炼钢学习心得体会.docx
《炼钢学习心得体会.docx》由会员分享,可在线阅读,更多相关《炼钢学习心得体会.docx(20页珍藏版)》请在冰豆网上搜索。
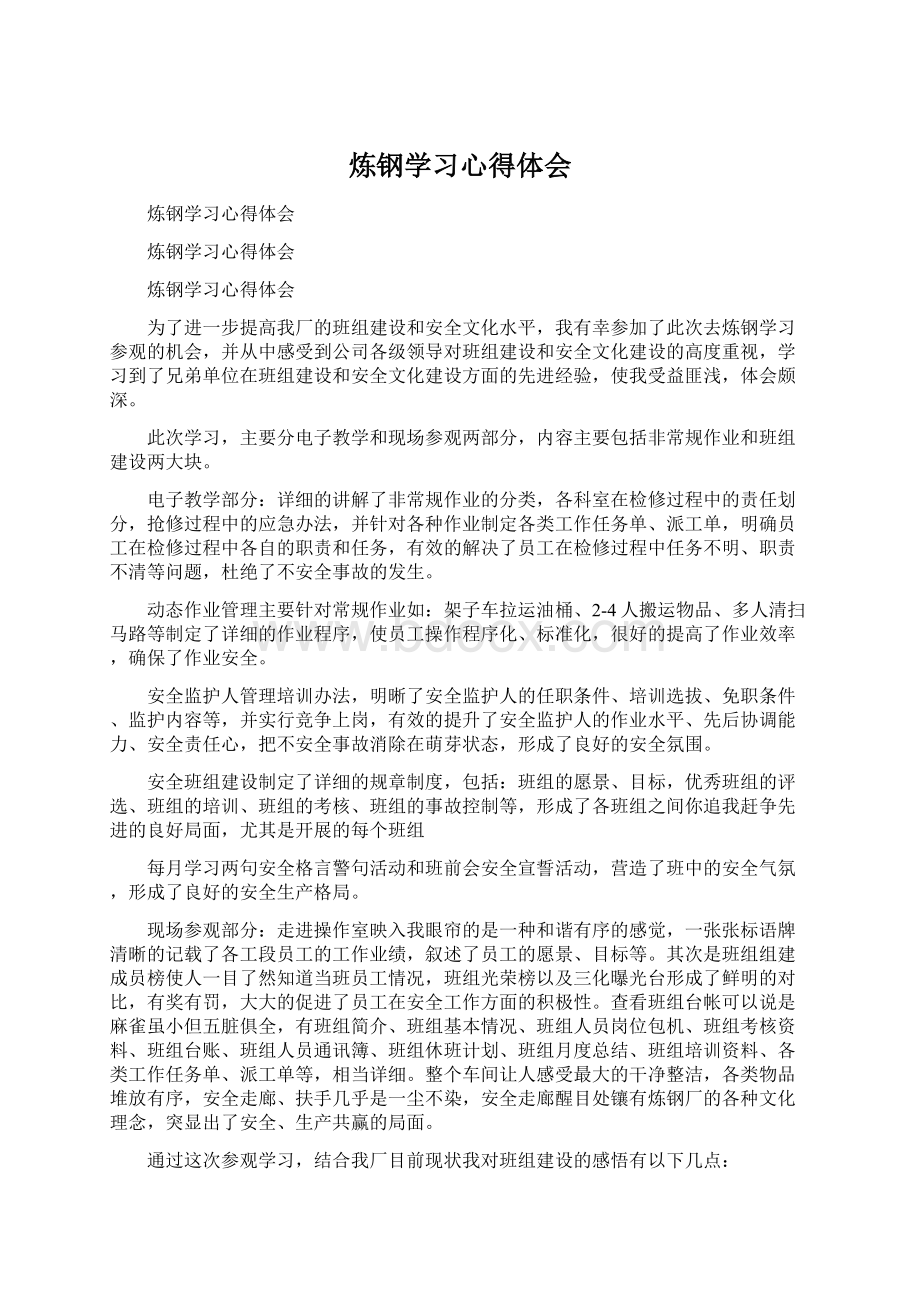
炼钢学习心得体会
炼钢学习心得体会
炼钢学习心得体会
炼钢学习心得体会
为了进一步提高我厂的班组建设和安全文化水平,我有幸参加了此次去炼钢学习参观的机会,并从中感受到公司各级领导对班组建设和安全文化建设的高度重视,学习到了兄弟单位在班组建设和安全文化建设方面的先进经验,使我受益匪浅,体会颇深。
此次学习,主要分电子教学和现场参观两部分,内容主要包括非常规作业和班组建设两大块。
电子教学部分:
详细的讲解了非常规作业的分类,各科室在检修过程中的责任划分,抢修过程中的应急办法,并针对各种作业制定各类工作任务单、派工单,明确员工在检修过程中各自的职责和任务,有效的解决了员工在检修过程中任务不明、职责不清等问题,杜绝了不安全事故的发生。
动态作业管理主要针对常规作业如:
架子车拉运油桶、2-4人搬运物品、多人清扫马路等制定了详细的作业程序,使员工操作程序化、标准化,很好的提高了作业效率,确保了作业安全。
安全监护人管理培训办法,明晰了安全监护人的任职条件、培训选拔、免职条件、监护内容等,并实行竞争上岗,有效的提升了安全监护人的作业水平、先后协调能力、安全责任心,把不安全事故消除在萌芽状态,形成了良好的安全氛围。
安全班组建设制定了详细的规章制度,包括:
班组的愿景、目标,优秀班组的评选、班组的培训、班组的考核、班组的事故控制等,形成了各班组之间你追我赶争先进的良好局面,尤其是开展的每个班组
每月学习两句安全格言警句活动和班前会安全宣誓活动,营造了班中的安全气氛,形成了良好的安全生产格局。
现场参观部分:
走进操作室映入我眼帘的是一种和谐有序的感觉,一张张标语牌清晰的记载了各工段员工的工作业绩,叙述了员工的愿景、目标等。
其次是班组组建成员榜使人一目了然知道当班员工情况,班组光荣榜以及三化曝光台形成了鲜明的对比,有奖有罚,大大的促进了员工在安全工作方面的积极性。
查看班组台帐可以说是麻雀虽小但五脏俱全,有班组简介、班组基本情况、班组人员岗位包机、班组考核资料、班组台账、班组人员通讯簿、班组休班计划、班组月度总结、班组培训资料、各类工作任务单、派工单等,相当详细。
整个车间让人感受最大的干净整洁,各类物品堆放有序,安全走廊、扶手几乎是一尘不染,安全走廊醒目处镶有炼钢厂的各种文化理念,突显出了安全、生产共赢的局面。
通过这次参观学习,结合我厂目前现状我对班组建设的感悟有以下几点:
第一,要统一思想、提高认识。
班组建设的目标是将班组建设成为“安全文明高效、培养凝聚人才、开拓进取创新、团结学习和谐”的班组,为职工搭建不断提升技能水平,充分展示自己能力的平台。
第二,要以人为本、构建和谐型班组。
一个班组就是一个大家庭。
在班组这个“家”中大家要像用对待亲人一样。
