涟钢转炉主副枪自动炼钢系统模型详细设计说明书.docx
《涟钢转炉主副枪自动炼钢系统模型详细设计说明书.docx》由会员分享,可在线阅读,更多相关《涟钢转炉主副枪自动炼钢系统模型详细设计说明书.docx(89页珍藏版)》请在冰豆网上搜索。
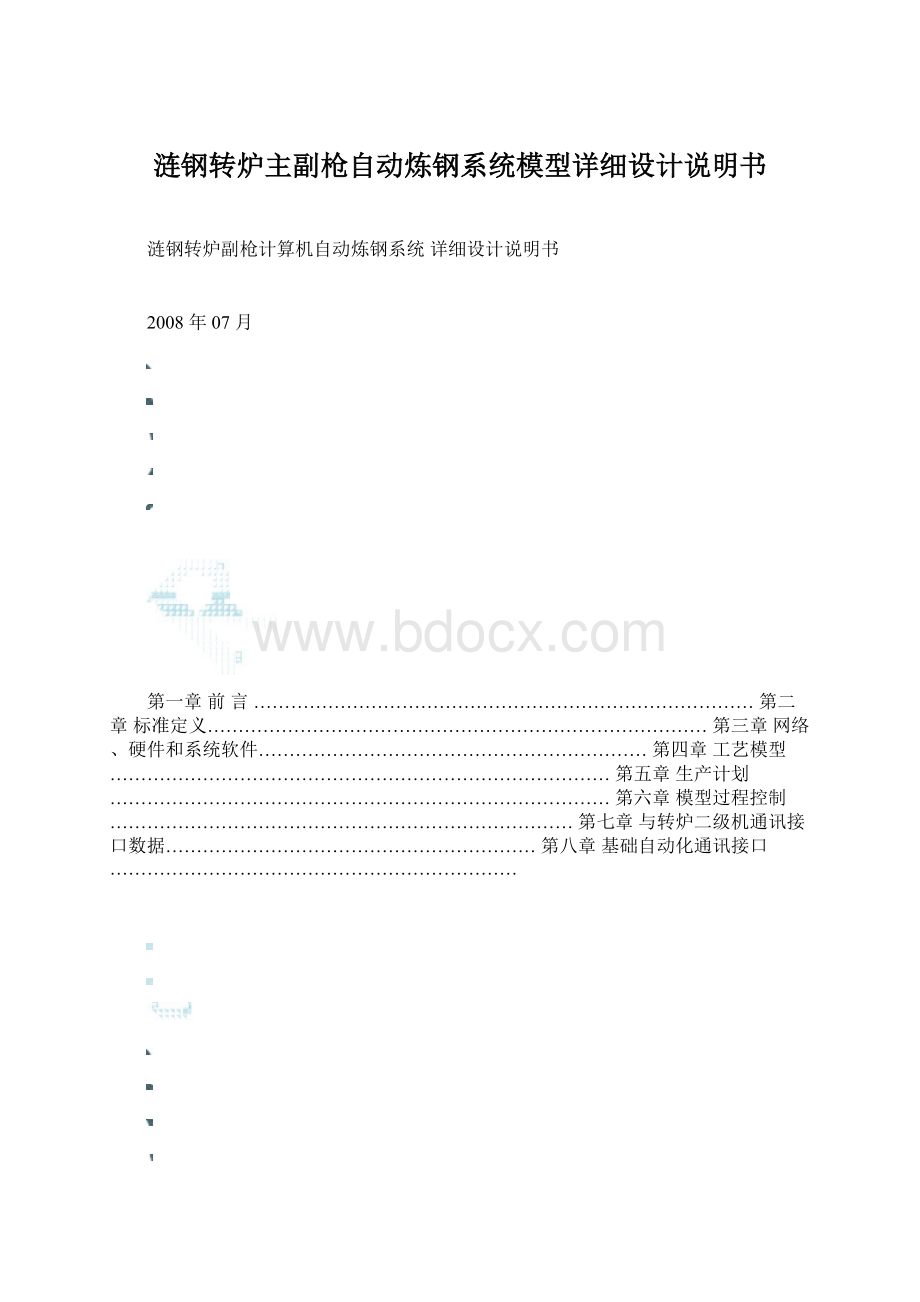
涟钢转炉主副枪自动炼钢系统模型详细设计说明书
涟钢转炉副枪计算机自动炼钢系统详细设计说明书
2008年07月
第一章前言………………………………………………………………………第二章标准定义………………………………………………………………………第三章网络、硬件和系统软件………………………………………………………第四章工艺模型………………………………………………………………………第五章生产计划………………………………………………………………………第六章模型过程控制…………………………………………………………………第七章与转炉二级机通讯接口数据……………………………………………………第八章基础自动化通讯接口…………………………………………………………
第一章前言
1.1说明转炉副枪计算机模型炼钢系统设计说明书是针对华菱涟钢即将实施的炼钢模型系统所
涉及的控制范围和应用功能的详细说明和描述。
该详细设计是受甲方的委托,并根据生产工艺的要求、有关行业规定和用户特别需求等进行编写,将由华菱涟钢的有关领导和专家进行审核,并将作为下阶段项目实施和软件编制的基础。
1.2设计范围
计算机模型炼钢系统的设计是针对华菱涟钢第一炼钢厂二座210吨转炉(1#和2#)实施的,设计应用控制功能范围包括从兑铁开始到转炉出渣结束等炼钢工序的全过程。
1.3设计要求设计和应用转转炉计算机模型炼钢系统的优点有:
D提高操作效率
D提高终点[C]、T双命中率
D减少补吹次数
D减少渣中铁含量
D延长炉衬寿命
D提高废钢融化效率计算机炼钢的目的是节约能源和物料消耗,降低吨钢成本,跟踪管理转炉炼钢过程,
提高生产管理水平,最终增产增效益。
1.4设计要求
应用软件具有良好的开放性和兼容性
控制系统稳定,可靠性高
系统面向实用,全部应用成熟技术和设备
操作人员具有熟练的炼钢操作技能
转炉已装备底吹系统,并运行良好
使用动态控制炼钢模型时,转炉装备副枪测量系统并可以正常运行。
1.5工艺背景华菱涟钢位于湖南省东部地区,是我国中部最重要的钢铁生产基地之一,其第一炼钢
厂拥有二座公称容量210吨的大型转炉,将装配副枪系统,另外,还配备有混铁炉、KR
脱硫、LF、RH和大型双流板坯连铸机等高效的生产设备。
由于管理科学,设备先进,生
产规模不断扩大,在可预计的将来,华菱涟钢第一炼钢厂将成为中国最现代化的炼钢厂之一。
工艺路线:
高炉——铁水罐车——混铁炉——脱硫——转炉——吹氩——LF精炼——连铸机冶炼周期:
转炉采用顶底复吹工艺,底吹惰性气体,以加强熔池搅拌,缩短吹炼时间,提高金属
收得率和氧气利用率。
采用副枪技术后,将可以通过动态过程控制提高终点命中率,缩短冶炼周期,增加转炉生产能力。
转炉平均冶炼周期:
37min
1.6操作方式对操作方式进行明确的定义对于模型控制和生产操作是非常必要的:
——手动方式操作工对各个设备进行独立操纵。
——自动方式
操作工通过PLC对各个设备进行自动顺序操作。
