开关按键的注塑模具设计说明书.docx
《开关按键的注塑模具设计说明书.docx》由会员分享,可在线阅读,更多相关《开关按键的注塑模具设计说明书.docx(17页珍藏版)》请在冰豆网上搜索。
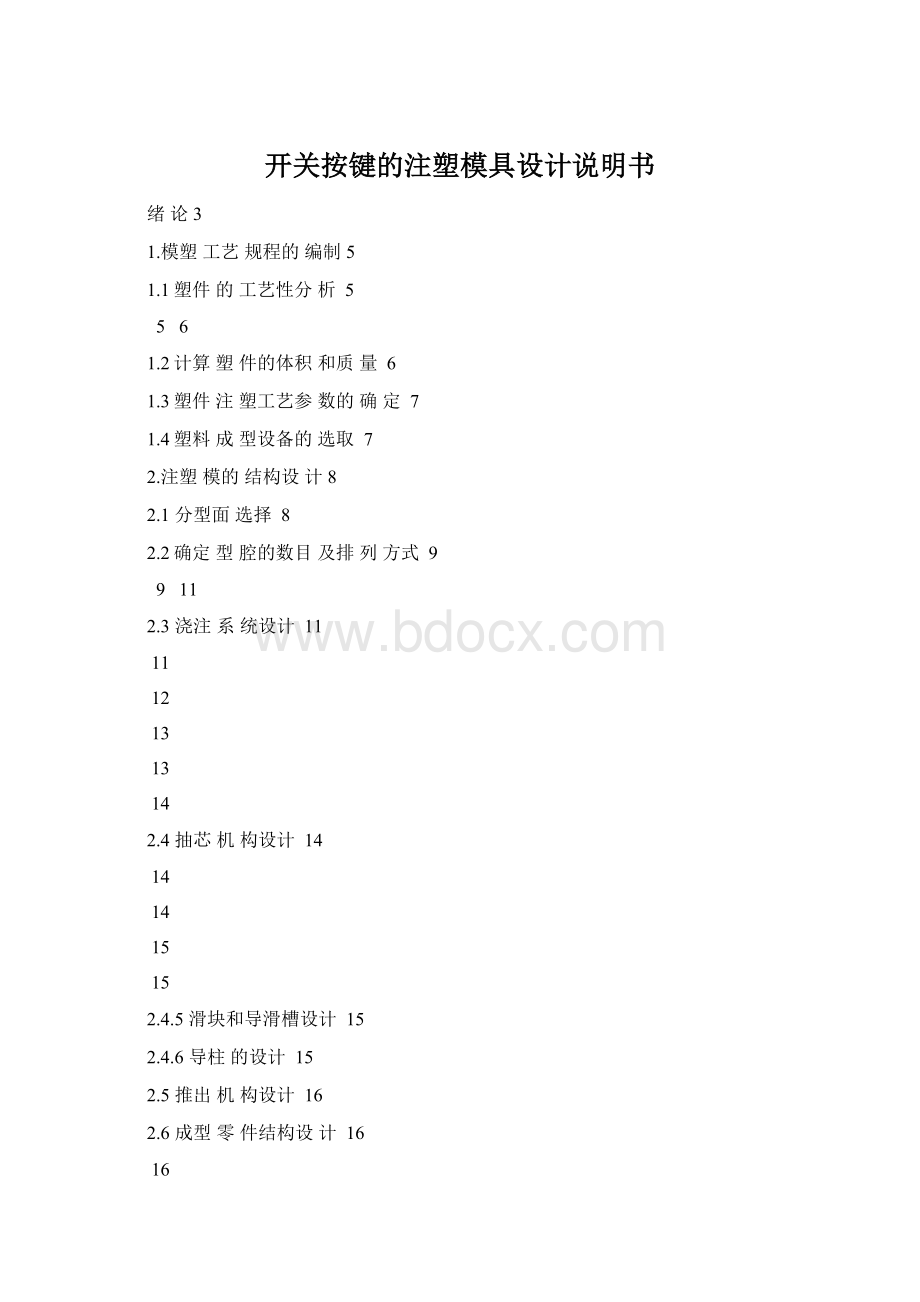
开关按键的注塑模具设计说明书
绪论3
1.模塑工艺规程的编制5
1.1塑件的工艺性分析5
56
1.2计算塑件的体积和质量6
1.3塑件注塑工艺参数的确定7
1.4塑料成型设备的选取7
2.注塑模的结构设计8
2.1分型面选择8
2.2确定型腔的数目及排列方式9
911
2.3浇注系统设计11
11
12
13
13
14
2.4抽芯机构设计14
14
14
15
15
2.4.5滑块和导滑槽设计15
2.4.6导柱的设计15
2.5推出机构设计16
2.6成型零件结构设计16
16
3.外壳注塑模具的有关计算18
4.模具加热和冷却系统的设计20
5.模具闭合高度确定20
5.1计算模具的闭合高度21
5.2校核注塑机的开,合模空间21
2121
6.注塑机有关参数的校核21
6.1模具合模时校核21
6.2模具开模时校核22
7.绘制模具总装图和非标零件工作图22
7.1本模具总装图和非标零件工作图见附图22
7.2本模具的工作原理22
结论23致谢24
参考文献25
绪论
大学的学习即将结束,毕业设计是其中最后一个实践环节,是对以前所学的知识及所掌握的技能的综合运用和检验。
随着我国经济的迅速发展,采用模具的生产技术得到愈来愈广泛的应用。
随着工业的发展,工业产品的品种和数量不断增加。
换型不断加快。
使模具的需要补断增加。
而对模具的质量要求越来越高。
模具技术在国民经济中的作用越来越显得更为重要。
根据业内专家预测,今年中国塑料模具市场总体规模将增加13%左右,到2005年塑料模具产值将达到460亿元,模具及模具标准件出口将从现在的9000多万美元增长到2005年的2亿美元左右,产值在增长,也就意味着市场在日渐扩大。
相当多的发达国家塑料模具企业移师中国,是国内塑料模具工业迅速发展的重要原因之一。
