变压器电抗器监造实施细则.docx
《变压器电抗器监造实施细则.docx》由会员分享,可在线阅读,更多相关《变压器电抗器监造实施细则.docx(29页珍藏版)》请在冰豆网上搜索。
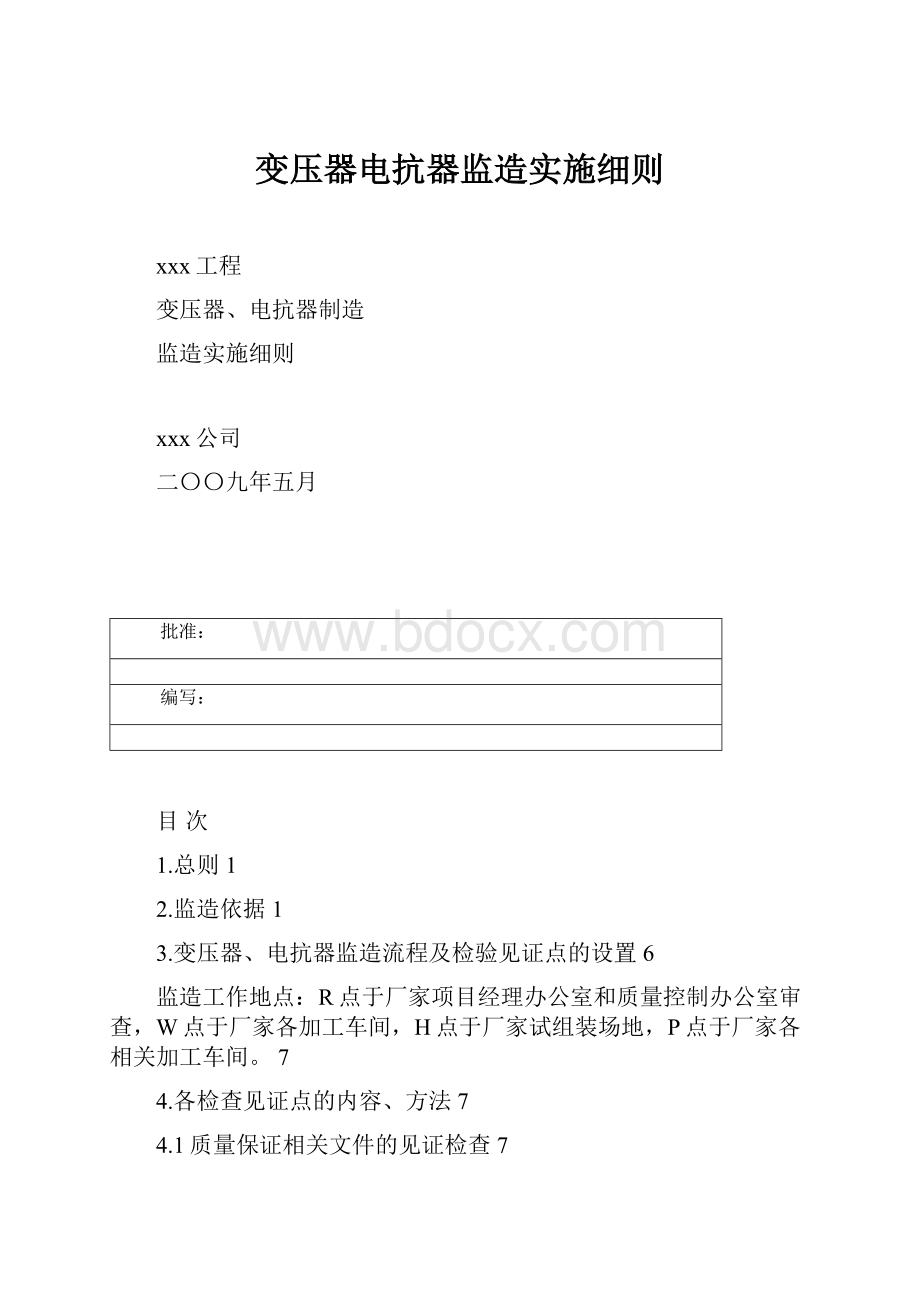
变压器电抗器监造实施细则
xxx工程
变压器、电抗器制造
监造实施细则
xxx公司
二〇〇九年五月
批准:
编写:
目次
1.总则1
2.监造依据1
3.变压器、电抗器监造流程及检验见证点的设置6
监造工作地点:
R点于厂家项目经理办公室和质量控制办公室审查,W点于厂家各加工车间,H点于厂家试组装场地,P点于厂家各相关加工车间。
7
4.各检查见证点的内容、方法7
4.1质量保证相关文件的见证检查7
4.2生产设备、检测设备与条件的见证与监督检查10
4.3铁芯检验与质量监督10
4.4绕线检验与质量监督12
4.5线圈预装质量监督检查13
4.6器身装配质量监督检查14
4.7器身气相干燥质量监督检查15
4.8器身整理质量监督检查15
4.9总装质量监督检查15
4.10真空注油质量监督检查16
4.11出厂电试17
4.12产品发运17
5.监造工作记录、监造报告制度18
4)遇重大事故,编写《设备监造急报》(附表6-3)当日由设备监造单位负责人直接上报业主。
18
6.1监造资料18
6.2出厂见证单及产品制造监理证明19
6.3监造总结的编写19
6.4合同档案制度20
7.其他20
附录A(规范性附录)21
注:
以下所有表格为参照使用表格,具体检查使用时,推荐但不仅限于其中的检查项目。
22
附表122
附表223
附表324
监造工作联络单24
附表426
附表527
监造总结模板37
苏丹东格拉—瓦地哈里法输变电工程
变压器、电抗器制造
监造实施细则
1.总则
为了保证xxx工程变压器、电抗器的制造质量,规范设备监造工作的进行,为设备监造提供指导,特制定本细则。
本细则依据《xxx工程变压器、电抗器制造监造大纲》编制,只适用于该工程变压器、电抗器在制造过程中的产品质量和制造工艺监督工作。
2.监造依据
2.1xxx工程变压器、电抗器监理合同;《监理大纲》。
2.2xxx工程变压器、电抗器供货合同、技术协议。
2.3合同范围
序号
设备名称
数量
卖方名称
1
变压器
2
电抗器
2.4相关标准
序号
标准名称
标准号
1
电力变压器第1部分总则
GB1094.1-1996
2
电力变压器第2部分温升
GB1094.2-1996
3
电力变压器第3部分:
绝缘水平、绝缘试验和外绝缘空气间隙
GB1094.3-2003
4
电力变压器第4部分:
电力变压器和电抗器的雷电冲击和操作冲击试验导则
GB/T1094.4-2005
5
电力变压器第5部分:
承受短路的能力
GB1094.5-2003
6
电力变压器第10部分:
声级测定
GB/T1094.10-2003
7
电流互感器
GB1208-1997
8
电工术语变压器、互感器、调压器和电抗器
GB/T2900.15-1997
9
三相油浸式电力变压器技术参数和要求
GB/T6451-1999
10
电抗器
GB/T10229-1998
11
电力变压器应用导则
GB/T13499-2002
