神华煤直接液化建设项目可行性研究报告可编辑.docx
《神华煤直接液化建设项目可行性研究报告可编辑.docx》由会员分享,可在线阅读,更多相关《神华煤直接液化建设项目可行性研究报告可编辑.docx(16页珍藏版)》请在冰豆网上搜索。
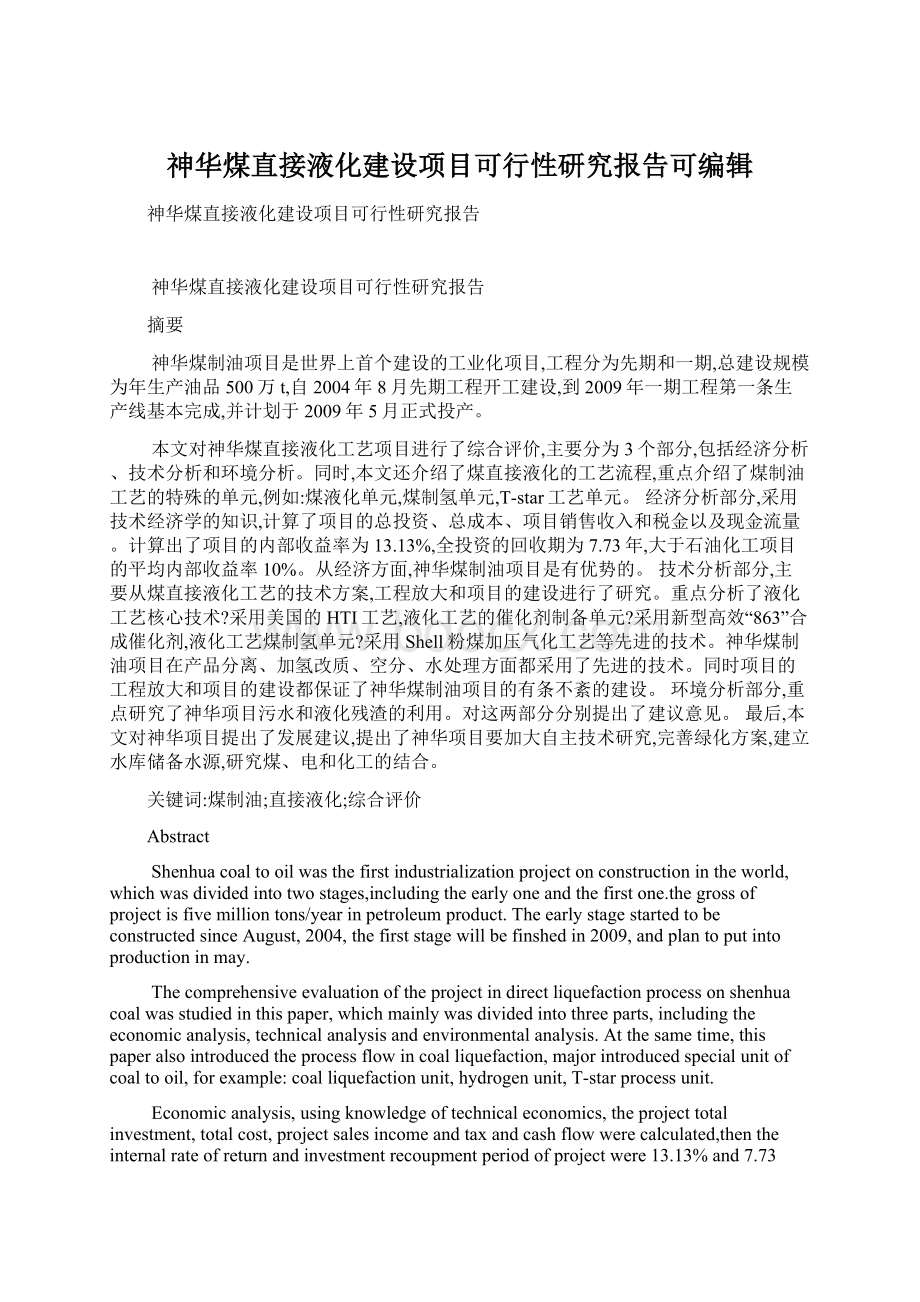
神华煤直接液化建设项目可行性研究报告可编辑
神华煤直接液化建设项目可行性研究报告
神华煤直接液化建设项目可行性研究报告
摘要
神华煤制油项目是世界上首个建设的工业化项目,工程分为先期和一期,总建设规模为年生产油品500万t,自2004年8月先期工程开工建设,到2009年一期工程第一条生产线基本完成,并计划于2009年5月正式投产。
本文对神华煤直接液化工艺项目进行了综合评价,主要分为3个部分,包括经济分析、技术分析和环境分析。
同时,本文还介绍了煤直接液化的工艺流程,重点介绍了煤制油工艺的特殊的单元,例如:
煤液化单元,煤制氢单元,T-star工艺单元。
经济分析部分,采用技术经济学的知识,计算了项目的总投资、总成本、项目销售收入和税金以及现金流量。
计算出了项目的内部收益率为13.13%,全投资的回收期为7.73年,大于石油化工项目的平均内部收益率10%。
从经济方面,神华煤制油项目是有优势的。
技术分析部分,主要从煤直接液化工艺的技术方案,工程放大和项目的建设进行了研究。
重点分析了液化工艺核心技术?
