YST20KW液压综合试验台的设计.docx
《YST20KW液压综合试验台的设计.docx》由会员分享,可在线阅读,更多相关《YST20KW液压综合试验台的设计.docx(25页珍藏版)》请在冰豆网上搜索。
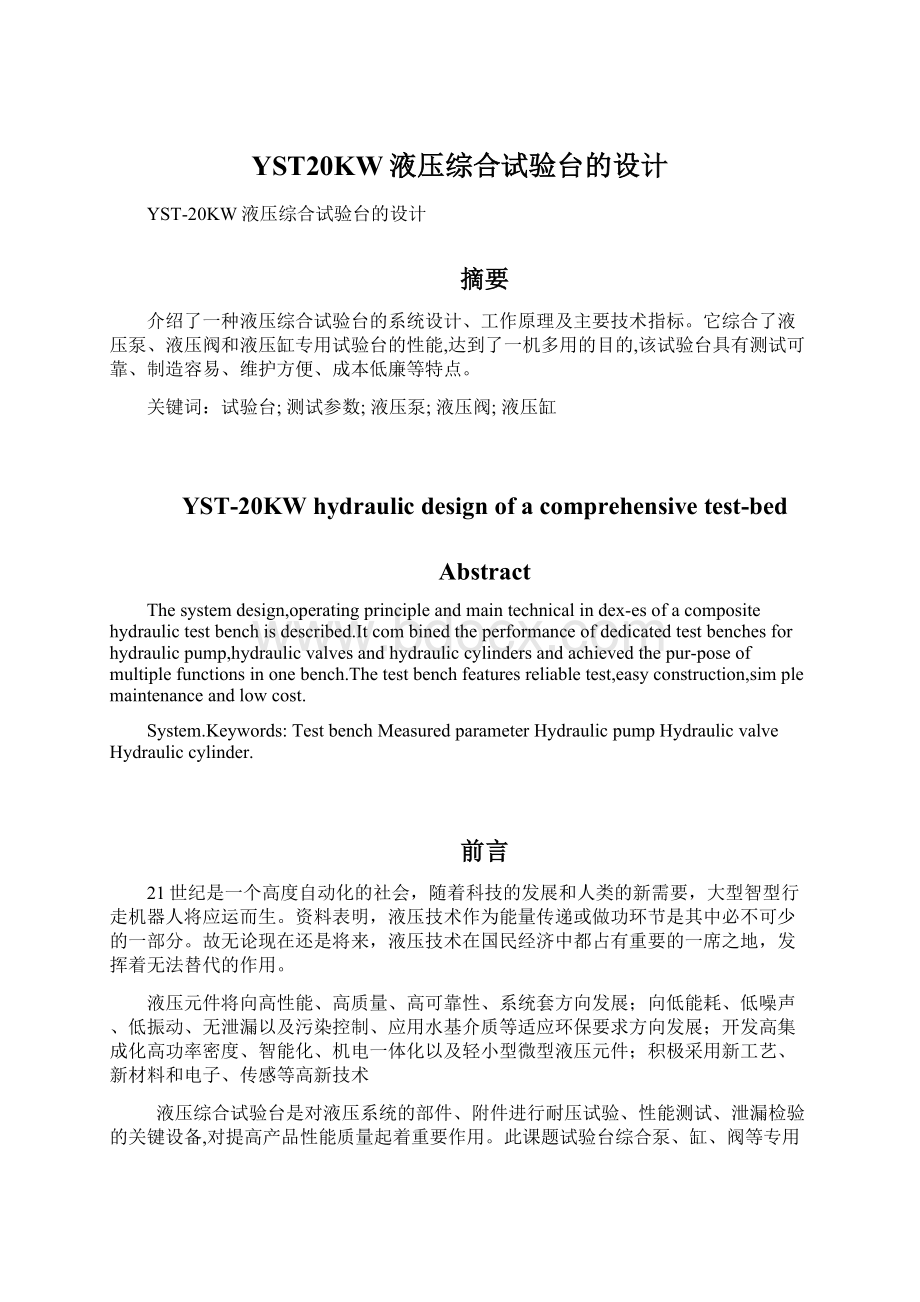
YST20KW液压综合试验台的设计
YST-20KW液压综合试验台的设计
摘要
介绍了一种液压综合试验台的系统设计、工作原理及主要技术指标。
它综合了液压泵、液压阀和液压缸专用试验台的性能,达到了一机多用的目的,该试验台具有测试可靠、制造容易、维护方便、成本低廉等特点。
关键词:
试验台;测试参数;液压泵;液压阀;液压缸
YST-20KWhydraulicdesignofacomprehensivetest-bed
Abstract
Thesystemdesign,operatingprincipleandmaintechnicalindex-esofacompositehydraulictestbenchisdescribed.Itcombinedtheperformanceofdedicatedtestbenchesforhydraulicpump,hydraulicvalvesandhydrauliccylindersandachievedthepur-poseofmultiplefunctionsinonebench.Thetestbenchfeaturesreliabletest,easyconstruction,simplemaintenanceandlowcost.
