年产100吨聚氯乙烯色母料车间工艺设计.docx
《年产100吨聚氯乙烯色母料车间工艺设计.docx》由会员分享,可在线阅读,更多相关《年产100吨聚氯乙烯色母料车间工艺设计.docx(67页珍藏版)》请在冰豆网上搜索。
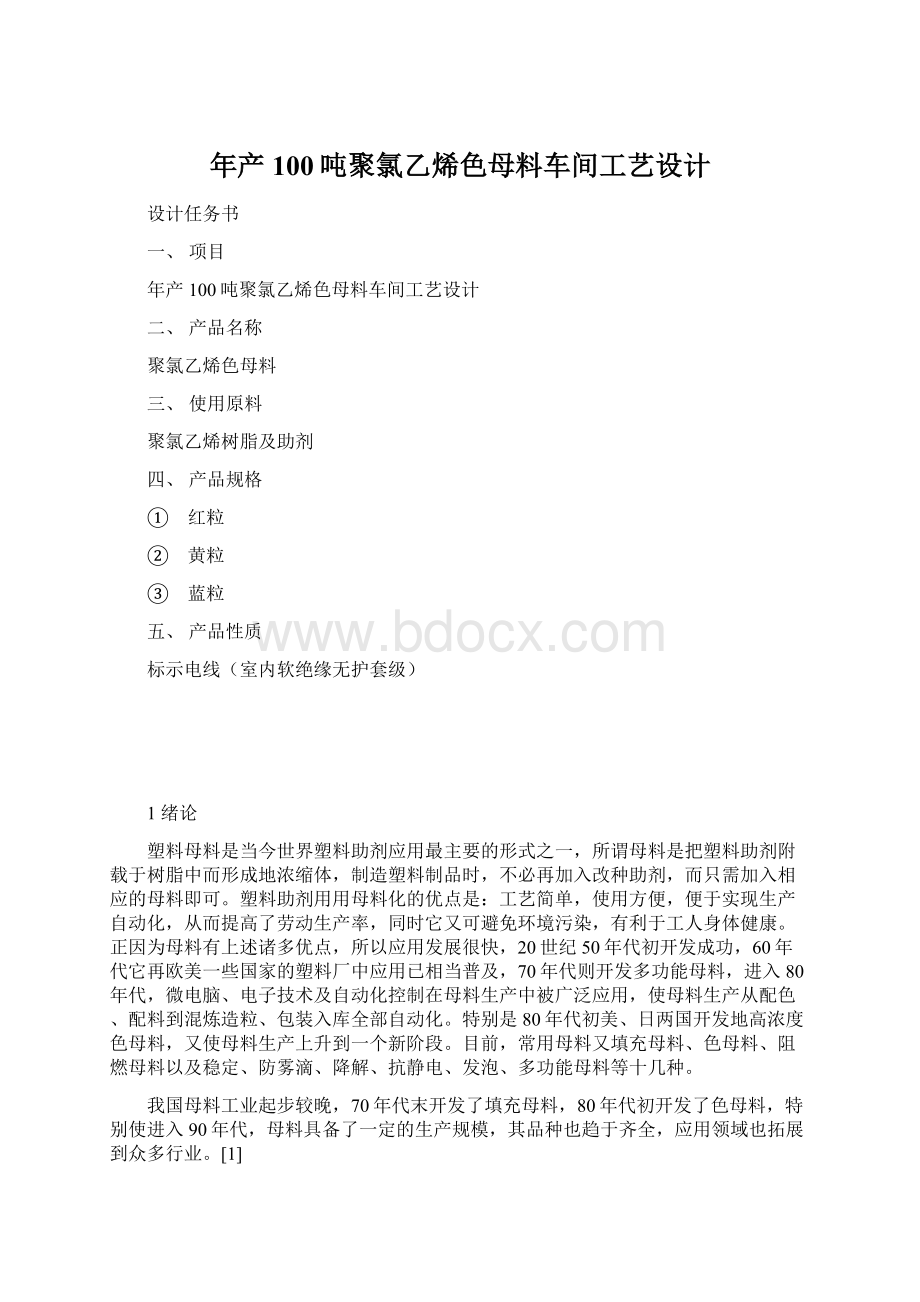
年产100吨聚氯乙烯色母料车间工艺设计
设计任务书
一、项目
年产100吨聚氯乙烯色母料车间工艺设计
二、产品名称
聚氯乙烯色母料
三、使用原料
聚氯乙烯树脂及助剂
四、产品规格
① 红粒
② 黄粒
③ 蓝粒
五、产品性质
标示电线(室内软绝缘无护套级)
1绪论
塑料母料是当今世界塑料助剂应用最主要的形式之一,所谓母料是把塑料助剂附载于树脂中而形成地浓缩体,制造塑料制品时,不必再加入改种助剂,而只需加入相应的母料即可。
塑料助剂用用母料化的优点是:
工艺简单,使用方便,便于实现生产自动化,从而提高了劳动生产率,同时它又可避免环境污染,有利于工人身体健康。
正因为母料有上述诸多优点,所以应用发展很快,20世纪50年代初开发成功,60年代它再欧美一些国家的塑料厂中应用已相当普及,70年代则开发多功能母料,进入80年代,微电脑、电子技术及自动化控制在母料生产中被广泛应用,使母料生产从配色、配料到混炼造粒、包装入库全部自动化。
特别是80年代初美、日两国开发地高浓度色母料,又使母料生产上升到一个新阶段。
目前,常用母料又填充母料、色母料、阻燃母料以及稳定、防雾滴、降解、抗静电、发泡、多功能母料等十几种。
我国母料工业起步较晚,70年代末开发了填充母料,80年代初开发了色母料,特别使进入90年代,母料具备了一定的生产规模,其品种也趋于齐全,应用领域也拓展到众多行业。
[1]
1.1塑料着色的含义及目的
