机械制造工艺及机床夹具设计毕业论文.docx
《机械制造工艺及机床夹具设计毕业论文.docx》由会员分享,可在线阅读,更多相关《机械制造工艺及机床夹具设计毕业论文.docx(20页珍藏版)》请在冰豆网上搜索。
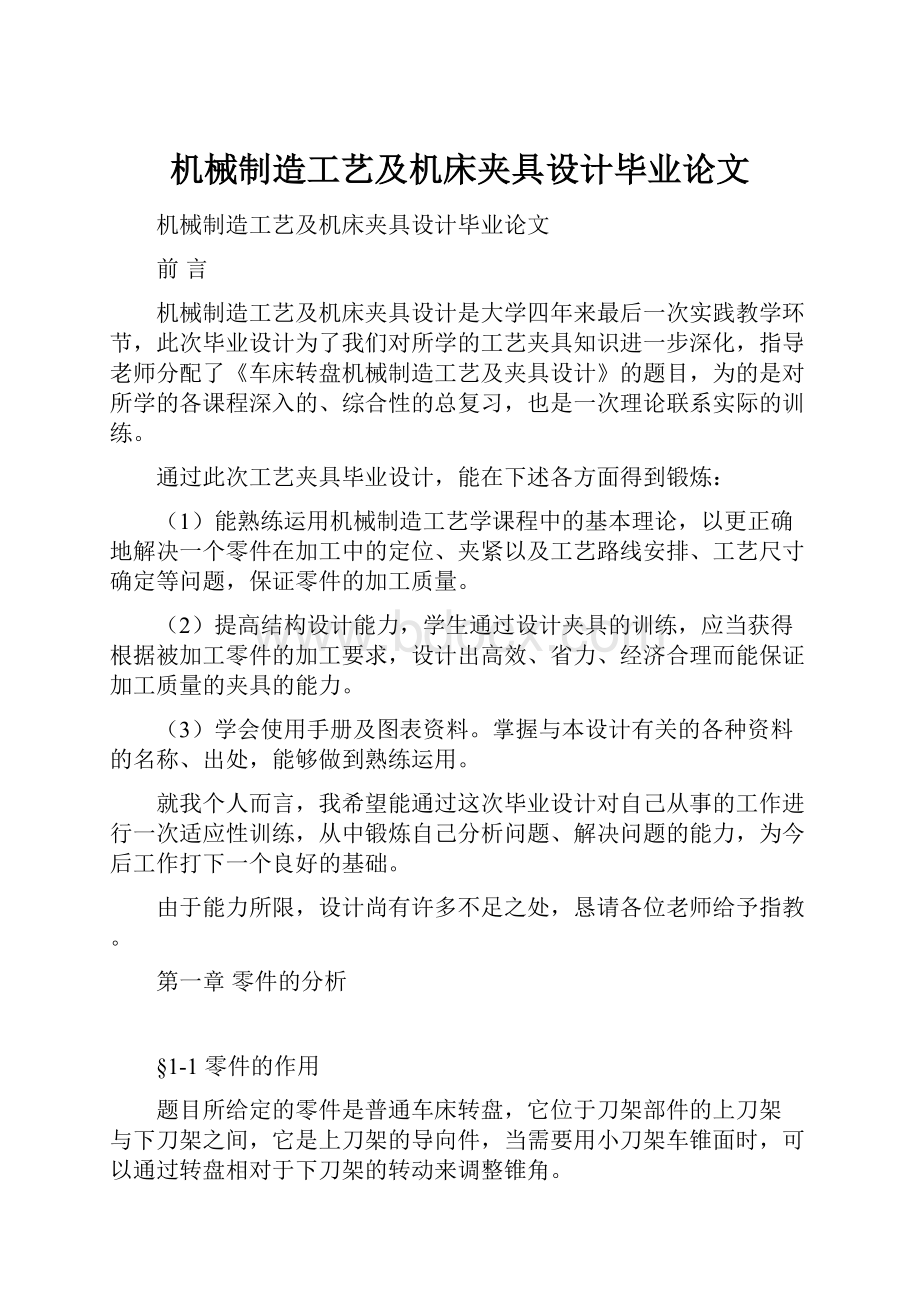
机械制造工艺及机床夹具设计毕业论文
机械制造工艺及机床夹具设计毕业论文
前言
机械制造工艺及机床夹具设计是大学四年来最后一次实践教学环节,此次毕业设计为了我们对所学的工艺夹具知识进一步深化,指导老师分配了《车床转盘机械制造工艺及夹具设计》的题目,为的是对所学的各课程深入的、综合性的总复习,也是一次理论联系实际的训练。
通过此次工艺夹具毕业设计,能在下述各方面得到锻炼:
(1)能熟练运用机械制造工艺学课程中的基本理论,以更正确地解决一个零件在加工中的定位、夹紧以及工艺路线安排、工艺尺寸确定等问题,保证零件的加工质量。
(2)提高结构设计能力,学生通过设计夹具的训练,应当获得根据被加工零件的加工要求,设计出高效、省力、经济合理而能保证加工质量的夹具的能力。
(3)学会使用手册及图表资料。
掌握与本设计有关的各种资料的名称、出处,能够做到熟练运用。
就我个人而言,我希望能通过这次毕业设计对自己从事的工作进行一次适应性训练,从中锻炼自己分析问题、解决问题的能力,为今后工作打下一个良好的基础。
由于能力所限,设计尚有许多不足之处,恳请各位老师给予指教。
第一章零件的分析
§1-1零件的作用
题目所给定的零件是普通车床转盘,它位于刀架部件的上刀架与下刀架之间,它是上刀架的导向件,当需要用小刀架车锥面时,可以通过转盘相对于下刀架的转动来调整锥角。
§1-2零件的工艺分析
从零件图上可以看出,它的加工部分可分成四部分:
1、底面P及φ70h6mm外圆面N,空刀面、凹台面及倒角;
2、燕尾面H及导轨面M,空刀面、凹台面及倒角;
3、φ35H7mm孔;
4、φ196mm圆弧面和尺寸132mm两侧面K及其端面Q;
以上各部分之间的位置要求为:
1、φ70h6mm外圆面N与P面有垂直度要求,垂直度公差为φ0.02mm;
2、燕尾面M与P面有平行度要求,平行度公差为0.04mm;
3、φ35H7mm孔与端面P有垂直度要求,垂直度公差φ0.1mm;
4、燕尾槽两55°斜面平行度为0.02mm;
由以上分析可知:
对于头二组加工面来说,我们可以先选择其中一组表面进行加工,然后再以加工过的表面为基准,加工其他各组表面,并保证它们之间的位置精度。
§1-3零件的材质.热处理及机械加工的工艺性
转盘采用HT200铸件,灰口铸铁是指具有片状石墨的铸铁,它在机械制造中占有重要地位,其产量占各类铸铁总产量80%以上。
灰口铸铁的性能有:
(1)机械性能:
灰口铸铁的抗拉强度和弹性模量均比钢低得多,通常σb仅120~250MPa,而塑性和韧性近于零,属于脆性材料。