在处理问题时应多从对方的角度去考虑问题,相互关心,相互理解,处处充满温馨和谐。
此次参观中、以及白国周班组管理学习中都证明了这样一个道理:
一
个和谐良好的班组环境能保证班组人员的思想稳定,提高班组人员工作热情,更加有利于班组凝聚力和战斗力的生成,为全面推进班组建设的开展提供保障。
第三,要把握关键,抓住重点。
班组长是班组建设的关键所在,一个班组管理水平的好坏班组长的素质起着非常关键的作用,班组长应将50%的时间用在班组的管理上。
班组建设要落到实处,就必须重视班组的生产工作,班组长必须要以身作则狠抓生产管理。
要做到查隐患疏而不漏,纠违章铁面无私,抓防范举一反三。
只要敢抓敢管,就能起到以点带面的作用,从而实现带动一批人,真正做好生产现场的班组建设工作。
第四,要强化培训,创建学习型班组。
只有平时多培训,多学习、多积累,关键时候才能用的上。
所以班组建设必须要认真开展好培训工作,培养班组成员善于学习、勤于思考的习惯,为每位员工营造浓厚的学习氛围,发挥每个员工的创新思维能力,把创建学习型班组作为班组建设的核心内容。
通过此次参观学习,不但学到了其他兄弟单位在班组建设上的先进经验,感受到了公司对班组建设的高度重视,更进一步提高了认识,理清了以后的工作思路。
明确了班组建设要抓什么,重点抓什么,怎么来抓。
我们共同努力,使我厂的班组建设工作迈上一个新的台阶。
扩展阅读:
炼钢学学习总结
炼钢学学习总结钢铁冶金
钢铁材料是人类社会最主要使用的结构材料,也是产量最大、应用最广泛的功能材料,在经济发展中发挥着举足轻重的作用。
尽管今年来钢铁面临着陶瓷材料、高分子材料、有色金属材料(如铝)等的竞争,由于其在矿石储量、生产成本、回收再利用率、综合性能等方面所具有的明显优势,在可以预见的将来,钢铁在各类材料中的重要地位仍然不会改变。
炼钢学是研究将高炉铁水(生铁)、直接还原铁或钢铁加热、溶化,通过化学反应去除铁液中的有害杂质,配加合金并烧铸成半成品铸坯的工程科学。
炼钢包括以下主要过程:
1.去除钢中的碳、磷、硫、氧、氮、氢等杂质组分以及由废钢带入的混杂元素铜、锡、铅、铋等;2.为了保证冶炼和浇铸的顺利进行,需将钢水加热升温至16001700℃;
3.普通碳素钢通常需含锰、硅,低合金钢和合金钢则需含有铬、镍、、、钒、钛、铌、铝等,为此在炼钢过程中需向钢液配加有关合金以使之合金化;4.去除钢液中内生和外来的各类非金属夹杂物;
5.将合格钢水浇铸成方坯、小方坯、圆坯、板坯等;
6.节能和减少排放,包括回收转炉炼钢煤气、炼钢烟气余热利用、减少烟尘和炉渣排放以及炼钢烟尘污泥、炉渣、耐火材料等的回收利用。
一、炼钢法的变迁:
1.1856年英国人H.Bessemer发明酸性底吹转炉炼钢法→1879年英国人S.G.Thomas发明碱性空气底吹转炉炼钢法→20世纪50年代氧气顶吹转炉炼钢法
1952年氧气顶吹转炉炼钢方法,在奥地利被发明成功。
→氧气底吹转炉炼钢法→了顶底复吹氧气转炉炼钢方法,