塑料着色就是采用某种技术手段将着色剂加入到树脂中使之具有某种颜色的过程。
塑料着色的目的主要以下三方面:
a美化塑料制品,提高制品得商品价值,增加顾客购买欲,这对于日用塑料制品尤为重要。
b标识电线得类别,给电工配线和检修带来极大得方便,并且还有向人们表示安危、警示的作用,如交通岗得红绿灯和公路路标等。
c着色剂不仅有着色作用,而且往往还有其他功能,如炭黑具有防老化作用、对紫外线的屏蔽作用、导电作用、填充和增强作用。
因此,塑料制品着色的同时,还可以改善塑料制品的某些性能(如改善光学性能和耐候性)或赋予塑料制品特殊功能(如赋予导电性、防紫外线透过、促进农作物增加产量等。
)
色母料是颜料粒子借助于分散剂和机械作用,稳定地分散成一定粒径并以超常浓度均匀分布到载体树脂中的颜料制备物。
塑料着色法是先制得色母料,然后再与大量树脂熔混,使后者着色,此法吸收了色粒着色法、糊状着色法、干法着色法等的优点,极大地提高塑料制品外观质量、节约能源、改善环境污染、减轻工人的劳动强度、减少费用、实现着色连续化、自动化等均极有利,因而有较高的经济价值和社会效益。
可以说,色母料着色法使目前最先进、最科学、最实用的一种着色方法。
1.2色母料配方设计及举例
色母料的结构常由颜料核、分散层、载体层三层构成。
由于塑料品种繁多,性能各异,加工条件和使用环境又有很大不同,所以对着色剂、分散剂、和载体树脂要求就不同。
PVC塑料着色过去多采用传统的色浆着色法。
近年来,开发了PVC色母料,后者具有以下优点:
aPVC色母料中,颜料含量高,一般在40%~70%(重量百分数),比相应色浆的颜料含量高一倍左右。
b色母料颜色分散均匀,能长期进行保存,而色浆随放置的时间加长,颜料产生沉降,影响着色质量
c使用色母料着色,其着色工艺简单,制品生产厂无环境污染,使用方便.
