毕业设计论文汽车车门扇形齿板精冲模具设计.docx
《毕业设计论文汽车车门扇形齿板精冲模具设计.docx》由会员分享,可在线阅读,更多相关《毕业设计论文汽车车门扇形齿板精冲模具设计.docx(20页珍藏版)》请在冰豆网上搜索。
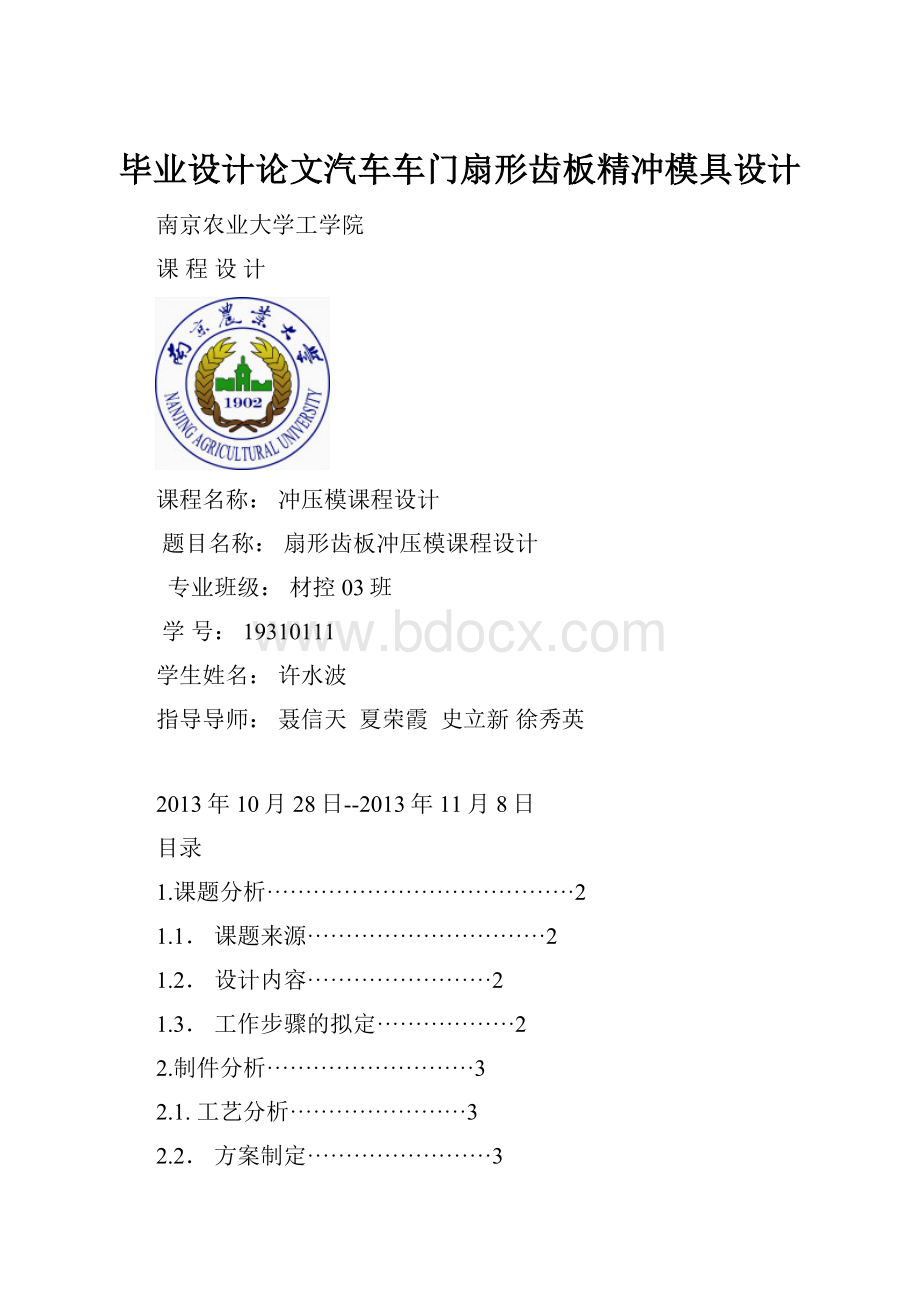
毕业设计论文汽车车门扇形齿板精冲模具设计
南京农业大学工学院
课程设计
课程名称:
冲压模课程设计
题目名称:
扇形齿板冲压模课程设计
专业班级:
材控03班
学号:
19310111
学生姓名:
许水波
指导导师:
聂信天夏荣霞史立新徐秀英
2013年10月28日--2013年11月8日
目录
1.课题分析········································2
1.1.课题来源·······························2
1.2.设计内容························2
1.3.工作步骤的拟定··················2
2.制件分析···························3
2.1.工艺分析·······················3
2.2.方案制定························3
2.3.工艺尺寸计算····················4
3、精冲工艺的力能参数························4
4、模具的结构设计·····························7
4.1凸模、凹模和凹凸模结构的设计················7
4.2确定模具的结构形式·····················7
4.3卸料与出料装置·······················8
5、模具零件的选用与设计···················9
6、模具的校核························13
7、总结·····························16
8、参考文献···························16
1课题分析
1.1课题来源
加工件是一扇形齿板,如图1所示,它是汽车车门玻璃升降器的重要传动零件,它的齿形精度、断面质量和平面度,对玻璃升降器的传动精度、传动平稳性和耐用度等都有很大影响。
由于使用普通冲孔落料技术冲压出来的产品有精度低、断面质量差的问题,所以进行技术改进,设计精冲方案进行生产。
该板材料45号钢,厚度2mm,齿板外形尺寸精度为IT10级。
图1-1加工件零件图
1.2设计内容
根据零件图的要求,设计出加工该零件的精冲复合模具,该模具需要完成外形和孔的精冲并满足精度要求。
该设计需要运用冲裁模具设计和精密冲裁的知识,合理运用。
具体要求如下:
(1)设计出生产该扇形齿板的冲裁模具;
(2)按照国家标准用AutoCAD软件绘制模具装配图以及非标准零件图;
(3)撰写说明书,用图片和文字结合说明,并注明计算公式的出处;
1.3工作步骤的拟定
通过对课题的研究和查找相关的资料,笔者拟定了整个设计过程中模具设计部分的设计方案,设计步骤如下:
(1)凹模、凸模和凹凸模结构的设计;
(2)计算凸模和凹模的刃口尺寸;
(3)选择模具的正倒装结构;
(4)确定卸料和出件方式;
(5)选择标准模架;
(6)对凸模进行校核;
2制件分析
2.1工艺分析
