壳体冲压工艺及模具设计.docx
《壳体冲压工艺及模具设计.docx》由会员分享,可在线阅读,更多相关《壳体冲压工艺及模具设计.docx(22页珍藏版)》请在冰豆网上搜索。
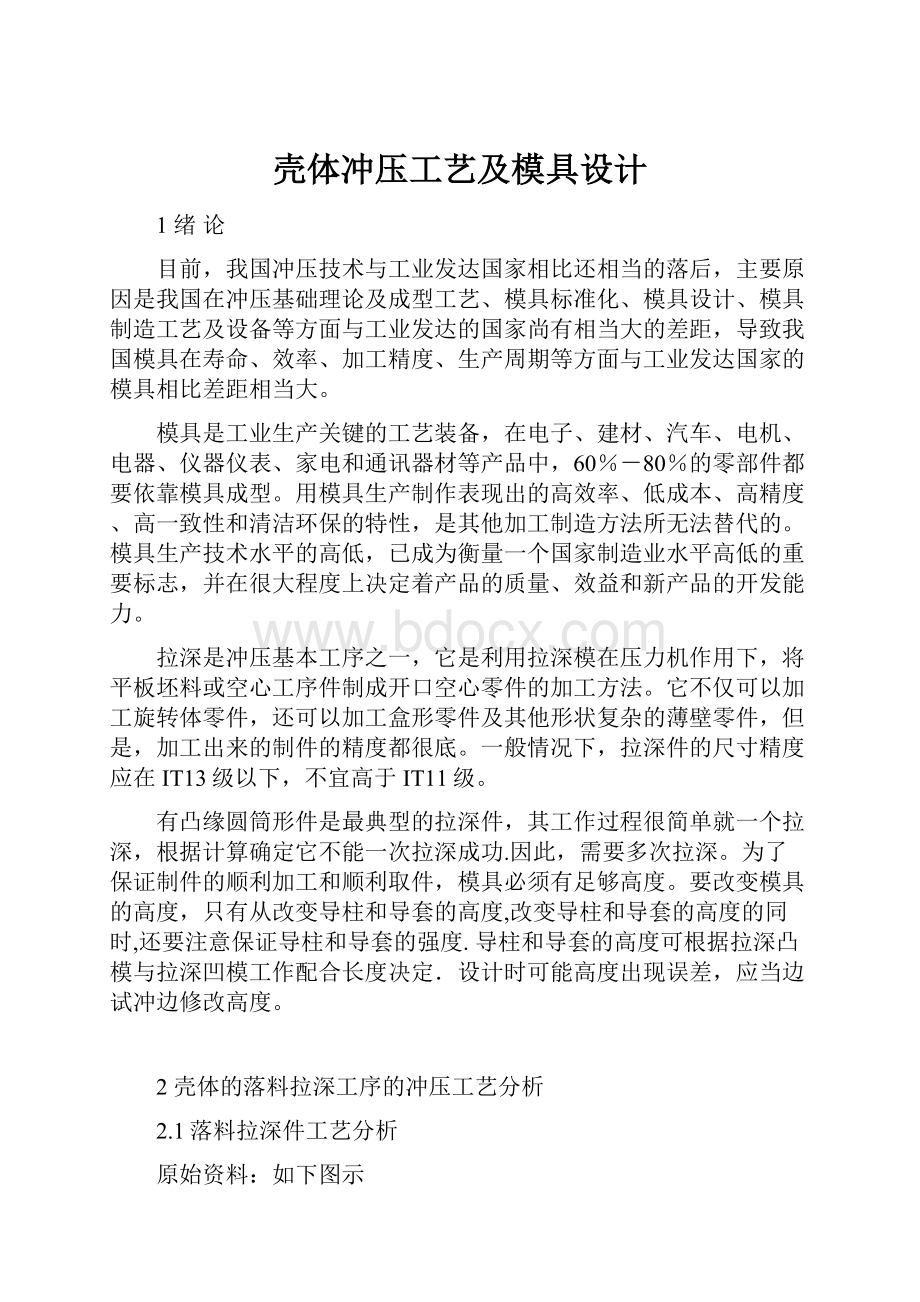
壳体冲压工艺及模具设计
1绪论
目前,我国冲压技术与工业发达国家相比还相当的落后,主要原因是我国在冲压基础理论及成型工艺、模具标准化、模具设计、模具制造工艺及设备等方面与工业发达的国家尚有相当大的差距,导致我国模具在寿命、效率、加工精度、生产周期等方面与工业发达国家的模具相比差距相当大。
模具是工业生产关键的工艺装备,在电子、建材、汽车、电机、电器、仪器仪表、家电和通讯器材等产品中,60%-80%的零部件都要依靠模具成型。
用模具生产制作表现出的高效率、低成本、高精度、高一致性和清洁环保的特性,是其他加工制造方法所无法替代的。
模具生产技术水平的高低,已成为衡量一个国家制造业水平高低的重要标志,并在很大程度上决定着产品的质量、效益和新产品的开发能力。
拉深是冲压基本工序之一,它是利用拉深模在压力机作用下,将平板坯料或空心工序件制成开口空心零件的加工方法。
它不仅可以加工旋转体零件,还可以加工盒形零件及其他形状复杂的薄壁零件,但是,加工出来的制件的精度都很底。
一般情况下,拉深件的尺寸精度应在IT13级以下,不宜高于IT11级。
有凸缘圆筒形件是最典型的拉深件,其工作过程很简单就一个拉深,根据计算确定它不能一次拉深成功.因此,需要多次拉深。
为了保证制件的顺利加工和顺利取件,模具必须有足够高度。
要改变模具的高度,只有从改变导柱和导套的高度,改变导柱和导套的高度的同时,还要注意保证导柱和导套的强度.导柱和导套的高度可根据拉深凸模与拉深凹模工作配合长度决定.设计时可能高度出现误差,应当边试冲边修改高度。
2壳体的落料拉深工序的冲压工艺分析
2.1落料拉深件工艺分析
原始资料:
如下图示
材料:
08F厚度:
1.5mm批量:
中批量
技术要求:
一般公差,线性尺寸的未注公差按GB/T1804
图1
t
图示零件材料为08钢板,能够进行一般的冲压加工,市场上也容易得到这种材料,价格适中。
外形落料的工艺性:
该带凸缘筒形件属于中等尺寸零件,料厚1.5mm,外形复杂程度一般,尺寸精度要求一般,因此可采用落料工艺获得。
拉深的工艺性:
观察零件图可知尺寸精度要求一般,属于带凸缘拉深。
此工件为带窄凸缘圆筒形工件,要求外形尺寸,没有厚度不变的要求。
此工件的形状满足拉深的工艺要求,可采用落料拉深工序加工。
工件底部圆角半径r=7.5mm,外形尺寸为
220mm,
220mm的公差等级为IT12级,满足拉深工序对工件公差等级的要求。
工件的总体高度到最后可由修边达到要求。
由以上分析可知,图示零件具有比较好的冲压工艺性,适合冲压生产。
2.2冲压工艺方案的确定
该工件包括落料、拉深两个基本工序,可有以下三种工艺方案:
方案一:
先落料,再拉深。
采用单工序模生产
方案二:
落料-拉深复合模冲压。
采用复合模生产。
方案三:
拉深采用级进模生产。
表一简单模、复合模、级进模比较
