炼钢工艺及操作要点详解精编DOC.docx
《炼钢工艺及操作要点详解精编DOC.docx》由会员分享,可在线阅读,更多相关《炼钢工艺及操作要点详解精编DOC.docx(28页珍藏版)》请在冰豆网上搜索。
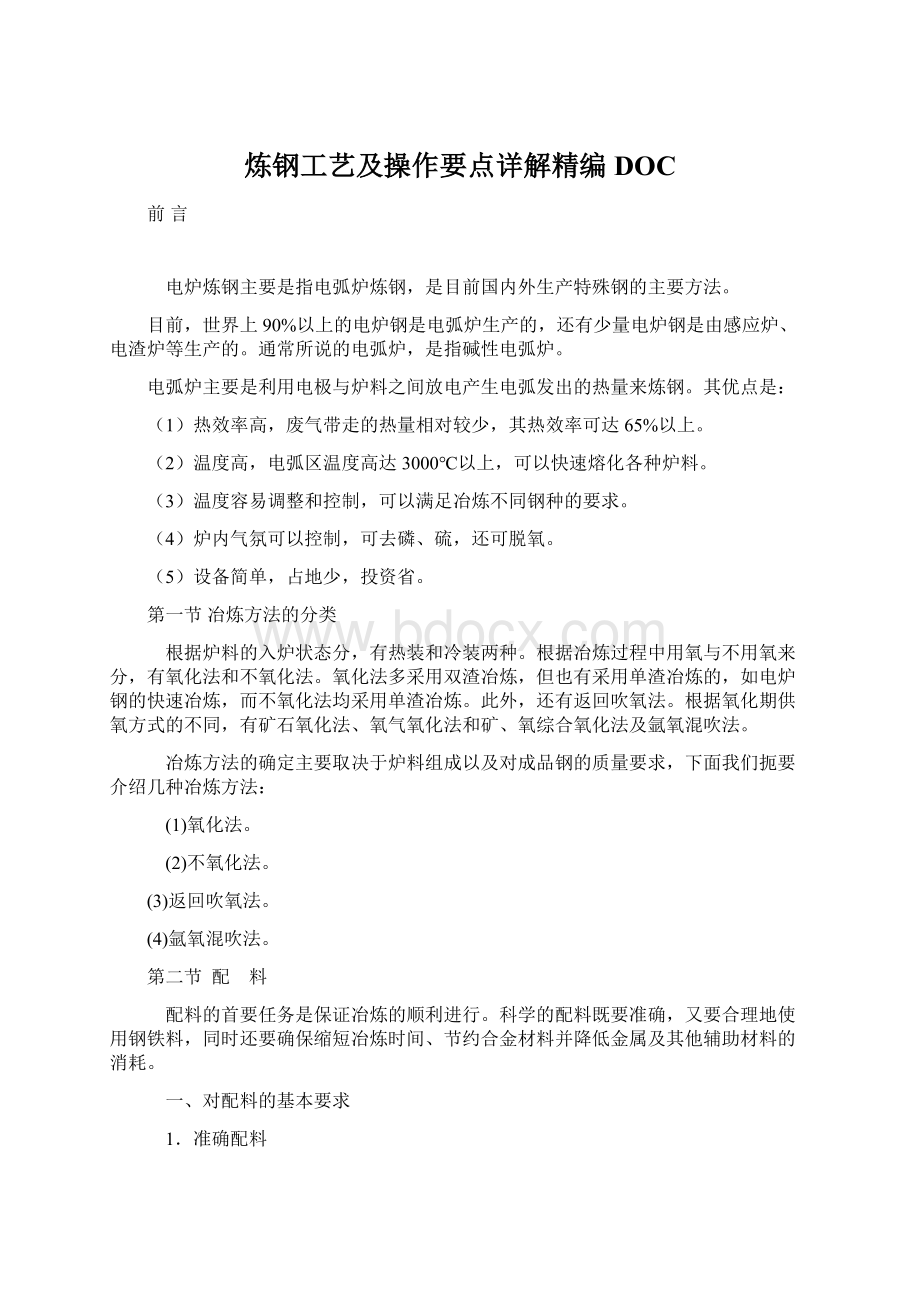
炼钢工艺及操作要点详解精编DOC
前言
电炉炼钢主要是指电弧炉炼钢,是目前国内外生产特殊钢的主要方法。
目前,世界上90%以上的电炉钢是电弧炉生产的,还有少量电炉钢是由感应炉、电渣炉等生产的。
通常所说的电弧炉,是指碱性电弧炉。
电弧炉主要是利用电极与炉料之间放电产生电弧发出的热量来炼钢。
其优点是:
(1)热效率高,废气带走的热量相对较少,其热效率可达65%以上。
(2)温度高,电弧区温度高达3000℃以上,可以快速熔化各种炉料。
(3)温度容易调整和控制,可以满足冶炼不同钢种的要求。
(4)炉内气氛可以控制,可去磷、硫,还可脱氧。
(5)设备简单,占地少,投资省。
第一节冶炼方法的分类
根据炉料的入炉状态分,有热装和冷装两种。
根据冶炼过程中用氧与不用氧来分,有氧化法和不氧化法。
氧化法多采用双渣冶炼,但也有采用单渣冶炼的,如电炉钢的快速冶炼,而不氧化法均采用单渣冶炼。
此外,还有返回吹氧法。
根据氧化期供氧方式的不同,有矿石氧化法、氧气氧化法和矿、氧综合氧化法及氩氧混吹法。
冶炼方法的确定主要取决于炉料组成以及对成品钢的质量要求,下面我们扼要介绍几种冶炼方法:
(1)氧化法。
(2)不氧化法。
(3)返回吹氧法。
(4)氩氧混吹法。
第二节 配 料
配料的首要任务是保证冶炼的顺利进行。
科学的配料既要准确,又要合理地使用钢铁料,同时还要确保缩短冶炼时间、节约合金材料并降低金属及其他辅助材料的消耗。
一、对配料的基本要求
1.准确配料
一般是根据冶炼的钢种、设备条件、现有的原材料和不同的冶炼方法进行配料。
以氧化法冶炼为例,如配碳量过高,会增加矿石用量或延长用氧时间;配碳量过低,熔清后势必进行增碳;配入不氧化元素的含量如果高于冶炼钢种的规格,需加入其他金属料撤掉多余的含量或进行改钢处理,既延长了冶炼时间,降低了炉衬的使用寿命,增加了各种原材料的消耗,又影响钢的质量,如果配得过高而又无其他钢种可更改时,只有终止冶炼。
2.钢铁料的使用原则
钢铁料的使用原则主要应考虑冶炼方法、装料方法、钢种的化学成分以及产品对质量的要求等。
根据冶炼方法的不同特点使用钢铁料,钢铁料的化学成分必须符合冶炼钢种的需要。
氧化法有较好的脱磷、去气、除夹杂的能力,应多使用普通的粗料;返吹法和不氧化法因脱磷、去气、除夹杂能力不强,但能回收贵重的合金元素,所以应尽量使用优质的返回精料。
一般炉料中应配入大块料30%~40%、中块料40%~50%、小块料或轻薄铁15%~25%。
当然,料源不好或采用炉外精炼时,轻薄杂铁也可多配。
表l2-1常见钢种的密度系数
二、配料计算公式
1.炉料成分的配定原则