System.Keywords:
TestbenchMeasuredparameterHydraulicpumpHydraulicvalveHydrauliccylinder.
前言
21世纪是一个高度自动化的社会,随着科技的发展和人类的新需要,大型智型行走机器人将应运而生。
资料表明,液压技术作为能量传递或做功环节是其中必不可少的一部分。
故无论现在还是将来,液压技术在国民经济中都占有重要的一席之地,发挥着无法替代的作用。
液压元件将向高性能、高质量、高可靠性、系统套方向发展;向低能耗、低噪声、低振动、无泄漏以及污染控制、应用水基介质等适应环保要求方向发展;开发高集成化高功率密度、智能化、机电一体化以及轻小型微型液压元件;积极采用新工艺、新材料和电子、传感等高新技术
液压综合试验台是对液压系统的部件、附件进行耐压试验、性能测试、泄漏检验的关键设备,对提高产品性能质量起着重要作用。
此课题试验台综合泵、缸、阀等专用试验台的性能,达到了一机多用的目的,使其具有造价低、加工制造容易、维护方便等特点能更好运用到生产实际中去达到高效,优质,低耗,安全的目的。
由于本人对液压知识了解有限,又无实际工作经验,所以设计难免有不合理之处,敬请教师和同学给予批评指正。
目录
摘要I
AbstractII
前言III
目录IV
1选题依据-1-
1.1我国液压行业的现状-1-
1.2国外液压技术发展状况-1-
1.3本课题的目的与意义-2-
2被测试元件的主要性能指标-2-
2.1油泵测试指标-2-
2.2阀类测试指标-2-
2.3油缸测试指标-2-
3对试验台的工作要求-2-
4拟定试验台油路系统的设计-3-
4.1油泵试验台液压系统的设计-3-
4.2阀类试验台液压系统的设计-4-
4.3油缸试验台液压系统的设计-5-
4.4综合试验台的设计-6-
5液压元件的选择与计算-6-
5.1泵的选择-7-
5.2电机的选择-7-
5.3各种阀的选择-7-
6绘制正式系统图-9-
7系统验算-10-
7.1压力损失的验算-10-
7.2系统发热温升及冷却的计算-11-
8泵站传动系统的设计-11-
8.1传动方案的确定-11-
8.2带轮传动的设计计算-11-
8.3小带轮的结构设计-12-
8.4其他传动件的选择与计算-12-
9加载油缸的设计-13-
9.1参数的确定-13-
9.2缸作用能力的计算-13-
9.3缸的结构设计-13-
10试验台的使用说明-14-
10.1油泵的测试方法-14-
10.2阀类的测试方法-15-
10.3油缸的测试方法-16-
11试验台的经济性能分析-16-
12结论-17-
结束语-18-
参考文献-19-
致谢-21-
附录-22-
1选题依据
1.1我国液压行业的现状
我国的液压技术是随着新中国的建立、发展而发展起来的,从1952年上海机床厂试制出我国第一台液压元件起,迄今,大致经历了创业奠基、体系建立、成长发展、引进提高等几个发展阶段。
20世纪50年代初期我国没有专门的液压元件制造厂,上海、天津、沈阳、长沙等地的机床厂的液压车间自产自用大部分都是仿制前苏联的元件此期间的液压产品多为管式联接,结构差,性能低。
1959年国内建立了首家专业化液压元件制造企业天津液压件厂。
20世纪60年代,液压技术的应用从机床行业逐渐推广到农业机械和工程机械等领域,为了解决仿苏联产品品种单调,结构笨重和性能落后的问题,并满足日益增长主机行业的需要,我国液压行业从仿制走上了自行开发的设计道路。
20世纪70年代,在高压液压阀品种规格逐渐增多的情况下,为了实现标准化,系列化,通用化,扩大品种,提高质量,追赶国际先进水平。
1973年多家单位组成液压阀联合设计组,整个70年代是我国液压元件品种发展最多的时期之一。
20世纪80年代,在国家改革开放的方针指引下,随着机械工业的发展,基础件滞后于主机的矛盾日益突出,并引起各有关部门的重视。
为此,原一机部于1982年组建了通用基础件工程局,将原分散在机床、农业机械、工程机械等行业归口的液压专业厂,统一划归通用基础件局管理,从而使该行业在规划、投资、引进技术和科研开发等方面得到基础件局的支持和指导。
