车工中级试题库车工84.docx
《车工中级试题库车工84.docx》由会员分享,可在线阅读,更多相关《车工中级试题库车工84.docx(79页珍藏版)》请在冰豆网上搜索。
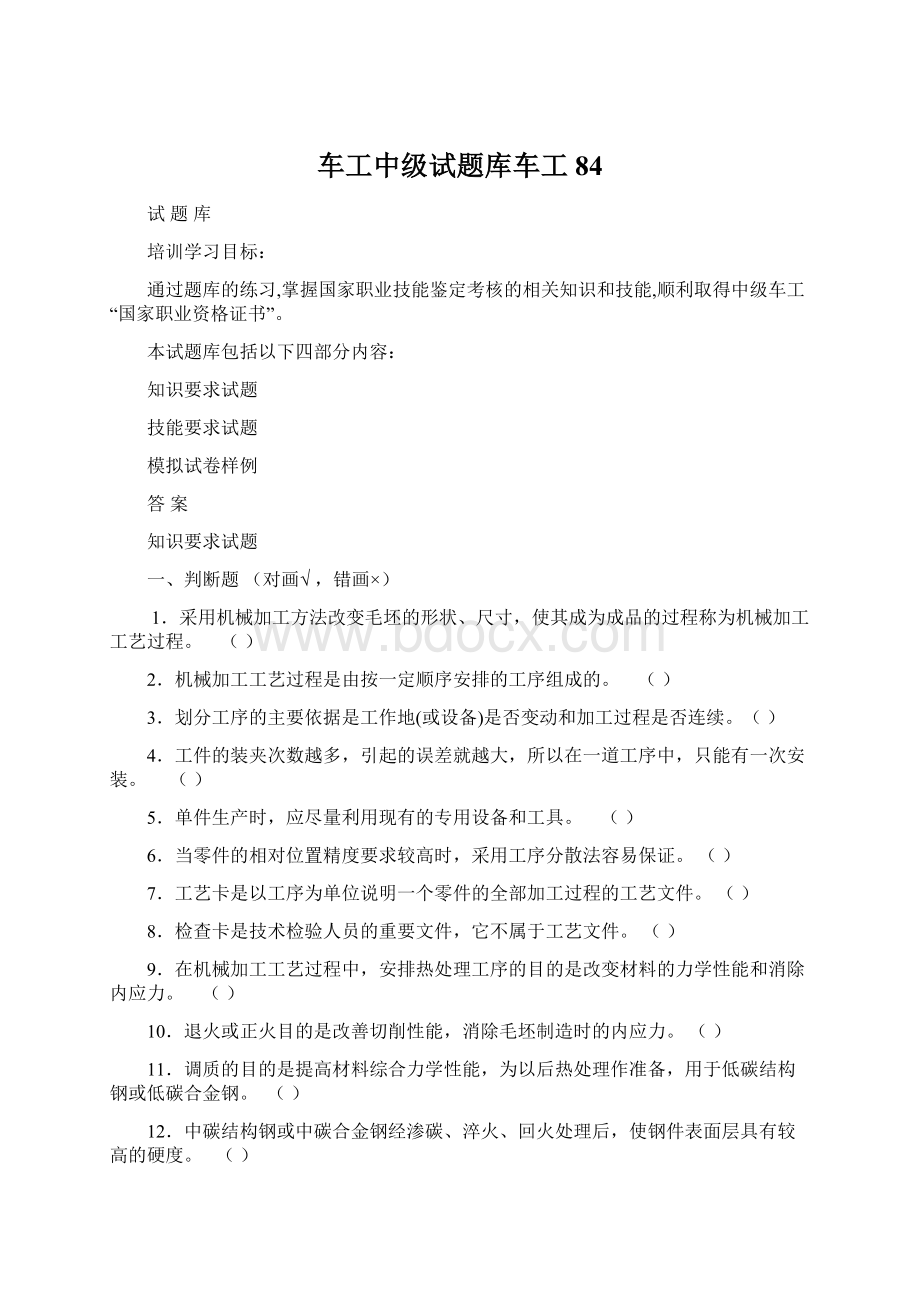
车工中级试题库车工84
试题库
培训学习目标:
通过题库的练习,掌握国家职业技能鉴定考核的相关知识和技能,顺利取得中级车工“国家职业资格证书”。
本试题库包括以下四部分内容:
知识要求试题
技能要求试题
模拟试卷样例
答案
知识要求试题
一、判断题(对画√,错画×)
1.采用机械加工方法改变毛坯的形状、尺寸,使其成为成品的过程称为机械加工工艺过程。
()
2.机械加工工艺过程是由按一定顺序安排的工序组成的。
()
3.划分工序的主要依据是工作地(或设备)是否变动和加工过程是否连续。
()
4.工件的装夹次数越多,引起的误差就越大,所以在一道工序中,只能有一次安装。
()
5.单件生产时,应尽量利用现有的专用设备和工具。
()
6.当零件的相对位置精度要求较高时,采用工序分散法容易保证。
()
7.工艺卡是以工序为单位说明一个零件的全部加工过程的工艺文件。
()
8.检查卡是技术检验人员的重要文件,它不属于工艺文件。
()
9.在机械加工工艺过程中,安排热处理工序的目的是改变材料的力学性能和消除内应力。
()
10.退火或正火目的是改善切削性能,消除毛坯制造时的内应力。
()
11.调质的目的是提高材料综合力学性能,为以后热处理作准备,用于低碳结构钢或低碳合金钢。
()
12.中碳结构钢或中碳合金钢经渗碳、淬火、回火处理后,使钢件表面层具有较高的硬度。
()
13.工件经淬火后,表面硬度较高,一般不再用金属切削刀具进行切削加工。
()
14.工件渗氮处理后有抗疲劳和抗腐蚀性的目的。
()
15.工件毛坯尺寸与图样中标注的尺寸之差称为工序余量。
()
16.在图样上所采用的基准,称为工艺基准。
()
17.在机械制造中,加工零件和装配机器所采用的各种基准,总称为工艺基准。
()
18.装配时用来确定零件或部件在产品中的相对位置所采用的基准,称为定位基准。
()
19.工件的各表面不需要全部加工时,应以不加工面做粗基准。
()
20.因粗基准的表面粗糙度值大,精度又低,所以可以重复使用。
()
21.采用基准统一原则,可减少定位误差,提高加工精度,有利于保证其位置精度。
()
22.工件在夹具中的六个自由度完全被限制了,即处于完全确定的位置,这种定位称为完全定位。
()
23.工件加工时,有时并不要求工件完全定位,限制的自由度满足工件加工要求即可。
()
24.工件以平面定位时,为保证定位的稳定可靠,一般采用四点定位。
()
25.当使用毛坯平面作定位基准时,为提高定位的刚性和稳定性,可尽量增加定位面的接触面积。
()
26.使用锥度心轴装夹工件时,心轴的锥度越大,定心精度越高。
()
27.在夹具中装夹工件时,夹紧力作用点应靠近加工表面,以增加工件的装夹刚性,减小振动。
()
28.细长轴通常用一夹一顶或两顶尖装夹的方法加工。
()
