工艺流程.docx
《工艺流程.docx》由会员分享,可在线阅读,更多相关《工艺流程.docx(21页珍藏版)》请在冰豆网上搜索。
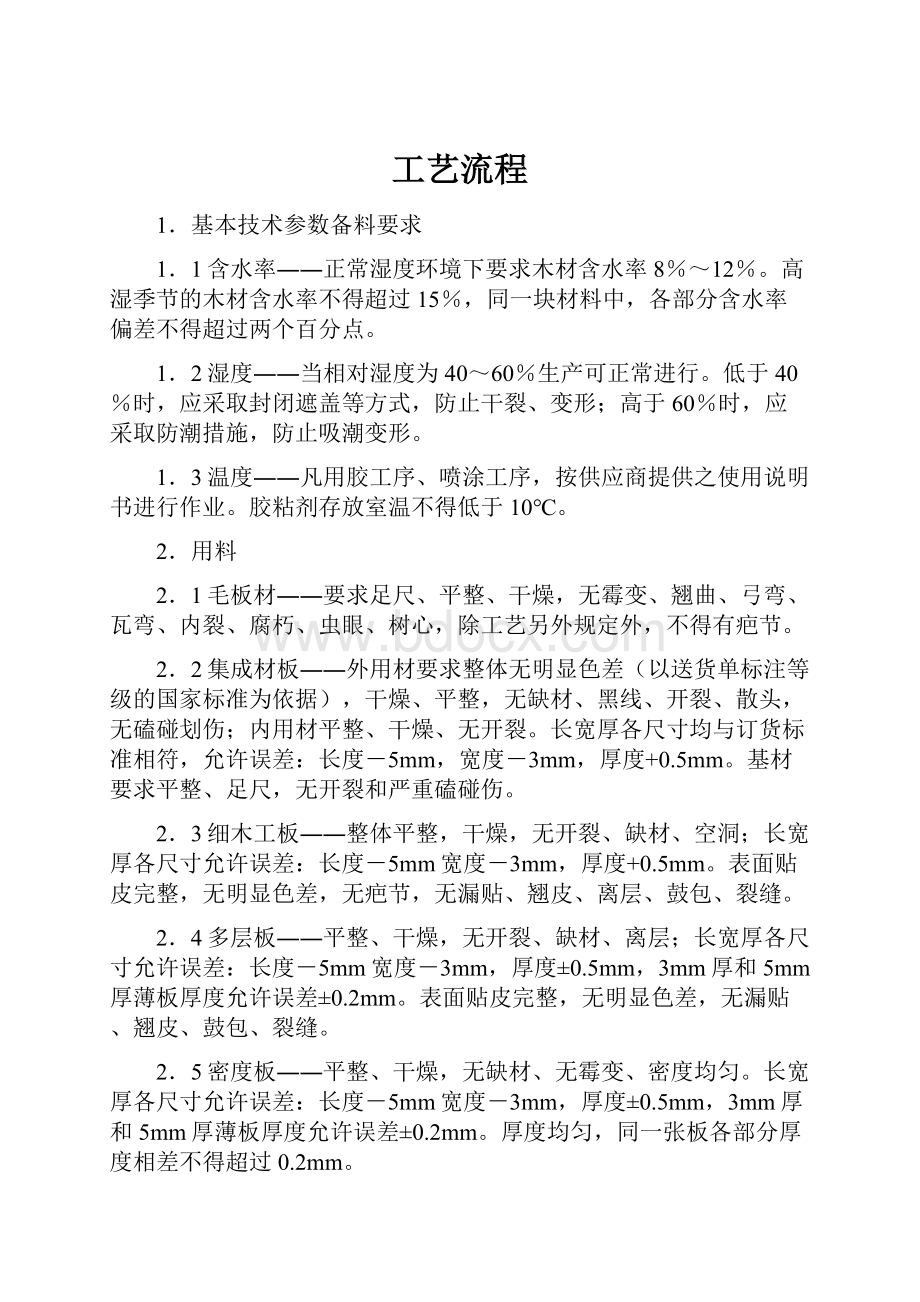
工艺流程
1.基本技术参数备料要求
1.1含水率――正常湿度环境下要求木材含水率8%~12%。
高湿季节的木材含水率不得超过15%,同一块材料中,各部分含水率偏差不得超过两个百分点。
1.2湿度――当相对湿度为40~60%生产可正常进行。
低于40%时,应采取封闭遮盖等方式,防止干裂、变形;高于60%时,应采取防潮措施,防止吸潮变形。
1.3温度――凡用胶工序、喷涂工序,按供应商提供之使用说明书进行作业。
胶粘剂存放室温不得低于10℃。
2.用料
2.1毛板材――要求足尺、平整、干燥,无霉变、翘曲、弓弯、瓦弯、内裂、腐朽、虫眼、树心,除工艺另外规定外,不得有疤节。
2.2集成材板――外用材要求整体无明显色差(以送货单标注等级的国家标准为依据),干燥、平整,无缺材、黑线、开裂、散头,无磕碰划伤;内用材平整、干燥、无开裂。
长宽厚各尺寸均与订货标准相符,允许误差:
长度-5mm,宽度-3mm,厚度+0.5mm。
基材要求平整、足尺,无开裂和严重磕碰伤。
2.3细木工板――整体平整,干燥,无开裂、缺材、空洞;长宽厚各尺寸允许误差:
长度-5mm宽度-3mm,厚度+0.5mm。
表面贴皮完整,无明显色差,无疤节,无漏贴、翘皮、离层、鼓包、裂缝。
2.4多层板――平整、干燥,无开裂、缺材、离层;长宽厚各尺寸允许误差:
长度-5mm宽度-3mm,厚度±0.5mm,3mm厚和5mm厚薄板厚度允许误差±0.2mm。
表面贴皮完整,无明显色差,无漏贴、翘皮、鼓包、裂缝。
2.5密度板――平整、干燥,无缺材、无霉变、密度均匀。
长宽厚各尺寸允许误差:
长度-5mm宽度-3mm,厚度±0.5mm,3mm厚和5mm厚薄板厚度允许误差±0.2mm。
厚度均匀,同一张板各部分厚度相差不得超过0.2mm。
3.零部件生产工艺流程
零部件名称
用 料
工 艺 流 程
柜类
实木
毛板
毛板截断-→刨压-→纵切修边-→拼板-→刨压-→开料(定宽)-→
精截(定长)-→平砂(定厚)-→打孔-→锯弯-→铣型-→雕刻-→
部件打磨-→贴皮-→组装-→精裁-→平砂
半成品
刨压-→开料(定宽)-→精截(定长)-→平砂(定厚)-→
打孔-→锯弯-→铣型-→雕刻-→部件打磨-→贴皮-→组装-→
精裁-→平砂
复合
杉木集成材
集成板截断-→开料-→冷压-→开料(定宽)-→平砂-→冷压(3厘板)-→实木封边-→精截(定长)-→平砂(定厚)-→打孔-→锯弯-→
铣型-→雕刻-→部件打磨-→贴皮-→组装-→精裁-→平砂
芯板
实木
毛板
毛板截断-→刨压-→修边-→拼板-→刨压-→开料(定宽)-→