2.1856年平炉炼钢方法(酸性炉衬)→碱性平炉炼钢方法很快被开发成功→1899年电弧炉炼钢方法也被发明成功。
最早起始于1856年英国人H.Bessemer发明的酸性底吹转炉炼钢法,该方法首先解决了大规模生产液态钢的问题,奠定了近代炼钢工艺方法的基础。
(空气与铁水的直接作用,具有很快的冶炼速度,当时的主要炼钢方法。
但是工艺采用的是酸性炉衬,不能造碱性炉渣,因而不能进行脱磷和脱硫。
)1879年英国人S.G.Thomas发明了碱性空气底吹转炉炼钢法,成功地解决了冶炼高磷生铁的问题。
由于西欧许多铁矿为高磷铁矿,直到20世纪70年代末,Thomas炼钢法仍被法国、卢森堡、比利时等国的一些钢铁厂所采用。
1856年平炉炼钢方法也被成功发明。
最早的平炉仍为酸性炉衬,但随后碱性平炉炼钢方法很快被开发成功。
在当时,平炉炼钢的操作和控制较空气转炉炼钢平稳,能适应用于各种原料条件,铁水(生铁)和废钢的比例可以在很宽的范围内变化。
--------1899年电弧炉炼钢方法也被发明成功。
在20世纪50年代氧气顶吹转炉炼钢法发明前,平炉是世界上最主要的炼钢法。
20世纪50年代氧气顶吹转炉炼钢技术和钢水浇铸开始推广采用的连铸工艺对后钢铁工业的发展起到了非常重要的推动作用。
1952年氧气顶吹转炉炼钢方法,在奥地利被发明成功。
(具有反应速率快、热效率高以及产出的钢的质量好、品种多等优点,该方法迅速被日本和西欧采用)。
在20世界70年代,顶吹转炉炼钢法已经取代平炉法成为主要的炼钢方法。
在顶吹转炉炼钢法迅速发展时,德、美、法等国成功发明了氧气底吹转炉炼钢法,该方法通过喷吹甲烷、重油、柴油等对喷口进行冷却,使纯氧能从炉底吹入熔池不致损坏炉底。
20世纪80年代中后期,西欧、日、美等相继开发成功了顶底复吹氧气转炉炼钢方法,在此法中,氧气由顶部氧枪供入,同时由炉底喷口吹入氩、氮等气体对熔池进行搅拌(也可吹入少部分氧气)。
顶底复吹氧气转炉炼钢既具备顶吹转炉炼钢化渣好、废钢用量多的长处,同时又兼备氧气底吹转炉炼钢熔池搅拌好、铁和锰氧化损失少、金属喷溅少等优点,因而目前世界上较大容量的转炉绝大多数都采用了顶底复吹转炉炼钢工艺。
液态金属连续浇铸专利在1886年就已经问世,在1937年德国人S.Junghans发明成功振动式连铸结晶器而大大减少了拉坯漏钢事故后,连铸开始在有色金属工业中被采用。
1954年,I.M.D、Halliday开发成功了连铸结晶器“负滑脱”振动技术,这使得拉漏率被进一步大幅度减少,连铸开始在钢水浇铸中被采用。
与模铸相比,连铸在节约投资、节能以及提高钢的收得率、产量和质量等方面具有明显的优势。
20世纪70年代后,西欧多国和日本的钢铁工业开始大规模采用连铸,至20世纪80年代,世界连铸比率超过模铸,至20世纪80年代末,连铸在日、欧、韩等钢铁发达国家连铸比均超过90%,。
目前,我国钢铁工业的连铸比也超过94%。
连续铸钢技术的采用不仅完全改变了旧的铸钢工序,还带动了整个钢铁厂的结构优化,因此,被许多冶金学家称之为钢铁工业的一次“技术革命”。
