典型零件的加工.docx
《典型零件的加工.docx》由会员分享,可在线阅读,更多相关《典型零件的加工.docx(12页珍藏版)》请在冰豆网上搜索。
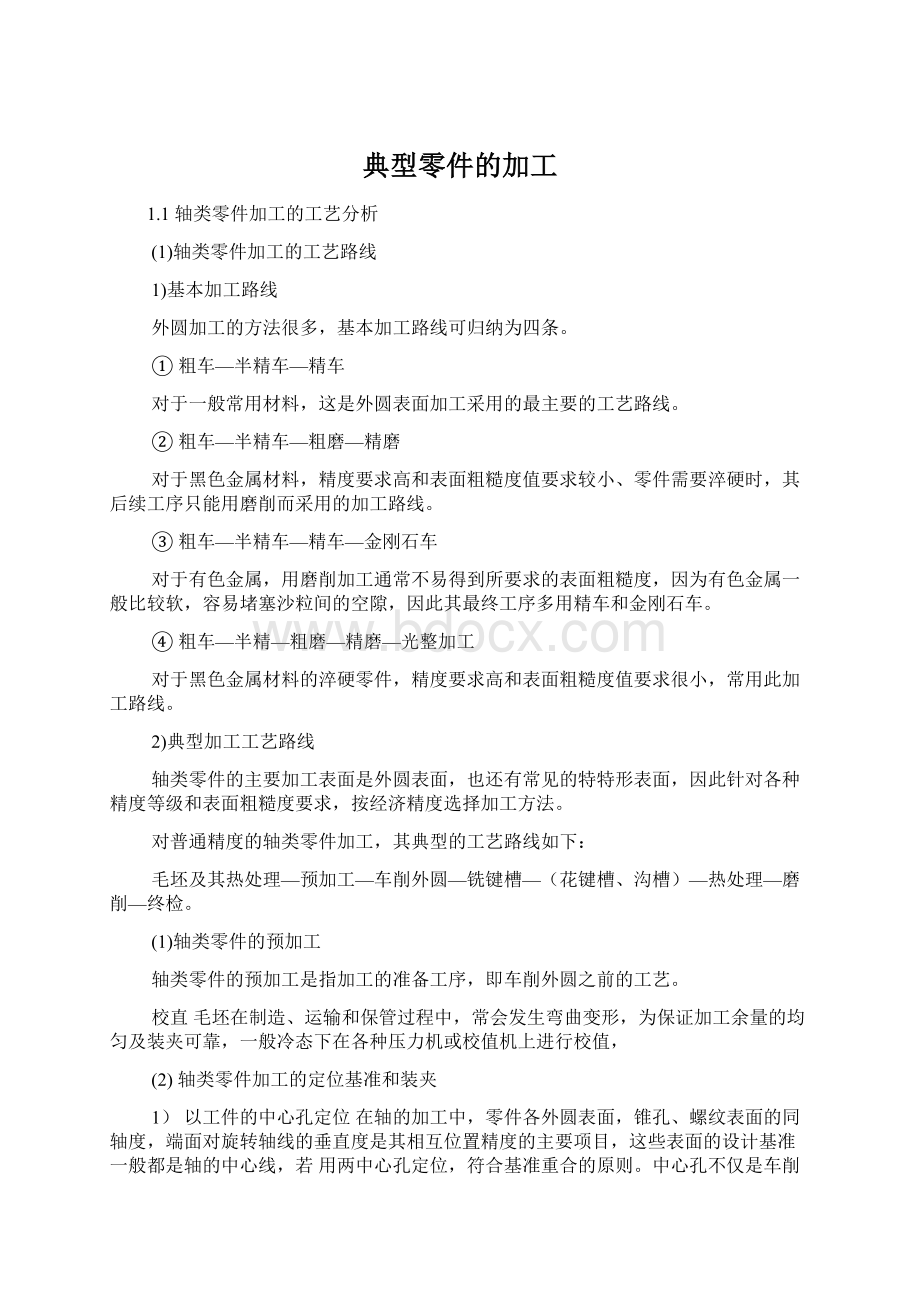
典型零件的加工
1.1轴类零件加工的工艺分析
(1)轴类零件加工的工艺路线
1)基本加工路线
外圆加工的方法很多,基本加工路线可归纳为四条。
①粗车—半精车—精车
对于一般常用材料,这是外圆表面加工采用的最主要的工艺路线。
②粗车—半精车—粗磨—精磨
对于黑色金属材料,精度要求高和表面粗糙度值要求较小、零件需要淬硬时,其后续工序只能用磨削而采用的加工路线。
③粗车—半精车—精车—金刚石车
对于有色金属,用磨削加工通常不易得到所要求的表面粗糙度,因为有色金属一般比较软,容易堵塞沙粒间的空隙,因此其最终工序多用精车和金刚石车。
④粗车—半精—粗磨—精磨—光整加工
对于黑色金属材料的淬硬零件,精度要求高和表面粗糙度值要求很小,常用此加工路线。
2)典型加工工艺路线
轴类零件的主要加工表面是外圆表面,也还有常见的特特形表面,因此针对各种精度等级和表面粗糙度要求,按经济精度选择加工方法。
对普通精度的轴类零件加工,其典型的工艺路线如下:
毛坯及其热处理—预加工—车削外圆—铣键槽—(花键槽、沟槽)—热处理—磨削—终检。
(1)轴类零件的预加工
轴类零件的预加工是指加工的准备工序,即车削外圆之前的工艺。
校直毛坯在制造、运输和保管过程中,常会发生弯曲变形,为保证加工余量的均匀及装夹可靠,一般冷态下在各种压力机或校值机上进行校值,
(2)轴类零件加工的定位基准和装夹
1)以工件的中心孔定位在轴的加工中,零件各外圆表面,锥孔、螺纹表面的同轴度,端面对旋转轴线的垂直度是其相互位置精度的主要项目,这些表面的设计基准一般都是轴的中心线,若用两中心孔定位,符合基准重合的原则。
