幕墙钢构件加工手册.docx
《幕墙钢构件加工手册.docx》由会员分享,可在线阅读,更多相关《幕墙钢构件加工手册.docx(21页珍藏版)》请在冰豆网上搜索。
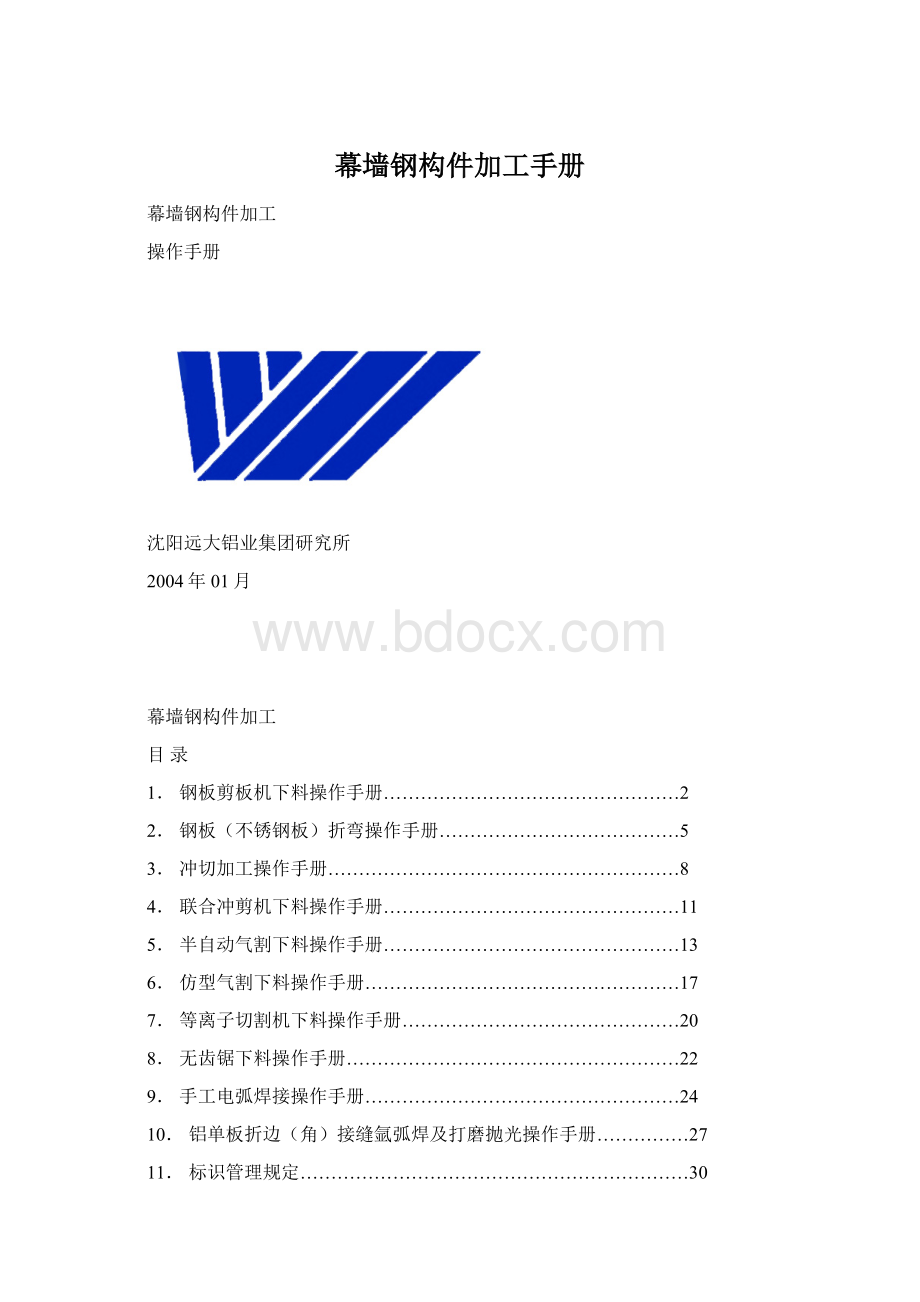
幕墙钢构件加工手册
幕墙钢构件加工
操作手册
沈阳远大铝业集团研究所
2004年01月
幕墙钢构件加工
目录
1.钢板剪板机下料操作手册…………………………………………2
2.钢板(不锈钢板)折弯操作手册…………………………………5
3.冲切加工操作手册…………………………………………………8
4.联合冲剪机下料操作手册…………………………………………11
5.半自动气割下料操作手册…………………………………………13
6.仿型气割下料操作手册……………………………………………17
7.等离子切割机下料操作手册………………………………………20
8.无齿锯下料操作手册………………………………………………22
9.手工电弧焊接操作手册……………………………………………24
10.铝单板折边(角)接缝氩弧焊及打磨抛光操作手册……………27
11.标识管理规定………………………………………………………30
钢板剪板机下料
操作手册
文件编号:
YBGYCZ-28
沈阳远大铝业集团研究所
2004年01月
1.质量标准:
1.1钢板下料加工尺寸允许偏差:
±1.0mm
1.2剪切面外观质量:
平整、无毛刺、飞边。
1.3钢板平面度允许偏差
钢板面积A
平面度允许偏差
合格品
A≤100×100
0.5
100×100<A≤300×300
1.0
300×300<A≤600×600
1.5
A>600×600
2.0
注:
转接件与型材接触部位平面度合格品1.0
1.操作过程
2.1根据工序卡,读懂相应图纸及细目要求,不清楚时,询问工艺员。
2.2按领料单到库房领料。
2.2.1核对所领的钢板规格、厚度,应与细目、工序卡、图纸相符,并检查板面外观质量,发现问题应及时反馈处理。
2.2.2将钢板放到周转车上,运到剪板机前,不锈钢板要避免表面划伤。
2.3用抹布擦净剪床工作台。
2.4根据材料及厚度选择上下刃口间隙,调整刻度δ=0.15h(板厚),见间隙调整表:
间隙调整表:
板厚h(mm)
刻度δ
板厚h(mm)
刻度δ
1
0.15
6
0.90
2
0.30
7
1.05
3
0.45
8
1.20
4
0.60
9
1.35
5
0.75
10
1.50
2.5间隙调整时,将夹紧螺钉旋松,转动手柄调整,到刻度后,将夹紧螺钉拧紧后,进行试切,查看下料是否有明显毛刺,有则适当调小间隙。
必要时可更换上下刀。
2.6检查导尺与刀刃是否与要求角度一致。
2.7根据下料长度或宽度调整定位块,检查并保证定位块(板)位置。
2.8定位块(板)调整距离不能满足时,可用工作台定位方式。
2.9下料时,注意板料的套裁(亚光不锈钢板注意纹理方向)。
2.10严禁剪切超过设备规定要求的材料。
2.11剪板后弯曲变形要进行校平并符合平面度要求。
2.12剪板后断面毛刺的,要用角磨机处理,达到要求。
2.13首件“三检”合格后(不锈钢板逐件进行标识和盖章)并在工序卡上盖章后方可批量生产。
2.14生产过程中,操作者检查,发现问题,及时调整。
2.15加工完成后向质检员报终检,检查合格并进行质量评定后,办理移交。
钢板(不锈钢板)折弯
操作手册
文件编号:
YBGYCZ-29
沈阳远大铝业集团研究所
2004年01月
1.
