超高分子油管内衬管可研报告.docx
《超高分子油管内衬管可研报告.docx》由会员分享,可在线阅读,更多相关《超高分子油管内衬管可研报告.docx(10页珍藏版)》请在冰豆网上搜索。
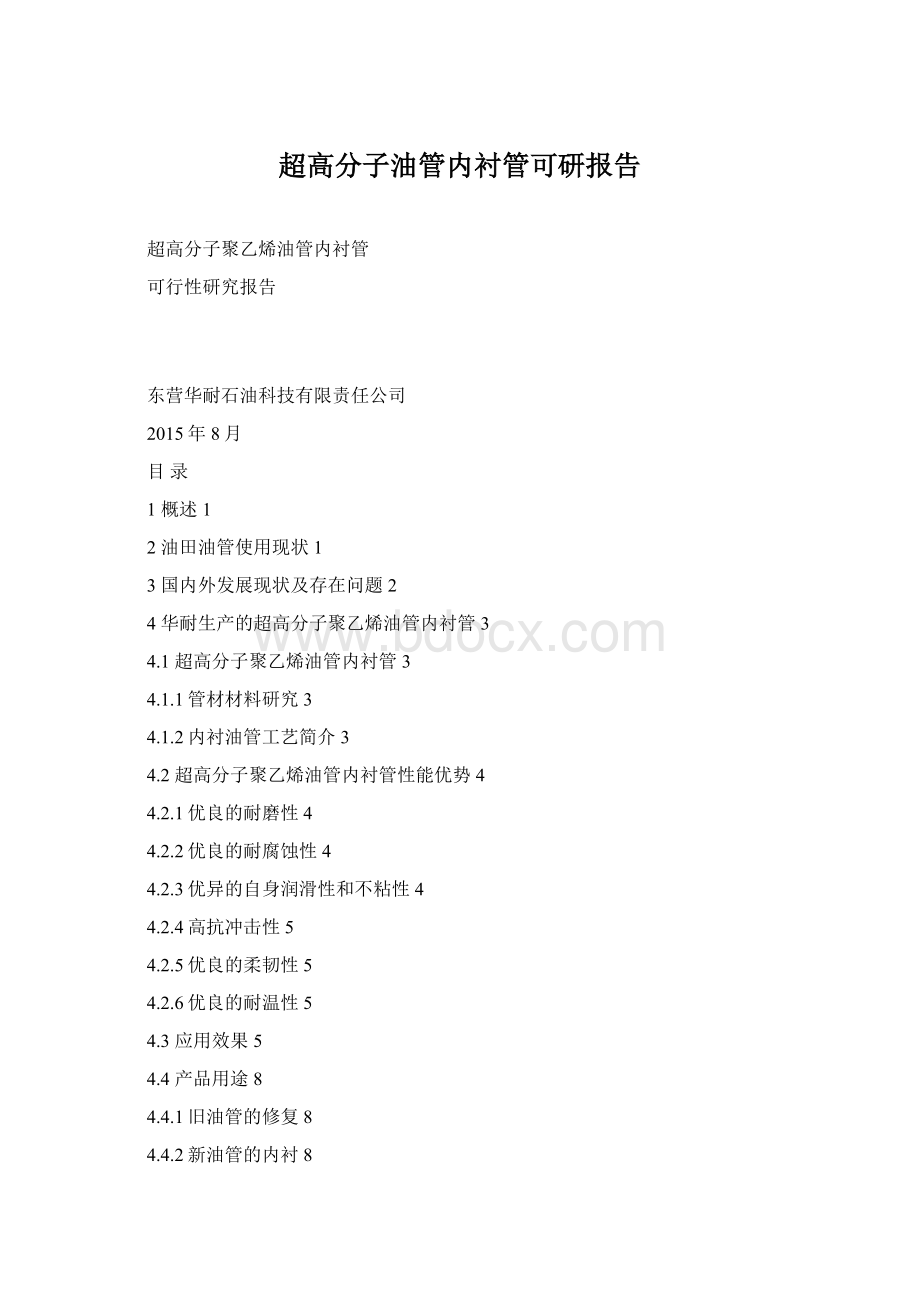
超高分子油管内衬管可研报告
超高分子聚乙烯油管内衬管
可行性研究报告
东营华耐石油科技有限责任公司
2015年8月
目录
1概述1
2油田油管使用现状1
3国内外发展现状及存在问题2
4华耐生产的超高分子聚乙烯油管内衬管3
4.1超高分子聚乙烯油管内衬管3
4.1.1管材材料研究3
4.1.2内衬油管工艺简介3
4.2超高分子聚乙烯油管内衬管性能优势4
4.2.1优良的耐磨性4
4.2.2优良的耐腐蚀性4
4.2.3优异的自身润滑性和不粘性4
4.2.4高抗冲击性5
4.2.5优良的柔韧性5
4.2.6优良的耐温性5
4.3应用效果5
4.4产品用途8
4.4.1旧油管的修复8
4.4.2新油管的内衬8
4.4.3其他用途8
5油管内衬生产工艺介绍8
5.1油管的选用8
5.2内衬管材的选用9
5.3内衬管生产作业线技术指标9
5.4衬管等径压缩并穿插进入油管9
5.5内衬油管热处理10
5.6衬管端部处理10
5.7管材成品10
6经济效益10
6.1单井效益10
6.2综合效益错误!
