不合格品处理流程.docx
《不合格品处理流程.docx》由会员分享,可在线阅读,更多相关《不合格品处理流程.docx(10页珍藏版)》请在冰豆网上搜索。
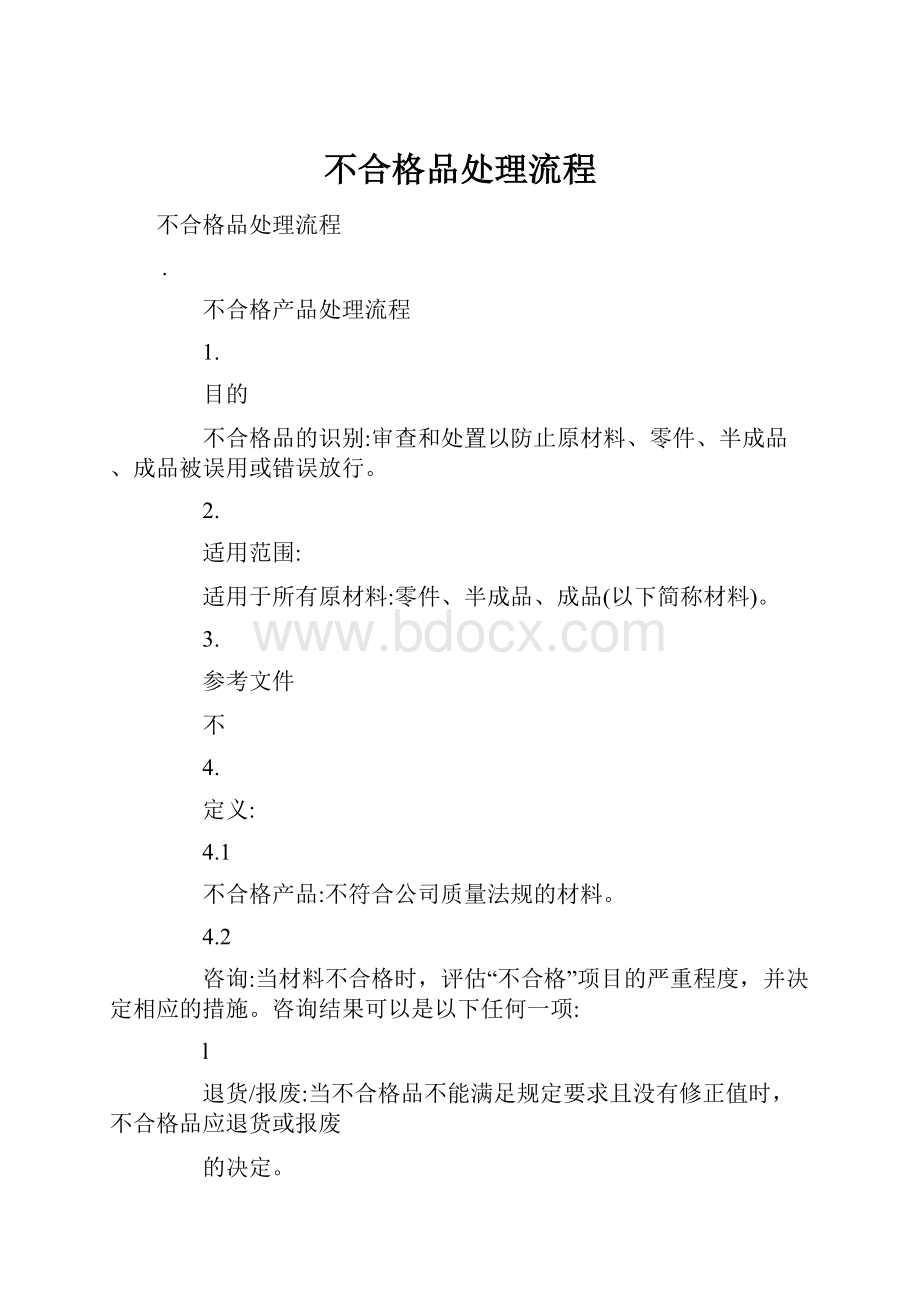
不合格品处理流程
不合格品处理流程
.
不合格产品处理流程
1.
目的
不合格品的识别:
审查和处置以防止原材料、零件、半成品、成品被误用或错误放行。
2.
适用范围:
适用于所有原材料:
零件、半成品、成品(以下简称材料)。
3.
参考文件
不
4.
定义:
4.1
不合格产品:
不符合公司质量法规的材料。
4.2
咨询:
当材料不合格时,评估“不合格”项目的严重程度,并决定相应的措施。
咨询结果可以是以下任何一项:
l
退货/报废:
当不合格品不能满足规定要求且没有修正值时,不合格品应退货或报废
的决定。
l
让步放行:
一种用于识别不合格产品批次的方法。
结果分为以下几类:
返工/返工;
照原样使用它;
(3)100%选择。
4.2.1
返工:
对不合格品采取的补救措施,不能使不合格品最终达到原设计要求,但能使其达到预期的使用要求。
4.2.2
返工:
为不合格产品最终达到原设计要求而采取的措施。
4.2.3
根据用途:
即提交的含有少量不合格产品的批次允许投入使用或直接放行,无需复检。
4.2.4
100%分拣:
从不合格批次中选择合格产品。
4.3
损坏检查:
损坏(有形或无形)被检查对象的质量并可能影响其正常功能的检查。
如跌落试验:
撕裂试验、和硬度试验未标注“可用”,整机耐久性试验、性能试验等。
5.
