、堵渣口机、及水冲渣设备等设备组成,渣铁处理系统的任务是处理高炉排放出的渣、铁,以保证高炉正常进行。
5.喷吹燃料系统:
由原煤的储存和运输、煤粉的设备和收集及煤粉喷吹等子系统组成,喷吹燃料系统任务是均匀稳定的向高炉喷吹大量煤粉,以煤代焦,降低焦煤消耗。
高炉炼铁过程是炼铁过程是连续不断的,高炉上部不断装入炉料和导出煤气,下部不断鼓入空气(有时富氧)和定期排放出渣铁。
1.2高炉喷煤技术
1840年S.M.Banks对于喷吹焦炭和无烟煤的设想开始发展高炉喷煤技术,根据S.M.Banks的这设想最早于1840~1845年间在Frenchbologne附近的MarneIronworks实现了该技术在世界工业上的成功应用。
该项技术在1881年获得专利权,现在已经成为谁都可以使用的技术。
不过此后的一段时间里,高炉炼铁喷煤技术发展缓慢。
一直到上世纪60年代初,中国、欧洲、美国的一些想提高工厂高炉炼铁效率的工厂陆续的开始在高炉生产过程中试验高炉喷煤技术。
上世纪7O年代末,出现了第二次石油危机,加快了高炉喷煤技术的研究和发展,到80年代初世界范围内开始广泛开发应用高炉喷煤技术,世界各国的钢铁厂高炉喷煤量在不断地提高发展。
其中西欧、日本等国的高炉喷煤量发展非常的迅猛,到上世纪90年代初就有部分钢铁厂的高炉喷煤比达到200kg/t铁,处于世界范围内的领先地位,目前大部分国家的高炉炼铁年平均的喷煤比达到160~200kg/t铁,最高的月平均喷煤比已经达到了210~250kg/t铁。
经过最近上世纪几十年对高炉喷煤技术的研究和实践,高炉喷煤技术水平日益提高,经济效益、环境效益都有很大的进步。
当前,钢铁冶金行业遭遇到全球性的原料价格上涨,焦炭、矿石的价格涨幅惊人,冶炼成本普遍提高,而且钢铁产业严重过剩,这给高炉炼铁业带来更大的困难。
所以,高炉喷煤技术已成为高炉炼铁系统工艺结构优化、能源结构变化的核心,它的发展增强了高炉炼铁工艺与新型非高炉炼铁工艺竞争的力量,缓解了炼铁生产受到资源、投资、成本、能源、环境、运输等多方面限制的压力。
1.3高炉喷煤的意义
高炉喷煤技术对现代高炉炼铁技术来说是一项非常重要的技术革命。
它已成为炼铁系统工艺结构优化、能源结构变化的核心,它的发展增强了高炉炼铁工艺与新型非高炉炼铁工艺竞争的力量。
使高炉炼铁工艺生产的铁在世界铁总产量中占有很大的比例。
所谓的高炉喷煤,就是从高炉风口向炉内直接喷吹磨细了的煤粉(无烟煤、烟煤或两者的混合煤粉以及褐煤),以代替焦炭向高炉提供热量和还原剂。
使高炉生产能够满足以最小的投入获得最大的产出,即做到高产、优质、低耗,有良好的经济效益的要求。
高炉喷煤技术具有以下的重要意义:
1.用低价的煤粉代替价格昂贵的焦炭,能够缓解了焦煤的供需紧张状况,也能够减少对炼焦设施的投资建设费用,降低了炼焦生产过程对环境的污染。
2.高炉喷煤可以有效地改善高炉炉缸的工作状态,使高炉能够稳定顺行。
3.高炉喷煤也是一种有效地调控高炉炉状态的手段。
4.给高炉富氧鼓风、提高风温制造了有利条件。
因为喷吹煤粉会使风口前理论燃烧温度降低,导致理论燃烧温度降低的主要原因有:
1)高炉炼铁喷吹煤粉后煤气量增加,加热煤气需要消耗热量;
2)喷吹煤粉带入的热量少,而焦炭进入风口区时已被充分加热,温度高达1450~1500℃,而喷吹的煤粉温度不超过100℃;
3)煤粉中的碳氢化合物分解需要热量。
5.喷吹煤粉带入高炉的的氢含量比焦炭有了很大的提高,氢含量提高了高炉煤气的穿透扩散能力和还原能力,非常有利于高炉操作指标和矿石的还原的改善。