质量标准:
1.1折弯件允许偏差
1.1.1折弯高度允许偏差
表1:
公称尺寸
折弯厚度
≤10
>10
≤20
±0.5
±0.8
20-40
±0.8
±1.0
40-60
±1.0
±1.2
≥60
±1.5
±1.5
注:
1)折盒板时,折边高度偏差取负差。
2)角埋件,转接件的非配合尺寸折边高度尺寸偏差,在此基础上可以放2mm。
1.1.2角度允许偏差
表2:
公差角度
折弯角度
≤10
>10
直角
±30′
-1°
非直角
±1°
-1.5°
1.2钢板折弯最小内弧半径R=δ(板厚)
1.3钢板折弯后的内外角不允许有有折,裂纹,分层等缺陷。
2.操作过程:
2.1根据工序卡,认真看懂相应图纸和细目要求,不清楚时,要及时找工艺员明确要求。
2.2操作前,操作者要检查钢板外观质量和尺寸规格,发现问题,及时反馈进行处理。
2.3根据板料厚茺及折边宽度,选择下模V型槽和上模。
2.4调整下模,使其V型槽和上模准确对中。
2.5用抹布清洁折弯机下模V型槽口内杂物。
2.6根据折弯尺寸调整定位块(板)位置,检查并保证位置准确。
2.7根据折弯长度和板厚选择合适的折弯力(参照折弯机标牌调整)。
2.8折弯时,折弯角度要从大到小调整,不要将角度折成小于图纸规定角。
2.9工作中要注意避免杂物落入下模V型槽内。
2.10折不锈钢板时,可先用余料试折,注意排队伤膜现象,必要时可采取垫布,贴保护胶带等方法。
2.11首件三检合格后,可进行批量生产,加工过程中,检查发现问题及时处理。
2.12加工完成后向质检员报终检,由质检员终检合格,在工序卡上盖检验章,评定质量情况后,操作者办理移交。
冲切加工
操作手册
文件编号:
YBGYCZ-30
沈阳远大铝业集团研究所
2004年01月
1.
质量标准:
表1:
序号
项目
允许偏差
测量工具
1
孔径尺寸
+0.5
卷尺或卡尺
2
孔距尺寸
±1.0
卷尺或卡尺
3
漏料尺寸
±0.5
卷尺或卡尺
4
外观质量
孔壁平整,无变形、飞边、毛刺。
目视
2.操作过程
2.1根据工序卡,看懂相应图纸和细目要求,不清楚时询问工艺员。
2.2操作前,操作者要检查板外观和尺寸规格,发现问题,及时反馈处理。
2.3根据图纸提供模具号,选用模具。
2.4安装模具
a:
将模具放到工作台上,上模柄对准滑块模柄孔。
b:
调整冲床封闭高度使得滑块运动到最低点时,上模柄进入滑块模柄孔内,使上模板上面与滑块下面贴合,则用垫板调整高度然后用螺栓顶死模柄,分别用两块压板压住上、下模,并保证两压板对称位置。
c:
调整滑块使凸模进入凹模2—3mm,然后锁紧滑块调节螺母。
d:
简易模要向下引模,四周用塞尺塞,保证间隙均匀。
加工件超过200件时,需要重新检查调整。
e:
冲切单元竖框时,将托架与模调到一个平面,将型材冲切部位,穿入模具腔内,保持进出自如,没有卡死现象,否则重新调整。
2.5下模面不许有杂物,以免冲切时垫伤及损坏模具。
2.6注意观察冲切件的毛刺,大时找模具外协员进行刃口修磨,或更换。
2.7冲切后,对板面弯曲的工件,应进行校平。
首先将专用校平模具装在压力机上,调整封闭高度,使其小于工件厚度1~2mm即可。
然后将工件放在模具下膜上进行逐件校平,从而达到平面度要求。
2.8冲切时,严禁冲切与模具规定不相符的材料及厚度。
2.9首件三检合格后,在工序卡上盖章后,可以批量生产。
2.10生产过程中,发现问题及时调整。
2.11加工完成后,向质检员报终检,合格并评定后进行移交,把模具存放指定地方。
联合冲剪机下料
操作手册
文件编号:
YBGYCZ-31
沈阳远大铝业集团研究所
2004年01月
1.
