江苏天成非标设备制作安装总体方案.docx
《江苏天成非标设备制作安装总体方案.docx》由会员分享,可在线阅读,更多相关《江苏天成非标设备制作安装总体方案.docx(37页珍藏版)》请在冰豆网上搜索。
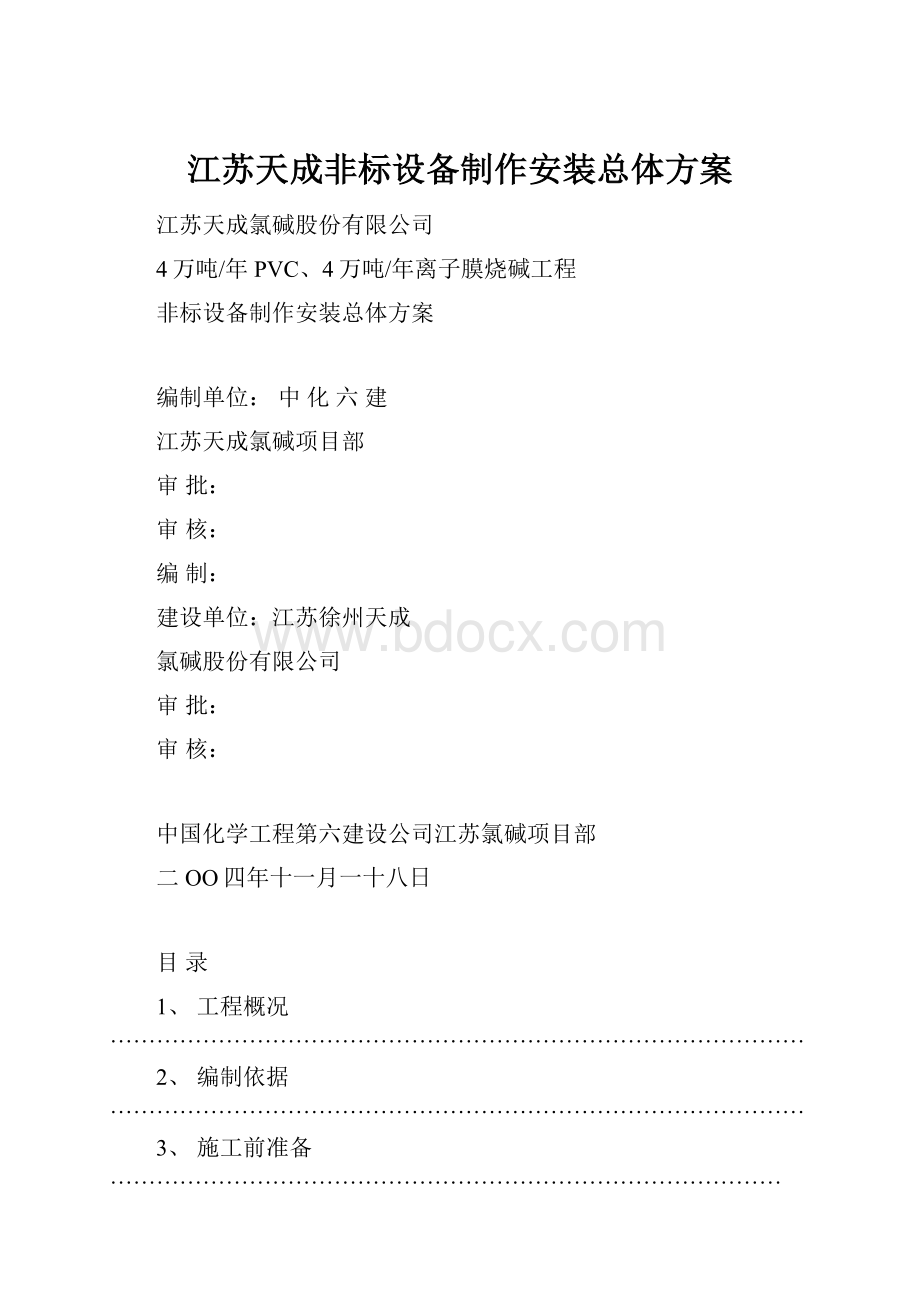
江苏天成非标设备制作安装总体方案
江苏天成氯碱股份有限公司
4万吨/年PVC、4万吨/年离子膜烧碱工程
非标设备制作安装总体方案
编制单位:
中化六建
江苏天成氯碱项目部
审批:
审核:
编制:
建设单位:
江苏徐州天成
氯碱股份有限公司
审批:
审核:
中国化学工程第六建设公司江苏氯碱项目部
二OO四年十一月一十八日
目录
1、工程概况………………………………………………………………………………
2、编制依据………………………………………………………………………………
3、施工前准备……………………………………………………………………………
4、主要施工方法…………………………………………………………………………
5、焊接……………………………………………………………………………………
6、焊接检验和总体试验…………………………………………………………………
7、质量保证措施…………………………………………………………………………
8、安全保证措施…………………………………………………………………………
9、劳动力计划……………………………………………………………………………
10、施工机具使用用料……………………………………………………………………
11、施工手段用料…………………………………………………………………………
12、检测与测量设备一览表………………………………………………………………
1.工程概况
江苏天成氯碱股份有限公司年产4万吨/年离子膜烧碱、4万吨/年PVC工程共有现场制作安装非标设备25台,其中贮槽23台,反应类设备1台,直升湿式气柜2台,主要设备的名称及基本参数见下表:
现场制作非标设备技术特性一览表
序号
设备位号
名称
规格
数量
材质
单重(t)
总重(t)
备 注
1
2V-0203
清夜贮槽
Φ6000×5500V=150m3
1
Q235-A
12.77
12.77
上拱顶下平底
2
2V-0202
上清夜贮槽
Φ6000×4500V=130m3
1
Q235-A
11.43
11.43
上锥顶下锥底
3
2V1303
乙炔气柜
Φ15900×14500V=1000m3
1
Q235-A
119.58
119.58
其中砼配重块25.624t、铸铁配重块26.624t
4
2V0501
氯乙烯气柜
Φ15900×14500V=1000m3
1
Q235-A
119.58
119.58
其中砼配重块24.412t、铸铁配重块24.412t
5
2V0417
热水槽
Φ3200×6500V=132m3
1
Q235-A
10.94
10.94
上锥顶下平底
6
TK-2G/4G
浆料混合槽
Φ5500×10050V=191m3
2
0Cr19Ni9
26.18
52.36
不锈钢12.445t
7
3V0501