经过半个世纪的努力,我国液压行业已形成一个门类比较齐全,有一定生产能力和技术水平的工业体系。
目前,我国的液压元件制造业已能为包括金属材料工程,机床与汽车工业,电力与煤炭行业,石油天然气探取与化工装备,矿山及冶金机械,铁路与公路运输,建材建筑,工程机械及农林牧机械在内的多种部门提供较为齐全的液压元件产品。
1.2国外液压技术发展状况
为了全方位地满足不同用户的需求,国外工程机械在朝着系列化、特大型化方向发展的同时,已进入多用途、微型化发展阶段。
推动这一发展的因素首先源于液压技术的发展———通过对液压系统的合理设计,使得工作装置能够完成多种作业功能;其次,快速可更换联接装置的诞生———安装在工作装置上的液压快速可更换联接器,能在作业现场完成各种附属作业装置的快速装卸及液压软管的自动联接,使得更换附属作业装置的工作在司机室通过操纵手柄即可快速完成。
液压技术是实现现代化传动与控制的关键技术之一,世界各国对液压工业的发展都给予很大重视。
世界液压元件的总销售额为350亿美元。
据统计,世界各主要国家液压工业销售额占机械工业产值的2%~3.5%。
以微电子、Internet为重要标志的信息时代,不断研制出集液压、微电子及信息技术于一体的智能系统,并广泛应用于工程机械的产品设计之中,进一步提高了产品的性能及高科技含量。
1.3本课题的目的与意义
液压综合试验台是对液压系统的部件、附件进行耐压试验、性能测试、泄漏检验的关键设备,对提高产品性能质量起着重要作用.
此课题试验台综合泵、缸、阀等专用试验台的性能,达到了一机多用的目的,使其具有造价低、加工制造容易、维护方便等特点能更好运用到生产实际中去达到高效,优质,低耗,安全的目的。
2被测试元件的主要性能指标
为了满足工作要求,在液压试验中,不仅要对被测元件进行定性分析,而且还要进行定量分析;这就要求有一定的测试指标。
2.1油泵测试指标
测试油泵能否达到额定工作压力,额定工作压力下的流量及其容积效率。
2.2阀类测试指标
测试阀类元件可靠性、压力损失及内泄漏。
2.3油缸测试指标
测试油缸的性能,采用拉力表拆测油缸拉力的办法进行测试。
3对试验台的工作要求
对试验台总的要求是结构紧凑,操作方便,测试准确,维修方便,效率高,成本低,寿命长。
该试验台主要由动力源,加载装置,测量仪表,辅助设备及试验机架组成。
动力源由发动机驱动,油泵为液压系统提供压力油。
加载装置:
考虑到该试验台的工作压力在中高压以下,因而采用节流加载通过改变通流断面积的大小而为系统提供所需压力。
测试仪表:
它是试验台的关键件,仪表的精确程度决定了被测液压元件指标的测量精确性。
它包括压力表,转速表,流量表,温度表等。
测量仪表表面使用刻度,一般为表盘满刻度的1/3—1/2.同时,应经常校验测量仪表表面的准确度。
辅助设备:
油箱、油管、滤油器、加热器、散热器、电气设备等组成它和试验台机架是构成完整的试验台不可或缺的部分。
对于机架应有足够的刚度,以免试验台引起振动从而影响测量仪表的读数。
另外,由于液压元件与油的温度及粘度有关,所以,一般液压试验台都应控制油温,在50℃±5℃范围内测定元件性能较为可靠。
4拟定试验台油路系统的设计
4.1油泵试验台液压系统的设计
4.1.1确定测试项目
能否达到额定工作压力
额定压力下的流量
容积效率的测试
4.1.2工况分析
根据本设计的工作场合及其设计要求等多方面进行考虑,在各类泵中选用齿轮泵。
齿轮泵的压力范围在2.5-25MPa内,流量范围在0.15-4550L/min,在此范围中可以选取本试验台设计所需的合适元件。
齿轮泵自吸能力非常好,输出压力脉动大,污染敏感度低,价格低。
最高工作压力P=12.5MPa,流量为Q=72L/min。
4.1.3拟定液压系统方案
确定本试验台的测试项目及试验台工作压力、流量后就可画出液压系统工作油路图。
由此可见,油泵试验台工作时要求有相当功率和转速的发动机带动被试油泵。
液压系统要求有一个可调的外载体油泵建立一定得压力值。
故采用通过改变油泵出口通流断面积的大小的液压节流加载来为油泵提供负荷。
为了防止由于操作不当而引起的系统压力超高而损坏元件。
