炼油装置开停工及检修过程典型事故事件汇编1.docx
《炼油装置开停工及检修过程典型事故事件汇编1.docx》由会员分享,可在线阅读,更多相关《炼油装置开停工及检修过程典型事故事件汇编1.docx(40页珍藏版)》请在冰豆网上搜索。
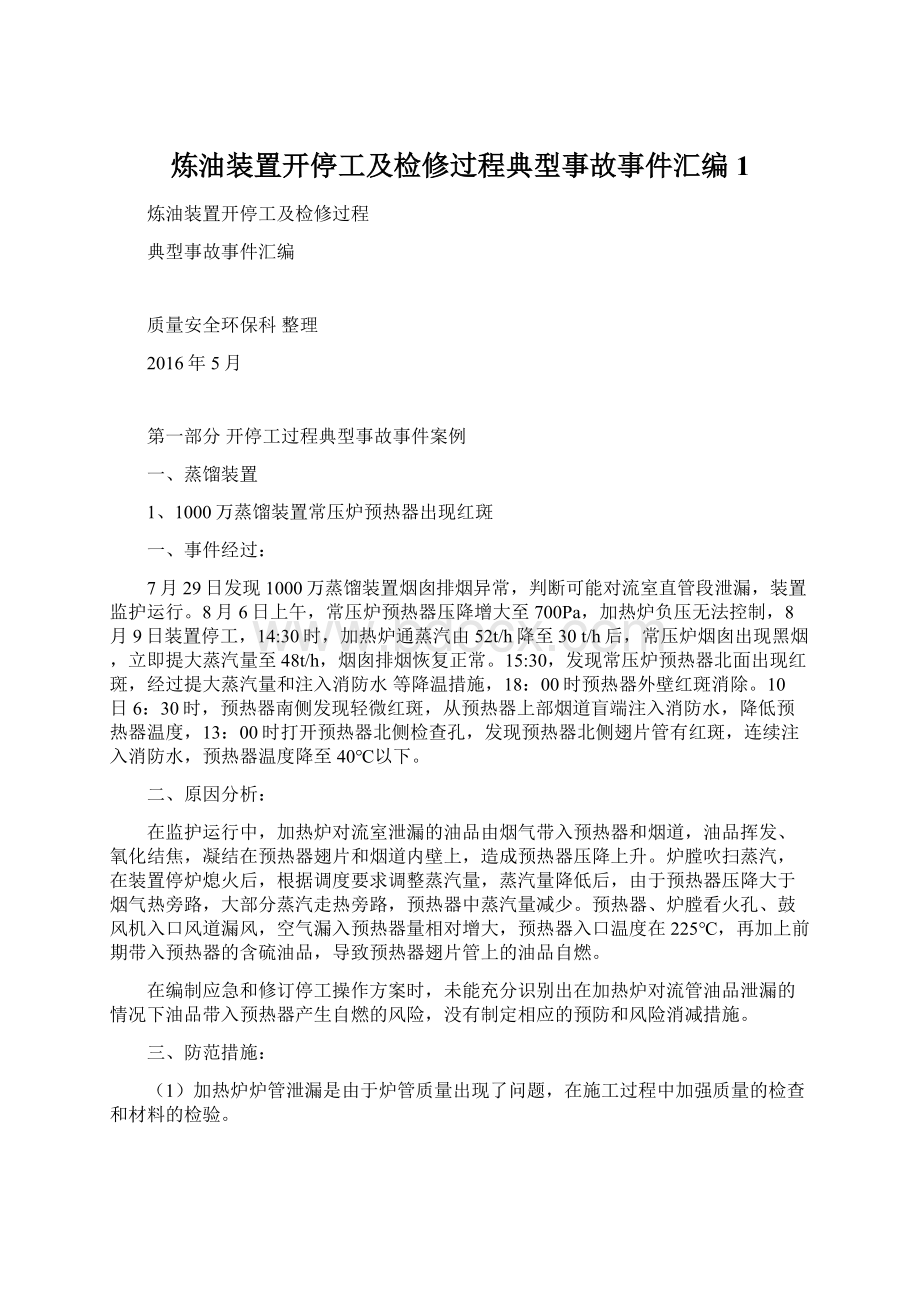
炼油装置开停工及检修过程典型事故事件汇编1
炼油装置开停工及检修过程
典型事故事件汇编
质量安全环保科整理
2016年5月
第一部分开停工过程典型事故事件案例
一、蒸馏装置
1、1000万蒸馏装置常压炉预热器出现红斑
一、事件经过:
7月29日发现1000万蒸馏装置烟囱排烟异常,判断可能对流室直管段泄漏,装置监护运行。
8月6日上午,常压炉预热器压降增大至700Pa,加热炉负压无法控制,8月9日装置停工,14:
30时,加热炉通蒸汽由52t/h降至30t/h后,常压炉烟囱出现黑烟,立即提大蒸汽量至48t/h,烟囱排烟恢复正常。
15:
30,发现常压炉预热器北面出现红斑,经过提大蒸汽量和注入消防水等降温措施,18:
00时预热器外壁红斑消除。
10日6:
30时,预热器南侧发现轻微红斑,从预热器上部烟道盲端注入消防水,降低预热器温度,13:
00时打开预热器北侧检查孔,发现预热器北侧翅片管有红斑,连续注入消防水,预热器温度降至40℃以下。
二、原因分析:
在监护运行中,加热炉对流室泄漏的油品由烟气带入预热器和烟道,油品挥发、氧化结焦,凝结在预热器翅片和烟道内壁上,造成预热器压降上升。
炉膛吹扫蒸汽,在装置停炉熄火后,根据调度要求调整蒸汽量,蒸汽量降低后,由于预热器压降大于烟气热旁路,大部分蒸汽走热旁路,预热器中蒸汽量减少。
预热器、炉膛看火孔、鼓风机入口风道漏风,空气漏入预热器量相对增大,预热器入口温度在225℃,再加上前期带入预热器的含硫油品,导致预热器翅片管上的油品自燃。
在编制应急和修订停工操作方案时,未能充分识别出在加热炉对流管油品泄漏的情况下油品带入预热器产生自燃的风险,没有制定相应的预防和风险消减措施。
三、防范措施:
(1)加热炉炉管泄漏是由于炉管质量出现了问题,在施工过程中加强质量的检查和材料的检验。
(2)在加热炉炉管发现泄漏时,应根据生产情况,及时采取措施停炉检查消漏,防止事态扩大。
在停炉操作过程中,严格控制烟道中的氧含量,落实防止预热器发生自燃的风险措施。
(3)考虑到炉管泄漏和硫化亚铁自然的风险,在本次大修中增加预热器系统消防蒸汽和注水设施。
2、1000万蒸馏装置酸性水带烃
一、事件经过:
2014年12月18日1:
30时,脱乙烷塔顶回流罐V-303界面上升至56%,装置内操联系外操切液,1:
35外操到现场进行切液操作,1:
46第二联合车间第一套非加氢型酸性水汽提装置原料缓冲罐V-101压力PI1004由5kPa上升至180kPa,安全阀启跳;2014年12月23日15:
10至15:
10时,脱丁烷塔顶回流罐V-302切液时,内外操沟通不及时,第二联合车间第一套非加氢型酸性水汽提装置原料缓冲罐V-101压力PI1004上升至94kPa;2014年12月27日12:
27至12:
30时,脱乙烷塔顶回流罐V-303切液,内操用调节阀操作,现场沟通不及时,12:
30时二联合酸性水汽提装置原料闪蒸罐压力迅速上升至150kPa,安全阀起跳。
二、原因分析:
(1)脱乙烷塔顶回流罐V-303脱水包进行切水操作时,将V-303内液化气串入酸性水出装置管线,进入酸性水汽提装置。
(2)脱乙烷塔顶回流罐V-303界面LC3008指示偏差大,切水操作时,V-303界面LC3008从56%下降至53.5%时,V-303内液化气即串至酸性水线;现场玻璃板界面计位置不便于观察。
(3)在《脱乙烷塔顶回流罐V-303切水操作卡》的风险提示卡中明确有“防止液化气串入酸性水进入下游装置”、“切液时阀门开度不可过大”的风险提示内容;在外操的操作步骤中,明确有“切液时与内操联系将现场界面计与DCS值进行对比”。
在操作过程中,操作卡执行不到位。
三、防范措施:
(1)定期查看现场玻璃板界面计指示值,与DCS上界面计测量值进行对比,发现异常及时联系仪表进行处理;V-303界面计指示偏差频繁,配合仪表车间查询原因,消除故障。
(2)严格执行操作卡,做到步步确认;
(3)更换现场玻璃板液位计,方便观察界面;
(4)增设低界位≤20%全关闭界面调节阀逻辑程序;
(5)将脱乙烷塔回流罐V-303切水改进脱丁烷塔回流罐V-302(V-302产生水量可以满足调节阀自动控制要求);
(6)排查评估全厂类似切水操作现状,举一反三,消除隐患。
(7)酸性水闪蒸罐安全阀定压值小调至0.12Mpa。
(8)增设酸性水闪蒸罐低液面关闭也为调节阀的逻辑程序。
二、催化裂化装置
1.催化裂化再生器超温
一、事件经过:
1998年6月4日Ⅰ催化装置开工进入两器升温后期,按计划进行原料循环脱水。
在16:
30分将原料引进装置至6月5日4:
30分长达12小时内,岗位操作人员只向原料车间量油岗位要了三次油位。
实际在此期间,原料已串入分馏塔。
到6月5日凌晨4:
40分再生器分布管下温度指示超程(>1000℃),造成再生器内分布管、一级料腿、大型卸料线、再生器部分衬里、热电偶及热电偶套管烧坏。
二、原因分析:
(1)分馏塔底油浆过滤器付线阀被焦块卡住未关严,且分馏塔底总阀未关,造成馏分油窜入分馏塔经900油气线进入反应器,有反应器的待斜管窜入再生气是引发这次事故的直接原因。
(2)操作规程不完善。
负责分馏系统开工的车间工艺技术员和分馏岗位操作工均是首次单独负责开工,开工经验不足,巡检又不到位。
当油位出现异常情况时,没有及时进行核算和查明原因,也未及时向车间领导汇报,继续进行原料循环操作,致使馏份油窜入分馏塔长达11个小时,这是造成此次事故的直接原因。
(3)当班人员在处理再生器超温时,启用主风自保后,但大型卸料线的输送风未及时关闭,是造成再生器内部构件烧坏的原因之一。
三、防范措施:
(1)在装置开停工等重要生产工作安排上,机关处室及机关领导要精心组织,加强力度。
(2)相关处室要督促检查车间对生产岗位责任制执行情况,尤其是在装置开停工过程中认真巡检,按时做好记录,严格执行操作规程。
对装置引物料进出装置一定要进行核算。
炼油厂相关处室一定要尽快制订出相应的管理制度,在操作过程中出现异常情况时要及时向车间领导和调度部门汇报,必须在查清原因在进行下一步操作。
(3)加强对开工中无法打盲板的流程上的关键阀门的试压工作,防止引物料或物料循环过程中窜入其它设备内。
(4)将分馏塔底油浆过滤器付线阀拆下除焦,并改为水平安装。
(5)要加强车间领导对开工全过程的层层把关和组织。
2.轻烃窜入单塔汽提装置造成原料罐损坏
一、事故经过:
2008年9月19日I催化装置开工至产品合格,9月20日工艺四班上二班,接班后值班干部李某安排班组投用R-206、R-301罐水洗。
当班班长殷某20:
20分联系调度准备投用。
岗位操作工陈某20:
30分先对R-206罐进行补水,于20:
47分R-206罐界面自动控制投用正常。
此时对R-301罐进行补水操作,随后岗位人员陈某直接将R-301罐界面控制阀前后手阀打开,导通外送污水流程。
20:
55分R-201罐界面开始上升,班组认为是R-206罐含硫污水外放影响,将R-206罐水洗水量关小,R-201罐界面仍然不下,后将R-301罐水洗水关小,21:
09分将水洗水全部关闭。
9月20日单塔汽提装置工艺四班上二班,20点59分突然听到两声异常响声,V-101/3液位从6.4米到1.2米之间波动,闪蒸塔压力由0.02MPa升至0.22MPa,V-101/3原料水罐罐顶周围冒出大量气体。
车间当班人员关掉V-101/3、4氮封,打开闪蒸塔脱水罐脱水阀泄压,联系调度汇报单塔原料水罐气相组分过大,23点13分闪蒸塔压力降至正常(0.02MPa)。
事后现场检查发现:
V-101/3原料水罐罐顶有约4米焊缝被拉裂,V-101/3,4两罐地脚螺栓被拉断、螺帽被拉掉,V-101/3罐顶部分栏杆损坏,两条进出口线轻微泄漏。
二、原因分析:
催化车间班组人员陈朝晖在向R-301罐内补水洗水后,R-301罐无水界面时,就把污水外送流程导通,导致R-301罐内富含液态烃的汽油组分随含硫污水窜到单塔汽提装置原料水罐,气化造成原料水罐闪爆,没有准确执行操作卡是此次事故发生的直接原因。
催化车间在装置开停工过程中组织协调不利,岗位间和内外操联系不足,在没有水界面时就把污水外送流程导通,班长、主操没有尽到监督、现场确认的责任是事故发生的重要原因之一。
2、催化车间近几年来由于员工变动大,车间的员工培训工作未跟上,操作工经验不足、技能欠缺,车间在此次开停工过程中,组织管理水平下滑,是事故发生的管理原因。
实际操作技能欠缺,凭操作经验做事。
三、防范措施:
(1)加强对开停工及其它重大操作的组织管理,加强岗位间、内外操的协调,保证能够准确按照规程和操作卡的内容执行操作调节,重视对操作结果的现场确认,杜绝和防止事故的发生。
(2)单位要加强对员工的培训,强化对上岗和考岗等考核中实际操作技能方面的要求。
(3)干部和班长安排工作,要进行风险识别,提醒操作工按照操作卡的内容,正确的完成操作步骤,并对关键的操作进行确认。
(4)要对开停工操作卡等进行严格评审和及时修订,要符合现场的实际,提高操作的可执行性,
增加操作卡提示栏中对操作风险和条件的相关内容,减少误操作。
(5)现场悬挂安全提示卡。
(6)安排技术课对本次事故进行学习,认真吸取教训。
(7)对开停工操作卡重新进行危害识别与评价,修订完善操作卡。
3、I催化检修气分丙烷窜入循环水线
一、事件经过:
2009年5月2日,一催化装置检修,催化车间自修人员发现L-304壳程放空有微量瓦斯汇报车间,车间立即组织对其他冷却器检查,发现L-301处放空也有微量瓦斯飘出,各施工点紧急停止施工。
检修前装置已吹扫并打盲板隔离,循环水系统因无总阀,关闭各冷却器循环水进出口阀,初步判断循环水中串入瓦斯,对I催化循环水出装置总线放空处取样分析,I催化循环水总排取样分析丙烷含量97%(v/v),判断气分L-207内漏,立即将气分L-207切除,联系检修对L-207进行处理,并对I催化所有水冷器进行循环水冲洗置换,催化车间、供排水车间对循环水系统线和装置线每2小时检测一次,防止可燃气再次窜入检修设备区域。
