NGL回收过程危险有害因素分析详细版.docx
《NGL回收过程危险有害因素分析详细版.docx》由会员分享,可在线阅读,更多相关《NGL回收过程危险有害因素分析详细版.docx(6页珍藏版)》请在冰豆网上搜索。
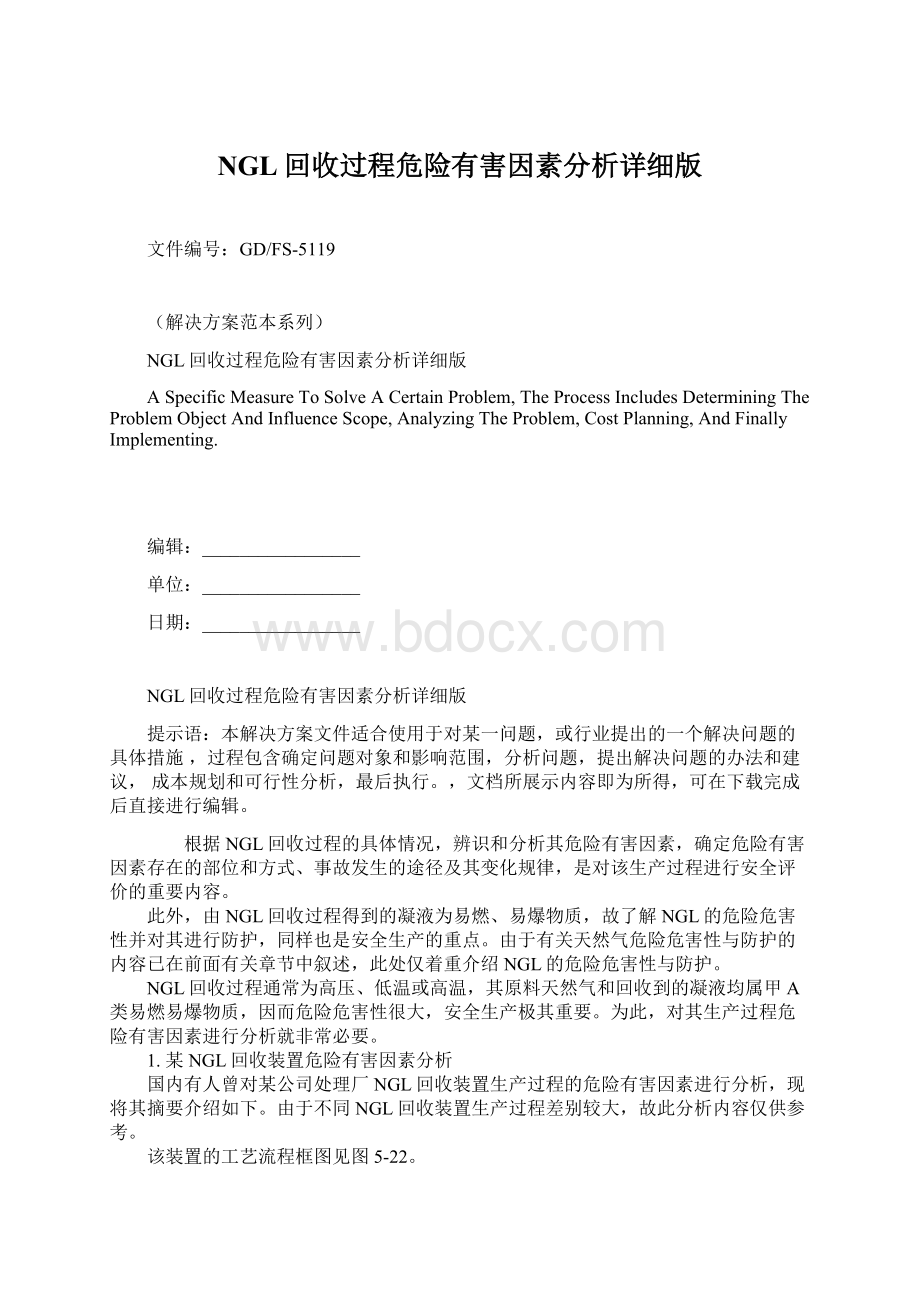
NGL回收过程危险有害因素分析详细版
文件编号:
GD/FS-5119
(解决方案范本系列)
NGL回收过程危险有害因素分析详细版
ASpecificMeasureToSolveACertainProblem,TheProcessIncludesDeterminingTheProblemObjectAndInfluenceScope,AnalyzingTheProblem,CostPlanning,AndFinallyImplementing.
