市政公路桥梁高架桥桩基后注浆施工试方案施工工艺.docx
《市政公路桥梁高架桥桩基后注浆施工试方案施工工艺.docx》由会员分享,可在线阅读,更多相关《市政公路桥梁高架桥桩基后注浆施工试方案施工工艺.docx(38页珍藏版)》请在冰豆网上搜索。
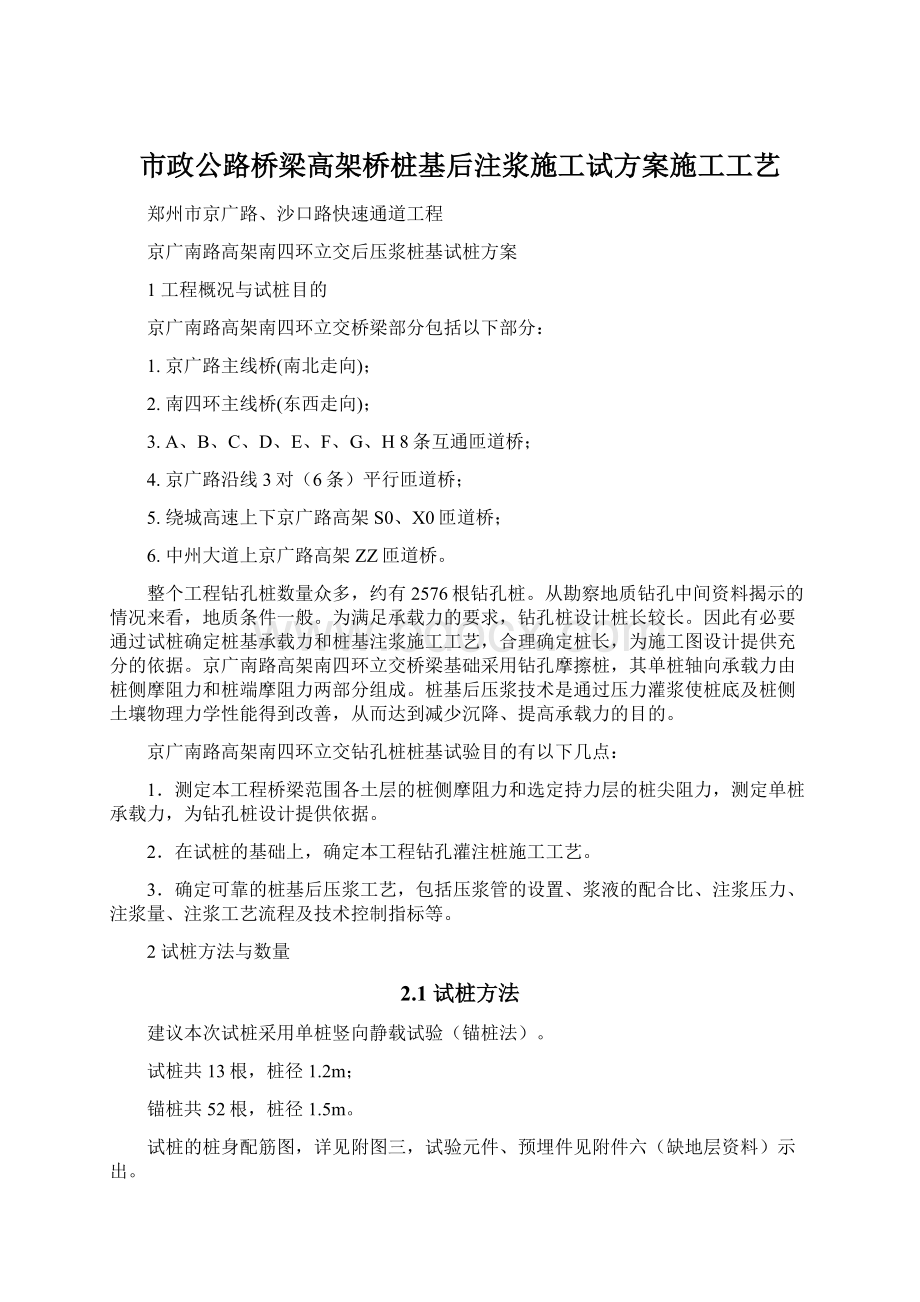
市政公路桥梁高架桥桩基后注浆施工试方案施工工艺
郑州市京广路、沙口路快速通道工程
京广南路高架南四环立交后压浆桩基试桩方案
1工程概况与试桩目的
京广南路高架南四环立交桥梁部分包括以下部分:
1.京广路主线桥(南北走向);
2.南四环主线桥(东西走向);
3.A、B、C、D、E、F、G、H8条互通匝道桥;
4.京广路沿线3对(6条)平行匝道桥;
5.绕城高速上下京广路高架S0、X0匝道桥;
6.中州大道上京广路高架ZZ匝道桥。
整个工程钻孔桩数量众多,约有2576根钻孔桩。
从勘察地质钻孔中间资料揭示的情况来看,地质条件一般。
为满足承载力的要求,钻孔桩设计桩长较长。
因此有必要通过试桩确定桩基承载力和桩基注浆施工工艺,合理确定桩长,为施工图设计提供充分的依据。
京广南路高架南四环立交桥梁基础采用钻孔摩擦桩,其单桩轴向承载力由桩侧摩阻力和桩端摩阻力两部分组成。
桩基后压浆技术是通过压力灌浆使桩底及桩侧土壤物理力学性能得到改善,从而达到减少沉降、提高承载力的目的。
京广南路高架南四环立交钻孔桩桩基试验目的有以下几点:
1.测定本工程桥梁范围各土层的桩侧摩阻力和选定持力层的桩尖阻力,测定单桩承载力,为钻孔桩设计提供依据。
2.在试桩的基础上,确定本工程钻孔灌注桩施工工艺。
3.确定可靠的桩基后压浆工艺,包括压浆管的设置、浆液的配合比、注浆压力、注浆量、注浆工艺流程及技术控制指标等。
2试桩方法与数量
2.1试桩方法
建议本次试桩采用单桩竖向静载试验(锚桩法)。
试桩共13根,桩径1.2m;
锚桩共52根,桩径1.5m。
试桩的桩身配筋图,详见附图三,试验元件、预埋件见附件六(缺地层资料)示出。
锚桩的桩身配筋图,详见附图四,其桩身主筋配筋采用三级钢,规范的标号为HRB400,强度为400Mpa;
2.2试桩数量与位置
本期试桩数量按总桩数的0.5%确定为钻孔灌注桩13根,桩径为1.2m,混凝土强度等级为水下C30。
试桩采用4根1.5m的锚桩压1根1.2m试桩的方式。
以下为试桩暂定位置。
注:
1#、3#、6#、9#试桩位置,因锚桩间距过大,位置根据现场情况待定。
1#试桩
桩基编号
桩基性质
桩径(m)
桩顶标高(m)
桩长(m)
桩位坐标
X
Y
锚桩1
工程桩
1.5
153.0
45
35427.049
69477.432
锚桩2
工程桩
1.5
153.0
45
35423.356
69478.968
锚桩3
工程桩
1.5
153.0
45
35430.653
69486.102
锚桩4
工程桩
1.5
153.0
45
35426.959
69487.637
试桩
试桩
1.2
153.0
40
35427.004
69482.535
2#试桩
