焦炭分析国标.docx
《焦炭分析国标.docx》由会员分享,可在线阅读,更多相关《焦炭分析国标.docx(54页珍藏版)》请在冰豆网上搜索。
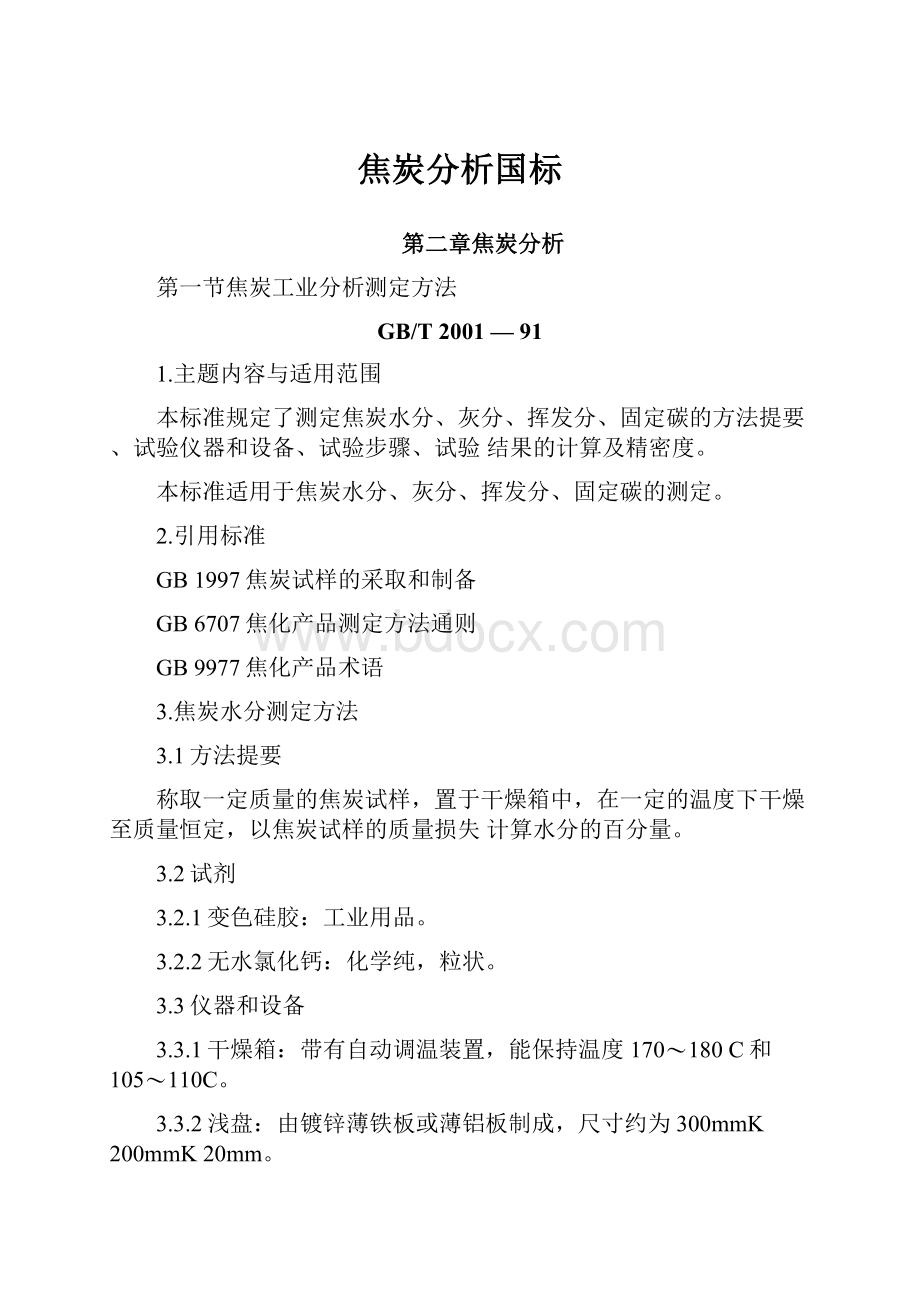
焦炭分析国标
第二章焦炭分析
第一节焦炭工业分析测定方法
GB/T2001—91
1.主题内容与适用范围
本标准规定了测定焦炭水分、灰分、挥发分、固定碳的方法提要、试验仪器和设备、试验步骤、试验结果的计算及精密度。
本标准适用于焦炭水分、灰分、挥发分、固定碳的测定。
2.引用标准
GB1997焦炭试样的采取和制备
GB6707焦化产品测定方法通则
GB9977焦化产品术语
3.焦炭水分测定方法
3.1方法提要
称取一定质量的焦炭试样,置于干燥箱中,在一定的温度下干燥至质量恒定,以焦炭试样的质量损失计算水分的百分量。
3.2试剂
3.2.1变色硅胶:
工业用品。
3.2.2无水氯化钙:
化学纯,粒状。
3.3仪器和设备
3.3.1干燥箱:
带有自动调温装置,能保持温度170〜180C和105〜110C。
3.3.2浅盘:
由镀锌薄铁板或薄铝板制成,尺寸约为300mmK200mmK20mm。
3.3.3玻璃称量瓶:
直径40mm,高25mm,并附有严密的磨口盖,如图1。
©40_
图1玻璃称量瓶
3.3.4干燥器:
内装变色硅胶或粒状无水氯化钙。
3.3.5分析天平:
感量0.0001g。
3.3.6托盘天平:
感量1g。
3.4试样的采取和制备
试样的采取和制备按GB1997的规定进行。
3.5试验步骤
3.5.1全水分的测定
3.5.1.1用预先干燥并称量过的浅盘称取粒度小于13mm的试样约500g(称准至1g),铺平试样。
3.5.1.2将装有试样的浅盘置于170〜180C的干燥箱中,1h后取出,冷却5min,称量。
3.5.1.3进行检查性干燥,每次10min,直到连续两次质量差在1g内为止,计算时取最后一次的质量。
3.5.2分析试样水分的测定
3.5.2.1用预先干燥至质量恒定并已称量的称量瓶迅速称取粒度小于0.2mm搅拌均匀的试样1±).05g(称准
至0.0002g),平摊在称量瓶中。
3.5.2.2将盛有试样的称量瓶开盖置于105〜110C干燥箱中干燥1h,取出称量瓶立即盖上盖,放入干燥器
中冷却至室温(约20min),称量。
3.5.2.3进行检查性干燥,每次15min,直到连续两次质量差在0.001g内为止,计算时取最后一次的质量,
若有增重则以增重前一次的质量为计算依据。
3.6试验结果的计算
3.6.1全水分按式
(1)计算:
Mt
m-m1
-X100
(1)
式中:
Mt—焦炭试样的全水分含量,%;
m—干燥前焦炭试样的质量,g;m1—干燥后焦炭试样的质量,g。
3.6.2分析试样水分按式
(2)计算:
Mad:
=X00/
m
\厶)
式屮:
Mad—
-分析试样的水分含量,
%;
m—
干燥前分析试样的质量,
g;
m1—
-干燥后分析试样的质量,
g。
试验结果取两次试验结果的算术平均值。
3.7精密度
重复性r,不得超过下表的规定值:
Mad
