冷水机组全寿命周期.docx
《冷水机组全寿命周期.docx》由会员分享,可在线阅读,更多相关《冷水机组全寿命周期.docx(59页珍藏版)》请在冰豆网上搜索。
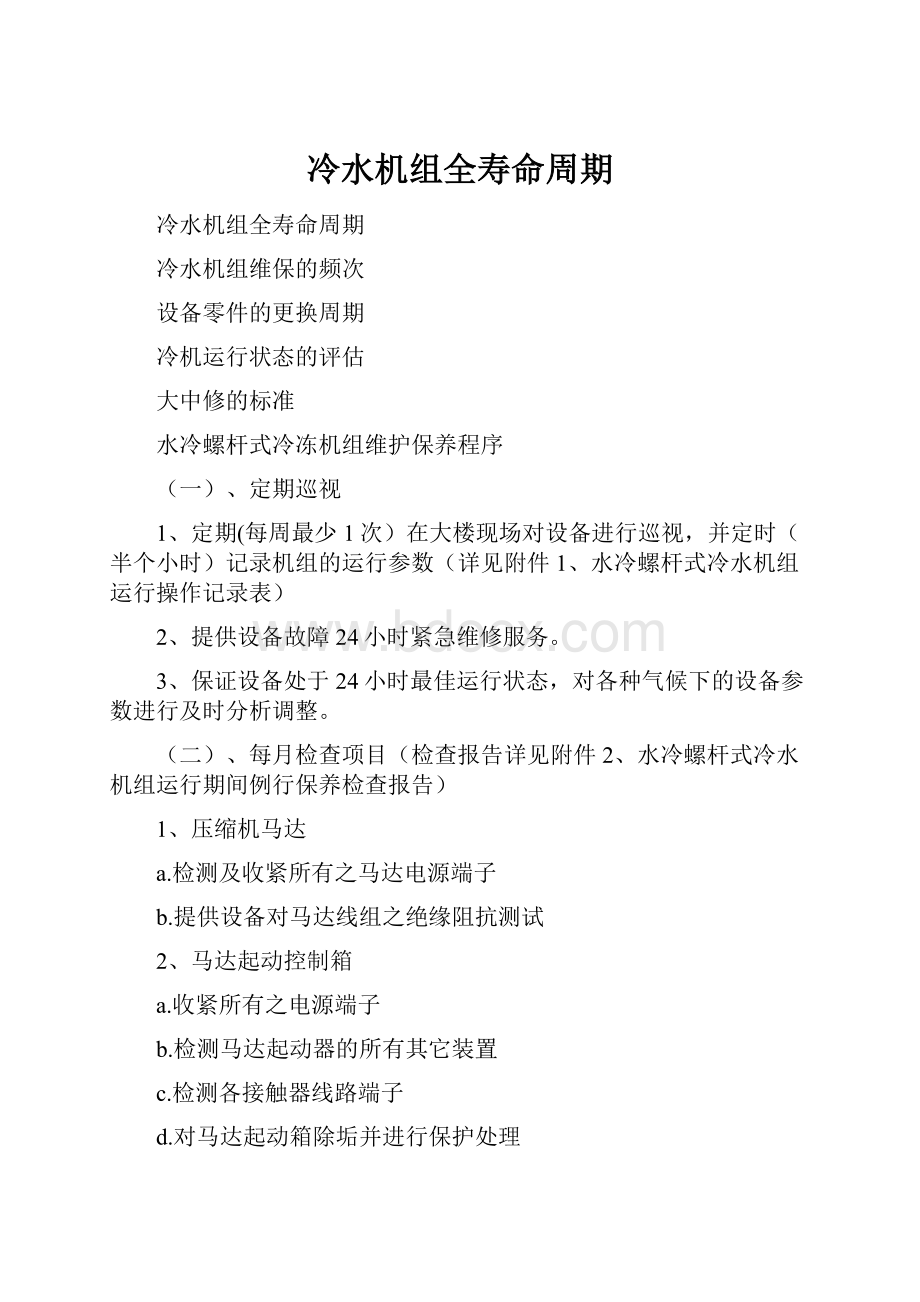
冷水机组全寿命周期
冷水机组全寿命周期
冷水机组维保的频次
设备零件的更换周期
冷机运行状态的评估
大中修的标准
水冷螺杆式冷冻机组维护保养程序
(一)、定期巡视
1、定期(每周最少1次)在大楼现场对设备进行巡视,并定时(半个小时)记录机组的运行参数(详见附件1、水冷螺杆式冷水机组运行操作记录表)
2、提供设备故障24小时紧急维修服务。
3、保证设备处于24小时最佳运行状态,对各种气候下的设备参数进行及时分析调整。
(二)、每月检查项目(检查报告详见附件2、水冷螺杆式冷水机组运行期间例行保养检查报告)
1、压缩机马达
a.检测及收紧所有之马达电源端子
b.提供设备对马达线组之绝缘阻抗测试
2、马达起动控制箱
a.收紧所有之电源端子
b.检测马达起动器的所有其它装置
c.检测各接触器线路端子
d.对马达起动箱除垢并进行保护处理
e.检测马达接线端子温度
f.检测各接触器接点
g.保护性的处理各接触器接点
3、润滑系统
a.检测油槽油位是否正常(运转中)
b.检测油温控制传感器
4、控制及保护电路
a.检测及校正低温传感器
b.检测及调整高压开关
c.检测及校正高压传感器(选择配备)
d.检测冷却水及冰水温度传感器
e.检测及调整冷却水及冷冻水流量开关
5、冷凝器
a.检测水及冷媒之温差并调整
b.检测冷媒饱和压力传感器
6、蒸发器
a.检测水及冷媒之温差并调整
b.检测及校正冷媒蒸发压力
7、一般系统检查
a.检测SLIDEVALVE之功能
b.检测不正常之噪音,振动及高温
c.检测及报告机组之温度计及压力表d.运转主机,检查及报告其操作状况
(三)每年服务项目(通常在机组冬季停机后或夏季开机前进行1次)
(检查报告详见附件3、水冷螺杆式冷水机组年检报告)
1、压缩机马达
a.检测及收紧所有之马达电源端子
b.提供设备对马达线组之绝缘阻抗测试
2、马达起动控制箱
a.收紧所有之电源端子
b.检测马达起动器的所有其它装置
c.检测各接触器线路端子
d.对马达起动箱除垢
e.检测马达接线端子温度
f.检测各接触器接点
g.保护性的处理各接触器接点
3、润滑系统
a.进行润滑油验酸化验一次
b.根据油化验结果确定是否更换压缩机润滑油(物料须另行报价)
c.检测油槽油位是否正常(运转中)
d.更换压缩机油过滤器(物料须另行报价)
e.检测油温控制传感器
4、控制及保护电路
a.检测及校正低温传感器
b.检测及调整高压开关
c.检测及校正高压传感器(选择配备)
d.检测冷却水及冰水温度传感器
e.检测及调整冷却水及冷冻水流量开关
f.校正及调整主机设定参数
5、冷凝器
a.检测水及冷媒之温差
b.检测冷媒饱和压力传感器
c.采用先进的设备对冷凝器进行化学及机械处理。
6、蒸发器
a.检测水及冷媒之温差
b.检测及校正冷媒蒸发压力
7、开机运转测试
a.检测马达线圈温度传感器
b.检测SLIDEVALVE之功能
c.检测冷媒过滤器温差
d.检测不正常之噪音,振动及高温
e.检测及报告损坏之零件
