催化裂化新工艺技术问答.docx
《催化裂化新工艺技术问答.docx》由会员分享,可在线阅读,更多相关《催化裂化新工艺技术问答.docx(24页珍藏版)》请在冰豆网上搜索。
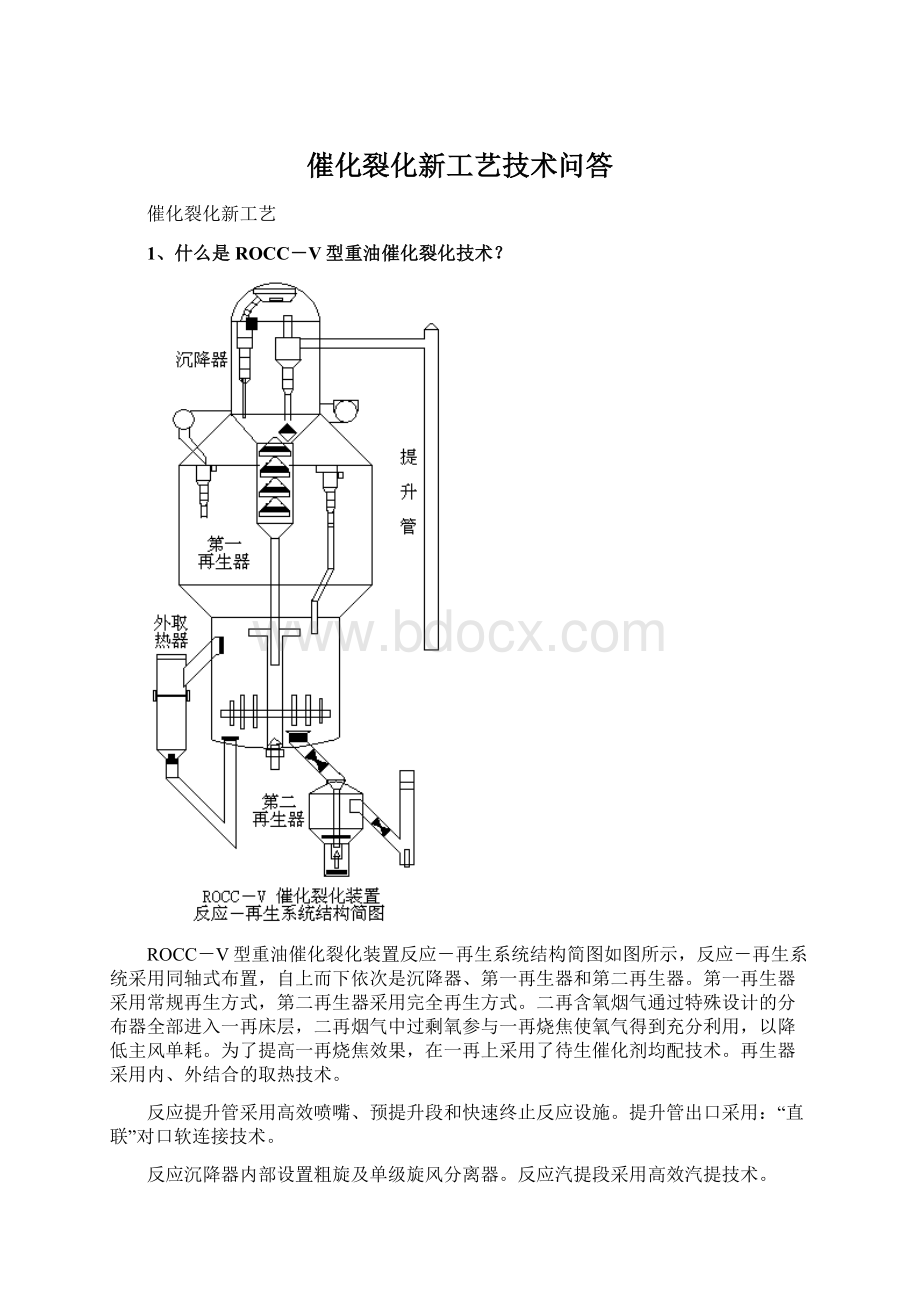
催化裂化新工艺技术问答
催化裂化新工艺
1、什么是ROCC-V型重油催化裂化技术?
