ABS塑料铭牌光亮镀铬工艺设计要点.docx
《ABS塑料铭牌光亮镀铬工艺设计要点.docx》由会员分享,可在线阅读,更多相关《ABS塑料铭牌光亮镀铬工艺设计要点.docx(28页珍藏版)》请在冰豆网上搜索。
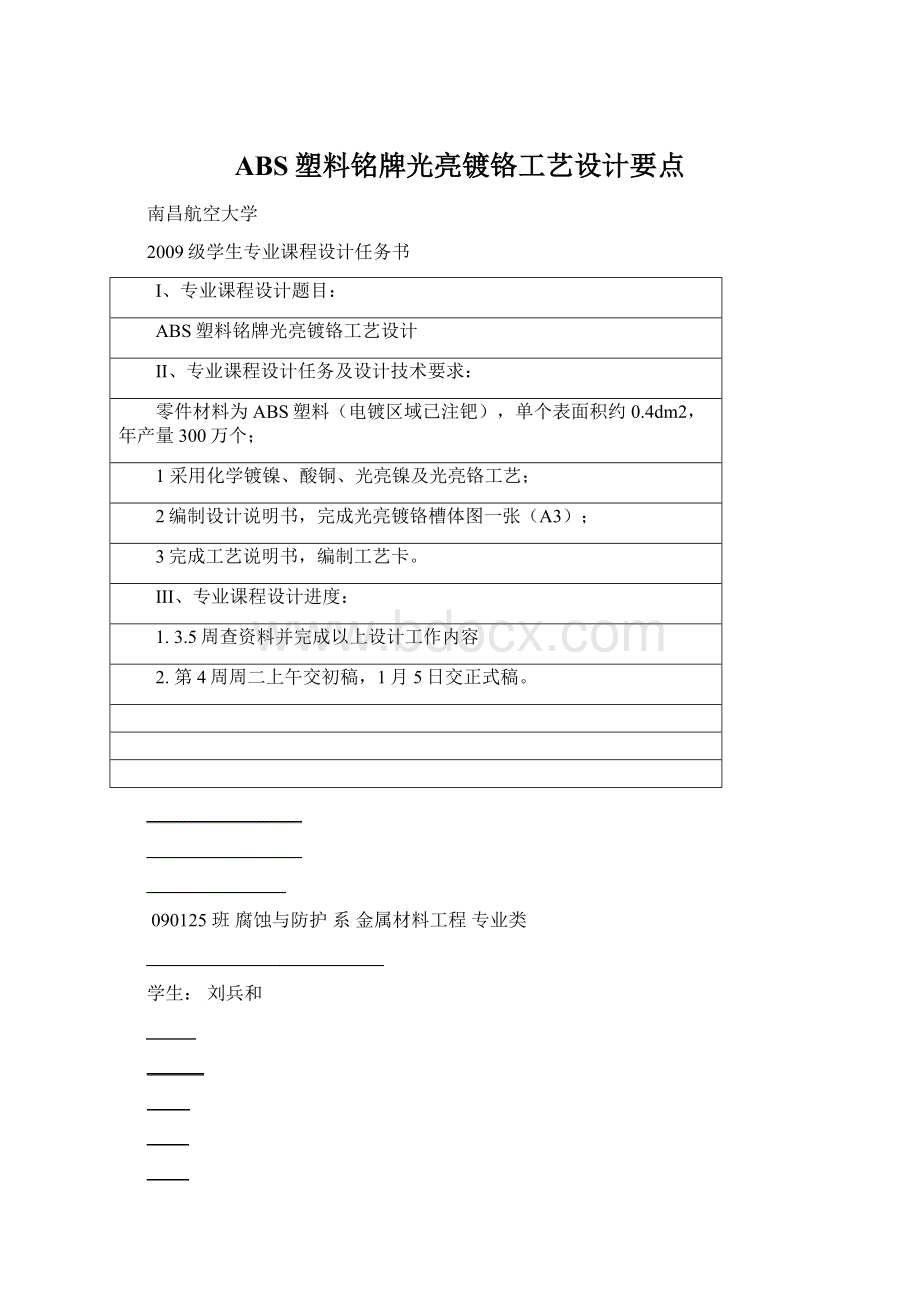
ABS塑料铭牌光亮镀铬工艺设计要点
南昌航空大学
2009级学生专业课程设计任务书
I、专业课程设计题目:
ABS塑料铭牌光亮镀铬工艺设计
II、专业课程设计任务及设计技术要求:
零件材料为ABS塑料(电镀区域已注钯),单个表面积约0.4dm2,年产量300万个;
1采用化学镀镍、酸铜、光亮镍及光亮铬工艺;
2编制设计说明书,完成光亮镀铬槽体图一张(A3);
3完成工艺说明书,编制工艺卡。
III、专业课程设计进度:
1.3.5周查资料并完成以上设计工作内容
2.第4周周二上午交初稿,1月5日交正式稿。
090125班腐蚀与防护系金属材料工程专业类
学生:
刘兵和
日期:
自2012年12月1日至2013年1月10日
指导教师:
系主任:
附注:
任务书应该附在已完成的专业课程设计说明书首页。
设计说明书1
设计说明书
1生产依据
零件材料为ABS塑料,电镀表面积为80cm2,年产量300万个,使用的是已经注钯的材料。
查阅资料大概各镀层的厚度如下:
化学镍0.3μm、光铜10μm、光镍8μm、光铬1.5μm。
工作中采用三班制,时间为8h、8h、7h,一天总共工作23h。
挂具采用一挂44的方式,每个镀槽放5挂,最长工序为镀光铜,时间为23min。
设备的年时基数为251×23-(251×23)×4%=5542小时,年产量为(5542×60/23)×220=318万个,生产纲领300×(1+5%)=315万个,故能完成生产任务。
2生产线上的主要设备及生产线的设计
2.1槽体的尺寸
槽体长度:
L=nL1+(n-1)L2+2L3
式中:
L——槽子长度
n——沿槽长方向的挂具数n=5
L1——沿槽长方向挂具的宽度L1=300
L2——沿槽长方向挂具间的距离(30~100)
L3——挂具边缘至槽壁的距离(电镀槽为80~100)
如果采用阴极移动,再加阴极移动的行程(40~140)取100
所以:
L=5×300+4×30+80+100=1800
槽体宽度:
b=nk×b1+2nk×b2+(nk+1)δ+2b3
式中:
b——槽体宽度
nk——挂具或阴极列数nk=1
b1——沿槽宽方向的挂具(工件)宽度b1=300
b2——挂具边缘至阳极表面的距离(150~250)b2=150
b3——阳极背面至槽壁的距离(30~50)b3=40
δ——阳极或阳极篮的厚度δ=20
如果采用加热或冷却管,还应考虑加热管道的直径及管道与阳极之间的距离50~100,管道与槽壁的距离50等。
取150
所以b=300+400+40+100=8400由表7-6知槽宽取1000
槽体高度:
h=h1+h2+h3+h4
式中h——槽子高度
h1——挂具工作部位(工件)的高度h1=440
h2——挂具(工件)下端距槽底的高度(100~200)h2=200
h3——挂具(工件)上端距液面的高度(80~150)h3=150
h4——液面至槽沿的距离(100~150)h4=150