中国技术人才水平的提高和平均劳动力成本低都是吸引外资的优势,所以中国塑模市场的前景一片辉煌,这是塑料模具市场迅速成长的重要因素所在。
按照我国国家标准,模具共分为10大类46个小类,塑料模具是10大类中的l个大类,共有7个小类:
热塑性塑料注塑模、热固性塑料注塑模、热固性塑料压塑模、挤塑模、吹塑模、真空吸塑模和其他类塑料模。
塑料模的发展是随着塑料工业的发展而发展的,在我国起步较晚,但发展却很快,特别是最近几年,无论在质量、技术和制造能力上,都有很大发展。
但就总体来看,与国民经济发展和世界先进水平相比,差距仍较大,一些大型、精密、复杂、高效、长寿命的塑料模具每年仍大量进口。
据悉目前全世界年产出模具约650亿美元,其中塑料模具约为260亿美元。
我国1999年模具总产值245亿元.其中塑料模具约为82亿元,2000年近100亿元。
七类塑料模具中,注塑模具所占比例很大,约占全部塑料模具的80%左右。
塑料模具的主要用户是家用电器行业、汽车、摩托车行业、电子音像设备行业、办公设备行业、建筑材料行业、信息产业及各种塑料制品行业等。
目前国内年需塑料模具约130-140亿元,真中有30多亿元仍靠进口,进口量最多的塑料模具有汽车摩托车饰件模具、大屏幕彩电壳模具、冰箱洗衣机模具、通讯及办公设备塑壳模具、塑料异型材模具等。
大学三年的学习即将结束,毕业设计是其中最后一个实践环节,是对以前所学的知识及所掌握的技能的综合运用和检验。
随着我国经济的迅速发展,采用模具的生产技术得到愈来愈广泛的应用。
1.模塑工艺规程的编制
该塑件是外壳产品,其零件图如图7-1所示。
本塑件的材料采用尼龙1010,生产类型为中等批量生产。
图7-1外壳零件图
该塑件是外壳产品,其零件图如图7-1所示。
本塑件的材料采用尼龙1010,生产类型为中等批量生产。
1.1塑件的工艺性分析
1.1.1塑件的原材料分析
塑件的材料采用尼龙1010,属热塑性塑料。
从使用性能上看,尼龙1010是半透明,吸水小,耐寒性较好,坚韧、耐磨、耐油、耐水,抗霉菌,但吸水性大;从成型性能上看,塑件壁不宜取厚,并应均匀,脱模度不宜取小,尤其对厚壁及深高塑件更应取大。