未定义书签。
6.3市场前景11
1概述
油管,是油田生产企业大量使用于油、水井内的钢制管道,属于大宗的基本生产物资。
随着油田开发建设进入高含水时期,影响石油开采成本的主要因素是短命井,采油井油管的偏磨、腐蚀和结垢(杆管偏磨、杆断、管漏)导致油井停产、减产。
因杆管偏磨造成报废占油管年总用量的1/6以上,造成巨大的资源浪费和生产成本增加。
基于以上情况,华耐公司开发的高分子聚乙烯油管内衬管具有防腐蚀,防油井结蜡、油水井结垢等特点,可广泛应用于油水井管柱。
为了避免或降低油管磨损带来的损害,将内衬管材作为常规油管的内衬薄层,提高油管的抗磨特性。
该产品可广泛应用于国内外油田生产企业,针对杆、管间磨损问题突出的单井,可在磨损严重的井段更换抗磨复合油管,延长其井下生产周期,减少因此带来的躺井和作业,综合提高油田生产效率和经济效益。
2油田油管使用现状
在采油井中,由于含水上升,井身不正,管柱问题或是在斜井/水平井的造斜段,抽油杆及其接箍与油管内壁发生刮擦,造成油管破损或抽油杆断脱,导致油井无法正常生产,给油田生产带来巨大损失。
(1)油井生产周期缩短
由于油井管、杆的问题,油井无法正常生产,就必须停井进行修理作业,在影响原油产量的同时,维护作业次数及费用也大幅上升。
(2)增加了管、杆报废,管杆投入大幅增加
据调查统计,因管杆偏磨年报废抽油杆达98.8万米,报废油管132.8万米,由此增加的管、杆年投入费用达1.8亿元。
因此,油田企业亟需一种抗磨抗腐蚀的油管内衬管解决严重的腐蚀、磨损、结垢等难题!
3国内外发展现状及存在问题
针对油管使用过程中的发生的损害,国内外更多的是关注在腐蚀损害方面,大致有两种方式:
一是采用金属隔离,即加衬金属衬管或金属镀层。
(1)加衬金属衬管:
采用不锈钢,铜合金材料等,预制成筒状,通常采用爆燃加衬或轧制加衬方式与油管内壁贴合,然后端部实施焊接。
经现场询问,当复合油管受到反复拉伸时,该产品内衬层于油管易开焊,影响使用。
(2)金属镀层:
一种是镍磷镀管。
镍磷镀由于对管道内表面质量,如光洁度、清洁度等要求很高,实际上很难达到。
镍磷镀对于使用多年的旧管进行修复非常困难;对于处理过的新管防腐镀膜层由于机械性能指标较差,易导致镀锡层断裂、脱落,造成局部腐蚀,防腐周期太短,目前不再大量使用。
二是采用非金属隔离,即涂敷非金属涂层或加衬非金属管。
(1)涂敷非金属涂层:
在油管内表加覆防腐涂层有一定的局限性,在高温高压多相流的条件下,不论是喷涂、表面渗透、离子注入等,因防腐膜层厚度很薄,仅为十几微米,涂层破损的概率很大,易发生脱落,从而导致严重的局部腐蚀,且无法对旧油管进行修复。
(2)加衬非金属管:
早先采用烧制陶瓷作为油管内胆,但造价高,易崩裂,玻璃钢管和玻璃钢内衬管耐温性差、成本也高。
国内最近有采用衬普通HDPE,已投入市场,国外检索发现已采用HDPE,尼龙11和PPR衬管,主要用于抗油井酸性介质腐蚀。
4超高分子聚乙烯油管内衬管
4.1超高分子聚乙烯油管内衬管
4.1.1管材材料研究
聚乙烯是通过乙烯(CH2=CH2)加成聚合而成,是由重复的–CH2–单元连接而成的,因其化学稳定性好、自润滑性能高、低吸水率和良好的绝缘性能而广泛应用于许多领域。
但用于有杆泵井抗磨防腐,需要对其抗磨性能、耐温性能、机械性能等方面进行提高和改进。