ROCC-V型重油催化裂化装置反应-再生系统结构简图如图所示,反应-再生系统采用同轴式布置,自上而下依次是沉降器、第一再生器和第二再生器。
第一再生器采用常规再生方式,第二再生器采用完全再生方式。
二再含氧烟气通过特殊设计的分布器全部进入一再床层,二再烟气中过剩氧参与一再烧焦使氧气得到充分利用,以降低主风单耗。
为了提高一再烧焦效果,在一再上采用了待生催化剂均配技术。
再生器采用内、外结合的取热技术。
反应提升管采用高效喷嘴、预提升段和快速终止反应设施。
提升管出口采用:
“直联”对口软连接技术。
反应沉降器内部设置粗旋及单级旋风分离器。
反应汽提段采用高效汽提技术。
ROCC-V型重油催化裂化技术在青岛石油化工厂1.0Mt/a催化裂化装置上进行了工业放大试验,达到了预期的目标。
用残炭为2.99%的蜡油及渣油混合进料时,轻质油收率为71.98%,液化石油气收率为10.88%,干气产率为3.23%(包括损失),汽油辛烷值(RON)为90.2,轻柴油十六烷值为33。
试运行中,装置运行平稳,反应-再生系统调节自如,再生剂含炭低。
2、ROCC-V型重油催化裂化技术的特点是什么?
ROCC-V型重油催化裂化技术的特点是:
(1)耗风量少,再生剂定炭低,可适应大比例掺炼渣油的要求。
二再含过剩氧的烟气可在一再进一步利用,而且,一再采用常规再生,因而耗风量少。
在青岛石油化工厂1.0Mt/aROCC-V型装置的设计耗风指标为每千克焦耗风(标准状态)9.6m3,工业示范装置运行已经达到每千克焦耗风(标准状态)8.8m3,主风机组、再生器和三旋等再生系统的投资可以大幅度降低。
另外,再生催化剂定炭可达到0.05%以下。
(2)合理布置沉降器、一再、二再(三器)之间的位置,尽量降低三器总高度。
沉降器顶切线标高仅为58.1m。
与国外类似的两段逆流再生工艺相比,两器总高度降低约15m左右,减少了反应油气在高温下的停留时间。
(3)三器间催化剂循环均为立管输送,可适应各种密度催化剂的要求,比国外用斜管输送催化剂的蓄压大、吹扫松动系统简单、输送催化剂畅通,能适应大剂油比操作的要求,装置的操作弹性大,抗事故能力强。
(4)采用结构特殊的分配器,将二再烟气及携带的少量再生催化剂均匀分布后输入一再密相床的适当位置,与一再密相床中的待生均配器、半再生催化剂抽出位置及一再主风分布器位置三者合理搭配,保证一再密相床流化均匀,并合理地利用二再含氧烟气中的过剩氧。
(5)二再采用湍流床及大小筒结构,使二再用风量不受操作线速度的制约,并可在较大范围内变化,大小筒结构可减少二再烟气携带的催化剂,避免大量催化剂在一、二再之间反复循环。
(6)一、二再烧焦比例调节灵活,调节范围大。
通过控制一、二再的主风量和控制一再温度可以在一定范围内调节再生烟气中CO/CO2的比例和两段烧焦比例,二再烧焦比例可在较大范围内变化。
当装置烧焦率低或处理量小时,大部分焦炭可在一再中烧掉,二再烧焦量仅作为维持一定的再生温度的手段。
再生温度降低有利于增加催化剂循环量,提高剂油比。
当装置生焦率增加时,可将烧焦转移至二再进行,可通过调节二再主风量改变一、二再之间的循环催化剂量。
与其它型式的两段再生相比,二再的烧焦比例可在0~40%的大范围内变化。
(7)为进一步改善产品分布,提高轻质油收率,降低干气及焦炭产率,在提升管反应系统设计中采用以下一系列措施:
A、优化反应操作条件,实现高温、大剂油比、短反应时间的操作。
提升管反应器设计出口温度510~515℃,剂油比6~8,反应时间2.5~3s。
B、采用高效雾化喷嘴,改善原料油雾化效果。
C、设置预提升段,使油气与催化剂接触前,以活塞流的形式向上运动,保持催化剂和油气均匀接触。
提升介质为自产干气和蒸汽。
以干气为提升介质可减轻催化剂的失活,减少蒸汽和污染水量,同时对重金属镍还有钝化作用。
D、提升管出口采用粗旋,这对加工高含镍原料更显必要,将粗旋气体出口管延伸至沉降器旋风分离器入口,采用“直链”对口软连接技术,以减少反应后油气的停留时间。
E、设置快速终止反应设施。
为了抑制氢转移等二次反应及减少热裂化反应,在提升管上部及粗旋出口设置若干终止剂注入点,以增加操作的灵活性。
终止剂注入也有助于实现反应的高温、短接触时间和大剂油比操作。
F、采用高效汽提技术。
提高汽提效果对降低再生器烧焦负荷和减轻催化剂水热失活有很大好处。
设计采用了粗旋料腿出口预汽提技术加两段汽提技术,并对汽提段档板进行特殊设计以改善汽提蒸汽与待生催化剂的接触,此外设计还采用较长的催化剂停留时间和较高的汽提温度,以提高汽提效果。
3、什么是MIP工艺?