Mt
水分范围,%
—
<5.0
5.0〜10.0
>10.0
重复性r,%
0.20
0.4
0.6
0.8
4.焦炭灰分测定方法
4.1方法提要
称取一定质量的焦炭试样,于815C下灰化,以其残留物的质量占焦炭试样质量的百分数作为灰分含
量。
4.2试剂
4.2.1变色硅胶:
工业用品。
4.2.2无水氯化钙:
化学纯,粒状。
4.3仪器和设备
4.3.1箱形高温炉:
带有测温和控温装置,能保持温度在815±0C,炉膛具有足够的恒温区,炉后壁的上
部具有直径25〜30mm、高400mm的烟囱,下部具有插入热电偶的小孔,孔的位置应使热电偶的测温点处于恒温区的中间并距炉底20〜30mm,炉门有一通气小孔,如图2。
炉膛的恒温区应每半年校正一次。
图2箱型高温炉
1—烟囱;2—炉后小门;3—接线柱;4—烟道瓷管;5—热电偶瓷管;6—隔层套;7—炉芯;
8—保温层;9—炉支脚;10—角钢骨架;11—铁炉壳;12—炉门;13—炉口
4.3.2灰皿:
瓷质,如图3。
60
图3灰皿
4.3.3灰皿夹:
由耐热金属丝制成,也可使用坩埚钳,如图4。
图4灰皿夹
4.3.4干燥器:
内装变色硅胶或粒状无水氯化钙干燥剂。
4.3.5分析天平:
感量0.0001g。
4.4试样的采取和制备
试样的采取和制备按GB1997规定进行。
4.5试验步骤
4.5.1方法一(仲裁法)
4.5.1.1用预先于815±0C灼烧至质量恒定的灰皿,称取粒度小于0.2mm并搅拌均匀的试样1±).05g(称
准至0.0002g),并使试样铺平。
4.5.1.2将盛有试样的灰皿送入温度为815±0C的箱形高温炉炉门口,在10min内逐渐将其移入炉膛恒温区,关上炉门并使其留有约15mm的缝隙,同时打开炉门上的小孔和炉后烟囱,于815±10C下灼烧1h。
4.5.1.31h后,用灰皿夹或坩埚钳从炉中取出灰皿,放在空气中冷却约5min,移入干燥器中冷却至室温(约
20min),称量。
4.5.1.4进行检查性灼烧,每次15min,直到连续两次质量差在0.001g内为止,计算时取最后一次的质量,
若有增重则取增重前一次的质量为计算依据。
4.5.2方法二
4.5.2.1用预先于815±0C灼烧至恒重的灰皿,称取粒度小于0.2mm并搅拌均匀的试样0.5±05g(称准至
0.002g),并使试样铺平。
4.522将盛有试样的灰皿送入815±0C的箱形高温炉的炉门口,在10min内逐渐将其送入炉子的恒温区,
关上炉门并使其留有约15mm的缝隙,同时打开炉门上通气小孔和炉后烟囱,于815±10C下灼烧30min。
4.5.2.3同4.5.1.3。
4.5.2.4同4.5.1.4。
4.6试验结果的计算
4.6.1分析试样的灰分按式(3)计算:
m1
Aad,%=1X100
(
m
(3)
式中:
Aad—分析试样的灰分含量,
%;
m—焦炭试样质量,g;
m1—灰皿中残留物的质量,
g。
4.6.2
干燥试样灰分按式(4)计算
:
Ad,%二…
上X100
/A\
100-Mad
(4)
式中:
Ad—干燥试样的灰分含量,
%;
Aad—分析试样的灰分含量,