29.为了增加细长工件的刚性,车削时常采用中心架或跟刀架作辅助支承。
()
30.使用三爪跟刀架支承车削细长轴的目的是车削时稳定,不易产生振动。
()
31.车削细长轴时,跟刀架支承爪跟工件的接触压力应大些,这样使工件不易走动。
()
32.使用三爪跟刀架支承车削细长轴,可以有效地补偿工件的热变形伸长。
()
33.用弹性回转顶尖支承车削细长轴,可以有效地补偿工件的热变形伸长。
()
34.薄壁工件受夹紧力产生的变形,仅影响工件的形状精度。
()
35.对于线胀系数较大的金属薄壁件,在半精车和精车的一次装夹中连续车削,所产生的切削热不会影响它的尺寸精度。
()
36.使用开缝套筒装夹薄壁工件的目的是增加装夹接触面,使夹紧力均匀分布。
()
37.车削薄壁工件时,最好应用径向夹紧的方法。
()
38.花盘盘面应平整,并与主轴轴线垂直,表面粗糙度值Ra不大于1.6μm。
()
39.两个平面相交的角度大于或小于90°的角铁叫做角度角铁。
()
40.角铁的两个平面不必精刮。
()
41.所有角铁装在花盘面上之后,它的一个平面都应与车床主轴轴线平行。
()
42.使花盘盘面与主轴轴线垂直的最好方法是,选用耐磨性较好的车刀,紧固床鞍后对花盘精车一刀。
()
43.平衡块不讲究形状和精度,只要装上花盘后能使工件在转动时平衡就可以了。
()
44.花盘盘面的平面度误差一般应小于0.02mm,并允许中间凸。
()
45.被加工表面的旋转轴线与基准平行,外形比较复杂的工件,可装夹在花盘上加工。
()
46.被加工表面的旋转轴线与基准平行,外形比较复杂的工件,可装夹在花盘的角铁上加工。
()
47.钨钴类硬质合金中钴含量越高,其韧性越好,适用精加工。
()
48.当切削条件比较平稳,要求刀具的强度和耐磨性高时,可以选用TiC(碳化钛)含量多的牌号的硬质合金。
()
49.钨钴钛类硬质合金的常用牌号有YG3、YG6、YG6X和YG8。
()
50.钨钴类硬质合金其韧性、磨削性能和导热性好。
主要适用于加工脆性材料(如铸铁)、有色金属和非金属材料。
()
51.当工件材料的强度和硬度低时,可取较大的前角。
()
52.当加工脆性材料时,车刀的前角应取较大值。
()
53.车刀后角的作用主要是减小后面与加工表面之间摩擦。
()
54.减小车刀的主偏角,会使背向力Fp减小,进给力Ff增大。
()
55.增大车刀的主偏角,使切削层厚度增大,切削层宽度减小,切屑容易折断。
()
56.粗加工、半精加工的硬质合金车刀,一般选择较大的主偏角。
()
57.车削细长轴时,由于工件刚度不足,应取较大的主偏角,以减小背向力和振动。
()
58.车床技术规格中的最大工件长度就是最大车削长度。
()
59.车削米制螺纹时和车削英制螺纹时用的交换齿轮是不相同的。
()
60.车削螺纹时用的交换齿轮和车削蜗杆时用的交换齿轮是不相同的。
()
61.车床主轴的旋转精度、刚度、抗振性等对工件的加工精度和表面粗糙度有直接影响。
()
62.主轴箱内主轴前端采用短圆锥连接盘结构主要是使主轴前端的悬伸长度缩短,增加工件的装夹长度。
()