(2)工艺性能:
灰口铸铁属于脆性材料,不能锻造和冲压。
同时,焊接时产生裂纹的倾向大;焊接区常出现白口组织,使焊后难以切削加工,故可焊性较差。
但灰口铸铁的铸造性能优良,铸件产生缺陷的倾向小。
此外,由于石墨的存在,切削加工时呈崩碎切屑,通常不需切削液,故切削加工性能好。
(3)减振性:
敲击铸铁时声音低沉,余音比钢短甚多,这是由于石墨对机械振动起缓冲作用、阻止了振动能量传播的结果。
灰口铸铁的减振能力为钢的5~10倍,是制造机床床身、机座的好材料。
(4)耐磨性:
灰口铸铁磨擦面上开成了大量显微凹坑,能起储存润滑油作用,使磨擦副内容易保持油膜的连续性。
同时,石墨本身也是良好的润滑剂,当其脱落在摩擦面上时,可起润滑作用。
因此,灰口铸铁的耐磨性比钢好,适于制造导轨、衬套、活塞环等。
(5)缺口敏感性:
由于石墨已使灰口铸铁在基体形成了大量缺口,因此外来缺口对灰口铸铁的疲劳强度影响甚微,故其缺口敏感性低,从而增加了零件工作的可靠性。
与之相比,钢件若有上述外来缺口,因应力集中作用,其疲劳强度将显著降低。
灰口铸铁的机械性能除取决于石墨的数量、大小和分布等因素外,还与金属基体的类别密切相关。
第二章零件工艺规程设计而塑性和韧性近于零,属于脆性材料。
(2)工艺性能:
灰口铸铁属于脆性材料,不能锻造和冲压。
同时,焊接时产生裂纹的倾向大;焊接区常出现白口组织,使焊后难以切削加工,故可焊性较差。
但灰口铸铁的铸造性能优良,铸件产生缺陷的倾向小。
此外,由于石墨的存在,切削加工时呈崩碎切屑,通常不需切削液,故切削加工性能好。
(3)减振性:
敲击铸铁时声音低沉,余音比钢短甚多,这是由于石墨对机械振动起缓冲作用、阻止了振动能量传播的结果。
灰口铸铁的减振能力为钢的5~10倍,是制造机床床身、机座的好材料。
(4)耐磨性:
灰口铸铁磨擦面上开成了大量显微凹坑,能起储存润滑油作用,使磨擦副内容易保持油膜的连续性。
同时,石墨本身也是良好的润滑剂,当其脱落在摩擦面上时,可起润滑作用。
因此,灰口铸铁的耐磨性比钢好,适于制造导轨、衬套、活塞环等。
(5)缺口敏感性:
由于石墨已使灰口铸铁在基体形成了大量缺口,因此外来缺口对灰口铸铁的疲劳强度影响甚微,故其缺口敏感性低,从而增加了零件工作的可靠性。
与之相比,钢件若有上述外来缺口,因应力集中作用,其疲劳强度将显著降低。
灰口铸铁的机械性能除取决于石墨的数量、大小和分布等因素外,还与金属基体的类别密切相关。
第二章零件工艺规程设计
§2-1确定零件生产类型
零件生产纲领为:
N=Qn(1+α%)(1+β%)
其中:
Q=200—产品的年产量(台/年)
n=1—每台产品中,该零件的数
量(件/台)
α=1%—零件备品率
β=3%—零件废品率
∴N=200×1×(1+1%)×(1+3%)
=208.06件/年
根据《机械制造工艺学》表1-3,可知零为中批生产。
§2-2确定零件毛坯的制造形式