桩基编号
桩基性质
桩径(m)
桩顶标高(m)
桩长(m)
桩位坐标
X
Y
锚桩1
工程桩
1.5
153.0
45
35459.368
69463.999
锚桩2
工程桩
1.5
153.0
45
35455.675
69465.534
锚桩3
工程桩
1.5
153.0
45
35462.347
69471.164
锚桩4
工程桩
1.5
153.0
45
35458.653
69472.700
试桩
试桩
1.2
153.0
40
35459.011
69468.349
3#试桩
桩基编号
桩基性质
桩径(m)
桩顶标高(m)
桩长(m)
桩位坐标
X
Y
锚桩1
工程桩
1.5
153.0
45
35484.779
69433.944
锚桩2
工程桩
1.5
153.0
45
35481.085
69435.479
锚桩3
工程桩
1.5
153.0
45
35488.617
69443.178
锚桩4
工程桩
1.5
153.0
45
35484.924
69444.713
试桩
试桩
1.2
153.0
40
35484.851
69439.328
4#试桩
桩基编号
桩基性质
桩径(m)
桩顶标高(m)
桩长(m)
桩位坐标
X
Y
锚桩1
工程桩
1.5
141.6
45
37608.857
68569.266
锚桩2
工程桩
1.5
141.6
45
37604.368
68568.259
锚桩3
工程桩
1.5
141.6
45
37607.388
68575.806
锚桩4
工程桩
1.5
141.6
45
37602.900
68574.798
试桩
试桩
1.2
141.6
40
37605.878
68572.032
5#试桩
桩基编号
桩基性质
桩径(m)
桩顶标高(m)
桩长(m)
桩位坐标
X
Y
锚桩1
工程桩
1.5
141.6
45
37637.802
68577.675
锚桩2
工程桩
1.5
141.6
45
37633.430
68576.247
锚桩3
工程桩
1.5
141.6
45
37635.485
68584.769
锚桩4
工程桩
1.5
141.6
45
37631.112
68583.341
试桩
试桩
1.2
141.6
40
37634.457
68580.508
6#试桩
桩基编号
桩基性质
桩径(m)
桩顶标高(m)
桩长(m)
桩位坐标
X
Y
锚桩1
工程桩
1.5
141.6
45
37657.257
68584.297
锚桩2
工程桩
1.5
141.6
45
37652.905
68582.807
锚桩3
工程桩
1.5
141.6
45
37654.107
68593.500
锚桩4
工程桩
1.5
141.6
45
37649.755
68592.011
试桩
试桩
1.2
141.6
40
37653.506
68588.154
7#试桩
桩基编号
桩基性质
桩径(m)
桩顶标高(m)
桩长(m)
桩位坐标
X
Y
锚桩1
工程桩
1.5
141.0
45
37857.039
68544.442