所以h=150+200+80+150=940,选用的槽子为长1800、宽1000、高1000容积1086L。
2.2镀槽数量的计算
n=p×(1+a)×t×k1/60×Y×T
式中n——镀槽数量
p——年生产量(㎡)p=240
t——每次电镀所需时间(min),包挂出入槽所需的辅助时间(3min~5min内)t=26min
a——返修率a=0.04
k1——应扣除的时间系数k1=1.02
Y——设备的平均负荷量(㎡)Y=0.42
T——设备的年时基数(h)T=5542
所以n=240×(1+0.04)×26×1.02/60×5542×0.42=0.4741﹤1所以镀槽数量取1,由于镀光铜的时间最长,镀槽也只需一个就可以,因此其他镀液所需的槽子也只需一个即可。
2.3槽体材料和加热管材料
酸性镀液必须选择耐酸材料制作槽体,小槽子一般用硬聚氯乙烯塑料制造,大槽子则用钢槽衬软聚氯乙烯塑料或用钢材做框架衬硬聚氯乙烯塑料。
碱性溶液对钢铁无腐蚀作用,可以直接用钢槽体,但是为了不污染镀液,维护镀液的清洁,常用聚氯乙烯板衬里槽。
化学镀镍的要求很高,因为化学镀镍溶液有较强的还原性,容易在金属上沉积,不宜采用金属材料制作槽体及加热器,又因镀液对杂质比较敏感,所以在实际生产中常用不锈钢、聚氯乙烯、搪瓷容器做化学镀槽。
镀铬液一般含有铬酐和硫酸,对钢铁有腐蚀作用,所以常用铅板、钛板、或硬聚氯乙烯作衬里。
由于加热管是排放在镀液中的,为防腐蚀,所以加热管材料常用铅锑合金做加热管材料[1]。
各槽子材料、尺寸、数量及槽子里加热管材料如表1所示。
表1各槽子材料、尺寸、数量及加热管材料
槽子名称
镀槽材料
镀槽尺寸
槽子数量
加热管材料
除油槽
碳钢
1800×1000×1000
1
碳钢
粗化
钢槽衬软聚氯乙烯塑料
1800×1000×1000
1
铅锑合金
中和
碳钢
1800×1000×1000
1
不需加热
敏化
钢槽衬软聚氯乙烯塑料
1800×1000×1000
1
铅锑合金
还原
钢槽衬软聚氯乙烯塑料
1800×1000×1000
1
铅锑合金
槽子名称
镀槽材料
镀槽尺寸
槽子数量
加热管材料
活化
钢槽衬软聚氯乙烯塑料
1800×1000×1000
5
铅锑合金(不加热不用)
化学镍
不绣钢
1800×1000×1000
1
铅锑合金
光铜
钢槽衬软聚氯乙烯塑料
1800×1000×1000
1
铅锑合金
铬酸钝化
钢槽衬软聚氯乙烯塑料
1800×1000×1000
1
不需加热
镀铬
钢槽衬软聚氯乙烯塑料
1800×1000×1000
1
铅锑合金
热水洗槽
碳钢
1800×1000×1000
1
碳钢
冷水洗槽
硬聚氯乙烯塑料
1800×1000×1000
30
不需加热
2.4整流器的选择
光铜选用可控硅整流器I=35AU=20VP=700W
光亮镍选用可控硅整流器I=20AU=30VP=600W
镀铬选用可控硅整流器I=20AU=25VP=500W[2]
直流供电方式采用单机单槽供电的形式,这种供电方式调节电流最方便,可使镀槽的电流电压平稳可靠,不受其他镀槽调节电流的干扰[1]。
2.5过滤机
需要连续过滤的溶液过滤机选择磁力泵加压的简式过滤机,其技术规格为:
最大过滤量为20m3/h,工作压力为0.23Mpa,过滤面积为1.53㎡,使用温度68℃,外形尺寸为700×670×1150mm。
光铜、镀光镍采用该过滤机。
溶液在一定使用周期内的间歇过滤选择离心泵加压的简式过滤机,选择的过滤机型号为XT-20,其过滤面积为9㎡,最大流量为20m3/h,使用温度≤70℃。
光铬采用该过滤机。
2.6水泵
由于生产过程中的多道水洗是采用的是逆流水洗,因此生产中需要用泵将后一道水洗槽的水不断的抽到前一道水洗槽中。
根据要求选用的水泵型号为1B-09型不锈钢涡流泵,其流量为2.7~10.8m3/h。
生产中需要19台这样的水泵[3]。
2.7生产线形式的选择
生产线为环形电镀自动线,用自动线生产即可以提高生产效率,降低劳动强度又能稳定镀层质量和改善工作条件,所以进行大批量生产的车间应该实现自动线生产。
环形电镀自动线由于采用机械连动运送装置,自动线上各个槽一般为满负荷状态,因此效率高,产量大,适合该生产要求。
2.8生产线的控制
生产线采用数据控制系统,各槽子采用温度自动控制系统来自动调节镀槽的温度。
3生产线上的水、电、气的设计
3.1水消耗量计算
3.1.1清洗槽用水量计算
多道水洗采用的逆流水洗,每次换水时只补充最后一道水洗槽的水。
小时用水量=槽体有效容积×小时换水次数
最大小时用水量=槽体有效容积×(维持用水小时换洗次数+1)0
计算平均小时用水量时,三班制生产的水槽按1小时最大用水量与22小时维持用水量之和,以23小时平均计算。
根据《腐蚀与防护工程》表9-2,热水槽的换水次数为0.3次/h,小时用水量为0.325m3/h,根据《腐蚀与防护工程》表9-3,最大小时用量为2.16m3/h。
根据《腐蚀与防护工程》表9-3,冷水槽的小时平均消耗量为1.08m3/h,最大小时用水量为.365m3/h,冷水槽的平均小时用水量为(2.16+22×1.08)/23×15=16.90m3/h,热水槽的平均小时用水量为(1.365+22×0.315)/23×1=0.36m3/h,冷水槽的小时用水最大量为2.12×15=31.8m3/h,热水槽的小时用水最大量为1.365×1=1.365m3/h。
3.1.2夹套用水量计算
夹套用水量按夹套的容积来计算的小时平均用水量为0.3~0.5夹套容积/h,小时最大用水量为2.0夹套容积/h。
夹套容积为1152m3,工艺中镀铬和化学镍槽均使用夹套式加热,因此夹套的小时平均用水量为2×0.4×0.1152=0.092m3/h,小时最大用水量为2×2×0.1152=0.4608m3/h。
3.1.3更换溶液用水
除油为30天换一次,粗化90天换1/2,因此更换溶液用水为1.05/(30×24)×1+1.05/(180×24)×1=0.0017m3/h。
3.1.4配制溶液液用水
配制溶液液所需用水为1.05×42=44.1m3
3.1.5车间用水总量计算
水量的总消耗按下式计算:
Qvag=Q1K1Qmax=Q2K2;
式中:
Qvag——车间小时用水平均总量Qmax——车间小时用水平最大总量;
Q1、Q2分别为各用水设备的小时平均及最大值;
K1——设备使用系数,采用0.7~0.9使用系数=工作班内实际用水时间/工作班时间;
K2——设备同时换水系数,采用0.8~0.9同时使用系数=同时使用的用水设备数/用水设备总数。