影响毛坯选择的因素通常包括:
1、零件材料的工艺性及零件对材料组织的要求;
2、零件的结构形状和外形尺寸;
3、零件对毛坯精度、表面光洁度和表面层性能的要求;
4、零件生产纲领的大小;
5、现有生产能力和发展前途;
车床转盘材料为HT200(灰口铸铁),由于零件年产量为375件,已达到中批生产水平,故可采用金属模铸造毛坯(金属型)。
金属型铸造具有许多优越性。
如可承受多次浇注,实现了“一型多铸”,便于实现机械化和自动化生产,从而大大提高了生产率;同时,铸件精度和表面质量比砂型铸造显著提高,从而节省金属和减少切削加工工作量;由于结晶组织致密,铸件的机械性能得到提高。
此外,节省许多工序,造型不用砂,使铸造车间面貌改观,劳动条件改善。
毛坯尺寸通过确定加工余量后决定。
§2-3制定工艺路线
一、制定工艺路线的依据
应使零件上的各尺寸精度、位置精度、表面光洁度和各项技术要求均能得到保证。
由本转盘生产纲领确定为中批生产,因此,可以考虑采用万能机床配以专用夹具,这样既可以提高生产率,又可提高加工精度,且可使生产成本降低,以获得最好的经济效果。
加工顺序按以下原则确定:
先粗加工,后精加工;先主要表面,后次要表面;先基准面,后其它面;先加工平面,后加工孔。
二、两种工艺路线方案
(一)工艺路线方案一:
工序1铸造毛坯
工序2时效处理
工序3粗铣燕尾面M、空刀槽、H
工序4粗铣尺寸234mm两端面Q
工序5粗车、半精车、精车φ70h6外圆
面N、空刀面、端面P、倒角
工序6精铣燕尾面M、H
工序7精铣尺寸234mm两端面Q
工序8倒角1×45°
工序9粗铣φ196圆弧面、132mm两端
面K
工序10倒角1×45°
工序11钻、扩、粗、精铰φ35H7mm孔
工序12钻2-φ13mm孔
工序13去毛刺
工序14检验
(二)工艺路线方案二:
工序1铸造毛坯
工序2时效处理
工序3毛坯划线
工序4粗车、半精车φ70h6外圆面N、
空刀面、端面P、倒角
工序5粗铣尺寸234mm的两端面
工序6粗铣空刀槽
工序7粗铣燕尾面M、H面、空刀面、
倒角
工序8精车φ70h6mm外圆面N、端面
P、倒角
工序9检验
工序10精铣燕尾面M、H、空刀面
工序11检验
工序12粗铣φ196mm圆弧面及尺寸
132mm两侧面K
工序13精铣尺寸234mm两端面Q
工序14检验
工序15精铣φ196mm圆弧面及尺寸
132mm两侧面K
工序16检验
工序17钻、扩、粗、精铰φ35H7mm孔
工序18钻2-φ13mm孔
工序18检验
工序19刮研燕尾面
工序20终检
三、工艺方案的比较与分析
方案一是先加工燕尾面M、H,然后以此面为基面加工其它各主要表面,从而保证各表面的技术要求。
而方案二是先加工底面P,然后以底面P为基面加工其它各主要表面来保证其技术要求。
燕尾面M位于小刀架下方,是保证上刀架加工精度的主要表面。
