液态硫酸铵转鼓造粒复合肥节能改造项目可行性研究报告.docx
《液态硫酸铵转鼓造粒复合肥节能改造项目可行性研究报告.docx》由会员分享,可在线阅读,更多相关《液态硫酸铵转鼓造粒复合肥节能改造项目可行性研究报告.docx(80页珍藏版)》请在冰豆网上搜索。
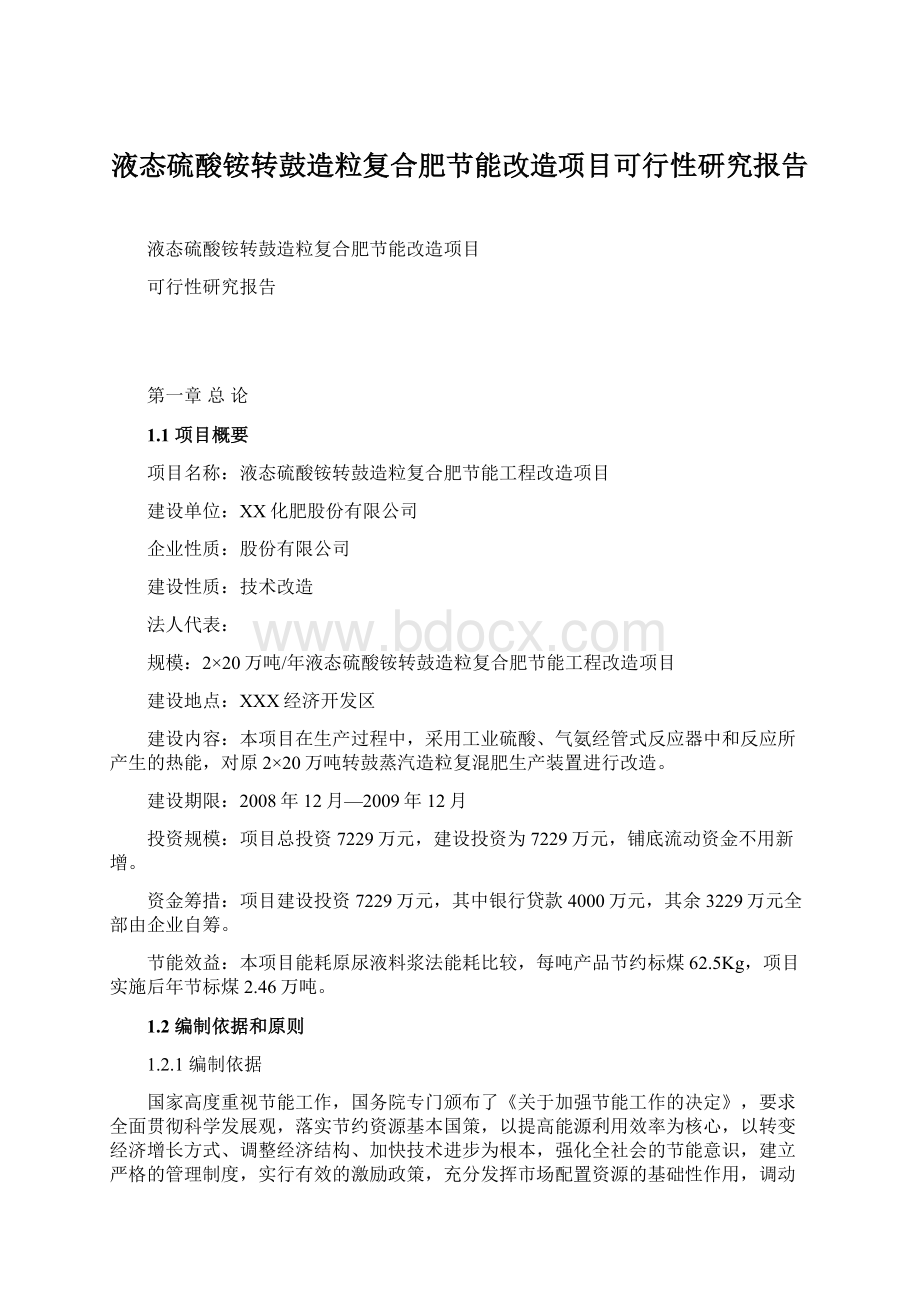
液态硫酸铵转鼓造粒复合肥节能改造项目可行性研究报告
液态硫酸铵转鼓造粒复合肥节能改造项目
可行性研究报告
第一章总论
1.1项目概要
项目名称:
液态硫酸铵转鼓造粒复合肥节能工程改造项目
建设单位:
XX化肥股份有限公司
企业性质:
股份有限公司
建设性质:
技术改造
法人代表:
规模:
2×20万吨/年液态硫酸铵转鼓造粒复合肥节能工程改造项目
建设地点:
XXX经济开发区
建设内容:
本项目在生产过程中,采用工业硫酸、气氨经管式反应器中和反应所产生的热能,对原2×20万吨转鼓蒸汽造粒复混肥生产装置进行改造。
建设期限:
2008年12月—2009年12月
投资规模:
项目总投资7229万元,建设投资为7229万元,铺底流动资金不用新增。
资金筹措:
项目建设投资7229万元,其中银行贷款4000万元,其余3229万元全部由企业自筹。
节能效益:
本项目能耗原尿液料浆法能耗比较,每吨产品节约标煤62.5Kg,项目实施后年节标煤2.46万吨。
1.2编制依据和原则
1.2.1编制依据
国家高度重视节能工作,国务院专门颁布了《关于加强节能工作的决定》,要求全面贯彻科学发展观,落实节约资源基本国策,以提高能源利用效率为核心,以转变经济增长方式、调整经济结构、加快技术进步为根本,强化全社会的节能意识,建立严格的管理制度,实行有效的激励政策,充分发挥市场配置资源的基础性作用,调动市场主体节能的自觉性,加快构建节约型的生产方式和消费模式,以能源的高效利用促进经济社会可持续发展。
XX化肥股份有限公司为节约能源,降低生产成本,采用氨酸法转鼓造粒及液态氯化铵粘结团粒工艺,对原2×20万吨转鼓蒸汽造粒复混肥生产装置进行改造,对原装置进行节能技术改造,在传统的转鼓造粒复混肥生产装置上开发出氯基复合肥新产品。
该项目采用氨酸法转鼓造粒工艺,充分利用工业硫酸、气氨经管式反应器中和反应产生的热能,达到节能降耗的目的,符合国家发改委《关于组织申报2009年资源节约和环境保护备选项目的通知》的节能方面中“能量系统优化(系统节能)”的要求,也符合《产业结构调整指导目录(2005年本)》“化工”类第三条“优质磷复肥、钾肥及各种专用复合肥生产”的要求,项目建设是必要的。
1.2.2编制原则
⑴本可行性研究报告编制的内容和深度按照中国石油和化学工业协会《化工投资项目可行性研究报告编制办法》(中石化协产发(2006)76号)。
经济评价参照国家发改委、建设部《关于印发建设项目经济评价方法与参数的通知》文件(发改投资[2006]1325号)。
⑵坚持勤俭建厂的方针和实事求是的原则,项目改造所用的技术应成熟、可靠,节约能源,降低原材物料消耗,保证产品质量,增加企业经济效益。
⑶本着“立足实际,优化工艺,留有余地”的原则,在设计中充分考虑利用国产设备,同时结合国内类似项目的实践经验进行设计建设,节省投资。
