密集丛式井组优快钻井关键技术研究与应用.docx
《密集丛式井组优快钻井关键技术研究与应用.docx》由会员分享,可在线阅读,更多相关《密集丛式井组优快钻井关键技术研究与应用.docx(16页珍藏版)》请在冰豆网上搜索。
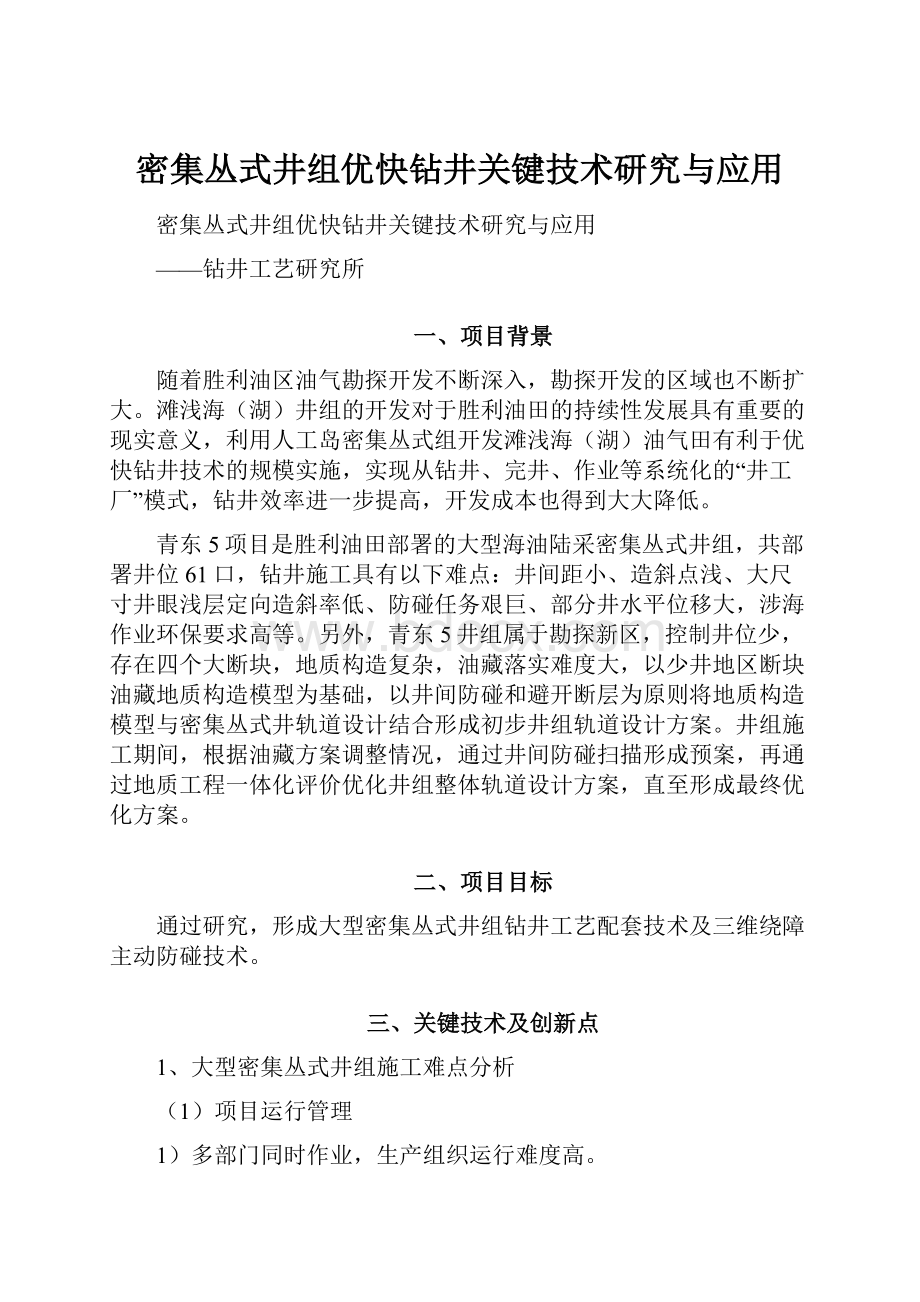
密集丛式井组优快钻井关键技术研究与应用
密集丛式井组优快钻井关键技术研究与应用
——钻井工艺研究所
一、项目背景
随着胜利油区油气勘探开发不断深入,勘探开发的区域也不断扩大。
滩浅海(湖)井组的开发对于胜利油田的持续性发展具有重要的现实意义,利用人工岛密集丛式组开发滩浅海(湖)油气田有利于优快钻井技术的规模实施,实现从钻井、完井、作业等系统化的“井工厂”模式,钻井效率进一步提高,开发成本也得到大大降低。
青东5项目是胜利油田部署的大型海油陆采密集丛式井组,共部署井位61口,钻井施工具有以下难点:
井间距小、造斜点浅、大尺寸井眼浅层定向造斜率低、防碰任务艰巨、部分井水平位移大,涉海作业环保要求高等。
另外,青东5井组属于勘探新区,控制井位少,存在四个大断块,地质构造复杂,油藏落实难度大,以少井地区断块油藏地质构造模型为基础,以井间防碰和避开断层为原则将地质构造模型与密集丛式井轨道设计结合形成初步井组轨道设计方案。
井组施工期间,根据油藏方案调整情况,通过井间防碰扫描形成预案,再通过地质工程一体化评价优化井组整体轨道设计方案,直至形成最终优化方案。
二、项目目标
通过研究,形成大型密集丛式井组钻井工艺配套技术及三维绕障主动防碰技术。
三、关键技术及创新点
1、大型密集丛式井组施工难点分析
(1)项目运行管理
1)多部门同时作业,生产组织运行难度高。
一个井场,二到四部钻机同时施工,钻井、录井、定向、测井、固井等多部门协同作业,且搬安、电测、固井加上泥浆拉运等作业环节施工车辆多,极易发生地面“拥堵、停待”现象,在生活、安全及管理方面压力巨大.
(2)项目施工技术
1)表层大井眼定向,造斜点浅,造斜率低。
平原组位于地表,地层非常疏松。
为了满足无线信号的正常传输和井下安全又必须达到一定的排量,井眼扩大率大,造斜率低,井眼轨迹控制难度大。
2)井网密集,防碰难度大。
井数多,井网密集,井口间距仅2-5mm,地下井眼轨道密集交错,既要考虑与已完钻井的防碰,又要考虑不能侵占待钻井的井眼轨道,且大位移井(>1500m)、大井斜井(>45°)多,轨迹控制精度要求更加严格,防碰绕障任务艰巨。
3)井组设计水平位移大,施工难度高。
大型井组设计必然会有水平位移超过1000m;井斜角超过50°。
这类井施工难度都很大,裸眼大斜度井段长,岩屑的运移距离长,运移难度大,容易在下井壁滞留形成岩屑床,造成摩阻扭矩大,易出现键槽。
起下钻和电测都会遇到困难。
4)三维定向井,摩阻扭矩大,易导致键槽卡钻。
井组剖面分为五段制(直-增-稳-降-稳)、(直-增-稳-增-稳)剖面;四段制(直-增-稳-降)、(直-增-稳-增)剖面;特别是三维定向井和双靶点定向井。