MIP的设计思想是既保留提升管反应器具有高反应强度的特点,同时又能够进行某些二次反应以多产异构烷烃和芳烃。
为此设计了一种新型提升管反应器。
该反应器具有以下特征:
新型提升管反应器是在现有的提升管反应器基础上将反应器分成两个反应区(如图所示)第一反应区类似现有的提升管反应器,油气和催化剂混合后,在该反应区以一次裂解反应为主,采用较高的反应强度,即较高的反应温度和剂油比,生成较多的烯烃和处理较重的原料油,经较短的停留时间后进入扩径的第二反应区下部,该反应区与传统的提升管反应器的不同之处在于降低油气和催化剂的流速,可以注入急冷介质和采用其它措施,降低该区反应温度,以抑制二次裂化反应,增加异构化和氢转移反应,从而使汽油中的异构烷烃和芳烃含量增加;物流在该反应区停留时间较长,然后进入径向收缩的出口区,该区也类似传统的提升管反应器顶部出口部分,物流在该区停留时间较短,也是为了抑制过裂化反应和增加流体线速;然后物流进入分离系统进行气固分离,分离出的气相由旋风分离器出口引出,催化剂颗粒经汽提后进入再生器。
MIP工艺已在中国石化高桥分公司炼油厂1.4Mt/a催化裂化装置顺利进行了工业试验。
在装置的原料性质、处理量、掺渣量和物料平衡基本不变的情况下,MIP工艺比RFCC工艺生产的汽油中的烯烃含量下降了10%左右。
4、什么是催化裂化过程中过裂化现象?
在催化裂化工艺中,汽油馏分通过二次裂化转变成轻烯烃叫作催化裂化过程中的过裂化现象。
由反应温度升高引起的催化裂化过裂化反应属于过度热反应。
过裂化点后干气和焦炭产率出现明显增加的趋势,但液化气产率则匀速增加。
由剂油比增加引起的催化裂化过裂化反应属于过度催化反应。
过裂化点后液化气和焦炭产率出现明显增加的趋势,但干气产率基本上没有变化。
5、什么是减压渣油催化裂化(VRFCC)技术?
VRFCC是一项加工大庆减压渣油的催化裂化新工艺,该工艺专利技术主要包括:
(1)高粘度原料的减粘雾化技术。
(2)无返混床剂油接触实现热击气化及高重油转化技术。
(3)短接触反应抑制过裂化和结焦技术。
(4)应再生温差及再生剂温度调控协调初始反应深度及总反应苛刻度技术。
(5)用VRFFCC专用催化剂(DVR系列)技术。
第一套VRFCC工业装置是由北京燕山石化公司炼油厂催化裂化装置改造成800Kt/aVRFCC装置,该装置工程设计的主要特点有:
(1)提升管反应器采用了新一代高效雾化喷嘴,提高了高粘度进料的雾化效率。
(2)采用带四层预汽提段和三臂旋流头的旋流快速分离器(VQR),有效降低焦炭氢含量。
(3)使用了在我国首次采用的富氧再生技术,解决了在再生器主体不动、主风量不足的前提下烧焦量增加约60%的难题。
(4)采用了新的防焦蒸汽注入设计,有效防止了加工高生焦母体渣油进料的反应系统、沉降器内部构件、穹顶及大油气管线等部位的设备结焦问题。
此外,该装置技改项目中还包括了7项我国近年来行之有效的重油催化裂化技术。
6、什么是毫秒催化裂化(MSCC)技术?