系统上最高的压力油安全阀来控制,从而起到安全保护作用。
数据的测量是通过压力表、流量计、转速表、温度计等仪表在一定条件下测取而得到的仪表的精度,直接影响着测试的精度。
辅助装置由油箱,散热器,加热器,油管,滤油器等组成。
其试验台系统图如下
(1)
4.2阀类试验台液压系统的设计
4.2.1确定测试项目
a换向阀的测试项目
1)换向可靠性的测试
2)压力损失的测试
3)内泄漏的测试
b流量阀的测试项目
1)流量调节范围的测试
2)最小稳定流量的测试
3)内泄漏的测试
4)进出口压力变化对流量影响的测试
c压力阀的测试项目
1)压力阀的压力调节范围的测试
2)卸荷压力的测试
3)内泄漏的测试
4)流量变化对被调压力的影响的测试
4.2.2工况分析
由于农机中分配器以FP1-75A,FP3-75A的流量和压力为最大,分别为P=10Mpa,v
Q=75L/min,故以此作为实验台的参数依据。
4.2.3试验台参数的确定
依据以上的工况分析,为了使试验台能够有较大的压力测试范围,因而其参数确定如下:
最大工作压力P=12.5Mpa最大流量Q=72L/min
4.2.4拟定液压系统方案
动力源部分用发动机带动常备油泵为系统提供油液,加载装置为一回路可调的节流阀,通过改变节流阀开度的大小为系统提供不同的压力。
油液的换向通过手动换向阀来实现,用以测试阀的换向可靠性,试验台的其他部分与油泵试验台相同,这里不再重复,系统图如下
(2):
4.3油缸试验台液压系统的设计
4.3.1确定测试项目
1)行程的测试
2)油缸提升力的测试
3)内泄漏的测试
4)外泄漏的测试
5)耐压测试
4.3.2工况分析
由于农业机械中常用的液压元件的YG型的压力最高为P=10Mpa,最大提升负荷以YG-110为最大,为900Pma。
4.3.3试验台参数的确定
因油缸的耐压实验的压力为1.5倍的额定压力,故试验台的最大工作压力为P=1.5Mpa,PN=15Mpa.其流量只影响运动的速度,故最大流量为72L/min。
4.3.4拟定液压系统方案
油缸试验台的基本组成与泵阀类试验台相似,只有加载有所不同,加载采用加载油缸来为被测油缸提供负荷,加载油缸采用进出口相连,中间串一双可调节流阀。
通过调节节流阀的开度来改变大小,其液压系统原理图(3)。
4.4综合试验台的设计
在上述三种分立元件试验台的基础上,以油泵测验台系统为主,将阀类和油缸试验台液压系统叠加,保留专用油路和仪表,合并公用的元件,组成综合液压实验台的油路系统。
5液压元件的选择与计算
5.1泵的选择
常备泵选择依据试验台的工作压力P=10Mpa,流量Q=72L/min,选择CB50型齿轮泵,其v=48ml/r,额定工作压力P=10Mpa,最大工作压力Pmax=12.5Mpa,转速n=1500r/min。
5.2电机的选择
功率的确定:
N=PQ/612η=21.4KW
考虑到被测泵转速各不同,且差距较大,因而选取调速发动机型号为调速电机,型号为YCT250-4B,N=22KW,n=132-1320r/min,电流三相交流电,频率为50Hz,电压为380V。
5.3各种阀的选择
表1
序号
名称
规格
数量
流量(L/min)
工作压力(Mpa)
公称通径(mm)
1
溢流阀
YF-L(B)20H2
1
100
4.0-16
20
2
节流阀
LF-L20C
2
75
20.6
20
3
单向节流阀
LDF-L20C
1
75
20.6
20
4
单向阀
S-20
6
115
31.5
20
5
多路换向阀
ZS2-L20E
1
100
16
20
6
手动换向阀
WMM
1
-31.5
10
5.4仪表的选择
表2
序号
名称
规格
数量
测试范围
1
压力表
Y-150
3
0-16MPa
2
压力表
Y-150
1
0-16MPa
3
真空表
YZ-150
1
4
流量计
LC12-25
1
5
压力表开关
AF6EA30/x250
4
0-25MPa
6
温度计
WTZ-288
1
7
转速表
CZ-636
1
300-3000r/min
8
液位计
YWZ-150T
1
9
计时表
1
5.5油管内径的选择计算及管接头的选择