类型因素
生产批量
尺寸精度
形状大小
制造安装成本
安全性
复合模
中大批量
高
中小型
高
差
级进模
中大批量
较高
中小型
较高
较好
简单模
小批量
低
无要求
低
较好
采用方案一模具结构简单,但需两道工序两套模具,生产效率低,工件的累计误差大,操作不方便,难以满足该工件大批量生产的要求。
方案二只需一副模具生产效率高,尽管模具结构较方案一复杂,但由于零件的几何形状简单对称,模具制造并不困难。
方案三也只需一副模具,生产效率高,但模具结构比较复杂,送进操作不方便,加之工件尺寸偏大。
通过对上述三种方案的分析比较,该件若能一次拉深,则其冲压生产采用方案二为佳。
2.3模具结构形式的选择与确定
1)工作零件安装结构:
本零件的冲压包括落料和拉深两个工序,为方便落料件和拉深件的落下,采用正装结构,即凸凹模安排在上模。
2)送料方式:
是中小批量生产,采用手动送料方式,能简化模具结构,更能节约成本。
3)定位装置:
本工件在拉深复合模中尺寸是相对较大的,又是批量生产,落料时采用挡料销定位,送料时废料孔与固定挡料销作为粗定距。
4)导向方式:
为确保零件的质量及稳定性,选用导柱、导套导向。
由于采用了手工送料方式,为了提高开敞性便于送料,且其工件较大,采用中间导柱模架可承受较大的冲压力。
5)卸料方式:
本模具采用正装结构,落料件的废料靠刚性卸料板从凸凹模上刮下,筒形拉深件靠上模回程时打杆和推件块的共同作用把其从凸凹模中顶出。
2.4拉深工艺计算和工艺方案
本制件的工艺计算属于相对简单的。
其主要的内容包括计算毛坯直径、确定拉深次数及相关尺寸等。
2.4.1工艺方案的确定
根据制件的工艺分析,知道制件是相对简单的带凸缘圆筒形拉深件。
所以它的工序只有一个:
拉深。
2.4.2计算毛坯尺寸
查冲压手册表4-5选取修边余量δ=6mm.
查冲压手册表4-7拉深件毛坯直径计算公式P187页序号20则可按下面的公式计算:
当r≠r1时D²=d1²+6.28rd1+8r²+4d2h1+6.28r1d2+4.56r1²+d4²-d3²
d1=208r=6.75d2=221.5h1=63r1=2.25d3=226
d4=280代入数据后得D≈373mm
2.4.3拉深次数的确定
采用查表法。
根据t/D×100=1.5/373×100=0.4和工件相对高度h/d=72/221.5≈0.325,查冲压手册表4-20得h1/d1=0.48。
因0.325〈0.48,且总拉深系数mt=d/D=221.5/373≈0.594>0.54(极限拉深系数值)故可以一次拉深成形。
d凸/d=280/221.5≈1.264<1.4,属窄凸缘筒形拉深件。
2.4.4确定是否用压边圈
拉深中,是否采用压边圈装置,主要取决于拉深坯料的相对厚度大小,具体选择方法可参照下表所列的条件决定采用压边圈的条件
表二采用压边圈的条件
拉深方法
第一次拉深
以后各次拉深
t/D×100
m1
t/D×100
mn
用压边圈
可用压边圈
不用压边圈
<1.5
1.5~2.0
>2.0
<0.6
0.6
>0.6
<1
1~1.5
>1.5
<0.8
0.8
>0.8