63.车削时产生径向圆跳动或轴向窜动主要原因是主轴轴承间隙过大。
()
64.检查主轴轴承调整后的间隙时,先用手转动主轴,感觉灵活,无阻滞现象(用外力旋转时,主轴转动在3~5圈内能自动平稳地停止)。
然后再进行测量。
()
65.片式摩擦离合器的间隙过大会减小摩擦力,影响车床功率的正常传递,但可减少摩擦片的摩擦。
()
66.主轴轴承间隙过小时,会造成主轴高速旋转时发热过高而损坏轴承。
()
67.片式摩擦离合器的间隙过小,在高速车削时,会因发热而“闷车”,从而损坏机床。
()
68.设备和基础的总重心与基础底面积的形心应尽可能在同一垂直线上。
()
69.CA6140型车床制动器是由制动轮、制动带和杠杆等主要零件组成的。
()
70.CA6140型车床主轴箱中的双向多片式摩擦离合器和制动器是用两个手柄同时操纵的。
()
71.制动器调整后,开动车床使主轴以n主=300m/min的转速正转,然后把制动手柄置于中间位置,主轴能在2~3转时间内制动,而开动机床时制动带完全松开,说明制动器的松紧调整得当。
()
72.安全离合器的作用是当机动进给过程中,进给力过大或刀架运动受阻时,自动断开机动传动路线,使刀架停止进给,避免传动机构损坏。
()
73.安全离合器正常情况下,在弹簧的压力作用下,左右两半部端面齿爪是打滑的。
()
74.CA6140型车床溜板箱内的安全离合器可在车螺纹时起保护作用。
()
75.安全离合器的调整,机床许可的最大进给抗力决定于弹簧调定的压力。
()
76.开合螺母的作用是接通或断开从光杠传来的运动。
()
77.床鞍是横向车削工件的控制背吃刀量时使用的。
()
78.小滑板是纵向车削较短的工件或圆锥面使用的。
()
79.床鞍与导轨间的间隙将影响刀具纵、横两方向的进给精度,从而影响工件的加工精度和表面粗糙度。
()
80.调整后的床鞍与导轨间的间隙,应保持刀架在移动时平稳、灵活,无松动或无阻滞感。
()
81.中滑板刻度圈过松时,拧紧调节螺母和并紧螺母即可并紧。
()
82.车削螺纹时,受螺纹升角的影响,使车削时前角和后角发生变化。
()
83.梯形螺纹有米制和英制两种,我国采用的是牙型角为29°的米制梯形螺纹。
()
84.梯形螺纹的公称尺寸是指外螺纹的螺纹大径尺寸。
()
85.内、外梯形螺纹的配合是以中径尺寸定心的。
()
86.Tr30×6-8e与Tr50×6-8e的螺纹升角是相同的。
()
87.梯形螺纹车刀的最大刀头宽度计算公式为:
W=0.536P-0.366ac(其中P为螺距,ac为牙顶与牙底间的间隙)。
()
88.用高速钢梯形螺纹粗车刀车钢料时,车刀的背前角必须取γp=0°。
()
89.车削一般要求不高的梯形螺纹时,为能车出表面粗糙度较细的齿面,取具有较大背前角的螺纹车刀,这时应修正刀尖角来补偿牙型角误差。
()
90.粗车螺距P<8mm的梯形螺纹时,常使用左右切削方法车削。
()
91.用三针测量梯形螺纹时,主要是测量梯形螺纹中径尺寸。
()
92.梯形内螺纹大径的上偏差是正值,下偏差是零。
()
93.根据梯形螺纹标记,当螺纹为右旋时,需在尺寸规格之后加注“LH”。