6.以低价的煤代替了日趋贫乏且价格昂贵的冶金焦,降低了焦化,使高炉炼铁的成本大幅下降。
1.4喷吹工艺技术的发展
当前,钢铁冶金行业遭遇到全球性的原料价格上涨,焦炭、矿石的价格涨幅惊人,冶炼成本普遍提高,这给高炉炼铁业带来更大的困难。
所以为了得到更高的经济效益。
最近十几年,世界各国的高炉喷煤喷吹技术发展都非常的迅速,普及率、喷吹量、计量及自动控制水平在不断提高,喷吹技术也不断的提高与创新,缓解了高炉炼铁行业生产受到资源、投资、成本、能源、环境、运输等多方面限制的压力,主要喷煤喷吹技术的发展表现在以下的几个方面。
1.4.1粒煤喷吹技术
首先采用粒煤喷吹技术并获成功的是英国的钢铁公司Scunthorpeplant和TheRavenGdanskCraigplant。
Scunthorpeplant喷吹的粒煤粒度95%虽小于2mm,但只有10%~3O%小于74μm,其中三座高炉炼铁通常的喷煤量是150kg/t。
在上世纪90年代初进行的l8周试验期间,QueenVictoria号高炉平均喷煤量为196kg/t,高炉喷煤平均喷煤量已经达到207kg/t在最后4周的时候,其焦比降至289kg/t,处于世界的先进水平。
原西德的克勒克纳钢铁公司,瑞典的律勒欧钢铁厂、德国的洛尔丰特钢铁厂的高炉也相继采用了粒煤喷吹技术,美国伯利恒钢铁公司也正在伯恩斯港厂C、D两座高炉上安装粒煤制备和喷吹系统。
1.4.2富氧大喷煤量技术
高炉鼓风中含氧每增加1%,可增产3%,可多喷煤8~lOkg/t。
原苏联是世界上富氧率最高的国家,鼓风中含氧一般在3O%左右。
西欧、日本由于钢铁限产,鼓风含氧一般只有22%~23%(有的高炉不富氧鼓风)。
我国鞍钢2号高炉在“七五”期间进行富氧大喷煤量试验,鼓风含氧由21%增至28.59%,喷煤量由73kg/t提高到170kg/t,取得了利用系数2.4t/m3·d、焦比428kg/t的好成绩。
高炉富氧大喷煤量操作步骤与常规的富氧鼓风有所不同,它在促进煤粉在风口区的燃烧和气化有了很大的提高,因为它采用煤氧喷枪提高煤粉燃烧区局部氧气浓度。
采用高炉直吹管及风口区局部富氧的方式来提高整个鼓风含氧量比其他的喷吹方式更为合理,国内外理论和实践都证明了这点。
在富氧量相同条件下,富氧大喷煤是投资少、增铁节焦有效且简单易行的措施,是本世纪高炉炼铁技术发展的必然趋势。
1.4.3复合喷吹技术
利用高炉喷煤设施开发复合喷吹技术,除喷吹煤粉外,可根据高炉冶炼的需要同时喷吹铁矿粉或熔剂。
能够保证喷吹需要的资源需求。
2喷煤工艺流程和控制要求
2.1喷煤系统的组成
高炉喷煤的生产工艺流程主要由原煤贮运系统、制粉系统、煤粉的输送、煤粉喷吹系统、干燥气体制备和动力系统、煤粉计量等组成。
其工艺流程如图2.1所示。
1.原煤贮运系统
原煤贮运系统由综合贮煤场、贮运方式、煤棚等组成,其设备主要有贮煤场、贮煤槽、原煤仓、原煤运输机械等。
综合贮煤场一般要都要充分考虑能够分别堆放两种或两种以上原煤或者其他的喷吹原料,并能够方便的按工艺要求进行配置原料作业。
煤棚的作用是用于原煤的风干,使制粉过程更为容易。
煤场与煤棚间的运输方式根据其距离的远近可以采用火车、汽车或皮带运输,但是煤棚到制粉间的运输方式通常采用皮带运输。
须设置筛分破碎装置和除铁器在原煤贮运的过程中,其主要的作用是除去原煤中的杂物和控制原煤粒度。
2.制粉系统
制粉系统包括原煤装卸、贮运、磨煤、干燥和煤粉的收集等设施。