二、原因分析:
(1)I催化装置的循环水系统在装置界区无进、出口总线界区阀,运行气分装置L-207内漏时,导致可燃气体窜入检修设备。
(2)催化车间对循环水无界区隔断总阀存在危害认识不足,对停工检修期间存在的漏、窜危害,无针对性预防措施。
三、防范措施:
(1)利用两套装置都停工的条件下,在I催化装置循环水进、出口总线上增加总阀。
(2)定期对循环水进行检查有无瓦斯泄漏情况,防止发生互窜导致事故发生。
(3)循环水流程动火和进入有限空间作业必须打盲板确保有效隔离,防止系统内可燃物随循环水互窜影响作业安全。
各项检维修作业认真开展作业危害识别和风险评估,严格落实能量隔离措施,正确选择隔离方式。
4.二催化停工污水COD超标情况事件
一、事件经过:
2013年8月5日二催装置根据厂部安排开始进行停工操作,8月6日16:
00分馏重油清洗完成后,开始进行新水顶油,此操作向31#罐退油、水,未向污水排凝。
22:
00顶水完成,将分馏塔底和回炼油关内水转至泵抽空后,将分馏塔底残夜排至下水,同时进行管线排空,在22:
30至23:
30接到肖虹电话说二循污水COD在线分析仪显示污水COD含量在880mg/l左右,车间立即关小放空,减少排放,向污水排新水进行稀释,同时向调度、技术进行汇报,23:
30左右肖虹电话说二循污水COD在线分析仪显示污水COD含量在860mg/l左右,有下降趋势。
此时分馏塔底基本排空,已开始全面吹扫。
8月7日3:
00二催化总排污水COD含量3430mg/l超指标,19:
00COD含量:
859mg/l合格。
8月8日3:
00COD含量:
3306mg/l又再一次出现不合格,11:
00COD含量:
2107mg/l、14:
00COD含量:
2004mg/l、19:
00COD含量:
1364mg/l。
8月8日14:
00车间联系槽车将污水拉至工业水共拉8车,污水没有再排下水。
21:
00污水分析COD含量:
750mg/l。
之后污水COD分析分别为659mg/l、568mg/l、527mg/l、454mg/l、690mg/l合格。
二、原因分析:
1、经车间排查和与清洗厂商沟通咨询分析原因如下:
重油清洗采用柴油置换,清洗剂为油溶性,重油清洗时溶解到柴油里,新水顶油时与水接触容易造成柴油乳化,随着排凝进入下水,影响污水COD。
除臭剂会与系统中硫化氢等硫、氮化合物反应生成黑色物质,并使得COD上升。
从吸收稳定系统吹扫冷凝液取样颜色发黑,并含有大量的黑色悬浮物,判断系统腐蚀严重,吹扫造成大量杂质对污水的颜色和分析都有一定的影响。
2.管理原因
1.对重油清洗和除臭吹扫方案制订不细,与技术商沟通不够,采用了2011年一催化重油清洗和除臭吹扫的方案,只关注了污水硫化物的影响,未对污水可能造成COD的影响进行评估。
2.出现不合格后与上级部门沟通不够,对原因和污水系统采取的措施没有理解,在装置内部没有采取彻底的隔离措施,造成多次超标。
三、预防措施:
1.与技术商进一步沟通和技术交流,确定重油清洗和除臭钝化的技术方案和操作卡,减少对污水系统的影响,为后续装置再次使用此技术提供经验共享。
2.建议完善装置停工吹扫排气、排凝的收集回收措施,从根本上解决因停工操作造成的污水超标情况。