降斜井段和扭方位段长,摩阻和扭矩大,容易出现键槽。
由于三维定向井和双靶点定向井按设计均需多次调整井斜和方位,如何解决钻井过程中的摩阻、扭矩和键槽问题,成为工程施工中突出的一个难点
2、大型密集丛式井组施工方案优化
针对以上钻井施工难点,在施工过程中探索出“一体化”生产运行模式、“动态化、及时化”轨道设计调控方法和“整体化、精细化”井眼轨迹控制方式,形成密集丛式井组高效井眼轨迹控制技术,为丛式井组的安全顺利完成提供了强力技术支撑。
(1)项目运行管理
1)“一体化”生产运行模式
针对岛上空间相对狭小,合作单位多,生产组织运行难度大的问题,提供技术支撑的钻井院,积极探索出资源配置一体化生产模式,优化人员,改变传统单井2名定向工程师、2名测量工程师标配模式,选配既懂测量又会定向复合人才,减少1名测量工程师。
部分特殊施工阶段,3名定向工程师同时负责2口井。
同时,驻井房由原来每队2栋减为1栋,井场中心的值班房,4个井队共用,成为现场“指挥中心。
平时,在岛人员控制在10人以内,驻井房由原来的8栋减少到3栋。
通过有效的进行内部人力资源优化,充分发挥复合型人才的积极作用,解放了劳动力,达到减员不减效的目的,提高了单位整体施工能力。
同时人员、驻井房的精减,既节约资源,又减轻了人工岛管理压力。
2)成立青东5现场项目组
针对施工作业部门多的特点,专门成立了项目组,以钻井公司为主体,录井、定向、测井和固井等各部门生产、技术和安全工作人员驻井,实行现场总项目长和分项目长制,在施工过程中大力实施队伍管理一体化、生产运行一体化、安全管理一体化、物料管理一体化及生活服务一体化,集中资源共享,使得所有工序实现无缝对接,减少停待时间,为提高整体施工效率提供了有力保障。
3)制定整体技术方案
多个井队同时施工,在有限的地面空间里各工序施工干扰不可避免,单井方案措施远不能满足优快钻井需要。
“一体化”模式下,多个井队钻井施工形成“一揽子”工程,固化成熟技术措施,比如螺杆度数、钻具组合、各井段钻井参数、钻井设计模式等等,项目长统筹安排运行。
施工前,项目组制定整体技术方案,施工中,及时汇总四口井轨迹数据,实时分析,制定措施,规范施工。
此前,定向工程师在某一个时间段内只需要负责一口井的轨迹控制工作,而今,每一位定向工程师,需要考虑的都不仅仅是一口井的井眼轨迹问题,四口井乃至后续要钻的所有井井眼轨迹都需要他们同时、提前考虑到。
4)建立现场例会制度
对施工队伍实行统一管理,每天早上7点,集中召开生产运行部署会,安排工作计划,晚上召开生产运行总结会,总结汇报当天完成的工作量。
跟踪、分析、评价施工过程,及时协调各单位施工措施、进度;分析节点问题,研究讨论解决方案,统一参加单位意见,同时由石油开发中心组织形成每月现场例会制度,进行工作总体部署和阶段总结,有效解决生产运行中遇到的各类难题。
5)优化装备配套,精选高素质队伍。
