知名日企SPC完美培训教材.docx
《知名日企SPC完美培训教材.docx》由会员分享,可在线阅读,更多相关《知名日企SPC完美培训教材.docx(51页珍藏版)》请在冰豆网上搜索。
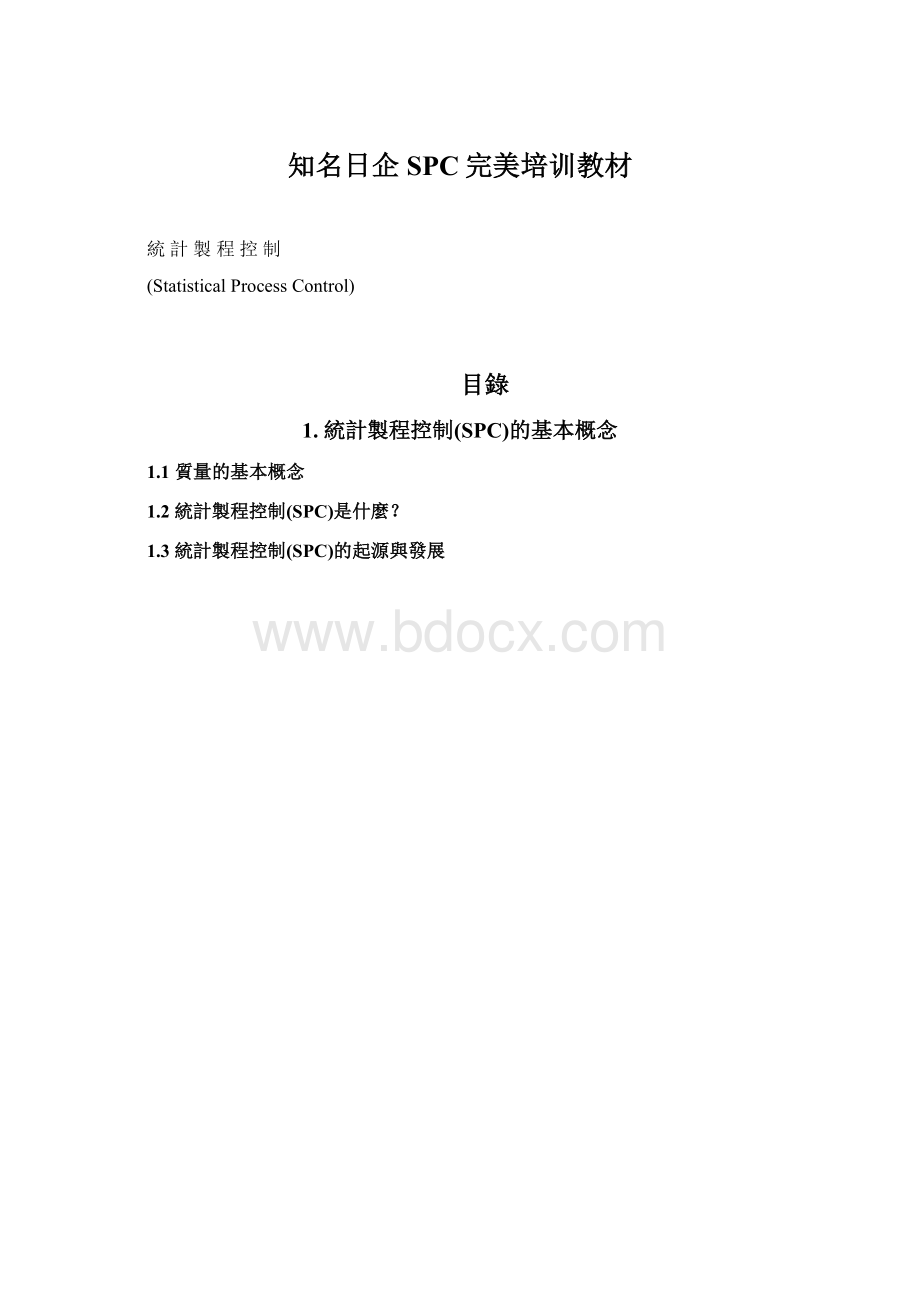
知名日企SPC完美培训教材
統計製程控制
(StatisticalProcessControl)
目錄
1.統計製程控制(SPC)的基本概念
1.1質量的基本概念
1.2統計製程控制(SPC)是什麼?