油管内径的大小直接影响着油管内油的流速,从而影响压力的损失大小,一般对流速有一定得要求,根据确定油管内径的经验公式和推荐,用流速,油管的内径确定如下:
推荐用流速:
吸油管v≤1-2m/s
压油管v≤3-6m/s
回油管v≤1.5-2.5m/s
流量Q=72L/min
吸油管d=39.1mm
压油管d=19.5mm
回油管d=27.6mm
依据上述的计算选取的管注见下表:
油管选15号冷拔无缝钢管,管接头选择焊接式端直通管接头
表3
公称通径(mm)
钢管外径(mm)
管接头螺纹
公称压力(MPa)
壁厚
(mm)
实际流速m/s
管接头
吸油管
40
50
M48
2
16
4.5
0.99
压油管
20
28
M27
2
16
2.5
3.97
JB966-77
回油管
32
42
M42
2
16
4
1.55
JB966-77
5.6滤油器的选择
滤油器的基本作用是使系统有野保持清洁,保护各种元件保证系统工作稳定,滤油器具有足够大的通油能力,并且压力损失小。
该实验台采用两级过滤,第一级过滤设置在进油口上,采用过滤精度很低的粗滤器;第二级过滤设置在回油路上用一较高精度的细滤器,故滤油器选为:
吸油口:
XU-B160
100公称直径40mm额定流量160L/min螺纹连接螺纹M48
2精度100
m
回油口:
YHK-160
10F额定流量160L/min过滤精度10
m法兰连接。
5.7油箱的设计及油的加热
5.7.1油箱的设计
见附图一
油箱在液压系统中除了储油外,还起散热、分离油液中的气泡,沉淀杂质的作用。
油箱必须有足够大的容积,一方面尽可能的满足散热要求,另一方面在液压系统停止工作时应容纳系统中的所有工作介质,而工作时又能保持适当的液位。
其油箱的有效容积一般选得较大,推荐为3-5倍的系统最大流量,故油管箱的有效容积初选为:
V=4Q=288L
由《机械设计手册》中可以查出油箱的有效容积占油箱容积的80%,故油箱的容积为V=288/80%=360L
设油箱的长、宽、高比为a:
b:
c=1.5:
1:
1,
则a=932mmb=621mmc=621mm
根据实际结构的要求,油箱尺寸取为:
a=1000mmb=650mmc=650mm
选热轧钢板3
1010
660一张,热轧钢板为3
660
1010两张,制好油箱后,对油箱内表面进行防腐,喷砂后进行喷塑。
5.7.2油的加热
液压系统中的油温,一般控制在30-50
范围内,最高不得超过70
,最低不应低于15
,油温过高将使油液迅速老化变质,同时使油液的粘度降低,造成元件内泄漏量的增加系统效率降低。
油温过低,使油液粘度过大,造成泵吸油困难。
加热器的发热能力可按下式估定:
采用电加热器加热,温开为30℃,加热时间为25min,
则所需热量为N≥1800
900
30
0.3/25
60=9.72KJ。
电加热器的功率为P=N/n=9.72/0.7=13.9KW。
选GYY4-220/8电加热器2个,每个功率P=8KW,电压220V,浸入油中深度为930mm,所以实际加热时间为T=1800
900
0.3
30/16=20min
6绘制正式系统图
见附图二
7系统验算
7.1压力损失的验算
系统的压力损失验算是检验能否保证被测元件的工作压力而满足正常的测试要求,这里仅以油缸的测试回路为例进行计算,其他回路的计算方法均相同。
7.1.1沿程压力损失的计算
已知油管内径及油的流速分别为:
V压力=3.97m/sd压=20mmV回=1.55m/sd回=32mm
V吸0.99m/sd吸=40mm
流动类型的判别,油温取平均测试温度50℃,v=60cst=0.6st
Re压=v
d
104/r=3.97
0.02
104/0.6=1323<2300
Re回=v
d
104/r=1.55
0.032
104/0.6=827<2300
Re吸=v
d
104/r=0.99
0.04
104/0.6=660<2300
所以均为层流
依据公式△PL=∑λ
(L/d)
(V2/2)
r压油管取钢管长L1=5m,回油管长L2=4m,吸油管L2=1m。
所以△PL=0.114MPa.