f.检测及报告其操作状况
离心式制冷机组的维护保养
(一)离心式制冷压缩机启动前的准备工作
1.压力检漏试验
压力检漏是指将干燥的氮气充人离心式制冷压缩机的系统内,通过对其加压来进行检漏的方法。
其具体操作方法是:
(1)充入氮气前关闭所有通向大气的阀门。
(2)打开所有连接管路、压力表、抽气回收装置的阀门。
(3)向系统内充入氮气。
充人氮气的过程可以分成两步进行。
第一步先充人氮气,至压力为0.05~0.1MPa时停止,检查机组有无大的泄漏。
确认无大的泄漏后,再加压。
第二步对于使用R134a为制冷剂的机组,可加压至1.2MPa左右。
若机组装有防爆片装置的,则氮气压力应小于防爆片的工作压力。
充入氮气工作结束后,可用肥皂水涂抹机组的各接合部位、法兰、填料盖、焊接处,检查有无泄漏,若有泄漏疑点就应做好记号,以便维修时用。
对于蒸发器和冷凝器的管板法兰处的检查,应卸下水室端盖进行检查。
在检查中若发现有微漏现象;为确定是否泄漏,可向系统内充入少量氟利昂制冷剂,使氟利昂制冷剂与氮气充分混合后,再用电子检漏仪或卤素检漏灯进行确认性检漏。
在确认机组各检测部位无泄漏以后,应进行保压试漏工作,其要求是:
在保压试漏的24h内.前6h机组的压力下降应不超过1%,其余18h应保持压力稳定。
2.机组的干燥除湿
在压力检漏合格后,下一步工作是对机组进行干燥除湿。
干燥除湿的方法有两种:
一种为真空干燥法,另一种为于燥气体置换法。
真空干燥法是用高效真空泵将机组内压力抽至666.6~1333.2Pa(5~10mmHg)的绝对压力,此时水的沸点降至10℃以下,使水的沸点远远低于当地温度,造成机组内残留的水分充分汽化,并被真空泵排出。
干燥气体置换法的具体方法是:
利用高真空泵将机组内抽成真空状态后,充人干燥氮气,促成机组内残留的水分汽化,通过观察U形水银压力计水银柱高度的增加状况,反复抽真空充氮气2~3次,以达到除湿目的。
3.真空检漏试验
根据《离心式冷水机组技术条件)(JB/T3355—91)标准中的规定,机组的真空度应保持在1333Pa(10mmHg)的水平。
真空检漏试验的操作方法是:
将机组内部抽成绝对压力为2666Pa的状态,停止真空泵的工作,关闭机组连通真空泵的波纹管阀,等待l~2h后,若机组内压力回升,可再次启动真空泵抽空至绝对压力2666Pa以下,以除去机组内部残留的水分或制冷剂蒸气。
若如此反复多次后,机组内压力仍然上升,可怀疑机组某处存在泄漏,应重做压力检漏试验。
从停止真空泵最后一次运行开始计时,若24h后机组内压力不再升高,可认为机组基本上无泄漏,可再保持24h。
若再保持24h后,机组内真空度的下降总差值不超过1333Pa,就可认为机组真空度合格。
若机组内真空度的下降超过1333Pa,则需要继续做压力检验直到合格为止。
4.充灌冷冻润滑油
离心式制冷压缩机在压力检漏和干燥处理工作程序完成以后,在制冷剂充灌之前进行冷冻润滑油的充灌工作。
其操作方法是:
(1)将加油用的软管一端接油泵油箱(或油槽)上的润滑油充灌阀上,另一端的端头上用300目铜丝过滤网包扎好后,浸入油桶(罐)之中。
开启充灌阀.靠机组内、外压力差将润滑油吸入机组中。
(2)对使用R123机组,初次充灌的润滑油油位标准是从视油镜上可以看到油面高度为5~10mm的高度。