相对厚度t/D×100=1.5/373×100=0.4,查表得,需要采用压边圈。
首次拉深时一般采用平面压边装置。
再次拉深时,采用筒形压边圈。
一般来说再次拉深所需要的压边力较小,而提供压边力的弹性力却随着行程而增加,所以要用限位装置。
2.4.5选取凸模与凹模的圆角半径
根据冲压手册P307页当工件直径d>200mm时,拉深凹模圆角半径应按下式确定:
r凹min=0.039d+2(mm)d为凹模内径=226mm
采用合适的R凸、R凹与凸凹模间隙Z可以减小拉深系数。
采用过小的R凸、R凹和Z会使拉深过程中摩擦阻力与弯曲阻力增加,危险断面的
变薄加剧,而过大的R凸、R凹和Z则会减小有效的压边面积,使板料的悬空部分增加,易于使板料失稳起皱,所以对拉深都不利。
且为了制造方便,综上考虑取r凹=11mm
2.5压力、压力中心计算及压力机的选用
因为本制件是轴对称零件,所以不用计算压力中心。
2.5.1压力计算
本制件拉深时需要采用压边圈。
其拉深力的计算公式应该以生产中常用的经验公式进行计算:
压边圈产生的压边力F压大小应适当,F压太小,防皱效果不好;F压太大,则会增大传力区危险断面上的拉应力,从而引起材料严重变薄甚至拉裂。
因此,实际应用中,在保证变形区不起皱的前提下,尽量选小的压边力。
其计算公式可按下式计算:
落料拉深工序
1落料力
P=1.3D
t
查表可知式中
=294MPaD=373t=1.5mm
则:
P=1.3×373×
×1.5×294N≈671.5KN
2卸料力
Q=kP查表可知式中k=0.04
则:
Q=0.04×671.5KN≈27KN
3拉深力
F=
d0tk1бb
查冲压手册表4-85可知式中k1=0.82бb=392MPa
则:
F=
×223×1.5×0.82×392N
≈337KN
4压边力
Q压边力=
查表可知式中q=2.5MPa
则:
Q压边力=
=272.13KN
确定压力机吨位:
这一工序的最大总压力F总=F落料+F卸料+F压边
≈671.5KN+27KN+272.13KN
≈970.6KN
选择压力机公称压力时需注意,当拉深工作行程较大,尤其落料拉深复合模时,应使工艺力曲线位于压力机滑块的许用压力曲线之下。
而不能简单地按压力机公称压力大于工艺压力的原则去确定压力机的规格,否则可能发生压力机超载而损坏。
在实际生产中可以按下式来确定压力机的公称压力:
Fg≥(1.6~1.8)FZ则可得:
Fg介于1553.0~1747.1之间
2.5.2压力机的选用
压力机的工作行程需要考虑工件的成形和方便取件,因此,工作行程根据拉深力的计算结果和工件的高度,选择压力机:
闭式压力机机身左右封闭,刚度好,多点压力机抗偏载能力强,综合考虑后,采用闭式双点压力机。
且所需压力机的公称压力Fg介于1553.0~1747.1kn之间故选用JB36-200B
表三JB36-200B所选择压力机的相关参数
压力机型号
JB36-200B
公称压力(KN)
2000
公称压力行程(mm)
13
滑块行程(mm)
400
滑块行程次数(次/分钟)
18
最大装模高度(mm)
600
装模高度调节量(mm)