()
94.硬质合金梯形螺纹车刀适用于车削一般精度的梯形螺纹。
()
95.精车矩形螺纹时,精车刀的刀头宽度应刃磨为b=[0.5P-(0.02~0.04)]mm。
()
96.车削螺距小于4mm的矩形螺纹时,一般不分粗精车,用直进法以一把车刀切削完成。
()
97.用公法线千分尺测量矩形外螺纹牙厚时,公法线千分尺的测量值即为牙厚尺寸。
()
98.锯齿形螺纹能承受较大的单向压力,通常用于起重和压力机械设备上。
()
99.锯齿形内螺纹的公称直径为36mm,导程为12mm、螺距为6mm、右旋。
标记为B36×12(P6)LH。
()
100.蜗杆蜗轮常用于传递两轴交错60°的传动。
()
101.蜗杆、蜗轮的参数和尺寸都规定在主平面内计算。
()
102.蜗杆、蜗轮分米制和英制两种。
()
103.米制蜗杆的齿形角为14°30′;英制蜗杆的齿形角为20°。
()
104.在CA6140型车床上车削蜗杆时,交换齿轮应使用64齿、100齿、97齿齿轮啮合。
()
105.车蜗杆时的交换齿轮计算方法与车削一般螺纹时相同。
()
106.使用交换齿轮车削蜗杆时,凡是计算出的复式交换齿轮,都能安装在交换齿轮架上。
()
107.蜗杆精车刀左右切削刃之间的夹角应小于两倍齿形。
()
108.两侧切削刃磨有较大前角的卷屑槽蜗杆精车刀,其前端切削刃是不能进行切削的。
()
109.刃磨米制蜗杆精车刀时,刀头宽度可用公式W=0.697mx(当h=2.2mx时)计算。
()
110.轴向直廓蜗杆的齿形在蜗杆的轴平面内为直线,法平面内为阿基米德螺旋线,因此又称阿基米德蜗杆。
()
111.车削轴向直廓蜗杆时,装刀时,应将蜗杆车刀左右切削刃组成的平面与工件轴线重合。
()
112.法向直廓蜗杆的齿形在蜗杆齿部的法平面内为曲线,在蜗杆轴平面内为直线。
()
113.车削法向直廓蜗杆时,装刀时,应将蜗杆车刀左右切削刃组成的平面垂直于齿面。
()
114.粗车蜗杆时,为了防止三个切削刃同时参加切削而造成“扎刀”现象,一般可采用左右切削法车削。
()
115.车削齿面放磨的双头蜗杆,分头时,可使用四爪单动卡盘分头方法较简便。
()
116.车削双头蜗杆分头时,当车床交换齿轮z1齿数是奇数时,就可以在交换齿轮上进行分头。
()
117.用小滑板刻度分头车削双头蜗杆时,小滑板的刻度盘应转过的格数与蜗杆的轴向齿距有关。
()
118.用三针测量蜗杆时,主要是测量蜗杆的分度圆直径。
()
119.用三针测量法测量梯形螺纹中径与蜗杆的分度圆直径时,合用一个量针测量距计算公式。
()
120.用三针测量蜗杆时,量针直径dD可用公式dD=P/[2cos(α/2)]计算。
()
121.用齿厚游标卡尺测量蜗杆齿厚时,测得的读数是蜗杆在分度圆直径处的轴向齿厚。
()
122.齿厚游标卡尺由互相垂直的齿高卡尺与齿厚卡尺组成。
()
123.使用中心架支承车削细长轴时,支承爪与工件的接触应紧些,这样车削时不易振动。
()
124.使用中心架车削细长轴过程中,应随时注意中心架各个支承爪的磨损情况,并及时调整和补偿。