12
油浸式电力变压器负载导则
GB/T15164-1994
13
油浸式电力变压器技术参数和要求500kV级
GB/T16274-1996
14
保护用电流互感器暂态特性技术要求
GB16847-1997
15
干式电力变压器负载导则
GB/T17211-1998
16
电力变压器选用导则
GB/T17468-1998
17
电力变压器、电源装置和类似产品的安全第4部分:
燃气和燃油燃烧器点火变压器的特殊要求
GB19212.4-2005
18
电力变压器、电源装置和类似产品的安全第13部分:
恒压变压器的特殊要求
GB19212.13-2005
19
电力变压器试验导则
JB/T501-1991
20
热带电力变压器、互感器、调压器、电抗器
JB/T831-2005
21
发电厂和变电所自用三相变压器技术参数和要求
JB/T2426-2004
22
变压器类产品型号编制方法
JB/T3837-1996
23
变压器用蝶阀
JB/T5345-2005
24
串联电抗器
JB/T5346-1998
25
变压器用储油柜
JB/T6484-2005
26
变压器用压力释放阀
JB/T7065-2004
27
柱式调压器
JB/T7067-2002
28
互感器用金属膨胀器
JB/T7068-2002
29
变压器用压力释放阀试验导则
JB/T7069-2004
30
调压器试验导则第3部分:
磁性调压器试验导则
JB/T7070.3-2002
31
油浸铁心式串联电抗器试验导则
JB/T7632-1994
32
有载分接开关试验导则
JB/T8314-1996
33
变压器用强油循环风冷却器
JB/T8315-1996
34
变压器类产品用密封制品技术条件第1部分:
橡胶密封制品
JB/T8448.1-2004
35
柱式自动调压器
JB/T8449-2002
36
无励磁分接开关
JB/T8637-1997
37
调压器试验导则第4部分:
柱式接触(自动)调压器试验导则
JB/T8638-1997
38
油浸式电力变压器带有油中溶解气体分析的温升试验导则
JB/T8639-1997
39
调压器通用技术要求
JB/T8749-1998
40
高压并联电容器用放电线圈
JB/T8970-1999
41
干式变压器用横流式冷却风机
JB/T8971-1999
42
封闭母线
JB/T9639-1999
43
试验变压器
JB/T9641-1999
44
变压器用风扇
JB/T9642-1999
45
防腐蚀型油浸式电力变压器
JB/T9643-1999
46
半导体电气传动用电抗器
JB/T9644-1999
47
气体继电器
JB/T9647-1999
48
控制用电流互感器
JB/T9652-1999
49
接触自动调压器
JB/T10089-2001
50
感应自动调压器
JB/T10090-2001
51
接触调压器
JB/T10091-2001
52
磁性调压器
JB/T10092-2000
53
感应调压器
JB/T10093-2000
54
变压器油泵
JB/T10112-1999
55
组合式变压器
JB/T10217-2000
56
单相油浸式配电变压器技术参数和要求
JB/T10317-2002