精截(定长)-→平砂(定厚)-→锯弯-→铣型-→雕刻-→
部件打磨-→贴皮-→组装
复合
细木工
精截(定长)-→开料(定宽)-→锯弯-→部件打磨-→贴皮-→组装
密度板
精截(定长)-→开料(定宽)-→平砂-→锯弯-→铣型-→雕刻-→
部件打磨-→贴皮-→组装
龙骨
杉木集成材
截断-→集成材开料-→冷压-→平砂-→开料(定宽)-→断肩-→
精截(定长)-→平砂(定厚)-→热压
面板
密度板
截断-→开料-→热压-→精裁-→平砂-→贴皮
芯材
桥墩板
截断-→集成材开料-→热压
密度板
截断-→集成材开料-→热压
线条,扣线、
实木
毛板
毛板截断-→刨压-→开料(定宽)-→精截(定长)-→平砂(定厚)-→锯弯-→铣型-→裁口-→雕刻-→部件打磨-→扣线
集成材
截断-→集成材开料-→刨压-→冷压-→开料(定宽)-→精截(定长)-→平砂(定厚)-→锯弯-→铣型-→裁口-→扒槽-→雕刻-→部件打磨-→组装
复合
桐木集成材
毛板截断-→集成材开料-→刨压-→定长-→平砂-→铣型-→裁口-→
部件打磨-→-→组装
密度板
毛板截断-→集成材开料-→刨压-→锯弯-→铣型-→裁口-→
部件打磨-→贴皮-→组装
套板
实木
毛板
毛板截断-→刨压-→修边-→拼板-→刨压-→开料(定宽)-→
精截(定长)-→平砂(定厚)-→加背条-→扒槽-→断肩-→部件打磨
集成材
截断-→集成材开料-→刨压-→平砂-→加背条-→扒槽-→断肩
-→部件打磨
复合
细木工
截断-→开料-→加背条-→扒槽-→断肩-→部件打磨-→贴皮
格条
毛板
毛板截断-→刨压-→开料(定宽)-→
精截(定长)-→平砂(定厚)-→铣型-→部件打磨-→组装
实木集成材
截断-→集成材开料-→刨压-→平砂-→铣型-→部件打磨-→扣线
菱形格
毛板
截断-→集成材开料-→刨压-→平砂-→铣型-→部件打磨-→扣线
4.材料选配
4.1木材板面、
4.1.1无明显色差(可随产品颜色而调节),无腐朽、虫眼、开裂、缺材。
4.1.2实木板材要求无疤节、崩缺,胶缝无黑线。
4.1.3复合板材要求贴皮完好,无漏贴、翘皮、裂纹、起鼓。
需要实木封边的,保证厚度均匀,不得有错层,胶缝无黑线,封边条要足厚,保证铣型后芯材不外露。
4.2芯板
4.2.1实木芯板,要求无疤节、戗碴、腐朽、虫眼、开裂、缺材,胶缝无超标黑线。
同一板件,顺纹顺色,保持木纹顺畅,无明显色差。
实色漆门可允许有不超过直径20mm的疤节间隔1000mm,不限制色差。
4.2.2复合芯板,要求贴皮完好,无漏贴、翘皮、裂纹、起鼓,所用密度板,不得有霉变、翘曲等现象。
4.3雕花板、板面效果――必须用全无直纹材,无白边黑线,同一板件顺纹顺色。
4.4.2复合套板要贴皮完好,无漏贴、翘皮、裂纹、起鼓,不可视面无须贴皮。
所用细木工板材不得有开裂、弯曲。
4.4.3实色漆板面要求无开裂、腐朽、缺材,允许有色差和直径小于20mm的疤节。