方案一先加工燕尾面,以底面P为定位面,再以燕尾面为精加工基准加工其它各主要表面能够很好保证燕尾面相对其它各面的精度要求,且使导轨面M有均匀的金相组织和较高的耐磨性,加工余量小而均匀。
方案二则先加工底面P,以燕尾面为粗基准,再以P面为精基准加工其它表面,能够保证P面(主定位面)与其它各表面的形位精度,且满足基准重合原则。
但两方案中燕尾面M和底面P间有较高的位置精度,可采用互为基准原则,同样都能保证M、P间形位精度,都能满足基准选择原则,为保证导轨燕尾面有较高精度,现取方案一为本次工艺编制的工艺路线。
但方案一中仍有不足之处,将粗、精加工分开是因为粗加工时切削余量大,其变形可能影响后道工序的加工精度,但本次设计零件采用金属型浇注,毛坯精度高,加工余量小,相对来说粗加工切削余量不是很大,考虑到为减少装夹次数,所以将方案一中有些工序粗、精加工放入一个工序中进行,以减少工时和人力的浪费,因此确定以下工艺路线:
工序1铸造毛坯
工序2时效处理
工序3粗铣燕尾面M、空刀槽、H
工序4粗铣尺寸234mm两端面Q
工序5粗车、半精车、精车φ70h6外圆
面N、空刀面、端面P、倒角
工序6精铣燕尾面M、H
工序7精铣尺寸234mm两端面Q
工序8粗铣φ196圆弧面、132mm两端
面K
工序9倒角1×45°
工序10钻、扩、粗、精铰φ35H7mm孔
工序11钻2-φ13孔
工序12去毛刺
工序13检验
§2-4基准的选择
基准选择是工艺规程设计中的重要工作之一。
基准选择得正确合理可以使加工质量得到保证,生产率得以提高。
否则,加工工艺过程中会问题百出,更有甚者,还会造成零件大批报废,使生产无法正常进行。
1、粗基准的选择
按照有关粗基准的选择原则,即当零件有不加工表面时,应以不加工表面为基准;为了合理确定加工余量,应以重要表面做为粗基准;粗基准为不加工表面时,只能用一次。
2、精基准的选择
选择精基准时,应能保证加工精度的装夹可靠方便,可按下列原则选取。
(1)基准重合原则
采用设计基准作为定位基准称为基准重合原则。
为避免基准不重合而引起的基准不重合误差,保证加工精度应遵循基准重合原则。
(2)基准统一原则
在工件的加工过程中尽可能地采用统一的定位基准,称为基准统一原则(也称基准单一原则或基准不变原则)。
(3)自为基准的原则
当某些表面精加工要求加工余量小而均匀时,选择加工表面本身作为定位基准称为自为基准原则。
遵循自为基准原则时,不能提高加工面的位置精度,只是提高加工面本身的精度。
(4)互为基准原则
为了使加工面间有较高的位置精度,又为了使其加工余量小而均匀,可采取反复加工、互为基准的原则。
(5)保证工件定位准确、夹紧可靠、操作方便的原则
所选精基准应能保证工件定位准确、稳定,夹紧可靠。
精基准应该是精度较高、表面精糙度值较小、支承面积较大的表面。
转盘的精基准采用互为基准原则进行加工这样可以保证位置精度,又可使其加工余量小而均匀。