质量标准:
1.1下料尺寸允许偏差:
±1.5mm。
1.2断面与型钢纵向垂直偏差:
±1.50
1.3外观质量:
断面无飞边,毛刺。
2.操作过程
2.1根据工序卡,看懂相应图纸和细目要求,不清楚时询问工艺员。
2.2按领料单领料,检查断面规格长度和外观质量,发现问题及时反馈处理。
2.3下料时注意型钢的套裁。
2.4根据下料的长度确定挡块的位置,保证位置准确。
2.5型钢送料加工时,保证纵向垂直于刃口,且平稳放在模具定位装置上。
2.6断口处有飞边毛刺时要用角磨机修整,有变形时及时找设备维修员调整设备。
2.7首件“三检”,合格后批量生产。
2.8加工过程中,进行检查发现问题及时反馈处理。
2.9加工完成后。
向质检员报终检,质检员终检合格后进行质量评定,操作者办理移交。
半自动气割下料
操作手册
文件编号:
YBGYCZ-32
沈阳远大铝业集团研究所
2004年01月
1.
质量标准:
1.1尺寸允许偏差:
±1.5
1.2表面质量:
切割面无飞边毛刺。
2.操作过程:
2.1根据工序卡,读懂相应图纸及细目要求,不清楚时,询问工艺员。
2.2按领料单领料,并核对所领的钢料的规格,厚度和外观质量,发现问题及时反馈处理。
2.3气瓶的存放和使用:
a:
气瓶存放和使用必须距明火10m以外,乙炔瓶和氧气瓶之间距离不小于5m。
b:
乙炔瓶在使用时必须立放,不得放倒。
c:
使用的乙炔压力不得超过0.15Mpa。
d:
乙炔气严禁用尽,必须留有不低于表1的规定的剩余压力,并关紧瓶阀,防止漏气。
表1:
环境温度
(℃)
<0
0-15
15-25
25-35
剩余压力不
低于(Mpa)
0.05
0.1
0.2
0.3
e:
必须严格遵守乙炔瓶、氧化瓶、减压器和橡胶软管的使用和保管安全事项,以免发生火灾和爆炸事故。
2.4气割前应垫平稳被加工钢板,按图纸要求确定切割位置进行画线。
2.5根据切割线位置和切割机导轨与火咀的距离,画出导轨定位线,保证导轨定位线与切割线平行。
导轨线可划在加工板上或与加工板同一平面的板上。
2.6将导轨放在定位线上,将切割机放在导轨上,调整火咀位置,对好切割线。
2.7气割前,割距应作射吸能力检查,查看割距是否正常。
2.8气割规范主要根据切割厚度选择(见表一)。
2.9切割时,对加工板进行预热。
根据板材厚度打开切割氧后,调整火焰和割咀位置使其与切割划线重合进行切割,火焰芯距切割金属表面4—6mm,当切割大于100mm以上钢材时,为防止金属飞溅,堵塞割咀,以使切割过热,割咀到工件的距离,可按公式确定:
h=5+0.5δ(切件厚)
2.10预热工件至红热状态,然后找开切割氧,金属熔化并在氧气中燃烧吹走,此时,再加大切割氧,当工件背后落下火焰时说明工件被切割透,此时以均匀速度向前移动,直至工件切完。
表一:
切割板厚
(mm)
割具
割速度
mm/min
气体压力(mpa)
型号
割嘴号
O2
C2H2
3-12
G01-30
1-2
560-650
0.3-0.4
0.01-0.12
12-30
G01-30
2-3
375-560
0.4-0.5
30-50
G01-100
2
325-375
0.5-0.6
50-100
3
145-250
0.6-0.8
100-150
G01-100
1-2
120-195
0.8-1.0
150-200
2-4
60-120
1.0-1.4
2.11发生回火时,应迅速关闭切割氧,以防止氧气回流进入乙炔管内,如仍发出嘶嘶声,应迅速关闭乙炔,回火排除后,作射吸能力检查,然后重新切割。
2.12切割完成后,用扁铲或角磨机清理飞边毛刺。
2.13首件三检合格后,可批量生产,加工过程中发现问题时调整处理。
2.14加工完成后报终检,合格后进行移交。
仿型气割下料
操作手册
文件编号:
YBGYCZ-33
沈阳远大铝业集团研究所
2004年01月
1.
