低硅冶炼技术应用.docx
《低硅冶炼技术应用.docx》由会员分享,可在线阅读,更多相关《低硅冶炼技术应用.docx(11页珍藏版)》请在冰豆网上搜索。
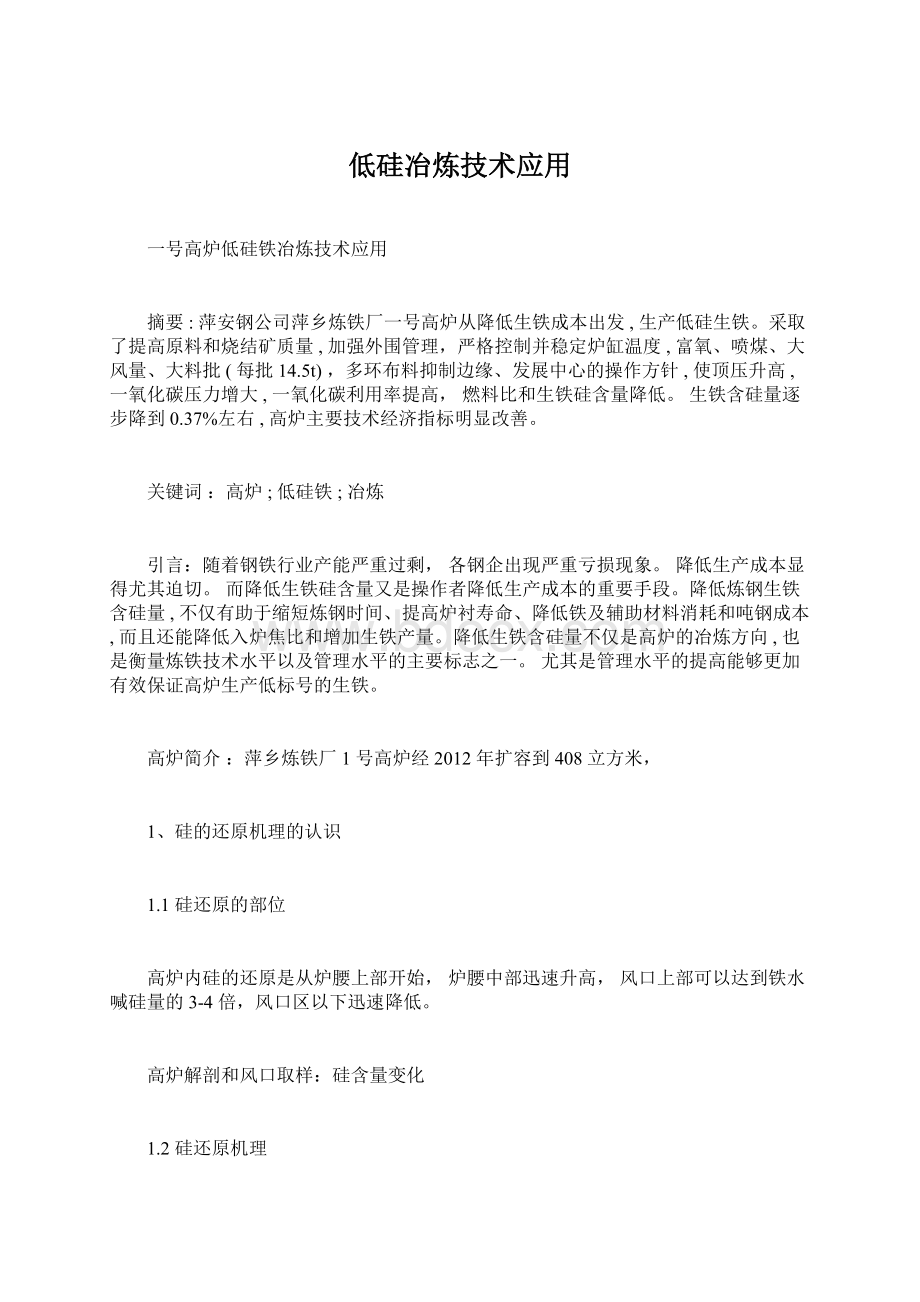
低硅冶炼技术应用
一号高炉低硅铁冶炼技术应用
摘要:
萍安钢公司萍乡炼铁厂一号高炉从降低生铁成本出发,生产低硅生铁。
采取了提高原料和烧结矿质量,加强外围管理,严格控制并稳定炉缸温度,富氧、喷煤、大风量、大料批(每批14.5t),多环布料抑制边缘、发展中心的操作方针,使顶压升高,一氧化碳压力增大,一氧化碳利用率提高,燃料比和生铁硅含量降低。
生铁含硅量逐步降到0.37%左右,高炉主要技术经济指标明显改善。
关键词:
高炉;低硅铁;冶炼
引言:
随着钢铁行业产能严重过剩,各钢企出现严重亏损现象。
降低生产成本显得尤其迫切。
而降低生铁硅含量又是操作者降低生产成本的重要手段。
降低炼钢生铁含硅量,不仅有助于缩短炼钢时间、提高炉衬寿命、降低铁及辅助材料消耗和吨钢成本,而且还能降低入炉焦比和增加生铁产量。
降低生铁含硅量不仅是高炉的冶炼方向,也是衡量炼铁技术水平以及管理水平的主要标志之一。
尤其是管理水平的提高能够更加有效保证高炉生产低标号的生铁。
高炉简介:
萍乡炼铁厂1号高炉经2012年扩容到408立方米,
1、硅的还原机理的认识
1.1硅还原的部位
高炉内硅的还原是从炉腰上部开始,炉腰中部迅速升高,风口上部可以达到铁水喊硅量的3-4倍,风口区以下迅速降低。