车间的小时平均总耗量和生产班次,可以算出车间的昼夜耗水量,而小时最大耗水量则作为车间管道计算的依据。
在确定系统中各管道直径时,其在管道当中的流速不宜大于2m/s,一般以1m/s为宜
Q1=14.91+0.36+0.092+0.0017+44.1/5124=15.37m3/h
Q2=31.8+1.365+0.4608+0.0017+44.1/5124=33.64m3/h
Qvag=Q1K1=15.37m3/h×0.8=12.296m3/h
Qmax=Q2K2=33.64m3/h×0.9=30.276m3/h
所以车间的年总耗水量为Qvag×5124=63004.704吨。
3.2蒸汽消耗量计算
3.2.1固定槽的蒸汽消耗量计算
(1)加热过程蒸汽计算
用蛇管或排管加热溶液所消耗的量为
Q=[V×ρ×c×(t2-t1)/t+V×q]β×4.186
Q——溶升温所需要的热量KJ/h
V——槽液体积(L)
ρ——溶液密度(Kg/L)
c——溶液比热容(KJ/Kg×℃)(水及水溶液ρc=1;油ρc=0.5;发蓝槽ρc=1.1)
t1——镀液初始温度(室温)
t2——镀液工作温度(℃)
q——单位体积水溶液加热过程中的平均耗热量,q值应根据槽子的体积和工作温度在图7-11中查找,图中温度按(t2+t1)/2计算。
β——热量损失系数,槽子有保温层时β=1.1~1.15,无保温层时β=1.15~1.3
t——升温时间(h),根据表7-7得加温时间为1.5h
蒸汽消耗量的计算G=Q/y
G——蒸汽消耗量(KJ/h)
Q——镀液加热或热水槽工作时所需的热量(KJ/h)
y——蒸汽的潜热当电镀车间蒸汽压力p=0.pa时,y=2164KJ/Kg;当p=0.2MPa时,y=2135KJ/Kg,计算中取p=0.3MPa
蒸汽加热管的面积计算,所需的传热面积:
S=Q/K△t
式中:
S——加热管所需的传热面积(㎡)
Q——镀液加热或热水槽工作所需的热量(KJ/h)
K——加热管的传递系数(见《腐蚀与防护工程》表7-9)
△t——饱和蒸汽温度与溶液平均温度差
所需加热管的长度的计算
L=S/D
式中:
L——所需加热管长度(mm)
S——所需传热面积(mm2)
D——选用的加热管的外径(根据《腐蚀与防护工程》表7-11选择)
(2)保温时蒸汽消耗量计算
溶液保温时蒸汽消耗量可分为两部分计算,一部分是槽体内溶液及水保温时的耗热量,另一部分是零件吸收的热量,可表示为:
Q1=V×q1+Wc1(t2-t1)β
G1=Q1/ρ
式中:
Q1——溶液保温所需要的热量KJ/h
q1——单位体积溶液及水保温时耗热量,查《腐蚀与防护工程》图7-11(相同于加热过程中的平均消耗)
W——单位时间内放进槽内的零件质量(Kg/h)
t1——放进槽内之前零件的温度
t2——槽子工作温度
β——加热损失系数(1.11.3)
根据以上各公式得到各加热槽所需的热量、蒸汽消耗量、加热管直径和长度如下:
除油:
Q=113896.87KJ/hQ1=1187.55KJ/hG=52.63Kg/hG1=0.54Kg/h管长L=4.58m管直径D=25mm
粗化:
Q=168486KJ/hQ1=2327.01KJ/hG=77.85Kg/hG1=1.07Kg/h加热管长L=6.36m管直径D=40mm