①优化钻机组合,合理调配施工井位
②配套先进顶驱,提高预防和处理能力
③购进和配套先进的固控设备,提高净化能力
④精挑细选各类人才,形成合力,提高钻井时效
在人员认识上,始终坚持“地面的问题不能带到井下去,杜绝地面问题叠加到井下问题上”,下井钻具认真检查,地面设备加强维护和保养,不能因为人为原因而导致井下出现复杂情况。
(2)项目施工技术
1))轨道设计“及时动态化”调整
对于勘探开发程度低的区块,每完钻一轮井,需要利用完钻资料,及时跟踪反演、跟踪评价、跟踪调整,提高单井钻井符合率,这样势必造成钻井顺序调整频繁,后续施工井需要重新进行井位分配和修正轨道设计。
为了提高效率,定向项目组需要与地质开发、工程设计和井队人员积极协同,项目组负责人保持24小时工作制度,随时随地与地质人员沟通交流,优化轨道设计,对每一口井的轨道进行反复的论证、对比和分析,在满足油藏开发的前提下,推荐最符合现场实际、最有利于提高钻井速度的井眼轨道优化方案,及时报批,避免出现停工待设计情况发生,大大提高了施工效率。
2)井眼轨迹“整体精细化”控制
①制定整体技术方案,形成“一揽子”模式。
多个井队同时施工,井间作业干扰时有发生,平常单井方案措施远不能满足优快钻井需要。
“一体化”模式下,多个井队定向施工形成“一揽子”模式,项目组长统筹安排运行。
施工前,项目组制定整体技术方案,施工中,及时汇总四口井轨迹数据,实时分析,制定措施,规范施工。
晨会、例会制度,每天早晚讨论部署,项目组成员一起分析当天工作,制定并严格执行施工要点。
此前,定向工程师在某一个时间段内只需要负责一口井的现场技术服务工作,而今,每一位定向工程师,需要考虑的都不仅仅是一口井的井眼轨迹问题,四口井乃至后续要钻的所有井井眼轨迹都需要他们同时、提前考虑到。
②注重“防碰”细节,强调过程控制。
密集丛式井顺利施工最关键的工作是井眼“防碰”,面对“蜘蛛网”一样的井眼轨迹,施工中,注重技术细节,通过采取表层深度和造斜点深度错开法,优化防碰总体设计,做好防碰预案;通过固定井组测斜仪器,降低轨迹测量误差;坚持一开表层直井段投测电子单多点,并根据磁场强度干扰情况筛选井斜、方位数据,校正施工剖面,提高轨迹控制精度。
重点强化施工过程控制,开钻前,通过对所施工井与完钻井实钻轨迹和待钻井设计轨道进行防碰扫描计算,提前做好防碰图,标明防碰井段。
对于直井段,坚持边测斜、边监控、边扫描和边记录的“组合拳”措施,确保直井段防斜打直;对于斜井段,缩短测斜间距加密监测,对易碰施工井段,采取绕障措施提前进行避让,并随时观察钻压、扭矩和返砂情况,出现异常情况立即停钻,及时分析,优化钻进措施,确保顺利通过“危险”地带,做好全井组的防碰工作。
③强化优快钻井技术集成应用,提高轨迹控制效率。
在确保施工质量的基础上,提速提效是密集丛式井组施工的重点。
在井眼轨迹控制过程中,集成应用了“表层直井段防斜打直技术”、“大井眼松软超浅地层定向技术”、“三维绕障防碰技术”、“长稳斜段导向钻井技术”和“一趟钻钻井技术”等一系列先进轨迹控制技术。