从产品的使用要求来看,扇形齿板的外形主要是要保证齿形部分的精度和光洁度,因为它是直接影响传动精度的。
在扇形齿板的四个孔中,主要是要保证φ13孔和φ2.25孔的位置精度,因为他们对装配精度有影响。
精冲工艺不用于普通冲压工艺。
精冲需要三重动作和压力,除主冲裁力外,还需要有齿圈压板压力和反压板压力,从而使变形区内外,上下形成三向压应力,并在近似于纯剪切状态下成形。
本文论述了采用通用压力机与液压模架、精冲模具组合的方式来实现精冲工件的目的,即靠压力机提供主冲裁力,通过液压模架上的两个液压缸获得齿圈压板压力和反压板压力,从而达到精冲的三重动作和压应力的要求,完成图1中所示扇形齿板的精密冲裁。
2.2方案制定
零件需要加工外形(齿板)和4个孔,用精密冲裁满足要求。
初拟的几个方案如下:
方案一:
先落料,再冲孔,采用单工序模进行生产。
方案二:
落料—冲孔复合冲压,采用复合模进行生产。
方案三:
冲孔—落料连续冲压,采用级进模进行生产。
方案一模具结构简单,但需要两道工序,两套模具,生产效率低,且两次定位难以满足精度要求,生产效率低。
方案三使用级进模,级进模的结构复杂,制造精度高,成本高,且同样有多次定位误差,不太合适。
个人比较倾向于方案二,用复合模进行生产可以提高生产效率,该零件精度要求较高,用复合模也可以满足要求。
2.3工艺尺寸计算
2.3.1毛坯尺寸
根据图1计算,得长度方向为164mm,宽度为95mm,厚度为2mm。
φ164.5扇形弧长:
L=π×d×θ/360=π×164.5×158/360=226.70mm
φ13孔周长:
L1=π×d=π×13=40.82mm
φ15孔周长:
L2=π×d=π×15=47.1mm
φ2.25孔周长:
L3=π×d=π×2.25=7.07mm
扇形边缘边长:
L4=85.48mm
2.3.2排样
排样搭边确定,采用直排。
根据参考文献[1]表11-1得x=4.5,y=5.5。
(x表示侧边距,y表示相邻两工件间距。
)
3精冲工艺的力能参数
3.1精冲工艺力的计算
精冲工艺过程是在压边力,反压力和冲裁力三者同时作用下进行的,这三个力对模具设计和保证工件质量以及提高模具寿命具有重要意义。
根据参考文献[1]p91~95的内容,分别计算冲裁力,压边力,反压力,总压力以及卸料力和顶件力。
3.1.1冲裁力
冲裁力P1大小取决于冲裁内外周边的总长度,材料的厚度和抗拉强度。
可按参考文献[1]p92由Timmerbeil提出的经验公式计算:
P1=f1Lttσb(2-1)
式中f1—系数,取决与材料的屈强比
Lt—内外周边的总长(mm)
t—材料厚度(mm)
σb—材料的抗拉强度(N/mm2)
其中Lt=L+L1+L2+L3+2×L4=775.35mm
t=2mm
σb=550N/mm2
考虑到精冲时由于模具的间隙小,刃口有圆角,材料处于三向受压的应力状态和一般冲裁相比提高了变形抗力,因此f1根据参考文献[1]图6-2取0.9。
故冲裁力为:
P1=0.9×775.35×2×550=1150KN(大约115T)
3.1.2压边力
V型环压边力的作用有三:
防止剪切区以外的材料在剪切过程中随凸模流动;
夹持材料,在精冲过程中是材料始终和冲裁方向垂直而不翘起;
在变形区建立三向受压的应力状态。
因此压边力对于保证工件剪切面质量,降低动力小号和提高模具的使用寿命有密切关系。
可以按照参考文献[1]p93经验公式计算:
P2=f2Le×2hσb(2-2)
式中f2—系数,取决于σb;