在PVC色母料配方设计中,应着重考虑以下几方面:
(1)载体树脂
颜料加入使PVC粘度增加,流动性下降,从而影响颜料的分散,所以必需要使含有大量颜料的PVC色母料流动性大于PVC本色料。
因为当为数量大的粘性熔体和少量的粘性熔体相混时,只有当数量少的粘性熔体粘度远小于数量大的熔体时,才能充分混合。
因此我们制得的PVC色母料,其熔体粘度要远小于本色料。
更具上述原则,载体树脂选用悬浮聚合的PVC,其聚合度840~1100为好。
有资料报道,国外用于PVC的色母料,其主体为聚邻笨二甲酸丁二甲酯,无PVC成分。
(2)增塑剂
多选用DOP或DBP,其用量90~100phr为宜。
(3)颜料
由于无机颜料和有机颜料吸油值不同,后者大于前者。
一般来说,无机颜料(炭黑除外)含量为60%~70%;有机颜料含量为40%~50%。
(4)其他助剂[2]
热稳定剂多选用液体Ba-Zn,由于母料加工时,塑炼温度较低,一般采用2.5phrBa-Zn复合稳定剂即可。
润滑剂多选用硬脂酸(Hst),其用量一般为0.3phr。
综上所述,PVC色母料大致配方如下:
载体:
SPVC(聚合度=840~1100)100份
增塑剂(DOP或DBP)90~100份
着色剂:
无机颜料60~70份稳定剂(Ba-Zn)2.5份
或有机颜料40~50份润滑剂(Hst)0.3份
1.3色母粒的应用
(1)色母粒在塑料加工业的应用
石油化工发展促使了塑料工业的发展,塑料加工设备不断创新,塑料加工助剂不断更新,使塑料可以替代传统的布匹、皮革、金属、木材等。
现在色母粒用于塑料着色已成为塑料加工工业重要材料之一,塑料着色使商品在漂亮的造型上增添和谐的色彩,使世界更加绚丽多彩。
主要有这种分类:
a包装薄膜中的应用
b流言复合膜中的应用
c吸塑片材中的应用
d包装容器中(中空吹塑成型)的应用
e泡沫塑料(PE/EVA)成型工艺中的应用
f注塑工艺中的应用
g粉末涂料中的应用
h单丝挤出工艺中的应用
(2)色母粒在电缆加工业上的应用
通讯能源的发展促进了电缆工业的大发展。
由于塑料本身具有电绝缘性能好、力学性能优越、耐化学腐蚀、易加工及成本低等优点,已广泛应用于电缆加工业上。
其中有聚氯乙稀绝缘电力电缆、交联聚乙烯绝缘电力电缆、电话通讯电缆等。
色母粒作为塑料进行着色及赋予其某些特殊性能,已在电缆加工业中应用越来越广泛。
主要有以下分类:
a市电话通信电缆中的应用
b交联架空电缆中的应用
c电缆护套料中的应用
(3)色母粒在合成纤维加工业的应用
合成纤维原液着色也就是将合成树脂和色母粒经过加工成为有色纤维直接用于纺织。
其与传统染色发相比,具有投资小、无三废污染,以及着色成本低的优点,因此该项工艺获得了长足进步。
然而促进这项工艺的开发主要因素市色母粒的研究和开发,几乎所有的著名色母粒制造商都有专门设计制造用于合成纤维的色母粒品种。
主要有以下的分类:
a丙纶纤维中的应用
b在涤纶纺前的着色应用[2]
在电线电缆的绝缘和护套材料中,PVC比较便宜,机械性能优良,加工方便,使得它长久以来成为电线电缆行业使用数量最多的材料。
20世纪末以来,PVC材料的环境问题被广泛的认识。
虽然,用无卤料取代PVC材料的呼声越来越高,但是PVC本身具有短期内还无法取代的优势(如价格低廉,阻燃性能好,工艺简单,电绝缘性好,耐油,耐化学试剂等)。
在我国,PVC电缆料发展相对比较早,品种、型号较多。
由于其低廉的价格,加之机械性能优越,使我国PVC电缆料依然具有一定的发展前景。
1.4产品性质和用途
塑料着色是塑料工业中不可缺少的一个组成部分,塑料着色除美化产品外,还可以赋予塑料多种功能:
起标识作用,改善塑料的某些性能或者赋予它某些特性,从而满足应用上的各种需要。