结合地层造斜特性分析,优化定向钻具组合、优选钻进参数,通过复合钻进控制钻压和转速的方法控制井斜及方位,实现“多复合少滑动”的目的,保证井眼轨迹平滑的同时也大幅度提高了机械钻速;针对大位移、大井斜的定向井,短程起下钻采用长短配合,并且辅以大排量,高转速,提高携砂效率,保证井眼干净。
3、大型密集丛式井组优快钻井技术
借鉴邻井施工经验,认真分析地层岩性和特点,确定施工重点和施工难点,细化施工措施,做好技术管理工作。
在井眼轨迹控制过程中,集成应用了“表层直井段防斜打直技术”、“大井眼超浅疏松地层定向技术”、“三维绕障防碰技术”、“长稳斜段导向钻井技术”和“大位移井钻井技术”等一系列高效轨迹控制技术,逐步形成了青东5密集丛式井组井眼轨迹高效控制技术。
(1)项目运行管理
形成定向施工“一体化”运行模式
1)资源配置一体化。
①减少住井技术人员数量。
②减少技术人员住井时间。
③减少住井房数量。
2)方案制定一体化。
多个井队同时施工,井间作业干扰时有发生,平常单井方案措施远不能满足优快钻井需要。
“一体化”模式下,多个井队定向施工形成“一揽子”工程,项目长统筹安排运行。
施工前,项目组制定整体技术方案,施工中,及时汇总轨迹数据,实时分析,制定措施,规范施工。
晨会、例会制度,每天早晚讨论部署,项目组成员一起分析当天工作,制定并严格执行施工要点。
3)工程设计一体化,减少停工等待。
由于地质油藏需要,钻井顺序调整频繁,每一轮井完钻后,后续施工井大多需要重新修正轨道设计。
为了提高效率,钻井院项目组与地质开发、工程设计和井队人员积极协同,推荐最符合现场实际、最有利于提高钻井速度的井眼轨道优化方案,及时报批,有效减少停工时间。
“一体化”生产运行模式,围绕一个“减”字,做到减员不减效,深挖人员和设备的潜力;突出一个“一”字,做到统一技术,统一决策,统一执行,形成区域化标准生产模式,提高运行效率。
(2)表层直井段防斜打直技术
表层井眼一开直井段打直、不碰和不串,为后续井的施工打好了基础。
如果表层直井段偏离了原设计井眼,而占用了其它井的井眼,那么会给后续施工井带来一系列的问题,因此保证表层井段钻直,给后续施工创造一个良好的开端,主要采用了以下技术措施:
1)采用了塔式钻具:
Φ346.1mm钻头+630×630+Φ203.2mm钻铤×3根(其中无磁1根)+631×410+Φ177.8mm钻铤×3根+Φ127mm钻杆。
2)采用小钻压、低排量进行吊打,确保直井段打直。
其钻进参数为:
钻压:
30~50kN、转速:
<40r/min、排量:
50~55l/s。
3)钻井中不划眼,不中途循环,打完进尺立即接单根等措施,保证了井眼规则,不出现大肚子井眼现象。
4)下套管不留(或少留)口袋,以防给后期二开施工留下隐患。
套管内留3~5m水泥塞,便于BOP试压需要)。
5)表层直井段完成后用NEMS投测电子单多点,跟踪扫描井眼轨迹。