采用美国的HTI工艺,液化工艺的催化剂制备单元?
采用新型高效“863”合成催化剂,液化工艺煤制氢单元?
采用Shell粉煤加压气化工艺等先进的技术。
神华煤制油项目在产品分离、加氢改质、空分、水处理方面都采用了先进的技术。
同时项目的工程放大和项目的建设都保证了神华煤制油项目的有条不紊的建设。
环境分析部分,重点研究了神华项目污水和液化残渣的利用。
对这两部分分别提出了建议意见。
最后,本文对神华项目提出了发展建议,提出了神华项目要加大自主技术研究,完善绿化方案,建立水库储备水源,研究煤、电和化工的结合。
关键词:
煤制油;直接液化;综合评价
Abstract
Shenhuacoaltooilwasthefirstindustrializationprojectonconstructionintheworld,whichwasdividedintotwostages,includingtheearlyoneandthefirstone.thegrossofprojectisfivemilliontons/yearinpetroleumproduct.TheearlystagestartedtobeconstructedsinceAugust,2004,thefirststagewillbefinshedin2009,andplantoputintoproductioninmay.
Thecomprehensiveevaluationoftheprojectindirectliquefactionprocessonshenhuacoalwasstudiedinthispaper,whichmainlywasdividedintothreeparts,includingtheeconomicanalysis,technicalanalysisandenvironmentalanalysis.Atthesametime,thispaperalsointroducedtheprocessflowincoalliquefaction,majorintroducedspecialunitofcoaltooil,forexample:
coalliquefactionunit,hydrogenunit,T-starprocessunit.
Economicanalysis,usingknowledgeoftechnicaleconomics,theprojecttotalinvestment,totalcost,projectsalesincomeandtaxandcashflowwerecalculated,thentheinternalrateofreturnandinvestmentrecoupmentperiodofprojectwere13.13%and7.73yearsrespectively.Theinternalrateofreturnwasmorethantheoneforpetrochemicalindustrywhichwas10%.Fromtheeconomicaspect,theprojectwasprofitable.
Technicalanalysis,mainlystudiedfromcoaldirectliquefactiontechnicalscheme,engineeringenlargementandprojectconstruction.Thecoretechnologyliquefactionprocess-HTIprocessemployingtheAmericatechnology,catalystpreparationprocess-usingnewefficient"863"synthesiscatalyst,coalliquefactionprocessforhydrogenproductionunitbyaddingpressurizedgasification-employingShelladvancedpressurizedgasificationtechnologywereemphaticallyanalyzed.Shenhuacoaltooilprojectinproductseparationunit,hydrogenationmodificationuint,airseparationunitandwatertreatmentwereadoptedadvancedtechnology.Meanwhiletheengineeringandconstructionoftheprojectalsoguaranteedthesystemofshenhuacoaltooilonconstructionorderly.
Environmentalanalysis,mainlystudiedsewageandliquefactionresiduesintheproject.TheSuggestionswereputforwardforthisproject.
Finally,thispapergavetheadvicesforshenhuaprogram,consistingofstrengtheningtechnologystudy,establishingreservoir,completinggreenprogramandstudyingelectricity,water,chemicalcombination.