制粉系统的任务是把原煤安全地加工成粒度为-200母的占70%以上,水分含量低于2%的符合喷吹要求的粉煤,并将制备好的粉煤输送到煤粉仓。
制粉系统主要由干燥气系统、磨煤系统及煤粉收集等三大部分组成。
3.煤粉的输送
煤粉的输送是指将煤粉仓的煤粉以气体的(空气或氮气)为载体,利用压差进行气力输送。
这种气力输送由煤粉仓下面的输送泵来完成的。
煤粉输送泵按输送形式分为风力螺旋输送和仓式泵两种。
仓式泵又分为下出料仓泵和上出料仓式泵。
4.喷吹系统
煤粉喷吹装置包括集煤罐、贮煤罐、喷吹罐、输送管道、煤粉分配器和喷枪。
根据高炉生产需要的不同,高炉喷吹大体上可以分为常压喷吹和高压喷吹两种。
5.煤粉计量
目前煤粉计量装置有单支管计量和喷吹罐计量两个大类。
喷吹罐计量,是高炉实现高炉喷煤自动化生产控制的前提。
单支管计量技术则是实现风口均匀喷吹或根据炉况变化实施自动调节的重要保证。
6.控制系统
现代的高炉喷煤系统中已经广泛开始采用了计算机控制自动化的生产的方式。
高炉喷煤控制系统可以将制粉系统与喷吹系统分开设置,由两个相对独立的控制站组成,再由高炉的中央控制中心用计算机进行分类控制;也可以将制粉系统和喷吹系统设计成一个操作控制站,让其集中在高炉的中央控制中心,与高炉生产过程采用一样的方式进行控制。
2.2喷吹工艺流程示意图
本喷吹工艺流程由两个系列组成,有两个系列相互配合,相互倒换,实现对高炉的连续喷吹。
高炉喷煤系统的主要工艺控制图如图所示,高炉喷煤系统采用的串罐方式向高炉喷吹煤粉。
主要由煤粉仓、储煤罐、喷煤罐、分配器、给料器及各控制阀和管道组成。
粉仓电子秤的量程为0~125t,不设定压力;储煤罐电子秤的量程为0~25t,储煤罐压力范围为0~0.85MPa;喷煤罐电子秤的量程为0~30t,喷煤罐压力范围为0~0.85MPa。
2.2.1
喷吹工艺的介绍
仓式或煤粉仓的煤粉被送到喷吹系统的集煤罐或直接输送到贮煤罐(中间罐),经倒罐后进入喷煤罐,喷煤罐用压缩空气或者氮气加压后,经混合器(或给煤器),通过管道或者煤粉分配器到高炉各风口的喷煤枪喷入高炉。
其流程图如图2.3所示。
2.2.2喷煤工艺流程的分类及特点
从制粉系统的煤粉仓后面到高炉风口喷枪之间的设施属于喷吹系统,根据制粉装置到高炉距离的远近、煤粉仓,喷吹罐安放位置的差异、喷吹管路的粗细、喷吹压力的高低、输送浓度的大小以及喷枪形式的不同,可以有直接喷吹、间接喷吹;串罐喷吹、并罐喷吹;总管喷吹、多支管喷吹;高压喷吹、常压喷吹;浓相喷吹、稀相喷吹和氧煤枪喷吹、常规枪喷吹等各种形式的喷吹。
1.根据喷吹煤粉设施的布置方式可以分为直接喷吹和间接喷吹。
1)直接喷吹方式是将喷吹设施布置在制粉站的下面,不设输粉站设施,直接将制粉站的煤粉喷入高炉风口,即集制粉、输送和喷吹“三位一体”的方式。
这个喷吹形式的特点是简化了喷吹工艺流程和设施,降低了工程投资而且减少了喷吹煤粉的中间环节,喷吹压力高、设备维修量少。
对喷吹煤粉,可大大降低不安全的因素,使用于高炉附近场地宽裕的大型高炉。
2)间接喷吹则是增加了输粉设施,将煤粉站制备好的煤粉有煤粉站的粉煤仓输送到喷吹站,再由喷吹站把制好的煤粉喷入高炉。
其特点也直接喷吹相反,中间环节多,不安全的因素多,喷吹压力低、设备维修量大,工程投资较大,占地面积大。
表格2.1直接喷吹工艺与间接喷吹工艺特点点的比较
项目
直接喷吹工艺
间接喷吹工艺
工艺流程
流程短,更适合于喷吹烟煤
煤粉需要二次收集,曾加了故障点
投资
