探测器后盖模具设计及其型腔仿真加工.docx
《探测器后盖模具设计及其型腔仿真加工.docx》由会员分享,可在线阅读,更多相关《探测器后盖模具设计及其型腔仿真加工.docx(15页珍藏版)》请在冰豆网上搜索。
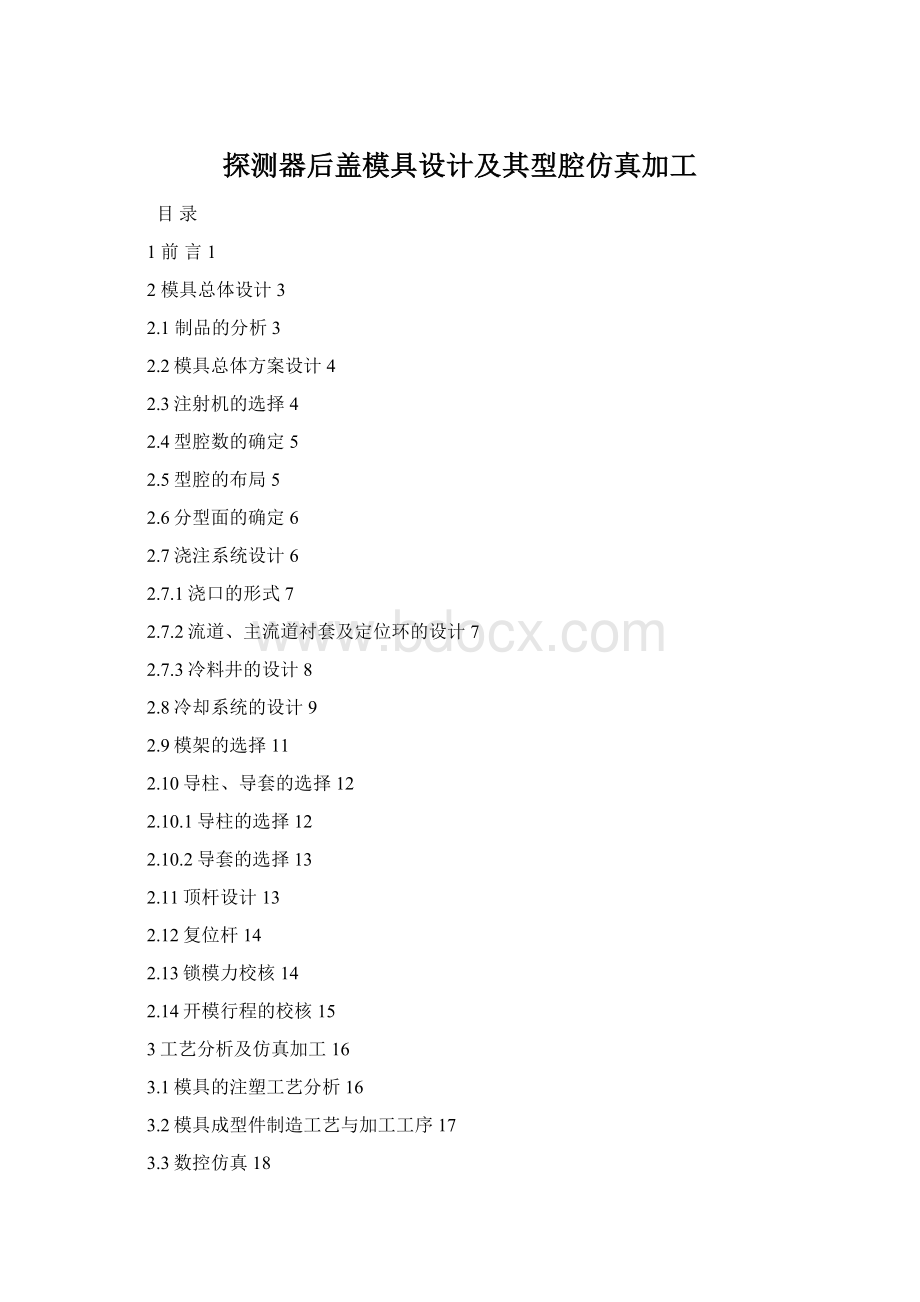
探测器后盖模具设计及其型腔仿真加工
目录
1前言1
2模具总体设计3
2.1制品的分析3
2.2模具总体方案设计4
2.3注射机的选择4
2.4型腔数的确定5
2.5型腔的布局5
2.6分型面的确定6
2.7浇注系统设计6
2.7.1浇口的形式7
2.7.2流道、主流道衬套及定位环的设计7
2.7.3冷料井的设计8
2.8冷却系统的设计9
2.9模架的选择11
2.10导柱、导套的选择12
2.10.1导柱的选择12
2.10.2导套的选择13
2.11顶杆设计13
2.12复位杆14
2.13锁模力校核14
2.14开模行程的校核15
3工艺分析及仿真加工16
3.1模具的注塑工艺分析16
3.2模具成型件制造工艺与加工工序17
3.3数控仿真18
4结论22
参考文献23
致谢24
附录25
1前言
随着塑料工业的飞速发展和通用塑料与工程塑料在强度和精度等方面的不断提高,塑料制品的应用范围也在不断地扩大。
在工业产品中,一个设计合理的塑料件往往能代替多个传统金属结构件,加上利用工程塑料特有的性质,可以一次成型非常复杂的形状,并且还能设计成卡装结构,所带来的效果是明显的,因此,近年来工业产品塑料化的趋势不断上升。
注塑成型是塑料加工中最普遍采用的方法,其中最主要之一的注塑模具已经很广泛的采用。
它在质量、精度、制造周期以及注塑成型过程中的生产效率等方面水平的高低,直接影响产品的质量、产量、成本及产品的更新换代,同时也决定着企业在市场竞争中的反应能力和速度。
注塑模具与其它机械行业想比,有以下三个特点:
第一,模具不能像其它机械那样可作为基本定型的商品随时都可以在机电市场上买到。
模具制造不可能形成批量生产,即模具是单件生产的,其寿命越长,重复加工的可能性越小。
因此,模具的制造成本较高。
第二,因为注塑模具是为产品中的塑料制品而订制的,作为产品,除质量、价格等因素之外,很重要的一点就是需要尽快地投放市场,所以对于为塑料制品而特殊定订制的模具来说,其制造周期一定要短。
第三,模具制造是一项技术性很强的工作,其加工过程集中了机械制造中先进技术的部分精华与钳工技术的手工技巧,因此要求模具工人具有较高的文化技术水平,特别是对企业来说要求培养“全能工人”,使其适应多工种的要求,这种技术工人对模具单件生产方式组织均衡生产是非常重要的。
综上所述,模具制造存在成本高,要求制造周期短,技术性强等特点,目前,随着科学技术的不断发展和计算机的应用,这些问题得到了很大的改善。
