小麦制粉研磨资料.docx
《小麦制粉研磨资料.docx》由会员分享,可在线阅读,更多相关《小麦制粉研磨资料.docx(80页珍藏版)》请在冰豆网上搜索。
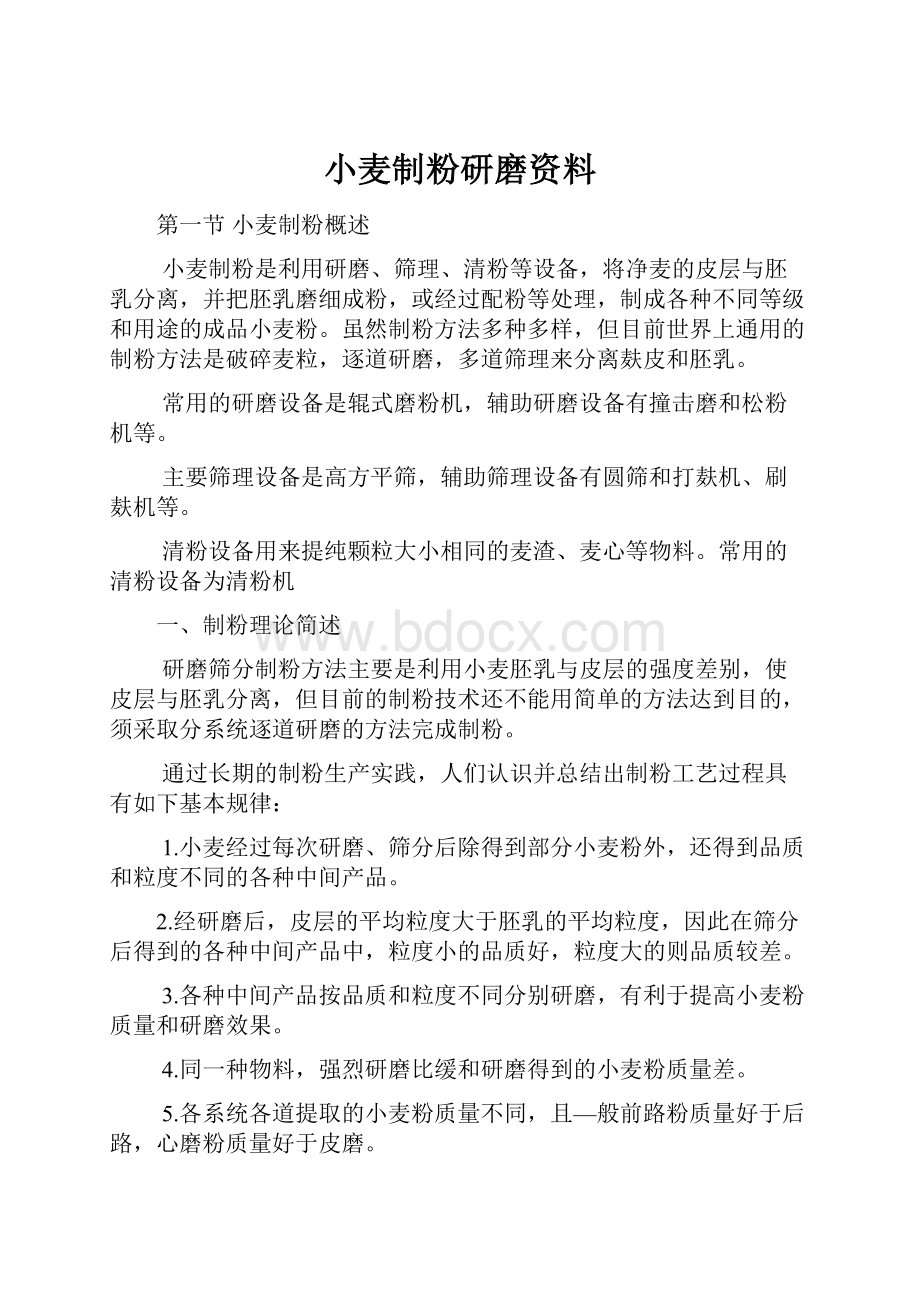
小麦制粉研磨资料
第一节小麦制粉概述
小麦制粉是利用研磨、筛理、清粉等设备,将净麦的皮层与胚乳分离,并把胚乳磨细成粉,或经过配粉等处理,制成各种不同等级和用途的成品小麦粉。
虽然制粉方法多种多样,但目前世界上通用的制粉方法是破碎麦粒,逐道研磨,多道筛理来分离麸皮和胚乳。
常用的研磨设备是辊式磨粉机,辅助研磨设备有撞击磨和松粉机等。
主要筛理设备是高方平筛,辅助筛理设备有圆筛和打麸机、刷麸机等。
清粉设备用来提纯颗粒大小相同的麦渣、麦心等物料。
常用的清粉设备为清粉机
一、制粉理论简述
研磨筛分制粉方法主要是利用小麦胚乳与皮层的强度差别,使皮层与胚乳分离,但目前的制粉技术还不能用简单的方法达到目的,须采取分系统逐道研磨的方法完成制粉。
通过长期的制粉生产实践,人们认识并总结出制粉工艺过程具有如下基本规律:
1.小麦经过每次研磨、筛分后除得到部分小麦粉外,还得到品质和粒度不同的各种中间产品。
2.经研磨后,皮层的平均粒度大于胚乳的平均粒度,因此在筛分后得到的各种中间产品中,粒度小的品质好,粒度大的则品质较差。
3.各种中间产品按品质和粒度不同分别研磨,有利于提高小麦粉质量和研磨效果。
4.同一种物料,强烈研磨比缓和研磨得到的小麦粉质量差。
5.各系统各道提取的小麦粉质量不同,且—般前路粉质量好于后路,心磨粉质量好于皮磨。
二、制粉过程中的系统设置
在粉路中,由处理同类物料设备组成的工艺体系称为系统,通常一个系统中应设置多道处理没备。
制粉过程一般设置皮磨、心磨、渣磨和清粉等系统。
皮磨和心磨系统是制粉过程的两个基本系统,其中每—道都配备一定数量的研磨、筛分设备。
各系统的主要作用是:
1.皮磨系统:
在尽量保持麸皮完整的前提下,剥开小麦,逐道刮净皮层上的胚乳,提取量多质优的胚乳粒和—定质量与数量的小麦粉。
2.渣磨系统:
对前中路提供的连麸胚乳粒进行轻研,使皮层与胚乳分开,从而得到纯净的麦心送往心磨制粉。
3.心磨系统:
将各系统提供的较纯净的胚乳粒,逐道研磨成具有一定细度的小麦粉,并提出麸屑。
4.尾磨系统:
位于心磨系统的中后段,专门处理心磨系统分离出的含有麸屑、质量较次的麦心,从中提出小麦粉。
5.清粉系统:
对皮磨及其他系统前中路提取的麦渣、麦心、粗粉、进行提纯、分级,再分别送往相应的研磨系统处理。
6.配粉系统:
将不同小麦粉分别存放,再按一定比例进行搭配、营养强化和混合,配制成各种不同用途的成品小麦粉。
制粉过程中各系统的流向见图4-1
图4-1现代制粉各系统流向图
三、在制品的分类