§2-5用查表法确定各工序余量、工序尺寸
及毛坯尺寸
《简明手册》表2.2-4及《机械制造工艺学》表1-10
(1)φ70h6外圆面N
(2)端面P
§2-6各工序工艺装备、切削用量
及工时定额
工件材料:
HT200,金属模浇注
HB=190N/mm2
1、粗铣燕尾面M、H
机床:
万能铣床X62W
刀具:
YG6单面铣刀GB6126-85
查《金属机械加工工艺人员手册》
铣刀直径D=80mm
每齿进给量af=0.20mm/z
切削速度v=1000V/(π×d0)=376.8m/min
(M面)
v=94.2m/min(H面)
进给量Sm=0.2mm/r
主轴转速?
n=1500r/min(M面)
n=375r/min(H面)
基本工时
Tj=2.22+8.46=10.68s=0.178min
2、铣空刀槽2×2mm
机床:
万能铣床X62W
刀具:
高速钢错齿三面刃铣刀GB1118-73
每齿进给量af=0.063mm/z
切削速度v=20m/min
主轴转速n=95r/min
基本时间T=46.6s=0.8min
3、粗铣234mm两端面Q
机床:
万能铣床X62W
刀具:
YG6镶齿圆柱铣刀
查《金属机械加工工艺人员手册》表8-38
每齿进给量af=0.30mm/z
切削速度v=60m/min
进给量Sm=0.3mm/r
主轴转速?
n=95r/min
基本工时Tj=90s=1.5min
4、粗、半精车Φ70h6外圆面N、端面P,粗车空刀面
机床:
WNC-700S数控车床
刀具:
刀片材料:
CNMG16016MR
刀片牌号:
3015
刀片外形:
80°外圆刀
切削深度ap粗=10mm
ap半精=3mm
切削速度v=80m/min
主轴转速n=1000v/(π×d0)=127r/min
切削工时Tj=15+10=25min
5、精车Φ70h6外圆面N、端面P
机床:
WNC-700S数控车床
刀具:
刀片材料:
DNMG150408KF
刀片牌号:
3005
刀片外形:
55°外圆刀
切削深度ap=1mm
切削速度v=120m/min
主轴转速n=191r/min
切削工时Tj=10min
6、精铣燕尾面M、H
机床:
选用立式铣床
刀具:
YG6单角铣刀GB6126-85
查《金属机械加工工艺人员手册》
铣刀直径D=80mm
每齿进给量af=0.20mm/z
切削速度v=376.8m/min(M面)
v=150.72m/min(H面)
进给量Sm=0.2mm/r
主轴转速?
n=1500r/min(M面)
n=600r/min(H面)
基本工时Tj=2.22+5.28=7.5s=0.125min
7、精铣234mm两端面Q
机床:
万能铣床X62W
刀具:
YG6镶齿圆柱铣刀
查《金属机械加工工艺人员手册》表8-38
每齿进给量af=0.25mm/z
切削速度v=70m/min
进给量Sm=0.25mm/r
主轴转速?