注塑模具的特点:
a)塑料的加热、塑化是在高温料筒内进行,而不是在模具内进行,因而模具不设加料腔,而设浇注系统,熔体通过浇注系统充满型腔。
浇注系统对注塑模来说至关重要。
b)塑料熔体进入型腔之前,模具已经闭合。
在注塑过程中需根据塑料特性,在模具中设加热或冷却系统。
c)注塑模生产适应性强,既可注塑小型制品,也可注塑大型制品;既可注塑简单制品,也可注塑复杂制品,生产率高,容易实现自动化。
d)注塑模一般是机动的,结构一般较复杂,因而制造周期较长,成本较高。
注塑模具的应用在当今的时代会越来越广的,它的特点使得它的用处越来越宽,涉及的范围也大了[8]。
模具表面的光整加工是模具加工中未能很好解决的难题之一。
模具表面的质量对模具使用寿命、制件外观质量等方面均有较大的影响,我国目前仍以手工研磨抛光为主(约占整个模具周期的l/3),不仅效率低,且工人劳动强度大,质量不稳定,制约了我国模具加工向更高层次发展。
因此,研究抛光自动化、智能化是重要的发展趋势。
日本已研制了数控研磨机,可实现三维曲面模具的自动化研磨抛光。
国外在模具生产中,计算机辅助设计与辅助制造(CAD/CAM)技术已得到十分成功的应用。
三维造型和型腔的数控加工都是由计算机辅助软件完成的,它大幅度的缩短了模具的生产周期,提高工作效率。
德、美、日、法、意等工业发达国家在模具设计制造领域仍处于国际领先水平,他们的一些先进的模具方面的技术被许多发展中国家,甚至是其它发达国家学习采用。
亚洲以日本和韩国模具技术水平最高,其它国家与之还有较大的差距,不过他们也正在以惊人的速度发展着,国家之间的交流会使之发展更快。
本课题是关于探测器后盖的注塑模具设计。
要求运用所学知识,能很好的对注塑模具进行设计.达到熟练的掌握注塑模具的设计知识,并能对注塑模具设计有更高层次的认识的目的。
该课题的设计要求通过基于现代CAD技术的注塑模设计,在设计过程中掌握模具设计的一般规律,对于运用现代CAD技术进行模具设计进行研究和应用,完成探测器后盖注塑模具设计.所设计探测器后盖注塑模具要能满足模具工作状态的质量要求,使用时安全可靠,便于维修,在注塑成型时要有较短的成型周期,成型后有较长的使用寿命,具有合理的模具制造工艺性.选择注塑模型腔进行加工分析,用数控加工进行编程加工。
本课题要解决的主要问题是壳体注塑模具工艺方案的拟定和壳体注塑模具的设计。
注塑模具设计总体思路如图1-1所示
图1-1模具设计思路图
本课题要达到的预期效果:
a.外观及尺寸均符合要求,未出现溢边、缩坑等缺陷;
b.结构合理;
c.镶拼简单,加工简便;
d.顶出动作平稳、可靠。
2模具总体设计
2.1制品的分析