受热时间不宜超过30min,料温高则收缩大,易出飞边,收缩小,取向性强,注射压力低易发生凹痕,波纹。
成型周期按塑件壁厚而定,厚则取长,薄则取短,为了减少收缩,凹痕、缩孔,一般宜取低模温、高注射压力的成形条件,以及采用白油作脱模剂;尼龙
1010的主要技术指标:
密度是1.04kg/dm3、比体积是0.96dm'/kg、吸水率是0.2〜0.4
、收缩率是1.3〜2.3s、熔点是205t/0c、热变形温度是550c、抗拉屈服强度是62Mpa、
3
拉伸弹性模量1.8X10Mpa、抗弯强度88Mpa、硬度9.75HB、击穿强度20KV/mm
另外,该塑件成型时易产生缩孔,凹痕,变形等缺陷,成型温度低时,方向性明显,凝固速度较快,易产生内应力。
因此,在成型时应注意控制成型温度,浇注系统应较缓慢。
散热冷却速度不易过快。
1.1.2塑件的结构和尺寸精度及表面质量分析
1.结构分析
从零件图上分析,该零件总体形状为长方形。
在宽度方向的一侧有两个高度6m,半
径为2mm的侧孔.因此,模具设计时必须设置侧向分型抽心机构,该零件属于中等复杂程度。
2.尺寸精度分析
该零件重要尺寸,如4mm,44mm等尺寸精度为皿巧级(GB/T14486-1993),次要尺寸,女口16mm,9mm,114mn3mn等的尺寸精度为皿丁5级(GB/T14486-1993)。
由以上分析可见,该零件的尺寸精度中等偏上,对应的模具相关尺寸加工可以得到保证。
从塑件的壁厚上来看,壁厚最大处为4mm壁厚均匀,符合尼龙1010的最小壁厚原则,在制件的转角处设计圆角,防止在此处出现缺陷,由于制件的尺寸较小,尼龙1010的强度较大不需增设加强。
制件尺寸选用尺寸精度MT5级(GB/T14486-1993),零件的尺寸精度中等,对应的模具相关零件的尺寸加工可以得到保证。
从塑件的壁厚来看,壁厚较均匀,有利于制件的成型。
3.表面质量分析
该零件的表面除要求没有缺陷、毛刺,内部不得有导电杂质外,没有什么特别的表面质量要求,故比较容易实现。
综上分析可以看出,注塑时在工艺控制得较好的情况下,零件的成型要求可以得到保证.