③敏化:
Q=21903.245KJ/hQ1=1074KJ/hG=10.12Kg/hG1=0.49Kg/h加热管长L=1.82m管直径D=15mm
④还原:
Q=21903.245KJ/hQ1=1074KJ/hG=10.12Kg/hG1=0.49Kg/h加热管长L=1.82m管直径D=15mm
⑤化学镍:
Q=68859.7KJ/hQ1=1156.26KJ/hG=31.82Kg/h
G1=0.53Kg/h管长L=3.184m管直径D=20mm
⑥活化:
Q=21903.245KJ/hQ1=1074KJ/hG=0.12Kg/hG1=0.49Kg/h加热管长L=1.82m管直径D=15mm
⑦光铜:
Q=27836.9KJ/hQ1=1088.64KJ/hG=12.86Kg/hG1=0.50Kg/h加热管长L=1.765m管直径D=20mm
⑨活化:
Q=79188.655KJ/hQ1=1156.26KJ/hG=36.59Kg/hG1=0.53Kg/h加热管长L=4.26m管直径D=25mm
⑩光镍:
Q=113896.87KJ/hQ1=1260KJ/hG=52.63Kg/hG1=0.58Kg/h加热管长L=6.42m管直径D=25mm
光铬Q=143887.47KJ/hQ1=2083.2KJ/hG=66.49Kg/hG1=0.96Kg/h加热管长L=3.74m管直径D=40mm
3.2.2车间蒸汽总消耗量计算
蒸汽消耗总量可按下式计算:
Gevg=G1k1Gmax=G2K2
式中:
Gevg、Gmax——分别为车间蒸汽平均及最大总消耗量(Kg/h)
G1、G2——各用蒸汽设备的平均及最大消耗量之和(Kg/h)
k1——设备使用系数,采用0.7~0.9
K2——设备同时加热系数,采用0.8~1.0
根据以上公式得:
Gevg=8.07×0.8=6.456Kg/h
Gmax=502.4×0.9=452.16Kg/h
3.2.3蒸汽的来源
用锅炉产生蒸汽,锅炉为燃气锅炉。
3.3压缩空气消耗量计算
3.3.1喷嘴压缩空气消耗量
采用直径为5mm的喷嘴,压缩空气压力为0.3MPa,连续工作时自由空气消耗量为0.8m3/min。
3.3.2搅拌溶液的压缩空气消耗量
根据生产经验数据,可将每个空气吹孔的送风量定为(8~14)L/min.所以搅拌的风量应为:
Q=0.06nq(m3/min)
式中Q——送入槽内的风量
n——空气管的孔数(取14)
q——每个孔的送风量(8~14)L/min.搅拌一般镀液时送风量应选小值,用于清洗槽及镀槽教深时选最大值。
搅拌一般镀液时:
Q=0.06×14×8=6.72m3/min
清洗槽及较深槽时:
Q=0.06×14×14=11.76m3/min
3.3.3压缩空气消耗量计算
在计算压缩空气的平均消耗量及最大消耗量时,应考虑用气设备的使用系数和同时作用系数。
同时作用系数与各用气设备的用气特点、数量及作用等因素有关,一般可取0.4~0.6。
使用系数根据用气设备的生产负荷、工作条件等具体情况确定,用气设备的使用系数为:
吹嘴:
0.1~0.3搅拌溶液:
0.5~0.8
根据以上数据可求出车间压缩空气的平均消耗量和最大消耗量:
压缩空气平均消耗量=设备数量×每台设备连续工作时自由空气消耗量×使用系数(m3/min)
