东港污水处理厂工艺现状分析.docx
《东港污水处理厂工艺现状分析.docx》由会员分享,可在线阅读,更多相关《东港污水处理厂工艺现状分析.docx(9页珍藏版)》请在冰豆网上搜索。
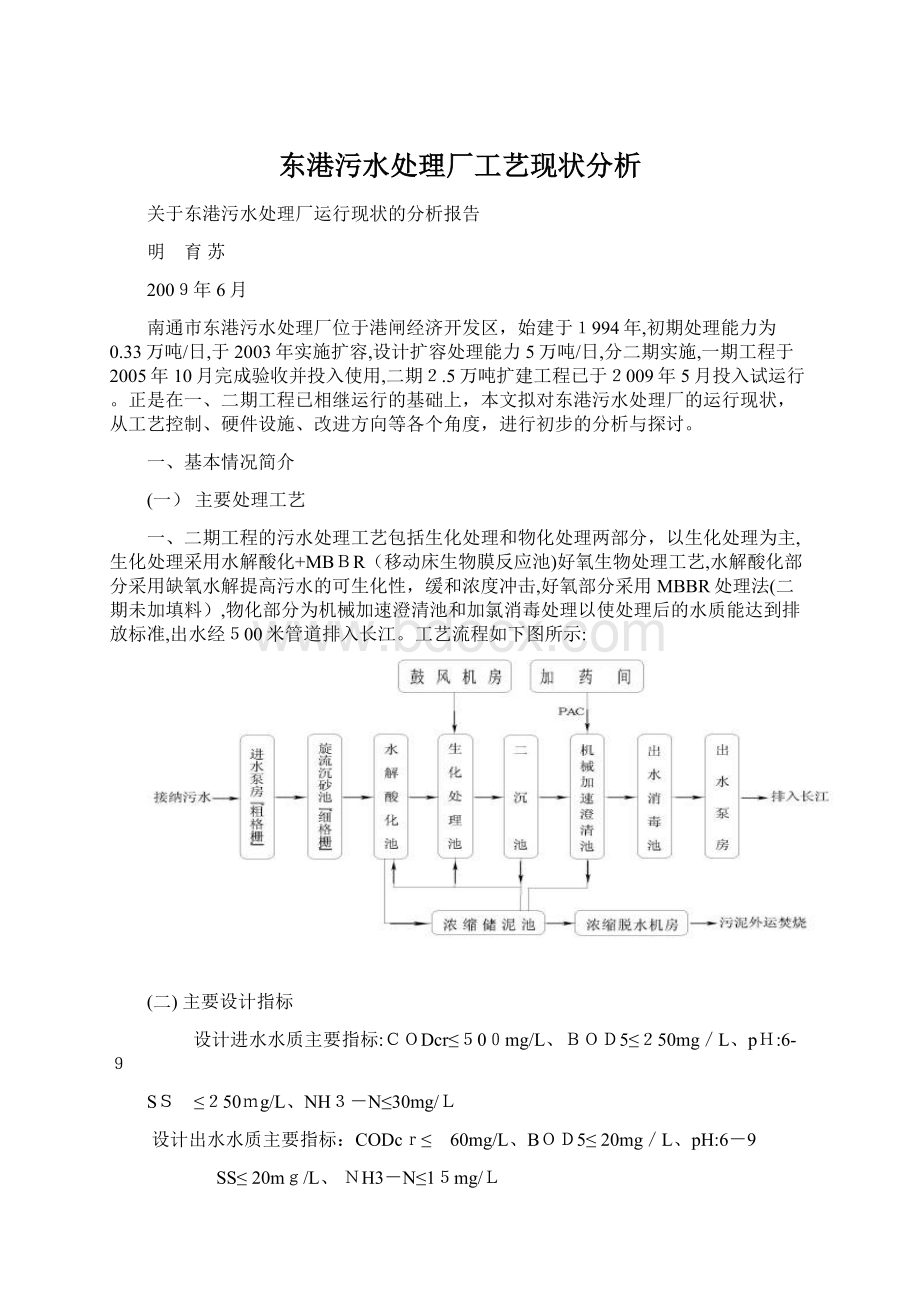
东港污水处理厂工艺现状分析
关于东港污水处理厂运行现状的分析报告
明 育苏
2009年6月
南通市东港污水处理厂位于港闸经济开发区,始建于1994年,初期处理能力为0.33万吨/日,于2003年实施扩容,设计扩容处理能力5万吨/日,分二期实施,一期工程于2005年10月完成验收并投入使用,二期2.5万吨扩建工程已于2009年5月投入试运行。
正是在一、二期工程已相继运行的基础上,本文拟对东港污水处理厂的运行现状,从工艺控制、硬件设施、改进方向等各个角度,进行初步的分析与探讨。
一、基本情况简介
(一)主要处理工艺
一、二期工程的污水处理工艺包括生化处理和物化处理两部分,以生化处理为主,生化处理采用水解酸化+MBBR(移动床生物膜反应池)好氧生物处理工艺,水解酸化部分采用缺氧水解提高污水的可生化性,缓和浓度冲击,好氧部分采用MBBR处理法(二期未加填料),物化部分为机械加速澄清池和加氯消毒处理以使处理后的水质能达到排放标准,出水经500米管道排入长江。
工艺流程如下图所示:
(二)主要设计指标
设计进水水质主要指标:
CODcr≤500mg/L、BOD5≤250mg/L、pH:
6-9
SS ≤250mg/L、NH3-N≤30mg/L
设计出水水质主要指标:
CODcr≤ 60mg/L、BOD5≤20mg/L、pH:
6-9
SS≤20mg/L、NH3-N≤15mg/L
(三) 近期运行情况
2008年全年共处理污水954万吨(设计900万吨),CODcr去除量为4816吨,已达到了设计年去除量3960吨的1.21倍;CODcr平均进水指标为603mg/L,处理后平均出水指标约82mg/L,平均去除率达到86%;剩余污泥外运焚烧7233吨。
今年以来,出水水质又有新改善,在进水水质、水量均超设计值的情况下,已能做到部分时段达标排放。
近两个月来的出水CODcr日变化曲线如下图所示(5月1日~6月25日)。
2009年在市环保局排污企业评级中被评为蓝牌企业。
二、运行现状分析
(一)进水水质水量状况
1、水质状况。
2006~2008年度月平均进水CODcr的变化情况如下图所示:
由上图可知,本厂进水CODcr一般大于500mg/L的设计值,CODcr平均值约为600mg/L。
一期工程自2005年投运以来一直面临着进水指标超标的困扰,主要表现为五个方面:
一是进水CODcr波动幅度大,瞬时值波动范围一般在400~1000 mg/L区间,造成曝气池负荷不稳定;二是进水pH值冲击频繁,约一半时段pH大于9,峰值可达12以上,抑制了微生物活性;三是可生化性不佳,B/C比一般约为0.3左右,难降解物质比例大,形成了出水BOD5稳定达标,CODcr经常超标的现象;四是进水氨氮常严重超标,一般在50-80mg/L间,峰值大于200mg/L;五是印染废水多色度高,造成出水CODcr即使达标,仍水色深表观不佳。