Le—工件外周边长度(mm);
h—V形齿高(mm);
σb—材料的抗拉强度(N/mm2)
其中Le=624mm;
h=0.8mm;
σb=550N/mm2
f2根据参考文献[1]表6-1查得取1.8。
故压边力为:
P2=1.8×624×0.8×550=494KN(大约49T)
3.1.3反压力
反压板的反压力也是影响精冲件质量的重要因素,它主要影响工件的尺寸精度,平面度,塌角和孔的剪切面质量。
反压力可以根据参考文献[1]p93经验公式计算:
P3=20%P1(2-3)
故反压力为:
P3=20%×1150=230KN(大约23T)
3.1.4总压力
工件完成精冲所需的总压力Pt是选用压力机的主要依据,根据参考文献[1]p94
PT=P1+P2'+P3(2-4)
式中P1—冲裁力(N);
P2'—保压压边力(N);
P3—反压力(N)
由于在实践过程中发现V形环压边圈压入材料所需的压边力P2,远远大于精冲过程中为了保证工件剪切面质量要求V形环压边圈保持的压力P2',一般P2'只有P2的30%~50%。
故保压压边力:
P2'=(30%~50%)P2=200KN(大约20T)
故总压力为:
PT=P1+P2'+P3=1150+200+230=1580KN(大约158T)
3.1.5卸料力和顶件力
精冲完毕,在滑块回程过程中不同步的完成卸料和顶件。
压边圈将废料从凸模上卸下,反压板蒋工件从凹模中顶出。
卸料力P4和顶件力P5可以按参考文献[1]p95经验公式计算:
P4=5%~10%P1=115KN(大约11.5T)(2-5)
P5=5%~10%P1=115KN(大约11.5T)(2-6)
4模具的结构设计
4.1凸模、凹模和凹凸模结构的设计
4.1.1凸模的结构形式
根据参考文献[3]p83表2-43选择凸模的结构形式,在经过比较之后,选择刚度好,便于装配,固定方便的圆形凸模B,如图4-1所示
图4-1凸模结构图
4.1.2凹模的结构形式
该凹模的作用是与凹凸模一起,冲裁出该扇形齿板的外形。
结构如图4-2所示。
图4-2凹模结构图
4.1.3凹凸模结构
凹凸模需要同时与凸模以及凹模配合工作,来完成对齿板外形的冲裁和内部孔的冲裁。
4.2确定模具的结构形式
因为制件的生产批量较大,选择复合模具和级进模都可以完成,但考虑到加工要求和设计的难度,所以采用复合模。
根据制件的尺寸和精度要求,齿板外形精度为IT10级,表面粗糙度值为Ra0.6微米,外形尺寸精度和表面质量要求都比较高,且整个零件表面要求平整光滑,断面质量要求良好。
这种条件下,复合模是最合适的加工方法,其他的加工方式都难免会有不足之处。
精冲模具的结构,有固定凸模式和活动凸模式两种。
对于在普通压力机上加液压模架的精冲,一般选择固定凸模式结构,即凹模和凸模装在下底板上。
这种结构受力平衡,但因精冲后制件,条料和冲孔废料都留在了模子上,操作不便。
因此,根据产品的使用个要求,决定只对外形精冲,对孔做一般冲孔来处理。
这样可以将固定凸模式结构倒过来装,冲孔废料可以从下面漏出,操作方便又安全,如图4-4所示。
倒装模具结构的优点:
(1)采用弹压卸料装置,使冲制出的工件平整,表面质量好。
(2)采用打料杆将制件或者废料冲凹模孔中打下,因而制件或废料不在凹模孔内积聚,可以减少制件或废料对孔的涨力。
从而可以减少凹模壁厚,使凹模的外形尺寸缩小,节省模具的材料。
(3)制件或废料不在凹模孔内积聚,可以减少制件或废料对刃口的磨损,减少凹模的刃磨次数,从而提高了凹模的使用寿命。