压缩空气最大消耗量=设备数量×每台设备连续工作时自由空气消耗量×同时作用系数(m3/min)
所以压缩空气平均消耗量=224.68m3/min
压缩空气最大消耗量=179.744m3/min
3.4电力消耗量计算
3.4.1各直流电源用电
镀光铜的可控硅整流器P=700W
镀光亮镍的可控硅整流器P=600W
镀光铬的可控硅整流器P=500W
所以各电镀槽电镀工作用电总共为P=1800W
3.4.2机械搅拌移动
机械搅拌选用阴极移动,阴极移动往复次数为为(10~30)次/min移动行程为40~140mm,长度为2000mm的镀槽使用370W电机。
生产线上总共有3个槽子需阴极移动,所以P=3×370=1110W[1]。
3.4.3照明用电
照明光源可采用荧光灯或白炽灯等,采用50W的白炽灯照明。
4挂具的设计
4.1挂具的装载量
电镀中采用每挂零件数为22个,零件总面积为1760cm2。
4.2挂具的结构
挂具支杆长860mm,主杆为480mm,支杆与提杆之间的距离为280mm,每个挂钩之间的距离为290mm。
4.3挂具的材料
挂具采用铜—钢合制的挂具,为保证挂具与导电杆接触并有良好的导电能力,吊钩用铜金属,提杆、主杆、支杆采用普通钢,挂钩采用弹簧钢。
对挂具需缘部位用涂覆环氧树脂的方法[4]。
5生产线上人员配置和管理
5.1生产工人的人数
自动生产线上每台吊车1人,溶液维护调整1人,装卸零件工人按自动机的量配备2人。
每台吊车在生产线上总共需要92min,每隔23装一挂,所以线上保持有四台吊车,一天3班制,从而每天有24个工作岗位,在此基础上增加5-8%的顶替缺勤工人的系数,即生产工人=岗位人员×(1+0.08)=24×1.08=25.92,所以需要生产工人26名。
5.2辅助工人
一般为生产工人的30-50%,所以辅助工人有13名。
5.3检验人员
检验人员一般为生产工人的4-5%,所以检验人员有2人。
5.4行政管理及工程技术人员
一般为生产工人的18-20%,即5人。
5.5勤杂人员
一般为工人总数的2-3%,即1人。
所以该车间的总人数为47人。
6车间的设计
6.1车间组成及面积
(1)生产部分
一般工艺流程确定后,按所绘平面布置图计算出所需生产面积。
其面积为S=48m2
(2)辅助部分
辅助面积=生产面积×20-50%=20m2
(3)生活部分
6.2车间区划分
生产部分布置在厂房中间,辅助部分及生活间布置在两端,另外设置底下室,地下室可布置通风室[3]。
7环保及安全措施
7.1电镀废水处理
7.1.1镀铬废水处理
处理电镀含铬废水常用的方法用亚硫酸盐还原处理法,主要优点是处理后水能达到排放标准,并能回收利用氢氧化铬,设备和操作也较简单。
处理电镀含铬废水流程如下:
亚硫酸盐还原法处理含铬废水,一般采用间歇式处理流程,适用小水量的处理。
当用于处理水量教大的场合时,可采用连续式处理流程,但必须设置自动检测和投试剂装置,以保证处理水的质量。
也有设计容积较大的两个调节池,交替使用,形成间歇式集水,连续式处理的流程[5]。
7.1.2硫酸镀铜废水处理
硫酸铜镀铜的镀件清洗水中,由于镀槽槽液的配方成分简单,因此,废水中的铜离子用阳离子交换离子树脂很容易除区。
一般采用H型强酸阳离子交换树脂.