高炉解剖和风口取样:
硅含量变化
1.2硅还原机理
国内外的诸多研究和生产实践表明
SiO(g)迁移来实现。
其还原分两步进行
硅的还原主要通过气相的
:
SiO2(灰分)+C(焦
炭)=SiO(g)+CO。
然后,SiO(g)在上升过程中通过滴落带与渗碳的铁滴相遇,即SiO(g)+C=Si+CO。
在高炉滴下带到炉缸渣铁层的宽广范围内,有多种硅的迁移过程存在于铁液、渣液、焦炭、SiO气体之间。
在风口带的高温回旋区,焦炭灰分中SiO2和通过滴落带流下来的炉渣中所含SiO2被碳还原成气态SiO。
气态SiO随高温煤气上升,当在滴落带遇到由软熔带向下滴落的渣及铁液时则被吸收,同时SiO被铁滴中的饱和碳还原,反应产物硅进入铁水,铁滴对于SiO气体的吸收
率可达到70%~100%。
铁滴不断下降因而吸收的硅越来越多,以至在风口上方达到最高含量。
当铁水下降通过风口时,由于风口部位的氧势
高,使铁水的含硅量因被氧化而明显降低。
进人炉缸后,渣铁之间硅的转移反应由于受到炉渣碱度的抑制,SiO2的活度将减小,而且由于渣中MnO,FeO等成分耦合作用的影响,生铁含硅量将进一步降低,达到最终的生铁含硅量。
2冶炼条件及生产实践
根据上述理论并结合萍乡炼铁厂的实际,为实现低硅冶炼采取了以下措施:
2.1严格监控燃料质量
在2012年9月份曾因煤粉灰分大幅上升到30%以上且未化验出结果导致一号高炉小凉一次,高炉成立专门的监察小组,现场对煤粉取样进行监督,防以次冲好,弄虚作假的事故发生。
。
2.2.