配料过程中,炉料化学成分的配定主要考虑钢种规格成分、冶炼方法、元素特性及工艺的具体要求等。
具体为:
(1)碳的配定。
炉料中碳的配定主要考虑钢种规格成分、熔化期碳的烧损及氧化期的脱碳量,还应考虑还原期补加合金和造渣制度对钢液的增碳。
熔化期碳元素的烧损与助熔方式有关,可根据实际生产的具体条件,总结固有规律,一般波动在0.60%左右。
氧化期的脱碳量应根据工艺的具体要求而定,对于新炉时的第一炉,脱碳量应大于0.40%。
不氧化法碳的配定应保证全熔碳位于钢种规格要求的下限附近。
(2)硅的配定。
在一般情况下,氧化法冶炼钢铁料的硅主要是由生铁和废钢带入,全熔后的硅不应大于0.30%,以免延缓熔池的沸腾时间。
返吹法冶炼为了提高合金元素的收得率,根据工艺要求可配入硅废钢或硅铁,但也不宜超过1.0%以上,对于特殊情况也可不配。
(3)锰的配定。
用氧化法冶炼的钢种,如锰的规格含量较高,配料时一般不予以考虑;如锰的规格含量较低,配料时应严格控制,尽量避免炼钢工进行脱锰操作。
对于一些用途重要的钢种,为了使钢中的非金属夹杂物能够充分上浮,熔清后钢液中的锰含量不应低于0.20%,但也不宜过高,以免影响熔池的沸腾及脱磷。
由于不氧化法或返吹法冶炼脱锰操作困难,因此配锰量不得超过钢种规格的中限。
高速钢中锰影响钢的晶粒度,配入量应越低越好。
(4)铬的配定。
用氧化法冶炼的钢种,钢中的铬含量应尽可能的低。
冶炼高铬钢时,配铬量不氧化法按出钢量的中下限控制,返吹法则低于下限。
(5)镍、钼元素的配定。
钢中镍、钼含量较高时,镍、钼含量按钢种规格的中下限配入,并同炉料一起装炉。
冶炼无镍钢时,钢铁料中的镍含量应低于该钢种规定的残余成分。
高速钢中的镍对硬度有害无利,因此要求残余含量越低越好。
(6)钨的配定。
钨是弱还原剂,在钢的冶炼过程中,因用氧方式的不同而有不同的损失。
矿石法冶炼,任何钢种均不人为配钨,且要求残余钨越低越好。
不氧化法和返吹法冶炼时,应按钢种规格含量的中下限配入,并同炉料一起装炉。
许多钨钢中的钼在成分上可代替部分钨,配料过程中应严加注意。
(7)刷锅钢种炉料成分的配定原则。
在电炉炼钢车间,在冶炼含Cr、Ni、M0、W或Mn等高合金钢结束后,接着需冶炼l~2炉含同种元素含量相应较低的合金钢,对上一炉使用的炉衬和钢包进行清洗,这样的钢种被称为刷锅钢种。
刷锅钢种如采用返吹法冶炼,被刷元素的含量应低于该钢种规格下限的0.20%~0.50%;如用氧化法冶炼,被刷元素的含量还要低一些。
另外,出钢温度越高的钢种,被刷元素的含量应配得越低。
(8)磷、硫的配定。
除磷、硫钢外,一般钢中的磷、硫含量均是配得越低越好,但顾及钢铁料的实际情况,在配料过程中,磷、硫含量的配定小于工艺或规程要求所允许的值即可。
(9)铝、钛的配定。
在电炉钢冶炼中,除镍基合金外,铝、钛元素的烧损均较大,因此无论采用何种方法冶炼,一般都不人为配入。
(10)铜的配定。