在制品是制粉过程中所有中间产品的统称,其分类是由筛理设备来完成,采用不同的筛网提取不同的在制品。
1.筛网
筛网是用于物料分级和提取小麦粉的重要材料,因此筛网的规格、种类及质量对控制各在制品的比例和小麦粉的粗细度有着决定性的影响。
按材料不同,筛网分为金属丝筛网和非金属丝筛网二大类。
根据材料与筛理对象的不同,筛网的编织方法也有区别。
常用的几种编织方法见图4—2。
图4-2常用筛网的编织方法
(1)金属丝筛网金属丝筛网具有强度大、耐磨、不虫蛀等优点,能承受较大的物料流量,使用寿命较长。
其缺点是无吸湿性,易受潮生锈,筛孔易变形。
一般用来筛理较粗大的物料。
金属丝筛网是用镀锌低碳钢丝、软低碳钢丝和不锈钢钢丝编织而成,编织形式如图4—2(c)。
镀锌低碳钢丝筛网颜色光亮,故称白钢丝筛网,多用于粗筛和分级筛。
软低碳钢丝筛网丝黑而粗,强度大,被称作黑钢丝筛网,常用于刷麸机。
不锈钢和准不锈钢丝筛网强度大,筛孔不易变形,延伸性小,使用寿命长,近年来正逐步取代上述两种金属丝筛网。
筛网规格通常以一个汉语拼音字母和一组数字表示其具体型号。
字母表示金属丝的材料:
例如Z表示镀锌低碳钢丝筛网;R表示软低碳钢丝筛网。
字母后面的数字表示每50㎜筛网长度或宽度上的筛孔数。
小麦粉厂也习惯延用英制单位,即以每英寸(1in=0.0254m)长度或宽度上的筛孔数来表示金属丝筛网的规格,并以W作为金属丝筛网的代号。
如20W即表示筛面每英寸长度上有20个孔的金属丝筛网。
小麦粉厂常用的金属丝筛网规格见表4—1,表4-2。
表4-1小麦粉厂常用的镀锌低碳钢丝筛网
表4-2小麦粉厂常用的软低碳钢丝筛网规格
(2)非金属丝筛网非金属丝筛网是指由非金属材料编制的筛网,目前小麦粉厂使用的有尼龙筛网、化纤筛网、蚕丝筛网、和蚕丝与锦纶丝交织筛网。
锦纶丝筛网是用聚酰胺纤维等合成纤维编织而成,具有孔径均匀、网面平挺、强度高、耐磨性好、不堵孔、不并丝、不变形等优点,但吸湿性差,易受湿、热的影响。
蚕丝筛网是用优质蚕丝编织而成,坚韧而有弹性,可在本身长度15%~20%范围内伸缩,保持筛网在筛框上张紧状态;具有吸湿性,可减少水汽在筛格内的凝结现象,从而避免筛孔堵塞;表面经化学处理后,增加了导电能力,避免细小粉粒因静电而粘附于筛面上。
缺点是不耐磨,久用易起毛,使筛理效率下降,若保管不当易受虫蛀,且成本较高。
锦纶与蚕丝交织筛网称锦蚕交织筛网,这种筛网具有锦纶与蚕丝的共同优点,耐磨性好、强度高、延伸性小、筛孔清晰等特点,耐磨强度比蚕丝筛网提高50%~100%,绷装后的筛面张紧不松弛,筛孔不变形,经久耐用。
筛网按编织方法一般分为全绞织(Q)和半绞织(B)两种。
其编织方式如图4-2(a),图4-2(b)。
全绞织筛孔不变形,筛网更牢固,一般用于筛孔较稀的筛网。
半绞织一般用于筛孔较密而小的筛网。