⑷充分依托现有的公用工程及生活设施潜力,减少储运、机修和车辆等方面的投资。
⑸重视劳动安全卫生和“三废”治理,改造工程与环保、安全和公共卫生设施同时考虑,消除“三废”对环境造成的不利影响。
⑹贯彻“工厂布置一体化,生产装置露天化,建(构)筑物轻型化,公用工程社会化,引进技术国产化”五化的设计原则。
1.3研究范围
本可行性研究工作的范围是对拟建项目的建设意义、建设条件、技术路线、环境影响、实施计划、经济效益等方面是否可行加以论证,以提供准确的资料和数据,并对拟建项目是否应该建设和如何建设做出论证和评价,以作为项目决策的依据和为下一步的项目运作提供依据。
1.4研究的主要过程
项目主办单位对自身的技术改造条件进行了研究后,对目前国内同行业节水技术、设备等情况进行了调查,经向有关领导汇报和请示,按要求决定对本项目开展可行性研究阶段的工作。
项目主办单位委托淄博市工程咨询院进行项目可研工作,并提供了有关的基础资料。
淄博市工程咨询院对本项目所涉及的相关问题进行了认真的、有重点的调研和分析,对项目建设在经济上的必要性与合理性、技术和设备的先进性、可靠性与适用性、财务上的盈利性与可行性、环境和建设上的可容纳性和可实施性等进行了详细的比较论证,同时对项目的建设、生产和经营进行风险分析、并适当留有余地。
1.5研究结论
该项目在原2×20万吨转鼓蒸汽造粒复混肥生产装置上进行技术改造,在生产过程中采用工业硫酸、气氨经管式反应器中和反应所产生的热能和转鼓造粒工艺,利用液态硫酸粘结成粒,不需加入蒸汽,大幅度减轻了烘干负荷,洗涤水循环使用,生产出颗粒外观光滑圆润,不易结块的氯基复合肥,节能效果显著,在同类复合肥生产工艺中具有明显的绝对优势;同时能够大幅度降低生产成本,对于企业抗拒金融危机的冲击,为农民提供价廉质优的复合肥,具有明显的经济效益、社会效益和广泛的推广使用价值。
目前,该项目工艺技术经临沂市科技查新:
“在国内未发现与本项目研究内容相关的文献和技术主要创新点有相同的报告”(见附件);2008年12月,XXX省科技厅组织国内著名复合肥专家鉴定认为“该项目节能效果显著,设备改造合理,质保体系完善,技术达到国内领先水平”(见附件)。
1.6主要技术经济指标
表1.6主要技术经济指标
指标名称
单位
指标
备注
项目年综合节能量
万吨标煤
2.46
其中:
节水
万吨
8
节约煤炭
万吨
2.36
节约电力
万kWh
1120
节约蒸汽
万吨
4.4
减少污染:
年SO2减排量
吨
300
项目投资
万元
7229
其中:
建设投资
万元
7111
建设期利息
118
年节约支出
万元
2120
年固定成本增加
万元
833
效益总额
万元
1219
计算期平均
财务内部收益率
%
24.04
所得税后
%
19.16
所得税前
财务净现值
万元
5602
所得税后
万元
3739
所得税前
总投资收益率
%
17.24
资本金利润率
%
38.61
投资回收期(含1年建设期)
年
5.33
所得税后
年
4.70
所得税前
借款偿还期
年
3.00
含1年建设期
第二章项目建设背景
2.1项目法人基本情况
XX化肥股份有限公司属股份制企业,现拥有总资产11亿元,职工1976人,工程技术人员795人,公司占地1062亩,形成了年产220万吨的复混(合)肥生产规模,其中20万吨/年复合(混)肥生产装置线6套、20万吨/年和40万吨/年塔式熔体造粒复合肥生产装置各1套。