目前所设计的年产100吨PVC色母料的产品性质是标识电线。
它是作为电线的绝缘塑料层,通过对PVC着色,使之容易区别,给配线及检修带来极大的方便,有效地防止操作上地失误。
[3]
1.5物理性能
表1-1为软聚氯乙烯管(电线电缆用)物理性能国家标准(GB/T13527.2-92)。
表1-1软聚氯乙烯管(电线电缆用)中华人民共和国国家标准
项目
指标
项目
指标
拉伸强/MPa
≥15
绝缘电阻/(MΩ.m)
≥1000
断裂伸长率/%
≥150
耐电压/(5000V.min-1)
不击穿
热老化性能拉伸强度残留率/%
≥90
耐热厚度变形率/%
≤10
热老化性能断裂伸长残留率/%
≥70
耐热长度变形率/%
≤10
耐油性拉伸强度残留率/%
≥70
耐寒试验-20±2℃
表面无裂缝
耐油性断裂伸长残留率/%
≥70
自熄性
离开烛面15秒内熄灭
表1-2列举了上海化工厂PVC电线电缆料的行业标准数据。
由于色母料没有固定的国家标准,无论在美国、欧洲、日本都没有特定的标准,所以只能通过各国家所属企业的行业标准来评定色母料的好坏。
聚乙烯色母料的行业标准最为广泛,聚氯乙烯色母料的行业标准却相对比较少,此处是上海化工厂,现在更名为上海化工厂有限公司的聚氯乙烯色母料的技术指标。
表1-2上海化工厂PVC电线电缆料性能
牌号
5320-2B
5320-4.
5320-6.
5320F
数值
J-70
JR-70
无
无
类型
绝缘型
柔软绝缘型
普通绝缘型
阻燃绝缘型
导电线芯最高允许通过温度/℃
70
70
70
70
拉伸强度/MPa
≥15.0
≥15.0
≥17.0
≥12.5
断裂伸长率/%
≥150
≥180
≥200
≥200
冲击脆化温度/℃
—15
—20
—
—
低温冲击压缩温度/℃
—
—
—5
—12
200℃时热稳定时间/min
≥60
≥60
≥80
≥60
200℃体积电阻率/(Ω.m)
1.0×1012
1.0×1012
3.0×1011
2.0×1010
体积电阻率/(Ω.m)
≥1.0×108
≥1.0×108
≥1.0×108
≥1.0×108
介电强度/(MV.m-1)
≥20
≥20
≥20
≥18
热变形/%
≤40
≤50
—
—
软化温度/℃
—
—
170~190
165~185
烘箱内热老化试验(100±2℃,168h)
拉伸强度/MPa
≥15.0
≥15.0
—
—
拉伸强度最大变化率/%
±20
±20
—
—
拉伸强度残留率/%
—
—
80~120
≥80
断裂伸长率/%
≥150
≥180
—
—
断裂伸长率最大变化率/%
±20
±20
—
—
断裂伸长率残留率/%
—
—
80~120
≥80
热老化质量损失/(g.m-2)
≤20
≤20
≤20
≤20
燃烧性氧指数值/%
—
—
—
≥28
高温下压力试验
试验温度/℃
—
—
80±2
—
试验时间/h
—
—
4
—
最大凹限深度/%
—
—
50
—
1-3列举了国内江苏鑫丰塑业有限公司三种牌号的软聚氯乙烯电缆料的物理性能。
表1-3三种软聚氯乙烯电缆料物理性能
试验项目
典型值
NB-70
NB-90
NB-105
绝缘
护层
绝缘
护层
绝缘
护层
拉伸强度/MPa
21
22
25
22
24
23
断裂伸长率/%
310
310
300
290
260
280
热老化时间/h
168
168
168
168
168
168
热老化温度/℃
113±2
113±2
121±2
121±2
135±2
135±2
拉伸强度保留率/%
98
96
97
96
106
101
断裂伸长率保留率/%