4.5木线
4.5.1要求无疤节、戗碴,腐朽、虫眼、开裂、黑线、缺材,拼接材顺纹顺色。
4.5.2复合木线,如果用桐木,要求无腐朽、开裂、缺材。
密度板要求无霉变,贴皮完整,无漏贴、翘皮、裂纹、起鼓,插口条不得有开裂、缺材、疤节。
5.裁断
5.1优先选用下角料和前批次余料,截断时,必须先长后短,去次留优,依次下料。
5.2截断时,长度按下表留出加工余量:
净料长度
余量
小于500mm
10mm
500~1500mm
15mm
大于1500mm
20mm
5.3截断面与直边成90度角
5.4截断后凡要拼板的实木板条,先进行粗刨压,消除轻度变形及厚度差过大现象,再进行纵切、修边。
6.纵切,修边
6.1视板面情况决定加工顺序,凡板面有瓦弯的应先疏开再修边,确保板面平整。
6.2除6.1条情况或单条宽度超出标准宽度外,不得先疏开后修边,必须同时疏、衍。
6.3疏料时,先选择一直边为基准,无直边时,先加工出一直边。
修边时,除胯楞和其它无法使用的缺陷外,每次锯切量不得超过2mm,有胯楞材现象的退回上工序进行第二次加工或作B级材使用。
胯楞材纵切时,要按最窄处加1~2mm定线加工。
6.4除定宽外,不得有四边见角的薄木条出现。
6.5修边前,必须按照板材尺寸加拼板压缩量配出宽度,防止板件定宽时切下不必要的薄木条。
6.6拼板板条单宽不超过100mm。
可视面不得斜向修边、拼板。
7.平刨、压刨
7.1首先检查材料有无弯曲,弯曲较大或使用部位不充许弯曲的必须先取直再进行加工,无法取直的退回前道工序。
7.2翘曲材料,应视其翘曲程度,达不到加工尺寸的,退回前工序,可以使用的,直接压刨。
7.3刨压后的材料,两垂直边为90度,必须两边平行且等厚,不得出现啃头、啃尾、戗碴。
7.4压刨加工必须两面刨光,不得留有锯痕,若因毛板不足尺或局部凹陷而达不到规定厚度时,不得擅自将尺寸减薄,必须请示工艺负责人,经批准后方可调整。
7.5压刨加工时,每次刨削要适量,不得超过3mm。
平刨每次刨削量不得超过1mm。
8.拼板、指接、冷压
8.1拼板前,按照材料标准对板条进行搭配并打好标记,同一工件要顺纹顺色,直纹与山纹不得混拼,有缺陷的拼在一起,统一进行表面处理。
8.2拼异形板(如BS-533上芯板),只拼四周,中间需要挖掉的部分空着(适当留少许余量),以利于挖洞并节省材料。
8.3涂胶必须均匀适量,以胶缝挤出小米粒状胶粒为准。
8.4涂胶后,必须在两分钟之内加压,防止胶液失效。
8.5加压时,要保证胶合面密缝且均衡受压,做到板面平整,错层不超过0.5mm,同时要保证一个端面为直线(做到平、直、严)。
8.6若有板条不平时,用垫块压平或用胶锤敲平,不得用铁锤或锐器敲击。
8.7拼板架或拼台上要及时清除胶粒,保持平整,防止硌伤板件。
8.8保压时间按下表掌握:
环境温度
保压时间
大于20℃
不少于40分钟
20~10℃
不少于60分钟
10~5℃
不少于80分钟
5℃以下不得拼板
8.9卸压后板件要竖立存放,胶缝平行于地面,不得平铺于地面。
8.10卸压后经过养护方可进行后续加工。
养护时间按下表:
环境温度
养护时间
大于20℃
12小时
10~20℃
24小时
0~10℃
36小时
8.11严格按照胶粘剂使用说明书规定的比例调胶,要少调快用,在规定的时间内用完。
禁止使用过期的胶。
注意在不同的季节,温度不同,调胶时固化剂的用量要有所增减。
调胶时,必须向同一方向搅拌。
8.12指接――待梳齿材料要等宽、等厚。
梳齿整齐、完整。
上刀、下刀宽度一致。
同批次梳齿规格一致。
涂胶适量,指接密缝,不得有错层。
指接后的材料须顺直。
可视面径切和弦切不得混接。
8.13冷压――复合板、横撑、抱条,冷压时所用芯材必须等厚,面板比芯材要宽5mm,长度相等。
涂胶适量。
压力和时间按下表控制:
名称
压力(MPa)
时间(小时)
≥20℃
20~10℃
10~5℃
复合产品
12~15
2
4~5
6~8
实木产品
12~15
8.14套板如有加背条,则背条应厚度均匀,粘合后不得有错层,正面不得透钉。
用钉要考虑套板开槽深,免伤锯片。
8.15冬季拼板、胶合,应提前将板条或工件摆放于室温不低于5℃的室内,使表面温度达到5℃以上时方可作业。
9.开料(定宽)
9.1开料时,要做到锯片锋利,切面光滑。
9.2做净尺门时,宽度不加余量。
9.3正常木料宽度加工余量按下表控制:
零件名称
加工余量
门边、上下横
10mm
中横、抱条、芯板、套板、木线条
0mm
10.精截(定长)
10.1截断面与直边成90度角。
10.2长度加工余量按下表控制:
零件名称
加工余量
前后称
10mm
铣端头
3mm
横条、竖条
2mm(有造型者为10mm)
芯板、套板、木线
0mm
11.平砂(定厚)
11.1木质品用前100#--240#砂光;芯板用前120#后240#砂光;套板、木线、扣线可视面用前120#后240#砂光,不可视面用80#砂平。
11.2可视面砂光后,不得有横向砂痕和波浪纹,不得有锯痕、刨痕和其它缺陷,加工完毕,必须防止表面磕、碰、划伤。
11.3复合门边砂光时,要力求两面的密度板等厚。
11.4厚度加工余量按下表控制:
零件名称
加工余量
边、横撑、抱条
1mm
芯板、套板、木线
0mm
12.打孔
12.1先选择一平整完好的面为基准面,把基准面向下放在台面上进行加工。
12.2打孔用的钻头直径应小于圆棒榫直径0.2mm,孔深为榫长的一半加1mm。
12.3待打孔的门边、码头、抱条料必须等厚,确保组装后无错层和尺寸准确。
13.做线(直线,弯线,线裁口)
13.1各种样板每次使用前进行检查,至少每15天全面、彻底检查一次,发现损伤必须进行修补或更新后方可使用。