2004年10月,公司成功建成投产了我国第一条年产20万吨高塔熔体造粒复合肥生产线,其工艺、技术、质量指标达到国际同行业先进水平,2006年4月又投资2.6亿元建设了年产100万吨的双塔熔体造粒缓释复合肥生产装备。
在此基础上2008年6月XX化肥股份有限公司又投资8200万元开工建设了年产60万吨两步氨化法硫酸钾复合肥节能改造工程。
该公司产品畅销全国28个省区600多个县市,出口日本、朝鲜、韩国、马来西亚等国家。
2008年公司实现销售收入23亿元,利税1.6亿元,其中上交税收4135万元,净资产60872万元,资产负债率45.3%。
公司先后通过了IS09001质量体系认证和IS014001环境管理体系认证,荣获农业部全面质量管理达标单位、全国消费者满意产品、农业产业化龙头企业、省级重合同守信用企业、XXX省农行“AAA”级信用单位、XXX省消费者满意单位、XXX省技术创新示范企业等荣誉称号。
在全国科研成果实用技术新产品展示会上复合肥项目荣获重大科技创新项目,高浓度复合肥被评为XXX省企业创新一等奖。
公司研究开发机构被XXX省经贸委认定为“XXX省企业技术中心”,国家知识产权局授权了“两步氨化法新型硫酸钾复合肥”和“生物腐植酸复合肥”两项发明专利,2007年9月被科技部认定为“国家重点高新技术企业”。
我公司复合肥产品在国家技术监督局的历次抽查中均为合格产品,2005年10月又被XXX省工商行政管理局评为“XXX省著名商标”,被XXX省质量技术监督局评为“XXX省名牌”,2007年9月还被国家工商总局授予“中国驰名商标”称号。
先后荣获获中国石油和化学工业协会技术发明三等奖、XXX省第九届专利发明三等奖,2007年12月被国家科技部、商务部、质量监督检验检疫总局、环保总局四部委联合认定为国家重点新产品。
本项目工艺技术研究于2008年12月通过了XXX省科技厅组织的专家鉴定,为国内领先水平。
2.2项目建设的目的、意义和必要性
随着我国资源节约型、环境友好型企业建设步伐的顺利推进,复混(合)肥产业面临着新的发展趋势,主要体现在整合资源、节能降耗、提高产品科技水平等产业可持续发展的核心领域。
XX化肥股份有限公司为节约能源,降低生产成本,采用氨酸法转鼓造粒及液态硫酸铵粘结团粒工艺,对原装置进行节能技术改造,在传统的转鼓造粒复混肥生产装置上开发出氯基复合肥新产品。
该项目具有投资省,改造工期短,效果好,可大大提高该装置的生产能力和产品质量,降低能源消耗,同时“三废”排放污染物经处理后达到国家相关标准要求。
该项目生产的复合肥成本低于同等养分的复混肥或复合肥生产成本,具有显著的经济、环境和节能效益。
通过该项目的实施,可提高传统的复混肥生产装备的技术水平,促进复混(合)肥行业的科技创新能力的发展。
该项目的实施具有一定的现实意义和较强的示范、推广、应用价值。
在工业生产中,传统的蒸汽造粒复合肥造粒能耗大,污染较重,是节能改造的重点行业,同时也是复合肥生产企业面临的生死存亡的重大问题。
当前,我国复合肥生产企业都在致力创造和谐统一的生产环境,推进化肥工业结构调整和重组,加大节能降耗及环境保护新技术、新装备投入,降低能源销耗,改革生产工艺,促进生产工艺路线多元化,提高资源再生综合利用的水平。