由于连铸生产节凑快,为了适应连铸,必须缩短炼钢冶炼时间。
传统炼钢工序功能被进一步分解,铁水预处理、电炉短流程、钢水炉外精炼等重要新技术因此而快速发展。
钢水预处理最初主要用于冶炼少数高级钢或用于高硫铁水辅助脱硫,脱硫剂最初主要使用镁焦、二碳化钙等,随后开发成功向铁水内喷吹氧化钙二碳化钙、Mg等进行铁水脱硫。
20世纪80年代日本钢铁厂开始大规模采用铁水“三脱”预处理(脱硅、脱磷、脱硫),在高炉出铁沟喷吹氧化铁和CaO进行脱硅,在铁水罐或混铁车内喷粉进行脱硫和脱磷处理。
90年代中期以后,日本钢铁厂又开始利用转炉对铁水进行脱磷处理。
采用铁水“三脱”预处理和钢水炉外精炼后,转炉炼钢功能被简化为“钢水的脱碳和提温容器”,炼钢转炉吹炼时间减少至912分钟。
此外,炼钢产生的炉渣量也显著减少,这大幅度减轻了炼钢生产的环境负荷。
传统旧式电弧炉炼钢时间长达46小时,采用连铸后,电炉冶炼时间必须缩短以与连铸节凑相匹配。
现代化的电弧炉炼钢采用了超高功率电弧炉、利用余热预热废钢、氧燃助熔等技术,电弧炉冶炼功能也由传统的溶化、脱碳、脱磷、脱硫、脱氧等简化为溶化和脱碳升温,冶炼时间缩短至4060分钟。
与氧气转炉炼钢工艺相比,电弧炉炼钢具有建设投资少、流程短、劳动生产率高、CO2排放量少等优点。
近年来电弧炉炼钢工艺发展很快,在美国、意大利等国,电弧炉炼钢生产量已经超高氧气转炉炼钢产量。
20世纪50年代中、后期,DH、RH等钢水炉外精炼方法被开发成功,最初主要用于高级钢的脱气(脱除氢、氮)精炼处理。
20世纪70年代后,尤其是钢铁工业大规模采用连铸技术后,钢水炉外精炼技术获得了迅速发展,精炼方式包括了吹氩搅拌、喂线、氩氧精炼、电炉加热、真空处理等多种方式,功能则由最初的钢水脱气发展为加热升温、渣钢精炼脱硫和脱氧、超低碳钢脱碳、成分微调、去除夹杂物等多种功能。
目前,现代化钢厂钢水炉外精炼比例已接近百分之百,原先由转炉和电炉炼钢承担的脱硫、深度脱碳、脱氧、合金化、夹杂物控制等转为主要由钢水炉外精炼工序承担。
炼钢学科的起步和发展要晚于炼钢生产。
在19世纪中期近代钢铁冶金方法发明成功后的相当长一段时间里,钢铁冶金仍是一项技艺而不是科学。
钢铁冶金从技艺发展为科学,是从20世纪30年代德国人H.Schenck、美国人J.Chipman等把化学热力学导入到冶金领域,用热力学方法研究冶金反应开始的。
20世纪40年代末至50年代,Schenck、Chipman等发表了大量有关炼钢反应的平衡常数、标准自由能变化等基础数据。
后来又有很多人做了大量的研究和测定工作。
至20世纪80年代后,与炼钢化学反应有关的标准自由能化、钢液中组元活度相互作用系数、炉渣主要组元的活度、炉渣硫酸盐和硫酸盐容量等大都有了较为可靠的热力学数据。
与热力学相比,有关炼钢反应动力学的研究开始得较晚。
在20世纪5060年代,动力学方面的研究主要集中在微观动力学方面,如化学反应级数、反应速度常数、反应活化能、多相反应限制性环节等方面的研究。