中心孔不仅是车削时的定为基准,也是其它加工工序的定位基准和检验基准,又符合基准统一原则。
当采用两中心孔定位时,还能够最大限度地在一次装夹中加工出多个外圆和端面。
2)以外圆和中心孔作为定位基准(一夹一顶)用两中心孔定位虽然定心精度高,但刚性差,尤其是加工较重的工件时不够稳固,切削用量也不能太大。
粗加工时,为了提高零件的刚度,可采用轴的外圆表面和一中心孔作为定位基准来加工。
这种定位方法能承受较大的切削力矩,是轴类零件最常见的一种定位方法。
3)以两外圆表面作为定位基准在加工空心轴的内孔时,(例如:
机床上莫氏锥度的内孔加工),不能采用中心孔作为定位基准,可用轴的两外圆表面作为定位基准。
当工件是机床主轴时,常以两支撑轴颈(装配基准)为定位基准,可保证锥孔相对支撑轴颈的同轴度要求,消除基准不重合而引起的误差。
4)以带有中心孔的锥堵作为定位基准在加工空心轴的外圆表面时,往往还采用代中心孔的锥堵或锥套心轴作为定位基准,见图6.9所示。
锥堵或锥套心轴应具有较高的精度,锥堵和锥套心轴上的中心孔即是其本身制造的定位基准,又是空心轴外圆精加工的基准。
因此必须保证锥堵或锥套心轴上锥面与中心孔有较高的同轴度。
在装夹中应尽量减少锥堵的安装此书,减少重复安装误差。
实际生产中,锥堵安装后,中途加工一般不得拆下和更换,直至加工完毕。
12.1轴类零件加工
12.1.1概述
1.轴类零件的功用与结构特点:
轴类零件是机械零件中的关键零件之一,在机器中,它的主要功用是支承传动零件、传递扭矩、承受载荷,以及保证装在轴上的零件等有一定的回转精度。
2.轴类零件的技术要求:
尺寸精度,几何形状精度,相互位置精度,表面粗糙度.