采用合理的造渣制度,是低硅冶炼的必要条件。
实践表明,当MgO含量达到10%左右时,炉渣三元碱度(R3)在1.35以上,流动性良好,利于炉渣脱硫、脱硅。
1号高炉在低硅铁的冶炼过程中注重控制好炉渣
碱度,控制由原1.1提高至1.20甚至是以上。
适当提高炉渣碱度R2
及保证MgO含量,可提高炉渣的熔化温度,增加炉缸热量的储备。
改善
炉渣流动性,提高了炉渣的脱硫能力,又可缩短熔滴带的厚度,使铁水
温度相对提高,这样在较高的焦炭负荷条件下,也能促使低硅生铁冶
炼顺利进行。
炉渣二元碱度升高能降低渣中SiO2的活度,起到抑制硅
还原的作用。
但是二元碱度过高会提高炉渣的熔化温度,引起焦比升
高,影响炉况顺行。
用MgO代替部分CaO的增加来提高三元碱度,有利于炉渣性能的稳定及渣铁流动性的改善,减少滴落带渣铁的滞留量和滞留时间,缩短反应时间,达到降硅的目的。
目前1号高炉的MgO含量程下行趋势,渣R2上升到较高的水平,对高炉的顺行存在一定的隐患。
具体数据如下表:
表一
月份
1
2
3
4
5
6
7
8
9
10
MgO
10.05
9.82
9.73
9.05
9.64
9.58
9.49
9.31
9.09
8.52
R2
1.119
1.1431.089
1.1081.122
1.146
1.21
1.174
1.179
1.222
[SI]
0.43
0.45
0.51
0.5
0.48
0.48
0.42
0.42
0.43
0.37
由上表可以看出随着低硅冶炼进程的推进,渣中MgO一直在下,且达到较低的水平,不利于低硅冶炼。
R2一直在上升,低硅高碱度操作存在较大的风险,易造成高炉悬塌料,引起气流波动。
风口易灌
渣,甚至是引起炉凉事故的发生。
在目前低硅水平较高的生产中提升渣中MgO的含量到10%以上显得比较重要。
2.3高风温措施
风温全送,规定到1190摄氏度换炉,开混风阀受到考核的管理措施促进使用高风温。
高鼓风温度使焦炭负荷增加,炉顶煤气利用率得到改善,软熔带水平下移,从而使反应时间缩短,有效控制了硅的还
原。
此外,由于风温提高后焦比降低,由焦炭带入炉内的灰分减少,所以在客观上也减少SiO2的入炉量。
2.4提高原料质量
炉料成分越稳定,炉况越平稳,生铁硅含量的波动也相应减少。
原料熔化温度高,可扩大块状带区域,减少高温区的热量消耗,使软熔带下移,缩短硅的还原区间,抑制硅的还原。
采用高MgO和高碱度还原性好的烧结矿,不但有较高的软化和熔化温度,而且生成的初渣可吸收风口高温区的SiO2,并能改善炉渣流动性。
煤比、焦比以及焦炭灰分越低,对冶炼低硅生铁越有利。
焦炭质量不断提高,近年来焦炭灰分含量达到l2.5%左右,焦炭硫约为0.80%,M40大于80%的稳定率与M10小
于7.0%。
改善烧结矿筛分、粒度均匀,粒径小于5mm的碎矿不准入炉。
四小时测定一次烧结粒级,出现超标现象严格考核烧结车间,为高炉降低焦比和冶炼低硅铁创造了有利条件。
入炉烧结料粒级情况如下
表:
表二
月份
5月
6月
7月
8月
9月
10月
烧结<10mm
24.44
24.14
24.17
23.61
23.36
23.08
2.5严格控制并稳定炉缸温度
炉缸温度包括两方面:
高温和热平衡。
在低硅的情况下需要较高
的理论燃烧温度,目前一号高炉的理论燃烧温度基本控制在2220摄
氏度以上.而热平衡方面主要采用稳定负荷,单小时燃料比以及各采用水分仪测定即时入炉焦水分这一有效措施来稳定炉缸热制度,从而稳定生铁的含硅量。
在低硅生铁的冶炼过程中,炉缸温度的高低关系到炉温的稳定。
高炉的含硅量按0.4%来操作,并努力防止炉温过低,确保炉况的顺行,一级品率也逐步提高。
采取的具体措施有:
(1)稳定风量,班料批控制在上限。
(2)稳定风温与综合负荷,在1190摄氏度时就及时换炉,煤比严格控制上下限5kg/tFe。
(3)加强原料入炉的电子秤的管理,执行定期校秤制度,防止原料称量变化引起炉温大起大落。
(4)加强三班操作统一,做好三班街接的综合炉况判断。
勤观察,勤析调剂,坚持早动、小动、小幅调剂。
(5)2个小时测定一次入炉焦炭水分,严防焦炭水分大幅波动造成炉温水平的波动。
尤其时在雨季时焦炭水分波动较大,严重影响到焦炭负荷的变化。
2.6铁水温度
铁水温度对硅迁移的影响要大于其它因素的影响。
因为铁水温度高,表示滴下带内铁液的温度相应升高,也说明与硅还原有密切关系的风口前焦炭温度相对提高,从而使滴下带内的铁液--焦炭、铁液--SiO气、焦炭灰分--焦炭,甚至渣液--焦炭、渣液--铁液等各种硅
还原过程都得到加强。
每降低铁水温度30!