因为当制冷剂充入机组后,制冷剂在一定温度、压力下溶于油中使油位上升。
机组中若油位过高,就会俺没增速箱及齿轮,造成油溅,使油压剧烈波动,进而使机组无法正常运行。
(3)冷冻润滑油初次充灌工作完成后,应随即接通油槽下部的电加热器,加热油温至50~60℃后,电加热器投人“自动”操作。
润滑油被加热以后,溶入油中的制冷剂会逐渐溢出。
当制冷剂基本溢出后,油位处于平衡状态时,润滑油的油位应在视镜刻度中线±5mm的位置上。
若油量不足,就应再接通油罐,进行补充。
(4)进行补油操作时,由于机组中已有制冷剂,使机组内压力大于大气压力,此时,可采用润滑油充填泵进行加油操作。
5.充灌制冷剂
离心式制冷压缩机在完成了充灌冷冻润滑油的工作程序后,下一步应进行制冷剂的充灌操作,其操作方法是:
(l)用铜管或PVC(聚氯乙烯)管的一端与蒸发器下部的加液阀相连,而另一端与制冷剂贮液罐顶部接头连接,并保证有好的密封性。
(2)加氟管(铜管或PVC管)中间应加干燥器,以去除制冷剂中的水分。
(3)充灌制冷剂前应对油槽中的润滑油加温至50~60℃。
(4)若在制冷压缩机处于停机状态时充灌制冷剂,可启动蒸发器的冷媒水泵(加快充灌速度及防止管内静水结冰)。
初灌时,机组内应具有0.866×105Pa以上的真空度。
(5)随着充灌过程的进展,机组内的真空度下降,吸入困难时(当制冷剂已浸没两排传热管以上时),可启动冷却水泵运行,按正常启动操作程序运转压缩机(进口导叶开度为15%一25%,避开喘振点,但开度又不宜过大),使机组内保持0.4×l05Pa的真空度,继续吸入制冷剂至规定值。
在制冷剂充灌过程中,当机组内真空度减小、吸入困难时,也可采用吊高制冷剂钢瓶,提高液位的办法继续充灌,或用温水加热钢瓶。
但切不可用明火对钢瓶进行加热。
(6)充灌制冷剂过程中应严格控制制冷剂的充灌量。
各机组的充灌量均标明在《使用说明书》及《产品样本》上。
机组首次充入量应约为额定值的50%左右。
待机组投人正式运行时,根据制冷剂在蒸发器内的沸腾情况再作补充。
制冷剂一次充灌量过多,会引起压缩机内出现“带液”现象,造成主电动机功率超负荷和压缩机出口温度急剧下降。
而机组中制冷剂充灌量不足,在运行中会造成蒸发温度(或冷媒水出口温度)过低而自动停机。
6.负荷试机
负荷试机的目的主要是检查机组和对其技术性能进行调整。
负荷试机前的检查及准备工作的内容是:
(1)检查主电源、控制电源、控制柜、启动柜之间的电气线路和控制线路,确认接线正确无误。
(2)检查控制系统中各调节项目、保护项目、延时项目等的控制设定值,应符合技术说明书上的要求,并且要动作灵活、正确。
(3)检查机组油槽的油位.油面应处于视镜的中央位置。
(4)油槽底部的电加热器应处于自动调节油温位置,油温应在50~60℃范围内,点动油泵使润滑油循环,油循环后油温下降应继续加热使其温度保持在50~60℃范围内,应反复点动多次,使系统中的润滑油温超过40℃以上。
(5)开启油泵后调整油压至0.2~O.3MPa之间。
(6)检查蒸发器视液镜中的液位,看是否达到规定值。
若达不到规定值,就应补充,否则不准开机。
(7)启动抽气回收装置运行5~10min,并观察其电动机转向。