3.轴类零件的材料与热处理:
4.轴类零件的毛坯:
轴类零件的毛坯常采用棒料、锻件和铸件等毛坯形式。
一般光轴或外圆直径相差不大的阶梯轴采用棒料,对外圆直径相差较大或较重要的轴常采用锻件;对某些大型的或结构复杂的轴(如曲轴)可采用铸件。
1.定位基准的选择:
(1)用两中心孔定位。
轴类零件最常用两中心孔为定位基准。
不仅符合基准重合的原则,并能够在一次装夹中加工出全部外圆及有关端面,这也符合基准统一的原则。
粗加工时为了提高零件的刚度,一般用外圆表面或外圆表面与中心孔共同作为定位基准。
内孔加工时,也以外圆作为定位基准。
(2)空心轴定位基准的选择。
对于空心的轴类零件,在加工出内孔后,为了使以后各工序有统一的定位基准,可采用带中心孔的锥堵或锥堵心轴,如图12-2所示。
(3)中心孔的修整。
中心孔在使用过程中会因磨损和热处理变形而影响轴类零件的加工精度。
1)用硬质合金顶尖修研,2)用油石、橡胶砂轮或铸铁顶尖修研,3)用中心孔磨床磨削。
2.外圆表面加工:
(1)外圆表面的车削加工。
轴类零件外圆表面的车削加工可划分为荒车、粗车、半精车、精车和细车等各加工阶段。
使用液压仿形刀架可实现车削加工的半自动化,更换靠模、调整刀具都比较简单,可减轻劳动强度,提高加工效率。
(2)外圆表面的磨削加工。
磨削是外圆表面精加工的主要方法,既能加工淬火件,也能加工未淬火件。
磨削可划分为预(粗)磨、精磨、细磨和镜面磨削。
提高磨削效率的途径有两条:
其一是缩短辅助时间,如自动装卸工件、自动测量及数字显示、砂轮的自动修整与补偿、开发新磨料和提高砂轮耐用度等;其二是缩短机动时间,如高速磨削、强力磨削、宽砂轮磨削和多片砂轮磨削等
3.其它表面的加工方法:
(1)花键的加工,花键按截面形状不同可分为矩形、渐开线形、梯形和三角形四种,其中矩形花键盘应用最广。
定心方式常见的是以小径定心和大径定心,轴类零件的花键加工常用铣削、滚削和磨削三种方法。
(2)螺纹的加工。
螺纹是轴类零件的常见加工表面,其加工方法很多,这里仅介绍车削、铣削、滚压和磨削螺纹的特点。
轴类零件的检验
1.硬度:
硬度在热处理后用硬度计全检或抽检。
2.表面粗糙度:
通常使用标准样板用外观比较法凭目测比较,对于表面粗糙度值较小的零件,可用干涉显微镜进行测量。
3.形状精度:
(1)圆度误差。
当圆柱面的误差为椭圆形时,可用千分尺测出同一截面的最大与最小直径,其差的半值为该截面的圆度误差。
当圆柱面的误差为奇数棱形状时,将被测表面放在V型架上用千分表测量,测出零件旋转一周表的最大与最小值,其差的半值为圆度误差。
精度高的轴用圆度仪测量。
(2)圆柱度误差。
将零件放在V型块或直角座上用千分表测量,精度高的轴用三坐标测量机测量。
4.尺寸精度:
在单件小批量生产中,一般用千分尺检验轴的直径;在大批大量生产中,常用极限卡规检验轴的直径。
尺寸精度高时,可用杠杆千分尺或以块规为标准进行比较测量。
长度尺寸可用游标卡尺,深度游标卡尺和深度千分尺等检验。
5.相互位置精度:
(1)两支承轴颈对公共基准同轴度。
两支承轴颈对公共基准同轴度的检验如图12-17所示;
(2)各表面对两支承轴颈的位置精度。
各表面对两支承轴颈的位置精度检验如图12-18所示.
1.短套筒类零件加工工艺分析:
(2)联接套加工工艺分析,联接套加工工艺过程见表12-2.加工方法选择;2)保证套筒零件表面位置精度的方法:
为保证各表面间的位置精度通常应注意以下几个问题:
①套筒零件的粗精车内外圆一般在卧式车床或立式车床上进行,精加工也可以在磨床上进行。
②以内孔与外圆互为基准,以达到反复提高同轴度的目的:
A.以精加工好的内孔作为定位基面,用心轴装夹工件并用顶尖支承心轴。
由于夹具(心轴)结构简单,而且制造安装误差比较小,因此可保证比较高的同轴度要求,是套筒加工中常见的装夹方法。
B.以外圆作精基准最终加工内孔。
采用这种方法工件装夹迅速可靠,但因卡盘定心精度不高,易使套筒产生夹紧变形,故加工后工件的形位精度较低。
若欲获得较高的同轴度,则必须采用定心精度高的夹具,如弹性膜片卡盘、液性塑料夹具,经过修磨的三爪卡盘和“软爪”等。