()
125.使用跟刀架车削细长轴时,跟刀架支承爪与工件接触松紧的调节是关键。
()
126.车削不允许接刀的长轴时,使用跟刀架支承车削较适合。
()
127.车削细长轴时,增大车刀主偏角的目的减小刀具对工件的背向力,以减少细长轴的弯曲变形。
()
128.车削细长轴时,选择负刃倾角车刀车削,可使切屑流向待加工表面,并可以减小切削力。
()
129.车削细长轴时,减少装夹接触面积的目的是避免工件被长卡爪夹死而引起弯曲变形。
()
130.使用反向进给车削细长轴的目的是使工件由受拉伸转变为受压,这样能有效地减少工件的径向圆跳动。
()
131.使用扇形软卡爪装夹车削薄壁工件时,扇形软卡爪的圆弧应与工件外圆基本一致或略小于工件外圆。
()
132.精车直径较大、尺寸精度和形位精度要求较高的圆盘薄壁工件的内孔及外圆时,可装夹在花盘上车削。
()
133.使用辅助支承或增加工艺肋车削薄壁工件,其目的是改善工件的装夹刚性。
()
134.车削短小薄壁工件时,为了保证内、外圆轴线的同轴度,可用一次装夹车削。
()
135.工件的内孔和外圆的轴线不在同一轴线上,平行而不重合的工件,叫做偏心工件。
又称偏心套。
()
136.偏心工件两条母线之间的垂直距离称为“偏心距”。
()
137.用四爪单动卡盘装夹加工偏心套时,若测得偏心距偏小时,可将靠近卡盘轴线的卡爪再紧一些。
()
138.用四爪单动卡盘装夹加工偏心轴时,若测得偏心距偏大时,可将靠近工件轴线的卡爪再紧一些。
()
139.用三爪自定心卡盘装夹车削偏心工件中,若测得偏心距小了0.1mm,则应将垫片再加厚0.1mm。
()
140.在三爪自定心卡盘上车削偏心工件时,应选用硬度较低的材料作为垫片。
()
141.在两顶尖间车削偏心工件,不需要用很多的时间来找正偏心。
()
142.偏心距较小的偏心轴,在钻偏心圆中心孔时若与基准圆中心孔相互干涉,就不能采用两顶尖装夹法加工此偏心轴了。
()
143.使用双重卡盘车削偏心工件时,在找正偏心距的同时,还须找正三爪自定心卡盘的端面。
()
144.用偏心卡盘装夹车削偏心工件时,偏心卡盘的偏心距可用量块或百分表测得。
()
145.用偏心套作为夹具能加工偏心轴。
()
146.用偏心轴作为夹具不能加工偏心套。
()
147.量块是具有精确尺寸的长度测量工具,所以要用线胀系数小,耐磨的合金材料制造。
()
148.量块组合的尺寸是各组成量块的尺寸之和,量块块数越多,组合的尺寸就越精确。
()
149.用量块测量时,量块的测量面要用手擦摸,防止油污或汗液影响量块的精度和研合性。
()
150.用游标卡尺测量偏心套的最厚孔壁与最薄孔壁,游标卡尺的读数差即等于偏心距。
()
151.用百分表测量装夹在两顶尖间的偏心轴时,偏心轴转动一周后,百分表上指示出的最大值和最小值之差的一半即为偏心距。
()
152.对于偏心距较大、长度较长的偏心工件,可以在车床上用百分表与中滑板刻度配合测量偏心距。
()
153.车削偏心距较大的两拐曲轴时,为了防止变形,应在曲柄颈空档处加支撑螺杆。
()
