哈工大综合课程设计卧式升降台铣床.docx
《哈工大综合课程设计卧式升降台铣床.docx》由会员分享,可在线阅读,更多相关《哈工大综合课程设计卧式升降台铣床.docx(21页珍藏版)》请在冰豆网上搜索。
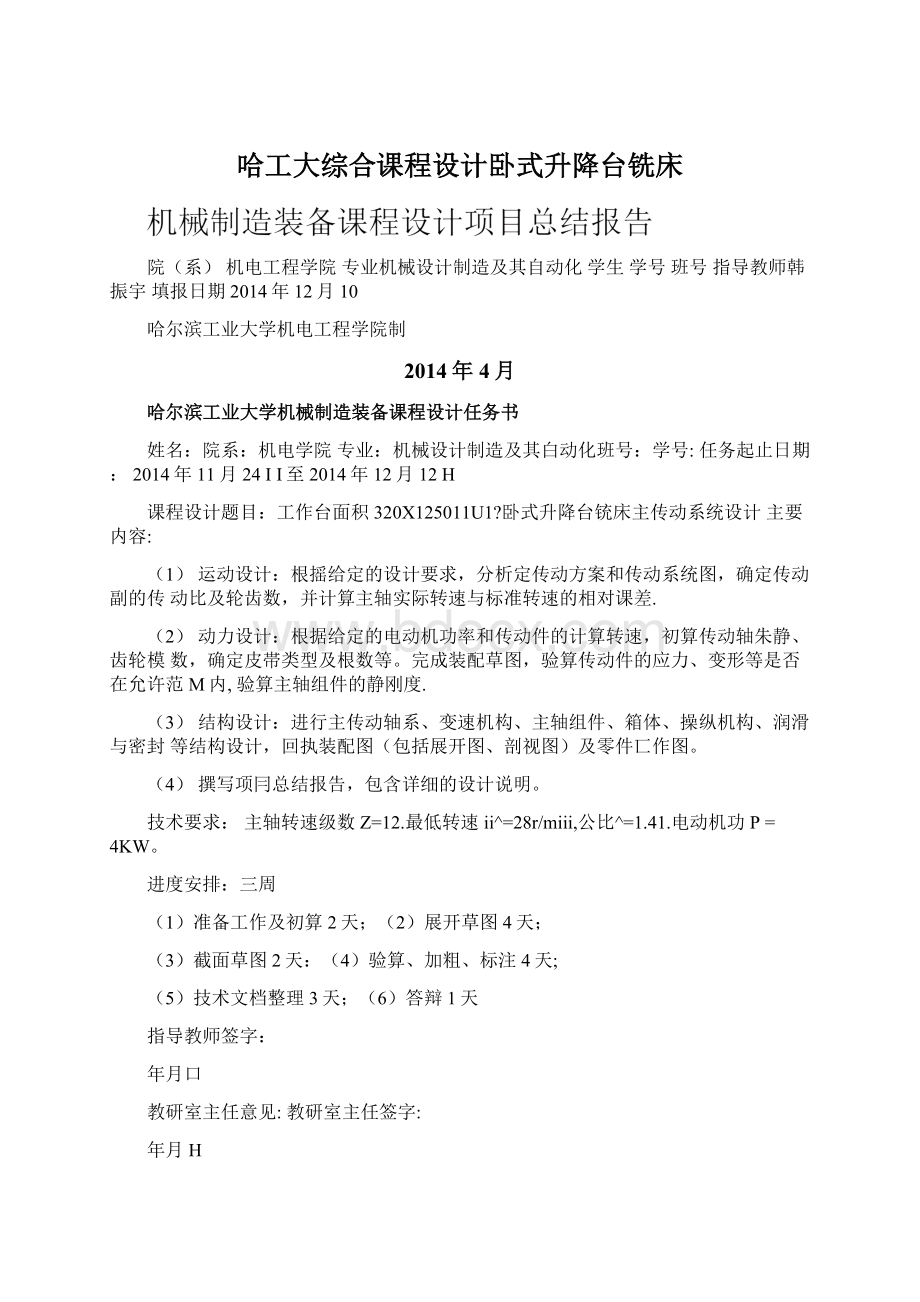
哈工大综合课程设计卧式升降台铣床
院(系)机电工程学院专业机械设计制造及其自动化学生学号班号指导教师韩振宇填报日期2014年12月10
哈尔滨工业大学机电工程学院制
2014年4月
哈尔滨工业大学机械制造装备课程设计任务书
姓名:
院系:
机电学院专业:
机械设计制造及其白动化班号:
学号:
任务起止日期:
2014年11月24II至2014年12月12H
课程设计题目:
工作台面积320X125011U1?