经过不懈努力,通过改善分子结构和特种添加剂,研究形成了性能优异的聚乙烯新材料,它具有分子量高、分子链长、分子排列紧密等特点(见下图),在兼顾抗磨耐温性能的同时,大大提高了抗拉性能,保证弹性,非常适合油管内衬管材的应用。
4.1.2内衬油管工艺简介
本产品采用特种超高分子聚乙烯为原材料,经特定挤出工艺生产出适合油田使用的新型管材,采用隔离原理将其紧衬到油管内,因其自身的高耐磨、抗腐蚀、耐高温、阻力小等特点,有效减轻抽油杆与油管内壁的磨损和腐蚀,提高油管和设备的使用寿命。
特种聚乙烯内衬新材料挤出工艺
内衬管
内衬油管新技术抗磨防腐双重特性的油管
4.2超高分子聚乙烯油管内衬管性能优势
4.2.1优良的耐磨性
超高分子聚乙烯油管内衬管最引人注目的一个特性就是它具有极高的耐磨性,是钢管的7-10倍,尼龙的3-4倍。
其耐磨机理不是仅靠它的硬度,而且还靠粘弹性和摩擦系数小来缓冲磨损。
超高分子聚乙烯油管内衬管是目前解决油井偏磨难题最有效的技术。
4.2.2优良的耐腐蚀性
超高分子聚乙烯油管内衬管稳定性极高,具有良好的耐化学腐蚀特性,除强氧化性酸液外,在一定温度和浓度范围内能耐各种腐蚀性介质(酸、碱、盐)及有机介质(萘溶剂除外),而且可在温度小于80℃的浓盐酸中应用,在海水和液体洗涤剂中也是很稳定的。
4.2.3优异的自身润滑性和不粘性
超高分子聚乙烯油管内衬管的磨损系数较小,表面吸附力非常微弱,抗粘附能力与特氟隆相当,有效防止结垢。
4.2.4高抗冲击性
超高分子聚乙烯油管内衬管的抗冲击性和吸收冲击性能优异,具有良好的消音降噪效果,不会产生小孔、裂缝、断裂和剥落等现象,对井没有污染。
4.2.5优良的柔韧性
超高分子聚乙烯油管内衬管断裂伸长率:
>400%,优良的弹性可适应由于油井温度和油管载荷的变化导致的油管变形,可始终保证衬管紧紧地涨紧在钢管的内表面,并且保持端面密封。
4.2.6优良的耐温性
超高分子聚乙烯油管内衬管适温性宽,可长期在-70℃—110℃的温度范围内工作。
4.3应用效果
对于减小井身内的磨损,油田生产企业已采用了不少措施,如可自动旋转井口装置,使管柱均匀自转,避免同一部位的反复磨损,通过均匀受损来延长使用寿命;加装防偏磨副,是加强局部的抗磨损性能;还有采用加重防偏磨抽油杆,扶正器等。
这些措施一定程度上缓解了磨损,但实际上并未提升油管自身的抗磨性能,可以作为采用抗磨复合油管后的辅助配套措施,全面综合地解决油管磨损问题。
加装复合内衬管能很好地解决抗磨问题,同时也提高了防腐性能,是提升油管性能的最佳方案。
近年来,超高分子聚乙烯材料作为一种经济、环保、高效的新型防腐材料,在国内外众多行业的管道、设备的防护中得到了越来越广泛的应用。
在国外,许多石油公司采用聚乙烯油管来减少和防止人工举升井和注水井由于抽油杆-油管磨损和油管腐蚀而引起的井下事故。
BP美洲公司、雪弗龙德士古公司、科诺科公司、发斯肯石油公司和阮池公司等已经在很多的油井和注水井中使用了这种聚乙烯衬管,明显降低了作业成本。
实践证明,超高分子聚乙烯油管内衬管还可以大幅度降低与抽油杆油管磨损和油管腐蚀故障有关的油井作业成本。
美国已经有10多年成功使用聚乙烯衬里油管的经验,在3000多口井中得到应用,不仅解决了与腐蚀、抽油杆磨损油管有关的问题,而且还节约了电力。
实践证明,在解决使用杆式泵或渐进式螺杆泵井的抽油杆磨损油管问题方面,聚乙烯衬里效果尤其明显。
在大斜度井和“狗腿”井中使用聚乙烯衬里油管能够在不增加小眼抽油杆节箍和抽油杆导向器费用的情况下,获得收益。