97
98
97
94
98
94
热变形/%
20
24
18
20
15
20
低温冲击脆化温度/℃
-20
-25
-15
-25
-15
-20
200℃热稳定时间/min
120
95
100
110
240
140
难燃性(UL94-0)/s
5
6
3
5
3
5
20℃体积电阻率/(Ω.m)
7×1012
6×1010
2.×1012
4×1010
4×1012
4.5×1010
PVC色母料的性质与表中所列性质一致。
2生产方法
2.1工艺选择
PVC造粒的流程有三种:
第一种:
树脂、助剂→捏合→密炼→开炼→出→冷却→平板切粒机切粒→粒料
第二种:
树脂、助剂→混合→密炼→单螺杆挤出→冷却→切粒机切粒→粒料
第三种:
树脂、助剂→混合→双螺杆挤出机→冷却→切粒机切粒→粒料
2.1.1混合塑化方式
第一种生产工艺出现的比较早。
尽管其方式在对工人操作能力上的要求比较低,但是无论在产量质量上、劳动强度上,还是在环保要求上都不能和后两种造粒方式相比较,所以在选择上首先淘汰。
第二种生产工艺目前在国内比较流行,因为单螺杆挤出机相对双螺杆挤出机价格比较便宜,生产效率相对第一种方式大为提高,工艺操作要求一般,但是由于单螺杆挤出机塑化造粒的工艺效果比双螺杆挤出机挤出工艺塑化效果差,排气不理想,在制造室内PVC标识电线时候,容易出现气泡,所以就要求在生产上要求控制原材料的质量及在操作上采取排气有利的措施来解决,增加了加工工艺的复杂性。
其次,单螺杆挤出塑化工艺生产电缆料时,还应该解决电缆料塑化质量要求和物料稳定性之间的矛盾,这就要求配方要更合理,以及低温塑化工艺。
第三种生产工艺是较先进的造粒工艺,而且产率高,符合大批量的生产。
挤出造粒操作连续,密闭,杂质滤出容易,产量高,劳动强度小,环境洁净、噪音小,但塑炼质量不如炼片方式那么容易控制,所以挤出机造粒对于工艺要求和操作要求较高。
[6]196~197由于PVC树脂是一种热敏性树脂,所以采用锥形双螺杆挤出机,因为其挤出段的直径比较小,大大减少了摩擦热,可以避免PVC热敏性树脂过热分解现象。
同时,其喂料区的螺杆和机筒表面积增大,传热好,物料受热快,容易压缩,输送效率高,大大提高了产量质量,并且锥形双螺杆挤出机传动机构紧凑,易于维修维护,且对螺杆拆装方便。
单、双螺杆挤出机的特性比较见表2-1。
啮合型双螺杆挤出机与单螺杆挤出机比较有以下优点:
[4]
a加料容易、挤出量高
b物料在双螺杆挤出机中停留时间短,剪切热小,加工温度低,便于控制,适于那些停留时间较长就会分解或固化或凝聚的物料的着色和混料。
更适合PVC类热敏性塑料的加工。
c优异的排气的性能。
如果物料中有气体和挥发物,可经与排气口连接的真空泵吸出,排气性能好,适合粉料直接挤出成型加工。
d物料的分散、均化、混合、塑炼效果好。
e自洁效果好,单位输入功率产量高,比功率消耗低,挤出效率高。
表2-1中可见,从衡量挤出机的三个要素来看,挤出速率、挤出物质和挤出机能耗均以异向寻装双螺杆挤出机好。
由于双螺杆挤出机具有以上特性,使物料在双螺杆中停留时间短而且塑化均匀,物料所经历的变化过程比较接近,不易产生局部降解,产品质量和产量提高,能耗低,这对于加工热敏性PVC塑料等热敏性物料具有特别意义。
综上所述,双螺杆挤出比单螺杆挤出塑化更均匀,质量更有保证,自动化连续化程度高,产量高,环境洁净、噪音小。
虽然设备投资比单螺杆高,工艺要求和操作要求较高,但是双螺杆投入产出比等经济效益比单螺杆要好。
所以本设计选用双螺杆挤出机挤出工艺。
表2-1单、双螺杆挤出机机性能比较
机种
单螺杆
啮合同向转转双螺杆
啮合异向旋转双螺杆
项目
低速型
高速型
输送作用