1.3統計製程控制(SPC)的起源與發展
2.常用的統計方法
2.1概率
2.2統計特徵數
2.3正態分佈(NormalDistribution)
2.4中心趨向定律(CentralLimitTheorem)
2.5正常狀態的統計規律
2.6常規控制圖及其3σ界限
2.7變異的基本概念
2.8數據的種類
2.9控制圖的種類
3.計量值控制圖的製作及應用
3.1選擇計量值控制圖
3.2數據收集
3.3控制界限的設定
3.4.控制界限的更新
3.5控制界限和規格的關係
4.計數值控制圖的製作及應用
4.1選擇計數值控制圖
4.2數據收集
4.3控制界限的設定
4.4控制界限的更新
5.控制圖的分析
5.1正常狀態
5.2異常現象
5.3失控行動表
6.製程能力的研究
6.1製程能力研究的目的
6.2製程能力指數的計算和分析
7.控制圖與七工具的關係
7.1七工具是什麼?
7.2統計分析表Checksheet
7.3分類法Stratification
7.4巴氏圖ParetoAnalysis
7.5直方圖Histogram/Barchart
7.6因果圖Cause-and-EffectDiagram
7.7散佈圖ScatteredDiagram
8.附錄
8.1控制圖用途總表
8.2控制圖的選擇
8.3控制圖工作紙
8.4控制圖樣本
8.5實習題
1.統計製程控制(SPC)的基本概念
1.1質量的基本概念
1.1.1品質的定義
●卓越的程度
比較的意義:
產品(功能、品質、安全、『級數』等)比較;
●品質水準
定量意義:
技術評估;
●適合用途(FitnessforUse)
產品或服務,在滿足特定需要的能力;
●滿足顧客要求。
1.1.2檢查與品質
●「品質」並不是靠檢查出來,而是靠生產出來的;
●檢查只是把所製成的,與規格要求的,作一個比較;
●檢查只能停止不合格品的流動,但不能停止它的產生;
●檢查本身都有品質問題,存在誤檢及漏檢,尤其是複雜和大量的檢查.
●檢查需要格外的成本和時間.
●如果產品在第一次便做得對,便可消除廢料、翻工及減少顧客投訴;
1.1.3品質與市場競爭能力
●商品要達到暢銷目的,通常要有三個必備的條件:
-
1.品質優良;
2.價格合理;
3.交貨期準。
1.1.4影嚮品質的因素
●人員(Man);
●機器(Machine);
●物料(Material);
●方法(Method);
●環境(Environment)
任何因素的變化都會導致產品或服務的變化,也即不同的品質.
品質控制的理念在于對生產過程的控制,而不在于對結果的控制.
一致的輸入和一致的過程導致一致的輸出(產品).
1.2統計製程控制(SPC)是什麼?
●統計製程控制的英文名稱是StatisticalProcessControl或簡稱為SPC。
●簡單地說就是應用“統計”(Statistical)技術,去分析“製程”(Process)中的特性,來“控制”(Control)製程變異。
●SPC的目的就是要控制製程達到“受控制的狀態”(inStatisticalControl)。
●SPC主要集中在製程的控制,因為製程是問題的根源。
它需要在製程中,加入定時的檢查,以達到盡早找出問題,來減少浪費;
●SPC典形運用的工具就有品質控制圖,利用簡單的圖表來提供以下的資料:
-質量改進
-決定工序能力
-產品規格的決定
-生產製程的決定
●SPC是一個有效的工具,去不斷地改善品質;
●SPC的最終目標在於做到“預防問題的發生”及“減少浪費”。
1.3統計製程控制(SPC)的起源與發展
●1917年一次世界大戰時,美軍需短時間預備軍衣、鞋等物資,結果尺碼比例按正態分布進行,基本吻合需要;
●1924年修華特博士(Dr.W.A.Shewhart)在貝爾試驗室發明了品質控制圖;
●1939年修華特博士與戴明博士(Dr.Deming)合作寫了一本『品質觀點的統計方法』(StatisticalMethodfromthepointofQualityControl);
●第二次世界大戰前後,英、美兩國將品質控制圖的方法引進製造業,並應用於生產過程中;
●1950年日本的JUSE邀請了戴明博士到日本演講,介紹了SQC的技術與觀念;
●為了紀念戴明博士的貢獻,JUSE於1951年成立了戴明獎;
●在1979年美國國家廣播公司(NBC)製作了一部『日本能,為何我們不能』的影片,SQC的理論與觀念,便受到注意及被應用於製造程序中;
●SQC的理論是不足夠的。
單是在發生問題後,才去解決問題,是一種浪費,所以進而發展出SPC;
●美國汽車製造業,在QS9000標准中對SPC的使用提出了自己的要求,推動了SPC的廣泛應用.