探测器后盖制品的形状由曲线和一些复杂的凹槽构成,由于测量工具的有限对曲面和较小的凹槽测量有较大误差。
在测绘曲面时采用多断面测量,对较小的凹槽测绘采用工具和估测相结合的方法,并且对探测器后盖结构进行了优化处理。
探测器后盖测制品图及三维造型如2-1、2-2所示。
图2-1制品图
图2-2制品的三维造型
该制品是ABS(苯烯腈-丁二烯-苯乙烯)塑料,重量约30g。
据参考文献[3]P20可知,ABS的密度1030~1070
,收缩率0.3~0.8%,模具温度50~80℃注射压力60~100Mpa,最大不溢料间隙0.04mm,塑件的尺寸精度为5~6级,则模具型腔的尺寸精度应为IT10~IT11级。
2.2模具总体方案设计
设计模具时,首先确定合适的注塑机,并了解它的技术规范要求:
注塑机的最大注塑量、最大注塑压力、最大锁模力、最大成型面积、模具最大厚度和最小厚度、最大开模行程、模板安装模具的螺钉孔的位置和尺寸、注塑机喷嘴孔直径和喷嘴球头半径值。
再根据现有注塑机的规格、所要求的塑件的质量、塑件成本及交货期等,确定型腔数目。
浇注系统分为主流道、分流道、浇口、冷料穴等。
由于主流道与高温高压的熔融塑料接触所以外面要加个浇口套。
分浇道的形状尺寸主要取决于塑件的体积、壁厚、形状以及所加工塑料的种类、注射速率、分浇道长度等。
主流道与分流道采用圆角过渡,这样可以减小料流转向过渡时的阻力。
分流道的布置要均匀处理,确保熔融塑料由主流道到各分流道的距离相等。
分流道表面不必很光,可以使熔融塑料的冷却皮层固定,有利于保温。
分流道与浇口采用圆弧过渡,有利于熔料的流动及填充。
浇口是连接分流道和型腔的桥梁,它具有两个功能:
第一,对塑料熔体流人型腔其控制作用;第二,当注塑压力撤销后,浇口固化,封锁型腔,使型腔中尚未冷却固化的塑件不会倒流。
根据制品的特点初采用潜伏式浇口。
型腔分型面和形状的确定:
注塑模有一个分型面和多个分型面的模具,分型面的位置有垂直于开模方向、平行于开模方向以及倾斜于开模方向几种,分型面的形状有平面和曲面等。
根据制品的形状采用平面分型。
拉料杆主要是保证浇注系统的凝料从定模浇口套中拉出,留在动模一侧,便于取出。
排气系统的设计:
本模具采用间隙排气,利用分型面的配合间隙自然排气。
推出机构的设计:
推动的动力来源有手动推出、机动推出和液压与气动推出机构。
本设计可采用机动推出,在部分的顶杆设计时可要特殊加工。
合模时复位杆首先与定模边的分型面接触,而将推板和所有的推杆一道推回原位。
本模具设计采用塑件留在动模,要保证塑件不应推出变形或损坏,还要保证塑件的良好外观和结构可靠。
2.3注射机的选择
注塑模具是与注塑机配套使用,因此设计时注塑机的选择尤为重要。
从模具设计的角度出发,应了解的注射机的技术要求有:
注射机的类型、最大注射量、最大注射压力、锁模力、最大注射面积、模具的最大和最小闭合厚度、最大开模行程以及模具在注射机上安装时所需的定位孔的大小、螺钉孔的位置等等。
根据制品的大小及企业生产状况,选择SZ-100/60注射机,其主要参数如表2-1所示。
表2-1注射机参数
型号
SZ-100/60
螺杆直径(mm)
Φ35
注射容量(cm3或g)
100`
注射压力(N/cm3)
150
锁模力(KN)
600
最大注射面积(cm2)
模具厚度(mm)
170~300
模板行程(mm)
300
喷嘴球半径(mm)
10
喷嘴孔直径(mm)
4
喷嘴伸出量(mm)
20
顶出行程(mm)
80
外形尺寸(m*m*m)
3.9X1.3X1.8
2.4型腔数的确定
据参考文献[3]可知,以机床的注射能力为基础,每次的注射量不超过注射机最大注射量的80%,按参考文献[3]公式计算模具的型腔数:
n=(0.8G-
)/
(2-1)
式中:
—注射机的最大注射量(g);
—单个塑件的重量(g);
—浇注系统的重量(g)。
n=(0.8x105-6)/30
n=2.5
模具型腔个数选一模二腔。
2.5型腔的布局
由于型腔的布置与浇注系统布置密切相关,因而型腔的排布在多型腔模具设计中应加以综合考虑。
型腔的排布应使每个型腔浇口处有足够压力,以保证塑料熔体同时均匀地充满型腔,使各型腔的塑件内在质量均一稳定,这就要求型腔与主浇道之间的距离尽可能最短,同时采用平衡的浇道和合理的浇口尺寸以及均匀的冷却等。
合理的排布可以避免塑件尺寸的差异、应力形成和脱模困难等问题。
本设计是一模两腔,为合理的设计浇注系统和容易脱模,型腔的布局如下:
图2-3型腔的布局
2.6分型面的确定
分开模具能取出塑件的面,称作为分型面,其它的面称作分离面或分模面,注射模只有一个分型面。
选择分型面时,应根据几何形状的外观质量、浇注系统的合理布置、便于取件、利于排气等因素综合考虑,为了便于脱模,分型面的位置宜取在塑件外形轮廓最大处。
分型面的方向尽量采用与注塑机开模是垂直方向,形状有平面,斜面,曲面。
由于本制品是下大上小的特点,根据上述选择分型面的原则,本制品的分型面选择在图2-4的最大轮廓处。
图2-4分型面位置图
2.7浇注系统设计
浇注系统的作用就是将熔融状态的塑料均匀、迅速地输入型腔,使型腔内体及时排出;并且将注射压力传递到型腔的各个部位,从而得到组织紧密的制品。
浇注系统通常由主流道、分流道、浇口和冷料穴四部分组成。
2.7.1浇口的形式
浇口是浇道与型腔之间最短的一段距离,能够增加和控制塑料进入型腔的流速并封闭装填在型腔内的塑料。
浇口位置的选择对制品的质量显得尤为重要,根据文献[3]浇口选择的一般要求是:
a.塑件能量的损失最小;
b.