在控制其他人工升举井和处理井中的管子腐蚀方面,聚乙烯衬里油管也都同样获得成功。
实验证明,该衬里对钢丝绳、酸类和化学损害都显示出了良好的抗蚀性。
(资料来源于美国《WorldOil》2003年1月)
例如,胜利油田有两家采油厂采用了复合内衬油管。
B采油厂于2004年4月先后在腐蚀偏磨严重的三口井:
营13-112、营12-186和营1斜57井试验应用了内衬复合内衬抗磨抗腐油管,除营1斜57井生产58天,检泵时由于上部普通3”油管磨漏不可对比外,其余两口井见到了明显的应用效果。
两口油井试验前,平均含水均在75%以上,配套前偏磨腐蚀严重,多次管漏上作,平均年作业3次,检泵周期94天,同时于2003年4月24日下井试验,与试验前相比,检泵周期延长72天,未出现因PEX内衬耐磨防腐油管质量问题造成的倒井,内衬管表面光滑,无起泡、裂痕等现象,两口井的内衬管均继续下井使用,目前正常生产已达704天。
A厂于2006年4月份在2口井上进行了试验,情况如下:
第一口是河110-24井,经查资料表明,该井在700-1500米处井身不正,并且在2005.12-2006.4三次偏磨管漏,于2006年4月30日从600-1500米共下入73mm内衬复合内衬抗磨抗腐油管900米,于2006年5月15日开井,正常生产446天。
第二口是河110-25井,由于该井在2005年2次偏磨管漏,且大范围偏磨,于2006年4月7日在600-1800米配套了1200米73mm内衬复合内衬抗磨抗腐油管,于2006年4月10日开井,正常生产370天。
由于超高分子聚乙烯油管内衬管的独特性能,通过B采油厂在三口井中的前期应用,在偏磨油井中试验效果非常明显。
能有效地消除杆管磨损,极大地减少了杆管报废,延长了油井的生产周期,起到了极好的降本增效的效果。
4.4产品用途
本产品可广泛应用于石油行业的井下油管管柱,包括克服偏磨、腐蚀、结蜡、油水井结垢、稠油井开采困难等。
4.4.1旧油管的修复
可对已经出现大量坑点腐蚀、不能正常使用的旧油管进行内表面油污、锈迹、垢质清洁处理,加衬内衬管修复,可重复使用、降低成本,避免资源浪费。
4.4.2新油管的内衬
新油管加衬内衬管,可在保证机械性能的前提下,提高油管的抗磨性能和耐腐蚀性能,延长使用寿命。
4.4.3其他用途
新、旧油管的防腐、防蜡、防结垢,配套稠油开采等。
本超高分子聚乙烯内衬油管不能下入超过材料许用温度的油井。
5.油管内衬生产工艺介绍
5.1油管的选用
待内衬的母油管必须是新油管或经过清洗、矫直、试压后满足油管使用条件的旧油管。
为了配合生产工艺,油管必须拧下管箍。
内衬的母油管规格型号为:
Φ73、Φ89的平式、外加厚油管。
5.2内衬管材的选用
采用不同材料的专用衬管以适应井底温度,管材的直径需大于母油管内径2~3mm。
内衬管材由本公司提供。
本内衬管具有耐高温,机械强度高,耐磨强度高特点。
5.3内衬管生产作业线技术指标
据作业的活动范围,平台的尺寸不小于30×6m.。
场地要求不小于30×25m。
平台高度应方便操作人员的工作活动范围,按照油管作业线布置图摆放生产设备。
内衬管生产作业线人员配置共计7人:
穿管区需2人,端部处理区2人,热处理区1人,机动人员1人,送管1人。
据作业的活动范围,平台的尺寸不小于30×6m.。
场地要求不小于30×25m。
配备3T行吊1部。