摩擦作用
摩擦作用和回流作用
器械强制输送推进
输送效率
小
中
中
大
分散混合作用
小
中
中
大
剪切作用
小
中
大
小
自净作用
微小
中
大
小
能量利用效率
小
中
中
大
自热
大
中
大
小
温度分布
大
中
小
小
停留时间分布
大
中
小
小
最高转速/(r.min-1)
100~300
25~35
250~300
35~45
螺杆最大有效长径比(L/D)
30~32
7~18
30~40
10~21
2.1.2造粒方式
在确定混合塑化方式之后,还需确定造粒方式。
各种造粒方法的工艺流程见图2.1:
图2.1造粒方法流程图
由挤出机塑化并向造粒机输送物料,机头和切粒方法有多种方法:
a.机头使物料形成片状,冷却后由平板切粒机切成立方体形状粒子。
b.物料经过机头被挤压成条状料,冷却后由辊刀或铣齿刀切成圆柱形或球形。
除拉片冷切法用平板切粒机造粒外,其余,都是用挤出机造粒。
挤出造粒有操作连续,密闭,机械杂质混入少,产量高,劳动强度小,噪音小等优点。
由于冷却方式的不同,聚氯乙烯造粒过程中的切粒可分为冷切和热切两大类,见表2-2。
无论何种切粒法方法,均要求粒料的颗粒大小均匀,色泽一致,外形尺寸不大于3~4mm,因为颗粒过大会造成成型时加料困难,熔融也慢。
粒料形状以球形或药片形状较好,因为堆砌紧密空隙小,夹带的空气少,有利提高产品质量。
对于软PVC一类熔体粘度较高的非结晶型物料,粒料的冷却方式可以采用干切粒或鼓风空中热切粒方法,这两种方法实际上都是切成颗粒后在空气中冷却,这两种方式切出的粒子均为短圆柱状或圆棋子状。
本设计选用鼓风空中热切粒法。
表2-2PVC树脂造粒的方式
造粒方法
冷切法
热切法
树脂
拉片冷切
挤片冷切
挤条冷切
干热切
水下热切
空中热切
软聚氯乙烯
适合
适合
适合
适合
适合
适合
硬聚氯乙烯
适合
适合
适合
适合
较适合
较适合
颗粒形状
长方形正方形
长方形正方形
圆柱形
球形药片形
球形药片形
圆柱形
耗能
高
低
低
低
高
低
对设备要求
单板切粒机
平板切粒机
切粒机
机头切粒
水下切粒机头
机头切粒
2.2总工艺流程
综上所述,本设计选用双阶挤出造粒法。
流程如图2.2:
助剂→计量→输送输送←计量←研磨←颜料
↓↓
聚氯乙烯树脂→过筛→计量→输送→混合→挤出造粒→切粒
↑↓
助剂→过筛→计量→输送包装
↓
PVC色母粒
图2.2总工艺流程图
树脂和粉末助剂经筛选干燥,颜料经过研磨后分别计量后加入到高速混合机混合,混合完毕通入到双螺杆挤出机挤出,到机头造粒,随后包装,成为产品。
所需要的主要设备是三辊研磨机、高速混合器、双阶挤出机、造粒机头、冷却装置等辅助设备。
3生产工艺
3.1配方
3.1.1红、黄、蓝色母料配方
表3-1PVC室内软绝缘电线红色色母料配方
物料名称
配比(质量分)
物料名称
配比(质量分)
PVC树脂SG2型
100
颜料红221
25
DOP
20
BaSt
1
氯化石蜡
18
PbSt
0.2
M-50
18
CaCO3
4
液体Ba-Cd-Zn稳定剂
6
煅烧陶土
6
表3-2PVC室内软绝缘电线黄色色母料配方
物料名称
配比(质量分)
物料名称
配比(质量分)
PVC树脂SG2型
100
颜料黄93
35
DOP
20
BaSt
1
氯化石蜡
18
PbSt
0.2
M-50
18
CaCO3
4
液体Ba-Cd-Zn稳定剂
6
煅烧陶土
6
表3-3PVC室内软绝缘电线蓝色色母料配方
物料名称
配比(质量分)
物料名称
配比(质量分)
PVC树脂SG2型
100
颜料蓝15:
1
30
DOP
20
BaSt
1
氯化石蜡
18
PbSt
0.2
M-50
18