锚桩2
工程桩
1.5
141.0
45
37855.945
68548.910
锚桩3
工程桩
1.5
141.0
45
37864.596
68546.293
锚桩4
工程桩
1.5
141.0
45
37863.502
68550.761
试桩
试桩
1.2
141.0
40
37860.270
68547.602
8#试桩
桩基编号
桩基性质
桩径(m)
桩顶标高(m)
桩长(m)
桩位坐标
X
Y
锚桩1
工程桩
1.5
142.8
45
37950.100
68238.376
锚桩2
工程桩
1.5
142.8
45
37945.643
68237.236
锚桩3
工程桩
1.5
142.8
45
37948.323
68245.322
锚桩4
工程桩
1.5
142.8
45
37943.867
68244.182
试桩
试桩
1.2
142.8
40
37946.983
68241.279
9#试桩
桩基编号
桩基性质
桩径(m)
桩顶标高(m)
桩长(m)
桩位坐标
X
Y
锚桩1
工程桩
1.5
143.5
45
37931.217
68231.263
锚桩2
工程桩
1.5
143.5
45
37926.753
68230.154
锚桩3
工程桩
1.5
143.5
45
37928.914
68240.527
锚桩4
工程桩
1.5
143.5
45
37924.450
68239.417
试桩
试桩
1.2
143.5
40
37927.833
68235.340
10#试桩
桩基编号
桩基性质
桩径(m)
桩顶标高(m)
桩长(m)
桩位坐标
X
Y
锚桩1
工程桩
1.5
144.5
45
37752.841
68279.635
锚桩2
工程桩
1.5
144.5
45
37753.464
68275.077
锚桩3
工程桩
1.5
144.5
45
37746.771
68278.805
锚桩4
工程桩
1.5
144.5
45
37747.394
68274.248
试桩
试桩
1.2
144.5
40
37750.118
68276.941
11#试桩
桩基编号
桩基性质
桩径(m)
桩顶标高(m)
桩长(m)
桩位坐标
X
Y
锚桩1
工程桩
1.5
144.5
45
37749.730
68302.128
锚桩2
工程桩
1.5
144.5
45
37750.346
68297.570
锚桩3
工程桩
1.5
144.5
45
37741.762
68301.051
锚桩4
工程桩
1.5
144.5
45
37742.378
68296.493
试桩
试桩
1.2
144.5
40
37746.054
68299.311
12#试桩
桩基编号
桩基性质
桩径(m)
桩顶标高(m)
桩长(m)
桩位坐标
X
Y
锚桩1
工程桩
1.5
131.7
45
38657.710
68028.358
锚桩2
工程桩
1.5
131.7
45
38653.847
68029.396
锚桩3
工程桩
1.5
131.7
45
38659.501