KeyWords:
coaltooil;directliquefaction;comprehensiveevaluation
摘要I
AbstractII
目录IV
第1章前言1
第2章文献综述3
2.1煤直接液化技术概论3
2.1.1煤直接液化的基本原理3
2.1.2煤直接液化工艺介绍3
2.1.3煤直接液化技术的发展5
2.1.4煤炭直接液化典型工艺6
2.2国外煤液化项目发展情况9
2.2.1美国、澳大利亚、印度、新西兰、和菲律宾的情况9
2.3神华项目简介12
2.3.1项目背景介绍12
2.3.2神华煤直接项目介绍13
2.3.3项目进展14
2.3.4神华集团发展煤直接液化的优势16
2.4小结17
第3章神华煤直接液化工艺流程18
3.1总加工流程18
3.1.1先期总加工流程简介18
3.1.2一期总加工流程简介20
3.2煤直接液化工艺特点22
3.2.1采用悬浮床反应器,处理能力大,效率高22
3.2.2催化剂制备单元24
3.2.2采用T-star工艺对液化粗油进行精制24
3.2.3加氢改质单元25
3.2.4重整抽提单元26
3.2.5异构化单元26
3.2.6煤制氢单元27
3.2.7空分装置28
3.2.8自备电站28
3.2.9水处理装置29
3.3小结29
第4章煤直接液化工艺经济分析30
4.1投资估算与资金筹措30
4.1.1建设投资与流动资金估算30
4.1.2资金筹措及用使用计划33
4.1.3总投资34
4.2总成本费用估算34
4.2.1炼油总成本的构成34
4.2.2生产成本35
4.2.3管理费用38
4.2.4财务费用38
4.2.5销售费用费用38
4.2.6合计39
4.3销售收入与税金计算39
4.3.1销售收入39
4.3.2流转税及附加计算40
4.4现金流量计算42
4.4.1计算依据42
4.4.2相关指标计算及其结果42
4.5其它指标计算43
4.6各种经济指标汇总44
4.6小结45
第5章煤直接液化技术研究46
5.1神华采用的技术方案46
5.1.1最核心工艺的选择47
5.1.2煤直接用煤的洗选49
5.1.3煤直接液化反应器的制造50
5.1.4煤直接液化催化剂51
5.1.5煤直接液化制氢单元52
5.1.6煤直接液化空分装置52
5.1.7煤直接液化自备电站52
5.1.7煤直接液化控制系统53
5.1.8煤直接液化固液分离系统53
5.1.9煤直接液化固液供氢溶剂53
5.1.10煤直接液化T-star工艺53
5.2神华项目工程放大研究54
5.3神华项目建设研究54
5.4小结55
第6章煤直接液化环境分析56
6.1神华煤直接液化污水回用56
6.1.1神东矿区污水回用分析56
6.1.2神华项目供水、污水回用方案57
6.1.3分析结论58
6.2煤直接液化残渣利用58
6.2.1干馏焦化59
6.2.2燃烧发电59
6.2.3气化60
6.2.4分析结果60
第7章神华煤直接液化项目发展建议61
7.1项目的发展前景61
7.1.1国家政策61
7.1.2我国的能源结构61
7.1.3神华集团的实力62
7.2项目的发展建议62
7.2.1优化技术方案,掌握核心技术62
7.2.2建立完善的绿化方案63
7.2.3建立水库储备水量63
7.2.4研究项目煤、电和化工的结合63
第8章结论与建议65
参考文献67
附图72
附表73
第1章前言
能源和环境是当今我国面临的两大严峻问题,如何在保护环境的条件下,合理高效的使用能源是大家共同关心的话题。
我国总的能源特征是“富煤、贫油、少气”,煤炭在我国石化能源总储量中居于首位,高达90%,而石油和天然气储量总共不到10%。
目前,在我国总的能源消费结构中[1],煤炭的消耗约占72.9%、油占22.5%、其他能源总共只占4.6%。
而且,在未来相当长的时间内[2],在一次能源消费结构中煤炭仍将居于主导地位。
开发、高效和环保的利用煤炭资源就显得格外重要。