(4)制件或者废料不再凹模内积聚,因此也就没有必要加工凹模的反面孔(出料孔)。
可以缩短模具的制作周期,降低模具的加工费用。
由于所选用的倒装结构是将凹凸模装在下模座上,所以不用考虑落料的废
料如何排出的问题,只需要考虑如何将制件和冲孔废料如何从凸模和凹凸模上卸下的问题。
这些问题已经通过精冲模具的常用方式解决。
4.3卸料与出料装置
精冲完成后,上模上行,下液压缸通过托杆,齿圈压板将条料从凹凸模上退出,上液压缸通过推杆和反压板将制件从凸模和凹模中顶出。
废料从凹凸模的孔中通过下模板的废料槽排出。
5模具零件的选用与设计
5.1模具零件的选用与设计
根据工件的加工特点,有冲孔φ13,冲孔2-φ15,冲孔φ2.25和齿板外形的精冲。
5.1.1固定板
上模固定板选用参考文献[3]p116~117表2-65矩形固定板,选取JB/T7643.2中的标准模版,有关数据315×250×28。
下模固定板选用参考文献[3]p116~117表2-65矩形固定板,选取JB/T7643.2中的标准模版,有关数据250×250×28。
5.1.2垫板
上模垫板选用参考文献[3]p118表2-67矩形垫板,选取JB/T7643.3中的标准模板,有关数据315×250×8。
下模垫板选用参考文献[3]p118表2-67矩形垫板,选取JB/T7643.3中的标准模板,有关数据250×250×8。
5.1.3凹模
凹模的材料选用Cr12MoV模具钢,该材料的淬透性、淬火回火的硬度、耐磨性、强度均比较高,适合做尺寸较大的冲孔凹模。
凹模采用板状结构和直接通过螺钉,销钉和上模座固定的方式。
根据参考文献[3]p96公式:
L=l+2c(5-1)
B=b+2c(5-2)
式中l—沿凹模长度方向刃口型孔的最大距离(mm);
b—沿凹模宽度方向刃口型孔的最大距离(mm);
c—凹模壁厚(mm)。
其中l=164mm;
b=95mm;
c考虑布置螺孔和销孔的需要,再参照参考文献[3]p97表2-48根据材料厚度为3mm选取c的范围为38~48mm。
故:
L=230mm;
B=190mm;
根据参考文献[3]p97公式:
H=
(5-3)
其中F—冲裁力(N);
—凹模材料修正系数;
—凹模刃口周边长度修正系数。
其中F=1150KN;
=1(材料为合金工具钢取1);
=1.37(根据参考文献[3]p97表2-49查得)。
故H=66.62mm。
由于该公式计算的是整体式凹模的厚度,本设计中凹模并不是直接固定在模座上,而是通过固定板再固定在模座上,所以可以在厚度上去除固定板的厚度28mm,再根据标准凹模尺寸系列进行修正,取40mm。
5.1.4凸模
材料选用Cr12MoV。
由于冲裁力较大,使用T10A等材料其硬度不够,因而使用淬透性、淬火回火的硬度、耐磨性、强度等性能均优良的Cr12MoV。
凸模的结构已经确定,需要计算凸模的长度。
根据图6倒装结构可以得出凸模的长度只需计算凹模与上模固定板的厚度。
凹模的厚度为40mm,固定板厚度为28mm,所以凸模长度为68mm。
根据参考文献[3]表10-2选取标准长度为70mm。
(1)冲孔凸模1
用于冲φ13孔,根据参考文献[3]表10-2,选取B型标准圆凸模。
(2)冲孔凸模2
用于冲φ15孔,根据参考文献[3]表10-2,选取B型标准圆凸模。
(3)冲孔凸模3
用于冲φ5.2孔,根据参考文献[3]表10-2,选取B型标准圆凸模。
5.1.5凹、凸模固定方式