n=95r/min
基本工时Tj=54s=0.9min
8、倒角1×45°
机床:
卧式车床C620-1
刀具:
成形车刀
切削深度ap=0.16mm
切削速度v=20m/min
主轴转速n=95r/min
切削工时Tj=0.64min
9、粗铣Φ196圆弧面
机床:
万能铣床X62W
刀具:
镶硬质合金刀片套式铣刀
铣刀直径D=20mm
《工艺人员手册》表8-38
每齿进给量Sz=0.08mm
切削速度v=80m/min
主轴转速n=118r/min
基本时间T=0.3min
10、粗铣132mmK面
机床:
万能铣床X62W
刀具:
镶硬质合金刀片套式铣刀
铣刀直径D=20mm
《工艺人员手册》表8-38
每齿进给量Sz=0.08mm
切削速度v=85m/min
主轴转速n=190r/min
基本时间T=0.64min
11、倒角1×45°
机床:
卧式车床C620-1
刀具:
成形车刀
切削深度ap=0.16mm
切削速度v=20m/min
主轴转速n=120r/min
切削工时Tj=1.34min
12、钻、扩、粗、精铰Φ35H7孔
1)钻Φ35H7孔
机床:
立式钻床Z535
刀具:
高速钢锥柄麻花钻
切削深度ap=1.75mm
切削速度v=25m/min
主轴转速n=275r/min
切削工时Tj=0.25min
2)扩Φ35H7孔
机床:
立式钻床Z535
刀具:
高速钢锥柄扩口钻
切削深度ap=0.58mm
切削速度v=15m/min
主轴转速n=140r/min
切削工时Tj=0.28min
3)粗铰Φ35H7孔
机床:
立式钻床Z535
刀具:
高速钢锥柄机用铰刀
切削深度ap=0.27mm
切削速度v=7.2m/min
主轴转速n=68r/min
切削工时Tj=0.41min
4)精铰Φ35H7孔
机床:
立式钻床Z535
刀具:
高速钢锥柄机用铰刀
切削深度ap=0.15mm
切削速度v=10.8m/min
主轴转速n=100r/min
切削工时Tj=0.52min
13、钻2-Φ13mm孔
机床:
立式钻床Z535
刀具:
高速钢锥柄麻花钻
进给量f=0.32mm/r
切削深度ap=7.5mm
切削速度v=27.6m/min
主轴转速n=275r/min
基本工时Tj=0.32min
以上各工序切削用量、工时定额的计算结果,
填入《机械加工工艺过程综合卡片》
第三章夹具设计
§3-1概述
在机床上对零件进行机械加工时,为保证工件加工精度,首先要保证工件在机床上占有正确的位置,然后通过夹紧机构使工件的正确位置固定不动,这任务就是由夹具完成。
对于单件、小批生产,应尽量使用通用夹具,这样可以降低落件的生产成本。
但由于通用夹具适用各种工件的装夹,所以夹紧时往往较费时间,并且操作复杂,生产效率低。
本零件属于中批生产,零件外形也不适于使用通用夹具,为了保证工件加工精度,提高生产效率,设计专用夹具就显得非常必要。
§3-2方案设计
方案设计是夹具设计的第一步,也是夹具设计关键的一步,方案设计的好坏直接影响工件的加工精度,加工效率,稍不注意就会造成不能满足工件加工要求,或加工精度不能达到设计要求,因此必须慎重考虑。
设计方案的拟定必须遵循下列原则:
①定位装置要确保工件定位准确和可靠,符合六点定位原理。
②夹具的定位精度能满足工件加工精度的要求。
③夹具结构尽量简单,操纵力小而夹紧可靠,力争造价低。
1、问题的提出:
本夹具主要用车外圆面N、空刀面、端面P、倒角,这几个面有一定的技术要求。
因在数控机床上加工,所以在本道工序加工时主要应考虑如何提高劳动生产率,降低劳动强度,而精度不是主要问题。
2、定位基准的选择:
工件以端面M限制三个自由度,以燕尾面H限制两个自由度,又以端面Q限制一个自由度来实现完全定位。
3、转盘车夹具原理
本夹具用于转盘中批生产工艺的工序8,在车床上加工转盘底面P、外圆面N、端面L和倒角、空刀等。
本工序前的已加工表面燕尾导轨面H、M及两端Q、R面。
