注册化工业绩年处理10万吨废润滑油再生循环利用方案.docx
《注册化工业绩年处理10万吨废润滑油再生循环利用方案.docx》由会员分享,可在线阅读,更多相关《注册化工业绩年处理10万吨废润滑油再生循环利用方案.docx(16页珍藏版)》请在冰豆网上搜索。
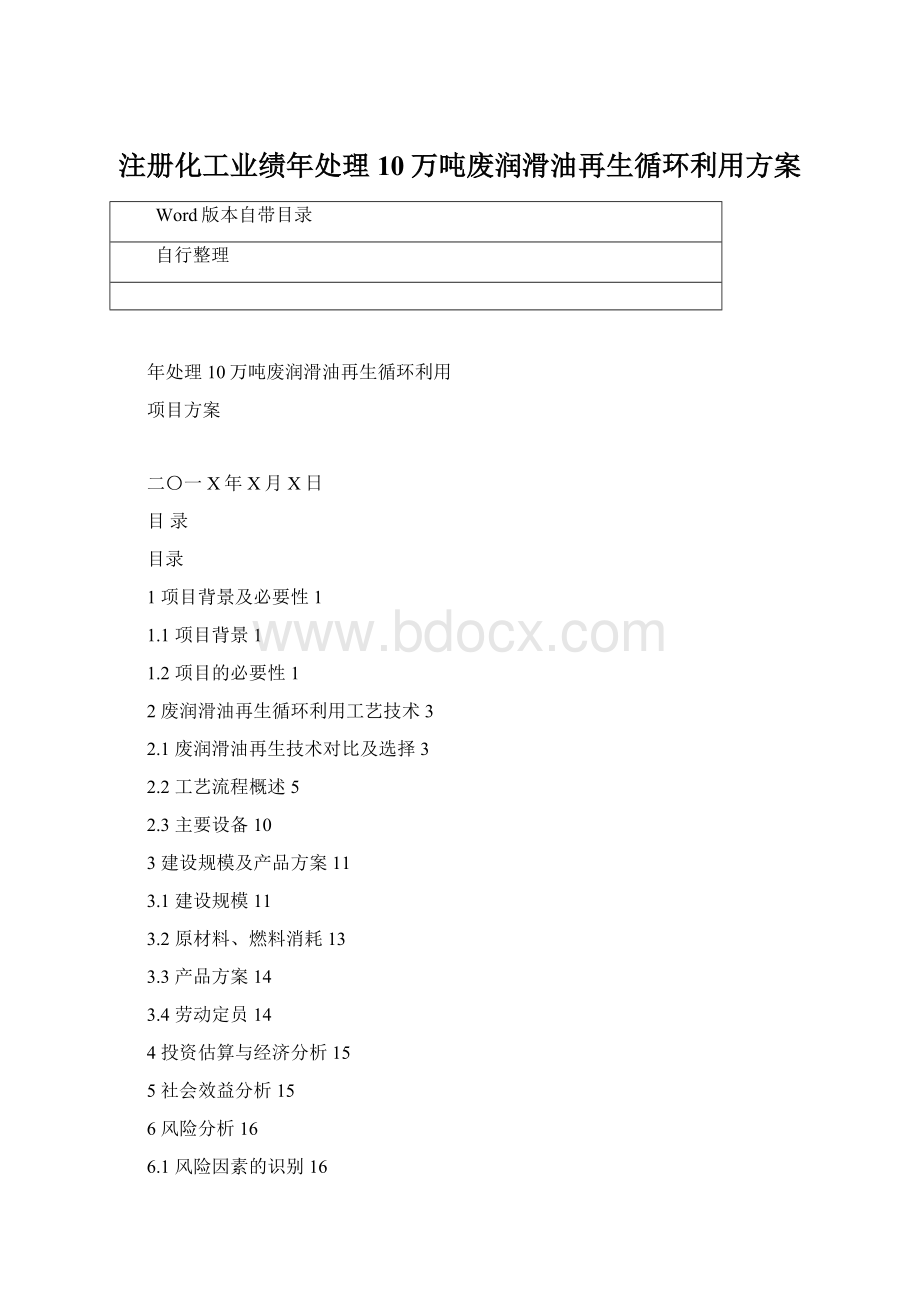
注册化工业绩年处理10万吨废润滑油再生循环利用方案
Word版本自带目录
自行整理
年处理10万吨废润滑油再生循环利用
项目方案
二〇一X年X月X日
目录
目录
1项目背景及必要性1
1.1项目背景1
1.2项目的必要性1
2废润滑油再生循环利用工艺技术3
2.1废润滑油再生技术对比及选择3
2.2工艺流程概述5
2.3主要设备10
3建设规模及产品方案11
3.1建设规模11
3.2原材料、燃料消耗13
3.3产品方案14
3.4劳动定员14
4投资估算与经济分析15
5社会效益分析15
6风险分析16
6.1风险因素的识别16
6.2风险分析结果的反馈16
7结论与建议17
7.1结论17
7.2建议18
1项目背景及必要性
1.1项目背景
随着经济的发展,各行业对润滑油的需求量也不断增加,每年换下来的废旧润滑油品量越来越大。
这些废油如丢弃到环境中去,将造成严重的环境污染。
随着国民经济的快速发展和人民生活水平的不断提高,生产和生活过程中产生的能够回收利用的各种再生资源日益增多。
大力开展再生资源回收利用,是提高资源利用效率,保护环境,建设资源节约型社会的重要途径之一。
事实上,废润滑油的组成中,除了含有2%-10%的变质物外,其余的90%~98%都是好的成分,是完全可以再利用的。
选择合理的工艺,规模化专业化进行废润滑油的再生利用,可以解决废润滑油再生技术上难于脱水脱杂质、难于分馏、加工单位费用大等一系列的问题。
废润滑油的规模化、专业化的再生利用,是保护环境的需要也是节约能源的需要。
同时,废润滑油的规模化、专业化的再生利用也是废润滑油加工生产企业获得经济效益的需要。
只有规模化、专业化地再生利用废润滑油才能获得环境效益、社会效益和经济效益的良好统一。
1.2项目的必要性
(1)项目建设符合国家产业政策
《国民经济和社会发展第十二个五年规划纲要(草案)》提出,面对日趋强化的资源环境约束,必须增强危机意识,树立绿色、低碳发展理念,以节能减排为重点,健全激励与约束机制,加快构建资源节约、环境友好的生产方式和消费模式,增强可持续发展能力,提高生态文明水平。
《“十二五”资源综合利用指导意见》中的重点领域中指出:
“要进一步提高工业废水循环利用和城镇污水再生利用水平;继续推进矿井水资源化利用;鼓励重点行业开展废旧润滑油、采油废水、废植物油、废酸、废碱、废液等回收和资源化利用”。
废润滑油再生符合《产业结构调整指导目录(2013修正)》中的鼓励类项目。
可见,废润滑油再生资源的产业化,属于生态型资源循环利用范畴,符合国家产业政策,符合国家发展循环经济、保护环境的要求。
(2)项目资源利用和环境保护效益显著
废润滑油会损坏机械设备,随意丢弃或简单处理对环境的破坏性很大。