(3)浅层大尺寸井眼定向技术
表层大尺寸井眼定向技术是密集丛式井组成功实施的关键技术之一,为了给后续施工井留下足够空间,需要确保表层定向成功。
1号钻机施工的井数多,位移大,因此该井组目前完成的8口井全部是表层定向,后续施工井也基本都是采用表层定向技术。
由于Ф346.1mm井眼尺寸是油田非常规井眼,施工经验少,定向钻具组合、钻进参数及螺杆结构型号等都需要进行优选。
1)钻具组合:
Φ346.1mm牙轮钻头+Φ244.5mm1.5º或1.75°单弯螺杆(扶正块Φ343mm)+Φ127mm无磁承压钻杆×1根+MWD短节+Φ127mm加重钻杆×10柱+Φ127mm钻杆;
2)钻进参数:
钻压:
40~120KN,排量:
40~55l/s;
3)主要技术措施:
①优选柔性钻具组合,钻具组合中不加钻铤,增加加重钻杆数量,减少钻具刚性,提高造斜能力;
②采用三牙轮钻头,工具面稳定,利于初期造斜,同时降低两井相碰时损坏或打破套管的机率;
③优化螺杆扶正块外径尺寸,常规Φ244.5mm螺杆钻具本体扶正块为Φ308mm,优化为Φ343mm,确保在非常规尺寸Φ346.1mm井眼中的造斜能力;
④对于井深150m以深地层定向时采用1.5°单弯螺杆,150m以浅地层定向造斜时采用1.75°单弯螺杆,能够满足设计10~15°/100m造斜率的要求;
⑤定向钻进过程中跟足钻压,一般在40KN以上,若出现放空现象,则加快送钻速度,确保钻头能吃住一定的钻压;
⑥初期定向适当降低排量至40l/s,不划眼、不定点循环,待井斜增至3~5°后,逐步提高排量,直到造斜率满足轨迹控制要求。
通过以上技术措施优化,形成了成熟的表层定向技术,确保了青东5块丛式井组25口井浅层非常规井眼尺寸定向钻进,为井组的成功实施奠定基础,表层定向井基本数据如表1所示。
25口表层定向井中造斜点最浅的是青东5-1-斜2井,造斜点井深55m,表层定向井设计造斜率一般在10~15°/100m,而实钻平均造斜率最小的为10.51°/100m,最大的为15.69°/100m,可以满足轨迹控制的需要,实现了密集丛式井组井位优化的目的,确保了青东五块密集丛式井组的顺利实施。
(4)增斜段优化控制技术
定向井增斜段控制的优劣是获得好的井眼轨迹的基础,关系到邻井防碰重点井段处理、最大井斜角的大小、增斜段滑动进尺的多少和井眼轨迹的圆滑度等方面。
根据青东五块地质资料,了解其增斜井段地层岩性特点,通过钻具组合造斜特性分析及第一轮试验井钻井施工情况总结分析,优化钻具组合和钻进参数,形成了基于青东五块地质工程特点的密集丛式井增斜段优化控制技术。
1)钻具组合:
Φ241.3mm牙轮钻头+Φ197mm1.25°单弯螺杆(扶正块Φ238mm)+Φ127mm无磁承压钻杆×1根+MWD短节+Φ127mm加重钻杆×10柱+Φ127mm钻杆;
2)钻进参数:
钻压:
80~160KN,排量:
38~42l/s,泵压:
8~10Mpa