68035.021
锚桩4
工程桩
1.5
131.7
45
38655.638
68036.059
试桩
试桩
1.2
131.7
40
38656.675
68032.217
13#试桩
桩基编号
桩基性质
桩径(m)
桩顶标高(m)
桩长(m)
桩位坐标
X
Y
锚桩1
工程桩
1.5
131.7
45
38661.577
68042.747
锚桩2
工程桩
1.5
131.7
45
38657.714
68043.785
锚桩3
工程桩
1.5
131.7
45
38663.367
68049.411
锚桩4
工程桩
1.5
131.7
45
38659.504
68050.449
试桩
试桩
1.2
131.7
40
38660.540
68046.598
注:
1.工程桩作为锚桩,其桩顶标高按高出设计承台底标高0.5m设计。
)
2.试桩桩位平面布置图见附件五。
3主要试验内容及技术要求
1.根据试桩附近的地质钻孔资料,结合静载试验,测定不同加荷等级下的桩侧各土层的摩阻力和桩尖阻力(测管安装与成桩同时进行)。
试桩要求加压至破坏荷载,确定单桩极限承载力,试桩单位应充分预留加载能力。
2.钻孔灌注桩成孔直径不小于设计直径,成孔倾斜度不大于1/100,沉淀厚度不大于150mm。
3.用声波透射法检测桩身质量,用高应变动力测试桩校核桩基承载力。
4.进行桩基压浆并钻孔取芯以检查压浆后水泥浆与土层的结合情况。
5.桩基压浆应在钻孔桩混凝土灌注完成至少1周后进行,桩基试验应在注浆完成15天后进行。
6.为确保试桩费用不超过初步设计概算,本次试验利用工程桩作为锚桩,试验需充分考虑对工程桩的保护:
加载反力确保工程桩所在的土体不发生剪切破坏而失效;工程桩的桩顶标高要满足设计要求。
试桩桩位平面布置图见附件五。
7、极限承载力与加载要求
根据未注浆单桩承载力计算结果,单桩极限承载力估算值为16000kN。
8、对于灌注桩的试桩,在成孔后进行混凝土浇注前,必须进行孔径、孔深、沉渣及垂直度检测。
4试桩施工工艺要求
4.1试桩后注浆要求及流程
1)试桩应严格按照相关规范进行二次清孔,二次清孔在下完导管后进行,二次清孔采用气举反循环或泵吸反循环,二次清孔后的孔底沉渣厚度<100mm,二次清孔完成后,立即灌注水下混凝土。
2)在郑州地区灌注桩后注浆施工中,为确保注浆管开塞,有在钢筋笼下放之后、灌注混凝土之前,往孔底填放碎石的做法。
本试桩桩底不填碎石,采用开塞时间提前的措施。
开塞在混凝土浇注后12~24小时进行,开塞后用清水冲洗注浆管道,直至溢出清水,然后用堵头重新封闭压浆管。
3)利用声测管作底注浆管,声测管布置3根,呈等边三角形,一般为Φ50钢管,顶端高出地面500mm,并用堵头封严,防止泥浆等杂物进入。
超声波检测后进行桩端注浆。
4)后注浆采用注浆压力和注浆量双控的措施。
当满足下列条件之一时可终止注浆:
(1)注浆总量和注浆压力均达到设计要求;
(2)对每一道注浆来说,注浆量达到设计值,但注浆压力没有达到设计值(侧注浆2.0MPa,底注浆2.5MPa)。
此时改为间歇注浆,再注设计值的30%水泥浆为止;