随着经济的发展,对润滑油的需求量也不断增加,每年换下来的废旧润滑油品量也越来越大。
废油不论是倒入下水道,或倒在空地地面,都会对环境造成严重的污染。
进入下水道中的废油,会随着污水流入河流,进入江湖河海;丢弃在陆地上的废油,渗透在土壤中,一小部分会被微生物分解,而多数部分则会由于雨水的冲洗最后也进入江湖河海中,造成对环境中土壤及水系的污染。
进入水系的油对水有很强的污染力,一桶(200L)废油流入湖海,能污染近3~5平方公里的水域。
在污染的水域,由于油膜覆盖在水面上,阻止了水中的溶解气体与大气的交换,将引起水生动植物的大量死亡,甚至还可以影响到鸟类的生存。
可见,废弃的废润滑油对环境所造成破坏性的影响是非常大的。
目前国内年消耗润滑油550万吨,已被回收再生利用的废油约为150万吨左右,回收潜力有400万吨之多。
目前废润滑油现金回收价格为每吨3300元左右。
而普通成品润滑油的销售价在每吨6500~9000元之间,特种润滑油品价格可达9500元以上。
对废旧润滑油进行资源化利用,并实现产业化,将变废为宝,实现资源利用和环境保护的双重效益。
2废润滑油再生循环利用工艺技术
2.1废润滑油再生技术对比及选择
使用后废油的主要成分并未改变,经精制去除不良组分或将其转化,提取出并未变质的成分,则可得到与原基础油性质接近甚至更好的再生油。
废油中75%~99%的成分都是好的,若能完全提取,既减少了污染又增加了效益。
简单的物理精制方法有沉降、离心、过滤等,可以去除废油中一些机械杂质、部分水分。
但是简单的物理精制方法无法完全去除废油中的杂质,精致效果差,不能满足日益提高的润滑油标准要求;另一方面,润滑油品使用条件愈加苛刻,其中加入了多种添加剂,如清净剂分散剂、粘度指数改进剂等,以提高润滑油的性能和使用期限,这导致废油更加难以简单的再生。
因此,必须用更好的精制方法,提取出有用的成分,将不好的组分如水分,燃油,酸性氧化物。
主要有以下几种工艺:
(1)硫酸-白土工艺法
硫酸白土工艺是最早的精制废油工艺,并由此衍生出沉降-酸洗-白土工艺,沉降-酸洗-碱洗-白土工艺,蒸馏-酸洗-白士工艺,沉降-蒸馏-酸洗-白土工艺等。
这些工艺虽能够生产较好的基础油,但硫酸耗量大,因此对设备的腐蚀严重;处理过程产生大量的酸性气体二氧化硫及大量的难以处理的酸渣、酸水、白土渣等,对环境造成严重二次污染。
在国外,硫酸工艺已逐渐被淘汰,国内也不提倡此法,但仍有很多的国内小工厂采用此工艺。
(2)蒸馏-溶剂精制-白土工艺法
该工艺处理过程分两步。
先通过减压蒸馏去除水分,轻质油及沥青,绝大部分含金属元素添加剂(沸点一般高于润滑油馏分),获得一定纯度的润滑油馏分。
但其闪点、粘度、酸值等仍不符合规格要求,还需进一步处理。
第二步再用溶剂对所得馏分进行精制,萃取液中的溶剂可回收循环使用,萃余液即精制后的再生油。
所选用的溶剂需要有较好的选择性,它与基础油不相溶,但可以溶解芳香烃、胶质等,溶剂须有良好的化学稳定性和合适的沸点从而利于回收利用。
糠醛、NMP.1叫等都可满足需求,可去除胶质,酸性氧化物等不良成分。
从而提取品质较好的基础油。