国家标准(GB2014-80)规定了非金属丝筛网的规格型号代号。
见表4-3。
表4-3非金属丝筛网的规格型号代号
原料类别及代号
原料类别及代号
全绞纱组织
Q
半绞纱组织
B
方平组织
F
平绞组织
P
蚕丝C
CQ
CB
CP
锦纶丝J
JQ
JF
JP
锦纶、蚕丝JC
JCQ
注:
1.筛网的规格以每厘米长度的孔数表示。
2.筛网型号按所用原料和织物组织来划分,基本由两个字母组成,第一个字母表示原料类别,第二个字母表示织物组织;由三个字母组成的型号,前两个字母表示原料的类别,第三个字母表示织物组织。
如:
CB50表示每1厘米筛网长度上有50个筛孔的半绞织蚕丝筛网。
JCQ20表示每1厘米筛网长度上有20个筛孔的全绞织锦纶蚕丝筛网。
小麦粉厂也常用英制表示,如GG表示特料筛网,例如54GG表示蚕丝特料筛网,每一维也纳寸(等于1.0375in或0.0264m)长度上有54个筛孔,XX表示双料筛网,规格用号数表示,如10XX表示10号蚕丝双料筛网,每英寸长度上有109个筛孔。
100目表示每英寸筛网长度上有100个筛孔。
常用规格及新老型号对照见表4-4~表4-7。
表4-4全绞织蚕丝筛网型号和规格
表4-5全绞织锦纶蚕丝筛网型号规格
表4-6全绞织锦纶筛网型号规格
表4-7半绞织锦纶蚕丝筛网型号规格
2.在制品的分类
在制品按粒度和品质的不同通常分为以下几种:
麸片—连有胚乳的片状皮层,粒度较大,且随着逐道研磨筛分,其胚乳含量将逐道降低。
麸屑—连有少量胚乳呈碎屑状的皮层,此类物料常混杂在麦渣、麦心之中。
麦渣—连有皮层的大胚乳颗粒。
粗麦心—混有皮层的较大胚乳颗粒。
细麦心—混有少量皮层的较小胚乳颗粒。
粗粉—较纯净的细小胚乳颗粒。
具体分类见表4-8。
表4-8在制品分类
平筛中提取在制品的常用筛面可分为以下几种:
粗筛筛面—皮磨系统中筛孔较大的筛面,其筛上物为麸片。
一般采用金属筛网。
分级筛筛面—将麸片和小麦粉之间的物料,按粒度大小进行分级的筛面,其筛上物通常为麦渣、麦心。
一般采用金属筛网或JC、CQ型筛网。
细筛筛面—属于分级筛范畴,是对略大于小麦粉的细小物料进行分级的筛面,筛孔较小,其筛上物为细麦心。
—般采用JC或CQ筛网。
粉筛筛面—各系统中筛孔最小的筛面,其筛下物为小麦粉,筛上物一般为麦心或粗粉。
—般采用JC或CB型筛网。
平筛中各类筛面的应用与所提取在制品的状态是对应的,如皮磨系统第一道设备处理物料的过程及提取的在制品状态如图4-3所示。
图4-3粉路中1皮磨筛设备处理物料的过程及各在制品的状态
3.在制品的表示方法
在制品粒度的大小通常用分式表示,分子分母分别表示该物料通过和留存筛网的型号规格。
如CQ21/CB30表示穿过CQ21筛面并留存在CB30筛面上的物料粗麦心。