154.工件在花盘上装夹的基准面,一般在铣(或牛刨)之后还要进行磨削或精刮。
()
155.在花盘的角铁上车削工件时,转速不宜太低。
()
156.在角铁上装夹、车削工件时,可以不考虑平衡问题。
()
157.立式车床用于加工径向尺寸小而轴向尺寸大,形状复杂的工件。
()
158.立式车床主轴轴线为垂直布局,工作台台面处于水平平面内。
()
159.在立式车床上可以加工大直径的盘、套类工件,但不能加工薄壁工件。
()
160.在立式车床的立刀架上装上磨头,可以磨削大型、淬硬的工件。
()
161.立式车床的立刀架和侧刀架都可以作垂直进给和水平进给运动。
()
162.立式车床的立刀架可向左或向右移动一个角度,进行锥形工件的()
163.在立式车床上装夹工件时,通常以端面定位,或以外圆、内孔作定中心轴线。
()
164.立式车床上的卡盘卡爪可以自动定心。
()
165.在立式车床上用普通压板,采用顶紧工件外圆的装夹方法时,压板的分布要均匀、对称高低要合适,而夹紧力并不要求在同一平面内。
()
166.在立式车床上车削环类工件或盘形工件的端面时,可使用普通压板顶紧工件外圆的装夹方法。
()
167.在立式车床上,一般用千斤顶支撑毛坯基准面,用等高块支撑已加工平面。
()
168.在立式车床上装夹外圆毛坯工件时,应先按其外圆尺寸,在工作台同心圆上作出相应标记,并按标记位置装上卡盘爪并紧固,再调整卡爪,使之与工件外圆尺寸基本相同,最后吊装工件。
()
169.在立式车床上精车端面时,车刀应由工件平面的外缘处向中心方向进给,使刀具磨损所造成端面的平面度误差,呈凹形状,不影响工件的使用。
()
170.在立式车床上车削内外圆时,立刀架或侧刀架行程应由上往下切削,使切削力始终压向工件与工作台贴合,这样可以减小工件的装夹变形。
()
171.在立式车床上不能车削沟槽。
()
172.在立式车床上不能车削精度要求较高的圆锥面。
()
173.在立式车床上精车圆锥面时,车刀刀尖中心应与工作台旋转轴线重合。
()
174.在立式车床上用成形车刀车削型面时,关键是找正成形刀的正确装夹位置。
()
175.用等高块支撑平面时,应用塞尺检验其接触是否良好,若塞尺能塞入,表示有间隙,应用铜棒敲击工件,消除接触面的间隙。
()
二、选择题(将正确答案的序号填入括号内)
1.工件经一次装夹后,所完成的那一部分工序称为()。
A安装B加工C工序
2.工件一次安装中()工位。
A只能有一个B不可能有几个C可以有一个或几个
3.将一个连接盘工件装夹在分度头上钻六个等分孔,钻好一个孔后要分度一次钻第二个孔,钻削该工件的六个等分孔,就有()。
A六个工位B六道工序C六次安装
4.在加工表面和加工工具不变的情况下,所连续完成那一部分工序称为()。
A进给B安装C工步
5.在一台车床上,对一个孔连续进行钻孔—扩孔—铰孔加工,其工艺过程为()工步。
A一个B三个C复合
6.在车床上,用三把刀具同时加工一个工件的三个表面的工步为()工步。
A一个B三个C复合
7.在工艺过程卡片中,对()一般不作严格区别。
A工步和进给B安装和工位C工步和工位