(8)检查蒸发器、冷凝器进出水管的连接是否正确,管路是否畅通,冷媒水、冷却水系统中的水是否灌满,冷却塔风机能否正常工作。
(9)将压缩机的进口导叶调至全闭状态,能量调节阀处于“手动”状态。
(10)启动蒸发器的冷媒水泵,调整冷媒水系统的水量和排除其中的空气。
(11)启动冷凝器的冷却水泵,调整冷却水系统的水量和排除其中的空气。
(12)检查控制柜上各仪表指示值是否正常,指示灯是否亮。
(13)抽气回收装置未投入运转或机组处于真空状态时,它与蒸发器、冷凝器顶部相通的两个波纹管阀门均应关闭。
(14)检查润滑油系统,各阀门应处于规定的启闭状态,即高位油箱和油泵油箱的上部与压缩机进口处相通的气相平衡管应处于贯通状态。
油引射装置两端波纹管阀应处于暂时关闭状态。
(15)检查浮球阀是否处于全闭状态。
(16)检查主电动机冷却供、回液管上的波纹管阀,抽气回收装置中回收冷却供、回液管上波纹管阀等供应制冷剂的各阀门是否处于开启状态。
(17)检查各引压管线阀门、压缩机及主电动机气封引压阀门等是否处于全开状态。
负荷试机的操作程序:
(1)启动冷却水泵和冷媒水泵。
(2)打开主电动机和油冷却水阀,向主电动机冷却水套及油冷却器供水。
(3)启动油泵,调节油压,使油压(表压)达到2~3MPa以上。
(4)启动抽气回收装置。
(5)检查导叶位置及各种仪表。
(6)启动主电动机,开启导叶,达到正常运行。
在确认机组一切正常后,可停止负荷试机,以便为正式启动运行做准备。
其停机程序是:
(1)停止主电动机工作,待完全停止运转后再停油泵;
(2)停止冷却水泵和冷媒水泵,关闭供水阀;
(3)根据需要接通油箱的电加热器或使其自动工作,保持油温在50~60℃范围内。
以便为正式运行做准备。
(二)离心式压缩机的开机操作
离心式压缩机的启动运行方式有“全自动”运行方式和“部分自动”即手动启动运行方式两种。
离心式压缩机无论是全自动运行方式或部分自动-手动运行方式的操作,其启动连锁条件和操作程序都是相同的。
制冷机组启动时,若启动连锁回路处于下述任何一项时,即使按下启动按钮,机组也不会启动,例如:
导叶没有全部关闭;故障保护电路动作后没有复位;主电动机的启动器不处于启动位置上;按下启动开关后润滑油的压力虽然上升了,但升至正常油压的时间超过了20s;机组停机后再启动的时间未达到15min;冷媒水泵或冷却水泵没有运行或水量过少等。
当主机的启动运行方式选择“部分自动”控制时,主要是指冷量调节系统是人为控制的,而一般油温调节系统仍是自动控制,启动运行方式的选择对机组的负荷试机和调整都没有影响。
机组启动方式的选择原则是:
新安装的机组及机组大修后进人负荷试机调整阶段,或者蒸发器运行工况需要频繁变化的情况下,常采用主机“部分自动”的运行方式,即相应的冷量调节系统选择“部分自动”的运行方式。
当负荷试机阶段结束或蒸发器运行的使用工况稳定以后,可选择“全自动”运行方式。
无论选择何种运行方式,机组开始启动时均由操作人员在主电动机启动过程结束达到正常转速后,逐渐地开大进口导叶开度,以降低蒸发器出水温度,直到达到要求值,然后将冷量调节系统转人“全自动’,程序或仍保持“部分自动”的操作程序。
1.离心式压缩机启动的操作方法
(1)启动操作。