在钢的冶炼过程中,铜无法去除,且钢中的铜在氧化气氛中加热时存在着选择性的氧化,影响钢的热加工质量,因此一般钢中的铜含量应配得越低越好,而铜钢中的铜多随用随加。
2.配料计算公式
出钢量
出钢量=产量+汤道量+中注管钢量+注余量
产量=标准钢锭(钢坯)单重×支数×相对密度系数
汤道量=标准汤道单重×根数×相对密度系数
中注管钢量=标准中注管单重×根数×相对密度系数
注余量是浇注帽口充填后的剩余钢水量,一般为出钢量的0.5%~l.5%。
对于容量小、浇注盘数多、生产小锭时,取上限值;反之取下限值。
配料过程中,不可不考虑钢的相对密度系数。
装入量
炉料综合收得率是根据炉料中杂质和元素烧损的总量而确定的,烧损越大,配比越高,综合收得率越低。
炉料综合收得率=∑各种钢铁料配料比×各种钢铁料收得率+∑各种铁合金加入比例×各种铁合金收得率
钢铁料的收得率一般分为三级。
一级钢铁料的收得率按98%考虑,主要包括返回废钢、软钢、平钢、洗炉钢、锻头、生铁以及中间合余料等,这级钢铁料表面无锈或少锈。
二级钢铁料的收得率按94%考虑,主要包括低质钢、铁路建筑废器材、弹簧钢、车轮等。
三级钢铁料的收得率波动较大,一般按85%~90%考虑,主要包括轻薄杂铁、链板、渣钢铁等,这级钢铁料表面锈蚀严重,灰尘杂质较多。
对于新炉衬(第一炉),因镁质耐火材料吸附铁的能力较强,钢铁料的收得率更低,一般还需多配装入量的l%左右。
配料量
配料量=装入量—铁合金总补加量—矿石进铁量
矿石进铁量=矿石加入量×矿石含铁量×铁的收得率
矿石的加入量一般按出钢量的4%算,如果铁合金的总补加量较大,需在出钢量中扣除铁合金的总补加量,然后再计算矿石进铁量。
矿石中的铁含量约为50%~60%,铁的收得率按80%考虑,非氧化法冶炼因不用矿石,故无此项。
各种材料配料量
各种材料配料量=配料量×各种材料配料比
三、配料计算举例
例1 用矿石氧化法冶炼38CrMoAl钢,浇注一盘3.2t钢锭6支,每根汤道重20kg,中注管钢重l20kg,注余重l50kg,其他已知条件如下:
炉中残余锰量为0.10%,残余铬量为0.15%,残余钼量为0.01%。
控制规格成分:
C0.38%、Mn0.45%、Crl.55%、M00.20%、Al0.90%。
铬铁含铬量为65%,收得率为96%;锰铁含锰量为60%,收得率为98%;钼铁含钼量为70%,收得率为98%;铝锭含铝量为98%,收得率为75%。
C生为4.00%,C返为0.30%,C杂为0.10%,炉料综合收得率为96%,38CrMoAl的相对密度系数为0.9872,矿石的铁含量为60%。
当配碳量为0.80%时,求配料量和配料组成?
解:
(1)出钢量=(3200×6+20×6+120+150)×0.9872
=19339.25(kg)
(2)
(kg)
(3)配料量:
(kg)
(kg)
(kg)
(kg)
铁合金总补加量=115.11+433.89+53.56+236.81
=839.37(kg)
矿石进铁量=(19339.25-839.37)×4%×60%×80%