13.2各种扣线铣型后,表面必须光滑、线条流畅、均匀、无毛刺、崩缺,各部分尺寸与样板一致。
铣型表面如发现有明显色差、黑线、内裂等缺陷,可根据实际情况修补或截断使用。
13.3弯线要保持线条流畅,与模具一致,且与直线形状一致。
13.4扣线裁口应严格按照工艺要求的尺寸进行加工,裁口的两个面应呈90度直角。
14.1待铣型的材料必须等宽、等厚,无开裂、缺材等缺陷。
铣型后必须线条顺畅,表面无疤节、开裂、崩碴等缺陷。
14.2门边、码头、抱条铣型时,注意找表面较好的一面作为基准面,铣型后,靠近基准面一侧的刀型边缘厚度与另一侧允差小于0.5mm。
14.3抱条铣型时先看生产单,再量材料尺寸,保证铣型后为净尺寸。
14.4有造型的要用模具画线后锯弯再铣型。
14.5实木门边码头铣型时,如果是扣线门,选择表面较差的一侧边铣型,不好的地方扣线可以掩盖;如果是装板门,应选择表面较好的一侧边铣型,不好的侧边在精裁时可以裁掉。
14.6铣型后,如存在开裂、缺材、疤节等现象必须进行修补使之达到选配标准方可使用,达不到要求的不得流转。
14.7芯板铣型时,必须保证两面吃刀量相等,铣型后的芯板四周厚度相等,无错层出现。
14.8需要进行锯弯的必须先锯弯再铣型,禁止直接进行铣型加工。
扣线工件锯弯时,锯条走画线中间;铣型工件锯弯时,锯条走画线外侧留3mm加工余量。
14.9推拉门铣扣手和导向槽时,要保证位置正确,深度、宽度合适,内部平整、光滑、无毛刺。
扣手打双面时,正反面要对正,不得错位。
14.10子母门、对开门裁口时,严格按照生产单进行加工,保证裁口方向正确,裁口均匀,无崩碴。
注意上下码头不要颠倒。
15.雕刻――纹理清晰、顺畅,镂铣深浅均匀,线条光滑,无毛刺,同批次同一花形必须造型一致。
清底要平整并打磨光滑,边沿线要圆滑顺畅,不合格的要进行修正。
如有严重色差、黑线、开裂和纹理不同的基板不得使用。
16.贴面(手贴,热压,包覆)
16.1待贴面的材料:
密度板不得有霉变、翘曲、塌陷、缺材,实木不得有毛刺、开裂、缺材。
16.2木皮要柔软,不能太过干燥和潮湿。
16.3木皮无蓝变、黑斑、黑线、孔洞等缺陷,同一工件、同一订单顺纹顺色,拼缝掩层不得超过5mm。
16.4木皮的裁割余量,宽度方向两边各≤5mm,长度方向两端各≤10mm。
16.5涂胶均匀,严格控制涂胶量,不可过多。
第一遍涂胶晾干后,再进行第二遍涂胶并贴皮。
16.6手贴时的熨烫时间要适度并有一定压力,保证贴皮平整,纹理顺畅,无缺皮、翘皮、裂纹、起鼓。
有拼缝的不得离缝。
16.7热压操作时,压机温度需达到120℃~130℃。
16.8贴皮后需稍晾几分钟再热压,晾干时间按下表控制:
环境温度
晾干时间
20℃以上
10~15分钟
5~20℃
15~20分钟
16.9压力和时间按下表控制:
名 称
压力(MPa)