工件以M面限制三个自由度,以燕尾面H限制两个自由度;又以端面Q限制一个自由度,实现完全定位。
夹具通过手动螺旋夹紧机构。
在夹紧工件时,首先拧动勾形压板12的夹紧螺母,使工件靠紧在定位钉8上。
然后拧动浮动压板4的夹紧螺钉7,在燕尾斜面分力的作用下使工件靠紧在主定位面上,实现工件的夹紧。
松夹时,先拧动浮动压板4的压紧螺钉7,在压簧6的作用下,使浮动压板离开工件。
然后拧松勾形压板12的压紧螺母,在压簧作用下勾形压板松开。
最后将勾形压板转过90°即可装卸工件。
本夹具安装在车床主轴上,以夹具D面与锥孔为基准,并用螺栓3紧固。
本夹具结构紧凑,操作方便,适合于中小批生产中使用。
4、转盘车夹具夹紧力计算
由图和《切削用量简明手册》37页表1.29知,
主切削力
Fc=CFc×apxFc×fyFc×vcyFc×kFc
径向切削力
Fp=CFp×apxFp×fyFp×vcyFp×kFp
进给力(轴向力)
Ff=CFf×apxFf×fyFf×vcyFf×kFf
公式中的系数及指数,由加工材料为灰铸铁,硬度为190HBS,刀具材料为硬质合金,加工形式为外圆纵车、横车选
CFc=900xFc=1.0yFc=0.75nFc=0
CFp=530xFp=0.9yFc=0.75nFp=0
CFf=450xFf=1.0yFf=0.4nFf=0
其中ap=3mmf=0.6mm/rvc=80m/min
由表1.29-2加工钢及铸铁时刀具几何参数改变时切削力的修正系数得,
kFc=kkrFc×kroFc×kλsFc×krεFc
kFp=kkrFp×kroFp×kλsFp×krεFp
kFf=kkrFf×kroFf×kλsFf×krεFf
其中kkrF为主偏角改变时切削力的修正系数
kroF为前角改变时切削力的修正系数
kλsF为刃倾角改变时切削力的修正系数
krεF为刀尖圆弧半径改变时切削力的修
正系数
80°外圆刀主偏角为90°,前角为-10°,刃倾角为-5°,
∴kFc=0.89×1.2×1.0×1.0=1.068
kFp=0.5×1.8×1.25×1.0=1.125
kFf=1.17×1.8×0.85×1.0=1.7901Fc=900×31.0×0.60.75×800×1.068
=1965.8N
Fp=530×30.9×0.60.75×800×1.125
=1092.6N
Ff=450×31.0×0.60.4×800×1.7901
=1970.02N
由Fp=G+FJ2
∴FJ2=1092.6-9×10=1002.6N
由FJ1×f1×r1+FJ2×f2×r2=Mc=Fc×rc
其中f1、f2由工程力学68页表2.2知钢对铸铁f1=f2=0.18
∴FJ1×0.18× +FJ2×0.18
×88=1965.8×88
∴FJ1=7307.4N
由FJ1实=FJ1×KK=1.5
得FJ1实=10961.1N
由FJ2实=FJ2×KK=1.5
得FJ2实=1503.9N
FQ1=FJ1×(1+3Lf/H)
=FJ1×(1+3×110×0.41/19.5+27)
=18739.94516N
其中L为力臂(mm)f为摩擦系数
F1手=FQ1/110=170N=17kg可实现。
同理可知,F2手可实现。
5、定位误差分析
设计基准与定位基准重合,误差为0。
参考文献
《机械制造工艺学课程设计指导书》赵家齐编机械工业出版社
《机床夹具设计手册》上海科学技术出版社
《机械制造工艺设计手册》王绍俊编哈尔滨工业大学
《简明手册》李益民编机械工业出版社
《切削用量手册》艾兴肖诗纲编机械工业出版社
《机械制造工艺学》郑修本主编机械工业出版社
《机械制图》高等教育出版社
《互换性与技术测量》廖念钊主编中国计量出版社
《金属切削原理与刀具》陆剑中孙家宁主编
《金属工艺学》邓文英主编高等教育出版社
《机械零件设计手册》冶金工业出版社
《金属机械加工工艺人员手册》上海科学技术出版社
《毕业设计指导书》辽宁科学技术出