2.常用的統計方法
2.1概率
2.1.1隨機現象
●在一定條件下,一件事情可能出現這個結果,也可能出現另一個結果,沒有一定規律,呈現一種偶然性,這就是隨機現象了。
2.1.2概率
●一件事情A在n次試驗中出現的次數為m,事情A出現的頻率等如m/n。
●隨著試驗次數n的增加,事情A出現的頻率m/n就穩定在某個數值p;
●而p就被稱為事情A的概率(即或然率),俗稱機會率。
●當n是無限大時,p=m/n。
2.2統計特徵數
2.2.1統計特徵數的定義
●任何由樣本計算出來代表樣本特徵的數字,都稱為統計特徵數。
2.2.2表示數據集中位置的數字
(MeasureofCentralTendency)
_
●平均數x(Mean)
●中位數(Median)
●眾數(Mode)
2.2.3表示數據離散程度的數字
(MeasureofDispersion)
●全距R(Range)
●標準差s(StandardDeviation)
2.3正態分佈(NormalDistribution)
2.3.1正態分佈圖形
=頻率分佈的平均值
=頻率分佈的標準差
如收集數據時樣本數目非常大,
_
x
s
2.3.2正態分佈的特點
●以x=這條直線為軸,正態分佈是一個左右對稱的。
●靠近出現概率較大;遠離出現概率較細。
●分佈曲線下的面積代表該段數值的出現機會。
曲線範圍
範圍內面積
68.26%
2
95.45%
3
99.73%
4
64PPM
全部範圍
100.00%
2.4中心趨向定律(CentralLimitTheorem)
2.4.1樣本數目與頻率分佈
●若於總體抽取樣本,每樣本中有n個個體,則該樣本平均數不一定會相等於總體的平均數。
●若抽取多個樣本,各樣本的平均數將會構成另一正態分佈如下圖:
2.4.2中心趨向定律(CentralLimitTheorem)
●若總體分佈並非正態分佈,各樣本的平均數會否構成另一正態分佈?
●以拋擲骰子為例:
拋擲骰子的數目越多,骰子的平均數愈趨向正態分佈。
一粒骰子
二粒骰子
三粒骰子
四粒骰子
十粒骰子
●中心趨向定律(CentralLimitTheorem)就是:
不論總體分佈是否正態分佈,若抽取樣本,而個別樣本的數目愈多,樣本的平均數愈趨向正態分佈。
2.5正常狀態的統計規律
◆產品質量按加工時間順序是上下波動的,沒有兩件產品是完全相同的.
◆產品或制程的數据趨向于一個中心值且對稱分散于兩邊.
◆生產條件標准化后,產品特征值的分布大都遵循正態分布
◆即使總体特征值的分布不遵循正態分布,它的許多重要的樣本特征,如樣本平均數和樣本方差都是漸進正態分布的.
2.6常規控制圖及其3σ界限
2.6.1第一類錯誤
●把正確的誤判斷為錯誤的.
●浪費人力物力
2.6.2第二類錯誤
●把錯誤的誤判斷為正確的.
●錯過改正的機會
2.6.33σ界限
●完全避免兩种錯誤是不可能的,只有將這兩种錯誤產生的損失和減低到最小
●若產品質量特性值服從正態分布,在正常的生產過程中,產品特征值落在控制界限±3σ之外的机會為0.27%.
●也就是說1000次中約有3次會將正常的狀態判別為异常.
●這樣的錯誤是可以保証質量並且成本可接受的.