就地控制机组时,按下“清除”按钮,检查除“油压过低”指示灯亮外,是否还有其他故障指示灯亮。
若有就应查明原因,并予以排除。
集中控制机组时,待“允许启动”指示灯亮时,闭合操作盘上的开关至启动位置。
(2)启动过程监视与操作。
在“全自动”状态下,油泵启动运转延时20s后,主电动机应启动。
此时应监听压缩机运转中是否有异常情况,如发现有异常情况就应立即进行调整和处理,若不能马上处理和调整就应迅速停机处理后再重新启动。
当主电动机运转电流稳定后.迅速按下“导流叶片开大”按钮。
每开启5%~10%导叶角度,应稳定3~5min,待供油压力值回升后,再继续开启导叶。
待蒸发器出口冷媒水温度接近要求值时,对导叶的手动控制可改为温度自动控制。
2.在启动过程中应注意监测的内容
(l)冷凝压力表上读数不允许超过极限值O.78×105Pa(表压),否则会停机。
若压力过高,必要时就可用“部分自动”启动方式运转抽气回收装置约30min或加大冷却水流量来降低冷凝压力。
(2)压缩机进口导叶由关闭至额定制冷量工况的全开过程,供油压力表上读数约下降(0.686~1.47)×105Pa(表压)。
若下降幅度过大,就可在表压l.57×105Pa时稳定30min,待机组工况平稳后,再将供油压力调至规定值(0.98~1.47)×105Pa(表压)的上限。
要注意观察机组油槽油位的状况,因为过高的供油压力将会造成漏油故障。
压缩机运行时,必须保证压缩机出口气压比轴承回油处的油压约高0.1×105Pa,只有这样才能使压缩机叶轮后充气密封、主电动机充气密封、增速箱箱体与主电动机回液(气)腔之间充气密封起到封油的作用。
(3)油槽油位的高度反映了润滑油系统的循环油最的大小。
机组启动之前,制冷剂可能较多地溶解于油中,造成油槽视镜中的油位上升。
随着进口导叶开度的加大、轴承回油温度上升及油槽油温的稳定,在油槽油面及内部聚集着大量的制冷剂气泡,若此时油压指示值稳定,则这些气泡属于机组启动及运行初期的正常现象。
待机组稳定运行3~4h后,气泡即慢慢消失,此时油槽中的油位,才是真正的真实油位。
在机组启动时.由于油槽中有大量的气泡产生,供油压力会呈缓慢下降的趋势,此时,应严密监视油压的变化。
当油压降到机组最低供油压力值(如表压0.78×105Pa)时,应做紧急停机处理,以免造成机组的严重损坏。
(4)机组启动及运行过程中油槽中的油温应严格控制在50~60℃。
若油槽中油温过高,可切断电加热器或加大油冷却器供液量,使油温下降。
(5)供油油温应严格控制在35~50℃之间,与油槽油温同时调节,方法相同。
(6)机组轴承中,叶轮轴上的推力轴承温度最高,应严格控制各轴承温度不大于65℃。
(7)机组在启动过程中还需注意以下几个问题:
l)压缩机进口导叶关至零位。
2)油槽中油温需大于或等于40℃。
3)供油压力需大于250KPa。
4)冷媒水和冷却水供应正常。
5)两次开机时间间隔大于20min。
若1)~5)中任何一项不具备,主电动机就不能启动。
3.确认机组机械部分运转是否正常
(1)注意监听压缩机转子、齿轮啮合、油泵、主电动机径向轴承等部分,是否有金属撞击声、摩擦声或其他异常声响,并判断压缩机在出现异常声响后是否停机。