三、焦化装置
1、120万吨/年装置清焦作业人员烫伤
一、事件经过:
2012年5月10日,120万吨/年焦化装置组织焦炭塔C-101A顶馏出线清焦和疏通东西两支急冷油线作业,车间技术员张宗有进行作业许可证、能量隔离许可证的构建,并进行隔离操作,关闭相关阀门,并挂牌上锁,车间技术员赵永山确认签发作业许可证。
因馏出线隔断威兰阀门有汽封保护,作业许可证措施要求,注水利用高位差(DN600垂直管线约35米)建立水封隔绝。
10:
20分张宗有安排班组导通馏出线压水流程,建立水封。
11:
00分,七化建维保人员开始清焦作业,16:
00分馏出线清焦完毕,开始回装工作。
16:
39分张宗有安排班组开冷焦水泵进行馏出线压水操作冲洗焦块,16:
49分馏出线盲法兰密封面处突然喷出热水,此时,七化建两名维保人员正站在馏出线上准备紧螺栓,一人被喷出热水烫伤,经医院诊断为30%的混合Ⅱ度烫伤。
二、原因分析:
(1)项目负责人在焦炭塔(C-101A)馏出线顶部盲法兰紧固作业未完的情况下,安排班组开泵向馏出线压水,打破了稳态的水封,使得管线内被汽封蒸汽加热的水,从盲法兰密封处喷出,是导致事故发生的直接原因。
(2)能量隔离措施不到位。
作业许可证中要求“清焦前工艺班组馏出线进行压水操作”建立水封,但实际车间没有制定馏出线清焦作业水封的操作卡和建立水封方案,凭经验建立水封,是导致事故发生的主要原因。
(3)车间管理人员风险防控意识差,作业未完就安排顶水冲洗,操作与检修作业交叉进行,未识别出管线内水封被阀门汽封蒸汽密闭加温后潜在的危害,是导致事故发生的重要原因。
三、防范措施:
(1)各级管理人员和技术人员要认真落实检修作业和生产操作的安全界面确认,已交付检修作业现场和工艺流程,不应交叉进行生产操作,杜绝工作中的随意性,存在相互关联的不同检修作业,对相互之间影响进行风险评价,确保整体安全受控。
(2)各单位要认真执行能量隔离管理规定,对特殊隔离方式(水封、汽封、气封、黄泥封堵)应制定隔离方案,严格落实上锁挂签,对隔离效果有监测确认方式和指标,并严格执行相关作业管理程序。
专业部门按照能量隔离管理制度要求,认真履行本部门监督管理职责,加强现场监督检查力度,确保在现场有效执行。
(3)一联合车间对焦炭塔馏出线清焦作业方案进行完善,隔离水封建立后,对补水流程进行工艺隔离上锁挂签,并监控水封温度。
(4)各单位对作业的个体防护选择必须有针对性,落实制定防控措施必须考虑应急疏散条件,高处作业根据作业风险,设置作业平台与逃生通道,便于应急撤离。
(5)各单位要严格按照事故事件报告制度对发生的事故进行上报。
对事故发生后隐瞒不报、谎报、迟报的单位要进行严肃处理并追究事故发生单位领导责任。
(6)各单位立即将事故处理通报传达到每位员工,从事故中吸取教训,引以为戒,并结合本单位的实际,举一反三,对工艺处理及隔离情况,个人防护(PPE)使用进行排查,切实做好安全生产工作。
四、重整加氢装置
1、重整装置反应器R-103顶氢气线拆除着火
一、事故经过:
2011年8月16日,炼建公司金属结构厂施工人员按计划对重整旧反应器R-103顶氢气线进行气焊切割拆除。
动火作业前,施工人员将阀门后法兰断开敞口处理(阀前打盲板),并确认放空阀门处于打开状态。
车间监护人用四合一报警器从断开阀门处及放空阀门处对管线内进行气体监测合格,随即由施工人员进行拆除作业。