MSCC是UOP公司开发的。
在MSCC过程中,催化剂向下流动形成催化剂帘,原料油水平注入与催化剂垂直接触,实现毫秒催化反应。
反应产物和待生催化剂水平移动,依靠重力作用实现油气与催化剂的快速分离。
这种毫秒反应以及快速分离,减少了非理想的二次反应,提高了目的产物的选择性,汽油和烯烃产率增加、焦炭产率减少,能更好地加工重质原料,且投资费用较低。
现在已有2套MSCC装置正在运转。
一套位于Coastal公司的EaglePoint炼油厂,处理能力为2.8Mt/a;另一套建在TranAmerican炼油公司,处理能力为5.0Mt/a;另外还有一套全新的MSCC装置将在土库曼斯坦炼油厂建成投产。
7、什么是催化裂解(DCC)工艺?
DCC工艺是一项重油制取低碳烯烃技术。
该技术现在已在国内建立6套装置,在国外建立1套工业装置。
近年来,DCC技术还在不断发展和完善。
这些新进展主要有两个方面:
一个是开发系列催化剂产品,另一个是改进工艺以进一步提高轻烯烃、特别是丙烯的产率。
在催化剂开发方面尽量使品种多样化,以满足不同用户的需要,而新开发的渣油催化裂解催化剂已经在全常压渣油催化裂解装置上使用。
在工艺改进方面也已经取得很好的实验结果,以大庆蜡油掺渣油为原料可以得到28%的丙烯产率,同现有的DCC技术相比,丙烯产率可以提高6个单位以上。
8、什么是多产柴油的催化裂化(MDP)技术?
石油化工科学研究院在传统的增产柴油工艺技术的基础上开发出催化裂化增产柴油的新工艺MDP。
该工艺主要具有以下特点:
(1)可以加工重质、劣质的催化裂化原料。
(2)采用配套研制的增产柴油催化剂,且维持平衡剂的活性适中。
(3)应用原料组分选择性裂化技术,将催化裂化原料按馏分的轻重及其可裂化性能区别处理,在提升管反应器的不同位置注入不同的原料组分,使性质不同的原料在不同的环境和适应的裂化苛刻度下进行反应
(4)采用较为苛刻的裂化条件和适应的回炼比,装置的加工量和汽油的辛烷值不会受到影响。
9、什么是单段两级再生(RegenMax)?
通过对单段再生和两段再生特点的研究,Kellogg技术公司和Mobil技术公司联合开发了RegenMax技术。
其特点是采用单个再生器,并在再生器密相的适当部位加入一块专利挡板,催化剂与主风逆流接触,通过这块挡板可以达到减少返混和多级再生的目的。
冷模试验表明,通过加入挡板可将再生器上部和下部的催化剂返混减少80%,使在再生器稀相的催化剂携带量减少50%以上。
使用RegenMax后,该装置可以以部分燃烧方式操作达到完全燃烧的再生效果,且能使再生器直径缩小11%,主风量降低22%,催化剂藏量减少5%。
10、什么是逆流两段再生技术?
济南炼油厂1.40Mt/a重油催化裂化装置的再生部分采用了同轴/串联/逆流两段再生工艺,施工周期短,投资少。
该工艺可使第二再生器(二再)的氧浓度达到5%以上,创造了富氧再生的有利条件,并将二再的富氧烟气引入第一再生器(一再),使主风得到充分利用,还避免了采用并列/并流两段再生工艺时富氧烟气与一再的富CO烟气混合引起的尾燃及设备超温问题,为实现再生器的平稳操作提供了有利的前提条件。
11、MGG和ARGG工艺技术的主要特点是什么?
以蜡油、掺炼渣油为原料的MGG工艺技术和在此基础上开发的以常压渣油等为原料的ARGG工艺技术,是采用具有特殊反应性能的RMG、RAG系列催化剂及相应的工艺条件,通过提升管或床层反应器,最大量地生产富含低碳烯烃的液化气和高辛烷值汽油的新型催化转化工艺技术。
该工艺技术的主要特点是:
(1)油气兼顾,既大量生产富含低碳烯烃的液化气,又大量生产高品质汽油,以石蜡基原油的VGO为例,MGG工艺技术可达到液化气产率35%(质),汽油产率45%(质)以上,汽油RON在92~94,诱导期500~1000min。
(2)原料广泛。
可以加工多种原料,如蜡油、掺炼油、常压渣油或原油等重质原料。
(3)采用活性高、选择性好、抗金属污染能力强,具有特殊反应性能的RMG、RAG系列催化剂。
(4)适宜的工艺操作参数与独特性能的催化剂合理配合,实现了同时兼有催化裂化正常裂化区与过裂化区二者的优点。
在转化率远高于一般催化裂化情况下,汽油安定性好,焦炭和干气无明显增加。
(5)操作灵活。
可根据市场变化的需要,通过改变工艺参数或采用不同操作条件(单程、重油回炼、重柴回炼等)来调整汽油、柴油和液化气等产品分布和收率。
12、MGG和ARGG工艺的工业运转结果怎样?