只建一座厂房,没有输煤系统,投资小
需要在高炉附近建喷吹站,投资高
动力消耗
消耗低,运行成本低
消耗高,运行成本高
总占地面积
小
大
通用性
新建高炉或高炉附近比较宽阔的工厂
高炉附近非常的狭窄,而且高炉座数多
2.根据喷吹罐布置形式分为并罐式喷吹和串罐式喷吹。
并罐式喷吹形式是由两个或多个喷吹罐在同一水平面上并列布置,一个喷吹罐喷吹时,另一个喷吹罐装煤和充压,这样两个或多个喷吹罐交替使用。
串罐式喷吹是将集煤罐、中间罐、喷吹罐3个罐串联起来与地面从上到下垂直的布置,他们之间用阀门连接和控制。
集煤罐处于常压状态,中间罐和喷吹罐处于高压状态。
通过连接上下罐的管道和阀门装置实现的装卸煤粉的倒罐操作。
根据实际工艺需要,串罐式常可采用多系列喷吹设备,以满足大型高炉多的工艺需要。
串罐式喷吹形式设备容量大,利用率高,向高空发展故装置占地小,连续喷吹,工作可靠作业率高。
现代国内外大型高炉大多采用这种喷吹形式的装置。
3.根据高炉喷煤罐的出粉方式多管路喷吹和单管路喷吹。
1)多管路喷吹,是指从喷吹罐引出多条喷吹管路到高炉各风口,每条喷吹管连接一只喷枪的喷吹形式。
多管路喷吹按出料方式可以分为上出料方式和下出料方式。
可以调节个风口的喷煤量。
2)单管路喷吹,喷吹罐下只设一条管路的喷吹形式。
但管路喷吹必须设置分配器,由分配把煤粉均匀地分配到高炉各风口。
各风口喷煤量的均匀程度取决于多头分配器的结构形式和支管补气调节的可能性,一般小型高炉通常设一个分配器,大型的高炉设置多个分配器。
单管路喷吹可以分为上出料喷吹和下出料喷吹两种。
下出料喷吹适用于一般的喷吹,而上出料喷吹可进行浓相输送喷吹。
2.3喷吹工艺控制要求
在此喷吹系统中要满足以下的控制要求:
1.由于煤粉的温度和碳氧浓度是引起火灾和爆炸的因素,所以煤粉仓的CO浓度要在一定的范围之内,温度也要在一定的限值之内,超过限值能够报警。
2.中间罐和喷吹罐的重量检测,压力检测,超过限值能够报警。
3.喷吹量的稳定,喷吹速度的稳定及其值的检测,超过限值能够报警。
4.煤粉罐、中间罐、喷吹罐的温度稳定在一定的值,超过限值能够报警。
5.喷吹管的压力、温度在一直的值范围内,防止度检测,用以防止压力升高或温度过高引起的喷吹支管堵塞和回火。
6.满足工艺的过程控制功能和多种控制方式:
如能全自动控制,手动控制及手自动控制相结合的控制方式。
能够完成罐压的调节,喷吹量的自动调节。
7.工艺要求能控制多样化,能随时改变控制方式及一些控制量,以适应高炉生产需要或检修需要。
3高炉喷吹生产控制系统设计
本文中的控制系统采用美国HONEYWELL公司的集散控制(DCS)系统来进行对各个检测点的参数进行数据收集、处理,然后通过执行器(调节阀)来对系统进行调节。
下面介绍A系列喷吹的工艺要求,B系列同A系列的控制要求一样,不再详述。
3.1
喷吹系统框图
3.2喷吹工艺及检测点布置
本工程喷吹站采用A,B系列两套喷吹装置进行喷吹煤粉,以保证喷吹的连续性和可靠性,满足喷吹量的要求。
以下是A系列的工艺检测点的布置。
按煤粉喷吹过程的流向分,喷吹设备的最上方是煤粉仓。
在煤粉仓上是布袋收粉装置。
煤粉仓是常压罐体,在设计方案中需设置3点热电阻测量煤粉仓温度;设置1台料位测量雷达来测量料位;设置1个压力测量装置;设置2个氧含量测量装置和1个一氧化碳测量装置。
在煤粉仓中设置1个煤粉仓放散阀;设置1个煤粉仓流化阀;设置1个煤粉仓下锥形阀。
煤粉仓下接中间罐,煤粉仓与中间罐之间采用软连接,设置1中间罐上锥形阀。