沉渣厚度极易增大,这些是本试桩工程的施工技术难点。
(3)对每一道注浆来说,注浆压力达到设计值,注浆量少于设计值,此时保证注浆量不低于设计值的80%即可。
注浆流程如下框图:
预埋注浆管下钢筋笼
图4-1压力注浆工艺流程图
4.2试桩施工方法与施工工艺
4.2.1施工工艺流程
本工程单桩竖向承载力大,桩径大,桩身长。
地质情况较复杂,桩施工钻进时扭矩大、清孔困难,钢筋笼对接与下放时间长,孔壁稳定性受到影响,拟采用GZ-2000型工程钻机进行泥浆护壁正循环钻进成孔,反循环二次清孔工艺施工。
为了保证成孔质量:
施工过程中严格控制钻机垂直度,每根施工钻杆用水平靠尺或2m靠尺检查,保证施工垂直度在0.5%以内;为防止桩孔塌空,严格控制泥浆比重,成孔前先制造泥浆,成孔泥浆比重控制在1.25左右、粘度不小于20秒。
采用商品混凝土,并配备混凝土运输车进行灌注混凝土,钢筋笼现场制作吊装。
钢筋笼分节制作,主筋采用机械连接,采用吊车下放,不同分段的钢筋笼在孔口连接。
后注浆采用BW-15注浆泵进行注浆。
钻孔桩施工之前先探明每根桩桩位处有否地下障碍物及市政管线。
每根试桩都应有完整的记录,内容包括孔径、孔深、垂直度、沉渣厚度、泥浆比重、泥浆黏度、泥浆含沙率、充盈系数等技术指标,钻孔两次清孔、水下混凝土灌注等施工记录。
施工工艺流程如下:
施工放验线→钻机就位整平→钻进成孔→测量钻孔深度→第一次清孔→提出钻杆→测孔底沉渣厚度及孔深→安装钢筋笼和注浆管→安放导料管→第二次清孔→测量孔径→灌注水下砼→测砼桩顶标高→拔出导料管→成桩→开塞→桩侧注浆→桩底注浆。
后注浆
图4-2灌注桩施工工艺流程图
4.2.2施工工艺要求
►钻头要求
采用三翼合金梳齿钻头,并在钻头上焊接一定数量的风镐头,可有效地提高施工的效率,减少钻具的磨损。
钻头配单腰带导正环,直径为1500mm。
►钻进参数要求
钻压:
粉土、砂土为5~15KN;粉质粘土层为10~25KN;
转速:
20~50r/min;
泵量:
108m3/h。
►钻进成孔要求
钻机就位后,泥浆循环后,开动钻机慢速回转,下放钻头,开始钻进时,应先轻压慢转至钻头正常工作后,逐渐增大转速。
调整钻压,以不造成钻头吸水口堵塞为极限。
在加接钻杆时,要将钻头提离孔底50cm,使用冲洗液循环3~5分钟以后,再拆卸加接钻杆;加完钻杆后用靠尺测量一次钻杆的垂直度。
钻孔达到要求孔深停钻后,钻具提离孔底50~80mm,进行第一次清孔,检查泥浆比重,一次成孔的泥浆比重不大于1.25,直到符合清孔标准为止,提钻时操作要轻稳,防止钻头拖刮孔壁,并向孔内补充泥浆,稳定孔内水头高度。
钻杆提完后,测量孔深,符合要求后进行下一道工序。
►第一次清孔要求
钻孔完成后进行第一次清孔,利用泥浆泵通过钻杆的向孔底输入较稀的泥浆以置换孔底的稠泥浆,并使稠泥浆携带着孔底的钻渣排出孔外的泥浆池中,如此循环,直到清孔完成为止。
清孔完毕,检查泥浆比重,一次清孔的泥浆比重≤1.25。
►钢筋笼制作、安放要求
钢筋笼在现场制作,钢筋堆放场地要平整。