进入本厂的污水组成成份比较复杂,根据设计院在扩建工程可研报告中提供的数据,本厂各种类型的污水对应比例如下表:
污水组成成分
序号
污水性质
比例(%)
1
印染废水
9
2
纺织废水
4
3
化工废水
44
4
酿造废水
1
5
医药废水
1
6
其它工业废水
12
7
生活污水
29
因调查的时效性上表仅作参考,但大致可知,生活污水与工业污水比例约为三七开,本厂与处理生活污水为主的城市污水处理厂在类别上实有区别。
进水超标其实也是以工业污水为主的污水厂面临的普遍性困难。
理论上讲,污水厂应对超标排污企业加强源头控制,但在本厂现行体制下实际难以操作。
首先是没有行政检查权,经常在一般性取水监测时遇到阻力;其次是与排污企业间没有经济纽带关系。
故本厂现能发挥的作用大致相当于“群众监督”,有用而有限。
多数情况下人们并不能改变环境,而只能设法去适应之,对于进水超标亦然。
纵观近几年进水变化趋势,虽持继超标,但幸未出现如设计院2007年在初步设计书中预测的“进水水质将愈来愈差”的状况,相反却呈有所好转之势。
原因可能是多方面的,但环保方面强化监管应为主要因素,属功不可没。
2、水量情况。
09年5月份二期工程试运行后,日处理量已达到5.5万吨。
但随着港闸区社会经济的飞速发展,整个区内的入网污水排放量迅速增长,进入夏季后每天入网水量已超过6万吨,雨天水量甚至超过10万吨,目前的处理能力仍不能满足需求。
三期工程上马已迫在眉睫。
(二)水解酸化池
水解酸化-好氧处理系统中的水解酸化段的目的,对于城市污水是将原水中的非溶解态有机物截留并逐步转变为溶解态有机物;对于工业废水处理,主要是将其中难生物降解物质转变为易生物降解物质,提高废水的可生化性,以利于后续的好氧生物处理。
以COD为例,首先水解反应器中的大量微生物将进水中颗粒物质和胶体物质迅速截留和吸附,这是一个物理过程的快速反应,截留下来的物质吸附在水解污泥的表面,慢慢地被分解代谢,其在系统内的污泥停留时间要大于水力停留时间。
在大量水解细菌的作用下将大分子、难于生物降解物质转化为易于生物降解的小分子物质后,重新释放到液体中,在较高的水力负荷下随水流移出系统。
水解反应池集沉淀、吸附、网捕和生物絮凝等物理化学过程以及水解、酸化过程等生物降解功能于一体。
这与功能单一的初沉池有本质的区别。
传统的水解酸化池具有以下主要特征:
一是采用升流式反应器,原水经池底进水管多点进入,向上升流穿过污泥层并与其反应后形成澄清层,汇流后出水。
二是水解工艺中的优势菌群是厌氧微生物,污泥需经过适当培养与驯化,同时污泥层具有较高浓度和厚度,可以达到15~25g/L,且可保持并不随出水流走。
需要说明的是,水解-好氧工艺中的水解酸化过程与好氧AO、A2O和AB等工艺A段中发生的水解过程是有较大区别的。
这表现在以下两个方面:
首先是菌种不同,如上所述在水解工艺中的优势菌群是厌氧微生物,而在好氧AO等工艺A段中的优势菌是以好氧菌为主;其次,在反应器内的污泥浓度不同,水解工艺采用的是升流式反应器,其中污泥浓度可以达到15~25g/L,而好氧AO等工艺中从二沉池回流的污泥浓度一般最高为5g/L。
以上的差别造成了水解工艺是完全水解,而好氧AO等工艺中A段仅仅发生部分水解。