此时,副枪二级计算机没有向一级发送设定值,但操作完成后,部分实际数据将由
一级系统向副枪二级计算机传送。
——计算机方式副枪二级计算机向一级系统自动发送设定值,经确认后,一级系统将根据模型计算
设定值自动完成操作。
操作完成后,实际数据将由一级系统向副枪二级计算机传送。
1.7参考资料
—技术附件
—计算机软件产品开发文件编制指南
—工艺操作说明书
1.8说明与约定
—为更形象描述各项功能,本设计以画面形式提供说明,并列有相关数据,这些数据仅具参考价值,与本设计没有直接必然关系。
第二章标准定义
2.1工程单位软件编制采用国际标准公制单位,下表为常用工程单位对照表:
名称
单位
缩写
长度
米
m
重量
公斤
Kg
重量
吨
t
时间
秒
S
气体容积量
标立方米
Nm³
温度
摄氏温度
℃
气体压力
兆帕
MPa
电流
安培
A
电压
伏特
V
功率
牛顿米
Nm
重力
牛顿
N
2.2专用术语
动态吹炼:
无特殊说明时,指副枪二级计算机通过副枪测量,不倒炉动态校正吹炼过
程。
+0炉:
即当前炉,指炼钢副枪二级计算机控制的从开吹到后续炉开吹之前的炉次。
+1炉:
即将要冶炼的炉次。
+2炉:
+1炉将要冶炼的下一炉次。
2.3缩写
为提高效率和统一识别,在应用软件编制过程中,使用了部分英语缩写词。
缩写词意义
BOF转炉TORP铁水罐
DES脱硫站
AR吹氩站LF钢包炉
RH或VD真空脱气装置CCM连铸
ASCII美国标准信息交换代码
(AmericanStandardCodeInformationInterchange)L1或BAS一级自动化系统或者基础自动化
L2副枪二级计算机系统L3三级计算机系统
SQL数据库查询语言HMI人机接口
PLC可编程逻辑控制器S7西门子S7系列PLC
TCP/IP文件控制传输协议/因特网通讯标准
2.3基本要素为了确保整个项目和软件模块的一致性,本节将对系统中所使用的一些最基本的要素
进行定义,本节所列的要素定义内容,仅限于与模型炼钢有关的部分。
—转炉号转炉号是对单个转炉的唯一标示,在本设计中其取值为1和2。
—炉次号目前,涟钢一炼钢厂在全厂范围内已运行计算机网络管理,因此炼钢生产计划是由
调度系统按照合同自动预先形成,炉次号是炼钢生产计划中每个炉次的唯一标示。
由公司或炼钢厂调度系统自动按一定的规则形成,每个具体炉次信息的查询和使用,必须以计划炉次号为索引关键字。
计划炉次号由8个数字组成:
第1位数字当前年号最末1位,如2008年,则取“8”。
另外,从每年元月1日零点起,当前年号最末1位按下一年度取值。
第2位数字脱硫站号,分别取1、2、3。
第3位数字转炉号,分别取1或2。
第4至8位数字本年度炉次顺序号,如“08888”表示本年度的第08888炉,顺序号的生成是同一座转炉每生产一炉后加1,每年元月1日零点起,顺序号从1开始重新计数,最大值为00000-99999。
例如:
81108888为一完整的炉次号。
—炉次状态在转炉工序范围内,对于一个具体炉次的生产状态定义如下:
状态码
描述
0
计划状态下的炉次
1
炉次开始
2
加料开始
3
加料结束
4
转炉吹炼开始
5
TSC测量开始
6
TSC测量结束
7
转炉吹炼结束
8
TSO测量开始
9
TSO测量结束
10
转炉出钢开始
11
转炉出钢结束
12
出渣开始
13
出渣结束(炉次结束)
—GE-NO