0℃盐水储槽
Φ4000×6500V=80m3
1
20R
9.39
9.39
锥顶平底
8
2V1401
渣浆槽
Φ4000×3963V=32m3
1
Q235-A
5.12
5.12
锥顶锥底
9
2V0802AB
成品料仓
Φ5400×15026V=240m3
2
CS/SS
21.84
43.68
锥底裙座、内壁松衬2mm不锈钢
10
D0107ab
后反应槽
Φ4000×5500V=69m3
2
Q235-A
12.89
25.77
衬胶、搅拌装置为钛材
11
1F0120
过滤精盐水贮槽
Φ7024×8000V=289m3
2
Q235-A
26.455
52.91
上拱顶下平、衬胶
12
1F0103A/B
配水槽
Φ7024×8000V=289m3
2
Q235-A
27.065
54.13
同前、衬胶,插入管为钛材(27.5Kg)
13
1F0102
澄清桶
Φ10000×7000V=573m3
1
Q235-A
57.91
57.91
上锥下锥、搅拌装置重5.8t
14
D0103
前反应槽
Φ5000×4000
1
CS/HRL
10.95
10.95
衬胶、搅拌装置为钛材
15
F0105
预处理器
Φ10000×15558V=709m3
1
CS/涂料
134.96
134.96
上下锥体
16
F0116
中间槽
8000×4000×3500
1
CS/涂
9.56
9.56
长方型
17
V2008a/b
成品碱受槽
Φ11000×11000V=1000m3
2
Q235-A
46.13
92.26
储罐
18
V2008c/d
成品碱受槽
Φ11000×11000V=1000m3
2
304L
46.6
93.20
储罐
合计
25
907.99
25台非标设备结构多样,既有典型的立式圆筒型刚制焊接储罐类、金属焊接结构湿式气柜等容器;又有上拱顶下锥底的异型槽罐类容器。
同时内衬要求各不相同(配水槽、过滤精盐水贮槽等6台设备需内衬丁基橡胶,成品料仓需内壁松衬不锈钢)。
因内衬胶、板技术条件的要求,内衬侧的焊缝应打磨,表面进行探伤。
且前反应槽、浆料混合槽等6台设备带搅拌装置;设备主材以碳素钢Q235-A为主;0℃盐水储槽主材为20R;成品碱受槽、浆料混合槽4台设备主材以0Cr19Ni9为主。
清液贮槽、热水槽、0℃盐水储槽、后反应槽、过滤精盐水储槽、配水槽、前反应槽、成品碱受槽、乙炔气柜、氯乙烯气柜均应在设备基础上倒装法制作安装。
浆料混合槽筒体和裙座采用在设备基础上倒装法进行制作安装,上、下锥体封头预制完后按顺序吊装。
渣浆槽、上清液储槽、中间槽应现场制作组对,整体吊装。
澄清桶现场预制,分四部进行分段组装。
锥体和筒体在预制场组焊完成后,运至安装现场,用吊车先将锥体吊装就位,找正固定后,再将筒体吊装组对,最后组对锥顶封头和搅拌支撑梁
成品料仓预制场内分两段制造,现场分段吊装组焊。
预处理器分五部分在预制场内预制,运至现场后,下锥上部带裙座部分(含糟钢支撑梁、下连接板)吊装就位,找正固定后,吊装下部筒节,内部七个锥体由外及里分次组装;上部筒节(含锥节组件、漏斗组件)吊装组焊;顶盖吊装组焊;外附件平台栏杆安装。