如下:
1)成型件制造工艺过程和顺序;
2)成型件成形加工,包括孔系加工,沟槽和平面加工等;
3)成型件热处理工艺,包括淬火、氮化工艺以及表面强化工艺等;
4)成型件型面的精饰加工,包括塑料模型腔皮纹加工、抛光与研磨加工等。
2.模具成型件的加工工艺。
1)粗加工工序粗加工为精加工的预加工工序,也可作为精度、表面粗糙度和质量要求不高,作为非配合面的最终加工。
2)精加工工序一般可作为最终加工工序,注射模具的凹凸模的成形铣削可达IT8~10、表面粗糙度可达Ra1.6~0.8um;电火花加工电极损耗可以达0.02%~0.1%、表面粗糙度可达Ra0.3~1.25um。
3)精饰加工工序一般在热处理后进行,其工艺内容包括研磨、抛光皮纹加工等。
即从模具凹凸模型面上去除极小余量,使工件最终达到形状、尺寸及其精度和表面粗糙度要求。
表3-2模具成型件常用加工工艺组合
模具类别
加工工序
加工工艺配置1
加工工艺配置2
成型模
凸、凹模加工
工艺组合
粗加工
普通立铣成形铣
CNC加工中心成形加工
精加工
普通立铣成形铣
CNC加工中心成形加工
研磨抛光
手工机械研、抛
手工机械研、抛
现选择模具中典型的零件分析其加工工艺:
1.板类零件的加工工艺分析——定模底座
铣六个面→精铣六个面→钻孔→扩孔→攻丝→磨精度要求高的部位
2.型腔的加工工艺分析——定模板
铣六个面→精铣六个面→数控铣削凹模→钻孔→扩孔→电脉冲加工凹模→磨上下表面和导柱孔→精磨凹模
3.轴类零件的加工工艺分析——导柱
铣两端面→车表面达到图样要求→磨表面
3.3数控仿真
MasterCAM是一套基于Windows的PC级CAD/CAM软件。
它具有优秀的数控编程功能,有效地解决了几何造型、零件几何形状的显示,交互设计、修改及刀具轨迹生成,走刀过程的仿真显示、验证等问题。
本设计采用MasterCAM对由Pro/e以igs形式另保存的型芯进行NC加工。
首先打开UG型腔造型图,以igs形式另保存。
在MasterCAM下进行仿真加工。
根据特征分析,考虑到圆角干涉,因此本设计加工采用横向行切法。
a.选择加工参数
MainMenu→File→Get选择以igs形式另保存的文件,然后MainMenu→
Toolpathe→Jobsetup出现如图4-1所示:
图4-1加工参数
单击Boundingbox出现对话框,进行设置。
b.刀具选择
根据尺寸精度要求及所选择的刀具要求,计算出刀具加工轨迹。
刀具轨迹包括了粗、精、残料加工的轨迹。
本设计采用12mm平底刀进行粗加工,然后采用8mm平底刀进行精加工。
MainMenu→Toolpathe→Contour→Chain选取外轮廓,选择Endhere→Done出现Toolparametersr选取刀具。
图4-2刀具选择
c.确定后出现刀具路径
d.一系列参数的设置见表5-1所示。
表4-1参数设置
Tooldia(刀具直径)
3
Depth(切削深度)
0.2
Spindle(主轴转速)
1500
Stepover(切削间距)
75%刀具直径
FeedRate(X、Y向进给)
150
Cuttingmethod(切削方法)
Zigzag
Plunge(Z向进给)
35
Max.RoughStep(粗加工切削量)
2.0
Retract(返回)