由6位字符组成,ERP系统中表示钢种代码的唯一关键字。
—钢种代码钢种代码是对钢水类别的描述说明。
在应用软件系统中,钢种文件包含了钢水成分,钢水质量等重要信息,而钢种代码
是钢种文件中的关键字,因此在钢种文件中钢种代码是唯一的。
另外,每一个钢种代码都附有相应的钢种描述。
钢种代码由20个字符组成
—铁水试样编码(待定)
—炼钢试样编码(待定)
—成分数据
序号标准名称单位格式中文说明
1
C
%
9.9999
碳
2
Si
%
9.9999
硅
3
Mn
%
9.9999
锰
4
P
%
9.9999
磷
5
S
%
9.9999
硫
6
Al
%
9.9999
铝
7
Ni
%
9.9999
镍
8
Cu
%
9.9999
铜
9
Cr
%
9.9999
铬
10
Mo
%
9.9999
钼
11
Als
%
9.9999
溶铝
12
V
%
9.9999
钒
13
Ti
%
9.9999
钛
14
Nb
%
9.9999
铌
15
Ca
%
9.9999
钙
16
Co
%
9.9999
钴
17
Pb
%
9.9999
钎
18
W
%
9.9999
钨
19
Mg
%
9.9999
镁
20
Ce
%
9.9999
铈
21
B
%
9.9999
硼
22
As
%
9.9999
砷
23
Sn
%
9.9999
锡
24
Bi
%
9.9999
铋
25
Sb
%
9.9999
娣
26
Zr
%
9.9999
锆
27
Cq
%
9.9999
碳当量
28
O
ppm
9.9999
氧气
29
N
ppm
9.9999
氮气
30
H
ppm
9.9999
氢气
—标准日期与时间
根据WINDOWS操作系统的标准,以下列形式表示内部日期和时间:
DD-MMM-YYYYHH:
MM:
SS但在操作画面中,仍使用中国公民所习惯的时间表示。
举例如下:
2008年8月8日8时8分8秒
第三章网络、硬件和系统软件
3.1概述本节是对转炉炼钢副枪二级计算机服务器、操作站和工程师站的硬件、系统软件和网
络结构的设计描述。
本项目的计算机设备系统设计所遵循的原则是尽可能统一设备型号,减少设备备件的
种类,简化设备维修。
在先进可靠和高性价比的前提下,确定PC服务器、PC计算机终端的型号,在可行的条件下,应与钢厂其它计算机型号保持一致。
3.2网络结构
说明:
炼钢副枪二级计算机系统网络图
按照中冶南方的计算机专业设计,炼钢全厂将形成非常完善的网络系统。
因此,炼钢
副枪二级计算机系统将成分利用全厂网络设施,与二级中心数据库和基础自动化相连接,
使用TCP/IP协议通讯,网络中的服务器和操作站的IP地址由炼钢厂统一分配。
3.3设备说明
--模型服务器模型服务器设计为二台,安装在转炉计算机房内。
序号
名称
数量
描述
1
服务器硬件
2
IntelPentiumXeon3.2GHZ双核CPU
—2GBDDR
—2*以太网接口(100/1000Mb)
—DVD-R/W
--4*72GSCSI硬盘
--RAID5
—3*72G硬盘
—19”LCD显示器
--PS2标准键盘和USB光电鼠标
--冗余电源
2
系统软件
2
1
2
2
2
Windows2003Server
Oracle10g
防病毒软件
VisualStudio.NET与基础自动化通讯软件
—客户端
序号
名称
数量
描述
1
硬件