1.2计算塑件的体积和质量
计算塑件的质量是为了选用注塑机及确定模具型腔数。
3
计算塑件的体积:
V=14.8cm
计算塑件的质量:
根据设计手册可查得尼龙1010的密度为p=1.04kg/dm3
33
塑件质量:
M=Vp=14.8X103X1.04X103=15.4g
采用一模两件的模具结构,考虑其外形尺寸,注塑时所需压力和工厂现有设备等情况,初步选用注塑机XS—ZY—125型。
1.3塑件注塑工艺参数的确定
查找有关文献和参考工厂时间应用的情况,尼龙1010的成型工艺参数可作如下选择:
(试模时,可根据实际情况作适当调整)注塑温度:
包括料筒温度和喷嘴温度。
料筒温度:
后段温度ti选用190〜2100c;
中段温度t2
选用200〜2200c;
前段温度t3
选用210〜2300c;
喷嘴温度:
选用200〜2100c;
注塑压力一:
选用40〜100Mpa
注塑时间:
选用20〜90s;
保压压力:
选用65Mpa;
高压时间:
选用0〜5s;
冷却时间:
选用20〜120s;
总周期:
选用45〜220s;
后处理方法:
采用油、水、盐水;
后处理温度:
0
90〜100t/c;
后处理时间:
4h。
说明:
3.1:
预热和干燥均采用鼓风烘箱。
3.2:
凡潮湿环境使用的塑料,应进行调湿处理,在100〜1200c水中加热218h。
1.4塑料成型设备的选取
根据计算及原材料的注射成型参数初选注塑机为XS-ZY-125查材料知:
标称注射量/cm3125
螺杆直径/cm①42
注射容量/克125
5
注射压力/105Pa116.6锁模力/t90
2
最大注射面积/m2320
300
模具厚度/伽200
模板行程/伽300
喷嘴球半径/伽12
孔半径/伽4
推出两侧孔径/伽22
孔距/mm230
2.注塑模的结构设计
注塑模结构设计主要包括:
分型面选择、模具型腔数目的确定、型腔的排列方式、冷却水道布局、浇口位置设置、模具工作零件的结构设计、侧向分型与抽芯机构的设计、推出机构的设计等内容。
2.1分型面选择
模具设计中,分型面的选择很关键,它决定了模具的结构。
应根据分面选原则和塑件的成型要求来选择分型面。
制品在模具中的位置,直接影响到模具结构的复杂程度,模具分型面的确定,浇口的设置,制品尺寸精度和质量等。
因此,开始制定模具方案时,首先必须正确考虑制品在其中的位置;然后再考虑具体的生产条件(包括模具制造的),生产的批量所需的机械化和自动化程度等其他设计问题。
制品在模具中的位置设计时应遵循以下基本要求:
制品或制品组件(含嵌件)的正视图,应相对于注塑机的轴线对称分布,以便于成型;制品的方位应便于脱模,注塑模塑时,开模后制品应留在动模部分,这样便于利用成型设备脱模;当用模具的互相垂直的活动成型零件成型孔、槽、凸台时,制品的位置应着眼于使成型零件的水平位移最简便,使抽芯操作方便;如果制品的安置有两个方案,两者的分型面不相同又互相垂直,那么应该选择其中能使制品在成型设备工作台安装平面上的投影面积为最小的方案;长度较长的管类制品,如果将它的长轴安置在模具开模方向,而不能开模和取出制品的;或是管接头类制品,要求两个平面开模的,应将制品的长轴安置在与模具开模相垂直的方向。
这样布置可显着减小模具厚度,便于开模和取出制品。
但此时需采用抽芯距较大的抽芯机构(如杠杆的、液压的、气动的等);如果是自动旋出螺纹制品或螺纹型芯的模具,对制品的安置有专门要求;最后制品位置的选定,应结合浇注系统的浇口部位、冷却系统和加热系统的布置,以及制品的商品外观要求等综合考虑。
该塑件为塑料外壳,表面无特殊的要求,其分型面选择如下图所示:
图2-1
如图2-1所示取A-A向为分型面,不影响零件外观质量,抽芯在动模构简单。
图2-2
如图2-2所示取A-A向为分型面,抽芯在定模,抽芯机构复杂,应当避免定模抽芯从以上两个分型面的比较可以很容易的看出应该选择第一个分型方法,有利于模具成型。