=355.20(kg).
配料量=20145.O5=839.37—355.20
=18950.48(kg)
(4)配料组成:
令杂铁配比为20%,则:
杂铁配入量=l8950.48×20%=3790.10(kg)
=2765.5(kg)
返回废钢配入量=l8950.48-3790.10-2765.75
=12394.63(kg)
第三节 装料方法及操作
装料操作是电炉冶炼过程中重要的一环,它对炉料的熔化、合金元素的烧损以及炉衬的使用寿命等都有很大的影响。
一、装料方法
电炉炼钢最常见的是冷装料,而冷装按钢铁料的入炉方式不同可分为人工装料和机械装料;机械装料因采用设备不同又分为料槽、料斗、料筐装料等多种。
目前,广泛采用的还是料筐顶装料。
二、对装料的要求
为了缩短时间,保证合金元素的收得率,降低电耗和提高炉衬的使用寿命,装料时要求做到:
准确无误、快速入炉、装得致密、布料合理。
操作时应注意以下几点:
(1)防止错装。
(2)快速装料。
(3)合理布料。
首先,各种炉料的搭配要合理。
一般料块重量小于lOkg的为小料,l0~25kg的为中料,大于50kg而小于炉料总重五十分之一的为大料。
根据生产经验,合理的配比是小料占l5%~20%,中料占40%~50%,大料占40%。
各种炉料在炉内亦即筐内的合理位置是:
底部装一些小料,用量为小料总量的一半,以缓冲装料时对炉底的冲击,同时有利于尽早在炉底形成熔池;然后在料筐的下部中心装全部大料,此处温度高,有利于大料的熔化,同时还可防止电极在炉底尚未积存足够深的钢液前降至炉底而烧坏炉衬;在大料之间填充小料,以保证炉料密实;中型炉料装在大料的上面及四周;最上面放上剩余的小料,以便送电后电极能很快“穿井”,埋弧于炉料之中,减轻电弧对炉盖的热辐射。
如果炉料中配有生铁,应装在大料的上面或电极下面,以便利用它的渗碳作用降低大料的熔点,加速其熔化。
若炉料中配有合金,熔点高的钨铁、钼铁等应装在电弧周围的高温区,但不能在电弧的正下方;高温下易挥发的铁合金如锰铁、镍板等应装在高温区以外,即靠近炉坡处,以减少其挥发损失;容易增碳的铬铁合金也不要直接放在电极下面。
(4)保护炉衬。
装料时,还应尽量减轻炉料对炉衬的损害。
为此,装料前,在炉底上先铺一层为炉料重量l.5%~2.0%的石灰,以缓解炉料的冲击;同时,炉底铺石灰还可以提前造渣,有利于早期去磷、加速升温和钢液的吸气等。
卸料时,料筐的底部与炉底的距离在满足操作的条件下尽量小些,一般为200~300mm左右。
第四节 炉料入炉与送电
一、炉料入炉
料筐顶装料要有专人指挥,抽炉或旋转炉盖时,炉盖要完全抬起,电极要升到顶点且下端脱离炉膛、以防剐坏炉盖或电极,同时又要求电极下端不许超出炉盖的水冷圈或绝缘圈,避免摇晃摆动时将电极折断而滚落到它处砸坏设备或砸伤人。
采用留钢留渣操作时,装料时应多垫些杂铁,并允许料筐抬得略高些。
二、送电