编辑:
_________________
单位:
_________________
日期:
_________________
NGL回收过程危险有害因素分析详细版
提示语:
本解决方案文件适合使用于对某一问题,或行业提出的一个解决问题的具体措施,过程包含确定问题对象和影响范围,分析问题,提出解决问题的办法和建议,成本规划和可行性分析,最后执行。
,文档所展示内容即为所得,可在下载完成后直接进行编辑。
根据NGL回收过程的具体情况,辨识和分析其危险有害因素,确定危险有害因素存在的部位和方式、事故发生的途径及其变化规律,是对该生产过程进行安全评价的重要内容。
此外,由NGL回收过程得到的凝液为易燃、易爆物质,故了解NGL的危险危害性并对其进行防护,同样也是安全生产的重点。
由于有关天然气危险危害性与防护的内容已在前面有关章节中叙述,此处仅着重介绍NGL的危险危害性与防护。
NGL回收过程通常为高压、低温或高温,其原料天然气和回收到的凝液均属甲A类易燃易爆物质,因而危险危害性很大,安全生产极其重要。
为此,对其生产过程危险有害因素进行分析就非常必要。
1.某NGL回收装置危险有害因素分析
国内有人曾对某公司处理厂NGL回收装置生产过程的危险有害因素进行分析,现将其摘要介绍如下。
由于不同NGL回收装置生产过程差别较大,故此分析内容仅供参考。
该装置的工艺流程框图见图5-22。
由图可知,原料气以0.20~0.30MPa、25℃进入一级分离器进行气液分离,分离出的气体经压缩机两级增压至3.0MPa(温度为150℃)后,经空冷器冷却至50℃、水冷器冷却至30℃进入压缩机出口分离器。
分离出的凝液经节流降压后送至液烃分离器,分出的天然气经分子筛脱水后在2.5MPa、30℃下进膨胀机组增压端增压至4.0MPa、62℃,然后由水冷器冷却至30℃进入三股流板翅式换热器,与初级吸收塔顶低温外输干气及来自低温分离器经节流降压后的低温液烃换热,降温至-40℃进入低温分离器。
低温分离器顶部气相以4.0MPa、-40℃进入膨胀机膨胀制冷至1.4MPa、-76℃。
低温分离器底部液相以1.3MPa、-64℃进入三股流板翅式换热器升温至25℃后去凝液分馏装置。
经膨胀机膨胀制冷后的低温气体在1.4MPa、-80℃进入初级吸收塔顶部。
脱乙烷塔塔顶气以1.4MPa、0℃进入初级吸收塔底部。
初级吸收塔塔顶气在1.4MPa、-80℃下先进入三股流板翅式换热器复热至21℃,再与脱丁烷塔塔底稳定轻烃换热至45℃后作为商品气外输。
初级吸收塔塔底凝液先进入脱乙烷塔顶部脱除乙烷,再进入脱丁烷塔分馏为液化石油气和稳定轻烃。
(1)工艺、设备或设旅的火灾爆炸危险因素
天然气凝液回收装置的脱水、气液分离、粉尘过滤、气体增压和膨胀、冷却和冷凝以及产品储运等系统的设备和设施,在运行时均有发生火灾爆炸的可能性,其原因主要如下。
②设备和管予制造、安装及检修缺陷装置中各个工艺设备和转动机械制造、安装,检修和焊接缺陷,以及密封损坏等原因导致开裂损坏或密封失效。
各个系统管线阀门及设备附属接管阀门的本体、焊缝及密封件因存在缺陷而损坏。
特别是高压管线,其管线焊缝和阀门出现缺陷的危险陛较大,如果不能严格控制焊接、安装质量,就可能发生泄漏,导致重大火灾爆炸事故发生。
②腐蚀失效各个系统工艺物料中腐蚀介质如H2S、CO2、地层水中的氯离子等的存在,严重时可造成设备、管线和阀门因腐蚀失效,从而导致泄漏和破裂。
③超压损坏装置中压力容器如高效旋流分离器、各级分离器和低温分离器等因压力容器窜气、堵塞、自控系统和安全阀故障等造成超压,严重时可能导致管线和压力容器破裂。
由于上述原因造成管线、设备和设施泄漏、损坏或破裂均可导致工艺物料泄漏,遇明火即可发生火灾爆炸事故。
④设备等低温损坏由于低温系统分离器、板翅式换热器以及膨胀机等设备、机械、管线及配套阀门中的工艺物料温度可低至-76%,故可发生如下低温损坏:
a.低温设备和管线选材不当,发生低温脆断;b.低温凝液去火炬放空时,可能因迅速气化降温造成管线及管架承受很大温度应力而引起断裂;c.低温凝液流经调节阀、减压阀等急剧气化所形成的高速气流,对管线弯头、法兰造成冲蚀损坏。
低温损坏严重时可造成低温凝液泄漏,而且一旦泄漏就会急剧气化与扩散,遇明火即可发生火灾爆炸事故。
⑤加热炉操作失误加热炉(用于加热分子筛脱水塔再生气)炉膛明火为危险源之一,以下因素可能引起火灾爆炸事故:
a.炉管由于局部过热而烧穿,造成炉管内气体泄漏;b.炉管、弯头选材不当或连接部位有缺陷出现开裂,造成炉管内气体泄漏;c.点火时未对炉膛内彻底吹扫(尤其是点火失败后再点火),或因点火工具不可靠、直接利用炉膛高温点火而引起爆炸(点火爆炸);d.由于紧急停电或燃料气系统波动等导致炉膛熄火,但因未及时切断燃料气源,使燃料气在炉膛高温下再点燃而引起爆炸(熄火爆炸);e.流程倒错,例如误将系统中高压天然气引入炉管加热,引起超压并造成炉管破裂漏气。
⑥重沸器内漏重沸器采用导热油加热,如果导热油发生泄漏,将会造成脱乙烷塔和脱丁烷塔塔内物料急剧气化升温升压。
可能引起塔器物料泄漏造成火灾爆炸事故。
⑦机泵泄漏脱丁烷塔塔顶液化气回流泵(出口压力1.3MPa)、导热油泵(介质温度可达280℃)、原料气压缩机(出口压力达3MPa)以及膨胀机(出口流体温度为-76℃)的安装、检修缺陷及作业不当等均可造成部件和机械密封损坏而出现泄漏,遇明火即可发生火灾爆炸事故。
其中,液化气、天然气泄漏严重时出现“蒸气云”爆炸。
⑧稳定轻烃和石油液化气灌装失误稳定轻烃产品采用敞开式装车,操作不当或机具故障可能导致泄漏,如遇装车车辆电气打火、排气管火星以及液流静电、人体静电和其他明火而着火爆炸。
液化气采用密闭装车相对危险较小,但液流静电和人体静电有可能引起火灾爆炸。
(2)电气、仪表的火灾、爆炸危险因素
①电气设备、仪表产生火花装置电气设备因接地设施失效、线路绝缘损坏、短路、接点接触不良,设备和线路、照明不符合防爆要求等产生火花以及电动仪表因能量积聚产生并泄放火花等,都是造成泄漏出的易燃易爆物质发生火灾爆炸的重要点火源。
②自控仪表及联锁保护失效自控系统仪表出现故障、信号受到电磁干扰、出现错误显示或产生误动作,DCS系统及安全仪表系统(SIS)出现故障,都可能造成压缩机、脱乙烷塔、脱丁烷塔、吸收塔以及其他设备的温度、压力、流量、液面仪表指示失真,严重时导致超压、超温、操作失控、物料溢出等后果,进而引发火灾爆炸事故。
③可燃气体检测报警器失灵装置各部位的可燃气体检测报警器失灵,将会导致泄漏的易燃易爆气体聚集,并不易发现,从而延误可燃气体泄漏事故处理时机,导致火灾爆炸事故。
(3)违章操作和检修
①正常生产期间由于违章操作可能引发火灾爆炸事故,例如:
a.直接向地面排放易燃易爆凝液;b.在易燃易爆危险区私自动火;c.使用非防爆工具等。
②检修作业期间不严格执行检修安全规程,可能在有限空间内发生火灾爆燃事故。
例如:
a.不坚持用火票制度;b.设备、管线吹扫、置换不彻底或未充分通风,就进行焊接或其他动火作业等。
(4)噪声
本装置的噪声源为天然气压缩机组、膨胀机组、空气冷却器、泵等,其中主要噪声源为压缩机组,如其装设的消音器失效将会出现严重噪声危害。
(5)机械伤害
装置区的燃气驱动天然气压缩机组、膨胀机组、导热油泵、液化气回流泵、混烃泵、潜污泵等转动机械具有转速较高、结构较复杂等特点。
其中,天然气压缩机和导热油泵轴功率较大。
它们在高速运转时可能发生损坏、伤人甚至停工停产等事故。
尤其是转动部分防护罩不完善、操作人员违章戴手套操作等,都会发生机械伤害事故。
(6)高处坠落
装置中各塔高度均在5m以上,其中脱乙烷塔、脱丁烷塔高12.8m,装置外的放空火炬高40m,人员在操作、巡检、检修作业中,有可能发生滑跌、坠落等伤亡事故。