250
导轨间距离(mm)
2430
滑块底面前后尺寸(mm)
1150
工作台板左右尺寸(mm)
2350
工作台板前后尺寸(mm)
1250
2.6排样设计
2.6.1确定零件的排样方案
设计模具时,条料的排样很重要。
排样合适恰当不仅可以降低成本,提高材料的利用率,而且可以提高生产效率。
根据该零件的图形分析可知:
筒形件是由落料件后续拉深成型的。
其排样方安比较简单,容易确定,这里就采用直排的形式来确定落料的排样。
其排样简图如下:
图2
2.6.2条料宽度、导尺间宽度和材料利用率的计算
查表取得搭边值为a=2mm和a1=1.5mm。
条料宽度的计算:
B=D+2a,代入数据计算得进距为377mm。
进距的计算:
由s=D+a1,代入数据计算得进距为374.5mm。
材料利用率的计算:
根据一般的市场供应情况,原材料选用A×L×t=1200mm×1600mm×1.5mm的冷轧薄钢板。
纵向剪板条数:
n1=
=
=3条余69mm
每条落料个数:
n2=
=
=4条余100.5mm
落料工序板料利用率:
=
代入数据n1=3n2=4D=284mm
得
=
=68.26%
横向剪板条数:
n1=
=
=4条余92mm
每条落料个数:
n2=
=
=3条余75mm
落料工序板料利用率:
=
代入数据n1=4n2=3D=373mm
得
=
=68.26%
因此采用纵排或横排均可以。
3模具的结构设计
3.1模具工作部分的计算
3.1.1拉深模的间隙
深间隙对拉深过程有较大的影响。
它不仅影响拉深件的质量与尺寸精度,而且影响拉深模的寿命以及拉深是否能够顺利进行。
因此,应该综合考虑各种影响因素,选取适当的拉深间隙值,既可保证工件的要求,又能使拉深顺利进行。
本模具的拉深间隙查表得出:
Z1/2=1.t=1.65mm
3.1.2拉深模的圆角半径
凸模、凹模的选用在制件拉深过程中有着很大的作用。
凸模圆角半径的选用可以大些,这样会减低板料绕凸模的弯曲拉应力,工件不易被拉裂,极限拉深因数会变小些;凹模的圆角半径也可以选大些,这样沿凹模圆角部分的流动阻力就会小些,拉深力也会减小,极限拉深因数也会相应减小。
但是凸、凹模的圆角半径也不易过大,过大的圆角半径,就会减少板料与凸模和凹模端面的接触面积及压边圈的压料面积,板料悬空面积增大,容易产生失稳起皱。
3.1.3模具工作部分的尺寸和公差
0
落料件尺寸公差为φ373-0.89
由表2-31公式进行计算:
D凹=(D-x△)+δ凹+0.060
=(373-0.5×0.89)0
=372.56~372.62
(查表2-30X=0.5δ凹=+0.060)
D凸=(D-x△-2c)-δ凸
0
=(373-0.5×0.89-0.132)-0.04
=372.38~372.42
δ凸=-0.040
Cmin=0.066Cmax=0.120
查表2-23
δ凹的绝对值与δ凸的绝对值之和=0.060+0.040〈2Cmax-2Cmin
=0.24-0.1332
=0.108mm
故上述计算是恰当的。
拉深前的毛坯取未注公差尺寸的极限偏差。
由《冲压手册》表4-75公式计算:
D凹=(d+0.4△+2c)+δ凹
+0.12
=(220+0.4×0.46+2×1.65)0
=223.48~223.60
C=1.1t=1.65mmδ凹=0.12
0
D凸=(d+0.4△)-δ凸=(220+0.4×0.46+)-0.08
=220.10~220.18
δ凸=-0.08
3.1.4凸模部分的设计及长度计算
由于工件的形状简单且对称,本模具为落料-拉深复合模,为了实现先落料后拉深,模具装配后,应使拉深凸模的端面应比落料凹模端面低。
凸模长度一般是根据结构上的需要而确定的,拉深凸模的L长度可按下式计算:
L=H固+H凹-H低
式中:
H固———凸模固定板的高度(50mm)
H凹———凹模的高度(210mm)
H低———装配后拉深凸模的端面低于落料凹模端面的高度,根据板厚太小,确定H低=5mm
则:
L=210mm+50mm-5mm=255mm
该模具凸模因为高度较大,为了防止淬火变形,除了采用工作部分局部淬火(硬度58—62HRC)外,材料用T10-A优质工具钢。
3.1.5凸凹模的设计及长度计算
外形落料凸模内形拉深凹模的凸凹模:
其外形可用数控车床加工和外圆精磨,用四个M30的螺钉固定在垫板上,由于其内部的拉深凹模的形状,致使凸凹模的强度和刚度下降,这里也采用淬火变形小的CrWMn模具钢。
为了加强强度和刚度,这里把凸凹模做成整体式的,不必再作凸凹模固定板。
其长度可按下式计算:
L=H凹+H卸+H固-H顶
其中:
H凹———凹模的高度(210mm)
H卸———固定卸料板的高度(50mm)
H固———凸凹模固定部分的长度(60mm)
H顶———顶件块的高度(80mm)
则:
L=210mm+50mm+60mm-80mm=240mm
3.1.6选用模架、确定闭合高度及总体尺寸
由于拉深凹模外形尺寸较大,为了工作过程稳定,选用中间导柱模架。
再按其标准选择具体结构尺寸见表3-1。
表3-1模架规格选用
名称
尺寸
材料
热处理
上模座
600×90
HT200
焖火
下模座
600×90
HT200
焖火
导柱
A70h7×550
A75h7×550
20
渗碳HRC58~62
导套
A70h7×550
A75h7×550
20
渗碳HRC58~62
模具的闭合高度H闭=H上+H凹模+H凸凹模+H下-(凸凹模刃面高度差+拉深件高度-料厚)=90+210+240+90-(3+73.5-1.5)=555mm
式中:
H凹—凹模厚度,H凹=210mm;
H压—压边圈的厚度,H压=80mm;
由此可见模具的实际闭合高度远远大于所采用模架的最大闭合高度。
查标准件的资料。
结果发现模具的实际闭合高度还是远远大于其它标准的最大闭合高度。
所以此制件不能采用标准模架。
为了节省加工时间,只有在模具标准模架的基础上进行修改。
因为模具的封闭高度H应该介于压力机的最大封闭高度Hmax=600mm和最小封闭高度Hmin之间,一般取:
Hmax-5mm≥H≥Hmin+10mm
由此可以看出,要想让制件顺利加工和从模具上取出,只有使模具有足够的封闭高度:
Hmax≥H+5mm=555+5=560mm
Hmin≤H-10mm=555-10=545mm