(2)监视供油压力表、油槽油位、控制柜上电流表、制冷剂液位等的摆动、波动情况,并判断发生强烈振动的原因,决定是否停机。
(3)若需用“部分自动”方法停机时,应记录(或自动打印出)停机时运行的各主要参数的瞬时读数值,供判断分析故障用。
(4)检查机组外表面是否有过热状况,包括主电动机外壳、蜗壳出气管、供回油管、冷凝器筒体等位置。
(5)冷凝器出水温度一般应在18℃以上。
为确保主电动机的冷却效果,冷凝器的进水温度与蒸发器的出水温度之差应大于20℃。
(6)轴承回油温度与供油温度之差应小于20℃,且应在运行过程中保持稳定。
(7)机组运行记录表应妥善保存,以备分析检查之用。
(三)离心式压缩机正常运行的标志
(1)压缩机吸汽口温度应比蒸发温度高1~2℃或2~3℃。
蒸发温度一般在O~10℃之间。
(2)压缩机排汽温度一般不超过60~70℃。
如果排汽温度过高,会引起冷却水水质的变化,杂质分解增多,使设备被腐蚀损坏的可能性增加。
(3)油温应控制在43℃以上,油压差应在0.15~0.2MPa。
润滑油泵轴承温度应为60~74℃范围。
如果润滑油泵运转时轴承温度高于83℃,就会引起机组停机。
(4)冷却水通过冷凝器时的压力降低范围应为0.06~O.07MPa,冷媒水通过蒸发器时的压力降低范围应为0.05~0.06MPa。
如果超出要求的范围,就应通过调节水泵出口阀门及冷凝器、蒸发器的进水阀门进行调整,将压力控制在要求的范围内。
(5)冷凝器下部液体制冷剂的温度,应比冷凝压力对应的饱和温度低2℃左右。
(6)从电动机的制冷剂冷却管道上的含水量指示器上,应能看到制冷剂液体的流动及干燥情况在合格范围内。
(7)机组的冷凝温度比冷却水的出水温度高2~4℃,冷凝温度一般控制在40℃左右,冷凝器进水温度要求在32℃以下。
(8)机组的蒸发温度比冷媒水出水温度低1~4℃,冷媒水出水温度一般为5~7℃左右。
(9)控制盘上电流表的读数小于或等于规定的额定电流值。
(10)机组运行声音均匀、平稳,听不到喘振现象或其他异常声响。
(四)离心式压缩机的停机操作
1.正常停机操作
机组在正常运行过程中,因为定期维修或其他非故障性的主动停机方式称为正常停机。
正常停机一般采用手动方式,机组的正常停机基本上采用正常启动的逆过程。
具体程序见下面的框图。
机组正常停机过程中应注意以下几个问题:
(l)停机后,油槽油温应继续维持在50~60℃之间,以防止制冷剂大量溶入冷冻润滑油中。
(2)压缩机停止运转后,冷媒水泵应继续运行一段时间,保持蒸发器中制冷剂的温度在2℃以上.防止冷媒水产生冻结。
(3)在停机过程中要注意主电动机有无反转现象,以免造成事故。
主电动机反转是由于在停机过程中,压缩机的增压作用突然消失,蜗壳及冷凝器中的高压制冷剂气体倒灌所致的。
因此,压缩机停机前在保证安全的前提下,应尽可能关小导叶角度、降低压缩机出口压力。
(4)停机后,抽气回收装置与冷凝器、蒸发器相通的波纹管阀、小活塞压缩机的加油阀、主电动机、回收冷凝器、油冷却器等的供应制冷剂的液阀,以及抽气装置上的冷却水阀等应全部关团。
(S)停机后仍应保持主电动机的供油、回油的管路畅通,油路系统中的各阀一律不得关闭。
(6)停机后除向油槽进行加热的供电和控制电路外,机组的其他电路应一律切断,以保证停机安全。