2编制依据
2.1《立式圆筒形钢制焊接油罐施工验收规范》GBJ128-90
2.2《钢制焊接常压容器》JB/T4735-98
2.3《中低压化工设备验收规范》HGJ209-83
2.4《钢制熔化焊接接头射线照相与质量分级》GB3323-88
2.5《钢制低压湿式气柜》HG-20517
2.6《金属焊接结构湿式气柜施工验收规范》HG212-83
3施工准备
3.1施工前应组织有关人员熟悉图纸及施工方案,认真作好技术交底。
3.2根据施工图要求绘制好底板、壁板、顶板的排版图。
3.3施工现场应做到“三通一平”,在罐区基础旁搭设10m×12m平台一个,以满足预制要求。
3.4现场施工用机具、卡具等到位,吊装卡具在使用前,对其材质、结构和尺寸的适用性和安全性应检查并确认。
3.5工程材料的采购要充分考虑设计、施工的相互一致性,先后提出材料计划、定购计划、加工计划、进场计划、使用计划,确保材料采购、进场、保管、发放、使用、回收的准确性、合理性。
3.6对现场到货的材料,应仔细核对材质、规格、合格证书并进行相应材料复验后方能使用。
3.7基础验收
3.7.1贮罐底板铺设前,应对贮罐基础进行验收,如发现不合格应及时处理,基础验收质量标准见下表:
基础尺寸验收表
名称
项目
允许偏差
储
罐
设
备
中心坐标
±20
标高
±20
支承表面平整度
<10m弧长内任意两点高差不大于6mm,整圆内不大于12mm
沥青砂层表面凸凹疤痕
≤25mm
直
升
气
柜
中心坐标
±20mm
标高
±10mm
支承表面平整度
<10m弧长内任意两点高差不大于5mm,整圆内不大于12mm
沥青砂层表面凸凹疤
≤25mm
起拱度
≥160mm
3.7.2基础应设有沉降观测点。
3.8材料采购
材料采购应附有质量证明书,应包括材料制造标准代号,材料牌号、材料生产单位名称及检验印鉴标志,材料质量证明书的内容必须齐全、清晰,并加盖材料生产单位质量检验章。
严格按业主及监理公司要求执行。
3.9材料验收及保管
3.9.1贮罐用的材料和附件必须有产品质量合格证书或复检合格报告。
3.9.2钢板外观不得有气孔、裂纹、拉裂、夹渣、拆痕、夹层、表面锈蚀减薄量、划痕深度与钢板实际负偏差之和,应符合下表中的规定:
钢板厚度(mm)
允许偏差(mm)
4
-0.3
4.5~5.5
-0.5
6~7
-0.6
8~25
-0.8
3.9.3进入现场的板材,型材应在四角式两端进行材质、规格标识。
3.9.4焊条应具有质量合格证书,合格证书应包括熔敷金属的化学成份和机械性。
3.9.5对焊接材料的管理现场应设立二级管理制度,由专人负责,建立台帐,对焊接材料的烘干不得超过三次。
不锈钢焊接材料实际限量发放,全过程跟踪,杜绝误用和混用。
3.9.6现场焊工携带焊条应使用保温筒,在保温筒存放的焊条若超过4小时则须交回二级库重新烘干,同一保温筒内不得存放两种焊接材料。
3.9.7不锈钢材料应放置在道木上并垫以橡胶板或石棉板,禁止铁离子物质接触和在地面上磨擦,并做好材料移植工作和运输装卸、倒运、下料、制作、焊接、吊装、组对、配管等全过程的外观保护工作。
3.10样板准备