炉料入炉后并在送电前,电炉炼钢工和设备维护人员应对炉盖、电极、水冷系统、机械传动系统、电气设备等进行检查,如发现故障要及时处理,以免在冶炼过程中造成停工;还应检查炉料与炉门或水冷系统是否接触,如有接触要立即排除,以免送电后被击穿。
第五节熔化期及其操作
熔化期的主要任务是在保证炉体寿命的前提下,以最少的电耗将固体炉料迅速熔化为均匀的液体。
传统的电炉炼钢熔化期约占全炉冶炼时间的一半,电能消耗占总电耗的50%~60%。
一、 炉料的熔化过程
送电开始后,就是熔化期的开始,炉料的熔化过程大体上分为如图12—1所示的四个阶段。
图12─1 炉料熔化过程示意图
a-起弧阶段;b-穿井阶段;c-电极回升阶段;d-低温区炉料熔化阶段
第一阶段:
起弧阶段。
第二阶段:
穿井阶段。
第三阶段:
电极回升阶段。
第四阶段:
熔化低温区炉料阶段。
二、影响炉料熔化的主要因素
电炉炼钢的能源主要是把电能转换成热能,目前发展趋势之一是加大电炉输入功率,从而有利于炉料的熔化,因此一些高功率、超高功率电炉相继投入生产;其次是利用外界辅助热源,如炉料预热、氧气及氧—燃烧嘴等助熔。
据资料介绍,废钢铁料入炉前的预热温度为500℃时,可节省电能l/4,而温度为600~700℃时,可节省电能l/3,如果温度达到900℃,只需冷装料时的l/2左右的电能。
这就意味着,变压器输入功率不变,熔化期将按相应的比例缩短。
此外,热的炉料入炉还可增加电弧的稳定性和提前吹氧助熔,也促使熔化期的缩短。
三、熔化期的物化反应
炉料熔化的同时,熔池中也发生各种各样的物化反应,主要有元素的挥发和氧化、钢液的吸气、热量的传递与散失以及夹杂物的上浮等。
1.元素的挥发
炉料熔化的同时,伴随着元素的部分挥发。
挥发有直接挥发和间接挥发两种形式。
直接挥发是因温度超过元素的沸点而产生的。
电弧的温度高达4000~6000℃,而最难熔元素W的沸点也仅为5900℃,至于低沸点的Zn、Pb等就更容易挥发了。
间接挥发是通过元素的氧化物进行的,即先形成氧化物,然后氧化物在高温下挥发逸出。
2.元素的氧化
炉料熔化时,除产生元素的挥发外,还存在着元素的氧化。
这是因炉中存在着氧的来源:
一是炉料的表面铁锈;二是炉气;三是为了脱磷而加入的矿石或为了助熔而引入的氧等。
在一般情况下,Al、Ti、Si元素在氧化法中几乎全部氧化掉,P只能大部分氧化,但这些元素在返吹法中,因不使用矿石助熔,氧化损失略少些,而在不氧化法中为最少。
3.钢液的吸气
在一般情况下,气体在钢液中的溶解度随温度的升高而增加,被高温电弧分解出的氢和氮会因温度的升高直接或通过渣层溶解于钢液中。
4.热量的传递与散失
热量的传递与散失属于物理过程。
熔化期熔池中主要进行着热传导。
5.熔化期非金属夹杂物的上浮
熔池出现后,钢液中就存在着内在夹杂和外在夹杂,随着熔池的扩大,这些夹杂物也就有不同程度的上浮,它们是熔化渣的来源之一。
实践证明,合理的吹氧助熔和尽早造好熔化渣能促使夹杂充分上浮。
四、熔化期脱磷操作