3)主要控制原则及技术措施:
严格执行设计造斜点,可适当提前10m左右进行定向,预防初期造斜率异常低;
②本井组增斜段设计造斜率为12~15°/100m,施工过程中全角变化率尽量不超过20°/100m,确保井眼轨迹圆滑度;
③注意控制最大井斜,实钻最大井斜尽量不超设计最大井斜2°;
④设计要求过A靶点后以3°/100m降斜至井底,因此控制过程中前期实钻轨迹走设计线上方,后期在A靶之前100m提前降井斜,过A靶后不再定向调整井斜即可达到轨迹控制要求;
⑤防碰重点井段一般都在初期定向阶段,实钻轨迹尽量贴近设计线,初期造斜率低的话,适当降低排量,不划眼,不定点循环,确保在30~50m内远离防碰重点井段;
⑥优化井眼轨迹控制方式,初期造斜率低,采取整根定向增井斜方式,后期造斜率高,进行每根钻进方式的优化,采取滑动钻进和复合钻进相结合的方式;控制造斜率在设计要求范围之内,确保井眼轨迹圆滑度;
⑦由于明化镇和馆陶组地层软,清水大排量钻进,井径扩大率大,稳斜段复合钻进时井斜3~5°/100m降斜,因此定向段增井斜至设计最大井斜左右,为后期复合钻进留有余地,防止轨迹落后过多,需要大井斜中靶情况发生。
(5)长稳斜段导向钻井技术
二开长稳斜段是每口井的主要井段,井段较长,是提高全井机械钻速的主力井段,优质快速施工本井段对于一口井的提速提效来说具有重要的意义。
为了达到预期的目的,采用了导向钻井技术来施工本井段,随时调整井眼轨迹,实现“一趟钻”钻井技术。
1)钻具组合1:
Φ具组合,是提高牙轮钻头+轮钻头,是提高全井机械钻单弯螺杆(扶正块Φ238mm)+531mm正块转换接头+411mm正块回压阀+压阀1mm正无磁承压钻杆+MWD短节(411D钻杆正)+521钻杆正块转换接头+Φ换接头+Φ加重钻杆10柱+0127mm钻杆;
钻具组合2:
Φ具组合7mm块PDC钻头+头组合7mm块PDC械钻单弯螺杆(扶正块Φ238mm)+531mm正块转换接头+411mm正块回压阀+压阀1mm正无磁承压钻杆+MWD短节(411D钻杆正)+521钻杆正块转换接头+换接头钻杆正斜坡钻杆(若干)+Φ坡钻杆(若加重钻杆10柱+0钻杆(若干钻杆;
2)钻进参数:
牙轮钻头钻压:
80~120KN,PDC钻头钻压:
30~50KN,排量:
40l/s,泵压10~12Mpa,转盘转速:
60r/min;
3)主要技术措施:
①以复合钻进方式为主,通过调整钻进参数控制井斜增降情况;
②沙三以上井段地层松软,清水大排量钻进,井径扩大率大,导向钻具组合复合钻进呈降斜趋势,则采用钻具组合1,牙轮钻头能够施加较大钻压,减缓降斜效果,提高复合钻进比例;
③沙三段上部含有一定厚度的粗砂砾岩,磨损钻头严重,待牙轮钻头磨损后,钻时变慢,基本可钻穿粗砂砾岩段,达到A靶点,起钻更换钻具组合2;
④沙三以下地层,胶结相对致密,采用钻井液钻进,井径扩大率小,导向钻具组合复合钻进呈稳斜趋势,则采用钻具组合2,PDC钻头适合小钻压、高转速,调整钻压,使其复合钻进呈降斜趋势,满足过A靶点降斜需要,提高复合钻进比例;