施工前,用δ=0.75mm的镀锌铁皮制做贮罐安装检验样板。
样板周边应光滑、整齐,并可折边加固,以防变形。
样板上应注明工程名称、曲率半径及尺寸。
其要求应满足GBJ128-90之要求。
4主要施工方法
本方案分两部分,分别以现场制作安装的储罐(1000m3拱顶储罐成品碱受槽)和湿式直升气柜(1000m3乙炔气柜)为主要编制内容,对其它非标设备的制作安装,只作简要说明。
4.1储罐施工方法及施工程序
4.1.1施工方法
储罐制作安装均采用胀圈群桅杆提升倒装法施工。
4.1.2施工程序
4.1.2.1碳钢贮罐V2008A/B施工程序见下图:
射线探伤、煤油渗漏
底板面防腐
顶板铺设
包边角钢组装焊接
顶圈壁板组装
群抱起升倒装就位组焊
依次组装其余壁板盘梯缝、罐体同时安装
围顶板下第二圈板
材料验收
排板
预制
罐底铺设
放罐体安装基准线
撑杆组焊
基础验收
群抱起吊倒装法桅杆、吊具设置
加热器安装试压
交工
罐体保温防腐
罐底真空试漏复验
人孔管接头安装及罐底边缘板伸缩缝焊接
罐底真空试漏
充水对罐体进行正负压试验、基础沉降观察
图3-1V2008AB施工工艺流程图
4.1.2.2不锈钢贮罐(V208CD)的施工程序见下图
图3-2V2008C/D施工工艺流程图
4.1.4贮罐预制和组装
4.1.4.1一般要求
a钢板的切割和焊缝的坡口加工:
碳钢板可采用半自动氧气、乙炔火焰切割,不锈钢板采用等离子切割或电动坡口机加工,但加工面应平滑,不得有夹渣、分层、裂纹及熔渣等缺陷。
焊缝坡口产生的表面硬化层应磨去。
b不锈钢材料禁止用一般磨片或切割片在表面打磨,一定要保护好其表面氧化保护膜,切割时防止等离子切割飞溅,电火花等,仅能用氧化铝切割片或砂轮片。
c除锈
碳钢罐除锈应安设计规定进行除锈,然后立即涂刷底漆。
4.1.4.2底板预制及铺设
a碳钢罐底板铺设前,应在底板底面进行预防腐处理(搭接部分除外)。
b底板方形板尺寸允许偏差见下表
允许偏差表
测量部位
允许偏差mm)
AB、CD
±2
AC、BD、EF
±2
对角线︱AD—BD︱
≤3
c底板中幅板(包括里板)尺寸允许偏差(mm)见下表。
测量部位
允许偏差(mm),板长<10m
AC、BD、
±1
AB、CD
±1.5
对角线︱AD—BD︱
≤2
直线度
AC、BD
≤1
AB、CD
≤2
d底板铺设时应按底板排板图进行。
e罐底板铺设焊接及增量,排板直径比设计直径约大2‰。
f底板铺设顺序,先拼边缘板,再铺中幅板,中幅板从中间开始向外围方向铺设。
g底板铺设时应注意相邻焊缝之间的距离≥200mm。
4.1.4.3拱顶预制、安装
a拱顶按设计几何尺寸及结构形式分块预制,单块顶板预制完成后存放在预先准备的托架上,以防变形。
b单块顶板弧度成形,借助拱顶成形胎具,将瓜瓣板置于胎具上找正,并用卡具将瓜瓣边缘与胎具牢牢地固定在一起,瓜瓣的中央部位借助千斤顶顶压使其达到弧度要求,用弧度样板检查整体成型符合要求后,按设计要求在其内表面先点焊固定径向筋板,再点焊固定周向筋板,最后按设计要求将筋板与瓜瓣焊接,再用弧度样板复查,其间隙不大于10mm,卸下瓜瓣,以备组装。
c顶板组装