质量标准;
1.1外形尺寸允许偏差:
±1.0
1.2切割面外观平整无飞边、毛刺。
2.操作过程:
2.1根据工序卡,读懂相应图纸和细目要求,不清楚时询问工艺员。
2.2按领料单到库房领料,核对所领的钢板规格,与细目图纸相符,发现问题及时处理。
2.3气瓶的存放和使用:
a:
气瓶存放和使用必须距明火10m以外,乙炔瓶和氧气瓶之间距离不小于5m。
b:
乙炔瓶在使用时必须立放,不得放倒。
c:
使用的乙炔压力不得超过0.15Mpa。
d:
乙炔气严禁用尽,必须留有不低于表1的规定的剩余压力,并关紧瓶阀,防止漏气。
环境温度
(℃)
<0
0-15
15-25
25-35
剩余压力不
低于(Mpa)
0.05
0.1
0.2
0.3
e:
必须严格遵守乙炔瓶、氧化瓶、减压器和橡胶软管的使用和保管安全事项,以免发生火灾和爆炸事故。
2.4样板由工艺室设计,加工时操作者应按图纸精度加工。
2.5将样板在切割机上固定好后,用螺母拧死,并保证样板与磁轮接触。
2.6切割前将钢板铺平垫稳,将切割机直接放到切割钢板上。
通过旋转主轴的升降螺母,调整钢板距离,小量调节,只需调节割距的位置。
2.7气割前割炬应作射吸能力检查,查看割炬是否正常。
2.8气割规范主要根据切割板厚选择(见表一)
表一:
切割厚度(mm)
火咀
编号
No
切割速度
mm/min
氧气压力
Pa
乙炔压力
Pa
8-20
1
450-550
2.94×105
>2.94×104
20-40
2
350-450
3.92×105
>2.94×104
40-60
3
250-350
3.92×105
>3.92×104
2.9切割时根据板材厚度调整预热火焰,预热工件至红热状态,慢慢打开切割氧,如果预热金属熔化并在氧化中燃烧吹走,此时应开大切割氧,当工件背后落下火焰时,说明工件被切割透,此时以均匀速度向前移动,直至工件割完。
2.10发生回火时应迅速关闭切割氧,以防止氧气回流,进入乙炔管内,如仍有嘶嘶声,应迅速关闭乙炔,回火排除后,作射吸能力检查,然后重新切割。
2.11切割完成后,用扁铲清理溶渣,用角磨机打磨毛刺和棱角,使表面光整。
2.12首件三检合格后,进行批量生产。
2.13加工过程要经常进行检查,发现问题,及时调整,处理。
2.14全部加工完成后报终检,由质检员检查合格进行评定后操作者办理移交。
等离子切割机下料
操作手册
文件编号:
YBGYCZ-34
沈阳远大铝业集团研究所
2004年01月
1.