(7)高温环境灼伤及低温环境冻伤
①高温灼伤装置中的加热炉、导热油炉、脱丁烷塔及重沸器、分子筛脱水塔及其再生气分离器、再生气换热器等操作温度在220~330℃之间,当设备及附属管线出现损坏,保温层破损以及操作不当时,作业人员有被喷出的高温介质灼伤和与高温介质接触灼伤的危险。
②低温冻伤装置低温系统的低温介质(例如低温分离器内的凝液),以及脱丁熔塔塔顶产品液化石油气等,在生产过程中可能因操作不当、设备和阀门发生故障等出现泄漏,急剧气化降温,造成作业人员低温冻伤事故。
(8)其他危害
①防雷、防静电接地设备和建(构)筑物的防雷、防静电接地设备的设置和配备不合格,引发雷击和静电火花,可能导致设备、设施损坏和火灾爆炸事故。
②管路加药和酸洗 a.因水质原因,循环水系统管线易于结垢。
管路结垢后采用酸洗清除时,含硫垢层会分解释放出硫化氢,有可能引起硫化氢中毒事故;b.循环水系统需要添加阻垢剂、缓蚀剂和杀菌剂等化学药品,作业人员接触后可对皮肤、眼睛产生刺激和腐蚀。
其中的有机膦表面活性剂组分具有增加人体皮肤细胞渗透性的副作用,可使毒物和病菌易于进入人体,有可能降低加药人员的免疫力。
③水合物冻堵装置低温系统可能生成水合物,造成设备或管线堵塞甚至破裂,可能造成设备、设施损坏、停工停产,若处理不当,甚至可能引发火灾爆炸等事故。
④意外停电因供配电系统及电气设备故障发生意外停电,会导致停工停产,处理不当还可能造成设备、设施及部件损坏,甚至引发火灾爆炸、窒息中毒等其他事故。
通过上述危险有害因素分析,就可有针对性地对所找出的各种危险有害因素制订相应的防护对策措施,以保证该NGL回收装置安全生产。
2.事故案例
现将澳大利亚长滩(Longford)天然气处理厂爆炸事故案例介绍于下。
长滩位于澳大利亚墨尔本以东180km处,在维多利亚省境内。
某公司在此经营有3座天然气处理厂和一座原油稳定厂。
原料气来自巴斯海峡(BassStrait)的气井。
其中,第一座天然气处理厂(GP1)建于1969年,其NGL回收装置采用低温油吸收法,工艺流程见图5-23。
第二座和第三座天然气处理厂(GP2和GP3)则分别建于1976年和1983年,其NGL回收装置采用透平膨胀机制冷的冷凝分离法。
1998年9月25日12时25分,GP1厂发生一系列爆炸并引发大火,消防人员用了31小时才将火扑灭,事故导致2人死亡及8人受伤,GP2和GP3厂以及原油稳定厂停产两周,巴斯海峡相关气井也被迫关井。
事故发生后中断了墨尔本及其他地区大部分用户的天然气供应,直到10月14日才恢复供气(事故发生时正值当地冬季用气高峰)。
这是澳大利亚历史上最严重的工业事故之一。
(1)事故经过
图5-23中脱乙烷塔塔底油进出该塔重沸器(GP905)管程的温度分别为60%和90%,蒸馏塔塔底热的贫吸收油先经换热器GP922再去重沸器,进出该重沸器壳程的温度分别为230%和120℃。
因此,该重沸器正常情况下系在热态工况下运行,设计未予考虑低温工况的要求。
该装置热的贫吸收油与冷的富吸收油(饱和吸收油)正常工况下换热流程示意图见图5-24。
事故发生前一天晚上,进入GP1的原料气流量和重烃含量增加,再加上十多天前塔底液位调节阀TRC3B已经损坏,低温吸收塔B中的凝液增多,液位升高,事故发生前夜班操作人员虽通过旁通阀调节液位,但效果不很理想,所以白班接班人员关闭了该旁通阀,导致情况进一步恶化。
9月25日8时19分,脱乙烷塔与蒸馏塔出现故障,吸收油泵GP1201和GP1202停止运转,所以热的贫吸收油不再流经GP922和GP905,操作人员虽试图重新启动吸收油泵,但未成功。
在此期间,由低温吸收塔进入脱乙烷塔冷的富吸收油(饱和吸收油,-30℃)和经过闪蒸的凝液仍继续流经GP922和GP905.使得GP922和GP905的温度降至-48℃,导致GP905壳体法兰泄漏。