此工艺缺点是,减压蒸馏需要高的操作真空度。
精馏过程温度高,油品易发生裂解,导致再生油闪点偏低,且高沸物易发生焦结。
溶剂用量大,回收溶剂耗热大,萃取剂糠醛易氧化,而NMP有水存在时易发生分解,也存在对没备腐蚀的问题。
为了克服糠醛易氧化的缺点,颜新副改用糠醇处理废真率泵油和内燃机油,废油回收率超过90%。
(3)高温—白土工艺法
用此法可以延长设备的使用寿命,提高生产效率。
(4加氢工艺法
该工艺的显著优势是没有废物处理问题,同时还具有回收率高、产品质量好等特点,但其设备投资高,并且需要合适的氢气来源。
2.2工艺流程概述
该技术的工艺过程如下:
废润滑油→预处理→蒸馏切割→白土精制→调和→成品润滑油。
废润滑油收集回厂,经过滤脱机械杂质、沉降脱水脱杂质,然后进入蒸馏装置进行减压切割分馏,减压各侧线馏分油就可以作为不同的润滑油原料,再经过白土精制装置进一步精制而获得合格的基础油,减底渣油和减顶轻组分可调和成燃料油供工厂作为燃料自用和外销。
精制后获得的合格基础油经调和后作为润滑油成品油销售。
2.2.1工艺流程环节说明
(1)预处理
废润滑油通过化验室化验进行品位分析,然后通过格栅进入卸油池内,接着通过油泵送入储油罐,在储油罐内通过蒸汽换热将废润滑油加温至50℃左右,自然沉淀4h左右,进行油、水及杂质的初步分离。
根据类比同类型的润滑油生产厂家,该过程分离出的油、水及杂质约为0.2%左右。
经沉淀处理后的废润滑油进入原料油罐以备下一步处理。
(2)脱水
经沉淀处理后的废油用油泵送入脱水塔内进行脱水,进入脱水塔前废油通过换热器与减压蒸馏得到的馏分基础油进行换热至90℃左右,再利用真空泵抽真空使脱水塔内保持一定的负压,然后根据油、水沸点差异进行蒸馏脱水,经过脱水后进入下一流程进行处理。
(3)初馏
经脱水塔处理后的废油由管道输送至换热器进行换热,温度达到200℃左右进入初馏塔,由真空泵保持塔内负压,利用油水物理性质差异彻底去除废油水分及其他杂质,油料中的极少量低碳组分随水分一起带出,塔顶轻组分废气进入加热炉燃烧。
(4)减压蒸馏
初馏塔塔底油经塔底泵升压后再次经加热炉间接加热到390℃进入减压塔。
控制减压塔内各馏分的馏出温度分别在150℃、280~300℃、300~310℃,得到一线馏分、二线馏分、三线馏分、减顶轻质油组分和塔底重油组分。
减顶轻质油和减压塔三条侧线产品分别换热、冷却后出装置得到基础油进原料罐区待下一步处理,同时也可以作为产品进行外卖;减压塔底部重组分经换热、冷却后进入重油罐内储存外卖;塔顶产生的少量不凝汽进入加热炉燃烧。
(5)白土精制
从减压塔生产出的基础油通过泵输送至白土精制罐内,通过锅炉蒸汽换热控制温度为80℃左右,根据油料的品位人工加入0.5%左右白土进行脱色,同时用机械搅拌约30min左右,然后通过离心泵送入板框式压滤机进行压滤,使得白土渣和油品进行分离,油品进入调节罐进行冷却30min左右进入调和车间处理,白土渣交与有相应资质的部门处理。
(6)调和
从白土精制车间精制后的各种基础油分别进入不同的调和罐,按照各种润滑油的产品标准泵入混合罐,同时加入一定比例的添加剂,搅拌30min左右后成品进入包装车间。