(1)罐顶板胎具制作与安装
(2)除中心柱和位于Φ2圈内的支柱用Φ89×4钢管外,其余立柱全部采用Φ76×3.5钢管制作,支柱布置示意图见下图所示。
立柱长度按公式计算确定:
L=H+H拱-(h+△+δ+δA)
式中:
H-顶层壁板的实际高度,依据罐的制作排板图
H拱-罐的拱顶高度
H-罐不同位置的坡度增高,由顶圈位置计算确定,计算公式为:
h1=R-√R2-(Φ/2)2;
Δ—各立柱位置的坡度增高,由立柱位置确定
δ—顶圈板板厚,中心顶圈厚度10mm,其余8mm
δA—顶板筋板宽度
(3)所有立柱顶垫板一律采用槽钢[12,与底板相连的垫板一般用δ=10mm(100×100)。
立柱根数,位于同一圆周内的立柱间距以5m为宜。
(4)胎具斜支撑
斜支撑用于各立柱的稳定,安装时由内向外支撑,东、南、西、北每根立柱一般设置2根斜支撑,斜支撑用∠63×6角钢,其长度约等于立柱长度的1.4倍。
(5)胎具顶圈
顶圈由钢板下料制作,安装用于立柱顶部,圈宽100mm,厚10mm和8mm(中心顶圈厚10mm)。
顶圈制作尺寸现场安装时决定。
为了保护储罐底板,所有与底板连接的立柱和支撑底部均设垫铁(δ=10mm)(100×100mm)与底板点焊。
包边角钢
包边角钢用滚圆机滚圆后,在平台上矫形、找圆,成型后用弧形样板检查,其间隙不得大于2mm,翘曲变形不得超过构件长度的0.1%,且不得大于4mm。
角钢对接时开V型坡口斜接。
(6)顶板组装前,先按倒数第一、二带壁板及包边角钢全部组焊完毕,并检查包连角钢半径偏差不大于±19mm,中心架应安装完,中心架安装应牢固,其中心对准底板中心,其垂直度不大于0.1%L,且不大于10mm。
(7)用专用吊架将瓜瓣吊装至罐体上部从0°方向开始依次组装,边组装边找正并点焊定位。
(8)顶板组装完成,经检查合格后,即可进行焊接。
4.1.4.4壁板顶板组装
a壁板预制应按壁板排板图进行。
b当底板组焊完后,即可组织对罐顶下的第一带板,组对时以底板上中心为圆心,以罐体半径为半径,在底板上划出贮罐筒体组装圆周线,并沿此圆周线内侧,每隔约1m,点焊一长为100mm的壁板组装定位角钢。
c根据排板图组装第一带板,组装时,壁板内侧应用角钢作临时支撑,以防倾斜,为调节带板松紧度和控制焊接收缩量,在圆周对称位置设两道活口,每道活口焊两组挂钩,以3t倒链拉紧即可焊接壁板立缝。
d每一带板立缝焊接完成后,在距下口300mm处设置涨圈,焊缝长度、高度必须满足方案要求,用10t千斤顶及楔子顶装涨圈,以同样的方法在第一带板外侧组对第二带板,并将立缝外侧焊接完成。
4.1.4.5罐体提升
a贮罐组装采用群抱杆提升倒装法。
b设置8根抱杆,管子为ф219×8钢管,导链采用5t长链导链。
c罐体提升时,应由专人负责统一指挥,负责拉导链的操作人员,均应按指挥号令同时拽拉导链,且每次的拽拉量和提升均应相同确保罐体平移起升导链,确认无安全隐患后,即可组装第二带板。
d为了环缝组对口方便,保证质量提高工效,应在罐内侧每隔500mm焊一个定位板。
e为保证环缝对接质量,组对前,在上下两对焊环缝上每隔2m放置一块定位板,通过楔子找平。