57
油浸式非晶合铁心配电变压器技术参数和要求
JB/T10318-2002
58
变压器用波纹油箱
JB/T10319-2002
59
变压器用多功能保护装置
JB/T10428-2004
60
三相组合互感器
JB/T10432-2004
61
电力变压器、电源装置和类似产品的安全第24部分:
建筑工地用变压器的特殊要求
GB19212.24-2005
62
变压器用片式散热器
JB/T5347-1999
63
变压器类产品机械制图补充规定
JB/T5355-2002
64
电流互感器试验导则
JB/T5356-2002
65
调压器试验导则第2部分:
感应调压器和感应自动调压器试验导则
JB/T7070.2-2002
66
调压器试验导则第1部分:
接触调压器和接触自动调压器试验导则
JB/T7070.1-2002
67
6kV-500kV级电力变压器声级
JB/T10088-2004
68
变压器用电子温控器
JB/T7631-2005
69
变压器用螺旋板式强油水冷却器
JB/T7633-1994
70
变压器用强油循环水冷却器
JB/T8316-1996
71
变压器冷却器用流量指示器
JB/T8317-1996
72
变压器用绝缘成型件技术条件
JB/T8318-1996
73
变压器类产品用密封制品技术条件第2部分:
软木橡胶密封制品
JB/T8448.2-2004
74
变压器用绕组温控器
JB/T8450-2005
75
电力变流变压器
JB/T8636-1997
76
变压器用速动油压继电器
JB/T10430-2004
77
高燃点绝缘油电力变压器
JB/T10431-2004
注:
上述标准是招标方最低要求。
除此标准以外,制造方可以推荐其他标准,但事先必须通过用户认可,或选择其中较高标准。
2.5制造厂家的生产进度计划、质量计划、质量检验计划和售后服务计划。
3.变压器、电抗器监造流程及检验见证点的设置
根据设备制造流程,对流程中的相关工序分别进行:
文件见证(R点)、现场见证(W点)、停工待检(H点)、日常巡检(P点)等监造方式。
制造过程各工序中具体检验见证点(监造方式)的设置对应表见附表1。
文件见证点(R点):
需要进行文件见证的质量监造点,由制造厂提供文件(如:
原材料合格证明、技术文件、检验记录、试验报告等)供监造人员进行审查。
与之对应的监造方式称为文件见证。
现场见证点(W点):
复杂、关键的工序、测试、试验要求进行旁站见证监造的质量控制点。
与之对应的监造方式称为现场见证。
停工待检点(H点):
对于重要工序节点、关键的试验验收点必须在监造人员的监督下进行,并对结果进行确认,该质量控制点称为停工待检点。
与之对应的监造方式称为停工见证。
日常巡检点(P点):
日常巡检是指监造人员在生产车间了解加工人员执行工艺规程情况、工序质量状况、各种程序文件的贯彻情况、零部件的加工及组装试验状况、不合格品的处置情况以及标识、包装和设备的发运情况,该质量控制点成为日常巡检点。
与之对应的监造方式称为日常巡检见证。
文件见证项目由监造人员查阅制造厂的检验、试验记录;现场见证项目应有监造人员在场;停工待检项目必须有用户代表或用户委托的监造人员参加,现场检验并签字后,才能转入下道工序;日常巡检项目由监造人员按生产进度每日巡检,并填写监造日志,定期向专业监造工程师提供监造报告。