我国传统的煤炭资源主要用于火电厂发电和水煤气制氨,少量的用于民用。
造成的问题一是环境污染大,发电产生的NOx和SOx是我国大气主要的污染物,另外还有大量的烟尘。
据2000年的数据统计表明[3],我国烟尘排放量为1719万吨,SOx排放量为2360万吨,NOx排放量为800万吨。
其中由燃煤产生的固体粉尘、SOx和NOx排放量分别占我国总排放量的77%、90%和70%,二是能源的使用效率不高,经研究,我国只有无烟煤很适合用来发电,其他的长焰煤、烟煤等较年轻的煤用来燃烧发电的效果并不好。
目前,我国煤炭的平均利用效率为30%,比世界平均水平低10%,比发达国家低25~28%;与国际先进水平相比,工业锅炉低15~20%,火电厂平均煤耗高约25%,城市居民生活燃煤热效率仅25~45%。
所以未来如何减少使用煤炭的污染和高效的使用煤炭资源就尤为重要了。
煤炭液化技术就是针对使用煤炭对环境造成污染所提出的技术对策,是最大限度利用煤的能源,同时将造成的污染降到最小限度的技术方案。
从概念上说,煤直接液化是煤在适当的温度和压力条件下,直接催化加氢裂化,使其降解和加氢转化为液体油品的工艺过程,煤直接液化也称加氢液化。
它将经济效益、社会效益与环保效益结合为一体,开创了煤炭开发利用的新局面,使煤炭成为高效、洁净、可靠的能源,可以满足国民经济的发展和环境保护的需要。
我国的神华集团就是世界上首个工业化煤炭直接液化项目的企业,项目总建设规模为年产油品500万t,分二期建设,其中,一期工程用煤970万t,建设规模为年产油品320万t汽油50万t,柴油215万t,液化气31万t,苯、混合二甲苯等24万t,由三条生产线组成,包括煤液化、煤制氢、溶剂加氢、加氢改质、催化剂制备等14套主要生产装置。
工程采取分步实施的方案,先建设一条生产线,装置运转平稳后,再建设其他生产线。
2004年8月一期工程开工建设,2007年7月建成第一条生产线,2010年左右建成后两条生产线。
项目做了详细的的研究,有关经济,技术和环境上的问题都做了充分的考虑,同时项目也得到了国家的大力支持,国家发改委在2004年印发了《关于2004~2005年度国家工程研究中心重点建设领域的通知》,将包括煤化工在内的一批产业列入国家工程研究中心重点建设领域。
本文对神华煤直接液化项目上做了详细的研究,包括工艺流程,经济收益和技术、环境可行性。
提出了对于神华项目的发展的前景和建议。
第2章文献综述
2.1煤直接液化技术概论
2.1.1煤直接液化的基本原理
煤炭直接液化[4]是指把固体状态的煤炭在高压和一定温度下直接与氢气发生加氢反应,使煤炭转化为液体油品的工艺技术。
在直接液化工艺中,煤炭大分子结构的分解是通过加热来实现的,桥键的断裂产生了以结构单元为基础的自由基,自由基非常不稳定,在高压氢气环境和有溶剂分子分隔的条件下,它被加氢生成稳定的低分子产物,在没有高压氢气环境和没有溶剂分子分隔的条件下,自由基又会相互结合而生成较大的分子。
煤炭经过加氢液化后剩余的无机矿物质和少量未反应煤还是固体状态,可采用各种不同的固液分离方法把固体从液化油中分离出去,常用的方法有减压蒸馏、加压过滤、离心沉降和溶剂萃取等固液分离方法。
煤炭经过加氢液化产生的液化油含有较多的芳香烃,并含有较多的氧、氮和硫等杂原子。
必须再经过提质加工才能生产合格的汽油和柴油产品。
不同的工艺路线,得到的直接液化产品也相差甚远,同时液化产品也与煤种和反应条件例如压力、温度和催化剂有关。
2.1.2煤直接液化工艺介绍
直接液化典型的工艺过程主要包括煤的破碎与干燥、煤浆制备、加氢液化、固液分离、气体净化、液体产品分馏和精制,以及液化残渣气化制取氢气等部分。
氢气制备是加氢液化的重要环节,大规模制氢通常采用煤气化及天然气转化。
液化过程中[5],将煤、催化剂和循环油制成的煤浆,与制得的氢气混合送入反应器。