(7)检查蒸发器内制冷剂液位高度,与机组运行前比较,应略低或基本相同。
(8)再检查一下导叶的关闭情况,必须确认处于全关闭状态。
2.事故停机的操作
事故停机分为故障停机和紧急停机两种情况。
(1)故障停机。
机组的故障停机是指机组在运行过程中某部位出现故障,电气控制系统中保护装置动作,实现机组正常自动保护的停机。
故障停机是由机组控制系统自动进行的,与正常停机的不同处在于,主机停止指令是由电脑控制装置发出的,机组的停止程序,与正常停机过程相同。
在故障停机时,机组控制装置会有报警(声、光)显示,操作人员可先按机组运行说明书中的提示,先消除报警的声响,再按下控制屏上的显示按钮,故障内容会以代码或汉字显示,按照提示,操作人员即可进行故障排除。
若停机后按下显示按钮时,控制屏上无显示,则表示故障己被控制系统自动排除,应在机组停机30min后再按正常启动程序重新启动机组。
(2)紧急停机。
机组的紧急停机是指机组在运行过程中突然停电、冷却水突然中断、冷媒水突然中断和出现火警时突然停机。
火警时紧急停机
在制冷空调系统正常运行的情况下,空调机房或相邻建筑发生火灾危及系统安全时,应首先切断电源,按突然停电的紧急处理措施使系统停止运行。
同时向有关部门报警,并协助灭火工作。
当火警解除之后,可按突然停电后又恢复供电时的启动方法处理,恢复系统正常运行。
制冷设备在运行过程中,如遇下述情况,应做故障停机处理。
(1)油压过低或油压升不上去。
(2)油温超过允许温度值。
(3)压缩机气缸中有敲击声。
(4)压缩机轴封处制冷剂泄漏现象严重。
(5)压缩机运行中出现较严重的液击现象。
(6)排气压力和排气温度过高。
(7)压缩机的能量调节机构动作失灵。
(8)冷冻润滑油太脏或出现变质情况。
制冷装置在发生上述故障时,采取何种方式停机,可视具体情况而定,可采用紧急停机处理或按正常停机方法处理。
3.离心式压缩机停机后制冷剂的移出方法
由于空调用离心式制冷压缩机大部分为季节运行,在压缩机停运季节或需要进行机组大修时,均应将机组内的制冷剂排出。
其操作方法是:
(l)采用铜管或PVC管,将排放阀(即充注阀)与置于磅秤上的制冷剂贮液罐相连。
从蒸发器或压缩机进气管上的专用接管口处,向机内充入干燥氮气,对机组内的液态制冷剂加压至(0.98~1.4)×105Pa的压力(表压),利用氮气压力将液态制冷剂从机组内压入到贮液罐或制冷剂钢瓶中。
在排放过程中应通过重量控制或使用一段透明软管,来观测制冷剂的排放过程。
当机组内的液态制冷剂全部排完时,迅速关闭排放阀,避免氮气混入贮液罐或制冷剂钢瓶中。
(2)存贮制冷剂用的贮液罐或制冷剂钢瓶,不得充灌得过满,应留有20%左右的空间。
制冷剂钢瓶装入制冷剂后应放在阴凉、干燥的通风处。
(3)机组内液体制冷剂排干净以后,开动抽气回收装置,使机组内残存的制冷剂气体被抽气回收装置中的冷却水液化以后排入到制冷剂钢瓶中。
(4)如果机组内的制冷剂混入了润滑油,并且润滑油又大量地漂浮在制冷剂液体表面时,可在制冷剂液体基本回收完毕时,断开向贮液罐或制冷剂钢瓶的输送,将机组内剩余的制冷剂与润滑油的混合物排入专用的分离罐中,然后再对分离罐进行加热,使油、气分离,对制冷剂进行回收。
如果没有专用的分离罐时,也可将混入大量冷冻油的制冷剂排入污水沟,排放时应严禁