水解酸化工艺的另一种方式是在上进水水解池后设置中沉池,水解厌氧污泥在中沉池沉淀分离后再经循环泵回流至水解池进口,形成污泥循环。
这样做的优点是可以避免下进水方式中布水管的堵塞等问题。
而本厂现有水解池与传统水解有很大区别,前面详细介绍水解工作原理的目的主要是为了表明这种区别,主要有几点:
① 污泥性质有区别。
传统水解工艺中的优势菌群是厌氧微生物,具有“留得住、可培养、专属性”的特点。
而现工艺中进入水解池的是来自二沉池的好氧活性污泥,与原水混合进入水解池后,因泥水分离效果差,活性污泥中的大部分随出水进入后续曝气池,即“留不住”。
少量污泥虽沉淀在池末端底部,但一期中并不能回流到水解池进口,二期中本厂自行增设了回流管,但回流量十分有限。
故缺少污泥的培养驯化过程,即“难培养”。
如此则水解池中的污泥缺乏“专属性”。
②污泥浓度有区别。
现有水解池采用的是上进水、上进泥方式,在池中经搅拌混合后出水,不可能形成特定的污泥层,池中污泥也不可能达到传统水解池中15~25g/L的高浓度,最多只能达到3~4g/L的水平。
③水解程度有区别。
传统水解在高浓度水解厌氧污泥作用下,水解反应比较完全,而本厂水解池在进泥方式、优势菌群、污泥浓度等方面则类似于AO等工艺中的A段,是一种不完全水解,水解反应的程度与作用十分有限。
设计理念上的先天不足必然导致应用效果的差强人意。
虽然本厂对水解酸化池的运行方式作了多次长时间的各类试验,但结果均不够理想。
归结为两点:
一是表征水解效果的进出水B/C比未见提高,二是全系统总去除率未有明显提升。
二期的水解池已作了部分改进,如在池中增加了导流墙,基本消除了一期的短流现象;专设了末端泥水分离区;采用了集泥坑;加大了排泥泵流量等等。
但我们以为,从根本原理上讲二期水解与一期相较并无实质性改变。
事实上经太平洋公司专业人员的多次调试,亦未能取得理想效果。
一期水解池还存在一问题,即搅拌设备故障率较高。
水解酸化池的另一作用是均质。
当原水成份急剧变化,pH、COD等指标大幅波动,将对生化池形成不利冲击时,通过水解池的缓冲可使进水得到均质。
这种均质作用主要是通过搅拌和较大的池容实现的。
如搅拌机发生故障,不仅均质作用减弱,而且原水中悬浮物下沉于池底形成积泥。
所以搅拌机的完好率就很重要。
但实际情况并不乐观,水下搅拌机经常发生故障,这已成了制约水解池均质作用的一个重要因素。
一、二期水解酸化池现在主要充当着均质池的作用,而本应有的水解作用则有点“名不符实”。
如何改进则成为颇棘手的难题。
(三)生物曝气池
一期曝气池采用了AO+MBBR工艺。
缺氧A段的水力停留时间为5小时,可选择使用水下搅拌或部分曝气方式。
好氧O段水力停留时间为10小时。
采用AO工艺主要为了增强脱氮效果,其中A段为反硝化,兼有部分水解功能,O段为好氧降解主功能区,同时具硝化作用。
为使AO工艺发挥脱氮作用,必须开启从曝气池出口到进口的内回流,方能形成反硝化过程。
池中还投加了大量悬浮填料,故又称MBBR工艺。
采用MBBR工艺的初衷是将活性污泥法与生物膜法相结合,增加生物处理量,提高处理效果。
运行实践表明,由于曝气池水力停留时间合计长达15小时,这也是本厂与某些污水厂相较具有的工艺优势,只要工艺控制得当,对于本厂以工业污水为主的进水则具较好的降解效果。