为诊断故障和维修,10时30分操作人员中断该厂进料,但未释放系统压力。
中午12时左右,操作人员发现GP922和GP905以及与之相连的管线表面结霜,于是决定重新启动吸收油泵使换热器升温。
但是,此时由于-48℃低温已使GP905的焊缝脆裂。
12时17分,当第一台吸收油泵启动后,温度为230。
C的贫吸收油进入GP905的壳程,而管程温度却低达-48℃。
12时25分,由于温度骤升造成的热冲击使GP905解体,数分钟内泄漏了10t工艺物料,形成了易燃的蒸气云。
之后,快速扩散的蒸气云被170m外的加热炉点燃,然后又回燃至GP905所在位置,并引起一系列后继火灾。
先是厂内一储存12t物料的储存库着火,继而蔓延到一个主要的管线桥架,使桥架上许多管线烧裂,管线泄漏的物料又使火势加大。
在随后的1.5小时内出现了三起重大泄漏,其中,有一处管线破裂后形成高达100m的大火球。
更糟糕的是,很难在事故现场隔离其他可燃物,大火燃烧了两天后才被扑灭。
事故导致2人死亡和8人受伤,他们都是最初在GP905附近排除故障的操作人员。
GP2和GP3两座处理厂也因这次事故而停产,花费数日才完全隔离了它们与GP1厂的85处连接点,然后再重新投产。
(2)事故原因
事故处理完毕后,澳大利亚皇家委员会组成专门的调查组对这次事故进行详细调查,认为导致该事故的主要原因为:
①该厂的工艺系统设计存在缺点,包括:
工艺设备的材质选择和制造没有考虑低温工况的要求,也没有考虑温度骤升的影响;低温吸收塔液位调节设计不恰当;紧急停车系统设计不合理;工艺系统缺少足够的隔离措施,发生火灾爆炸时没有自动截断装置隔离其他可燃物料。
②生产管理缺少科学、合理而且针对性强的应急预案,操作人员缺乏应急预案的培训和演练工作。
③该厂在“报警模式”下坚持生产,操作人员平均每天需要处理400起报警,使得他们对此不再敏感,只是有选择性地处理那些他们认为重要的报警,对其他报警通常不做任何响应就确认取消,包括本案例中低温吸收塔液位报警就被操作人员归于不重要的范畴。
④现场没有工艺工程师提供技术支持。
当操作人员发现重沸器GP905及相连管线结霜这一异常情况时,既没有人意识到问题的严重性,又没有人告诫他们要避免低温设备的温度骤升。
⑤交接班时沟通不充分。
在本案例中,晚班操作人员未向白班操作人员交代清楚吸收塔内液位高的情况,结果白班操作人员关闭了调节阀TRC3B的旁通阀,使得情况进一步恶化。
⑥尽管该公司对新建的GP2和GP3厂进行过HAZOP分析,但对GP1厂的工艺装置HAZOP分析一直拖延,始终没有落实。
⑦安全审计质量不高。
尽管在事故发生前的一年内曾对该厂进行过一次全面的安全审计,但未发现任何可能导致本次事故的危险因素,特别是居然没有发现该厂从未应用HAZOP方法对工艺装置进行过分析。
⑧汇报程序导致关键信息遗漏。
在1998年8月28日曾发生过类似事故,但未产生严重后果,而且操作人员没有向主管部门报告该事件,因此工厂未能从中吸取教训。
⑨强调职业安全但却忽视工艺安全。
在天然气处理厂,事故可以分为两类:
一类是发生率高但后果较轻的职业安全事故,例如跌落、滑倒摔伤等;另一类是发生率低但后果非常严重的工艺安全事故,包括火灾爆炸等灾难性事故。
该厂的事故报告主要是职业危害,不包括工艺故障事件和未遂事故报告,也不对它们进行调查,并忽视了对工艺故障可能导致重大工艺安全事故的预防。
总之,造成这次事故的原因是多方面的,例如培训、事故调查、安全审计等多项安全管理要素都存在缺失,特别是没有应用HAZOP方法对工艺装置进行分析,使得该厂错过了预防这次事故的机会。
针对本次事故,AndrewHopkins对其发生原因进行了非常细致的分析,图5-25为其对这次事故中各种错综复杂原因的分析汇总。
可在这里输入个人/品牌名/地点
Personal/BrandName/LocationCanBeEnteredHere