中间罐设置2点热电阻测量中间罐温度;设置1台电子称重传感器测量中间罐煤粉重量;设置1个压力传感器测量中间罐压力;设置1中间罐料空信号测量点。
罐中设置1个中间罐充压阀,1个中间罐流化阀,1个放散阀。
中间罐下方设置喷吹罐,中间罐与喷吹罐之间采用由气动锥形阀组成的软连接。
喷吹罐设置2点温度传感器测量罐中温度;设置1个压力传感器测量喷吹罐压力;设置1台电子称重传感器测量喷吹罐煤粉重量;设置1喷吹罐料满信号测量点;设置1个喷吹罐流化阀;1个中间罐与喷吹罐的均压阀;设置1个喷吹罐放散阀;设置1个喷吹罐压力调节阀。
喷吹罐下方设置1下煤球阀,并设置可以连续调节的给煤器用于调节喷煤量。
煤粉仓、中间罐、喷吹罐的放散阀均接入不袋式除尘器。
各管冲压、流化用氮气从氮气包引出,喷吹用压缩空气从空气包引出。
为防止冷气直接接触煤粉时,造成罐壁和管道粘连,氮气和脱水、脱油的压缩空气经蒸气加热到60℃~~70℃,气体温度通过调节蒸气量进行自动控制。
喷吹用的压缩空气总管上设置喷吹阀,设置有压力、流量检测,并有流量调节阀,用于调整喷吹风的流量,给煤器后设置安全阀用于安全切断。
喷吹总管上设置2个喷吹总管压力测试点。
喷吹总管延伸到炉前的喷吹总管分配器。
从分配器上分配出16根喷吹支管。
每根喷吹支管上安装一台喷吹支管压力变送器。
I/O点的数量是系统选择和配置的基础,I/O点数是衡量一个控制系统大小的重要标志。
根据工艺的要求及设备的特性,对整个喷吹站的I/O点数统计如下。
表格3.1系统I/O点的统计
模拟量输入/输出(I/O)点数
100
数字量输入/输出(I/O)点数
120
3.3喷吹系统操作方式
通过CRT可以在键盘上实现系统基本操作方式的转变,操作非常的方便,基本操作方式分为:
全自动操作、手动操作和检修(强制手动)操作。
1.全自动操作:
是在控制室人员通过键盘或鼠标发出“启动”命令后,按规定的程序自动完成自动计量、自动倒罐等。
2.手动操作:
除必要的安全操作外还可以人工的对个单体设备进行手动操作。
3.检修(强制手动)操作:
检修操作是在手动操作之下的一种操作,是进行完全的人工手动操作个单体设备。
3.4喷吹系统过程控制描述
喷吹站的工艺流程分为:
倒罐、喷吹罐加料、喷吹控制等连续的控制过程。
各个过程通过对罐重、罐压的监测,控制各双向气动球阀的开关及调节阀开度的调节来完成。
图3.2是喷吹过程关系框图
1.中间罐加料,既将煤粉从煤粉仓到中间罐顺序的控制描述:
中间罐加料前的条件:
1)中间罐必须为“空信号”。
2)中间罐压力必须小于0.02MPa。
3)中间罐放散阀处于“打开”状态。
4)中间罐充压阀和流化阀处于“关闭”状态。
5)中间罐上锥阀和下锥阀处于“关闭”状态。
6)中间罐与喷吹罐之间的均压阀处于“关闭”状态。
煤粉从煤粉仓到中间罐倒罐顺序:
1)若上述条件没有全部满足,则先调整满足上述条件后在进行以下操作
2)开煤粉仓下锥形阀
3)开中间罐上锥形阀
4)关煤粉仓放散阀
5)开煤粉仓流化阀
6)中间罐“料满”信号发出时再进行以下操作
7)关煤粉仓流化阀
8)开煤粉仓放散阀
9)关煤粉仓下锥形阀
10)关中间罐上锥形阀
11)煤粉从煤粉仓到中间罐倒罐顺序结束,中间罐处于“料满”位置
备注:
1)中间罐的加料同时受时间控制,倒罐开始计时,若在规定的时间(如5分钟)内,没有达到“料满”,则说明出现“故障”,发出报警信号,提示操作工人手动控制或检修。
2)连续生产时,中