环缝按要求组对完成后,点焊固定,点焊长度40~60mm、间隔500mm,最后将环缝焊接。
f按同样方法组装其它带板,直至最后一带板。
4.1.4.6接管安装
a罐体组装完后,按照管口方位位置画出管口的安装位置,内罐开孔采用等离子切割,用氧化铝砂轮片打磨掉氧化层,接管伸出长度应符合设计要求,焊缝做着色检验。
b管道对接焊缝焊接采用手工电弧焊,不锈钢管煨弯时采用冷煨,严禁用气焰加热煨弯,煨弯时不得用铁锤敲打管道。
c接管与罐体组装前,对所有的组装物件经检验合格方可进行组装,对所有的管件、接管管线进行清洗,去油污处理,并经检验合格,才可组装。
d接管安装允许偏差见HGJ128-90
e管接头须经清洗后才能进行安装。
f管子的端面和焊接坡口应采用机械切削并去除毛刺。
4.1.4.7梯子平台栏杆施工
a梯子平台栏杆施工应符合设计要求及钢结构施工规范的规定。
b梯子平台栏杆安装时应先焊一块连接衬板,且距离罐体焊缝不得小于200mm。
c所有手能触及的部位均应打磨
4.1.4.8质量标准
a罐壁组装质量标准,见下表
项目
允许误差mm
备注
底圈壁板
与上带板上口水平偏差
≤2
整个圆周上任意两点水平偏差
≤6
铅垂允许偏差
≤3
半径允许偏差
1m高处任意两点测量
局部凹凸变形
≤13
焊缝的棱角
≤10
δ≤12
≤8
12<δ≤25
环向对接头的组装间隙
2+10
其它壁板铅垂度
≤3h/1000
除底圈壁板
纵向为焊缝错边量
≤1
δ<10
≤1/10δ且≤15
≥10
环向焊缝错边量
≤1.5
上圈板厚δ<8
≤1/10δ且≤15
上圈板厚δ≥8
注:
δ――壁板厚度
b罐顶组装质量标准,见下表
顶板组装检查标准表
项目
允许偏差(mm)
备注
包边角钢的半径
±19
顶板搭接宽度
±5
c罐体几何形状及尺寸质量标准,见下表
罐体几何形状和尺寸检查
项目
允许偏差(mm)
检验方法
罐壁高度允许偏差
≤5H/1000
钢尺测量
罐壁铅垂允许偏差
≤4H/100且≤50
吊线测量
底圈壁板内表面半径允许偏差
±19
钢尺、样板检查
罐壁的局部凹凸变形
≤2L/100且≤50
罐底拉线检查
固定好局部凹凸变形
≤15
用弧形样板检查
4.21000m3直升湿式气柜制作安装
4.2.1构件预制
4.2.1.1底板条板与带板预制
气柜底板、钟罩、水槽壁按排版图预制,并标出安装所需的中心线、搭接线及搭接(或对接)顺序、方向和接口位置;
下料时底板圆直径按设计直径加大32mm(2/1000),以补偿焊接收缩量;
下料时用机械方法切割。
如:
半自动切割机、氧乙炔切割,并将切口上的氧化物打磨干净。
水槽、钟罩壁板除δ=3mm的矩形板外,其余均应滚圆且端部带头处理,用长不小于1.5米圆弧样板检查,其间隙不大于2mm。
预制板的尺寸允许偏差(mm)见表
测量项目
对接接头允许偏差
搭接接头允许偏差
板宽
±1
±2
板长
±1
±2
对角线之差
≤2
≤3
4.2.1.1型钢圈、立柱及拱顶骨架和导轨的预制
a型钢圈分段预制,分段长度不小于6米,弧长总长度应大于展开长度250mm左右。
b型钢圈煨制后,应在预制平台上进行弧度校园,其径向允差:
±3mm;水平允差:
≤5mm.