在液化反应器内,煤首先发生热解反应,生成自由基“碎片”,不稳定的自由基“碎片”再与氢在催化剂存在条件下结合,形成分子量比煤低得多的初级加氢产物。
出反应器的产物构成十分复杂,包括气、液、固三相。
气相的主要成分是氢气,分离后循环返回反应器重新参加反应;固相为未反应的煤、矿物质及催化剂;液相则为轻油(粗汽油)、中油等馏份油及重油。
液相馏份油经提质加工(如加氢精制、加氢裂化和重整)得到合格的汽油、柴油和航空煤油等产品。
重质的液固淤浆经进一步分离得到重油和残渣,重油作为循环溶剂配煤浆用。
煤直接液化粗油中石脑油[6]馏分约占15~30%,且芳烃含量较高,加氢后的石脑油馏分经过较缓和的重整即可得到高辛烷值汽油和丰富的芳烃原料,汽油产品的辛烷值、芳烃含量等主要指标均符合相关标准(GB17930-1999),且硫含量大大低于标准值(≤0.08%),是合格的优质洁净燃料。
中间油约占全部直接液化油的50~60%,芳烃含量高达70%以上,经深度加氢后可获得合格柴油。
重油馏分一般占液化粗油的10~20%,有的工艺该馏分很少,由于杂原子、沥青烯含量较高,加工较困难,可以作为燃料油使用。
煤液化中油和重油混合经加氢裂化可以制取汽油,并在加氢裂化前进行深度加氢以除去其中的杂原子及金属盐。
煤在一定温度、压力下的加氢液化过程基本分为下面三大步骤[7,8]:
(1)当温度升至300℃以上时,煤受热分解,即煤的大分子结构中较弱的桥键开始断裂,打碎了煤的分子结构,从而产生大量的以结构单元为基体的自由基碎片,自由基的相对分子质量在数百范围。
(2)在具有供氢能力的溶剂环境和较高氢气压力的条件下、自由基被加氢得到稳定,成为沥青烯及液化油分子。
能与自由基结合的氢并非是分子氢(H2),而应是氢自由基,即氢原子,或者是活化氢分子,氢原子或活化氢分子的来源有:
①煤分子中碳氢键断裂产生的氢自由基;②供氢溶剂碳氢键断裂产生的氢自由基;③氢气中的氢分子被催化剂活化;④化学反应放出的氢。
当外界提供的活性氢不足时,自由基碎片可发生缩聚反应和高温下的脱氢反应,最后生成固体半焦或焦炭。
(3)沥青烯及液化油分子被继续加氢裂化生成更小的分子。
2.1.3煤直接液化技术的发展
煤炭直接液化技术已经走过了近一个世纪的发展历程。
每一步进展都与世界的政治、经济科技及能源格局有着密切的关系。
归结起来可以看作三个阶段,每一个阶段都开发了当时最先进的工艺技术[9]。
第一代液化技术:
1913年到第二次世界大战结束。
在这段时间里,德国首先开启了煤炭液化的进程。
1913年,德国的柏吉乌斯首先研究了煤的高压加氢,从而为煤的直接液化奠定了基础,并获得世界上第一个煤直接液化专利。
1927年,德国在莱那Leuna建立了世界上第一个煤直接液化厂,规模10万t/a。
在1936~1943年,德国又有11套直接液化装置建成投产,到1944年,生产能力达到423万t/a,为发动第二次世界大战的德国提供了大约70%的汽车和50%装甲车用油。
当时的液化反应条件较为苛刻,反应温度470℃,反应压力70MPa。
第二代液化技术:
二次世界大战后,由于中东地区大量廉价石油的开发,使煤直接液化失去了竞争力和继续存在的必要。
1973年后,西方世界发生了一场能源危机,煤转化技术研究又开始活跃起来。
德国、美国、日本等主要工业发达国家,做了大量的研究工作。
大部分的研究工作重点放在如何降低反应条件,即降低反应压力从而达到降低煤液化油的生产成本的目的。
主要的成果有:
美国的氢-煤法、溶剂精炼煤法、供氢溶剂法、日本的NEDOL法及西德开发的德国新工艺。
这些技术存在的普遍缺点是:
1)因反应选择性欠佳,气态烃多,耗氢高,故成本高;2)固液分离技术虽有所改进,但尚未根本解决;3)催化剂不理想,铁催化剂活性不够好,钻-镍催化剂成本高。
第三代液化技术[10]:
为进一步改进和完善煤直接液化技术,世界几大工业国美国、德国和日本正在继续研究开发第三代煤直接液化新工艺。
具有代表性的目前世界上最先进的几种煤直接液化工艺是:
1)美国碳氢化合物研究公司两段催化液化工艺;2)美国的煤油共炼工艺COP。
这些新的液化工艺具有反应条件缓和,油收率高和油价相对低廉的特点。
2.1.4煤炭直接液化典型工艺
自从德国发明了煤炭直接液化技术之后,美国、日本、英国、俄国也都独自研发出了拥有自主知识产权的液化技术。
以下简单介绍几种[11]型的煤炭直接液化工艺。
1)德国IGOR工艺[12]
该煤炭直接液化工艺以炼铝赤泥为催化剂,催化剂加入量为4%,不进行催化剂回收。
该工艺的主要特点是:
反应条件较苛刻,反应温度470℃,反应压力30MPa;催化剂使用炼铝工业的废渣赤泥;液化反应和液化油加氢精制在一个高压系统内进行,可一次得到杂原子含量极低的液化精制油。
该液化油经过蒸馏就可以得到低辛烷值汽油,汽油馏分再经重整即可得到高辛烷值汽油;配煤浆用的循环溶剂是加氢油,供氢性能好,煤液化转化率高。
其工艺流程框图见图2-1。
图2-1德国IGOR流程
与老工艺相比,新工艺主要有以下改进:
①固液分离不用离心过滤,而用闪蒸塔,生产能力大、效率高。
②循环油不但不含固体,还基本上排除了沥青烯。
③闪蒸塔底流出的淤浆有流动性,可以用泵输送到德士古气化炉,制氢或燃烧。
④煤加氢和油精制一体化,油收率高,质量提高。
2)日本NEDOL工艺
该煤炭直接液化工艺是日本解决能源问题的阳光计划的核心项目之一。
它以天然黄铁矿为催化剂,催化剂加入量为4%,也不进行催化剂回收。
反应压力为19MPa,反应温度为460℃。
其主要特点是循环溶剂全部在一个单独的固定床反应器中,用高活性催化剂预先加氢,使之变为供氢溶剂。
液化粗油经过冷却后再进行提质加工。
液化残渣连同其中所含的重质油即可进一步进行油品回收,也可直接用作气化制氢的原料。
现己完成原料煤用量分别为0.01万t/a、0.1万t/a、1万t/a以及150万t/d规模的试验研究[13]。
它集聚了“直接加氢法”、“溶剂萃取法”和“溶剂分解法”这三种烟煤液化法的优点,适用于从次烟煤至煤化度低的烟煤等广泛煤种。
目前日本此项煤液化技术已达到世界先进水平。
其工艺流程框图见图2-2。
图2-2日本NEDOL工艺流程
NEDOL工艺特点:
①反应压力较低,为17~19MPa,反应温度455~465℃;②催化剂采用合成硫化铁或天然硫铁矿;③固液分离采用减压蒸馏的方法;④配煤浆用的循环溶剂单独加氢,以提高溶剂的供氢能力;⑤液化油含有较多的杂原子,必须加氢提质才能获得合格产品。
3)美国HTI工艺
该煤炭直接液化工艺使用人工合成的高分散催化剂,加入量为0.5wt%,不进行催化剂回收。
反应压力为17MPa,反应温度为450℃。
HTI工艺是在H-Coal工艺基础上发展起来的,主要特点:
①采用近10年来开发的悬浮床反应器和HTI拥有专利的铁基催化剂;②反应条件比较温和,反应温度440~450℃,反应压力17MPa;③固液分离采用临界溶剂萃取的方法,从液化残渣中最大限度回收重质油,从而大幅度提高了液化油收率;④在高温分离器后面串联有在线加氢固定床反应器,对液化油进行加氢精制。
其工艺流程框图见图2-3.
图2-3美国HTI工艺流程
HTI工艺的主要特点是:
反应条件比较缓和,反应温度440~450℃,压力17MPa,采用悬浮床反应器,达到全返混反应模式;催化剂采用HTI专利技术制备的铁系胶状催化剂,催化活性高,用量少;在高温分离器后面串联在线加氢固定床反应器,起到对液化油加氢精制的作用;固液分离器采用临界溶剂萃取法,从液化残渣中最大限度地回收重质油,大幅度提高了液化油收率;液化油含350~450℃馏分,可用作加氢裂化原料,其中少量用作燃料油。
2.2国外煤液化项目发展情况
2.2.1美国、澳大利亚、印度、新西兰、和菲律宾的情况
目前国外仅南非建设有间接液化法煤制油装置。
Sasol公司Secunda煤制油装置将煤转化为汽油、柴油、液化石油气和石化原料,石化原料用于45万t/a乙烯装置。
还有一