%
Mad—分析试样的水分含量,
%。
4.6.3试验结果取两次试验结果的算术平均值。
注:
每次测定灰分时,应先进行水分的测定,水分样与灰分测定试样应同时采取。
4.7精密度
重复性r:
不大于0.20%;
再现性R:
不大于0.30%。
5.焦炭挥发分测定方法
5.1方法提要
称取一定质量的焦炭试样,置于带盖的坩埚中,在样质量的百分数,减去该试样的水分含量。
5.2试剂
5.2.1变色硅胶:
工业用品。
5.2.2无水氯化钙:
化学纯,粒状。
5.3仪器和设备
5.3.1挥发分坩埚:
带严密盖的瓷坩埚,形状和尺寸如图
900C下,隔绝空气加热7min,以减少的质量占试
5所示。
坩埚总质量为18〜22g,其中盖的质量为
5〜6g。
图5挥发分坩埚
5.3.2箱形高温炉:
带有测温和控温装置,能保持温度在900±0C,炉膛具有足够的恒温区,炉后壁的上
部带有直径为25〜30mm,高400mm的烟囱,下部具有插入热电偶的小孔,小孔的位置应使热电偶的测温
点处于恒温区的中间并距底20〜30mm,如图6。
图6箱型高温炉
1—烟囱;2—炉后小门;3—接线柱;4—烟道瓷管;5—热电偶瓷管;6—隔层套;
7—炉芯;8—保温层;9—炉支脚;10—角钢骨架;11—铁炉壳;12—炉门;13—炉口
炉子的热容量应该是:
当起始温度为900C时,放入室温下的坩埚架和若干坩埚,关闭炉门后,在3min
内炉温应恢复到900±10C。
炉膛恒温区应每半年校准一次。
5.3.3坩埚架:
用镍铬丝或其它耐热金属丝制成。
其规格尺寸以能使所有的坩埚不超出恒温区为限,安放
在架上的坩埚底部距炉底间的距离应为30〜40mm,如图7。
图7坩埚架
图8坩埚架夹
5.3.4坩埚架夹:
由镍铬丝或耐热金属丝制成,形状如图
5.3.5分析天平:
感量0.0001g。
5.3.6秒表。
5.3.7干燥器:
内装变色硅胶或粒状无水氯化钙。
5.4试样的采取和制备
试样的采取和制备按GB1997的规定进行。
8,也可用坩埚钳。
5.5试验步骤
5.5.1用预先于900±10C温度下灼烧至质量恒定的带盖瓷坩埚,称取粒度小于
0.2mm搅拌均匀的试样
1±0.01g(称准至0.0001g),使试样摊平,盖上盖,放在坩埚架上。
注:
如果测定试样不足六个,则在坩埚架的空位上放上空坩埚补位。
5.5.2打开预先升温至900±10C的箱形高温炉炉门,迅速将装有坩埚的架子送入炉中的恒温区内,立即开
动秒表记时,并关好炉门,使坩埚连续加热7min。
坩埚和架子放入后,炉温会有所下降,但必须在3min
内使炉温恢复到900±10C,并继续保持此温度到试验结束,否则此次试验作废。
5.5.3到7min立即从炉中取出坩埚,放在空气中冷却约称量。
5min,然后移入干燥器中冷却至室温(约20min),
5.6试验结果的计算
5.6.1分析试样的挥发分按式(5)计算:
m-mi
m
X100-Mad
(5)
式中:
Vac—
-一分析试样的挥发分含量,
%;
m
试样的质量,g;
m1
—加热后焦炭残渣的质量,
g;
Mad
-一分析试样的水分含量,
%。
ad