在编制制粉流程流量及质量平衡表时,在制品的数量和质量也用分式表示,分子表示物料占1皮流量的百分数;分母表示物料的质量(灰分%)。
如2皮分出的麸片,记为21.58/3.75表示麸片数量为1皮流量的21.58%,灰分为3.75%。
四、粉路图
制粉流程是将制粉工序组合起来,对入磨净麦按一定的精度等级标准进行加工的生产工艺流程,简称粉路。
粉路图是表达整个制粉工艺过程的工程图。
通常用图形及符号表示各种工艺设备,用箭头、文字或代号表示物料的流动方向。
1.粉路图的内容粉路图主要包括以下内容:
①各类工艺设备的规格、数量、主要技术参数。
②工艺过程中各设备间的联系和各种在制品、产品的流动方向。
③小麦粉或副产品的分类与收集方法,配粉方式与设备。
2.绘制粉路图的要求
①设备及其技术参数必须采用统一的图形或符号。
②在图形符号的—侧要注明系统名称、设备的规格数量和主要技术参数。
磨辊技术特性亦可单独列表说明。
③各种物料的流向用箭头表示,并在箭头处用文字或代号注明去向。
④各系统中各道设备的工艺符号,按制粉过程中的大致顺序,在图中自左向右,自上而下进行绘制。
3.粉路图中的图形符号及代号
粉路图中的图形符号应能简单明确地反映设备的特点。
一般用该设备最具代表性的剖面或一个投影面的示意图来表示。
GB/T12529.3-90规定了粉路图中通常使用的图形符号,(附录二)。
在该标准中还规定了有关代号,见表4-9。
表4-9粉路中常用代号
系统代号
意义
产品代号
意义
设备代号
意义
B
皮磨系统
F
小麦粉
BrF
打麸机
S
渣磨系统
Br
麸皮
BrB
刷麸机
M
心磨系统
G
麦胚
D
重筛
T
尾磨系统
P
清粉
注;1.各系统先后顺序用阿拉伯数字1、2、3……表示。
如1B、2M。
2.各道磨分粗细时,分别在系统代号右下角用小写的c、f表示。
如2BC、1MF。
3.不同品种小麦粉,在代号前用阿拉伯数字区别。
如1F、2F。
4.设备顺序,在相应代号前用阿拉伯数字区别。
如1Br、2D。
四、小麦粉的等级标准
1.通用粉质量标准
我国通用小麦粉的等级主要以加工精度来评定,2005年修订的《小麦粉》国家标准将通用小麦粉与专用小麦粉合并成一个小麦粉标准,按照小麦粉的筋力强度和食品加工适应性能分为3类:
强筋小麦粉—主要作为各类面包的原料或其他原料。
中筋小麦粉—主要用于各类水饺、面条、馒头、油炸类面食品、包子类面食品等。
弱筋小麦粉—主要作为蛋糕和饼干的原料。
由于中筋小麦粉对应的筋力强度和食品加工适应性能较广,将中筋小麦粉又分为强中筋小麦粉和弱中筋小麦粉。
将强中筋和弱中筋小麦粉分成1、2、3、4四个等级,强筋小麦粉和弱筋小麦粉分成l、2、3三个等级。
具体标准见表4-10,表4-11。
表4-10中筋小麦粉质量标准
表4-11强筋小麦粉、弱筋小麦粉质量标准
2.专用粉质量标准