卧式升降台铳床主传动系统设计主要内容:
(1)运动设计:
根摇给定的设计要求,分析定传动方案和传动系统图,确定传动副的传动比及轮齿数,并计算主轴实际转速与标准转速的相对课差.
(2)动力设计:
根据给定的电动机功率和传动件的计算转速,初算传动轴朱静、齿轮模数,确定皮帯类型及根数等。
完成装配草图,验算传动件的应力、变形等是否在允许范M内,验算主轴组件的静刚度.
(3)结构设计:
进行主传动轴系、变速机构、主轴组件、箱体、操纵机构、润滑与密封等结构设计,回执装配图(包括展开图、剖视图)及零件匸作图。
(4)撰写项冃总结报告,包含详细的设计说明。
技术要求:
主轴转速级数Z=12.最低转速ii^=28r/miii,公比^=1.41.电动机功P=4KW。
进度安排:
三周
(1)准备工作及初算2天;
(2)展开草图4天;
(3)截面草图2天:
(4)验算、加粗、标注4天;
(5)技术文档整理3天;(6)答辩1天
指导教师签字:
年月口
教研室主任意见:
教研室主任签字:
年月H
1・项目背景分析
1.1.综合课程设计II的目的
1.2.金屈切削机床在国内外发展趋势
2.研究计划要点与执行情况
2.1.设计任务
2.2.进度安排
3•项目关键技术的解决4.具体研究内容与技术实现
4.1.机床的规格及用途
4.2.运动设计
1.确定极限转速:
2.确定结构网或结构式:
3.绘制转速图:
4.绘制传动系统图
1)确定变速组齿轮传动副的齿数
2)核算主轴转速误差
4.3.动力设计
1.传动件的计算转速
2.传动轴直径初定
3.主轴轴颈直径的确定
4.齿轮模数的初步计算
4,4.结构设计
4.5.零件的验算
1宜齿圆柱齿轮的应力计算
2齿轮精度的确定
3传动轴的弯曲刚度验算
4主轴主件静刚度验算
5.存在的问题与分析6・技术指标分析
参考文献
1・项目背景分析
综合课程设计H的目的
机床课程设计,是在金屈切削机床课程之后进行的实践性教学环节。
其目的在于通过机床主运动机械变速传动系统的结构设计,使学生在拟定传送和变速的结构方案中,得到设计构思、方案分析、结构工艺性、机械制图、零件计算、编写技术文件和查阅技术资料等方面的综合训练,树立正确的设计思想,議握基本的设计方法,并培养学生具有初步的结构分析、结构设计和计算能力。
1.2.金属切削机床在国内外发展趋势
机床作为加工的母机,总是要保证和提髙加工质最和生产率,随着科技的不断进步,各种机床也相应地不断发展与更新,如性能参数的提高、功能的扩大、切削功率的加大,门动化程度的提髙,机床动态性能的不断改善,加工精度的不断提高,基础元件的不断创新,控制系统的更新等等。
我国机床工业的发展趋势:
根据机床工具工业局对振兴我国机床工业的设想,要在以后相当长时期内限制和压缩落后机床的生产,要化大力气发展高性能、高效率、髙水平的适合国民经济需要的"高档"产品,改善机床品种的构成比。
重点发展机、电、仪结合的产品。
注意在冲压、电加工、激光、等离子加工中应用数控技术。
国外机床工业的发展,特别讲究机床的精度、效率,讲究机床制造工艺技术水平,试验分析与理论研究。
从七十年代以来,国外己普遍推广使用数控机床。
n本和美国已建成柔性自动化生产车间和柔性自动化工厂,整个机床制造的技术水平和H动检测控制技术已有大幅度提高。
2•研究计划要点与执行情况
2.1.设计任务
机械制造及其自动化专业的“综合课程设计是以车床和铳床主传动系统设计为内容,每个学生设计参数不同,完成展开图和截面图各一张及相关计算和文件和项目结题报告。
(1)设计内容要求
图纸工作a:
画两张图。
其中:
开展图(A0):
轴系展开图。
其中摩擦离合器、制动和润滑不要求画,但要求靠握:
操纵机构只画一个变速手柄。
截面图(A1):
画剖面轴系布置示意图(包括截面外型及尺寸、车床标中心高人
(2)标注:
中心距、配合尺寸、定位尺寸、中心高(车床)、外型尺寸。
(3)标题栏和明细栏
不设明细表,件号采用流水号(1,2,3,…)标注,标准件的标准直接标在图纸上(件号下面);
标题栏采用标准装配图的标题栏(180X56),其中,图号:
KS01(表示:
课设01号图纸”单位:
哈尔滨工业大学;图名:
主传动系统装配图。
(4)主轴端部结构要按标准画。
(5)按模板编写《项目总结报告》,相关设计计算内容,写到“具体研究内容与技术实现"项中。
要求验算:
一对齿轮,小齿轮验算接触弯曲强度,大齿轮验算接触弯曲强度,一根传动轴,主轴按两支撑计算。
2.2.进度安排
一、运动设计
根据给定设备的用途规格、调速范围、极限转速的、公比和功率要求,拟定传动方案,确定传动系统图和转速图。
二、动力设计
根据功率和速度,选择电机型号,确定各传动件计算转速,初算传动件尺寸、绘制装配图草图,验算传动件的应力、刚®、寿命等参数。
三、结构设计
绘制主传动系统展开图和截面图,完成传动件、箱体、操纵机构零部件结构设计。
完成相关技术文档,形成项H总结报告a
3•项目关键技术的解决
减速箱内各级减速比分配、齿轮模数齿数齿宽的选取和机床功率的计算为本次设计的关键内容,解决以上问题可以完成机床基本功能的实现以及机床正常运行的保证。
同时主轴箱内传动件的空间布置是极其重要的问题之一,变速箱内各传动轴的空间布置rr先要满足机床总体布W对变速箱的形状和尺寸的限制,还要考虑各轴受力情况,装配调整的操纵维修的方便。
其中齿轮的布置与排列是否合理将直接影响主轴箱的尺寸大小、结构实现的可能性以及变速操纵的方便性。
主轴传动件的合理布置.也很重要。
合理布置传动件在主轴上的轴向位置,可以改善主轴的受力情况,减小主轴变形,提高主轴的抗振性。
4.具体研究内容与技术实现
4.1.机床的规格及用途
通用机床,加工范ra广泛,用于各种圆柱铳刀.盘铳刀.成型铳刀.端铳刀.角度铳刀等來铳削各种斜面.成型表面、沟槽及齿轮.螺旋槽等。
参数如下:
类型
工作台(mm')
公比(P
级数Z
功率(KW)
卧式升降台铳床
320X12500
1.41
28
12
4
4.2.运动设计
1•确定极限转速:
由己知设计要求,车床的主轴最小转速是,主轴转速级数,公比,故可得出,O根据己知的公比、最小转速和级数计算最大转速和^^"级转速,查标准数列得到各级转速分别为:
28.40、56、80、112.160.224、315.450.630.900和
1250。
2•确定结构网或结构式:
根据传动副“前多后少”的原则,选择主轴转速结构式。
根据级数耍求,需
要有一组16复的转速。
故其转速结构式及级比指数为Z=\x2^x2^.符合要求。
则系统的结构网如卜图:
3•绘制转速图:
1)选定电动机
铳床为一般金属切削机床的驱动,没有特殊性能要求,所以采用Y系列封闭门扇冷式鼠笼型三相异步电动机。
Y系列电动机高效、节能、启动转矩大、噪声低、振动小、运行安全可靠。
根据《机床使用设计手册》选择电动机的型号为Y112S-4,同步转速1500r/min,满载转速1440r/min.功率5.5kW。
2)分配总降速传动比
最后扩大组的级比指数为6,同时升速和降速都不能超过极限范围,所以III轴的最低转速只能为112r/min,根据“前慢后快”的原则II轴的最低转速可以为224r/min或315r/niin,选择较低转速虽然可以减小发热利噪声,但这两根轴上的齿轮副模数会略大,所以选择为315r/mino电机转速为1450r/min,II轴的转速定为630r/min,可选出电机传入齿轮传动比。
3)确定传动轴的轴数
变速机构共需要5个轴。
绘制转速图如下:
4•绘制传动系统图
因为零件的参数尚未确定,先根据转速图,按传动副的传动比拟定一个主传动系统草图如下:
n
1)确定变速组齿轮传动副的齿数可用计第法或查表法选定齿轮的齿数各个变速组双轴间的齿数和的确定sR+丄]
IUmxn丿式中:
同一变速组中的最小传动比,第一、二变速组U^=l/2.第三变速
u^,=l/4;同一变速组中®小齿轮齿数,Z唤=18〜20。
由参考文献【2】表5J査表选定选定第一变速组的齿数和为72,小齿轮齿数分别为24、30、36。
第二变速组的齿数利为80,小齿轮齿数分别为21、40。
第三变速组为避免出现齿轮轴,选择齿数和为U5,查表得小齿轮的齿数分别为23和38。
2)核算主轴转速误差
实际传动比所造成的主轴转速误差,一般不超过±10(0-1%,即