可降约0.1%,目前1号高
炉的铁水温度基本控制在1440~1470摄氏度.以保证出铁顺利和生铁
成分稳定。
根据国内外先进经验来看铁水温度还有进一步下降到
1400-1420摄氏度,[Si]可降到0.3%左右。
上述主要数据如下表:
表三
月份
1
2
3
4
5
6
7
8
9
10
富氧率
2.19
2.43
2.64
2.31
2.4
2.38
1.8
1.88
1.88
2.01
煤比
143
141
137
133
131
132
135
133
132
128
铁水温度
1485
1484
1481
1486
1484
1487
1479
1480
1474
1468
理论燃烧温度2225
2238
2255
2252
2256
2254
2226
2233
2237
2243
2.7利用系数
随着利用系数的提高,高炉的冶炼周期缩短,意味着焦炭在风口带的高温回旋区停留时间缩短,同时反应生成的SiO气通过滴落带的
时间缩短。
据文献可知利用数每提高0.75t/(m3*d),[Si]可降低
0.1%。
2.8适应气流变化的压差控制及顶压调整
在高炉的实际操作中,当炉内气流发生较大变化或炉内的压量关系紧张且不匹配时,可以在减风的同时适当短时间调整顶压,控制合理压差,确保尽快消除由于气流变化对炉况带来的不良影响,当炉内气流稳定、压量关系正常后,必须维持正常顶压操作,本高炉根据长期生产经验压差控制在115kpa以下,在炉矿气流波动情况下压差控制在110kpa以下.
2.9低焦比操作
一号高炉自2012年大修以来,实现了高风温、多风口均匀大喷
吹。
风温达到1205摄氏度,吨铁喷煤量130kg,最高达到过145kg/Fe.高炉煤气利用率也由42%提高至45%左右,入炉焦比的降低,有效地降低了SiO2的带入量,同时也减少了硅的还原。
2.10稳定合理的操作炉型
合理的炉型稳定高炉气流,提升煤气利用,入炉焦比降低,减少
SiO2的带入量,同时也减少了硅的还原.而且低硅冶炼最害怕的就是
气流失常,气流起冲极意引起炉凉.一号高炉自11月5日炸瘤后合
炉型相对合理生产得到了巨大的提升见下表:
表四
项目
Si
平均日产量煤气利用
燃料比
焦炭水分
炸瘤前
0.37
1477.35
44.3
556
5.15
炸瘤后
0.38
1501.66
44.8
540
6.25
对比
-0.01
-24.31
-0.5
16
-1.1
由上可以看出炸瘤后对气流以及煤气利用的影响,焦比下降达16Kg/tFe,产量上升24t/d.大幅减少减少了焦带入的SiO2量同时也缩短了炉料在炉内
的停留时间,减少Si的还原.目前我们的[Si]未进一步降低主要
是过渡最近雨水较多且检修后炉况在进一步恢复过程中.