所谓专用粉,就其字面而言就是用于加工某种食品的小麦粉。
这是面粉加工的发展方向。
也是人们日益提高的生活水平的要求。
面粉根据面筋含量可分为高筋面粉(湿面筋含量为35%以上)、中筋面粉(湿面筋含量在28%~34%之间)和低筋面粉(湿面筋含量在28%以下)。
一般而言高筋粉适合做面包;中筋粉适合做馒头、面条等中式食品;低筋粉适合制作饼干和糕点。
对于专用粉而言,加工精度不是其分等的惟一指标,灰分含量、湿面筋含量、面筋筋力稳定时间以及降落值等面团流变特性在分等中占重要地位。
3.营养强化小麦粉
《营养强化小麦粉》是一项全新的国家标准,参考了国际食品法典委员会(CAC)的标准(X)DEXS—TAN152—1985《小麦粉》编写。
要求按照GB14880《食品营养强化剂使用卫生标准》规定的品种和使用量,对铁、锌、钙、尼克酸、维生素BI、维生素B2、叶酸7种营养素进行强化,使其含量和均匀度符合规定的要求。
(其质量标准即将颁布)
第二节小麦及在制品的研磨
一、研磨的任务和研磨效果的评定
1.研磨的任务和要求
研磨的任务是将麦粒碾开,从麸片上刮下胚乳,并将胚乳磨成具有一定细度的小麦粉。
在逐道研磨筛分制粉工艺中,每道研磨设备应选择合理研磨力度,在破碎胚乳的同时,保持皮层的完整,以提取品质较好的小麦粉;同时与筛理设备配合,研磨作用的强弱还将控制各类制品的分类状态,影响后续设备的工作流量,因此,对每一道研磨设备的研磨效果都应有相应的要求。
2.研磨效果的评定
各道磨粉机的研磨效果通常以剥刮率、取粉率或粒度曲线进行评定。
(1)剥刮率剥刮率是指物料由某道皮磨研磨后,经筛理,粗筛筛下物流量占本道进机物料流量的百分比(相对剥刮率),或占1B流量的百分比(绝对剥刮率),在日常生产管理中,常采用相对剥刮率。
在测定除1B外其他皮磨的剥刮率时,由于入磨物中可能已含有较细小的物料,所以实际剥刮率应按下式计算:
K=(4-1)
式中:
K—指定磨粉机的相对剥刮率,%;
A—研磨后物料中粗筛筛下物的含量,%;
B—研磨前物料中已有粗筛筛下物的含量,%。
其中A、B均采用小麦粉专用检验筛测定。
绝对剥刮率(%)=K×本道流量占1皮流量百分比。
正常生产中,为简化测定操作,可不计B,直接用A来反映操作情况。
剥刮率的高低,主要反映皮磨的操作情况,也将影响粉路的流量平衡状态,若某道皮磨的剥刮率高于指标,下道皮磨的流量就会减少,而后续渣、心系统的流量则会增加,造成后续设备工作失常。
(2)取粉率取粉率是指物料经某道研磨后,经筛理,粉筛筛下物流量占本道进机物料流量的百分比(相对取粉率),或占1B流量的百分比(绝对取粉率)。
其测定、计算方法与剥刮率类似。
取粉率是衡量心磨研磨效果的主要指标。
(3)测定用筛网的配备在测定剥刮率或取粉率时,检验筛通常配备与对应平筛同规格的粗筛或粉筛筛网。