工业运转结果表明,MGG、ARGG工艺技术可靠,催化剂活性高,选择性好,抗金属污染能力强。
炼厂名称
兰州炼化总厂
扬州石化总厂
原料油
新疆、青海混合蜡油掺渣油
常压渣油
掺渣比21.66%
掺渣比12.77%
主要操作条件
反应压力/MPa
反应温度℃
回炼比
0.138
534
0.15
0.147
538
0.49
0.106
530
0.27
0.130
534
0.29
产品质量产率/%
干气
液化气
其中C3
C4
iC4*
C5*汽油
轻柴油
焦炭
损失
3.97
26.78
8.79
7.26
6.75
48.07
12.36
8.20
0.62
5.13
27.38
9.73
7.22
6.84
51.87
4.94
9.64
1.04
4.72
27.18
9.88
10.05
-
47.72
11.23
8.6
0.53
4.31
30.01
11.17
10.70
-
43.31
13.17
8.76
0.44
转化率/%(质)
87.64
95.06
88.77
86.83
汽油性质
RONC
MONC
诱导期/min
胶质/mg·(100ml)-1
93.1
80.5
675
1.2
93.5
80.7
870
2.0
92.1
80.5
535
4.0
92.7
80.0
680
1.6
装置生产操作灵活,液化气和汽油产率高;汽油质量好,可达到90号汽油规格标准或作为93号汽油的主要调合组分;液化气经一般的气体分馏,丙烯纯度可达到聚合级精丙烯的要求,碳四各组分均为可满足后部加工装置要求;柴油馏分可与直馏柴油等调合为商品柴油。
所排放的污水、废气内的有害物质和一般催化裂化相当。
其工业结果见上表。
13、MGG和ARGG工艺的经济效益如何?
该工艺技术经济效益好,40万吨/年规模的MGG装置与催化裂化相比,每年可以增加利税1994万元,即每加工一吨原油提高效益50元。
扬州石油化工厂7万吨/年ARGG装置投产后也取得了十分可观的经济效益。
MGG、ARGG产品的进一步利用可带来更大的经济效益,一条应用途径是生产高辛烷值汽油和低碳烯烃。
低碳烯烃是重要的有机化工基本原料,发展下游加工,可生产更多的石油化工产品;另一条应用途径是液化气作为烷基化、MTBE和叠合等原料生产高品质的汽油组分,和MGG、ARGG汽油调合生产93号或更高标号的汽油,这对我国汽油的升级换代、逐步生产新配方汽油有着重要意义。
14、什么是MIO工艺技术?
多产异构烯烃(MIO)工艺技术是石油化工科学研究院开发的最大量地生产异构烯烃的新工艺技术。
该工艺技术以掺炼部分渣油的重质馏分油为原料,使用RFC催化剂,在特定的工艺条件下,采用特定的反应工艺条件,以达到大量生产异构烯烃(异丁烯、异戊烯)和高辛烷值汽油的目的。
15、什么是MIO工艺的技术特点?