5
PCIntel酷睿双核2.0
——1GDDR主存
——以太网接口(100/1000Mb)
——CD-ROM
——160G硬盘
——19“液晶显示器,标准键盘,鼠标
2
系统软件
5
1
WindowsXP
中文软件包,防病毒软件OracleClient软件
3
激光打印机
1
A3幅面,黑白,带有以太网接口
4
彩色打印机
1
A4幅面,带有以太望接口
5
网络设备
1
网络设备及电缆
6
机柜
1
国标1.8米高,色标待定
3.4电源
所有计算机(包括服务器)和网络设备的设计供电为220VAC/50Hz,所有的服务器、操作站、网络设备都必须使用UPS电源。
UPS电源由用户提供,交接点均为设备就近的电源插座。
设备功耗如下表所示:
设备类型
部件
耗电(W)
服务器类
系统单元
显示器
450
40
PC类
系统单元LCD显示器
350
40
3.5环境
所有安装计算机和网络设备的室内必须安装有空调。
计算机设备要求如下的使用环境条件:
温度(℃):
10~30湿度(%):
20~80
3.6资料硬件设备和系统软件资料均由设备厂家提供。
第四章工艺模型
4.1概述炼钢工艺模型主要包括主原料计算、静态模型和动态计算等转炉全部工艺的过程模
型。
模型的计算机理主要是基于熔池内各种元素的化学反应和由此带来的物料平衡和热平衡。
铁水的重量、温度和成分(C、Si、Mn、P、S)、废钢量、钢水量、终点温度、熔剂加入量、渣量和供氧量等将作为物料平衡和热平衡的主要项。
下面对转炉工艺模型的常规分类及通用机理作简要介绍。
模型名称
描述
主原料计算
根据钢种的要求选择熔剂组号,计算终渣的成分。
并根据铁水量和出钢量决定废钢量
熔剂和静态计算
熔剂和供氧量的计算根据终渣的成分要求和渣量来计算熔剂的量。
根据铁水和废钢量、终点成分温度的要求,在转炉静态自学习的基础上,根
据相关的校正系数来进行供氧量和冷却剂的计算。
过程控制
吹炼过程的枪位、氧流量、底吹流量和副枪测量的控制吹炼过程的枪位、氧流量和底吹流量的控制是根据氧枪的设计、炉型的状况
和终点成分的要求等来确定。
副枪测量在吹炼氧量占总氧量85%左右开始。
动态计算
动态过程供氧量和冷却剂的计算
副枪1测量以后,根据副枪1测量的温度和碳(TSC)以及终点钢水温度和钢种成分的要求,计算供氧量和冷却剂(包括发热剂),并进行动态校正。
4.2参数维护系统
—参数维护画面参数维护画面主要包括计算边界条件、温度校正系数画面、静态计算系数画面(包含
主原料计算系数的内容)、吹炼方式画面、动态计算系数画面、熔剂计算系数画面、出钢合金计算系数画面。
相应维护参数的输入和修改都可以在对应的窗口中完成。
模型参数调整的权限仅为冶金工程师所有。
所有参数调整后的值就作为常数使用,但静态模型和动态
模型计算参数在作为常数使用的同时还在进行自学习功能的修正。
具体系数调节的内容请见《第六章计算机过程控制》中相应画面。
—模型参数清单
参数
单位
描述
常规参数
铁水数据
铁水成分、温度和重量
钢水成分
〔%〕
钢水温度
〔℃〕
熔剂加料量
〔Kg〕
供氧量
〔Nm3〕
原材料参数
主要指废钢、矿石(冷却剂)、石灰、轻
烧白云石和其它熔剂
收得率
〔%〕
冷却效率
动态和静态过程的冷却效率或升温效率
要区别对待
升温效率
热力学参数
平衡参数
钢渣之间的P、Mn的分配系数
冶金参数