但各厂配备的筛网有所不同,为便于厂际间比较,可参考表4-13选用筛网。
表4-13剥刮率和取粉率测定用筛网
系统
粗筛(W)
粉筛
特制一等粉
特制二等粉
标准粉
1B
20
CB39
CB33
CQ21
2B
24
CB42
CB36
CQ23
3~4B
28
CB46
CB39
CQ29
S
CB42
CB36
CQ23
1M
CB39
CB33
CQ21
2M
CB42
CB36
CQ23
3~5M
CB46
CB39
CQ29
6M以后
CB50
CB42
3.粒度曲线
粒度曲线可体现研磨后不同粒度物料的分布规律。
该曲线的横坐标表示筛孔尺寸,单位通常为mm,纵坐标表示对应筛面所有筛上物的累计百分比,横坐标原点对应的筛上物累计量恒等于100%。
测定的方法有两种:
—种是重量法,即在磨下物中取样,通过检验筛筛分后分别称重求得;另一种是流量法,即在粉路测定时测取平筛各出口物料流量后求得。
若平筛的筛理效率较高,两种方法所得曲线应重合;若差别过大则说明平筛的筛理效率低。
在日常生产中通常采用重量法。
如某厂在1B磨下取样120g,经检验,结果见表4-14,由此求得该厂1B粒度曲线,见图4-4。
表4-14某厂1B磨下物筛分结果统计
格数
检验筛网
物料粒度
筛孔宽度/mm
物料
数量/g
筛上物
比例/%
筛上物
累计/%
1
18W
-/18W
-/1.07
78
65
65
2
32W
18W/32W
1.07/0.57
15.6
13
78
3
CQ20
32W/CQ20
0.57/0.338
12
10
88
4
CB42
CQ20/CB42
0.338/0.132
9.6
8
96
5
底板
CB42/-
0.132/-
4.8
4
100
图4-4某厂1B磨粒度曲线
纵坐标的定义为检验筛逐层筛上物的累计百分含量,对于同—种磨下物料,使用不同规格的筛网进行筛理,将结果标定到坐标图上,所得到的点都将分布在同一条连续的曲线上。
曲线的形状、位置与筛网的规格无关,主要取决于磨粉机的研磨效果。
原料的性质及磨辊的表面状态对粒度曲线的形状有影响,原料为硬麦、磨下物中粗颗粒状物料较多时,曲线大多凸起;研磨软麦、磨下物中细颗粒状物料较多时,曲线一般下凹。
由于—般粒度曲线的弯曲度较小,在对磨下物进行粗略的估算时,可将其粒度曲线画成直线。
小麦粉厂制粉效果达到最佳状态时得到的粒度曲线,称为最佳粒度曲线。
通过指定曲线可较准确地反映出对应磨粉机的研磨状态及各在制品的分配情况,也可由设定的在制品数量,根据曲线确定对应的平筛筛网规格。
因此最佳粒度曲线既可指导操作,又是同类粉路技术参数选配的主要参考依据。
如图4-4,粒度18W/32W的物料为13%,粒度32W/JMG52的物料为10%,若研磨状态不变而要求筛分后两者的提取量相等,须将原32W的筛网适当放稀,在图中作辅助线可初选对应筛网。