MIO工艺技术以减压蜡油掺炼20%(质)左右减压渣油为原料,混合进料的残炭为3%、重金属Ni含量为3μg/g、V含量为5μg/g。
MIO工艺技术在加工上述原料时,其目的产物异构烯烃(iC4=+iC5=)产率可达到10.18%(质),丙烯+异构烯烃产率可达到20.41%(质),同时93号汽油产率可达到40.74%(质)。
MIO工业装置的原料性质、主要操作条件和产品分布见下表。
MIO工艺技术的催化剂为石油化工科学研究院开发的RFC专利催化剂。
它选用了新型催化材料和专利分子筛,具有良好的异构烯烃选择性和抑制氢转移反应的能力,可减少中间裂化产物烯烃进行氢转移反应的程度;它增加了反应物分子,特别是重油大分子对酸性中心的可接近性,加强了一次裂化深度;同时它优化了孔尺寸分布,较好地抑制了二次反应深度,改变了产物中碳三、碳四、碳五烯烃的比例。
RFC催化剂以上这些特点在工业试验中得到了较好的验证。
MIO工艺技术所使用的RFC催化剂不仅具有良好的异构烯烃选择性,同时具有良好的抗金属污染性能,在平衡剂Ni、V总污染量为5000μg/g的情况下,活性维持在60左右,表面积损失率只有47%。
主要操作条件
产品质量分布/%
反应压力/MPa
0.15
干气
3.51
反应温度/℃
531
液化气
29.72
回炼比
0.12
汽油
40.52
原料性质
柴油
18.07
密度(20℃)/g·cm-3
0.8898
焦炭
7.66
残炭%
3.1
主要烯烃产率
Ni/μg·g-1
2.66
C3=
10.23
V/μg·g-1
5.74
iC4=
4.82
iC5=
5.36
16、MIO工艺的产品性质如何?
MIO工艺技术的目标产物异丁烯在液化气中的浓度达到13.90%(质),丙烯浓度达到39.21%(质),异戊烯在汽油中的浓度达到12.69%(质),经过气体分馏后,丙烯纯度可达到聚丙烯的要求,异丁烯和异戊烯可作为MTBE和TAME的原料。
MIO工艺技术另一主要目标产物汽油的MON为81.5、RON为94.6。
与常规催化裂化汽油相比,MON提高1.0~1.6个单位、RON提高3.5~4.5个单位,安定性相当,符合国家93号高辛烷值汽油的标准。
MIO工艺技术所产柴油十六烷值为27~30,需用直馏柴油调合后方可出厂。
17、什么是MGD工艺技术?
多产液化气和柴油工艺技术(MGD-MaximizingGasandDiesel)是石油化工科学研究院(简称石科院)以重质油为原料,利用现有的催化裂化装置经过少量改造,即可在常规催化裂化装置上同时增产液化气和柴油,并大幅度地降低催化汽油中烯烃含量的一项新工艺技术。
MGD工艺技术的工业试验是石科院与福建炼油化工有限公司、广州石化总厂共同合作完成的。
MGD工艺技术要求新鲜裂化原料的轻重组分(蜡油和常渣)采用不同进料方式,进行选择性裂化反应。
重质原料油要求在高苛刻度下进行反应,以增加重质原料油的一次裂化深度并协调柴油馏分的生成和保留率。
为调节产品结构,MGD工艺技术采用粗汽油进料,通过粗汽油在密相床层的二次反应,一方面使其裂化成低碳烯烃,另一方面通过调节新鲜裂化原料的反应环境和苛刻度,增加柴油馏分的生成率。
MGD专用催化剂RGD-1是根据MGD工艺技术的工艺特点专门开发的一种催化剂。
该催化剂采用具有大、中孔结构的担体和具有二次孔分布的超稳Y型分子筛,作为提高重油转化能力以及提高柴油和液化气产率的基本材料,通过Y型分子筛孔内表面酸性调节Y型分子筛的酸强度,以控制柴油馏分的再裂化,并有利于汽油馏分的再裂化。
同时,采用择形分子筛能够进一步促进汽油馏分的链烯烃和烷烃的再裂化,以保证催化裂化催化剂提高柴油和液化气产率及降低汽油烯烃含量的综合效果。
18、MGD工艺的特点是什么?