CODcr去除率一般可在75~90%之间,BOD5去除率在85~95%之间。
从2008年下半年开始,我们主要从以下几方面优化了工艺控制:
1、合理调整污泥负荷。
污泥负荷F/M是运行控制中的重要指标,大多数运行故障多与污泥负荷的控制不合理存在关联。
以往考虑到进水以工业污水为主,为了提高抗冲击能力,曝气池污泥浓度一般控制在6~7g/L之间,相对应的污泥负荷则小于0.1 kg BOD5/kgMLSS·d。
但抗冲击性有所增强的同时也带来了一定的负面效应:
一是较高的污泥浓度形成了偏低的污泥负荷,易造成污泥龄偏大、污泥老化活性下降;二是污泥沉降比偏大,SV30经常达50~70%,污泥指数偏高,SVI可达150~230,发生轻度污泥膨胀;三是污泥浓度越高,曝气电耗则越大,造成电能浪费。
为此我们多次进行比对试验,在保证处理效果的前提下,将污泥浓度一降再降,目前控制在2.5~3g/L左右,污泥负荷则在0.15~0.2 kgBOD5/kgMLSS·d间。
调整取得了较好效果。
目前SV30一般在15~30%间,SVI一般在50~100间,污泥吸附、沉降性能良好,镜检情况亦有改善,钟虫增加,丝状菌减少。
最主要的是生化去除率有了提高,出水BOD5现在一般稳定在10mg/L左右,完全达到一级B标准中出水BOD5小于20mg/L的要求。
2、提高溶氧控制的合理性。
溶解氧在实际的污水处理操作中具有举足轻重的作用。
这一指标的恶化或波动太大,往往会迅速地导致活性污泥系统的稳定性大幅波动。
控制的合理性主要体现在两个方面:
一是控制取值范围要合理。
溶氧过低,有机物氧化分解需氧量不足,降解不充分,且抑制污泥活性。
过高则部分污泥氧化,随出流水漂走;二是全池的溶氧分布要合理。
供气量要随推流式曝气的特点沿水流方向逐步减少。
过去往往疏于调节,另在线仪表及分析化验方面数据的准确性均存在问题,所以调节效果并不理想。
我们从2009年年初开始,对曝气池全池的溶氧分布作了十多次动态测试,较好掌握了分布规律,在此基础上实行了分段式曝气控制,使污水进入好氧段后,始终处于适宜的溶氧环境,一般均在1.5~3mg/L范围内,既增加了有效好氧降解时间,提高了降解率,又避免了过曝现象。
3、控制合适的回流比。
污泥回流比的高低主要影响曝气池的污泥浓度,其次与二沉池污泥停留时间、进水稀释比等参数有一定关联。
以往回流比取值较大,一般在50~100%间,单从数值看与经验值相符,然而在实际运行中,因本厂回流污泥浓度一般为12~15g/L,而经验值一般为8 g/L左右,故在前述回流比下,易形成曝气池偏高的污泥浓度,达6~7g/L左右。
为此对工艺设施在硬件上进行了改造,将回流比控制在25~30%左右,改进后既使曝气池污泥浓度调适在合理范围,解决了两个二沉池的偏流问题,同时又使至储泥池的污泥浓度不至过低而影响脱泥效率。
从现状看曝气池业已发挥了较好功效,但从工艺完善的意义而言,一期曝气池仍存在以下问题:
1、悬浮填料造成堵塞。
悬浮填料起作用的必要条件是填料上必须挂生物膜,然经长期观察,球形填料始终未见挂膜,由此可推断,悬浮填料不具正面的生物膜处理作用。
但填料的负面影响却是显而易见的:
下沉的填料球在水流推动下堆积在曝气池格与格间过水孔洞的水下格栅处,造成经常性堵塞,致使曝气池污水溢出。