±10(1.41-1>=4,1%0则通过齿轮齿数计算的实际主轴转速误差如下表:
主轴转速误差与规定值之间的比较
标准转速
r/min
实际转速计算式
实际转速
r/min
转速误
差%
在标准范围内
28
21242123aX—X—X—X—r48485992
28.0
0
40
21302123
ILXXXX'
48425992
40.0
0
56
21362123n,X—X—X—X—
48365992
56.1
0.1
80
21244023n,X—X—X—X—
48484092
78.8
1.6
112
21304023
1LXXXX
48424092
112.5
0.4
160
21364023aX—X—X一X—
48364092
157.5
1.6
224
21242177r48485938
227.2
1.4
315
21302177aX—X—X—X—
48425938
324.6
3.0
450
21362177
11XXXX—
r48365938
454.4
1.0
630
21244077
11X—X—X—X—
48484038
6383
1.3
900
21304077
11XXXX
48424038
911.8
1.3
1250
2136祀77
ILXX—XX
48364038
1216.6
2.1
4-3.动力设计
零件的计算,需耍知道它们的计算转速W即参与传递全功率的域低转速、传递全扭矩的最离转速。
各零件的计算转速可从转速图上按主轴的计算转速确定。
1•传动件的计算转速
计算转速为主轴或传动件传递全部功率时的绘低转速,所以各轴的计算转速和齿轮的计算转速分别如下表
专动轴计算转速表
轴序号
I
II
III
IV
V
计算转速r/min
1440
630
315
112
80
各齿轮计算转速表
序号
1
2
3
4
5
6
1
8
计算转速r/min
1440
630
630
630
630
315
315
450
序号
9
10
11
12
13
14
15
16
计算转速r/min
315
315
315
112
224
112
315
80
2•传动轴宜径初定
传动轴直径按扭转刚度用下式进行概算
卄9】佛r
式中〃一传动轴直径(mm);
N—该轴传递的功率(kW);
Hj—该轴的计算转速(r/min);
[间一该轴每米长度允许扭转角(deg/m),一般传动轴取同=0.5。
〜1°这里取0.8°。
则各个轴的初算直径为
I轴
I4.996
dj=91^nim=23-12niin
V1440X0.8
取为dj=25imuo
II轴
d,=91』4.702I述=28.28mmV630x0・8
取为djj=301111110花键轴尺寸取6x28x30。
III轴
dm=91Jimi=32.30mm
FV315x0・8
取为dm=40mm。
花键轴尺寸取8x36x40。
IV紬
drv=91Jnmi=41・83nim
V112X0.8
取为div=50mm°花键轴尺寸取8x46x50。
3•主轴轴颈直径的确定
由参考文献[1]表3-13査得主轴前轴颈的直径D严60~95mnb取为80min。
后轴颈的直径Dj=(0・7〜0・85)D]=56〜6&nm。
取为65mm。
尽最使主轴截而变化要小,外径尺寸要缓减。
铳床主轴内孔直径按铳床主轴端部尺寸标准选取。
主轴材料选为45号钢,调质处理,在主轴端部、锥孔、定心轴颈和定心锥面处进行高频W部淬火。
4•齿轮模数的初步计算
同一变速组中的齿轮取同一模数,选择负荷故重的小齿轮,第一变速组选择齿轮1计克,第二变速组选择齿轮6计算,第三变速组选择齿轮11计算。
按简化的接触疲劳强度公式进行计算:
111=1633&I—mm
式屮叫一按接触疲劳强度计算的齿轮模数(nun);
N,一一驱动电动机功率(kW):
iijil算齿轮的il算转速(r/min
u—一大齿轮齿数与小齿轮齿数Z比U>1
Z]小齿轮齿数;
齿宽系数,%=色(B为齿宽,m为模数),取%=&
111
[aj一一许用接触应力(MPa),一般的机床寿命为6~10年,Z/l,
齿轮材料为调质45号钢表面淬火,査得许用接触应力0」=137OMPa。