铁的收得率
〔%〕
温度补偿系数
不同因素造成的温度补偿系数
物理热损失
〔℃〕
物理原因造成的额外的热损失
氧气的利用率
〔%〕
氧气的利用率考虑炉型的变化和氧枪喷
孔的变化
动态降碳系数
动态过程的降碳系数
动态升温系数
动态过程的升温系数
渣中目标(MgO)
〔%〕
渣中目标碱度
(CaO)/(SiO2)
4.3主原料计算
根据予先准备的铁水量和出钢量计算废钢量。
—所需数据表
所需数据名称
单位
描述
实际过程数据
钢水量
〔t〕
已设定
铁水温度
〔℃〕
测量
铁水成分
〔%〕
化验
钢种数据
废钢方式
已设定
目标成分
〔%〕
已设定
熔剂方式
已设定
目标温度
〔℃〕
在设定的基础上已进行修正
工艺数据
冷却剂的加入量
〔Kg〕
包括静态加入量和动态过程的加入量
(最大值、目标值、最小值)
—计算结果
计算结果
单位
描述
废钢重量
〔t〕
废钢总重量和不同类型的废钢重量
4.4熔剂和静态计算
在完成主原料计算并将相关主原料数据进行输入后,伴随着熔剂的计算。
操作工也可根据操作的具体情况对熔剂的数据做出适当的修改。
在完成熔剂计算以后,就可以进行静态计算,即对吹炼静态氧量和冷却剂量的计算。
—所需数据
所需数据名称
单位
描述
实际过程数据
铁水量
〔t〕
已设定
铁水温度
〔℃〕
测量
铁水成分
〔%〕
化验
废钢重量
〔t〕
废钢的总重量和不同类型的废钢重量
钢种数据
目标终点温度
〔℃〕
已设定
目标终点成分
〔%〕
已设定
熔剂方式(终渣方式)
已设定
熔剂特性数据
熔剂的化学成分
〔%〕
已设定
熔剂的收得率
〔%〕
已设定
熔剂冷却剂当量系数
已设定
—功能描述
根据实际入炉的铁水量、铁水成分、铁水温度、废钢量、钢种相关数据和熔剂的相关数据进行熔剂计算和静态计算。
熔剂具体计算是在主原料计算的过程中完成,是同主原料计算同时进行的。
但因主原料计算时的条件(铁水成份、温度等均为预测值)或未完全按主原料计算模型计算结果最终确定主原料的量,因而熔剂计算在主原料确定完后并根据实际的主原料条件再进行熔剂计算。
熔剂计算是根据主原料的计算和对应钢种的相关熔剂方式、废钢方式等进行的。
第一次熔剂计算以冷却剂为目标值、发热剂为0,以碱度为目标终渣要求计算边界条件,得出第一次熔剂的计算结果(包括计算得出的冷却剂量)。
然后在第一次计算的基础上,以冷却剂为允许范围、发热剂为0,碱度为终渣碱度范围,再进行第二次熔剂的计算。
对于主原料计算完全按主原料模型进行计算的炉次,熔剂的计算只是一个确认过程或是作少量的修改过程。
但是在主原料计算未按主原料模型进行的炉次,第一次熔剂计算过程同主原料未作修改的过程相同。
第二次计算时,根据第一次计算的热平衡状况,决定冷却剂或发热剂的量。
在计算过程中,是通过调整终渣的控制范围(在要求内)再进行第二
次熔剂计算和冷却剂(发热剂)的计算。
如计算需加发热剂,则模型将终渣成分往下限调
整,直到不需要加发热剂(终渣成份在控制范围内)或者终渣成份已在控制范围下限且需要加发热剂。
反之,需要加冷却剂的可采取增加熔剂的方式使冷却剂的加入量控制在目标值的范围内(当终渣成份超上限时,采取增加冷却剂的方式来完成)。
静态计算是用吹炼的冶金反应过程的热平衡、物料平衡、氧平衡来进行计算。
但因冶炼过程对静态计算的影响是一个很复杂的系统问题,因而在进行静态计算时,同时必须利用静态自学习模型中的参考炉次的特征数据和三大平衡来共同完成。