2、内回流不能开启。
因悬浮填料的堵塞问题,造成从曝气池出口至进口的内回流根本不能开启,曝气池内虽有硝化阶段而不能形成反硝化过程,脱氮效果下降,且COD的去除率也受到影响。
3、曝气管多处断裂。
因水下曝气管的材质、安装方式及穿孔曝气震动力大等原因,目前水下曝气管已有十余处断裂,只能采用关闭或调节支路阀门的办法维持,对正常曝气影响越来越大。
2006年曾为此停产检修两个月,现断裂情况正呈增加之势。
4、曝气电耗居高不下。
为了产生足够的气搅拌力,使球形填料在水中处于运动悬浮状态。
设计中采用了穿孔曝气,但随之带来的突出问题是曝气效率很低,电耗很高,一期的曝气耗电较二期要高一倍,水处理单位成本明显高于同类企业。
产生问题的根本原因是池中悬浮填料与穿孔曝气方式。
正是根据笔者的建议,二期曝气池未加填料并换用了微孔曝气方式,才未重蹈一期之复辙。
针对以上四方面问题,我们认为还是要通过技术改造与科技进步加以解决。
二期工程试运后,微孔曝气方式取得了极为显著的节电效果,曝气量仅为一期曝气量的约三分之一,耗电量约为一半。
由此出现了一个重大的技改契机:
将一期穿孔曝气改造为微孔曝气。
初步框算,改造后一、二期合并计算的年节电量可达100~150万元之间。
一期改造后不仅可显著节约运行费用,且可同时解决堵塞、内回流、脱氮等问题。
关键是需100多万元一次性技改经费和一段停产改造的时间。
为此要认真做好技改的前期论证工作,以可信的数据与可行的方案积极争取上级部门的支持,力争在2010年能顺利开展此项工作。
(四) 机械加速澄清池
机械加速澄清池(简称机加池)是将混合、絮凝和澄清工艺组建在一个池子内,并采用机械搅拌使活性泥渣呈循环回流方式,促使泥渣和原水接触起絮凝作用,提高澄清的效果。
主要由第一、二反应室和分离室组成。
经投药后的原水进入第一、二反应室后与回流泥渣接触,结成大而重的絮凝体,在分离室内分离澄清后出流。
机加池普遍应用于自来水厂的水质处理,一般可取得较好效果。
但很少用于污水处理。
主要是因为上下水水质有较大区别。
江河水中的杂质一般以无机泥砂居多,而污水中则以有机悬浮物为主,造成在加药絮凝后形成的污泥有明显区别。
污水中杂质形成的污泥粘性大,易挂壁易堵塞,比重小难下沉,造成泥水分离较上水困难。
这也是机加池用于污水后效率下降,不易管理的原因之一。
以往在运行操作中,由于对机加池应用于污水的运行规律掌握不够,产生回流量严重偏小,加药量明显偏大及积泥过多等问题,一直未能取得理想效果。
每日平均加药运行时间仅只8小时左右,去除率在5~8%间,加药量则高达1‰左右,且需经常停产清池。
从2008年3月份开始,我们组织技术攻关,前后历经约三个月时间,取得了明显效果。
去除率从原来约5~8%提高到15~20%左右。
且使絮凝药剂投加量大量减少,同比使用药量仅为技改前的约五分之一,从而能在现有运行药剂经费的范围内,从原平均日加药8小时改为实行24小时不间断投加,大大降低了单位运行成本,全面提高了处理效果。
机加池运行上主要作了四点改进:
一是提高搅拌机转速约两倍,大幅度提升了回流量,加速泥渣和原水接触起絮凝作用;二是大幅度降低了PAC加药量,掌握了最佳药量范围并减轻了排泥负担;三是撤除了斜管填料,解决了污泥严重堵塞问题;四是加强了工艺控制,采用了独特的排泥方式,将二室沉降比控制在合适范围。