2.11保持高炉稳定顺行
采用合理的操作制度,保持高炉顺行稳定,正确地应用上、下部调
剂以取得合理的煤气流分布及良好的炉缸工作状态。
炉况的稳定顺行
不但是高产、优质、低耗和长寿的主要手段,也是冶炼低硅、低硫生
铁的必要条件。
在改变料柱透气性的基础上,采取大风量、大料批(每
批14.5t)、多环布料、抑制边缘、发展中心的操作方针,使顶压升高,PCO增大,燃料比和生铁硅含量进一步降低。
同时也采取了以下管理措施:
(1)强化出渣出铁的作业管理,提高出铁正点率和均匀率,减少炉缸内的贮铁贮渣量,避免渣铁贮量过多而使风压过高、料速变慢而炉温升高。
每天出铁从16次,正点率从50%提高至85%。
均匀率由
60%提升到80%
(2)加强设备管理,保证设备的稳定率与完好率,防止
设备故障造成非计划休风而引起热量补充不足。
(3)对主沟、渣铁沟、
撇渣器、铁罐等系统的耐火材料的侵蚀加强跟踪管理,特别是对主沟
的修补已做到不影响出铁次数。
3
根据长期的生产实践,同行业有以下经验公式:
含硅量降低0.1%可增产2%、吨铁节焦4kg。
含硅量降低不仅因燃料比降低使产量提高,
而且使炉缸热储备和煤气量均相应减少。
结合上、下部调剂,通过改
善煤气流分布,使中心活跃,压差降低,为加风创造了条件,提高了冶
炼强度并增加了产量。
同时体现在炼钢工序的效益有:
降低氧气消耗,
减少渣量,从而降低石灰、合金和钢铁料消耗;缩短冶炼周期,降低生
铁含硅量,也对提高炼钢工序的效率和效益做出了贡献。
4低硅冶炼注意事项
低硅冶炼虽能带来巨大的经济效益但同时也具有较大的风险,
对操作者素质要求较高一不小心极度容易引起炉凉甚至是炉缸
冻结.个人总结低硅冶炼需要注意的几点注意事项:
(1)加强料
单的检查,防止出现装料错误.
(2)定期热炉.(3)加强工长的操作素养,对气流以及低料线危害的认识.(4)加强基础工作的管理,尤其是炉前出铁操作的管理.(5)加强冷却设备的检查,严防漏水.(6)加强原燃料的管理,避免质量及水分的大幅波动造
成热制度不稳定.(7)稳定用风氧,及时控制好料速,均匀跑料。
(8)减少碱金属的入炉,防止结厚结瘤影响操作炉型的变化。
5目前一号高炉存在的不足
(1)新班长较多,三班出铁堵口操作上统一意识需加强。
(2)渣中MgO含量尚略显偏低。
(3)频繁出现高碱度渣相,三班工长对渣的调剂需进一步加强。
(4)三班出铁均匀率以及正点率仍显偏差,铁口合格率有待进一步提高。
(5)炉身上部仍存在一定的结厚,对气流产生一定的影响,偶有渣皮滑落的现象造成风口小套冷却器的破损。
(6)三班工长对气流的认识仍有所欠缺。
结语
采取提高原料质量、在保证炉况顺行的条件下严格控制并稳定炉
缸和铁水温度,实施高风温、高顶压等适合新冶钢低硅冶炼的操作方
针,可使焦比和生铁的硅含量降低,为炼钢提供优质生铁,也能降低冶
炼成本,创造经济效益。
操作中切忌盲目大幅降硅,稳中求进,逐步推进。
参考文献
[1]金智彬.浅谈降低炼钢先铁含硅量.海南矿冶,1994,(4).
[2],,王荣成.译自
TheironandsteelinstituteofJANPAN,NO.3,1988[3]李献琥.湘钢2#高炉的降硅冶炼,湖南冶金,1995,
(1)
[4]韩金玉.天铁700m3高炉低硅冶炼实践.天津冶金,2005,(5):
3-5.