⑤调整钻进参数若达不到轨迹控制要求,则采取滑动钻进方式调整,采取“勤调微调”方式,原则上调整幅度都在±2°以内,决不让井眼出现拐角,保持井眼光滑;
⑥随着位移的增加,适当倒装钻具,利于钻压传递,提高滑动钻进效率;
⑦加强固控设备的利用率,及时清除钻井液中的大量砂子,降低摩阻扭矩;
每150~200m进行一次短程起下钻,及时破坏岩屑床,提高井眼净化程度。
通过采用导向钻井技术,青东五井组所有定向井二开仅需两趟钻完成,井深在1800m以内的井(不含粗砾石层)一趟钻即可完成,大大节约了钻井周期,达到了提速提效的目的。
(6)三维防碰主动绕障技术
密集丛式井顺利施工最关键的工作是井眼“防碰”,面对“蜘蛛网”一样的地下井眼轨迹,项目组组制定了“精、准、细、严”四字防碰方针,全方位加强三维防碰绕障工作。
1)精确防碰扫描设计
根据井组部署的待钻新井和周边已钻老井,对每一口井的实钻井眼轨道都要与其他已钻井实钻轨迹和待钻井设计轨迹进行防碰扫描,既考虑完钻井轨迹绕障,又要为后续井留有充分防碰余地,确保三维空间中每一口井都有最安全的通道。
2)减少系统误差,提高数据准确性
加强定向仪器质量控制,严格按规程进行仪器室内校验,完钻后测多点校验MWD数据,减少仪器测量误差;
为减少仪器测量系统误差,固定使用同一种、同一套探管,以保证探管测量数据的稳定;
全程监测磁场强度,排除邻井套管的磁干扰影响,提高数据准确性。
3)细化防碰技术措施
采取表层深度和造斜点深度错开法,利用椭圆锥形理论优化防碰总体设计,做好防碰预案;
开钻前,通过对施工井与完钻井实钻轨迹和待钻井设计轨道进行防碰扫描计算,提前做好防碰图,标明防碰井段;
对于直井段,坚持边测斜、边监控、边扫描和边记录的“组合拳”措施,确保直井段防斜打直;
对于斜井段,缩短测斜间距加密监测,对防碰危险井段,采取绕障措施提前进行避让;
重点井段加密测斜,提高轨迹精度,勤预判轨迹趋势,做到心中有数;
重点防碰井加测陀螺,与MWD测量数据比对,防止出现较大偏差。
4)强化防碰意识,严格技术规程
强化现场人员防碰意识,定向、工程技术、现场监督三方相互沟通,紧密协作,将防碰工作落实到每个施工环节。
;
严格执行防碰技术规程,施工中遇憋跳等异常情况立即停钻并进行分析,查明原因后再恢复钻进,不得盲目打钻,造成严重后果。
(7)大位移井钻井技术
井组大位移井具有以下几个特点:
井斜角大(55°~65°),是携砂最困难的井斜,极易形成岩屑床;
裸眼段长(2000~2500m),表层定向完后,表套下深一般在600m左右,大斜度裸眼段长,摩阻扭矩大;
馆陶以上地层松软,井径扩大率大,短起下钻或起下钻过程中易出新眼;
沙三段地层砂岩发育,渗透性好,有缩径现象,对钻井液性能要求高;
随着位移的延伸,摩阻增大,定向滑动困难,轨迹控制效率低。