20世纪70年代后,单纯微观动力学理论已远远不能适应炼钢工艺技术发展的要求,对炼钢反应宏观动力学的研究(炼钢反应器内流动、混合、扩散、传热等)开始活跃起来。
G.H.Geiger、Szekely等将化工学科的“三传”(热量传递、质量传递、动量传递)用于分析研究冶金过程的速率问题,鞭岩、濑川清等提出了冶金反应工程学的名称,并引入化学反应工程学有关反应器设计、单元操作、最优化等方法来分析研究冶金反应问题。
20世纪90年代后,冶金反应宏观动力学和反应工程学取得了重要进展,有关炼钢冶炼和连铸过程流体流动、传热、反应等均基本可以用数学模型加以描述并计算求解。
除冶金热力学、动力学外,炼钢学科进展还表现在冶金知识与材料、计算机、电磁、环境等学科知识的交叉、融合和应用上。
如在氧气喷头和喷粉冶金中应用空气动力学中可压缩流体和气相输送等知识,在冶炼过程控制中广泛采用了声学、图像识别、专家系统、神经元知识,在连铸过程采用电磁、金属压力加工等知识。
预计在今后相当一段时间内,炼钢热力学不好再有显著的
发展,但在宏观动力学和反应工程学方面还会有一定的发展,而炼钢学科最重要的发展将会在液态的凝固加工、减少排放、排放物和废弃物再回收利用以及与信息、材料、环境等学科知识的交叉、融合和应用方面。
历经150多年的发展历程,钢铁工业已成为高度成熟的产业。
但是,钢铁工业在科技进步方面仍面临着很大的压力,这主要表现在:
1.要求有更高的生产效率。
钢铁冶金生产过程大量消
耗原材料和能源,从生态环境和可持续发展方面考虑,必须对现有生产工艺流程进行改进以提高效率,降低消耗。
2.要求产品具有更高性能。
钢铁材料目前面临其他材料的激烈竞争,以汽车为例,目前已先后制造出“全铝”汽车和“全塑”汽车。
进一步提高钢材性能的重点是要提高钢材的强韧性以及抗疲劳破坏和抗腐蚀性能。
3.要求对环境更加友好。
这就是要求尽量减少废弃炉渣、烟尘、NOx、SOx、CO2的排放,并利用冶金工艺过程处理废弃钢铁、塑料、城市垃圾等。
钢铁工业面临的科技进步压力是钢铁冶金学科继续向
前发展的前提和动力,而钢铁冶金学科的发展反过来又会极大地促进钢铁冶金技术的进步。
近20年来,中国钢铁工业取得了令人瞩目的发展,1996年中国钢产量超过1亿t,成为世界第一产钢国,201*年钢产量达到2.72亿t,产量超过居世界钢产量第二、三位的日本和美国钢产量的总和。
除钢产量外,中国钢铁工业在装备、工艺技术水平和钢材品种质量等方面也取得了显著的进步,已达到或接近国际先进水平。
中国钢铁工业对国民经济的快速发展起到了重要的支持作用,但目前在整体生产效率、能耗、高级产品性能、环境保护、重要技术研发能力等方面与发达国家相比还存在差距。
今后,中国钢铁工业还将会有更大的发展,而随着钢铁工业的不断发展,中国也将会成为世界钢铁科学研究和教育的中心之一。
二、炼钢基本反应
刚和铁都以铁元素为基本成分,铁又被称为生铁。
由于含碳量的不同,导致组织结构不同,在性能上产生了较大的差异。