CaCO3
4
液体Ba-Cd-Zn稳定剂
6
煅烧陶土
6
3.1.2树脂选择[5]
本产品是用于室内的起绝缘标识作用的软电线,所以根据国家标准(GB5761-93)选用SG2型PVC树脂。
(规格一级A型,用于电绝缘材料。
)
性质:
强极性聚合物、分子间作用力大
软化温度和熔融温度较高,熔融温度160~210℃
特点:
受热后不稳定
不添加稳定剂易在120℃发生分解氯化氢
用量:
100份(质量份)
毒性:
长时间或反复接触粉尘能引起肺、皮肤、肝脏和血液的损伤,空气中氯化氢最大允许浓度为百万分之5到10。
3.1.3助剂选择
为了达到环保的目的,选用的配合剂和添加剂尽量使用无毒无害的配合剂和添加剂。
(1)增塑剂
增塑剂是能降低树脂的熔融温度和熔融粘度,并使塑料制品在常温下具有柔软性的物质。
随着增塑剂用量的增加,树脂的成型温度降低,流动性能增加,易于成行,但制品的拉伸强度,耐热性、电绝缘性能下降。
增塑剂的用量取决于制品的性能要求。
配方中所用的增塑剂有:
a邻苯二甲酸二辛酯(DOP),简称二辛酯。
[6]
性质:
油状透明液体,分子量391,密度0.978g/cm3,沸点230℃,粘度25厘泊。
特点:
相容性好,挥发性和吸水性小,电绝缘性好,毒性低微。
具有良好的防潮性和光稳定性,可以使薄膜有良好的使用性能
耐寒性差
用量:
20份左右(质量份)
毒性:
本品能刺激眼和上呼吸道粘膜;口服后能引起恶心、呕吐、腹泻。
侵入途径为吸入,摄入,与眼和皮肤接触。
[7]
b氯化石蜡(含氯量65%)阻燃剂。
[6]
性质:
琥珀色粘稠液体,密度1.41~1.45g/cm3,粘度200~400泊,软化点95~105℃,适用于聚氯乙烯塑料,是阻燃性增塑剂。
特点:
具有良好的电绝缘性、和阻燃性,低价格,应用普遍。
用量:
18份(质量份)
毒性:
工业氯化石蜡不燃、无毒、无臭、和无腐蚀性。
含氯40%的氯化石蜡,大鼠经口26.1g/Kg。
大鼠皮下注射,6~15个月后,33只动物18只生成肉瘤,对动物局部作用不明显,未见职业中毒报道。
[7]
cM-50石油酯型增塑剂[6]
性质:
浅黄色透明油状液体,分子量390,密度1.03~1.07g/cm3,沸点211~279℃,不溶于水。
特点:
既可以作为增塑剂又可以作为稳定剂。
但用量不能太大,否则有渗出现象。
用量:
18份(质量份)
毒性:
一般无毒。
(2)稳定剂
聚氯乙烯树脂再加热到130℃时,会产生分解现象,放出氯化氢气体。
放出的氯化氢会促使聚氯乙烯树脂继续分解,降低了树脂的粘度和强度,使树脂无法软化,分解后的聚氯乙烯树脂表面特征为由本色变为深棕色。
稳定剂的加入,使树脂加热时候析出的氯化氢固定起来,使其不再继续分解树脂。
配方中使用的稳定剂为:
液体Ba-Cd-Zn稳定剂。
性质:
液体Ba-Cd-Zn稳定剂一种较为理想的新型PVC液体稳定剂,既有防止聚合物在热加工过程中的降解性能,又可保证制品的耐候性。
特点:
使用方便,本品无须轧浆,可直接混于树脂中进行加工;
污染少,免用了粉状的硬脂酸类钡镉锌,减少粉尘污染;
制品抗大气老化性好,制品经两年大气老化,未见明显斑点,断裂伸长率仍在200%上,制品透明度高;
具有润滑性,在加工过程中,润滑剂可适量减少。
用量:
6份(质量份)
毒性:
其中镉成分为低毒,经过处理合成液体Ba-Cd-Zn稳定剂后基本无毒。
(3)颜料
聚氯乙烯色母料常用的着色剂是颜料。
着色剂不仅可以美化塑料管材的外观,而且兼有抗氧、耐热耐光和稳定剂作用。
着色剂需具有良好的耐热性;容易均匀分散在PVC树脂中,不影响树脂的性质;有较好的气候适应性;粒度细,具有较高的着色力;不具有迁移