目前存在的问题:
一是一、二期合并运行后,机加池的排泥量成倍增加,而污泥提升井的容量偏小;二是机加池中部集泥斗排泥不彻底,易造成积累污泥厌氧后上浮,影响机加池表观和导致出水SS增加。
(五) 污泥脱水系统
如果将污水处理全过程视为一个完整的系统,则污泥脱水子系统的运行状态对全系统能否正常运转具有决定性意义。
我们知道,活性污泥法的处理效果取决于活性污泥的数量与质量,而每日排出的剩余污泥量,即脱泥量的多少对曝气池污泥数量及污泥泥龄、生物活性、污泥指数、污泥性状等质量指标具有直接关联。
保证工艺要求的脱泥量是污泥脱水系统的基本任务。
目前一、二期合计有四台带式污泥脱水机,其中两台为2米带宽,两台为1.5米机。
从现状看,若每天脱泥约40吨(含水80%)则可基本保持污泥量平衡。
单就脱水机能力而言可满足上述工艺需要。
但在配套设施、设备保障等方面仍存在以下问题:
1、排水系统不能满足需求。
一期单独运行时,排污下水系统尚能满足要求。
二期试运后脱泥量成倍增加,经测算,仅以开两台脱泥机计,污泥压榨水、带机冲洗水、提升井上清液、储泥池上清液等合计瞬时流量可达300吨/小时。
而厂内排污管仍沿用了一期的Dg300的下水管道,经计算,流通能力不足200吨/小时。
故此经常出现污水从排污井溢出现象,在进水泵房集水井水位较高时影响更甚,已成为当前污泥脱水的主要制约因素。
目前建设单位正着手对厂内相关的排污管进行改造。
2、铰龙输送能力不够。
目前在提高脱泥速度上面临两方面瓶颈,一是排污管问题;二是铰龙输送能力。
如同时开四台脱泥机,则斜面铰龙难以将污泥向上输送至泥斗,原因为铰龙倾角偏大。
要解决此瓶颈需申请专项改造资金。
3、冲洗水杂质多。
滤布冲洗对带机运行影响甚大,为确保冲洗效果,有的污水厂用自来水作冲洗水,有的则用深井水,虽然水量大,单机水量约15吨/小时,成本很高,但水质好无杂质,不会造成冲洗水喷头堵塞。
相比之下,本厂采用机加池出水为冲洗水,虽节约了成本,却出现喷头经常堵塞、不利滤布冲洗、脱泥效率下降的问题。
之前我们已对机加池取水口加装了大面积过滤罩,取得一定效果,但未能彻底解决。
4、设备故障率高。
由于设备已使用四年多,加上污泥腐蚀性强,如脱泥机本体、冲洗水泵、污泥泵、药泵、配药机等故障频发。
偏高的故障率对保证脱泥量产生了不利影响。
5、药量控制不到位。
为了提高污泥絮凝效果的保险系数,操作工往往将脱水用药量放得较大,这样做对脱泥本身影响不大,但耗药量偏高使成本上升,造成不必要的浪费,目前虽已考核,但需加大力度,提高实效。
以上虽列举了五方面问题,但总体看目前污泥脱水系统尚能维持。
但欲将勉强维持状态提升到确保水准,要提高设备利用率,如同时开启四台脱水机,确保系统脱泥量有足够裕度,则上述前两个问题是必须切实解决的,解决问题的主体是设计与建设方。
后三个方面则可通过内部管理使之完善。
(六)关于降本增效
目前本厂运行成本较高,一期的单位成本为0.8元/吨水(综合成本),二期投运后由于产生规模效应,估计单位成本可降至0.6~0.65元/吨水之间,但仍有下降空间。