高炉以及其他方法生产的铁含碳量高,硬而脆,冷热加工性能差,因而必须经再次冶炼才能得到良好的金属特性。
一般情况下,把含碳量低于2.11%
的铁碳合金称为钢,但绝大多数的实用钢种含碳量都低于1.2%。
铁中除了含有较高的碳之外,还含有其他元素,如Si、Mn、P和S等,其中P和S对大多数钢种来说是有害杂质元素。
为了得到具有高的强度和韧性或其他特殊性能的钢,需要通过冶炼降低生铁中的碳,去除有害杂质P和S,脱除冶炼过程中作为氧化剂使用而残留在钢水中的氧及混入液态钢水中的氮和氢,再根据对钢性能的要求加入适量的合金元素,最后脱除各种杂质元素在钢水中生成的或卷入的夹杂物颗粒。
由于钢水中杂质元素含量在冶炼过程中不断减少,钢水的熔化温度随之提高,因此为保证得到合乎成分要求的钢水并最终能够铸造成为理想形状的铸坯或钢锭,炼钢过程中要把钢水温度提高到合适的程度。
综上所述,炼钢过程的基本任务可以概括为以下9项:
1.脱碳;2.脱磷;3.脱硫;4.脱氧;5.脱氮、氢等;6.去除非金属夹杂物;7.合金化;8.升温;9.成型凝固。
完成这些基本任务的方法在本书中逐一进行论述。
炼钢炉内的主要反应:
121302(g)=[0]ΔG=-111700-6.78TJ/mol
Fe2O3=Fe(L)+[O]ΔG=-159300-88.62TJ/mol
32[0]+[c]→CO(G)[0]+[Si]→(Si02)[0]+[Mn]→(MnO)5[0]+2[P]→(P205)(Ca0)+[s]→CO(G)
热源氧化剂铁水生铁废钢钢水炼钢炉1823~1923K钢渣造渣剂图1炼钢过程示意图
长流程与短流程现代炼钢工艺主要的流程有两种,即:
以氧气转炉炼钢工艺为中心的钢铁联合企业生产流程和以电炉炼钢工艺为中心的小钢厂生产流程。
通常人们习惯上把前者叫做长流程,把后者叫做短流程。
长流程工艺就是:
从炼铁原燃料准备开始,原料入高炉冶炼得到液态铁水,高炉铁水经过铁水预处理(或不经过)入氧气转炉吹炼,再经二次精炼(或不经过)获得合格钢水,钢水经过凝固成型工序(连铸或模铸)成坯或锭,再经轧制工序最后成为合格钢材。
由于这种工艺流程生产单元多,规模庞大,生产周期长,因此称此工艺流程为钢铁生产的长流程工艺(见图2)。
可入炉矿、球团、烧结矿高炉混铁矿转炉模铸均热炉初轧机/开坯机加热炉二次成型焦炭铁水预处理辅料2冷处理加热炉热轧机3转炉二次精炼连铸热处理加热炉热轧机4加热炉热轧机5角部加热热轧机6缓冲加热精轧机7
卷起装置图2高炉-转炉-轧钢流程(长流程)
1-模铸钢锭冷装轧制;2-连铸坯冷装炉轧制;3-连铸坯热送轧制;4-无缺陷连铸坯;直接热装炉轧制;6-连铸坯热送轧制;7-薄带连铸
短流程工艺就是:
将回收再利用的废钢(或其他代用料),经破碎、分选加工后,经预热直接加入电炉中,电炉利用电能作热源来进行冶炼,再经二次精炼,获得合格钢水,后续工序同长流程工序。
由于这种工艺流程简捷,高效节能,生产环节少,生产周期短,因此此工艺流程为钢铁生产的短流程工艺(见图3)。