时间(分钟)
复合门贴皮
10
10~12
平板门合门
12~16
20
平板贴皮
8~10
10~12
16.10包覆机的上下温度和时间要严格按工艺要求进行操作,不得随意变更,以保证贴皮质量。
17.零件打磨、组装、精裁、平砂
17.1组装前,对组装后不易打磨的零部件或位置进行打磨,使之达到白坯标准方可进行组装。
17.2门边与码头、抱条组装前,胶合部位和圆棒榫必须均匀涂胶,胶量要适当,挤出的胶必须在半干状态时清掉,不得遗留胶痕;组装过程中禁止使用铁锤或利器直接敲击部件;组装后,胶合部位必须严密、平整,无错层。
17.3装芯板时,海绵条应放置均匀,确保芯板、雕花板位置居中,上下左右横平竖直。
如果是复合芯板,白漆门需先用白漆涂边10~20mm。
17.4在组装台上,要保持门扇整体平整,如有多节抱条,必须保持顺直。
不可挤压过度,对角线相差不得超过2mm,翘曲不超过2mm。
17.5缷压后,要养护12小时以上,方可进行精裁净尺。
要四周裁条,不得只在一边精裁净尺。
精裁后,要保证两侧门边等宽。
17.6精裁以后的门扇,对角线相差不得超过2mm。
17.7平砂时,在保证整体厚度的前提下,先砂凸面,以提高表面质量。
贴皮面不得砂穿暴露基材。
17.8平砂时使用180#~240#砂带,砂光完成后,表面不得有锯痕和波浪纹,保证边角完整。
17.9复合门平砂时,要做到两面密度板等厚,以防变形。
18.扣线,圈玻璃
18.1扣线过程中,必须防止表面出现划伤、碰伤、硌伤。
18.2涂胶量要适当,挤出的胶必须在半干状态时清掉,不得遗留胶痕。
18.3扣线斜接部位要密缝,不得出现劈裂、崩碴,扣线与门边、码头、抱条胶合不得有缝隙。
18.4使用钉枪时,一般枪距为150~200mm,禁止在一处集中打钉。
枪钉打穿、打偏的必须立即拔出,修补钉眼。
禁止流入下道工序。
19.检修、
19.1首先根据图纸检查各部位尺寸,门型、款式、材质、玻璃等均符合生产单要求。
19.2各连接部位无缝隙、无崩碴,各芯板无松动,各抱条、扣线顺直。
19.3眼皮线或扣线无凹凸、钉眼、边角、无缺损,贴皮完好,工艺缝深度、宽度均匀、顺直。
19.4各尺寸允许误差按下表检验:
名称
允许偏差mm
检验方法
套板、门扇厚度
±0.5
钢尺,千分尺
门套高、宽
+1.5 ±0.5
钢尺
门扇高、宽
-1.5 -1
钢尺
门扇对角线
≤2
钢尺(量外角)
门扇表面平整度
≤2
1米靠尺和塞尺
门扇翘曲度
≤2
塞尺
19.5表面效果按下表进行检验:
缺陷名称
缺陷范围
套板
门边码头
芯板
麻点
直径1mm以下,距离30mm
不限
3
6
麻面
均匀颗粒,手感不刮手
不限
划伤
不允许
不允许
压痕
不允许
不允许
起鼓
粘贴不牢固
不允许
褶皱
饰面重叠
不允许
缺皮
不允许
不允许
翘皮
不允许
不允许
离缝
连接缝隙
不允许