处理硫酸镀铜废水流程如下:
一般均采用双阳极柱全饱和处理流程。
第1个交换柱与第2个交换柱串联运行,当第1交换柱树脂达到饱和后进行再生,再生后串联于第2个交换柱后,这样反复交替运行水循环使用.过滤柱,交换柱的反洗,淋洗等的排水排入电镀混合废水系统中,处理合格后排放.交换柱的再生洗脱液,一部分直接返回镀槽作为补充液,其不平衡部分的量定期进行电解回收金属铜。
7.1.3含镍废水处理
由于镍盐价格较高,为节省资源,处理含镍废水多采用回收方法.离子交换法能达到回收镍的目的,工艺操作比处理含铬废水简单,但其有独特之处.
处理含镍废水流程如下:
采用固定床离子交换,一般采用双阳柱全饱和处理流程,即设置2个离子交换柱,当第1交换柱泄漏镍时,串联第2交换柱进行运行;当第1交换柱阳树脂交换达到饱和后进行再生,此时第2个交换柱单柱运行;待第2交换柱泄漏镍时,再与已再生的第1交换柱串联,这样2个交换柱交替换用。
固定床树脂再生在柱内进行[5]。
7.2安全措施
7.2.1局部排风
(1)电镀车间中,在位置固定的产生有害物质的槽边及工作地必须设置局部排风,以排出散发出来的有害气体、有机溶剂挥发物以及在喷砂、抛光过程中产生的大量粉尘。
由于槽宽为800,大于500,所以宜采用双侧或周边风罩,且槽子长度大于1200,槽边风罩应设置导流板或做成楔形条缝口或分段设置风罩。
各固定槽的条缝式低截面双侧性能如表2所示。
表2固定槽的条缝式低截面双侧性能
槽子名称
产生的有害气体
Vx(排风计算风速)
排风量
排风罩的长度
条缝高度
光亮铬或钝化或粗化
铬酸雾
0.4
2880
1000
58
镀镍或化学镍或镀铜
酸性蒸汽
0.5
4360
1000
54
化学除油
碱雾
0.3
2500
1000
42
(2)排风管道的设计及敷设
①排风管道的风速和管道截面积的计算
排风管道的风速以固体不积累在管内为度,工业上排风系统的推荐风速和阻力可参考《腐蚀与防护工程》表7-26。
如果槽子的排风量已确定,再根据《腐蚀与防护工程》表7-26选定管内的风速,就可以依下式计算凤管的截面积:
S=Q/3600v
式中:
S——管道截面积(㎡)
Q——排风量(m3/h)
v——管道风速(m/s)
根据上式可以得出上表中的各管道的截面积分别为28.8、43.6、25.00.风管材料采用硬聚氯乙烯板焊接而成。
②风道的敷设方式
风管的敷设方式采用地下室形式,将通风管道和通风设备安装在车间的地下室,通风设备集中,管理方便。
车间