质量标准:
1.1尺寸允许偏差±1.0mm
1.2切割边缘处打磨后无明显变形或凸凹。
2.操作过程:
2.1根据工序卡,读懂相应图纸、细目要求,不清楚时,询问工艺员。
2.2按领料单到库房领料,核对所领板材的规格厚度应与细目、图纸相符,并检查板面外观质量,发现问题及时反馈处理。
2.3样板由工艺设计,公司加工时,操作者要严格按样板加工精度进行加工。
2.4加工板放平稳后,将样板放在加工板上,打开气泵,根据板厚调整气压,当加工板厚为1-3mm时,压力为0.3-0.4MPa,板厚4-6mm时,压力为0.5-0.6MPa。
2.5打开离子束,割咀紧靠样板边缘进行切割,板材在气流作用下,将加热熔化的部分吹开,切割时注意割咀气流垂直于钢板平面。
2.6切割完成后,用角磨机清理飞边毛刺溶渣。
2.7切割完成后,用角磨机清理飞边毛刺溶渣。
2.8首件“三检”合格后,在工序卡上盖章后可批量生产。
2.9加工过程中要经常进行检查,发现问题及时调整处理。
2.10全部加工完成后报终检,由质检员检查合格并进行评定后办理移交。
无齿锯下料
操作手册
文件编号:
YBGYCZ-35
沈阳远大铝业集团研究所
2004年01月
1.质量标准:
1.1下料尺寸允许偏差:
±1.5mm。
1.2断面与型钢纵向垂直偏差:
±1.50
1.3外观质量:
断面、平整、无飞边毛刺。
2.操作过程:
2.1根据工序卡,看懂相应图纸和细目要求,不清楚时询问工艺员。
2.2按领料单领料,检查型钢长度规格和外观质量,发现问题及时处理。
2.3下料前要检查锯片是否破损、紧固、空转是否平稳。
2.4下料时注意型钢的套裁,保证型钢纵向垂直于锯片。
2.5根据下料尺寸、数量可采用划线或挡块形式进行切割。
尺寸较大、数量较少,可采用划线方式、尺寸较小,数量较多,可采用挡块形式,按下料尺寸确定挡块或划线的位置。
2.6加工时夹紧工件进行切割。
2.7切割时,要均匀加力,按画线或挡块位置加工,避免因用力过大,造成锯片损坏,甚至烧坏电机发生意外。
切割中,不允许在切割片端面垂直地加工磨削,或站位正对切割件,要注意周围其它人员安全,防止意外。
2.8加工后,用角磨机清理飞边毛刺,将棱边倒钝,保证表面质量,首件完成进行“三检”,合格后批量生产。
2.9加工完成后,操作者报终检,合格后进行移交。
手工电弧焊接
操作手册
文件编号:
YBGYCZ-36
沈阳远大铝业集团研究所
2004年01月
1.焊缝质量等级要求:
1.1焊缝平直饱满,无内部及外观缺陷,符合图纸要求。
2.操作方法:
2.1焊前准备。
2.1.1焊前焊工应了解产品图纸及技术要求,了解所焊件和焊条特点。
2.1.2对工件表面质量较差(质检员确认)的应用角磨机清理待焊处两侧20mm油污,铁锈氧化皮等。
2.1.3选择焊条
Q235、10、20钢,一般结构选焊条结422(国际标准E4303)
较高的结构选焊条结426(国际标准E4316)
不锈钢焊条选择奥132
灰口铸铁选择E208
Q235与不锈钢焊接时选择焊条奥307
中碳钢焊接选焊条结506(国际标E5016)
2.1.4焊件厚度与焊条直径的选择
焊件厚度mm
≤2
3-6
8-12
焊条直径mm
2
3.2
4
2.1.5根据焊条直径选择电流
焊条直径mm
1.6-2.5
3.2
4
5
5.8
焊接电流(A)
50-90
100-130
160-200
200-250
250-300
2.2焊接构件时,应尽可能避免焊接应力及变形,可先点焊定位,对称焊,分段焊等。
变形大的需校正。
2.3对变形要求很高的工件要有焊接夹具。
2.4焊接完毕,应清除焊渣,进行外观检查,若发现缺陷,如裂纹、气孔、夹渣、咬边等应补焊。
2.5清除焊渣的工具应为工具钢制成,淬火硬度HRC52-56,形状为一头扁刃,一头尖刃,中间焊一手柄,并经常刃磨保持锋利。