(7)包装
成品油通过自动罐装机进行罐装、封盖、喷码、打包后进入成品仓库。
图2-1废润滑油再生循环利用工艺流程框图
图2-2废润滑油再生循环利用物料平衡图
2.3主要设备
项目主要设备选用国内先进节能设备。
序号
名称
型号规格
数量
1
加热炉
160万大卡
2
2
初馏塔
Φ1200×26000
2
3
减压塔
Φ1800×36000
2
4
脱水塔
Φ1800×23000
2
5
污水处理塔
Φ1800×9800
2
6
换热器-1
BES500-55-25-4B=200
2
7
换热器-2
BES500-65-25-4B=150
2
8
换热器-3
BES600-90-25-2B=200
2
9
换热器-4
BES600-90-25-2B=200
4
10
冷凝器-1
BJS600-90-25-2B=300
2
11
冷凝器-2
BJS700-120-25-2B=300
2
12
冷凝器-3
BJS600-90-25-2B=300
2
13
冷凝器-4
BJS500-70-25-2B=300
14
冷凝器-5
BJS600-90-25-2B=300
15
冷凝器-6
BJS600-90-25-2B=300
16
冷凝器-6
BJS500-70-25-2B=300
17
储罐1
1.6m3
1
18
储罐2
20立方
2
19
储罐3
40立方
4
20
储罐4
150立方
4
21
原料油泵
Q=24m3∕h,H=100m
2
22
脱水塔底泵
Q=24m3∕h,H=110m
2
23
初馏塔底泵
Q=24m3∕h,H=110m
2
24
减一线泵
Q=20m3∕h,H=80m
2
25
减二线泵
Q=32m3∕h,H=100m
2
26
减三线泵
Q=18m3∕h,H=100m
2
27
减底泵
Q=12m3∕h,H=100m
1
28
真空泵冷水泵
Q=32m3∕h,H=5m
29
原料注碱泵
Q=8m3∕h,H=30m
1
30
倒油泵
Q=56m3∕h,H=40m
2
31
循环水泵
Q=400m3∕h,H=50m
2
32
尾气真空泵
100L∕s
1
33
轻油装车泵`
Q=60m3∕h,H=70m
1
34
水环真空泵
24m3∕s
1
35
熔胶釜
Ф2400×4800,V=40m3
2
36
调合釜1
Ф3000×4800
2
37
调合釜2
Ф2000×3000
2
38
污油罐
Ф1900×4700
2
39
添加剂罐
Ф2400×5000
1
40
齿轮泵
YCB5/0.4-1
2
41
齿轮泵
YCB12/0.6-1
2
42
齿轮泵
YCB20/0.6-1
1
43
齿轮泵
YCB20/0.6-1
2
44
搅拌机
YCB30/0.6-1
2
45
搅拌机
XLD11-7
2
46
搅拌机
XLD7.5-6
2
47
搅拌机
XLD15-7
4
48
粉碎机
NGW-L41
1
49
单刀切胶机
SWP-30E
1
50
单刀切胶机
660-1
3建设规模及产品方案
3.1建设规模
项目拟建成一套年处理10万吨废润滑油的再生利用设施及其配套系统,主要分以下装置:
(1)10万吨/年预处理装置:
脱去废润滑油中的机械杂质和部分水分。
(2)10万吨/年蒸馏装置,减压切割分馏。
将脱除机械杂质及水分的废润滑油进行减压蒸馏,各侧线馏分就可以作为不同的润滑油原料。
(3)10万吨/年白土精制装置,进一步精制而获得合格的基础油。
(4)10万吨/年调和装置,对精制后的各种基础油加入功能剂调和后生产符合国家标准的柴油润滑油、汽油润滑油和工业润滑油。
(5)增建储运设施,装卸、储存回收的废润滑油、中间原料、产品等。
(6)配套公用设施和配套设施。
项目工程内容包括主体工程、辅助工程、公用工程、环保工程、储运工程及生产装置。
表3-1工程项目组成及主要内容一览表
类别
项目组成
主要工程内容
主
体
工
程
白土精制
加入白土进行机械搅拌后通过压滤机进行压滤将白土和润滑油进行分离。
精制罐4个15m3,调节罐4个15m3。
调和
将各种静置好的基础油按照不同的配合比混合,并加入各种添加剂通过一定时间的反应、均化后形成成品。
包装
根据需要将成品润滑油进行分装。
主
生
产
装
置
预处理装置
经化验室化验后,经格栅粗滤、沉淀除去污油中的杂质和部分水。
脱水塔
脱去原料油中的水分和少量挥发性有机质。
初馏塔
彻底脱去原料油中的水分,同时带出油料中的部分轻组分
减压分馏塔
通过保持塔内负压,分别控制三线温度将油品分三条侧线馏出,后再进行余热回收后经冷却塔冷却至常温回收进基础油原罐。
辅
助
工
程
和
公
用
工
程
供热装置
160万大卡加热炉,为进入减压塔油料提供热量。
馏出的高温基础油通过热换器进行余热回收,与待反应的冷油进行换热。
冷却系统
循环冷却水池和冷却塔,对换热过后的基础油进行冷却
给排水设施
有城市自来水供应水管网接入,排水由公司总排水口接入园区污水管网后经污水处理厂处理。
供电系统
由市电接入10kv电源经变压器变换供给用电单位,自备150kw柴油发电机组做备用电源。
办公设施
综合办公楼、化验室、职工倒班宿舍、职工食堂及浴室、消防室,占地面积约500m2。
消防
全厂消防水系统分生产水给水系统(低压)和高压消防水给水系统。
设地下式消防水池和半地下式消防水泵房,罐区和各车间岗位配备足够的灭火器,设消防值班室并制定相关消防紧预案。
维修
设立维护车间,占地面积约150m2,并配备专业的维修人员负责机械、电力电气和仪表维修。
环
保
工
程
污水处理塔
去除含油污水中的油以及其他杂质。
油水分离塔
对含油污水进行油水分离
三级气浮隔油池
除去含油污水中的浮油,处理量200m3/d。
三级隔油池
处理厂区车间冲洗废水及初期雨水,处理规模30m3/h。
危险物储存间
储存白土废渣以及压滤机的废旧滤布。
冷却塔
对经换热器进行余热回收后的基础油进一步冷却。
储
运
工
程
原料油罐
储存原料油,2个2000m3。
原料油储存罐
6个,Φ12×11.5米
成品油储存罐
20个,Φ5.5×7.5米
包装仓库
储存成品润滑油20个40m3。
基础油罐
储存外购和生产出的基础油6个1200m3。
3.2原材料、燃料消耗
本项目原料主要是回收的废旧柴油润滑油、汽油润滑油和工业润滑油。