又称“三位一体”流程(即由电炉-炉外精炼-连铸组成),或者“四个一”流程(即由电炉-炉外精炼-连铸-连轧组成)。
进入21世纪,在自然资源保有量不断锐减和环保状况日益恶化的背景下,社会更加关心人来今后的生存空间和可持续发展的战略问题。
因此,用全新的观点改造传统的工艺流程,已成为今后社会发展的必然要求。
根据资源的多样化,钢铁生产将来采用多种冶炼工艺,见图4
主原料:
废铁直接还原铁(DRI)热压块(HBI)生铁电炉精炼碳化铁粒铁热铁水等图3钢铁生产短流程工艺
现代钢铁生产工艺流程
连铸只送连休轧制铁矿石高炉熔融还原炉直接还原炉铁水直接还原铁废钢氧气转炉炉外精炼电弧炉精炼模铸连铸板坯/大方坯粗热轧棒材厚板开坯精热轧厚板坯连铸方坯、圆坯连铸薄板坯连铸薄带连铸冷轧薄板图421世纪钢生产的各种流程
冶炼方法(按炉别可分为):
平炉钢、转炉钢、电炉钢。
平炉钢是靠燃料(煤气或重油)的燃料来熔化炉料和提高钢液温度,靠炉气中的氧气和加入的铁矿石进行氧化反应。
(由于平炉钢消耗大量燃料,因此在我国已被淘汰。
)
转炉钢是把空气或氧气吹入铁液中,使铁液中的C、Mn、Si、P、S等迅速氧化,靠氧化时放出的热量来升温,而不靠燃料供热的炼钢方法。
转炉钢由于节省燃料,因而是目前主要的炼钢设备。
电炉钢是电能作为热源的炼钢方法。
电炉钢主要用来生产高质量的高合金钢。
冶金辅助原料
学科:
固体矿产工业要求词目:
冶金辅助原料
英文:
metallurgicalauxiliarymaterial
释文:
冶金辅助原料是冶金工业中用作熔剂和耐火材料的原料的总称。
用作熔剂的原料有石灰石、白云石、硅石、萤石、铁矾土等。
熔剂在冶金过程中用作造渣的配料。
有富含CaO、MgO的碱性熔剂;富含SiO2、Al2O3的酸性熔剂,分别用来提高炉料的碱度和酸度,使炉料冶炼时达到酸碱中和,渣铁分离,并用来增强炉渣的流动性,排除硫、磷杂质等。
用作耐火材料的有菱镁矿、耐火粘土、高铝粘土、白云石、硅石、高铝矿物原料(红柱石、矽线石、蓝晶石等)以及型砂等。
它们分别用来做炉壁、炉衬的酸性和碱性耐火砖、铸造模型等。
蓝晶石专用作不定型高级耐火材料。
[1]
展望:
我国近几年来,生产钢的总重量居世界第一,正在由钢铁生产大国向钢铁强国转变的时期。
能生产出高质量的钢材,又能节约资源,减少排放,是衡量一个国家的钢铁技术的重要参数,(如飞机、航母、坦克构架等高性能材料)。
要达到节能减排,就是要求我们的绿色制造,绿色设计中的思想方法尽量考虑产品的整个生命周期,考虑从生产产品的原料到产品使用完等回收利用问题,从而对每一道工序,尽量对其优化,从而使得整个产品不仅质量好,又能使得在生产的过程和产品的使用回收再利用等整个生命周期中最大限度的实现节能减排的目标。
炼铁
百科名片
高炉法将金属铁从含铁矿物(主要为铁的氧化物)中提炼出来的工艺过程,主要有高炉法,直接还原法,熔融还原法,等离子法。
炼铁liàntiě