2.7變異的基本概念
2.7.1隨機變異原因(ChanceCause)
●一定存在各製程中;
●形成一個較穩定的狀態;
●對質量波動的影響不大
●不易識別
●難以避免
●例如:
刀具的磨損,溫度的變化
2.7.2特殊變異原因(SpecialCause/AssignableCause)
●偶然性發生,具有特別的條件
●引起質量的較大變化
●易于識別
●易于消除
●例如:
材料規格變更,模具變更,新的工藝
2.8數據的種類
2.8.1計量值數據
●如長度、重量等;
●其特點是可以連續地讀取這些數據。
2.8.2計數值數據
●如不合格個數、缺點數等;
●其特點是不可以連續地讀取這些數據,只可讀取整數。
2.9控制圖的種類
2.9.1常用計量值控制圖
_
●平均值-全距控制圖x-R控制圖
_
●平均值-標準差控制圖x-s控制圖
●個別值-移動全距控制圖x-R控制圖
●中心值–全距控制圖x-R控制圖
2.9.2常用計數值控制圖
●不良數控制圖np控制圖
●不良率控制圖p控制圖
●缺點數控制圖c控制圖
●單位缺點數控制圖u控制圖
3.計量值控制圖的製作及應用
3.1選擇計量值控制圖
●計量值控制圖是監察在製程中質量特性自然變化的傾向,而所提供的數據都是以可量度的數值為單位,圖表是用作測試製程中是否存在特殊變異原因的影嚮。
●常用的計量值控制圖種類及用途有:
控制圖種類
用途
代表性
平均值-全距
及
平均值-標準差
●平均值的圖表是用于觀察樣本平均值的轉變;
●全距和標準差是用于觀察誤差的變化情況
每一樣本的
平均數
個別值-移動全距
●個別值的圖表是用于觀察每一個數值的變化;
●移動全距用作觀察誤差的變化情況。
每一數據的
平均數
●選用計量值控制圖,通常會按檢查抽樣數目多寡來決定。
抽樣數目
管制圖種類
2-6
平均值-全距管制圖
6
平均值-標準差管制圖
=1
個別值-移動全距管制圖
●附錄I和II提供各種管制圖的方法和選擇準則以供參考。
接下來,我們將先集中在『平均值–全距控制圖』;然後才解說『平均值–標準差控制圖』和『個別值–全距控制圖』。
_
『平均值–全距控制圖(x-R控制圖)』包括了兩個控制圖,它們是『平均值控制圖』和『全距控制圖』。
『平均值控制圖』是用作觀察樣本平均值的變化;而另一種控制圖,『全距控制圖』是用作觀察數據收集的散佈情況。
這裏要指出的是『全距控制圖』通常是適用於少於七的抽樣數。
而超過或於七的抽樣數,『標準差控制圖』較為適合。
3.2數據收集
3.2.1選擇有代表性的質量特性
●收集數據的目的是:
a.製程管理:
掌握製程生產的波動範圍,決定製程生產是否穩定,有無特殊變異。
b.情況分析:
掌握和分析製程或產品出現特殊變異的原因,及制訂出糾正和預防再發生的措施。
c.產品檢查:
檢查收發的物品是否合格。
●收集的數據一定是要選擇具有代表製程質量控制的特性;而數據是可量度的。
●當選擇有代表性的質量特性時,可以參考以下的指引。
a.優先選取經常出現次品的質量特性;可以利用柏拉圖分析法去決定優先次序。
b.識別工序的變異因素和對成品質量的影嚮,繼而決定應用控制圖的生產工序。
例如:
模溫、塑料的溫度、壓力、塑注件重量等都是一些會影嚮塑注件尺吋的工序變異因素。
3.2.2選取樣本
當我們袛選取一個數據抽樣數,我們應該取最末的數據或差不多最末的,因為我們希望能獲得最新及最遲的資料;
當我們選取較大的抽樣數,例如5個,我們也要包括最末的數據,或差不多最末的。
但我們選取其他4個數據時,有兩個選取的辦法。
a.即是抽樣方法
當成品在某一個時間開始生產,即時任意地抽取樣本。
b.期間抽樣方法
在某一期間內選取樣本,即時抽樣方法可以提供時間上的參考作為找出變異的因素和更快地顯示工序平均值的轉變。
期間抽樣方法可以提供較全面的結果。
3.2.3設定抽樣數目
抽取一部機器或工序的變數通常都以“數量少和經常性”為原則。
在某一情況下,抽樣數的決定有以下的決定因素。
a.抽樣頻率
b.經濟因素
c.統計學上的準確度