原材料、燃料动力、生产辅助材料供应及消耗情况见下表:
表3-2原材料、燃料动力供应及消耗量表
序号
项目
单位
用量
来源
备注
一
原材料
1
废润滑油油料
万吨/年
10.0
外购
2
润滑油添加剂
吨/年
270
外购
二
辅助材料
1
白土
吨/年
450
外购
三
燃料
0.0
1
燃料油
万吨/年
0.2
工厂自给
2
天燃气
万m3/年
109.1
外购
四
动力
0.0
1
新鲜水
万吨/年
1.1
市政供水
含生活用水
2
循环水
万吨/年
218.2
3
电
万Kwh
170.9
市电供应
4
压缩空气
Nm3
2.7
间断
5
蒸汽(1.0Mpa)
万吨/年
2.2
自给
3.3产品方案
本项目的产品主要是柴油润滑油、汽油润滑油、一线基础油料、二线基础油料等国标基础油料以及工业用各种润滑油和重质燃料油。
表3-3主要产品一览表
序号
产品名称
产品规格
产品标准
产品产量
1
汽油润滑油
SG汽油润滑油
GB11121-1995
合计
50000吨
SH汽油润滑油
GB11121-1995
2
柴油润滑油
CD柴油润滑油
GB11122-1997
CF柴油润滑油
GB11122-1997
CE柴油润滑油
GB11122-1997
3
通用润滑油
SG/CF通用润滑油
GB11122-1997
SF/CD通用润滑油
GB11121-1995
4
普通车辆齿轮油
GL-4
SH/T0350-1992
5
压缩润滑油
DAB压缩润滑油
Q/YLY005-2004
6
液压油
普通液压油HL
GB11118-1994
抗磨液压油HM
GB11118-1994
7
基础油料
40196吨
8
重质燃料油
4991吨
3.4劳动定员
本项目本着精简高效的原则,拟新增人员50名管理、技术人员及生产工人。
为适应废润滑油再生利用的工作需要,提高服务质量,本项目将通过派出进修、到实践中锻炼、接纳大学毕业生,选调有实践经验的专业技术人员等途径,建立结构合理、素质较高的工作队伍。
4投资估算与经济分析
项目建设投资7200万元,其中:
建筑工程费900万元,安装工程费400万元,设备购置费3800万元,工程建设其他费用1700万元,预备费400万元。
项目建成后达产后正常年份预计出售收入5000万元,投资回收期(不含建设期)为3年。
5社会效益分析
中国的经济近年来得到了迅猛发展,伴随而来的环境污染问题也非常突出。
废物消化和处理已成为国民经济发展中的重大课题。
而废物处理与再生资源的合理开发是保护环境、节约资源、实现可持续发展的重要途径。
合理利用资源和保护环境将有助于国家基础工业和整个国民经济的协调发展。
发展国民经济必须兼顾环境保护,合理开发利用资源为子孙后代造福。
废润滑油再生资源的产业化,属于生态型资源循环利用范畴,可以在一定程度上缓解我国由于石油类资源短缺导致其在制造业实施可持续发展和人民生活水平进一步提高方面所产生的压力,从而使我国的生态恶化和资源超常规利用两大难题得到一定程度的缓解决。
项目建成后将形成有效的废润滑油回收途径,可以有效的解决资源浪费的问题,大大的节约了社会成本,提高相关行业的经济效益。