3)防止套筒变形的工艺措施。
套筒零件由于壁薄,加工中常因夹紧力、切削力、内应力和切削热的作用而产生变形。
故在加工时应注意以下几点。
①为减少切削力和切削热的影响,粗、精加工应分开进行。
使粗加工产生的热变形在精加工中可以得到纠正。
并应严格控制精加工的切削用量,以减少零件加工时的变形。
②减少夹紧力的影响,工艺上可以采取以下措施:
改变夹紧力的方向,即变径向夹紧为轴向夹紧,使夹紧力作用在工件刚性较好的部位;当需要径向夹紧时,为减少夹紧变形和使变形均匀,应尽可能使径向夹紧力沿圆周均匀分布,加工中可用过渡套或弹性套及扇形夹爪来满足要求;或者制造工艺凸边或工艺螺纹,以减少夹紧变形。
③为减少热处理变形的影响,热处理工序应置于粗加工之后、精加工之前,以便使热处理引起的变形在精加工中得以纠正。
2.长套筒类零件加工工艺分析:
液压系统中的液压油缸本体(图12-22)是比较典型的长套筒零件,结构简单,壁薄容易变形,加工面比较少,加工方法变化不多,其加工工艺过程见表12-3。
现对长套筒零件加工的共性问题进行分析。
(1)液压油缸本体的技术要求。
(2)工艺过程分析。
为保证内外圆的同轴度,长套筒零件的加工中也应采取互为基准、反复加工的原则。
12.2.3深孔加工
孔的长度与直径之比L/D>5时,一般称为深孔。
深孔按长径比又可分为以下三类:
L/D=5~20属一般深孔;L/D=20~30属中等深孔;L/D=30~100属特殊深孔。
(1)深孔加工的特点。
深孔加工中必须首先解决排屑、导向和冷却等几个主要问题,以保证钻孔精度。
保持刀具正常工作,提高刀具寿命和生产率。
(2)深孔加工时的排屑方式:
外排屑(内冷外排屑);2)内排屑(图9-23b)。
(3)深孔加工方式。
深孔加工时,由于工件较长,工件安装常采用“一夹一托”的方式,工件与刀具的运动形式有以下三种。
1)工件旋转、刀具不转只作进给;2)工件旋转、刀具旋转并作进给;3)工件不转刀具旋转并作进给。
12.3.1概述
1.箱体类零件的功用与结构特点:
箱体是机器中箱体部件的基础零件,由它将有关轴、套和齿轮等零件组装在一起,使其保持正确的相互位置关系,彼此按照一定的传动关系协调运动。
结构上有共同的特点:
构造比较复杂,箱壁较薄且不均匀,内部呈腔形,在箱壁上既有许多精度较高的轴承支承孔和平面,也有许多精度较低的紧固孔。
箱体类零件需要加工的部位较多,加工的难度也较大。
2.箱体类零件的材料及毛坯
材料一般采用灰铸铁,常用的牌号为HT200~HT400。
一般采用木模手工造型,毛坯的精度低,加工余量大。
大批大量生产时,通常采用金属模机器造型,
3.箱体类零件的主要技术要求
支承孔的精度和表面粗糙度,支承孔之间的孔距尺寸精度及相互位置精度,主要平面精度和表面粗糙度,支承孔与主要平面的尺寸精度和相互位置精度.
1.箱体类零件平面的加工:
箱体类零件平面的加工常采用刨削、铣削和磨削。
2.箱体类零件的孔系加工:
(1)平行孔系的加工--找正法(可分为划线找正法,心轴块规找正法和样板找正法,适用于单件小批量生产)、镗模法及坐标法。
(2)同轴孔系的加工。
同轴孔系的主要技术要求是孔的同轴度。
保证孔的同轴度有如下方法。
1)镗模法
2)利用已加工过的孔作支承导向。
3)利用镗床后立柱上的导向套支承镗杆。
4)采用调头镗法。
(3)交叉孔系的加工。
交叉孔系的主要技术要求是各孔的垂直度,在普通镗床上主要靠机床工作台上的回转精度。
箱体类零件的检验项目主要有:
各加工表面的粗糙度及外观,孔的尺寸精度,孔和平面的几何形状精度,孔系的相互位置精度。
1.各加工表面的粗糙度及外观
2.孔的尺寸精度:
塞规检验
3.孔的形状精度:
用内径量具(如内径千分尺、内径百分表等)测量,对于精密箱体,需用精密量具来测量。
4.平面的几何形状精度:
平面的直线度可用水平仪、准直仪及平尺等检验。
平面度可用平台及百分表等相互组合的方法进行检验。
5.孔系的相互位置精度:
(1)同轴度:
使用检验棒。
(2)平行度:
如图12-34。
(3)垂直度:
如图12-35。