具体方法如图中虚线:
在图中纵向于两物料等分处,作水平线交粒度曲线于A点,由A点作垂线交于横坐标,得筛孔尺寸为0.64mm,由表4-1,初定筛网型号为30W。
二、研磨工作原理
研磨工作的基本原理是:
通过对物料的挤压、剪切作用,使物料逐步破碎,从皮层将胚乳刮离并磨细成粉。
目前普遍采用的研磨设备为辊式磨粉机。
1.磨粉机工作状况简介
辊式磨粉机最早出现在19世纪初,经过近二个世纪的发展,磨粉机的控制、操作机构等方面进步较快,虽工作机构相似,但在研磨效果的控制性能、稳定性等方面有很大的提高。
图4-5辊式磨粉机工作状况
1-快辊;2-慢辊;3-研磨区;
4-磨上物;5-磨下物
如图4—5,辊式磨粉机的工作机构是一对相向差速转动的等径圆柱形磨辊,其中转速较高的磨辊称为快辊,另一只称为慢辊,两辊的转速比称为速比。
两辊同时接触物料的工作区称为研磨区,由喂料机构将物料均匀地送入研磨区,研磨前的物料称为磨上物,经研磨后的物料称为磨下物。
由于两辊转速不同,辊面加工成特定的形状,两辊对物料产生一定的压力,所以物料在经过研磨区时,受到挤压、剪切、搓撕等综合作用。
由于这些作用在一定范围内可进行调节,故可根据有关指标对物料进行适当的研磨。
2.研磨区的长度
如图4—6所示,物料落入研磨区且两辊恰好同时接触物料时,两辊夹住物料,并开始对物料进行破碎剥刮,此时物料所处位置(A点)称为起轧点。
此后,两辊间距越来越小,最后到达最小间距处,此处(B点)称为轧点,而两辊间的距离称为轧距g。
经过轧点后,物料不再受到研磨。
起轧点与轧点间的距离称为研磨区长度。
对于指定物料,若对应研磨区的长度较长时,物料与辊面接触的时间较长,受到破碎的机会较多,破碎较均匀,研磨效果相对较好。
图4-6磨辊研磨区
由图,根据勾股定律,研磨区长度S为:
S=
展开后,忽略相对较小的量(d2/4-g2/4),得:
S=(4-2)
式中:
S—磨辊研磨区的长度,/m;
D—磨辊直径,/m;
d—物料粒度,一般为粒径,/m;
g—轧距,/m。
由公式4-1知,研磨区长度随磨辊直径的增大而增大,随轧距的增大而减小。
所以在其他条件相同的情况下,磨辊直径较大时,研磨效果较好;当入磨物料粒度较小时,S较小,故心磨物料磨细较困难,宜选用直径较大的磨辊。
S的大小随各系统而异,一般为4~20mm。
3.物料在研磨区中的受力状态
(1)物料通过研磨区的速度物料进入研磨区后,在两辊的夹持下快速向下运动。
由于两辊的速差较大,紧贴物料一侧的快辊运动速度较高,有使物料加速的趋势,而紧贴物料另一侧的慢辊则将对物料的加速起阻滞作用。
如图4—7所示,有Vk>Vw>Vm,的关系。
通常取物料通过研磨区的速度Vw为快慢辊线速的平均值,即:
Vw=(Vk+Vm)/2