8.在大量生产中,广泛采用()。
A专用机床、自动机床和自动生产线
B数控机床和加工中心
C通用机床
9.在单件生产中,常采用()法加工。
A工序集中B工序分散C分段
10.对于碳的质量分数大于0.7%的碳素钢和合金钢毛坯,常采用()作为预备热处理。
A正火B退火C回火
11.采用正火热处理,可以提高()碳钢的硬度。
A低B中C高
12.锻件、铸件和焊接件,在毛坯制造之后,一般都安排()热处理。
A退火或正火B调质C时效
13.调质热处理用于各种()碳钢。
A低B中C高
14.淬火工序一般安排在()。
A毛坯制造之后,粗加工之前
B粗加工之后,半精加工之前
C半精加工之后,磨削加工之前
15.低碳钢经渗碳、淬火、回火后,可提高()硬度。
A表面层B心部C全部
16.基准一般分为()大类。
A设计基准和工艺基准两
B定位基准、测量基准和装配基准三
C设计基准、工艺基准、定位基准、测量基准和装配基准五
17.定位基准、测量基准和装配基准()基准。
A都是工艺B都是设计C既是设计基准、又是工艺
18.采用设计基准、测量基准、装配基准作为定位基准时,称为基准()原则。
A统一B互换C重合
19.任何一个工件在空间的位置,都可以沿()坐标轴移动。
A二个B三个C四个
20.限制部分自由度就能满足工件加工要求,这种定位称为()。
A完全定位B不完全定位C欠定位
21.锥度心轴的锥度(),定位精度越高。
A越大B不大不小C越小
22.如果工件与夹具定位面(或工作台面)的接触部位是未加工表面,这是一般只需选用()接触点。
A二点B三点C四点
23.精车薄壁工件时,车刀的前角γo应()。
A适当增大B适当减小C和一般车刀同样大
24.车削薄壁工件时,应设法()装夹接触面积。
A减小B增大C避免
25.使用弹性涨力心轴()车削薄壁套外圆。
A不适宜B最适宜C仅适宜粗
26.车削薄壁工件时,()应用轴向夹紧的方法。
A不能使用B最好C避免
27.直角形角铁装上花盘后,它的一个平面应与车床主轴轴线()。
A垂直B平行C允许倾斜
28.在花盘上装夹工件后产生偏重时,()。
A只影响工件的加工精度
B只影响车床的主轴和轴承的损坏
C不仅影响工件的加工精度,还会损坏车床的主轴及其轴承
29.外形较复杂、加工表面的旋转轴线与基面()的工件,可以装夹在花盘上加工。
A垂直B平行C倾斜
30.()钢是一种含钨、铝、铬、钒等合金元素较多的高合金工具钢。
A碳素工具钢B高速钢C合金工具
31.()类硬质合金(YG)是由Wc和Co组成的,其韧性、磨削性能和导热性好。
A钨钴B钨钴钛C钨钛钽(铌)钴
32.()牌号硬质合金,适用于铸铁、有色金属及其合金的粗加工,也可断续切削。
AYG8BYT5CYNo5
33.()牌号硬质合金,适用碳素钢、合金钢的精加工。
AYG3BYG6XCYT30
34.床身上最大工件回转直径相同的车床,最大工件长度()。
A都相同B不相同C有多种
35.CA6140型卧式车床床身上最大工件回转直径是()mm。
A205B210C400
36.CA6140型车床主轴箱内主轴部件采用了前、中、后三个支承,其中()支承为