[ironsmelting]将金属铁从含铁矿物(主要为铁的氧化物)中提炼出来的工艺过程,主要有高炉法,直接还原法,熔融还原法,等离子法。
高炉炼铁是指把铁矿石和焦炭,一氧化碳,氢气等燃料及熔剂(从理论上说把活动性比铁的金属和矿石混合后高温也可炼出铁来)装入高炉中冶炼,去掉杂质而得到金属铁(生铁)。
其反应式为:
Fe2O3+3CO=3CO2+2FeFe2O3+3H2=3H2O+2Fe2Fe2O3+3C=3CO2+4Fe元素个数右下标。
编辑本段
高炉炼铁原理简介:
高炉生产是连续进行的。
一代高炉(从开炉到大修停炉为一代)能连续生产几年到十几年。
生产时,从炉顶(一般炉顶是由料种与料斗组成,现代化高炉是钟阀炉顶和无料钟炉顶)不断地装入铁矿石、焦炭、熔剂,从高炉下部的风口吹进热风(1000~1300摄氏度),喷入油、煤或天然气等燃料。
装入高炉中的铁矿石,主要是铁和氧的化合物。
在高温下,焦炭中和喷吹物中的碳及碳燃烧生成的一氧化碳将铁矿石中的氧夺取出来,得到铁,这个过程叫做还原。
铁矿石通过还原反应炼出生铁,铁水从出铁口放出。
铁矿石中的脉石、焦炭及喷吹物中的灰分与加入炉内的石灰石等熔剂结合生成炉渣,从出铁口和出渣口分别排出。
煤气从炉顶导出,经除尘后,作为工业用煤气。
现代化高炉还可以利用炉顶的高压,用导出的部分煤气发电。
编辑本段高炉炼铁流程
高炉冶炼是把铁矿石还原成生铁的连续生产过程。
铁矿石、焦炭和熔剂等固体原料按规定配料比由炉顶装料装置分批送入高炉,并使炉喉料面保持一定的高度。
焦炭和矿石在炉内形成交替分层结构。
高炉冶炼工艺--炉前操作:
一、炉前操作的任务
1、利用开口机、泥炮、堵渣机等专用设备和各种工具,按规定的时间分别打开渣、铁口,放出渣、铁,并经渣铁沟分别流人渣、铁罐内,渣铁出完后封堵渣、铁口,以保证高炉生产的连续进行。
2.完成渣、铁口和各种炉前专用设备的维护工作。
3、制作和修补撇渣器、出铁主沟及渣、铁沟。
4、更换风、渣口等冷却设备及清理渣铁运输线等一系列与出渣出铁相关的工作。
高炉基本操作制度:
高炉炉况稳定顺行:
一般是指炉内的炉料下降与煤气流上升均匀,炉温稳定充沛,生铁合格,高产低耗。
操作制度:
根据高炉具体条件(如高炉炉型、设备水平、原料条件、生产计划及品种指标要求)制定的高炉操作准则。
高炉基本操作制度:
装料制度、送风制度、炉缸热制度和造渣制度。
[高炉设备]高炉:
横断面为圆形的炼铁竖炉。
用钢板作炉壳,壳内砌耐火砖内衬。
高炉本体自上而下分为炉喉、炉身、炉腰、炉腹、炉缸5部分。
由于高炉炼铁技术经济指标良好,工艺简单,生产量大,劳动生产效率高,能耗低等优点,故这种方法生产的铁占世界铁总产量的绝大部分。
高炉生产时从炉顶装入铁矿石、焦炭、造渣用熔剂(石灰石),从位于炉子下部沿炉周的风口吹入经预热的空气。
在高温下焦炭(有的高炉也喷吹煤粉、重油、天然气等辅助燃料)中的碳同鼓入空气中的氧燃烧生成的一氧化碳和氢气,在炉内上升过程中除去铁矿石中的氧,从而还原得到铁。
炼出的铁水从铁口放出。
铁矿石中未还原的杂质和石灰