在第一处切割点(打盲板阀门后)切割后没发现异常情况,后在第二处切割点(阀门前弯头处)开始切割拆除,12:
05分切割点处存留凝水流出,凝水带残油被引燃,现场用1具灭火器灭火,12:
07分熄灭。
二、原因分析:
(1)此处管线弯头处无支撑,重力下沉形成局部低点,吹扫后冷凝水(有残油)积存在低点处,距管线放空阀门约3米,未检测到可燃气体,切割弯头时引燃残油是着火的直接原因。
(2)查R-103顶氢气线(拆除线)吹扫记录,8月8日15:
30分开汽扫至放空阀门排汽(阀门前盲板隔离),下部给汽向上吹扫,8月11日14:
20分停汽,吹扫70小时50分钟,排汽放空DN20管径,介质吹扫不彻底,残留可燃介质,是着火的重要原因之一。
(3)施工人员在切割点2时发现带少量残油的冷凝水流出,在切口处着火,没有停止作业,并通知车间处理,而是继续割除该段管线,凝水流出量增大,在架板上继续燃烧,是导致着火范围扩大的重要原因之一。
三、防范措施:
(1)严格执行所有管线、设备,第一次动火前采取断开法兰、开放空阀进行管线内部检查确认,内部经可燃气体检测合格后,方可进行动火作业的要求。
(2)动火切割设备和管线,尽量避开无法放空和拆开放空的低点部位,无法避开时,先在低点
锯开一小口,检查是否有残留,并进行气体检测合格后,方可动火。
(3)工艺吹扫过程严格确认检查,对易积存凝液的低点流程、副线盲端等部位进行放空或卸法兰确认,保证吹扫效果。
(4)动火点设置防火毯、湿毛毡,小火及时扑灭。
5、施工单位动火切割作业发现异常时,及时撤离并汇报。
2、重整装置四合一炉误操作停炉
一、事件经过:
2014年5月6日18:
02时,重整四合一炉F-202瓦斯压力在131-209KPa波动,18:
04分38秒将控制阀改为手动,F-202主火嘴瓦斯压力迅速下降,18:
04,四合一炉加热炉主瓦斯压力低低联锁(四合一炉主瓦斯联锁值70KPa),重整装置四合一加热炉联锁停炉,现场检查长明灯正常,进料正常,切除四合一炉加热炉主瓦斯联锁,点炉升温。
18:
17时各反应器入口温度恢复正常。
未对生产造成大的影响。
二、原因分析:
(1)班组人员将瓦斯控制阀自动改手动时,时机选择不当,处于该阀自动调节阀位输出值在低位时,手动调节滞后于自动调节,造成瓦斯压力持续下降,导致联锁是直接原因。
(2)车间根据调度安排,降低重整氢气外放量,多余氢气排入装置瓦斯系统,装置瓦斯含氢量增加,瓦斯压力从0.3MPa上升到0.42MPa。
四合一加热炉F202负荷最大,受瓦斯压力和性质变化影响较大。
是该加热炉联锁发生的重要原因之一。
(3)四合一加热炉F202先控自动切除,报警记录中有记录,但无声光报警,操作人员未及时发现。
操作人员对先进控制系统出现异常故障的原因不清楚,判断和处理方法学习不到位,是导致联锁发生的重要原因之一。
(4)DCS的PID参数设置不合理,导致先控切除后控制发散波动加剧;瓦斯火嘴的根部阀门没有全开,导致联锁参数失真,存在脱火或回火的风险;DCS上没有对瓦斯压力控制阀的下限进行限位等上述原因是导致联锁的诸多失控条件。
(5)调度安排提氢气量对提降氢气风险评估不足,班组接到指令后未通知车间干部,操作波动造成本次事故的重要原因之一
(6)技术和操作人员操作技能不过关,培训不到位,未对先控切除原因进行分析。
三、防范措施:
(1)提降氢气量严格按操作指南执行,短时间内大幅度提降氢气量应征得车间工艺管理人员同意