daf
100-(Mad+Aad)
X100
(6)
5.6.2干燥无灰基挥发分按式(6)计算:
式中:
Vda—干燥无灰基挥发分含量,%;
Aad—分析试样的灰分含量,%;
Mad分析试样的水分含量,%;
Vad—分析试样的挥发分含量,%。
5.6.3试验结果取两次试验结果的算术平均值。
5.7精密度
重复性r:
不大于0.30%;
再现性R:
不大于0.40%。
6.焦炭固定碳测定方法
6.1方法提要用已测出的水分含量、灰分含量、挥发分含量进行计算,求出焦炭固定碳含量。
6.2固定碳的计算
分析试样固定碳按式(7)计算:
式中:
FCad=100MadAadVad(7)
FCad――分析试样的固定碳含量,%;
Mad焦炭分析试样的水分含量,%;
Aad焦炭分析试样的灰分含量,%;
Vad――焦炭分析试样的挥发分含量,%。
第二节焦炭全硫含量的测定方法
GB/T2286—2008
1范围本标准规定了焦炭全硫含量测定的原理、试剂和材料、仪器设备、试样的采取、试验步骤、结果计算和精密度。
本标准使用于焦炭全硫含量的测定,方法一为艾氏卡法,方法二为高温燃烧法,在仲裁分析时应采用艾氏卡法。
2规范性引用文件
下列文件中的条款通过本标准的引用而成为本标准的条款。
凡是注日期的引用文件,其随后所有的修改单(不包括勘误的内容)或修订版均不适用于本标准,然而,鼓励根据本标准达成协议的各方研究是否可使用这些文件的最新版本。
凡是不注日期的引用文件,其最新版本适用于本标准。
GB/T601化学试剂标准滴定溶液的制备
GB/T1997焦炭试样的采取和制备
3方法一(艾氏卡法)
3.1原理将试样与艾氏剂充分混合,在一定温度下灼烧,使焦炭中硫转化成硫酸盐。
然后使用硫酸根离子生成硫酸钡沉淀,根据硫酸钡的质量计算试样中的全硫含量。
3.2试剂和材料警告——处理试剂时应小心,其中很多时有毒和有腐蚀性的。
除非另有说明,在分析中仅使用确认为分析纯的试剂和蒸馏水或去离子水或相当纯度的水。
3.2.1氯化钡。
3.2.2氧化镁:
化学纯。
3.2.3无水碳酸钠:
化学纯。
3.2.4硝酸银。
3.2.5艾氏剂:
称取2份质量的氧化镁与1份质量的无水碳酸钠,研细至粒度小于0.2mm,混合均匀,贮
于密闭的容器中。
3.2.6过氧化氢:
浓度30%。
3
3.2.7盐酸溶液:
密度1.19g/cm。
3
3.2.8硝酸:
密度1.42g/cm3。
3.2.9氯化钡溶液(100g/L):
称取100g氯化钡,溶于水,用水稀释至1000mL。
3.2.10盐酸溶液:
(1+1)。
3.2.11硝酸银溶液(10g/L):
称取1g硝酸银,溶于水,用水稀释至100mL,加几滴硝酸,贮于深色瓶中。
3.2.12甲基红指示剂溶液(1g/L):
称取0.1g甲基红,溶于50mL乙醇中,用水稀释至100mL。
3.2.13定型滤纸:
中速,①90mm〜①110mm。
3.2.14定量滤纸:
中速,①90mm〜①110mm。
3.3仪器和设备
3.3.1分析天平:
感量0.0001g。
3.3.2托盘天平:
感量0.01g。
3.3.3马弗炉:
带有测温和控温装置,能保持温度800C〜850C,附有热电偶和高温计。
炉子后壁插入热
电偶的小孔位置应使热电偶的测温点处于恒温区的中部,并距炉底20mm〜30mm,后部有一导出废气的烟
囱。
3.3.4干燥器:
内装变色硅胶或粒状无水氯化钙。
3.3.5烧杯:
400mL。
3.3.6瓷坩埚:
30mL和20mL两种。
3.4试样的制备
按GB/T1997的规定进行。
3.5试验步骤
3.5.1于30mL瓷坩埚(336)内称取艾氏剂(3.2.5)2g(称准至0.1g)和粒度小于0.2mm的试样1g(称准至0.0002g),用镍铬丝混合均匀,再用1g(称准至0.1g)艾氏剂(3.2.5)覆盖。
3.5.2将盛有试样的坩埚移入马弗炉(3.3.3)内,在1h〜1.5h内将炉温逐渐升至800C~850C,并在该温
度下加热1h〜1.5h。
3.5.3将坩埚从马弗炉中取出,冷却至室温后,用玻璃棒搅松灼烧物(如发现有未烧尽的试样颗粒,应在
800C~850C下继续灼烧0.5h),并将其移入400mL烧杯中,用热水仔细冲洗坩埚内壁,将冲洗液加入烧杯中,再加入100mL〜150mL热水,用玻璃棒捣碎灼烧物(如果这时发现尚有未烧尽的试样颗粒,则本次试验作废)。
3.5.4加1mL过氧化氢(3.2.6)于烧杯中,将其加热至80C,并保持30min。
3.5.5用定型滤纸(3.2.13)过滤,并用热蒸馏水将灼烧物冲洗至滤纸上,继续以热蒸馏水仔细冲洗滤纸上的灼烧物,其次数不得少于10次。
3.5.6将滤液煮沸2min〜3min,排出过剩的过氧化氢,向滤液中加2〜3滴甲基红指示剂溶液(3.2.12),以
指示其排除是否完全。
滴加盐酸溶液(3.2.10)直至颜色变红,再多加1mL,煮沸5min,除去二氧化碳,
此时溶液的体积约为200mL。
3.5.7将烧杯盖上表面皿,减少加热量至溶液停止沸腾,取下表面皿,将10mL氯化钡溶液(329)缓缓滴
入热溶液中,同时搅拌溶液,盖上表面皿,并使溶液在略低于沸点的温度下保持30min。
3.5.8用定量滤纸(3.2.14)过滤,并用热水洗至无氯离子为止[用硝酸银溶液(3211)检验]。
3.5.9将沉淀物连同滤纸移入已知质量的20ml瓷坩埚(3.3.6)中,先在电炉上灰化滤纸,然后移入温度为
800C〜850C的马弗炉内灼烧20min,取出坩埚,稍冷后放入干燥器(3.3.4)中,冷却至室温称量。
3.5.10空白试验
每批试样应进行空白试验。
除不加试样外,其他试验步骤同3.5.1〜3.5.9。
3.6结果计算
3.6.1空气干燥基全硫(St,ad)测定结果按式
(1)计算:
S,ad
(mi-m2)X0.1374
m
X100
式中:
m1—硫酸钡的质量,单位为克(g);
m2—空白试验硫酸钡的质量,单位为克(g);m—试样的空气干燥基质量,单位为克(g);
0.1374—每克硫酸钡相当于硫的质量。
试验结果取两次测定结果的算术平均值。
并表示至小数点后二位。
3.6.2干基全硫(St,d)的结果按式
(2)计算:
St,d
St,ad
=100-Mad
X100
(2)
式中:
Mad分析试样的水分含量,质量分数(%)。
3.7精密度二次测定结果间的差值不得超过表1的规定:
表1
St,d/%
重复性St,d/%
再现性St,d/%
<1.00
0.04
0.1
>1.00
0.1
0.2
3.8试验报告
试验报告应包含下列信息:
a)试样编号;
b)依据的标准;
c)使用方法;
d)结果计算;
e)与标准的偏离;
f)试验中观察到的异常现象;
g)试验日期。
4方法二(高温燃烧法)
4.1原理
在1250C管式炉内,焦炭试样于氧气流中燃烧,焦炭中硫生成硫的氧化物,被过氧化氢溶液吸收,生成硫酸溶液,用氢氧化钠溶液滴定,根据其耗量,计算焦炭中全硫含量。
4.2试剂和材料
警告一一处理试剂时应小心,其中很多是有毒和有腐蚀性的。
除非另有说明,在分析中仅使用确认为分析纯的试剂和蒸馏水或去离子水或相当纯度的水。
4.2.1氢氧化钠:
优级纯。
4.2.2氧气:
纯度不低于99.5%。
4.2.3过氧化氢:
浓度30%。
4.2.4硫酸:
1.84g/cm。
4.2.5过氧化氢[约3%(质量分数)]溶液:
取100mL过氧化氢(4.2.3),用水稀释至1000mL。
4.2.6氢氧化钠标准滴定溶液[c(NaOH)=0.01mol/L]。
4.2.6.1氢氧化钠标准滴定溶液使用前按照附录A的要求配制氢氧化钠标准溶液[c(NaOH)=0.1mol/L]稀
释或按照GB/T601规定进行。
注:
也可使用四硼酸钠(优级纯)标准滴定溶液[c(1/2Na2B4O710H20)=0.01mol/L]。
4.2.7硫酸标准溶液[c(1/2H2SO4)=0.01mol/L]。
注:
硫酸标准溶液使用前用附录中配制的硫酸溶液[c(1/2H2SO4)=0.1mol/L]稀释。
4.2.8甲基红一次甲基蓝混合指示剂的配制:
4.2.8.1将次甲基蓝乙醇溶液(1g/L)与甲基红乙醇溶液(1g/L)按1+2体积混合。
4.2.8.2称取0.125g甲基红溶于50mL乙醇中,用水稀释至100mL,称取0.083g亚甲基蓝,溶于50mL乙醇中,用水稀释至100mL,分别贮存于棕色瓶中。
使用前按1+1体积混合,贮存于棕色滴瓶中。
注:
上述两种指示液,可任选一种,混合后的指示液有效期为7天。
4.3仪器设备
4.3.1高温管式炉:
用硅碳棒或硅碳管加热,带有控温装置,使炉温能保持在1250C±10C的范围内。
4.3.2燃烧管:
用高温瓷、刚玉或石英制成,管总长约750mm,一端外径22mm,内径19mm,长约690mm,另一端外径10mm,内径约7mm,长约60mm。
4.3.3燃烧舟:
用高温瓷或刚玉制成,长77mm,上宽12mm,下宽9mm,高8mm。
4.3.4吸收瓶:
锥形烧瓶,容积250mL。
4.3.5镍铬丝钩:
直径约2mm,长650mm,一端弯成小钩。
4.3.6硅橡胶管:
外径11mm,内径8mm,长约80mm。
4.4试样的制备
按GB/T1997的规定进行。
4.5试验步骤
4.5.1试验准备
4.5.1.1将仪器按图1顺序连接备用。
7
图1高温燃烧法定硫装置