职责:
5.1
质量部门:
l
不合格品的识别:
隔离;
l
重新检查修复/返工的材料;判断一下。
l
参与“咨询”工作。
5.2
物料控制专员:
l
参与“咨询”
工作;
l
安排返工/维修等。
l
将不合适的原材料/零件退回给供应商;
l
安排供应商补充材料,并对供应商施加经济和其他限制。
l
加强供应商管理:
咨询、评估
5.3
生产部门:
l
制造过程中发现的不合格零件:
半成品应回收隔离,并用红色标记。
l
选择:
质量检验员拒绝的返工/返工产品(IQC\IPQC\FQC\质量保证);
l
参与“咨询”;
l
查询本部门生产的不合格产品的申请。
5.5
开发部门:
l
参与“咨询”。
6.
程序:
6.1
“不合格”材料的处理(IQC)。
6.1.1
当来料的批次质量合格,但检验样品中有不合格品时,来料检验员会在不合格品或外包装上贴上红色。
放置在指定不合格产品区域的“不合格”标签应由材料收集者返还给供应商。
6.1.2
当来料成批不合格时,当来料检验员在外包装材料上贴上黄色的“待加工”标签后,收料员将有效隔离它们。
同时,进货检验人员应在“检验单”上注明不良信息:
“零件/材料进货检验报告”并提交质量工程师审核。
对于该批不合格品,根据“不合格品”的类别和程度,各部门应按照以下原则进行处理。
6.1.3
不合格的最终确定:
6.1.3.1如果“不合格”仅涉及轻微外观超标或轻微严重缺陷,且一般互换性尺寸超标,质量工程师应决定是否“让步”。
6.1.3.2如果“不合格”涉及明显的外观超标或严重程度在严重缺陷以上,以及关键和重要尺寸超标和安全项目超标,质量工程师应通知买方处理。
咨询按照以下步骤进行:
相关材料来源信息和质量信息应由材料检验员在《材料申请表》上填写;
当不良项目仅涉及外观时,商务部只需与客户协商决定。
开发部项目组签署意见;
生产部签署意见;
经副总经理或其指定代表批准;
“咨询”表审批后,应下发至采购部:
物料控制部、质量控制部、生产部、商务、开发等相关部门
6.1.4
最终判决后的处理:
6.1.4.1
质量工程师应填写并发布“零件/材料缺陷改进通知”,解释缺陷的原因,并提示供应商改进。
同时,质量工程师还应在“部品/材料进货检验报告”中注明加工结论,并退回IQC。
6.1.4.2
来料检验员用与判定结果一致的标签替换黄色“待加工”标签,标签应覆盖原标签。
如果最终判定结果为“退货/报废”,将贴上红色“不合格”标签;如果判断结果是“让步放行”,将贴上白色“让步放行”标签。
6.1.4.3
如果最终判断结果是“返回”:
①
IQC应在黄色“待加工”标签上贴上红色“不合格”标签,收料员应将材料移至退货区并处理退货。
②
采购部根据《供应商评价程序》进行材料补充和供应商评价。
6.1.4.4
当最终判断的结论是“修理/返工”时:
(1)①IQC保留待加工的黄色标签;
(2)材料控制部安排供应商或生产部门实施“修理/返工”;
(3)供应商或生产部门应根据《物资需求表》的要求实施“修理/返工”;
④已“修复/返工”的材料应提交材料控制部门进行复检。
只有当材料符合《材料需求表》的要求时,绿色合格标签才能覆盖待加工和发放使用的黄色标签;
(5)材料控制部根据《供应商评价程序》处理供应商,并根据材料控制部的通知补充材料。
6.1.4.5
当最终判决的结论是“100%排序”时,
(1)①IQC保留待加工的黄色标签;
(2)物控部组织相关部门实施“100%分拣”;
(3)所选材料在发放使用前应重新检验并贴上绿色合格标签。
对于选中的不合格品,IQC公司应标记红色的“不合格品”标签,放在指定的不合格品区域,然后由仓库管理部处理退货。
(4)物资管理部根据《供应商评价程序》进行补货和供应商处理。
6.1.4.6
当最终判决的结论是“后续”时,
(1)①IQC用绿色合格标签覆盖黄色“待加工”标签;
(2)仓储部门进行仓储;
(3)采购应根据物资管理部的通知进行补充,供应商应根据《供应商评价程序》进行评价。
6.1.5
如果在生产过程中发现不合格的材料,它们将被放入红色的“次品”箱中。
在每个工作日结束前,直线领导将收集整理并提交给进货检验和检验。
如果合格,将返回生产线使用。
如果不合格,则判定为“来料废料”或“生产废料”。
贴上红色“不合格”标签后,返回仓库管理部。