凸模采用凸缘固定方式,结构简单,刚度好。
凹模是使用螺钉紧固,销钉定位的方式。
紧固可靠。
由于在确定压力中心时,压力中心与模柄中心并未重合,加工时会产生一个扭矩,采用如粘结方式的固定方式容易被破坏。
5.1.6定位
使用的是两个挡料销进行对板料定位。
5.2凸、凹模的尺寸计算
5.2.1φ13冲孔的凸、凹模尺寸计算
已知孔φ130+0.11
根据参考文献[2]p277冲孔零件的要求,当精冲件要求内形尺寸N+Δ时,应以凸模为基准。
凸模尺寸:
B=G-25%Δ(5-4)
式中B—内形凸模名义尺寸(mm);
G—零件的最大尺寸(mm);
Δ—零件的公差(mm)。
其中G=13.11mm;
Δ=0.11mm。
故凸模名义尺寸:
B=13.11-25%×0.11
=13.083mm
根据参考文献[2]p279精冲间隙图5-66查得该孔的精冲间隙为0.008mm。
故φ13孔的凹模尺寸为13.099。
5.2.2φ15冲孔的凸、凹模尺寸计算
已知孔φ15。
由于该孔没有公差要求,可以按照普通冲裁的方式来处理。
根据参考文献[3]
p53表2-20查得冲裁间隙为0.25mm。
故凸模尺寸为15mm.
凹模尺寸为15.5mm。
5.2.3φ5.2冲孔的凸、凹模尺寸计算
已知孔φ5.2与扇形的圆心有位置公差要求,所以根据参考文献[2]p277,
按照以凹模为基准。
凹模尺寸:
A=K+25%Δ(5-5)
式中A—凹模名义尺寸(mm);
K—零件的最小尺寸(mm);
Δ—零件公差(mm)。
其中K=5.105mm;
Δ=0.19mm。
故凹模名义尺寸:
A=5.105+25%×0.19
=5.1525mm
根据参考文献[2]p279精冲间隙图5-66查得精冲间隙为0.015mm。
故凸模尺寸为:
5.1225mm。
5.2.4外形冲裁的凸、凹模尺寸计算
如图1-1所示,扇形外形尺寸为φ164.5-0.160。
根据参考文献[2]p277落料零件的要求,当精冲件要求外形尺寸为N-Δ时,
应以凹模为基准。
凹模尺寸:
A=K+25%Δ(5-6)
式中A—凹模名义尺寸(mm);
K—零件的最小尺寸(mm);
Δ—零件公差(mm)。
其中K=164.34mm;
Δ=0.16mm。
故凹模名义尺寸为:
A=164.34+25%×0.16
=164.38mm
根据参考文献[2]p279精冲间隙图5-66查得外形的精冲间隙为0.011mm。
故凸模尺寸为164.369mm。
5.3复合凸模的设计
材料选用Cr12MoV。
由于冲裁力较大,使用T10A等材料其硬度不够,因而使用淬透性、淬火回火的硬度、耐磨性、强度等性能均优良的Cr12MoV。
复合凸模的结构如图5-3所示。
图5-3凹凸模
本模具组合了冲孔和落料的结构,另外废料的排除通道也在该复合凸模的内部,加工精度比较高,且略复杂。
该模具采用嵌入固定板的方式,用螺钉将其与垫板固定,固定方式比较简单,且容易更换。
5.4模架选用
由于该加工件精度要求较高,所以选用液压模架来配合进行加工。
模具的周界尺寸为230*190,所以选用YMA-1型精冲液压模架。
其最大闭合高度为310mm,最小闭合高度为280mm。
5.6压力机选用
为了节约成本,选用普通压力机来完成冲压过程。
根据参考文献[3]p36
表1-40,选择型号为J31-160A的闭式单点压力机。
公称压力为1600KN大于总压力1580KN。
闭合高度为265~360mm,模具高度在其工作范围内。