正常來說,平均值和全距控制圖的抽樣數大約在4和7之間。
因為5是一個較為方便處理的抽樣數,所以,我們通常以5作為一個標準。
當然,如果有另外一個抽樣數更適合,我們可以使用。
3.2.4設定抽樣的次數
決定抽樣的次數基本上是一個經濟上的問題。
–抽樣次數越多,查驗的成本當然越大;
–抽樣次數越少,不合標準的產品生產也越大。
因此,抽樣次數的目的是希望上述兩種成本的總和達到最少。
通常的慣例是兩次開機之間,抽樣次數是20-25次。
另一種方法是在生產的初期,抽樣數較頻密;當確定工序受到控制,續漸減少抽樣次數。
理論上,抽樣的頻率和抽樣數可以用數學的方式計算。
而實際上,它是根據下列的因素決定。
a.產品/工序的質量表現歷史
b.查驗機械/人手的資源
c.估計的查驗成本和損壞成本
作為一個指引,下列附表是可以用來估計初部抽樣需要的數目。
批量
樣本數
1-65
5
66-110
10
111-180
15
181-300
25
301-500
30
501-800
35
801-1300
40
1301-3200
50
3201-8000
60
8001-22000
85
例如:
某製程每一班生產3000件產品。
由上例的附表,我們應該每一班制抽取50件。
如果我們使用每一組別是5的抽樣數,那麼10個抽樣組(50/5)會在每一班制內抽取。
在一個8小時的班制內共有480分鐘。
那麼,我們需要每48分鐘(480/10)抽取一組樣本。
所以,在這例子中,我們便要每48分鐘抽取5件樣本。
3.2.5收集樣本的次數
在設立控制圖的時侯,我們需要收集最少20組抽樣數。
當然,有某些數據是會在計算控制界限時被棄置的,那麼25個抽樣組會比較更適合。
3.3控制界限的設定
3.3.1設定『全距控制圖』的控制界限
_Ri
R=
k
_
UCLR=D4R
_
LCLR=D3R
註:
Ri=第i個控制分組的全距數據
_
R=所有樣本的平均全距
k=樣本個數(組數)
UCLR=全距的上控制界限
LCLR=全距的下控制界限
樣本數目
D3
D4
2
0
3.267
3
0
2.574
4
0
2.282
5
0
2.114
6
0
2.004
7
0.076
1.924
8
0.136
1.864
9
0.184
1.816
10
0.223
1.777
3.3.2測試全距是否在統計控制之內
有三種可能的形式
a.所有的樣本全距數據都所括在控制界限之內
b.一個或二個樣本全距數據超越控制界限
c.三個或以上樣本全距數據超越控制界限
以下是一個用來修正以上可能性的決策圖。
3.3.3設定『平均值控制圖』的控制界限
當發現樣本全距在統計的控制範圍後,我們便可以繼續用下面的方程式去計算平均值圖的控制界限。
_
=xi
x=
k
=_
UCLx=x+A2R
=_
LCLx=x-A2R
=
註:
x=所有抽樣組平均值的平均值
_
xi=第i個抽樣組的平均值
k=樣本個數(組數)
UCLx=平均值的上控制界限
LCLx=平均值的下控制界限
樣本數目
A2
2
1.880
3
1.023
4
0.729
5
0.577
6
0.483
7
0.419
8
0.373
9
0.337
10
0.308
3.3.4測試平均值是否在統計控制之內
如全距測試一樣,平均值也有三種可能的形式:
a.所有的樣本平均值都所括在控制界限之內
b.一個或二個樣本平均值超越控制界限
c.三個或以上樣本平均值超越控制界限
以下是一個用來修正以上可能性的決策圖。
3.3.5設定『平均值和標準差控制圖』的控制界限
因計算上的便利,『平均值和全距控制圖』,以成為最常用的計數值控制圖。
但也有一些較喜歡使用標準差‘S’作為觀察抽樣組中數據的分佈。
在『標準差控制圖』的計算,是計算抽樣組中所有的數據,而不是像『全距控制圖』祗選取最高和最低的數據。
當抽樣組中的抽樣數目增大,『標準差控制圖』是較『全距控制圖』準確的。
在這裏,我們提議在可能的情況下或當抽樣數大於6的時侯使用標準差控制圖。