监造人员在监造过程中根据指定的监造方式及具体的监造要点与制造厂共同把好质量关,在关键见证点见证完成后要及时填写相关质量见证单(附表2),监造人员和制造厂检验员应在质量见证单上签字,监造人员和制造厂各执一份。
监造人员平常与厂家沟通尽量采用书面形式按监造工作联络单(附表3)填写。
监造工作地点:
R点于厂家项目经理办公室和质量控制办公室审查,W点于厂家各加工车间,H点于厂家试组装场地,P点于厂家各相关加工车间。
4.各检查见证点的内容、方法
监造单位将按照上述监造依据派监造人员对生产供货厂家在以下主要方面进行监督、检查、记录归档,并要求生产厂定期或按生产工序各阶段报送有关资料。
监造单位派人参加生产厂的监造工作既不能解除或减轻生产厂按照合同规定承担的责任,也不能替代工厂的产品质量管理与检查和货到工地后的现场质量检验。
4.1质量保证相关文件的见证检查
4.1.1审核施工文件、图纸及施工工艺等质量体系文件。
(1)明确制造厂质量保证管理工作的范围和边界。
(2)审查制造厂质量管理体系、安全、环境、计量认证证书是否在有效期内。
(3)审查制造厂质量手册、程序文件、作业指导书是否满足变压器、电抗器质量管理和产品实现全过程的要求。
(4)审查制造厂质量管理体系运行的有效性,并针对存在的问题提出有关整改建议。
(5)审查生产设备、工器具、检验设备、人力资源、生产环境和管理水平等是否满足生产变压器、电抗器的要求。
(6)审查外购原材料和配件的质量文件以及供应商的资质认证。
4.1.2制造方应指定专人负责施工图纸与相关资料的清点交接工作,应仔细检查、确认图纸资料及设计说明的正确性、审核图纸及资料是否有效、完整、有无缺陷或不符合规定的要求,放样后,应及时标注放样尺寸并提供标有放样尺寸的图纸一套供监造人员及时查阅。
4.1.3监造人员应检查制造方质量保证计划、检验验证计划、生产进度计划及售后服务计划,还应审查制造方的质量保证体系的建立情况和运行有效性。
(1)产品质量计划
产品质量计划包括:
生产能力、工艺技术、资源配置、特殊措施和先进技术应用、质量控制技术验证活动;采购、包装、交付、服务、生产设备管理、测试设备和计量管理内容。
产品质量计划编制内容应满足合同规定及用户的要求,明确为达到所要求的质量而采取的控制手段、工艺、设备(包括测试设备)、工装、资源和技能。
(2)检验验证计划
检验验证计划是制造方以生产全过程的关键工序、关键点、关键部位为检验重点,其中应包括:
1)原材料进厂检验计划:
外观、尺寸、机械性能、化学成分;
2)零部件抽检方案及几何尺寸检验计划;
3)组焊件质量检验计划;
4)包装质量抽检方案与检验计划。
(3)生产进度计划:
检查制造厂根据变压器、电抗器供货明细(按附表4填写)以及交货时间要求制定详细的生产进度计划(按附表5填写)。
1)严格检查制造厂的生产厂的进度计划,并督促执行;
2)检查加工进度计划落实情况,按计划控制,做好计划完成的统计工作;
3)对照厂家制造进度,定期每月对制造厂设备制造进度进行检查,检查生产进度是否符合预期情况,督促被监造单位采取有力措施保证产品按期按质完成。
(4)售后服务计划:
检查制造方按合同编写详细可行的售后服务计划,是否满足工程的要求:
中标方在合同签订后,是否指定负责本工程的项目负责人,负责中标方在工程全过程的各项工作,如工程进度、设计制造、图纸文件、包装运输、现场安装、验收等。
变压器、电抗器在安装过程中、中标方是否派出工地服务代表,及时解决施工过程中的产品质量问题,如发现质量不能满足合同要求,中标方是否进行修正或更换,做好售后服务工作。
4.1.4检查各类技术人员上岗资质证书、复检情况。
各工种的操作人员也应持有相应的资格证书或上岗证书
4.2生产设备、检测设备与条件的见证与监督检查
4.2.1检查主要生产设备使用期、复检期是否在有效期内,生产工艺成熟,生产条件配备情况。
4.2.2检查检测设备使用期、复检期是否在有效期内,检测条件配备情况,检测程序是否规范。
4.2.3检查探伤设备使用期、复检期是否在有效期内,对探伤人员资质进行见证与监督检查。
4.2.4检查生产过程的安全性、和环境影响的符合性。
4.3铁芯检验与质量监督
4.3.1.变压器所用硅钢片是否符合合同中规定的制造厂商。
4.3.2.硅钢片规格型号是否符合图纸和工艺文件要求。
4.3.3.卷料包装是否完好,开卷后查看表面绝缘膜(没有破损,绝缘膜均匀,光泽一致)。
4.3.4.是否有合格证和试验报告。
4.3.5.铁芯各级片料纵剪切时的宽度尺寸\毛刺是否符合图纸和工艺要求(宽度:
按图纸和规范,毛刺<0.025)(见证硅钢片卷料使用记录,铁芯剪切的毛刺高度和尺寸偏差记录)
4.3.6.铁芯各级片料横剪切时的长度尺寸\毛刺是否符合图纸和工艺要求(长度:
按图纸和规范,毛刺<0.025,片数:
按图纸要求)(见证铁芯剪切的毛刺高度和尺寸偏差记录,迭片高度记录)(收集铁芯剪切过程记录)
4.3.7.铁芯叠装打底:
夹件和拉板并处同一平面,绝缘材料和阶梯支撑块布置符合图纸并处同一平面,第一层叠片布置:
接缝<2mm,没有重叠,对角线尺寸正确,铁芯窗口尺寸正确(停止点)。
4.3.8.叠片操作:
接缝<2mm,没有重叠,对角线尺寸正确,铁芯窗口尺寸正确,铁芯端面平整,没有参差不齐,各级叠片厚度符合图纸要求。
(见证叠片过程记录表和铁芯迭装厚度测量记录表)
4.3.9.油道布置:
油道垫条的尺寸\数量和布置位置符合图纸要求,查看所使用的胶水名称和有效期,油道绝缘>50kΩ。
(见证铁芯油道绝缘试验记录)
4.3.10.铁芯绑扎:
支撑垫块安装满足要求;下夹件和拉板按图纸要求放置;无纬带宽度(50mm);绑扎力>392kg,傍轭和上轭的绑扎力油压表压力35Mpa;绑扎道数和位置符合图纸要求;树脂涂装置满足要求,并彻底干燥,内部没有气泡。
(监督点)
4.3.11.铁芯起立与装入下油箱:
检查铁芯应无扭变形;用水平仪测量垂直度(不超过0.3%);表面应无损伤;铁芯在下油箱油池中位置应是对边距相等;螺栓顶紧力矩:
500N,并作防松处理。
(监督点)(收集铁芯叠装过程检验记录)
4.4绕线检验与质量监督
4.4.1.检查纸筒厚度:
设计值±0.5mm;检查纸筒外圆周长:
设计值0,+3mm;检查纸筒长度:
设计值0,-2mm。
(见证)
4.4.2.检查粘接撑条厚度:
设计值±0.2mm;撑条粘好后的直径:
设计值0,+1mm;(内线圈);0,+2mm(外线圈)。
(见证)
4.4.3.检查绝缘件尺寸:
设计值;检查铜线线规:
设计线规。
(见证电磁线的制造厂商是否符合合同要求,并收集合格证和试验报告)
4.4.4.检查绕线旋向和盘数是否与图纸要求相同;测量辐向尺寸:
设计值-1,+2mm;引线的位置\长度\绝缘厚度和支撑是否与图纸要求相同;起头和收头相对设计位置偏差≤±5mm;换位突起部位与设计值+3mm;引线是否按图纸要求进行加强;每层线圈内径:
设计值0,+2mm。
检查引线出头是否包扎到规定的绝缘厚度;同一撑条上的垫块是否在一条线上;内外撑条是否在同辐线上;测量线圈电阻并与设计值进行比较。
(停止点,未经确认后续工慰问团必须停止)
4.4.5.线圈压紧,压紧力:
按图纸要求,测量烘燥前线圈高度(见证记录);测量烘燥后线圈调整后的高度:
按图纸设计值±5mm。
(见证记录)
4.4.6.烘燥后预装前检查线圈换位局部起≤3;绝缘无损伤;纸筒无脱胶\分层和局部变形;油道畅通远杂物;线间无短路。
(停止点)
4.5线圈预装质量监督检查
4.5.1.测量各相序每个线圈的高度与设计值的差值,上下对称调节,记录调整项和调整量。
(见证)
4.5.2.各相序每套装一个线圈时,检查线圈纸筒内径,设计值0,+4mm。
(见证)
4.5.3.按图摆放底部绝缘件(傍站);撑条位置以内撑条为准在同一辐线上(傍站),引线位置按国在底部绝缘上标出的引线位置为准±5mm。
(见证)
4.5.4.线圈在套装中绝缘无损伤;按图摆放顶部绝缘件,不阻油道;顶部绝缘环引线位置正确;顶部引线长度达到规定要求,绝缘厚度≥1mm。
(见证)
4.5.5.预装结束后,检查引线绝缘厚度和长度应符合图纸要求;电气绝缘距离应大于技术要求的最小间隙;垫块不松动;油道进出口没有堵塞;电气过程试验合格。
(停止点)
4.5.6.检查线圈组烘燥前后压紧力(按图纸要求)Mpa;记录线圈组烘燥前后高度,前后相差-5,+3mm;记录线圈高度表;内纸筒无气泡\分层和开裂。
(见证)
4.6器身装配质量监督检查
4.6.1.线圈套装前检查铁芯芯柱间距误差0,+3mm;直度相差0.3%;按图要求检查磁屏的长度\宽度和厚度;支撑垫块处在同一平面上。
(见证)
4.6.2.线圈组套装,低压引线位置符合图纸要求;支撑垫块与下压板之间无间隙;检查内纸筒是否已压装到位。
(见证)
4.6.3.插上轭铁芯,检查各级芯片是否少片;边沿有无损伤;接缝公差0,+2mm;相邻两片之间的高度差≤2mm;铁芯与油道及纸板间的绝缘≥50MΩ。
4.6.4.铁芯接地片安装位置和数量与图弤一致;上铁轭绑扎力矩符合图纸要求(35Mpa);铁芯中心油道在同一直线上;最宽的三级铁芯片之间无间隙;其他各级芯片之间在间隙≯3mm;上压板左右对称;上下垫块排列整齐并在同一线上。
(见证)
4.6.5.线圈组压紧图纸规定的压紧力(中间拉螺杆57.6Mpa,两侧拉螺杆50.8Mpa);所有垫块不松动。
(见证)
4.6.6.过程电气试验测量:
变压比和直流电阻应符合相关要求。
(见证)
4.6.7.分接开关(有载分接开关或无载分接开关)在吊装中无碰撞;分接开关的接线端子的位置与图纸一致。
(见证)