500
FinishCuts(精加工切削次数)
4
FinishStep(精加工切削量)
0.5
e.进行加工
f.数控加工后置处理程序的生成
利用MasterCAM,根据加工机床数控代码的约定处理,生成数控程序。
图4-3刀具选择
图4-4刀具选择
4结论
通过这次的毕业设计,我对注塑模模具进行了深入的研究,而我设计的探测器后盖塑模模具,有以下特点:
a.模具采用的是单分型面注塑模具。
b.模具采用潜伏式进料口浇注的方式,这样可以保证产品外表面有较高的工艺性。
c.本设计采用是一模两腔式模具,生产效率完全可以达到生产要求。
d.模板零件大部分均采用标准件,这样就大大缩短了模具的开发周期,模具的型腔结构复杂,加工时应该考虑使用电火花。
e.根据制品的特点对部分顶杆进行特殊加工。
由于本人水平有限,设计时有缺陷,尚待改进。
参考文献
[1]李德群等.注塑模CAE的三维等值线生成算法[N].华中理工大学学报,1996.6(24).
[2]杨占尧.UGNX3.0注塑与冲压级进模具设计案例精解[M].化学工业出版社,2006.10.
[3]许发樾.模具实用技术设计手册[M].机械工业出版社,2005.8.
[4]赵中华,曹阳根.逆向工程在快速模具制造中的应用研究[J].现代模具,2007.1.
[5]ICAD.逆向工程技术在模具制造中的应用[J].ICADBBS,2006.05.
[6]叶久新,王群.塑料制品成型及模具设计[J].湖南大学学报,2006.04.
[7]付宏生,刘京华.注塑制品与注塑模具设计[M].化学工业出版社,2003.7(02).
[8]杨占尧.塑料注塑模结构与设计[M].清华大学出版社,2004.9.
[9]程嫣,李建华.基于ANSYS的杆形件正挤压组合凹模优化设计[J].模具工业,2006.8.
[10]耿铁.模具型腔数控加工计算机辅助刀具选择研究[N].华中科技大学学报,2004.2(05).
致谢
通过刘道标老师的指导加上自己参考大量的资料完成了此次的毕业设计。
在这次毕业设计中,我学到了许多新知识,而且对以前所学的机械知识巩固加深了。
同时也深深的感觉到以前学习中的不足之处,尤其是在模具的零件图绘制当中,发现自己的机械绘图功底还是比较薄弱,我会在以后的工作学习当中进一步的加强此项基本功。
在设计当中,刘老师不辞辛劳,毫不吝啬的指导我,给予我巨大的帮助。
在此,我对帮助教育过我的指导老师致以深深的感谢。
在审核中我也被他严谨的治学态度所感染。
我内心深深的对他表示尊敬。
在此我同时也向在毕业设计过程中帮助、指导过我的老师和同学表示谢意。
附录
名称图号图幅
装配图(手工图)CX-07-00A0
装配图CX-07-00A0
动模底座CX-07-01A1
垫块CX-07-02A3
动模板CX-07-03A1
定模板CX-07-04A1
导套CX-07-05A4
定模具底座CX-07-06A2
导柱CX-07-07A4
复位杆CX-07-08A4
浇口套CX-07-09A4
顶杆1CX-07-10A4
顶杆2CX-07-11A4
拉料杆CX-07-12A4
顶杆3CX-07-13A4
顶杆4CX-07-14A4
顶杆固定板CX-07-15A2
三维图集一本
工序卡片一本
工艺卡片一本
注塑工艺卡片一张
仿真加工截图和部分程序一本