『平均值和標準差控制圖』的制作部驟是近似『平均值和全距控制圖』。
兩者不同的是計算平均值和標準差控制界限的方程式。
計算初試控制界限的方程式如下:
_
=xi
x=
k
_si
s=
k
=_
UCLx=x+A3s
=_
LCLx=x-A3s
_
UCLs=B4s
_
LCLs=B3s
=
註:
x=所有抽樣組平均值的平均值
xi=第i個抽樣組的平均值
_
s=所有樣本的平均標準差
si=第i個抽樣組的標準差
k=樣本個數(組數)
UCLx=平均值的上控制界限
LCLx=平均值的下控制界限
UCLs=標準差的上控制界限
LCLs=標準差的下控制界限
樣本數目
A3
B3
B4
2
2.659
0
3.267
3
1.954
0
2.568
4
1.628
0
2.282
5
1.427
0
2.089
6
1.287
0.030
1.970
7
1.182
0.118
1.882
8
1.099
0.185
1.815
9
1.032
0.239
1.761
10
0.975
0.284
1.716
3.3.6設定『個別值和全距控制圖』的控制界限
『個別值和全距控制圖』是用於特別的情況。
例如:
加工時間較長或當我們監察工序的狀態,如電鍍液的pH值,此控制圖是根據個別的量度數據而不是小量抽樣的。
『個別值和全距控制圖』是適用於盡快發現並消除異常原因,零件批量較少,加工時間較長,測量費用較高的場合,工序產品內部質量均勻,不需測取多個數值的情況。
要設立一個『個別值和全距控制圖』,我們需要大約20個數據。
而設立的步驟和控制界限大致和『平均值和全距控制圖』相同。
中心線和控制界限的方程式如下:
_x
x=
k
_R
R=
k-1
Ri=|xi-1-xi|
__
UCLx=x+2.66R
__
LCLx=x-2.66R
_
UCLR=3.268R
LCLR=0
_
註:
x=所有樣本的平均個別值
xi=第i個抽樣組的個別值
_
R=所有樣本的平均移動全距
Ri=第i個抽樣組的移動全距
k=樣本個數(組數)
UCLx=個別值的上控制界限
LCLx=個別值的下控制界限
UCLR=全距的上控制界限
LCLR=全距的下控制界限
3.4控制界限的更新
控制界限設立後,便可以作為正常工序生產的監察和控制。
初期用作計算的工序質量特性,會隨著環境而轉變。
因此,理想的做法是控制界限會定期檢討。
定期檢討和是否重新計算的需要會視符工序和操作情況的轉變而定。
我們提議重新計算會在下列的情況實行。
a.使用新的工序
b.使用新的機器
c.現時的工序情況有改變
d.機器操作的情況有改變
3.5控制界限和規格界限的關係
我們一定要避免把規格界限放置在控制圖,理由有兩個:
首先,控制圖的控制界限是根據製程中的可變性而設定,但規格界限是從設計階段決定。
它們沒有(或不定有)直接的關係。
第二點理由是規格界限以控制個別的數值而不是平均的數值或其他統計的數值。
很多統計製程控制的初學者時常把控制界限和規格界限的真正意義混淆。
下面把控制界限和規格界限作一直接比較。
控制界限
規格界限
●用作決定工序是否在統計控制的範圍內
●用作決定元件是否乎合規格
●好的工序控制,控制界限一定在規格界限之內
●為了達到最低的生產成本,規格界限一定要在控制界限之外
●如果有點子在控制界限之外,即表示工序不在管制範圍和有非機遇性的因素存在
●如果點子在控制範圍之內,而不在規格界限之內,即表示工序已在統計控制範圍內,但仍沒有能力生產乎合規格產品
4.計數值控制圖的製作及應用
4.1選擇計數值控制圖
●計數值在質量控制的範圍中是用作為量度那些不可以用量度數值代表的質量特性。
更簡單的是那些質量特性可以判定允收或拒收。
●典形的計數值有:
–汽車檔風玻璃的氣泡
–塗漆表面的抓痕
–測試不合規格的單位
–外殼的缺點
●計數值控制圖的作用,包括:
a.決定質量的平均水平;
b.當平均質量水平轉變,給管理階層一個信息;
c.提高產品的質量;
d.在付運給顧客前決定產品的允收特徵。