钢筋选用正规厂家的合格产品,进场钢筋必须附有产品质量合格证明,进场后,按规格分类堆放,设置标识牌。
进场钢筋规格符合要求,并附有厂家的材质证明,现场按批次及见证取样规定送试验室进行原材料及机械连接试验检验。
钢筋焊接人员必须持证上岗。
1)钢筋笼加工制作前,严格依据设计图纸对操作工人进行技术交底,对钢筋下料、焊接进行全程检验核对,钢筋笼加工制作及安放在技术人员指导下,按技术方案要求制作。
2)各分段钢筋笼制作时,首先把内加强箍焊接成型,按桩径确定外径,按照主筋数量把加强箍等分,并把此数值标注于操作平台上,主筋放在做出标志的相应位置,这样依次把加强箍与主筋焊接起来,钢筋笼的主筋接长采用机械连接,钢筋笼的加劲箍筋采用单面焊焊接,单面焊焊缝长度为10d以上,主筋与箍筋焊成钢筋笼骨架,接着按照箍筋的间距在已焊成骨架的主筋上做标识,按标识的间距焊接外箍筋。
纵向钢筋接头每隔一根错开,满足每个断面接头数不超过总数的50%。
错开连接,断面间距不小于1.2m。
3)螺旋箍筋与主筋点焊,螺旋箍筋钢筋接长采用点焊搭接,搭接长度为300mm。
4)加强箍筋全长配置,与主筋焊接,两端及主筋接头处必须设置。
5)笼子制作严格依设计进行,允许偏差符合现行规范、规程规定。
6)分段钢筋笼之间连接时,采用机械连接,纵向钢筋接头应每隔一根错开,满足每个断面接头数不超过总数的50%。
相临接头应错开1.2m。
同时,把三根超声波声测管等距离焊接在钢筋笼内侧。
。
7)本工程桩保护层厚50mm,按要求安放垫块,垫块采用细石高强度砼块,每3米1组,每组不少于4块。
8)钢筋笼制作质量要求如下:
主筋间距和笼直径偏差:
±10mm;
箍筋间距偏差:
±20mm;
钢筋笼总长度偏差:
±100mm;
同一截面连接根数不大于50%,接头间距1200mm;
螺旋箍筋搭接长度为300mm(均点焊),第一圈应是整圈;
钢筋笼的垫块用φ8钢筋及直径φ100的砼园柱体制作在沿圆周长均等的4个点上安放,间隔3m。
螺旋箍筋与主筋间按梅花形点焊。
笼子成型后,经过监理验收合格后方可使用。
9)钢筋笼的吊放
钢筋笼吊放前要再次对钢筋笼进行检查,检查扶正器是否完好,齐全,必要时进行补焊。
钢筋笼堆放场地平整,钢筋笼在运输过程及吊放中防止扭转与弯曲,采取临时插钢管或方木措施。
下放钢筋笼前,用水准仪测量出护筒标高,以计算吊杆长度。
分段制作的钢筋笼在孔口采用机械连接,连接质量应满足规范规定。
钢筋笼定位采用吊杆与钢筋笼通过特殊接头相连接,根据护筒标高计算出地面标高后,把钢筋笼下放到位,将压杆固定在孔口横担上,以防灌注时钢筋笼上浮或下移。
钢筋笼顶标高允许偏差:
±100mm,钢筋笼中心与桩中心允许偏差:
±10mm。
钢筋笼吊放方法:
用钻机吊放钢筋笼,钢筋笼吊入孔内时,不得碰撞孔壁,在吊放钢筋笼入孔的全过程中,保证其垂直,防止产生弯曲变形。
钢筋笼要沉放到底,不得悬挂,下笼受阻时不得撞笼、墩笼、扭笼。
起吊过程中要注意安全、密切配合。
对于后压浆试桩、超声波检测试桩,在钢筋龙吊装前安放注浆管和声侧管。
检验合格后吊装入孔。
►埋置注浆管施工要求