2.2确定型腔的数目及排列方式
2.2.1模腔数量的确定
塑件的生产属中等批量生产,宜采用多型腔注塑模具,其型腔个数与注塑机的塑化能力,最大注射量以及合模力等参数有关,此外还受制件精度和生产的经济性等因素影响,有上述参数和因素可按下列方法确定模腔数量。
1.按注射机的额定锁模力确定型腔数量N1
N1=(F/PC)/A-B/A
其中:
F注塑机的锁模力N
PC型腔内的平均压力MPa
2
A每个制件在分型面上的面积(伽)
B流道和浇道在分型面上的投影面积(伽2)
在模具设计前为未知量,根据多型腔模具的流动分析B为(0.2〜0.5),常取B=0.35,熔体内的平均压力取决于注射压力,一般为25〜40MPa实际所需锁模力应小于选定注塑
机的名义锁模力,为保险起见常用0.8F,贝
N仁(0.8F/PC)/1.35A=0.6F/(APC)=900000X0.6/(30X3870.6)=4.65(个)
2.注射机注塑量确定型腔数目N2
N2=(G-C)/V
3
其中:
G注射机的公称注塑量(伽)
V单个制件体积(伽3)
3
C流道和浇口的总体积(伽)
生产中每次实际注塑量应为公称注塑量的0.8倍,同时流道和浇道的体积为未知量,
据统计每个制品所需浇注系统是体积的0.2〜1倍,现取C=0.6则:
N2=0.6G/1.6V=0.375G/V=(0.375X125)/14.8=3.1(个)
从以上讨论可以看到模具的型腔个数必须取N1,N2中的较小值,在这里可以选取的
个数是1,2,3,个,考虑的制件的取出和模具的开模等情况,以及模具的主流道长度最好小于60mm以防止因为注塑压力的降低而带来的制件充型不足等缺陷。
我们所设计的端盖注塑模具采用一模一件的方案,即N=1
2.2.2型腔的排列方式
图2-2-2-1
本塑件在注塑时采用一模一件,综合考虑浇注系统,模具结构的复杂程度等因素采取如图2-2-2-1所示的型腔排列方式。
采用2-2-2-1的型腔排列方式的最大优点是便于设置侧向分型抽芯机构。
2.3浇注系统设计
2.3.1主流道设计
制品在模具中的位置,直接影响到模具结构的复杂程度,模具分型面的确定,浇口的设置,制品尺寸精度和质量等。
因此,开始制定模具方案时,首先必须正确考虑制品在其中的位置;然后再考虑具体的生产条件(包括模具制造的),生产的批量所需的机械化和自动化程度等其他设计问题。
制品在模具中的位置设计时应遵循以下基本要求:
制品或制品组件(含嵌件)的正视
图,应相对于注塑机的轴线对称分布,以便于成型;制品的方位应便于脱模,注塑模塑时,开模后制品应留在动模部分,这样便于利用成型设备脱模;当用模具的互相垂直的活动成型零件成型孔、槽、凸台时,制品的位置应着眼于使成型零件的水平位移最简便,使抽芯操作方便;如果制品的安置有两个方案,两者的分型面不相同又互相垂直,那么应该选择其中能使制品在成型设备工作台安装平面上的投影面积为最小的方案;长度较长的管类制品,如果将它的长轴安置在模具开模方向,而不能开模和取出制品的;或是管接头类制品,要求两个平面开模的,应将制品的长轴安置在与模具开模相垂直的方向。
这样布置可显着减小模具厚度,便于开模和取出制品。
但此时需采用抽芯距较大的抽芯机构(如杠杆的、液压的、气动的等);如果是自动旋出螺纹制品或螺纹型芯的模具,对制品的安置有专门要求;最后制品位置的选定,应结合浇注系统的浇口部位、冷却系统和加热系统的布置,以及制品的商品外观要求等综合考虑。
根据XS-ZY-125型注塑机喷嘴的有关尺寸
喷嘴前端孔径:
d0=①4mm
喷嘴前端球面半径:
R0=12mm
根据模具主流道与喷嘴的关系:
R=R0+(1〜2)mm
D=d0+(0.5〜1)mm
取主流道的球面半径:
R=13mm
取主流道的小端直径:
d=①4.5mm