20.涂装(白坯打磨,打油磨,喷底漆,喷面漆)工艺要求
20.1检验合格的白坯门,应先补土,再用180#~240#砂纸打磨横茬和未经平砂的部位,然后用320#砂纸精细打磨一遍。
打磨后的白坯不得有钉眼、波浪纹、砂痕、碰伤、划伤及其它未处理好的缺陷,不得有尖锐棱角和木纤维,手感平整、光滑、细腻;边角棱不得走形。
20.2白坯打磨必须顺纹理进行,避免表面出现横向砂纹。
20.3复合门不得将贴皮砂透,不得有翘皮,如有起鼓现象立即用白胶处理好。
20.4打磨后的白坯进行吹灰检验合格后,先进行封闭(含芯板铣型截面),根据工艺要求进行着色修色,着色后的表面颜色必须均匀一致,不得有色差、花色和漏色现象。
20.5喷底漆时,应走枪均匀,保证漆膜丰满,避免漏喷或出现挂流、桔皮、泛白等现象。
20.6喷过底漆,完全干燥的产品,须经检查修补后,方可进行砂磨。
一遍底漆进行240#砂磨,二遍底漆和三遍底漆进行320~400#砂磨。
砂磨时必须注意边、角、棱,避免砂透露白。
20.7底漆打磨的产品表面无光(45°斜视无亮点),手感平整、光滑、细腻,扣线与门边、扣线与芯板、扣线与扣线无缝隙,连接完好,工艺缝均匀顺直,雕花的线条顺畅、光滑,板底平整,无砂透现象,整体表面无砂痕,波浪纹。
20.8涂装车间必须保持清洁,防止灰尘,杂物污染产品。
20.9面漆调色需与色板对照,保持各批次一致。
喷涂后质量检验按下表:
名称
要求
漆膜划痕
不允许
漆膜鼓泡
不允许
漏漆
不允许
污染(包括凹槽线型套色部分)
不允许
针孔
实色漆,不限;全封闭面漆不允许
表面漆膜皱皮
不允许
表面颗粒
门中线以上不允许,中线以下每面不超过3粒。
套板、脸线每面不超过3粒。
凹槽线型部分
平整、光滑、细腻
套色线型结合部分塌边
套色线型分界线流畅,均匀,一致
色差
目测不明显,与色板一致
21.检验,包装
21.1检查门型、订单号、款式、材质、颜色、玻璃型号、正反面等与生产单相符,将商标和绿色环保标志等正确粘贴在指定位置。
21.2整个产品表面平整,光滑,细腻,无泛白,失光,挂流,桔皮,气泡,颗粒、针孔,微缝和腻子下陷等缺陷。
21.3油漆后装玻璃时,要注意轻拿轻放,避免破碎,有花纹的玻璃要注意花型和正反面,不得混装、误装。
安装后要牢固,平整,钉孔必须修补好。
两层玻璃内的格条安装前必须擦拭干净,不得有灰尘。
21.4包装时,先将门表面擦拭干净,边角、玻璃和雕花处不得有灰尘存在。
覆膜必须能将门整体包裹,雕花和玻璃处加放泡沬板并用胶带固定,大块玻璃需用硬板包装以防破碎。
门边必须加装护角方可外包纸箱。
封箱带要粘贴牢固,不得出现翘头脱落现象,套板和护角类必须成套包装,禁止混包。
21.5一包内有多件时,各部件之间必须有间隔防护,避免相互碰撞划伤。
21.6五金件单独包装,严禁与套板或护角等木质产品混包。
以免硌伤产品表面。