(1286+1)x5.5
则初步计算各个传动组的齿轮模数如下:
第一变速组的齿轮1
m.=16338引J~—_—Tnun=l・53niin
)VSx21-X1286x1370-X1440
第二变速组的齿轮4
in=16338』12+1职5弓二]皿1=i.88nun
)V8x24-x2xl370-x630
第三变速组的齿轮10
第四变速组的齿轮15
4.4.结构设计
见A0及A1图纸。
4.5.零件的验算
1宜齿圆柱齿轮的应力计算
弯曲应力验算公式为
191x10XK.K,KN「,
屯=一(MP町勻氐]
式中:
N--传递的额定功率(kW),N=〃Ni;
Nd-一电动机的功率(kW);
"——从电动机到计算齿轮的传递效率;
——计算转速(r/min);
Ill齿轮模数(mm);
B齿宽(mm);
Z——小齿轮齿数;
U一一大齿轮齿数和小齿轮齿数之比:
K,——寿命系数:
0——工作期限系数:
T一一齿轮在机床工作期限T,内的总工作时间(h).对于中型机床的齿轮
取1=15000-200001】«同一变速组内的齿轮总工作时间可近似地认为T=T/p,p为该变速组的传动副数。
此处取Ts=15000h,p=2,则T=7500ho
Uj——齿轮的最低转速(r/min),此处小齿轮为315,大齿轮为80;
C。
一一基准循环次数,钢和铸铁件:
接触载荷取Co=lO\弯曲载荷取
q=2x106;
m——疲劳曲线指数,钢和铸铁件,接触载荷取m=3,弯曲载荷时,对正火、调质及整体淬硬件取m=6,对表面淬硬(高频、渗碳、氮化等)取m=9;
此处解得Kr=1.95(小)/2.60(大)。
此处取0.97/0.98:
瓦一一转速变化系数,
解得瓦=1.09/2.11。
K3一一1:
作状况系数,考虑载荷冲击的影响•主运动(中等冲击)取K31.6;
Kl-动载荷系数.此处取1.1;
齿向载荷分布系数,此处取L05;
丫~齿形系数,大齿轮取0310:
[丐卜许用接触应力(MPa),査表3-9,]=1370/WPo;
[q卜许用弯曲应力(MPa),査表39[片]=283MPa。
代入式中得
符合要求。
符合要求。
2齿轮精度的确定
齿轮精度等级的选择根据它的用途.圆周速度-载荷状况和对振动、噪声、使用寿命等方面的要求确定。
本设计中齿轮传递的速度和功率都不太大,故选用7级精度的圆柱齿轮。
3传动轴的弯曲刚度验算
(1)传动轴III的弯曲载荷
齿轮传动轴同时受输入扭矩的齿轮驱动力Qa和输出扭矩的齿轮驱动阻力
Qb的作用而产生弯曲变形,当齿轮为直齿圆柱齿轮时,其啮合角a=20%齿而靡擦角P=5.72。
时,其弯曲载荷由下式计算:
Q(Q)"怙N)
式中:
N一一该齿轮传递的全功率(kW),此处取N=S.SkWm,z——该齿轮的模数(mm}.齿数
n该传动轴的计算工况转速(r/min),
IL,一一该轴输入扭矩的齿轮计算转速(r/min)
该轴输出扭矩的齿轮计算转速(r/min)
选取III轴进行弯曲刚度验算,输入齿轮选取48.其计算转速为315r/min,输出齿轮选取21,其计算转速为315r/min,则II轴的计算工况转速为315r/mino带入
式(4-8)计算得:
5.5
Q=2.12x10^————(N)=5875.5N
3x315x21
(2)验算两支承传动轴的弯曲变形
齿轮传动轴的抗弯刚度验算,包括轴的域大挠度,滚动轴承处及齿轮安装处的倾角验算。
梵值均应小于允许变形量[y]及[&],允许变形量见参考文献[6]表3.10-7.得
[y]=(0.01-0.03)m=3(0.01^0.03)=(0.03"0.09)mm
[<9]=O.OO5rad
为了计算上的简便,可以近似地以该轴的中点挠度代替最大挠度,其最大误差不超过3%。
若两支承的齿轮传动轴为实心的圆形钢轴,忽略其支承变形,在单在弯曲载荷作用下,其中点挠度为:
式中:
/两支承间的跨距(mm),对于轴llhMOOmm
D--该轴的平均直径(mm).本轴的平均直径D=4QmmX丄
%——齿轮的工作位置至校近支承点的距离{mm)70mm:
130mm代入数据得:
7070
400^x5.5x(0,75x—-(—)3)