7.1.2局部压力损失计算
阀的局部压力损失的计算
各种阀的压力损失分别为:
溢流阀0.2Mpa调速阀<0.3Mpa手动换向阀0.1-0.25Mpa单向阀0.1-0.15Mpa
滤油器:
0.2Mpa
所以∑△P向=1.25Mpa
管路内部压力损失计算
进油路上有四个圆弧90º弯道,回油路上有三个圆弧90º弯道,两个折90º弯道,依据公式△Pr=∑ξ(V2/2)
r可计算出局部压力损失。
对于折90º弯道ξ=1.12,90º圆弧弯道ξ=0.21
△Pr=0.09Mpa
所以总的局部压力损失为△P局=1.34Mpa
7.1.3管路总的压力损失为
△P=△PL+△P局=1.454Mpa
在测试YG型油缸时的工作压力为10Mpa,此时实验台压力为:
P=△P+PN=1.454+10=11.454Mpa<12.5Mpa。
7.2系统发热温升及冷却的计算
液压系统产生的热量主要包括泵的功率损失,溢流阀的溢流损失及管道的压力损失所产生的热量,溢流阀及管道压力损失所产生的热量极易散失,故忽略不计,则泵的发热量为Ph1=P(1-η)=22
(1-0.8)=4.4KW
而油箱的散热量为
Phc=KA△T取K=16W/(
)△T=30º所以Phc=1.65KW
由于Phc<Ph1,所以系统应设置冷却设施,选用风扇冷却。
基于工作环境,经济效益等多方面考虑选用YA-N32(20号)普通液压油。
8泵站传动系统的设计
见附图三
8.1传动方案的确定
传动形式采用V带传动,因为发动机的最高转速过低,故需进行增速,因为CB50型泵的转速为的1500r/min,因而选择传动此为1.2:
1的传动系统使泵站可以达到,满足测试要求的速度。
8.2带轮传动的设计计算
已知所传递功率,P=22KWn=1320r/mini=1.2
确定皮带型号:
SPA型窄V带
小带轮直径:
d1=180mm
大带轮直径:
d2=220mm
带速:
v=
d2n2/60
1000=12.43m/s
初定轴间距:
初选a0=500mm
所需皮带长度:
L0=2a0+(d1+d2)
/2+(d2-d1)2/4a0=1629mm
取Ld=1800mm,L0=1629mm
实际轴间距:
a≈a0+(Ld-L0)/2=586mm
小带轮包角:
a1=180º-(d2-d1)
57.3º/a=175º>120º
单根V带传递的额定功率:
P1=6.10KW,额定功率增量△P=0.21KW
V带的根数:
Z=Pd/PrKaKc=2.9取3根
单根V带的预紧力:
F=500(2.5/Ka-1)Pd/ZV+Mv2=410N
作用在轴上的力:
Fr=2F0Zsinα1/2=4096N
大带轮见附图
8.3小带轮的结构设计
由YCT250-4B,电动机可知,其轴伸直径d=48mm,长度L=110mm,故大带轮轮直径应取d0=48mm,毂长应小于110mm,实心轮轮槽尺寸及轮宽如图示下,
带轮宽B=(Z-1)
e+2f=81mm
外径da=dd+2ha=226mmφ=38°
电机与大带轮选用A型平键联接14
9(GB/71095-1979)。
小带轮与轴之间的联接选用A型平键10
8(GB/71095-1979)。
小带轮结构图如下所示:
8.4其他传动件的选择与计算
8.4.1滚动轴承的选择
由于轴承仅受径向力作用,故选择深沟球轴承
所受力P=Fr/2=2048N
选取ε=3ft=1Lh=10000h
则
=19.77KW
选用6306深沟球轴承(GB/276-1994)
所以选择c=27.0KN
其实际使用寿命Lh为Lh=(106/60n)
(c/p)3=25433h
轴承座的选择
型号SN306(GB/7813-1987)
用M12螺栓固定。
固定电机用的螺栓M16,离合皿的锁定螺栓M8。
8.4.2轴的设计
见附图