为了方便将凝料从主流道中拔出,将主流道设计为圆锥形式其斜度取1〜3度经换算得主流道大端直径D曲8.5mm为了使料能顺利的进入分流道,可在主流道的出料端设计半径r=5mm的圆弧过渡。
2.3.2分流道设计
由于分流道可将高温高压的塑料熔体流向从主流道转换到模腔,所以,设计时不仅要求熔体通过分流道时的温度下降和压力损失都应尽可能小,而且还要求分流道能平稳均衡地将熔体分配到各个模腔。
从这些要求出发,分流道应设计得短而粗,但过短过粗时又会增加塑料消耗量,并使冷却时间延长,另外还会使模腔布置发生困难。
因此,恰当合理的分流道形状和尺寸应根据制品的体积、壁厚、形状复杂程度、模腔的数量以及所用塑料的性能等因素综合考虑。
分流道的种类和截面形状很多,从压力传递角度考虑,
要求有大的流道截面积,从散热少考虑应有小的比表面积•圆形截面最理想,使用越来越多,方形截面由于脱模困难,多不采用,梯形截面比表面虽然大些,但因加工和脱模方便,应用广泛,所以分流道采用梯形截面分流道。
以其t/d=2/3-4/5,梯形侧边斜度5°-15°
为宜.截面尺寸由经验公式计算•但计算结果须按现有刀具尺寸圆整,并校核熔料剪切速率在5X102〜103S-1范围内,方才合理。
经验公式d0.27、M4L
式中d—圆分流道直径或各截面分流道的当量直径
M—流经的塑料物料质量
L—该分流道的长度此长度根据型腔板尺寸确定
d0.27■27.596£172.88伽根据刀具圆整为3mm
此式适用于壁厚3伽以下,小于200g的塑料。
对于高粘度物料,适当矿大25%,一般分流道直径在3〜10m,高粘度物料可达13〜16m,分流道表面粗糙度常取
Ra>0.63〜1.6,以增大外层流动阻力,避免熔流表面滑移,使中心层有较高的剪切速率。
取浇道斜度为10°根据几何关系可算出d仁1.94伽t=3伽
截面形状为U型,在流道设计中要减小压力损失,则希望流道的面积大。
要减少传热损失,又希望流道的面积小。
因此可用流道的面积与周长的比值来表示流道的效率。
U型实质上是一种双梯形流道截面。
效率为0.195D
分流道的尺寸:
3.8---7.5
分流道直径/mm选取6mm
分流道表面粗糙度:
分流道表面不要求太光洁,表面粗糙度常取1.25—2.5Ra卩m
这可增加对外层塑料熔体流动阻力,使外层塑料冷却皮层固定,形成绝热层。
有利于保温。
但表面不得凸凹不平,以免对分型不利。
2.3.3浇口设计
浇口是流道和型腔之间的连接部分,也是注塑模进料系统的最后部分,其基本作用
是:
使从流道来的熔融塑料以最快的速度进入并充满型腔。
型腔充满后,浇口能迅速冷却封闭,防止型腔内还未冷却的热料回流。
浇口的设计与塑件形状,断面尺寸,模具结构,注塑工艺条件(压力)及塑料性能等因素有关。
浇口截面要小,长度要短,因为只有这样才能满足增料流速度,快速冷却封闭,便于与塑件分离,以及浇口残痕最小等要求。
根据塑件的成型要求及型腔的排列方式,选用侧浇口较为理想。
设计时考虑选择从塑件的表面进料,而且在模具结构上采取镶拼型腔、型心,有利于填充、排气。
故采用轮辐式浇口,查表初选尺寸为(bxlxh)2mr^1mnh<1mm试模时修正。
2.3.4排气结构的设计
在注塑模具的设计过程中,必须考虑排气结构的设计,否则,熔融的塑料流体进入模具型腔内,气体如不能及时排出会使制件的内部有气泡,甚至会产生很高的温度使塑料烧焦,从而出现废品。
排气方式有两种:
开排气槽排气和利用合模间隙排气。
由于端盖注塑模是小型镶拼式模具,可直接利用分型面和镶拼间隙进行排气,而不需在模具上开设排气槽。
(尼龙1010塑料的最小不溢料间隙为0.03mm间隙较小,再加
上尼龙1010的流动性较好,也不宜开排气槽。
2.3.5主流道衬套的选取
主流道衬套时应注意以下事项:
对于小型注塑模,可将主流道衬套与定位环设计成