要使模具具有足够的封闭高度,只有改变导柱和导套的高度:
导柱:
A70h7×550A75h7×550;
导套:
A70H7×180×73A75H7×180×73
为了使模座有足够的强度,上,下模座的厚度应该再增加一些。
模具选用中间导柱标准模架,可承受较大的冲压力,为了防止装模时上模旋转180度装配,将模架中两对导柱与导套做成粗细不等。
导柱α/mm×L/mm为φ70×550
导柱α/mm×L/mm为φ75×550
导套α/mm×L×D为φ70×180×73
导套α/mm×L×D为φ75×180×73
H上模=90mm———上模座厚度
H垫板=30mm———下模座垫板厚度
H卸=50mm———固定卸料板厚度
H凸模固定=35mm———凸模固定板厚度
H下垫板=30mm———下模垫板厚度
H下模=30mm———下模座厚度
模具实际闭合高度:
H闭=H上模+H垫+H凸凹模+H凹模+H下垫板+H下模-H入=90+30+240+210+30+30-75=555mm
式中:
H凸凹模=240mm———凸凹模的高度
H凹模=210mm———凹模的厚度
H入=75mm———凸凹模进入落料凹模深度
由此可见该模具实际闭合高度小于所选压力机的最大装模高度600m所以可以使用。
3.2模具零件的结构设计
3.2.1拉深凹模
内、外形尺寸和厚度已由前面的计算确定;拉深凹模需要有三个以上的螺钉与上模座固定,还需要两个与上模座同时加工的销钉孔。
3.2.2拉深凸模图3
拉深凸模的外形尺寸〔工作尺寸〕由前面的计算确定。
它需要三个以上的螺纹孔,以便与下模座固定。
拉深凸模上一般开有出气孔,这样会使卸件容易些,否则凸模与工件由于真空状态而无法卸件。
查表,本凸模出气孔的直径为φ9.5mm
3.2.3压边圈
在拉深工序中,为保证拉深件的表面质量,防止拉深过程中材料的起皱,常采用压边圈用合适的压边力使毛坯的变形区部分被压在凹模平面上,并使毛坯从压边圈与凹模平面之间的缝隙中通过,从而制止毛坯的起皱现象。
压边圈的内形与拉深凸模间隙配合,外形套有半成品制件。
一般与顶料杆(三根以上)、橡皮等构成弹性卸料系统。
3.2.4导柱、导套
对于生产批量大、要求模具寿命高的模具,一般采用导柱、导套来保证上、下模的导向精度。
导柱、导套在模具中主要起导向作用。
导柱与导套之间采用间隙配合。
根据冲压工序性质、冲压的精度及材料厚度等的不同,其配合间隙也稍微不同。
因为本制件的厚度为3mm,所以采用H7/h6。
3.2.5卸料弹簧的选择
F卸=27KN拟选用12个弹簧,每个弹簧担负卸料力约为2250N。
弹簧的工作压缩量h工=73.5+1.0+0.5=75.0mm
式中a为落料凹模高出拉深凸模的距离,取a=1mm
b为卸料板超出凸凹模刃口的距离,以保证卸料,取b=0.5mm
查《冲压手册》表10-1选用弹簧为D2=95mmd=10mmh0=300mm
hj=184mmFj=2870N除去75mm的工作压缩量
h预=(hj/Fj)F预=72mm
计算后且应满足如下条件:
hj>h工+h预+h修磨
hj=184>72+75+6=153mm故所选弹簧是合适的.