MGD工艺技术具有以下特点:
(1)采用粗汽油控制裂化工艺技术。
通过粗汽油在密相上行床的二次反应,一方面使其汽油中低碳烯烃裂化及部分烯烃芳构化,达到降低汽油烯烃含量及提高汽油辛烷值的双重目的;另一方面通过调节新鲜裂化原料的反应环境和反应苛刻度,可较大幅度增加柴油馏分的生成量和保留度。
(2)重质原料油在高苛刻度下反应,轻质原料在低苛刻度下反应,新鲜裂化原料的轻重组分采用不同的进料方式进行选择性裂化,可增加重质原料油的一次裂化深度和柴油馏分的生成与保留率。
(3)常规催化裂化装置只要按MGD工艺技术的要求进行少量的改造,即可使原催化裂化装置灵活地增产液化气和柴油,液化气和柴油产率明显大于常规的催化裂化工艺技术,同时汽油中烯烃含量有较大幅度的降低。
(4)高价值产品产率(液化气+汽油+柴油)与常规催化裂化工艺技术相当。
(5)MGD工艺技术专用催化剂RGD-1具有优良的重油转化能力和抗金属污染能力,产品选择性特别是干气和焦炭选择性优异。
(6)MGD工艺技术具有高度的操作灵活性和产品灵活性,可以进行汽油方案、柴油方案、液化气+柴油方案和液化气等方案的操作,各操作方案的调整十分方便而且调整时间短。
(7)MGD工艺技术的反应机理表明,本工艺技术降低汽油烯烃和损失辛烷值不是一对矛盾。
在MGD的汽油裂化反应中,在汽油烯烃含量大幅度降低的同时,芳烃和异构烷烃含量大量增加,使RON、MON明显提高,这是MGD工艺技术在生产清洁燃料方面的重要特点。
19、什么是两段提升管催化裂化工艺技术?
石油大学开发了两段提升管催化裂化技术,强化和改善了催化反应过程,有效提高了反应深度、轻质油收率和液体产率,改善了产品质量,显著降低了催化汽油中的烯烃含量,增加了催化汽油中的异构烃和芳烃的含量,提高了汽油的辛烷值。
两段提升管催化裂化工艺技术的反应器如图所示,具有以下特点:
(1)两段提升管的总反应时间约为1.6s左右,相当于常规催化裂化反应时间的二分之一。
反应时间的缩短大大减少了过裂化反应的机会,为追求高转化率提供了条件。
(2)两段提升管催化裂化工艺技术能够在催化剂活性和选择性严重降低时,及时将其分出并更换为新的再生催化剂进行第二段反应。
这样,尽管总反应时间缩短,但催化剂的活性和选择性却大大提高,有利于中间产物的生成,提高反应过程中催化裂化反应的比重,减少过裂化反应和不利的二次反应,降低催化汽油中的烯烃含量,增加催化汽油中的异构烃和芳烃的含量。
石油大学用同种牌号的催化剂(RHZ-300、RHZ-200混合工业平衡催化剂),处理同种原料油(孤岛蜡油掺10减压渣油),分别采用最优的操作条件进行试验的结果表明,两段提升管催化裂化工艺技术具有明显的优势:
(1)大幅度提高了单程转化率(平均提高8.78%,最高提高10%以上)。
(2)高转化率下仍能获得好的产品分布:
汽油收率提高2%,轻油收率提高1%,液体收率提高6%。
(3)催化汽油中的烯烃含量降低10%,可降低到35%以下;催化汽油中的异构烷烃提高6~7%;芳烃含量也有相应的增加。
年加工能力10万吨/年催化装置工业试验显示,该项工艺技术可使装置处理能力提高30%至40%,轻油收率提高3%以上,液体产品收率提高2%至3%,干气和焦炭产率明显降低,汽油烯烃含量降低20%。
催化柴油密度下降,十六烷值提高。
20、什么是灵活多效催化裂化工艺(FDFCC)?
灵活多效催化裂化工艺FDFCC采用一套设有两根提升管反应器的催化裂化装置,通过双提升管实现工艺操作的可选择性,为汽油理想二次反应提供独立的改质空间和充分的反应时间,从而实现降低催化裂化汽油的烯烃含量和硫含量,改善柴汽比,提高催化汽油的辛烷值,同时增产液化气和丙烯的目的。
对比工业试验数据表明,采用该工艺技术与常规催化裂化工艺相比,催化汽油的烯烃含量降低20~30个体积百分点,硫含量可降低15~25%,辛烷值可提高1~2个单位。
同时该工艺对提高重油催化裂化装置的柴汽比和丙烯产率的效果也十分显著,柴汽比一般可提高0.2~0.7,丙烯产率也可提高3%~6%。
21、灵活多效催化裂化工艺(FDFCC)的特点是什么?
灵活多效催化裂化工艺(FDFCC)的特点是:
1、原料适应性强。
两个提升管反应器均可以在各自最优化的反应条件下单独加工不同原料油。
重油提升管反应器的原料可以是各种馏分油、常压渣油或掺炼部分减压渣油;第二提升管反应器原料可以是催化裂化汽油,也可以是掺入部分焦化汽油、热裂化汽油、直馏汽油和油田凝析油等炼厂