y=171397(mm)=0・078mm
'40^x15x48x315
4003x5.5x(0.75x1^-(12^)3)
%=17139型~型一(null)=0.24911U11
b40^x3x21x315
计算在驱动力Qa和驱动阻力Qb同时作用下,传动轴中心的合成挠度儿,可按余弦定理计算
Yh=Jy:
+K_2y"%cos0(uun)
式屮:
Yh一一被验算轴的中心合成挠度(mm)
y,--输入扭矩的齿轮在轴的中点引起的挠度(mm)
乂一—输出扭矩的齿轮在轴的中点引起的挠度(mm)
P——驱动力oQ和阻力bQ在横剖面上,两向量合成时夹角
6—一在横剖面上,被验算的轴与其前、后传动轴连心线的夹角,按被验算的轴的旋转方向计最,由剖面图上可得^=180\啮合角a=20。
,齿面磨擦角P
=5.72,得
0=180-2(20+5.72)=128.56
代入式中计算,得y、=j0・078'+0.249'—2x0・078x0・249xcosl28・56(mm)=0303nun<[y]
未满足要求。
传动轴在支承点A,B处的倾角&A垢时」J按下式进行近似计算:
乞=-务=-y^(rad)=,再:
=0.0045(rad)S[&]
满足要求
4主轴主件静刚度验算
(1)主轴支承跨距L的确定
选定前端悬伸最C.主轴前端的悬伸长度,即从主轴外侧前支撐中点(滚锥轴承及向心推轴承
则是接触角法线与轴线的交点处)到主轴前端的距离,这电选定C=75mmo
一般最佳跨距L0=(2〜3)C=140^225muio考虑到结构以及支承刚度会因
磨损不断降低,应取跨趴L比最佳跨距L0大一些。
再考虑到结构需要,这里取
L=370ninio
(2)计算条件的确定
变形最允许值:
验算主轴轴端的挠度yo,对普通机床前端挠度的允许值[yo]t目前广泛彳^^^^经
本设计中L=370imin
验数据为;[y0]<0W02L(mm),英中L为主轴两支撩间的距离(mm)°
故前端挠发的允许值[yO]应不大于0・0740mm。
验算时以此作为是否合格的依据。
(3)轴组件的静刚度验算
1.切削力的确定
最大圆周切削力R须按主轴输出全功率和最大扭矩确定,其计算公式为:
式中:
Nd——电动机额定功率(kW),此处Nd=4kW
张——主传动系统的总效率,%取为各传动副、轴承的效率,总效
率缶=0.7〜0.85,此处,为方便起见,起%=0.75
®—一主轴的计算转速(「九血),由前知,主轴的计算转速为80r/min
Dj——计算直径,对于铳床,Dj为最大端铳刀计算直径,对于升降台宽度
为320x1250的卧式铳床,其端铳刀的计算直径及宽度分别为Dj=160nim
B=60nun
得R=4476N
验算主轴组件刚度时,须求出作用在垂宜于主轴轴线的平而内的最大切削合力P•对于升降台式铳床的铳削力,一般按端铳计算,不妨设本铳床进给系统
的末端传动副有消隙机构,应采用不对称顺铳,则各切削分力与R的比值可大致
则P=应苫".98「4386N,P严1.1P严4923.6N,即E与水平面成60。
角,
Pt在水平面的投影与Ph成65°角.
3切削力的作用点
设切削力P的作用点到主轴前支承的距离为s,则
S=C+W(11U11)式(449)
式中:
C——主轴前端的悬伸长度,此处c=75imu
W——对于普通升降台铳床w=B=60inm
代入,切削力P的作用点到主轴前支承的距离为s=135111111
4.受力分析及计算:
由于主轴上的大齿轮比小齿轮对主轴的刚度影响较大,故仅对大齿轮进行计算.
为了计算上的简便,主轴部件前端挠度可将各载荷单独作用下所引起的变形值按
线性进行向量迭加,其计算公式为:
(1)计算切削力P作用在S点引起主轴前端C占的挠度儿P
_r3sC"-C^IsC(1+S)(1+C)SC,,、+苗+cl+市]仙)
6EIc3EICglC」式(4・20)
对圆锥滚子轴承:
Ca或G=3.01i°®z°V^R°®cos'®a
i—-滚动体的列数
z——每列中的滚动体数zA=16.zB=20
10——滚子的有效长度10A=26;10B=35
a-一轴承的接触角
3=15°
R——轴承的径向负荷RA=210000;RB=4400