4.6.8.检查引线与电缆(铜排)的压接(焊接)是否有毛刺和铜屑;止\通规检验是否合格;引线绝缘搭接包扎\引线长度和绝缘厚度是否符合图纸要求;电气绝缘距离应大于图纸要求;螺栓紧固是否正确可靠;铁芯绝缘≥20MΩ;(变压比和直流电阻)过程电气试验合格。
(停止点,收集器身装配过程记录)
4.7器身气相干燥质量监督检查
4.7.1.进入烘房后由电脑自动控制。
(见证并收集控制记录)
4.8器身整理质量监督检查
4.8.1.器身出烘房吊装时无损伤和污染;在油压表压力达到35Mpa时紧固所用绑扎带螺栓;油压表压力达到(工艺要求)Mpa时紧固线圈组中间螺杆,油压表达到(工艺要求)Mpa时紧固两侧拉螺杆;电气绝缘距离大于图纸规定的要求;铁芯对地≥200MΩ,铁芯油道绝缘≥50MΩ;露空时间不大于规定的时间。
(停止点)
4.9总装质量监督检查
4.9.1.总装前检查上\下油箱\升高座和油枕是否由合同规定的厂商生产,有无合格证,试验报告。
(见证并收集合格证)
4.9.2.总装前检查下列附件的制造厂商是否符合合同的规定,有无产品合格证和试验报告。
(见证并收集合格证)(有)无载开关;高压套管;中压套管;(高\中压)电流互感器;主油位计;开关油位计;主体瓦斯继电器;开关瓦斯继电器;压力释放阀;绕组温度计;油温度计;冷却风扇。
4.9.3.套管应按供应厂商的说明书要求进行组装,瓷面无损伤,金属部位无缺陷,均压罩正确包裹绝缘,密封件安装正确,引线与箱壁的绝缘距离足够,放气时有少量油渗出。
(见证)
4.9.4.分接开关控制箱安装后,分接开关和操纵机构同步,切换档位指示正确。
(见证)
4.9.5.油温度计和绕组温度计应按供应厂商的说明书安装。
(见证)
4.9.6.压力释放阀和气体继电器按图纸和供应厂商的说明书进行安装。
(见证)
4.9.7.检查铁芯和夹件绝缘≥200MΩ;检查套管引线\器身和油箱壁之间的间隙大于图纸要求;分接开关工作同步,档位正确;风扇转动无阻滞;油枕油位正确;套管之间\套管与油枕之间电气间隙大于图纸要求。
(停止点)
4.10真空注油质量监督检查
4.10.1.抽真空达到0.011Mpa,并保持16小时。
(见证)
4.10.2.真空注油前,检查所注入变压器的油种类符合合同规定要求,并经油样化验合格。
加注油速度应符合规范要求,先2t/4h,后4t/1h。
(见证)
4.10.3.热油循环出口温度70℃,并保持24小时。
(见证)
4.10.4.注油后加压渗漏试验,下部表压0.08Mpa,上部表压0.05Mpa。
两表中只要有一只表达到规定值即可。
各密封处无渗漏,保持24小时表压正常。
(见证)
4.10.5.静放时间大于48小时。
(见证)
4.11出厂电试
4.11.1.根据有关标准和用户特殊要求进行电试,应符合相关标准和最终用户的要求。
(由用户见证)
4.11.2.电试前\后和电试中间抽取的油样化验应合格。
(见证收集油样化验报告)
4.12产品发运
4.12.1.电试合格后箱沿焊接,焊缝饱满,焊缝高度应符合规范要求;焊缝着色探伤应无砂眼\断裂等缺陷;施加压力渗漏试验,箱沿无渗漏。
(停止点)
4.12.2.套管拆卸\包装时瓷套上无损伤;引线固定牢固;变压器本体与组件的色标应与技术协议一致,无流挂现象;铭牌内容与图纸\试验结果一致;充氮后24小时无泄漏;包