对废旧润滑油进行资源化利用,并实现产业化,将变废为宝,实现资源利用和环境保护的双重效益。
项目建成后将全面推进废润滑油再生循环利用行业的健康发展,有利于产业结构调整和优化。
本项目可新增就业岗位50个,对解决社会就业问题,进一步推进当地经济社会的快速发展具有积极意义。
6风险分析
6.1风险因素的识别
本项目属资源循环利用项目,为国家和地方支持项目,无政策风险和社会风险。
现阶段可能的主要风险因素包括:
(1)市场风险。
主要指因宏观经济波动等原因引起的产品需求量减少,库存增加、价格下降等风险。
(2)技术风险。
主要指生产过程中由于工艺先进性、工人技能、生产经验等方面原因引起的技术问题造成的损失。
(3)工程风险。
指工程地质条件、水文地质条件和工程设计本身发生重大变化,导致工程量增加、投资增加、工期拖长所造成的损失。
(4)资金风险。
主要指资金来源中断或供应不足,导致融资成本提高,给建设和生产运营造成的损失。
(5)外部协作风险。
指投资项目所需要的供水排水、供电供气、通讯、交通等主要外部协作配套条件发生重大变化,给建设和生产运营带来困难。
6.2风险分析结果的反馈
(1)资源风险分析
公司主要的生产资源是生产原辅材料及燃料、公用工程的水、电等,其价格波动对生产有直接影响,项目为节能降耗技术改造项目,本身即可降低资源消耗风险。
(2)建设规模与产品方案风险分析
本项目产品规模和方案是在现有市场需求的情况下作出的,加上近年来该产品在国内外市场份额持续上升,公司技术先进,产品质量可靠,故在建设规模与产品方案上风险不大。
(3)工艺技术、设备及自动化风险及规避
本项目计划选用国产成熟的设备,项目工艺技术及设备先进且成熟可靠,在工艺和技术方面风险不大。
7结论与建议
7.1结论
通过对10万吨/年废润滑油再生加工利用项目的技术、经济的全面研究和论证,得出以下结论:
(1)项目具有良好的市场和稳定的原料来源,并可通过实施该项目实现资源节约和环境保护的双重效益。
(2)项目技术工艺成熟,生产工艺组合了成熟可靠的传统润滑油精制工艺技术和自创的废润滑油脱水脱杂质的独特技术,优化了废润滑油再炼制再生工艺,既保证了生产过程得以连续稳定进行并使得到的产品的质量达到相应的产品标准。
(3)项目的财务分析表明项目具有良好的经济效益。
本项目不论从市场和企业发展需要来看,还是从经济效益和社会效益来看,是必要的、可能的和可行的。
项目在技术上可行,经济上合理。
7.2建议
综上所述,本项目的建设具有较强的可操作性;但是由于项目规模较大,时间较紧,开发过程中各方面工作协调难度较大。
建议强化项目进程中的投资、质量、进度计划,注重对可能发生的不利条件及变化因素的预测与防范对策,以保证项目按期完成。
(1)实行速度管理,加强项目运作进度,以避免市场可能的由高峰期向下降期转折的风险。
(2)公司各部门紧密配合,以加快项目运作进度。
(3)项目成本须合理控制,以保留市场波动时的降价应对空间。
(4)注意严格的按照既定方案去做每一件事,统一调配资金、物资和各项工作。
特别要准备好抗风险资金,不可挪用。