平台高度应方便操作人员的工作活动范围,按照油管作业线布置图摆放生产设备。
详见附图
内衬管生产作业线主要设备功率不大于15kw(不含加热设备)。
内衬管生产作业线用电量:
穿管区缩径机功率3KW/台,共2台;管端处理机功率5KW/台,共2台。
内衬管生产作业线工作效率为80根/工日成品管;其中:
穿管区2分钟/根左右,端部处理5分钟/根左右。
5.4衬管等径压缩并穿插进入油管
1.选用的内衬管材外径大于母油管内径,将管材通过衬管缩径机,暂时缩小衬管的外径顺利进入母油管中。
2.衬管具有记忆效应。
衬管进入母油管后,逐渐恢复原始直径,涨紧在油管内壁上。
5.5内衬油管热处理
内衬油管端部处理完毕,采取热处理措施,在热力作用下加快记忆效应;内衬管材缩径后,材料本身会产生一定的内应力,经过高温使衬管消除一部分内应力并保持适当的内应力,提高内衬油管在使用过程中的稳定性。
5.6衬管端部处理
将油管一端穿插后剩余的内衬管材保留合适长度,用夹具卡住,将油管匀速旋转,目的为了将油管加热均匀。
将其衬管热熔,达到设定的温度之后,通过成型装置形成可靠的端部。
而后进行另一端的端部处理。
5.7管材成品
检验油管两端处理情况,符合标准的内衬油管方可安装接箍。
接箍安装完毕,两端拧上内外护丝,保护内衬管材不受破坏。
6经济效益
6.1单井效益
以泵挂800米油井来计算,按治理前检泵周期115天,治理后延长检泵周期209天。
配套800米高分子聚乙烯内衬油管,100米为普通油管,同时需配套抗磨接箍85个,高分子聚乙烯内衬油管使用3年计算:
(1)增加生产成本:
800米×54元/米+85个×150元/个=5.595万元;
(2)减少生产成本:
节约劳务费用(按单次作业劳务0.8万元计算):
3年×(365/115-365/324)次/年×0.8万元=4.9万元
节约更换油管、抽油杆泵材料费用(按单次作业更换油管700米、更换抽油杆500米计算,其中新管杆按1/3,修复管杆按2/3更换):
修复油管费用:
13元/米×800米×2/3×6.3=3.843万元
抽油泵费用:
5000元×6.3=3.15万元
避免报废管、杆费用(按偏磨井单次报废油管300米、抽油杆150米计算)
(300米×85元/米+150米×30元/米)×6.3=18.9万元
每年按照减少停井时间10天,产量每天按照0.15吨,每吨按照4000元计算:
10天×0.15吨×4000元/吨=0.6万元
合计:
4.9+3.843+3.15+18.9+0.6=31.393万元
(3)直接经济效益:
31.379-5.595=25.784万元
年效益:
25.784/3=8.59万元
6.2市场前景
(1)超高分子聚乙烯油管内衬管具有优良的弹性、柔韧性、耐磨等物理特性和耐H2S、CO2、酸、盐等化学稳定性,而且用途广泛,特别适用于腐蚀、结垢严重的注水井,油管偏磨与腐蚀严重、抽油杆故障率高的油井,以及受硫化氢、二氧化碳腐蚀的气井。
(2)其优异的性能有效地降低油井中油管、油杆的磨损及磨阻,将管杆系统的使用寿命提高三倍以上,延长偏磨油井的检泵周期3-5倍,在提高工作效率的同时,又大大降低了维护作业的费用。
(3)超高分子聚乙烯油管内衬管技术,可回收废旧油管(井下不适用的腐蚀和偏磨严重的旧油管)经内衬处理后多次再利用。
同时油管、抽油杆使用寿命的延长,生产成本也大幅降低,无形中给油田企业带来巨大经济效益,符合国家“节能减排”的方针。