21.7每件产品包装完成后,应及时填写装箱单、地址、订单号等资料,避免混乱。
要求加盖印章的必须按要求加盖。
有玻璃的要注明“小心玻璃”等字样,防止途中破损。
23.附则
23.1概念与术语
23.1.1可视表面――可直接看到的面,如门的正反面和侧面、套板正面和侧面、木线的正面,在所有的表面中,可视表面最为重要,成品不允许有任何未经处理或处理不到位的缺陷。
23.1.2不可视表――处于不可见位置的表面,如门的上下端面、套板和木线的反面、护角的内侧面,此类表面要求较低,允许适当的缺陷存在。
23.1.3矿物线(黑线、黑斑)――楸木在生长过程中自然形成,有线状条状团状等,大多形状不规则,矿物线对材料物理性能无影响。
但影响美观,受用户投诉较多,生产中应按下表选配及修补。
零部件
标准
木线、雕花板
线状的长度不超过20mm,条状的长×宽不超过20×2,团
状的不超过10mm2其它型状依以上标准掌握,每一零部件
仅限一处。
其它
线状的长度不超过50mm,条状的长×宽不超过50×3,团
状的不超过15mm2其它型状的依以上标准掌握,每一零部
件上不超过两处。
在加工过程中应注意,凡在门中线以上部位,应从严掌握,尽量避免使用。
确实无法避免的,必须在标准之内;门中线以下部位则可适度放宽。
不论在哪个部位,凡超过标准的,必须进行挖补,并做到顺纹顺色。
23.1.4白边――木材的边部发白部分,以楸木为多。
白边对木材的物理性能影响不大,只是稳定性稍差。
但对美观性影响很大。
为节省木材,在零部件加工过程中,除雕花板、木线之外,均可保留。
但涂装时,必须先进行修色,使之与相邻部位颜色一致。
方可进行涂装。
23.1.3内裂――由于干燥不当或受外力作用,木材表面或内部出现裂纹,内裂对家具表面质量影响极大,原则上必须在备料工序锯开或锯掉,但由于细微裂纹在涂装前不易发现,或在生产过程中变粗变深,所以难以完全避免,可采用以下方法处理:
如果是浅表性的,且长度在100mm以内的,可用刻刀划开,加胶插入木皮,并用腻子修补后磨平,很细微的,可在底漆后点502胶加腻子填平,磨平修色后使用,裂透的或在面板端头出现较粗较深的,一般不得使用。
23.1.4开裂、散头、黑线――拼板时压力不足,或衍缝不密合,导致胶缝裂开或沿胶缝出现的黑线。
开裂或黑线对质量影响极大,各道工序如发现开裂或黑线,不得继续加工,应退回备料重新拼板。
散头是开裂发生在板缝头、尾,处理方法相同。
23.1.5缺材――零部件某一部位局部缺少或崩掉或脱落即造成缺材。
如已出现必须进行修补或填平。
23.1.6瓦弯――木材沿截面方向发生的弯曲。
瓦弯料不得直接修边、拼板,应先疏开,确保板面平整。
23.1.7弓形弯――木材纵向弯曲为弓形弯。
如轻微的弓形弯,不影响修边拼板,如弯曲度过大,则必须热烘取直后方可使用。
23.1.8翘曲――是指木材板件不