因此该项目的建设符合我国节约资源,环境保护基本国策的需要。
我国是一个化肥生产和消费大国,随着我国经济的快速增长和社会发展,党和国家对“三农”问题更加重视,化肥的需求量持续增加,复合肥产业已成为支撑我国农业发展的重要条件。
因此国家制定出台了一系列相关政策,把化肥列为优先发展主题。
但是进入二十一世纪,国际能源趋于紧张,石油价格一路飙升,生物能源应运而生,大量粮食被加工成燃料乙醇,造成了世界粮食紧张,导致化肥使用量猛增,价格上涨。
我国虽然高度重视“三农”问题,粮食储备足,价格稳定,但受国际基础化肥原料价格影响,化肥生产成本居高不下,市场销售价格迅速增长,增加了农业生产成本,一定程度上挫伤了农民种粮积极性。
因此,国内化肥生产企业适应市场环境,满足市场需求,降低化肥生产成本势在必行。
目前,受国际金融危机的冲击,复合肥产品市场和原料价格极不稳定,生产复混(合)肥所用原料氮肥和磷肥的价格在短短的2个月内就完成了从历史上的巅峰期跌落到6年来的谷低,尤其是生产磷肥的原料硫酸所用硫磺,近期国际交易价格每吨从800美元骤跌到60美元,国内工业硫酸也从每吨1200元(人民币)跌落到目前的每吨280元(人民币)。
因此采用硫酸、液氨生产复混(合)肥成本低,利润空间大,经济效益好,能够较好的抗御金融危机的冲击。
2.3国内复合肥生产现状
目前国内外复合肥的生产方法主要有:
料浆法、团粒法、挤压法、掺混法和熔体法等,且以上几种方法都比较成熟,均建有不同规模的生产装置。
熔体法造粒工艺,我国从1997年起开展熔体造粒法制备高浓度尿基复合肥技术的研究,科研人员先从尿基复合肥料的理化性质,混合反应机理,熔体料浆性质等多方面进行研究,取得了突破性的进展,获得了一系列工艺和技术参数。
在此基础上,XX化肥股份有限公司在国内率先建设了2套累计年产100万吨的单塔和双塔熔体造粒工艺的复合肥生产装置。
并在该装置上研究开发高氮基质复合肥与生物抑制剂缓释控释复合肥料,经XXX省科技厅组织的专家鉴定达到国际先进水平。
为节能降耗,实现创新发展,该公司将在原2×20万吨转鼓蒸汽造粒复混肥生产装置进行改造生产氯基复合肥新产品,已通过省级鉴定,其工艺技术达到国内领先水平。
XX化肥股份有限公司液态硫酸铵转鼓造粒复合肥节能工程改造项目,充分利用工业硫酸、气氨经管式反应器中和反应所产生的热能,对原2×20万吨转鼓蒸汽造粒复混肥生产装置进行改造,节约能源消耗,提高产品的质量和技术含量,能够使企业实现节能、高效运转,降低生产成本,使企业产生良好的经济效益。
项目改造后,能够节省大量煤炭资源,实现清洁生产,“三废”排放达到国家相关标准要求。
综上所述,该项目的建设能够实现经济、环境和社会三方面协调持续,具有很强的推广意义。
第三章项目改造内容及及前期工作情况
3.1装置改造前情况
3.1.1原生产工艺流程
蒸汽
氯化钾尿素磷一铵氯化铵上料
一级烘干机
一级冷却机
造粒机
返料
筛分机
二级冷却机
筛分机
包装入库
二级烘干机
烟筒
除尘室
风机
除尘室
项目实施前年产20万吨蒸汽造粒复合肥工艺流程图
工艺流程说明:
工艺采用滚筒蒸汽物理团粒法造粒,来自蒸汽总管的蒸汽,来自上料工段的尿素、氯化铵、磷酸一铵、氯化钾、中量及微量元素、添加料经计量后与系统返料一起在造粒机内团聚造粒,经皮带机及斗提机输送、进入一级烘干机烘干及一级冷却机冷却;冷却后去粗级筛分筛分下大颗粒,再经细级筛分筛分下小颗粒及粉子后去二级烘干机烘干及二级冷却机冷却。
经二级冷却机冷却后的中颗粒进入精品筛筛分,筛面上的物料作为成品经包膜机包膜进行防结块处理,处理后去自动包装机包装,包装后去成品库作为成品出售。
粗级筛分筛分下的大颗粒返料经粉碎机粉碎后,同细级筛分筛分下的小颗粒、粉子及精品筛筛分下的粉子一起返回造粒机头部,作为系统返料在造粒机内团粒。
一级烘干机、一级冷却机、二级烘干机、二级冷却机的尾气通过除尘室,风机加压,,经30米烟囱放空。
系统所需添加剂由磨粉工段提供,石块经鄂式破碎机破碎后,经雷蒙磨磨碎,磨碎后去二级旋风除尘收集细粉,供生产车间使用。
3.1.2原工艺需要解决的问题
原工艺的返料比为1.8~2.2:
1,造粒机出口水分8%,用黏性添加剂造粒,与国内同行业相比,居于上游水平;国内同行业返料比为2~3:
1。
黏性添加剂的加入只是增加造粒过程的黏性,提高成品率,对肥效无帮助。
返料比的降低,可减少吨成品需要烘干的物料总量,相应增大产量,降低消耗。
造粒机出口水分的降低,可减少吨成品烘干需要的燃煤量。
在同一配比情况下,造粒机出口水分的降低,靠造粒温度的升高来实现。
在同一造粒温度情况下,造粒机出口水分的降低,靠合理配比来实现。
工艺上的节能,靠降低返料比,降低造粒机出口水分,不用或少用添加剂来实现。
通过蒸汽冷凝水余热回收利用,二次蒸汽等压回收节能措施来节煤。
调整锅炉及热风炉燃烧状况,使一次燃烧室及二次燃烧室燃烧充分,采用炉渣分拣混烧,合理控制原煤颗粒度,煤层厚度,合理控制原煤的低位发热值,实行掺烧工艺,烟道尾气余热回收,用热风设备全部保温等节能措施来节煤。
原工艺需要解决的问题,可通过以上节能措施途径来实现。
3.1.3项目实施前设备节能需要完善的问题
项目实施前风机为4-73型普通风机,风机效率只有60-70%,提高风机效率成为风机节能的重点。
主要耗电设备应用变频调速器,节能电机,超过37KW的电机实行降压启动成为节电的重点。
加强热风炉及锅炉炉体保温措施。
3.1.4项目实施前公用工程概况
1、给排水
该公司目前用水主要为生产和生活用水,生产用水为蒸汽冷却水,日用量约90吨,日最大用水量约150吨。
生产用水由市政自来水单路供水系统接入,并根据生产工艺要求进行相应的处理。
直接冷却水和间接冷却水系统设有循环水池,通过水泵房供给各车间使用。
厂区给水为生产、生活与消防合用一套给水管网。
厂区排水采用雨污分流系统。
所排生活用水经过化粪池进行初级预处理后,通过厂内污水管道与车间所排生产废水一道排入自建污水处理厂进行处理,然后达标排放。
2、供电
负荷等级:
本项目生产设备用电负荷按三级;办公、生活用电均属三级负荷;消防用电负荷属二级负荷,采用充放电式电源箱作为备用电源。
电压等级选择:
外部供电电压为10千伏,车间用电负荷为380/220电压的设备,配电室降压后用380/220伏三相四线系统向生产车间供电。
车间配电系统:
变压器的低压侧耳母线分段运行并设有联络开关,保安电源接于低压母线,其开关与正常供电的变压器低压侧总开关设有联锁,生产车间动力照明各用一线,配电室设置单独照明配电盘供生活用电。