所以选用该压力机没有问题。
6模具的校核
6.1凸模的校核
凸模的强度,通常核算最小断面的压应力和纵向保持稳定的最大长度。
6.1.1φ5.2冲孔凸模校核
根据参考文献[1]p253表4-1中圆形凸模的强度核算公式:
lmax=π/8
(6-1)
式中E—凸模材料弹性模量(MPa);
—凸模大端直径(mm);
t—冲件材料厚度(mm);
τ—冲件材料抗剪强度(MPa)。
其中E=210000MPa;
=8mm;
t=2mm;
τ=300MPa;
故:
lmax=π/8
=π/8
=135mm
l=70mm<lmax=135mm
所以φ5.2冲孔凸模的强度足够。
6.1.2φ13冲孔凸模校核
根据参考文献[1]p253表4-1中圆形凸模的强度核算公式:
lmax=C
(6-2)
式中C—系数;
E—凸模材料弹性模量(MPa);
—凸模大端直径(mm);
t—冲件材料厚度(mm);
τ—冲件材料抗剪强度(MPa)。
其中E=210000MPa;
=18mm;
t=2mm;
τ=300MPa;
C根据参考文献[1]p254表4-2查得为0.191。
故:
lmax=C
=0.191
=222.8mm
l=70mm<lmax=222.8mm
所以φ13冲孔凸模的强度足够。
6.1.3φ15冲孔凸模校核
根据参考文献[1]p253表4-1中圆形凸模的强度核算公式:
lmax=C
(6-3)
式中C—系数;
E—凸模材料弹性模量(MPa);
—凸模大端直径(mm);
t—冲件材料厚度(mm);
τ—冲件材料抗剪强度(MPa)。
其中E=210000MPa;
=18mm;
t=2mm;
τ=300MPa;
C根据参考文献[1]p254表4-2查得为0.196。
故:
lmax=C
=0.196
=228.6mm
l=70mm<lmax=228.6mm
所以φ15冲孔凸模的强度足够。
总结
在这次精冲模具设计之后,我对冲裁模和精冲模具有了一些了解。
此次的设计题目是汽车车门扇形齿板精冲模具设计。
该制件有一个扇形的齿形外形和4个孔组成,需要4个凸模,一个凹模和一个凹凸模来完成冲裁。
计算工艺参数过程中,参考了许多经验公式进行计算,保证所得尺寸比较合理。
在选择凸模时选用了带凸缘的圆形凸模,便于固定装配。
凹模和凹凸模一起完成对外形的冲裁。
模具整体采用了倒装的结构,便于材料和废料的取下。
由于冲裁力比较大,在选择模具材料时,选择了性能较好的Cr12MoV。
卸料则是通过反压板和齿圈压板分别将凸模和凹凸模上的板料褪下。
齿圈压板和反压板的工作都是通过液压模架来实现的,因此还根据模具周界尺寸选择了YMA-1型的液压模架。
最后选择了普通的压力机来完成冲裁过程。
本次设计过程中遇到的最大的问题在于设备选用。
由于该加工件的精度要求高,需要用到精冲技术。
精冲有两类设备可以选择,精冲机和普通压力机加液压模架的组合。
在参考了一些前辈的经验和生产成本以及考虑到对精冲机的不了解,所以选用了普通压力机和液压模架的组合。
由于手头关于液压模架的资料比较有限,也没有看到过液压模架的实物,因此在装配的时候可能存在不少问题。
由于时间仓促,不足之处,敬请指正。
参考文献
1、冲模设计手册机械工业出版社2006
2、实用冲压技术手册机械工业出版社2004王孝培
3、冲压工艺及冲模设计机械工业出版社2011翁其金徐新成
4、冲模技术新版机械工业出版社2010涂光祺赵彦启
5、互换性与测量技术中国电力出版社2011徐秀英齐新丹