针对以上钻井技术难点,结合完成的青东5-斜9、青东5-9-斜2、青东5-9-斜3和青东5-2-斜7等4口大位移井的实际施工情况,逐步形成了以下几点大位移井施工关键措施:
1)配备顶驱,可以倒划眼和正划眼,随时进行开泵循环,提高处理井下复杂事故能力;
2)优化井身结构,表套下深600m左右改为1200m左右,封住上部明华镇组地层;
3)优化井眼轨道设计,增斜段造斜率控制在15°/100m左右,最大不超过20°/100m,提高井眼轨迹圆滑度;
4)优选钻进参数,通过改变钻压大小控制井斜增降,提高稳斜段旋转钻进比例,减少滑动调整井段,并坚持“勤调少调”原则,井斜变化幅度不超过2°,提高井眼质量;
5)优化水力参数,坚持大排量、高转速钻进,二开钻进排量42l/s,转速70~90r/min,提高钻井液携砂能力;
6)加强短起下钻措施,进入沙三段后,每钻进100~150m短起下钻一次,并坚持长短结合,及时清除岩屑床。
3、创新点
(1)人工岛密集丛式井组“工厂化”钻井施工模式;
(2)大位移密集丛式井水力携岩动态优化方法;
(3)丛式井振动测距防碰监测技术。
四、应用效果
大型密集丛式井组优快钻井关键技术在青东5项目成功运用。
“一体化”项目管理保证了项目的顺利运行,关键技术的应用取得了良好的效果,并创下青东5多项技术指标:
1)青东5-1-斜3井是一开表层定向,二开稳斜段钻进,一只牙轮钻头一趟钻钻进进尺1420m;创造区块单只牙轮钻头钻进进尺最高纪录;青东5-2-斜3井是二开定向,然后稳斜段钻进,一只牙轮一趟钻钻进进尺1360m,全井钻井周期仅4.1d,创造青东5区块钻井周期最短纪录。
2)形成了以振动测距提供参考数据的密集丛式井组主动防碰绕障轨迹控制技术,实现了多口井空间距离在2m以内的小间距防碰绕障,其中青东5-2-斜12井与青东5-3-斜7、青东5-3-斜6和青东5-6-斜2井最小空间距离均在0.5m左右,成功的绕过了3口井的层层“阻扰”,顺利钻达油气储层,实现地质开发目的。
3)通过强化优快钻井技术集成应用,青东五井组所有定向井二开仅需两趟钻完成,井深在1900m以内的井甚至一趟钻即可完成,大大节约了钻井周期。
例如青东5-2-斜3井一只牙轮一趟钻完成二开进尺1360m,全井钻井周期仅4.1d,创造青东5井组钻井周期最短纪录。
4)建立了丛式井钻井工厂化实施成本评价模型,提出了以降低钻井综合成本为目标的“工厂化”钻井施工模式优化方案,形成一套基于多钻机联合施工的密集丛式井组“工厂化”钻井施工模式,并在青东5密集丛式井组试验应用,平均机械钻速34.7m/h,最高机械钻速62.68m/h,单井平均钻井周期仅为8.08天,平均缩短15.09天,累计缩短钻井周期920.49天;
密集丛式井组优快钻井关键技术的各项技术在生产和试验中均表现出了显著的提速效果,进一步丰富、完善了胜利油田海油陆采密集丛式井组优快钻井技术,并顺利推广到白鹭湖丛式井组,在白鹭湖密集丛式井组中又有了新的创新。
目前白鹭湖密集丛式井组已经推广应用8口井,取得良好开发