由此可知,研磨区中的物料与快、慢辊之间均有明显的相对运动,快辊相对物料向下运动,而慢辊相对物料向上运动,也可以理解为慢辊阻滞物料,快辊对物料进行破碎剥刮。
图4—7研磨区内物料的运动速度
(2)物料在研磨区中的受力状态
图4—8物料受齿辊研磨时的受力状态
① 采用齿辊研磨时物料的受力状态。
用来破碎较粗大物料的磨辊表面通常具有磨齿,见图4-8。
物料进入研磨区后,根据相对运行趋势,快辊向下的齿面施力于物料,而慢辊是向上的齿面对物料施加作用力。
施力于物料的齿面称为前齿面,前齿面与本身齿顶半径的夹角α称前角。
对应后齿面与本身齿顶半径的夹角β称后角。
前齿面对物料有作用力P,因齿面较光滑,P的方向与前齿面垂直。
可将P分解为垂直于两辊中心连线的力P1和平行于两辊中心连线的力P2。
由图4-8知:
P1=Pcos(α+λ)P2=Psin(α+λ)
P2/P1=tg(α+λ)
式中λ角一般较小,且物料在轧点位置时λ角为零,故可忽略其影响,得:
P2/P1=tgα(4-3)
由公式4-2可知,α的大小将影响P1与P2的比值。
因慢辊同时也对物料产生作用,即同时存在P与P′,故P1与P1′对物料起剪切作用,P2与P2′对物料起挤压作用。
当前角α不变、作用力P增大时,P1和P2同时增加,对物料的挤压与剪切作用同时加强,剥刮率和取粉率同时增加。
当前角α减小时,P1相对P2增大,对物料的剪切破碎作用加强,剥刮率增加,磨下物中渣心比例提高,细粉数量减少,皮层易碎,粉中麸星增多,品质可能下降,但因较多地利用了剪切作用,故能以较低的动力消耗处理较高的物料流量。
当前角α增大时,P2相对P1增强,挤压力的作用占主导地位,磨下物料中麸片增大,渣心减少而细粉增多,品质较好,但破碎能力下降,动耗较高,处理流量较低。
因此,前角的大小对研磨效果的影响较大。
②采用光辊研磨时物料的受力状态。
若对物料的剪切作用过强,会导致皮层的过度破碎,而使粉中麸星增多。
为提高小麦粉质量或高等级粉的出粉率,目前多数粉厂在心、渣磨系统使用光辊。
与齿辊比较,光辊可看成α=90°的情况,此时P1=0,P2=P,即直接对物料只有挤压力存在而无剪切作用,如图4-9。
但由于相对运动趋势的存在和光辊面具有一定的粗糙度,两辊与物料间存在较大的摩擦力,即物料在光辊研磨区中,受到挤压与摩擦的综合作用。
因主要由挤压力起作用,光辊研磨物料时,动耗较高,磨下物中麸屑完整,细粉多,粉中麸星少,粉质好。
图4-9物料在光棍研磨区的受力状况
4.剥刮齿数
指定物料在通过齿辊研磨区时,快、慢辊相对其刮过的磨齿数之和称为剥刮齿数。
物料通过研磨区时,若剥刮齿数较多,物料接受剥刮的次数多,对物料的破碎能力增强,剥刮率、取粉率相应较高。
当调小轧距、研磨区的长度增加,物料通过研磨区的时间延长,剥刮齿数亦增加;快慢辊的速