生产部每日将退料情况记录在退料单上,并将退料单发送给物料控制部,由物料控制部进行补料。
6.2
“首件检验”不合格产品的处理:
在工作站进行“首件检验”时,如果有一个“首件检验”失败,则允许对后续产品逐个进行“首件检验”。
如果“不符合”再次出现,IPQC(过程检验人员)应填写“产品异常通知”并提交质量工程师确认。
质量控制部应召集相关单位进行分析和处理。
生产车间决定修理或报废不合格的首件。
修理后的产品必须重新检查。
6.3
过程中不合格品的处理(IPQC):
在巡检过程中,如果发现生产状态失控,过程检验员(IPQC)应填写《产品异常通知单》,并提交质量工程师确认。
之后,要求生产部对相应项目的相应过程中的所有成品进行全面检查。
如有异议,生产部应发起“协商”。
咨询程序和处理方法应按照第6条.1的规定执行。
(2)当生产部发现过程失控(不良品率超过20%)时,应填写《产品异常通知单》,并分发给物料控制部及相关部门。
材料控制部应召集相关部门讨论并实施解决方案。
6.4
“终检”(FQC)期间不合格品的处理:
6.4.1
如果终端检验员(FQC)发现任何不合格品,应标记不合格品的相应原因,并将不合格品放入红色不合格品容器中,由维修人员定期收集和修理。
修理时应填写《修理记录表》,并对修理后的产品进行复查。
不能修复的应报废。
6.4.2
在终检中,当同类型的不合格品率达到10%时,生产部应填写《产品异常通知单》,提交工艺工程师或部门经理审核,然后分发给物料控制部及相关部门。
材料控制部门应要求生产:
开发、质量控制,其他部门分析原因、制定纠正和预防措施。
结论记录在《产品异常通知单》后,相关责任部门进行整改,质量控制部进行跟踪检查。
6.5
“质量审核”不合格品的处理:
6.5.1
质量审核根据顺序抽样检验标准按订单批次检查成品。
如果发现不合格产品,质量保证部将在托盘上贴一个红色的“不合格”标签,生产部门将托盘拖到红色的“不合格”区域。
之后,质量审核员将填写“产品异常通知”并提交给质量工程师或部门经理审核,然后分发给生产部门,生产部门将安排对整个托盘进行100%的检查。
6.5.2
生产部对检验中发现的缺陷产品进行返工或返修。
修理时应填写《修理记录表》,并对修理后的产品进行复查。
生产部门应决定报废那些不能修复的。
6.6
顾客退货不合格品的处理:
6.6.1
售后服务部通知仓库管理部接收退货。
仓库管理部将产品放在“退货区”,售后服务人员填写“检验单”并提交给质量管理部质量工程师。
6.6.2
质量控制部质量工程师应安排相应的检验员对退回的产品进行检验,并填写“质量审核发货清单”,注明缺陷的原因和数量。
6.6.3
质量工程师将向销售部门分发质量审核发货清单和检验表。
6.6.4
工厂经理召集生产:
质量控制、开发部门(必要时)和其他部门讨论修理/返工计划,组织材料并实施“修理/返工”。
6.6.5
“返工/返工”由生产部实施。
维修/返工时,应填写维修记录表。
6.6.6
“修理/返工”后的产品必须重新检验。
6.7
库存不合格品的处理:
在搬运和库存过程中,不合格的标识状态不得改变。
如果发现材料变质或损坏,发现单位应通知质量控制部检查。
如果材料不是
对于合格的产品,发现部门应回到前一个过程,直到相关责任部门被发现。
责任部门负责人应遵循以下原则
正在处理:
l
对于个别不合格品,责任部门应填写《材料废品单》或《材料工作废品单》,并提交材料控制部审批。
l
对于批量不合格品,由责任部门填写《材料咨询表》,然后参照第6.1条进行“咨询”
安排维修/返工:
选择、报废、退货、补充等。
l
当出现严重不合格品(即批量不合格或安全等关键质量指标超标)时,责任部门应制定
实施纠正/预防措施。
详情请参考持续改进控制程序。
6.8
交付:
顾客未识别的不合格品的处理:
产品交付后,如果公司发现产品的安全性和可靠性严重不合格,发现部门应通知商务部。
门商务部通知总经理办公室:
开发部、质量控制部、生产部等相关部门讨论对策并进行现场修复、销毁、或召回等。
业务部门应将处理结果及时通知客户。
6.9
所有通过“损坏检验”的产品或零件应视为不合格产品,并标有红色“不合格”标签。
并从原始批次开始执行提货程序。
“破坏性”测试显示在提货清单上。
6.10
如有合同要求,所有“特许权授予”应通知客户并经客户批准。
6
/
6