我们认为,降本增效是管理者义不容辞的工作职责,应认真研究和探索成本降低的有效途径并努力实施。
因成本管理涉及面广,此处仅择要作粗线条分析。
影响生产直接成本的主要因素为药剂费与电费两项。
其中药剂又分为物化处理用药剂PAC和脱泥用药剂PAM两种。
用量方面,如前所述,PAC用量已降至最低,为保证处理效果已降无可降;PAM用量则以加强管理来实施控制。
在价格方面,自2008年始已全面实行招投标并取得了明显效果,在今年的招标中对有关细则还要进一步完善。
如此则降低成本的最主要途径是节省电耗。
目前电耗成本占总成本约一半,经分析主要有两项可行措施,一是前已提及的一期曝气管改造,改造后有可能出现一种最理想的情况,即一、二期合计七台风机中,仅需开启一台风机即可满足一、二期曝气池全部的曝气需求(目前开三台)。
此项年节电费可达100~150万元。
二是在此基础上可报停一台变压器。
目前一、二期各有一台1600KVA变压器,一期改造后用电总功率大幅降低,一台变压器即可满足一、二期总容量要求,此时可报停一台变压器,则每年可节约变压器基本电费约50万元。
以上两项合计年节电150~200万元,单位成本则可降至0.5~0.55元/吨水,经济效益十分可观。
(七) 其它方面
1、二期运行概况。
二期工程2009年5月初开始调试,因直接采用一期活性污泥,缩短了培菌驯化过程,故仅用约一周时间即基本调试完毕。
试运一个多月来情况良好,日处理水量在2.5万吨以上,处理水质与一期基本相当,部分时段二沉出水水质还优于一期。
各类设施设备、电器仪表运行正常。
2、关于CODcr、BOD5化验分析。
本厂进水中化工废水占比40%多,导致氯离子含量偏高。
经测试,氯离子浓度一般在400~1000mg/L之间。
偏高的氯离子浓度虽然对水处理本身影响不大,但在CODcr化验过程中作为还原剂的氯离子如未能有效掩蔽,则与强氧化剂重铬酸钾发生反应,造成正常的CODcr值外又额外增加了一附加值,极易使出水CODcr化验值出现较大正误差(进水因化验时稀释倍数高,影响较小)。
过去对此不够重视,在化验中掩蔽剂的用法与加量均有问题,造成CODcr化验值普遍偏高。
经比对试验,因氯离子掩蔽不当而产生的出水CODcr误差区间一般在5~20 mg/L。
另本厂以往BOD5化验值亦偏高,主要原因是在5天的测试过程中有漏气现象,正误差一般在0~15mg/L区间内。
自今年5月份始,按规程改进后以上问题已基本解决,目前本厂CODcr、BOD5的化验分析值与环保方面同比数据基本相当。
同时也说明以往本厂的部分自测出水CODcr、BOD5数据存在偏高现象。
三、结语
以上对东港污水厂的运行现状作了初步的分析探讨,所述内容难免有偏颇之处,尚望指正。
总体来看,经前一阶段的不懈努力,通过加强理论研究,优化工艺控制,实施技术改造,使本厂的处理水平有了提升,也得到了环保部门的认同,但仍存在不少有待解决的问题。
我们的工作目标是:
在进水超标的困难条件下,力争通过锲而不舍的努力,使出水基本达标。
一年多来的努力,使我们正在向目标逼近。
能否实现目标,则一靠领导支持,二靠自身努力,三靠科技进步。
从以上分析中也可以看到,本厂仍有不断进步之空间和潜力。
我们有信心使东港污水处理厂更上一层楼,再上新台阶。
2009年6月25日