3.2.6橡胶的选择
查教材表2.9.12拟采用圆筒形的橡胶d=30mm
D=√(d²+1.27Fxy/p)=73mm图4
此外0.5≤(HO/D)≤1.5取HO=75mm
3.2.7推杆长度
推杆长度〉模柄总长+凸凹模高度-推件块厚度
=90+240-40=290mm
3.2.8其他零件
模具其他零件的选用见表五.表五模具其他零件的选用
序号
名称
数量
材料
规格/mm
热处理
1
卸料板
1
45
50×850×850
2
上模座
1
HT200
600×90
焖火
3
弹簧
12
65Mn
10×300×95
40~45HRC
4
挡料销
3
45
M30×240
5
螺钉1
4
40
M30×180
40~45HRC
6
上模固定板
1
Cr12
280×400×220
7
模柄套
1
45
260×110
渗碳58~62HRC
8
打杆
1
20
80×670
40~45HRC
9
模柄
1
40
220×200×260
50~56HRC
10
推件块
1
45
φ272×270
40~45HRC
11
凸凹模
1
CrWMn
500×240
60~62HRC
12
销钉1
2
T10A
M30×180
30~35HRC
13
退料板螺钉
4
45
M30×240
30~35HRC
14
导套
2
20
70×180×73
渗碳56~58HRC
15
导柱
2
20
70×550
渗碳56~58HRC
16
下模座
1
HT200
90×670
焖火
17
落料凹模
1
T10A
φ600×210
渗碳58~62HRC
18
销钉2
2
45
M30×270
19
螺钉2
4
45
M30×240
20
销钉3
2
45
φ20×150
21
螺钉3
1
45
M30×180
22
螺钉4
2
45
M20×150
23
夹板
2
45
600×600
40~45HRC
24
推销
4
T8A
φ40×180
45~50HRC
25
拉深凸模
1
T10A
φ300×255
60~62HRC
26
压边圈
1
T8A
φ390×80
56~58HRC
27
下模固定板
1
45
600×600×40
40~45HRC
3.3模具总装图
由以上设计,可得到模具的总装图,其工作过程是:
将条料沿挡料销送进,前端再由挡料销进行精定位,坯料放在落料凹模表面上,卸料板在此兼起压料作用,由凸凹模和落料凹模完成第一道落料工序,凸凹模继续下行,毛坯在凸凹模、拉深凸模以及压边圈共同作用下,被反向拉入凸凹模中,产生塑性变形而制成所要求的零件。
当凸凹模随上模部分回升时,零件制品在推件块及推杆的作用下,将其从凸凹模内推出。
而压边圈在缓冲器系统作用下又回到原位,准备下一次拉深。
结束语
壳体属于简单拉深件,分析其工艺性,并确定工艺方案。
根据计算确定本制件是由落料拉深和切边冲孔两道工序复合而成的,然后相应选取各工序所需的压力机。
本设计是壳体的第一个工序落料拉深模具设计,需要计算拉深时的间隙、工作零件的圆角半径、尺寸和公差,并且还需要确定模具的总体尺寸和模具零件的结构,然后根据上面的设计绘出模具的总装图。
由于在零件制造前进行了预测,分析了制件在生产过程中可能出现的缺陷,采取了相应的