计算原理如下:
·模型输入的数据:
已设定的钢种、铁水和废钢边界条件:
目标终渣要求、发热剂为0计算结果:
熔剂(其中包括冷却剂)
·模型输入的数据:
钢种、初计算冷却剂量、铁水和废钢量边界条件:
目标终渣要求、发热剂为0或冷却剂在目标范围内计算结果:
熔剂(其中包括冷却剂或发热剂)
·模型输入的数据:
钢种、计算的废钢、铁水、熔剂和冷却剂(发热剂)量和参考炉次特征数据
计算结果:
总供氧量(可根据测量副枪的时机和静态供氧量推出)
—铁平衡和热量平衡此模型计算时有三个变量(钢水量、冷却剂重量、发热剂重量),并由这三个变量组
成两个等式。
系统初计算时的边界条件之一为发热剂的加入量为0。
计算结果为钢水重量和冷却剂量。
如计算结果冷却剂量为负,则说明需要加发热剂。
那么该模型将以冷却剂为
0进行再次计算,通过调整终渣成份来调整热平衡。
—氧平衡在铁平衡和热平衡的基础上,根据冷却剂或发热剂的量和废钢方式进行静态计算。
静
态计算的相关参数可以通过工程师直接设置和自学习模型自动修正两种方式来共同完成。
—计算结果
计算结果
单位
描述
熔剂加入量
〔kg〕
石灰、轻烧的加入量
冷却剂(发热剂)
〔kg〕
冷却剂(发热剂)的加入量
钢水量
〔t〕
计算吹炼终点的钢水量
渣量
〔t〕
计算吹炼终点的渣量
总供氧量
〔Nm3〕
可根据静态过程的氧量进行总氧量的
计算
4.5动态计算
过程控制主要包括吹炼过程的枪位、氧流量、底吹流量和副枪测量的控制。
过程控制是以氧耗进程作为控制的参照标准的。
吹炼过程的枪位、氧流量是根据氧枪的设计、炉型的状况和终点成分的要求并对应氧耗进程等来确定。
在整个吹炼过程(除副枪测量阶段外)都采用均衡流量供氧。
氧枪枪位的高度根据钢种的不同都已固定为吹炼模式。
底吹控制过程是根据不同钢种对复吹气体(N2/Ar)的不同要求,决定底吹气体的流量、底吹气体的种类以及N2/Ar的切换时间和末期后复吹的后搅时间。
副枪测量的启动时间是吹炼氧量达到总氧量的85%左右时开始,具体副枪的测量所需时间是由副枪的性能来决定的。
在副枪测量过程中,氧气流量为正常吹炼流量的50%,底吹流量也是正常吹炼时底吹流量的50%。
当吹炼到总氧量的85%左右进行副枪1的测量。
测量完副枪1以后,就进入了动态控制的阶段。
动态计算包括动态氧量、动态冷却剂(动态发热剂)重量等的计算。
—所需数据
所需数据名称
单位
描述
废钢方式
根据钢种已设定
熔剂加入量
〔kg〕
副枪1之前的加入量
过程测量数据
副枪1温度
〔℃〕
副枪1测量
副枪1的碳
〔%〕
副枪1测量
终点目标数据
终点成份
〔%〕
终点的目标成份
终点目标温度
〔℃〕
主原料计算时已设定
原材料数据
加入料的成份
〔%〕
冷却剂、发热剂、石灰等
加入料的温降或发热系数冷却剂、发热剂、石灰等
—功能描述动态计算是根据废钢方式不同对应不同的升温系数和根据不同的复吹状况和终点碳
的要求对应不同的脱碳系数进行动态供氧量、冷却剂、发热剂的计算。
·模型输入的数据:
已设定的钢种(废钢方式、终点要求、动态组别)、副枪1的温度和碳
边界条件:
目标终点成份、冷却剂为0
计算结果:
最初动态供氧量和终点温度
·模型输入的数据:
已设定的钢种(废钢方式、终点要求、动态组别)、副枪1的温度和碳和计算出的最初