c立柱下料前应进行调直。
断面翘曲:
≤2.5mm.纵向弯曲:
≤3mm。
立柱与垫板采用两面链状间断焊,间断长50mm;
d钟罩拱形骨架的主、次梁预制后长度偏差:
≤3mm;纵向弯曲:
≤3mm。
e导轨下料前应进行调直,纵向弯曲全长应小于3mm,样板号料,复查尺寸合格后氧乙炔切割,导轨自身必需连接时应开V型坡口对接接头,焊条采用:
J422,Φ3.2。
4.2.2直升湿式气柜组装
4.2.2.1水槽壁底板的组装和焊接
水槽底板的组装和焊接与储罐相近,内外底环搭接焊缝的焊接需水槽壁板最下一带壁板纵逢焊接完毕后施焊;支墩焊接待气柜本体完,提升钟罩焊接。
4.2.2.2钟罩和水槽壁的组装
钟罩和水槽壁的组装采用倒装法施工:
由钟罩开始有内向外安装,最后组装水槽壁。
a钟罩组装
组装顺序:
最上节带板组装→上部圈板、筋板、异型板安装→骨架中心环定位→边缘环形板组焊→拱顶扇形板组焊→拱顶及上带板提升固定→钟罩下带板及底环组装→立柱(含其δ=5mm垫板)安装→矩形壁板安装→钟罩壁上的角钢、下部环形角钢圈安装
工艺要求:
(1)骨架中心环(槽钢圈)应比设计抬高100mm左右,用支撑管支撑固定;
(2)上部垫圈、筋板焊接,接着组焊拱顶盖板的边缘环形板,后组焊瓜皮之间的搭接焊缝,最后焊接与边缘环形板的搭接焊缝;
(3)上部圈板、筋板、异型板组焊后,与钟罩顶盖板的边缘环形板环缝先焊,与壁板连接的环焊缝最后焊接;
(4)利用Φ325×8mm长约15m的进气管做中心桅杆,均设4点,用4个3t倒链提升钟罩顶部至设计高度;若需要时顶部可临时加固;
(5)钟罩下带板及底环组装:
焊接前应在壁板与底环板间筋板点固后,施焊其角焊缝;
(6)立柱安装应保证其垂直;立柱(件7~3)与上、下带板连续焊接,与壁板不焊;
(7)矩形壁板的安装
Ⅰ.8块矩形壁板的安装应在:
钟罩上、下带板及底环板、上衬圈、异型板、拱顶盖板施焊组对完毕;拱顶及上带板提升至设计安装高度,带衬板的立柱安装就位,同时立柱两两间应进行临时加固后进行。
矩形壁板安装时相错180℃,“十字对称式”逐块安装,点固就位。
Ⅱ.矩形板与立柱垫板对接;与上、下带板搭接,搭接量上口40mm、下口230mm。
Ⅲ.矩形板焊接采用“十字对称法”两两施焊,先焊对接纵缝,8块板对接纵缝施焊后,焊与上、下带板搭接的环向搭接内外焊缝。
钟罩检查标准表
序号
项目
允许偏差
备注
1
壁板椭圆度
≤10mm
2
水槽壁垂直度
≤6.5mm
顶板局部凸凹度
径向:
≤6mm
旋长1.5m的弧形样板检测
纬向:
≤15mm
3
立柱垂直度
≤7mm
立柱中心位置
≤10mm
沿圆周方向
≤5mm
两立柱间水平旋长
b水槽壁组装
(1)利用钟罩8根立柱为吊点用8个3t倒链提升带板组焊安装,顺序与要求与储罐罐壁的方法相同。
(2)