1――缓冲瓶;2――流量计;3――T形管;4――镍铬丝钩;5――翻胶帽;
6――橡皮塞;7――温度控制器;8――热电偶;9――燃烧舟;10――高温管式炉;
11――燃烧管;12――硅胶管;13――吸收瓶。
4.5.1.2用量筒量取100mL过氧化氢溶液(425),倒入吸收瓶中,加(2~3)滴混合指示液(428),根据溶液的酸碱度,用硫酸标准溶液(427)或氢氧化钠标准溶液(426)调至溶液呈灰色,装好橡胶塞和气
体导管。
在工作的条件下,检查装置的各个连接部分的气密性,并通氧气(422),保持吸收液呈灰色。
4.5.2称取约0.2g粒度小于0.2mm的试样(称准至0.0002g),于预先在1250C灼烧过的燃烧舟中。
4.5.3将高温管式炉升温至1250C±10C,通入氧气(422),并保持流量700mL/min左右。
用镍铬丝钩
(4.3.5)将盛有试样的燃烧舟(433)缓缓地推入燃烧管的恒温区,燃烧10min后供氧。
取下吸收瓶的橡
胶塞,并用镍铬丝钩取出燃烧舟。
注1:
也可以用水抽或真空泵抽吸空气进行试验,其流量为1000mL/min左右。
注2:
当所用气体对试验结果有影响时,应加高锰酸钾溶液,氢氧化钾溶液和硫酸等净化装置。
4.5.4将吸收瓶取下,用水冲洗气体导管的附着物于吸收瓶中,补加混合指示剂溶液(2~3)滴,用0.01mol/L
的氢氧化钠标准滴定溶液滴定至溶液由紫红色变成灰色,即为终点,记下氢氧化钠标准滴定溶液的消耗量。
4.5.5空白试验
每批试样应进行空白试验。
除不加试样外,其他试验步骤同4.5.1.2~4.5.4。
4.6结果计算
4.6.1分析基全硫(St,ad)测定结果按式(3)计算:
VXcX0.016
S,ad=X00(3)
m
式中:
V――试样测定时氢氧化钠标准滴定溶液的用量,单位为毫升(mL);
c氢氧化钠标准滴定溶液的浓度,单位为摩尔每升(mol/L);
m试样的质量,单位为克(g);
0.016――与1.00mL氢氧化钠标准滴定溶液[c(NaOH)=1.000mol/L]相当的硫的质量,单位为克(g)。
试验结果取两次测定结果的算术平均值,并修约至小数点后二位。
4.6.2干基全硫(St,d)的结果按式(4)计算:
St,d
S,ad
100-Mad
X100
(4)
式中:
Mad分析试样的水分含量,质量分数(%)。
4.7精密度
重复性:
不大于0.05%。
再现性:
不大于0.1%。
4.8试验报告
试验报告应包含下列信息:
a)试样编号;
b)依据的标准;
c)使用方法;
d)结果计算;
e)与标准的偏离;
f)试验中观察到的异常现象;
g)试验日期。
附录A
(规范性附录)
标准溶液的配制与标定
A.1氢氧化钠标准溶液(4.2.6)[c(NaOH)=0.1mol/L]
A.1.1配制
称取110g氢氧化钠,溶于100mL水中,注入聚乙烯容器中,密闭放置至溶液清亮。
用塑料管虹吸5.4mL上层清液,注入1000mL无二氧化碳的水中摇匀。
A.1.2标定
称取0.75g于105C~110C电炉箱中干燥至恒量的工作基准试剂邻苯二甲酸氢钾,溶于50mL无二氧化
碳的水中,力口2滴