注浆管在现场加工制作,注浆管制作要和桩钢筋笼制作同步进行,按设计方案要求把注浆管安装在钢筋笼上随钢筋笼一起下放入孔。
►安放导料管施工要求
本工程采用φ195导管。
采用承插连接,用橡胶圈或橡胶板密封,导管每节长度2m左右,最下端一节长度为3m。
每节导管应平直,长度偏差:
L≤L%(L:
单节导管长度);连接部位内径偏差:
<2mm;连接好的导管轴线偏差:
≤1%。
导管下放前要在地面检查其连接的密封性,试水压力0.6—1.0MPa。
下放导管过程中,必须认真检查每道密封圈,有损坏的立即换掉。
接导管前先清洗丝扣,接管时要上紧丝扣。
►第二次清孔施工要求
1)试桩应严格按照相关规范进行二次清孔,二次清孔在下完导管后进行,二次清孔采用气举反循环或泵吸反循环,二次清孔后的孔底沉渣厚度一般应小于设计要求(本工程要求沉渣厚度小于100mm),二次清孔完成后,立即灌注水下混凝土。
2)对二次以上清孔后成渣厚度仍大于100mm小于200mm的桩,应做好记录,并在随后的桩底注浆时适当增加注浆量。
►商品砼的运输与灌注
桩身混凝土灌注在二次清孔完成并检验沉渣厚度和泥浆比重符合规定后的半小时内进行,并连续灌注直至桩完成。
本工程采用商品混凝土。
首先,应严把质量关,选择质量经过认证、实力雄厚、生产供应能力强、服务到位的供应商,与之签订供货合同。
材料进场应附有质量证明,严格按程序报验和试验,合格后才能用于工程。
其次,根据每天需用的砼量与商品混凝土站联系,确保连续供应,以便连续施工。
在灌注混凝土前,首先吊入隔水塞,隔水塞比导管内径小20~25mm,灌注砼前用铁丝吊挂在导管内,砼达到初灌量时剪断放塞,初灌时导管埋深不低于1.2m,每次提升导管之前测一次导管内外砼面的高度,填写水下砼灌注记录表,绘制水下砼灌注曲线。
当孔内砼面将要接近钢筋笼的底端时,要防止钢筋笼上浮。
当灌注砼面接近设计标高时,要注意砼面使其符合设计要求,每次拆下的导管应及时冲洗干净,灌完后必须冲洗漏斗、储浆斗及其它专用工具。
灌注工作必须连续进行,尽可能压缩上料运输吊斗、提管、拆管时间,严禁中途停工,每根桩灌注砼之前应测量砼坍落度,砼坍落度控制在180~220mm。
混凝土灌注充盈系数大于1。
每个灌注台班不少于1组(3块)试块(边长为100mm的立方体),标准养护。
混凝土灌注完成后缓慢将导管拔出,导管提离砼面之前要反复插实,避免空心桩。
水下混凝土连续施工,不许间断,灌注过程须详细记录。
对浇注过程中的一切故障都要记录备案。
►泥浆外运施工要求
钻进、清孔过程中产生的废浆应及时外运,泥浆外运时要结合市政管理规定,对外运泥浆车制定切实可行的行走路线,泥浆车为封闭铁皮罐车,泥浆外运车出场前采取措施使其满足环保要求,不对道路造成污染。
►后压浆施工要求
1、注浆装置制作及安装
1)注浆装置应该按设计要求制作,加工时一定要逐根检查,防止管内有杂物及管子破损裂缝。
2)注浆装置管路的所有焊接作业不得焊透,以防渗漏。
3)桩端注浆
利用声测管作底注浆管,声测管布置3根,呈等边三角形,声测管为Φ50钢管,顶端高出地面500mm,并用堵头封严,防止泥浆等杂物进入。
超声波