一个整体,但在多数情况下均分开设计;主流道衬套应选用优质钢材(如T8A等),热处理后硬度为53〜57HRC衬套的长度应与定模配合部分的厚度一致,主流道出口处的端面不得突出在分型面上,否则不仅会造成溢料,而且还会压坏模具;衬套与定模之间的配合采用H7/m6。
为了提高模具的寿命在模具与注塑机频繁接触的地方设计为可更换的主流道衬套形
式,选取材料为T8A热处理以后的硬度为50〜55HRC主流道衬套和定模的配合形式为H7/m6的过渡配合。
2.4抽芯机构设计
此设计的塑件侧壁有两个突台,它们均垂直于脱模方向,阻碍成型后塑件从模具脱出因此成型小突台的零件必须做成活动的型心,即必须设置抽芯机构.本模具采用斜销抽芯机构。
2.4.1确定抽芯距抽芯距一般大于侧凹的深度本副模具设计中必须高于制件最小高度的一半
H1=B2/2=22.5/2=11.25mm
另加3〜5mnm勺抽芯安全系数,可取抽芯距S抽=15mm。
2.4.2确定斜销的倾角
斜导柱的倾角a是斜销机构的主要技术参数,它与抽拔距和抽芯距有直接关系,一
般取15°〜25°本副模具取a=20°。
2.4.3确定斜销的尺寸斜导柱的直径取决于抽拔力及倾角可按设计资料有关公式进行计算,本例可采用经
验估值,取斜导柱的直径d=O10mm。
2.4.4斜导柱的长度
可根据抽拔距,固定端模板的厚度,斜销直径及斜角大小确定:
L=L1+L2+L3+L4+L5
=D/2xtana+h/cosa+d/2tana+H/sina+(5〜10)
=51.38mm
取:
L=52mm
2.4.5滑块和导滑槽设计
由于侧凹的尺寸较小型芯滑块可采用整体式加工增加强度,导滑槽的导滑长度和定位装置的设计可采用经验法,侧向抽芯的抽拔距较小,也无须滑块的定位装置。
2.4.6导柱的设计
导柱的选择直形导柱和阶梯形导柱的前端都设计为锥形,便于导向。
两种导柱都可以在工作部分带有贮油槽。
带贮油槽的导柱可以贮存润滑油,延长润滑时间。
直形导柱用于塑件生产批量不大的模具,可以不用导套。
阶梯形导柱用于塑件大批量生产的模具,或导向精度要求高,必须采用导套的模具,装在模具另一侧的导套安装孔可以和导柱安装孔采用同一尺寸,一次加工而成,保证了严格的同轴,本模具采用有肩导柱I型
导柱直径尺寸随模具分型面处模板外形尺寸而定,模板尺寸愈大,导柱间的中心距应愈大,所选导柱直径也应愈大。
除了导柱长度按模具具体结构确定外,导柱其余尺寸随导柱直径而定。
本模具的中心距为150mm本模具选用I型,直径为16mm选用
d=16mm,L=71mm,L1=25mfm肩导柱.
2.5推出机构设计
图2-5-1
如图2-5-1所示模具开模后,塑件包紧动模型心的力并不大,适当考虑脱模斜度,采用顶杆并不会将塑件顶变形,且模具结构简单。
图2-5-2
如图2-5-2所示是采用推管和顶杆联合顶出,顶出平稳,塑件不会变形,但推管与中间的型心想配合,会造成制造和装配上的困然。
由以上两种方法的比较不然看出图2-5-1的方法比图2-5-2的方法更经济也可以给制造带来方便。
2.6成型零件结构设计
2.6.1定模板与动模板的设计
本副模具型腔板开设在定模板,由于制件结构简单,模具牢固,不易变形,制件没拼界逢,适用用于本制件的模具。
如图所示:
图2-6-1-1
料选用T8A,硬度在50HRC以上。
根据分流道与浇口的设计要求,分流道与浇口设在凹模型腔上其结构见上图所示。
动模板尺寸:
根据矩形凹模最小壁厚经验曲线知,此塑件的成型压力小于30MPA,
那么尺寸见下图:
图2-6-1-2
由经验可知:
长为150mm.
宽为260mm.
凹模高为h=45mm
17mn为制件高
加工可以直接用铣刀铣出,也可以用成型电极。
为了节约成本。
在这里我选用铣刀铣。
3.外壳注塑模具的有关计算
4.
本例中成型零件工作尺寸计算时均采用平均尺寸,平均收缩率平均制造公差和平均磨损率来计算。
总高;