2.6首件“三检”合格,在工序卡上盖章后,方可批量生产。
2.7加工过程中,进行检查发现问题进行调整处理。
2.8全部加工完成后,操作者报终检,质检员检查合格,进行产品评定,在工序卡上盖章后,操作者进行移交。
铝单板折边(角)接缝氩
弧焊及打磨抛光
操作手册
文件编号:
YBGYCZ-37
沈阳远大铝业集团研究所
2004年01月
1.质量标准:
1.1沿焊缝全长连续、均匀、饱满;焊缝形状如简图
(1)。
1.2焊缝无裂纹、夹渣、飞溅气孔、虚焊等缺陷。
1.3不允许的焊缝形状
1.4焊后盒板长、宽及对角线允许偏差:
项目
允许偏差
检测工具
优等品
合格品
板块长宽尺寸
±1.0
±1.5
钢卷尺
板块对角线差
≤2000
≤2.0
≤2.5
卷尺
>2000
≤2.5
≤3.0
1.5焊缝打磨光滑,两边圆滑过度,无棱角。
2.操作过程:
2.1按工序卡读懂图和细目,不懂时问工艺员。
2.2核准上序板材规格、数量、代号、长宽、厚尺寸及角部缝隙,有质量问题报告质检员。
2.3折边及角部缝隙不规整时,用胶锤轻击修正。
2.4钨极和电流对照表:
钨极直
径mm
尖端角
度(O)
电流(A)
恒定电流
脉冲电流
1.0
12
3-15
3-25
1.0
20
5-30
5-60
1.6
25
10-50
10-100
2.0
35
20-90
20-160
2.4
45
20-160
2.5焊接:
2.5.1用砂纸或锉刀去除焊口上的毛刺、飞边。
2.5.2距焊缝10mm(当缝长≤20mm时,从中点)开始引弧。
2.5.3焊接过程中根据槽口大小,确定焊枪和送丝速度。
手势沿焊缝线方向,平稳移动,保证钨极移动轨迹平行焊缝。
2.5.4
氩弧焊接:
2.6首件焊后,用角磨机打磨焊缝。
角磨机磨片平行于铝板折边,手平稳,均匀用力,铝板三个平面交汇点,要打磨成球面,与平边圆滑过度,不允许出现折线及棱角。
2.7首件”三检”,首件”三检”合格后,可批量生产,抽检,并逐件帖标识。
2.8工序完成后,操作者向质检员报终检。
终检合格后,移交下序。
标识管理规定
文件编号:
YBGYCZ-09
沈阳远大铝业集团研究所
2004年01月
一、首件标识(见标识1)
1、每道工序操作者首件自检合格后,填写首件标识
(1),并在首件标识“操作者”栏盖章后交互检,互检合格后,互检人员在“互检”栏上盖章,操作者将标识贴在产品首件上并交专检,质检员检验合格后,在“检验”栏盖章。
2、组板。
二、过程标识
(2)、(3)
操作过程中,第一道工序除首件外每件产品加工后都要填写标识
(2)并盖章后,逐件贴在产品实物上,第一道工序以后的各道工序每件产品加工后都要逐件贴标识(3)。
标识
(2)对板、玻璃、组框、填写代号,对型材加工填写规格。
三、抽检标识(4)
加工过程中,质检员要按10%比例进行抽检,抽检合格后,贴抽检标识(4)并盖章。
四、标识粘贴位置要求
1、板加工:
标识粘贴在左上角300×300mm区域内。
2、板组装:
标识粘贴在板折边外侧,距上端头300mm内,标识外沿距板饰面≥4mm。
3、铝型材加工:
1)竖框标识粘贴在距端头300mm范围。
2)横框标识粘贴在前端面距端头300mm范围内。
3)副框标识粘贴在压板侧外端面,距端头300mm范围内。
4)翻窗扇框标识粘贴在安装支撑一侧。
距端头300mm范围内。
5)翻窗边框标识粘贴在边框外侧(与横竖框接触面)距端头300mm范围内。
6)上述未涉及到的型材标识应粘贴在非装饰面和非粘贴面(结构胶、耐候胶、3m胶带粘结面)距端头300mm范围内。
五、标识种类:
1、标识
(1)
工序
工程名称
产品代号
序卡号
操作者
检验
规格
互检
图号
2、标识
(2)
代号/规格
操作者
检验
3、标识(3)4.标识(4)
操作者