动力及照明:
电气车间和公用设施配电、动力、照明共用一个电源,三相四线制,动力干线380伏,三相三线制供电,采用铜芯全塑电缆穿管暗敷,支线用电缆或绝缘导线穿管暗敷,局部地方选用电缆桥架敷设。
车间使用双管防爆日光灯,厂区及生活等其它照明为白炽灯。
3、供汽
生产用汽使用公司根据产量选型10t自备锅炉,能够满足生产需要。
3.1.5主要能耗设备
XX化肥股份有限公司主要耗能设备见下表
表3.1主要能耗设备
序号
分段工程名称
设备清单
设备规格
数量
(台)
设备功率(KW)
1
造粒烘干工段
造粒机
∮2800×8000
2
55×2
一级烘干机
∮2800×28000
2
90×2
一级冷却机
∮2400×24000
2
55×2
二级干燥机
∮2200×22000
2
45×2
二级冷却机
∮1800×18000
2
37×2
包膜机
∮1800×6000
2
22×2
滚筒筛
∮2400×7000
4
90×2
精品振动筛
2200×5000
2
3×2
卧式破碎机
PCH8065
2
100×2
立式破碎机
XLP-1000
6
55×2
皮带秤
B1000
2
5.5×2
包装机
DCS50/B2
4
2.2×2
空压机
0.7-7
2
15×2
包膜泵
2
2.2×2
包膜槽
∮1000×1000
2
2.2×2
螺旋喂料机
∮133×3000
2
1.1×2
搅拌机
∮3200×800
4
90×2
一烘热风炉
560万大卡/小时
2
18.6×2
二烘热风炉
320万大卡/小时
2
12.1×2
斗提机
TH800-TH1000
8
118×2
一烘风机
14D
2
90×2
一冷风机
12D
2
55×2
二烘二冷风机
10D
4
74×2
造粒风机
6D
1
15×2
2
电器系统
变压器
总1800
2
控制柜2台
3
仪表系统
自动调节系统2台套
上料自控调节系统
1
蒸汽自控调节系统
1
测温测压表
4
控制柜2台
4
锅炉岗位
10吨锅炉
1
62.7×2
总计
2231.2
3.1.6主要耗能分析
从主要耗能设备表可以看出,耗电的主能耗设备为烘干机、冷却机、风机、粉碎机;耗煤的主能耗设备为一烘热风炉、二烘热风炉、10吨锅炉;耗蒸汽的主能耗设备为造粒机。
原工艺采用滚筒蒸汽物理团粒法造粒,吨耗电40度,吨耗原煤71公斤,吨耗蒸汽130公斤,吨耗一次水0.24m3,
本公司原工艺吨消耗与国内同行业吨消耗相比居于中游,国内同行业吨耗电38-56度,吨耗原煤68-96公斤,吨耗蒸汽130-160公斤,吨耗一次水0.2-0.4m3。
3.2项目改造内容
本项目采用工业硫酸、气氨经管式反应器中和反应、转鼓造粒工艺对原有2×20万吨转鼓蒸汽造粒复混肥生产装置进行技术改造。
主要改造内容如下:
(1)采用“液态硫酸铵转鼓造粒复合肥工艺”对装置主要生产工序进行改造,需要改造造粒尾气吸收系统、供氨系统、供酸系统、造粒反应系统,需增强筛分系统、仪表控制系统、配电节能系统,同时改造一些辅助生产系统。
(2)采用变频调速器节能电机,对超过37KW的电机实行降压启动。