(2)技术处对目前投用的Ⅰ催化、气分、芳烃、200万加氢裂化装置的先控报警情况进行检查,梳理先控管理情况,编制炼油厂先控管理要求,纳入日常专业管理
(3)对涉及联锁等重要控制回路阀位进行合理限位,建立清单,发布培训,严格修改权限管理,不得随意修改
(4)车间对重整装置DCS工程师权限锁定,各参数的PID数据建立台账,班组不得调整DCS各参数的PID值,参数不合适影响平稳操作时,白天时联系车间技术干部,由车间技术人员根据波动情况调整PID参数,并且在工艺记录中记录,台账进行更新;技术干部不在时联系仪表专业人员,开具检修联络单,调整PID参数,并在工艺记录记录和台账中更新
(5)技术处联系加热炉火嘴设计及生产厂家,核算运行工况,评估加热炉瓦斯火嘴根部阀门未全开操作方式存在风险,完善操作控制方案
(6)在平稳氢网运行上,指导车间总结固化调节经验,加强班组培训,先进控制投用、切除、异常问题分析判断及处理的日常培训,避免长时间先进控制操作致使操作人员人工调节能力下降的现象
(7)全厂共享,组织有先控的车间自查类似问题,采取措施,杜绝同类问题再次发生。
五、300万直柴加氢装置
1.2009年300万直柴加氢开工紧急泄压事件
一、事件经过:
2009年8月31日13:
00,装置硫化全面结束,反应器入口温度降至290℃,14:
00联系原料送罐区直馏柴油,初期引入量为20~30t/h,反应器床层无明显温升;15:
00逐渐提大罐区柴油量至100t/h,反应器床层温升最高至7~8℃。
15:
30装置联系调度引蒸馏柴油,初期引入量控制在30~50t/h,由于蒸馏柴油控制较为困难,16:
00提量至120t/h,17:
00提至200t/h,17:
30分床层温升上升至14℃,安排操作人员降反应器入口温度,但是反应温升仍然有上升趋势,由于反应器出口温度高,因此反应器入口温度逐渐上升至310℃;17:
45分,反应器进出口温差达到28℃,按照UOP开工专家要求,装置17:
50分启动紧急泄压程序。
当班班组执行《反应器飞温事故操作卡》,操作卡执行到位,紧急泄压7分钟后停止,18:
30所有操作控制稳定,反应系统继续循环降温至205℃。
二、原因分析:
(1)UOP提供的预硫化催化剂活化后没有要求钝化过程,因此活性高,UOP提供的低于正常生产温度28℃的进料温度(310℃)偏高,实际车间进料温度为290℃;
(2)装置在切换过程中切换速度过快;
(3)蒸馏直供柴油中没有常一线组分,而车间取得的原料分析数据是常一线、二线和三线的混合柴油分析数据;
三、防范措施:
(1)反应温度控制在280℃进料;
(2)重新开工后切换速度要缓慢,初期引入量控制在40~50t/h;
(3)切换过程首先引入罐区柴油;引入直柴要和罐区柴油性质相差不大。
(4)每次提量速度控制在40~50t/h,等待反应器温升和温波通过后在进行下一次的提量。
(5)联系UOP修改飞温定义:
当温升大于正常温升28℃以上或催化剂床层任一点温度大于370℃时,确定反应器床层发生飞温。
(6)对《反应器飞温事故操作卡》进行修订。
六、200万吨加氢裂化装置
1、200万吨加氢裂化装置分反应器床层飞温
一、事件经过:
2011年9月28日,200万吨加氢裂化装置开工过程中,14:
10分反应器3床层飞温,床层温度450℃,操作人员启动2.1Mpa紧急泄压阀,装置泄压降温,进入停工退守状态。