(3)对热风炉及锅炉炉体保温、一次燃烧室及二次燃烧室进行改造,实行掺烧工艺,采用炉渣分拣混烧,控制原煤颗粒度,对烟道尾气余热回收,同时对热风设备全部保温。
(4)对蒸汽冷凝水余热回收利用,蒸汽管道及蒸汽加热设备保温,余压利用,二次蒸汽等压回收等节能改造。
(5)通过直接节能措施的实施,本生产装置消耗已经降低,但降低幅度不太大,只降低了20%左右。
3.3前期工作准备
通过直接节能措施对原装置实施改造,能量消耗降低幅度不太大,只降低了20%左右。
要想获得大的节能空间,只有通过工艺的改进,为此该项目承办单位成立了科技攻关组,以降低返料比,提高产出率,降低电耗,降低蒸汽消耗,减少原料中填充料的使用为研究课题,攻克了“无水分引入液态硫酸铵转鼓造粒复合肥工艺”这一新课题。
“无水分引入液态硫酸铵转鼓造粒复合肥工艺”的研制成功可利用液氨与硫酸的反应热加热成蒸汽进行造粒,不用蒸汽或少用蒸汽造粒,节约蒸汽,减少煤耗;可减少了造粒机出口水分,降低了烘干能耗;可利用液态硫酸铵的黏性来提高成品率,省去原工艺中的黏性添加剂,省去加工黏性添加剂所需耗电;可提高造粒成品率,降低烘干负荷,提高产量,降低电耗,煤耗。
经过对“液态硫酸铵转鼓造粒复合肥工艺”这一节能工艺的效果分析,XX化肥股份有限公司决定实施本项目的建设。
第四章工艺技术方案
4.1改造工艺原理、设备、工艺数据分析和研究
4.1.1液态氨酸转鼓造粒复合肥生产原理分析和研究
液氨与硫酸中和反应。
浓硫酸经稀释后与定量的液氨在管式反应器中进行中和反应,生成硫酸铵料浆并放出热量,其化学反应式如下:
H2SO4(稀)+2NH3=(NH4)2SO4+Q
氯化钾、磷酸一铵、硫酸氨间的复分解反应及复盐生成。
从配料岗位输送到造粒机内的氯化钾和磷酸一铵在低温下可进行复分解反应生成磷酸二氢钾和氯化铵,但该反应在温度低时反应缓慢生成的磷酸二氢钾量相对较低,当硫酸与液氨进行中和反应放出大量的热量时,物料温度升高加速了其反应速度,同时液氨与硫酸进行中和反应生成的硫酸铵又与物料中的氯化钾发生复分解反应生成硫酸钾和氯化铵。
其化学反应式如下:
KCl+NH4H2PO4=KH2PO4+NH4Cl
(NH4)2SO4+2KCl=K2SO4+2NH4Cl
复盐固溶体的形成。
该物料中氯化钾和磷酸一铵发生复分解反应生成的氯化氨与原料中的氯化钾将形成氯化铵钾复盐固溶体[(NH4,K)Cl]。
硫酸与液氨进行中和反应生成的硫酸铵又与氯化钾复分解反应所产生的硫酸钾形成硫酸铵钾固溶体[(NH4,K)2SO4]。
氯化钾和磷酸一铵反应生成的磷酸二氢钾与原料中的磷酸一铵又形成磷酸铵钾固溶体[(NH4,K)H2PO4]。
这些固溶体将是该肥料的主要成分,并在造粒过程中起到成球作用。
其化学反应式如下:
(1~p)NH4Cl+pKCl=(NH4,K)Clp=0~1
(1~q)(NH4)2SO4+qK2SO4=(NH4,K)SO4q=0~1
(1~n)NH4H2PO4+nkH2PO4=(NH4,K)H2PO4n=0~1
4.1.2设备选择和研究
管式反应器。
传统的氨酸中和反应采用悬埋式双喷管法,生产中经常出现反应不完全造成局部物料粘结、赌塞等现象,影响物料的成球速率,而且悬管容易在高温下弯曲变形,阻挡物料导致酸管断裂,使氨酸中和反应受阻。
为保证硫酸与气氨的充分反应,该采取在造料机入口端安装