熔化期的正确操作,可以把钢中的磷去除50%~70%,剩余的残存磷在氧化期借助于渣钢间的界面反应、自动流渣、补造新渣或采用喷粉脱磷等办法继续去除。
因此,一个成熟电炉炼钢工,应在熔化期紧紧地抓住脱磷操作。
熔化期提前造好熔化渣,并使之具有适当的碱度和较好的流动性,能为前期脱磷创造有利的条件。
另外,在条件允许的情况下,除加入助熔矿石外,还可在大半熔时分批加入料重l%的氧化铁皮或矿石粉,或在垫炉底灰的同时装入少量的铁矿石等,从中提高熔化渣的氧化能力;在炉料大半熔或全熔后扒除部分熔化渣,对于高磷炉料或磷规格要求较严的钢种,也可全部扒除,然后重造新渣,更是强化脱磷的行之有效的好办法,此时去磷效率可达50%~70%,而钢液中的剩余磷移到氧化初期去继续处理。
五、熔化期操作
在炉料熔化过程中,还应适时地进行吹氧、推铁或加矿助熔及早期造渣与脱磷等操作。
熔化末期如果发现全熔碳不能满足工艺要求,一般应先进行增碳操作。
熔化渣的渣量一般为料重的2%~3%,电炉功率越高越取上限值。
炉料全熔并经搅拌后,取全分析样,然后扒除部分熔化渣,补造新渣。
如果认为脱磷困难或发现熔渣中含有大量的Mg0,也可进行全扒渣,重新造渣。
当熔池温度升到符合工艺要求时,方可转入下一阶段的冶炼。
第六节 氧化期及其操作
目前,氧化期主要是以控制冶炼温度为主,并以供氧和脱碳为手段,促进熔池激烈沸腾,迅速完成所指定的各项任务。
在这同时,也为还原精炼创造有利的条件。
不配备炉外精炼的电炉氧化期的主要任务如下:
(1)继续并最终完成钢液的脱磷任务,使钢中磷降到规程规定的允许含量范围内;
(2)去除钢液中的气体;
(3)去除钢液中的非金属夹杂物;
(4)加热并均匀钢液温度,使之满足工艺要求,一般是达到或高于出钢温度,为钢液的精炼创造条件。
一、氧化方法
1.矿石氧化法
矿石氧化法属于间接方式的供氧,它主要是利用铁矿石或其他金属化矿石中的氧通过扩散转移来实现钢液中的C、Si、Mn等元素及其他杂质的氧化。
该法的特点是渣中(FeO)浓度高,脱磷效果好。
2.氧气氧化法
氧气氧化法又称纯氧氧化法。
它主要是利用氧气和钢中的C、Si、Mn等元素及其他杂质的直接作用来完成钢液的氧化。
氧气氧化和矿石氧化存在着本质的不同。
氧气氧化时,由于纯氧对钢液的直接作用,各元素氧化的动力学条件好,在供氧强度较高的情况下,更有利于低碳钢或超低碳钢的冶炼。
氧气氧化属于放热反应,进而也有利于提高和均匀熔池温度而减少电能消耗。
此外,氧气氧化后,钢液纯洁,带进其他杂质少,且吹氧后,钢液中的氧含量也少,所以又有利于后步钢液的脱氧。
但由于(FeO)含量不高,因此脱磷效果差,熔渣的流动性也差。
3.矿、氧综合氧化法
在电炉钢生产过程中,矿石氧化和氧气氧化经常交替穿插或同时并用,这就是所谓的矿、氧综合氧化。
其特点是脱碳、升温速度快,既不影响钢液的脱磷,又能显著缩短冶炼时间。
但该法如不熟练,难以准确地控制终脱碳。
二、脱碳操作
1.钢液的加矿脱碳
由于矿石的熔化与分解及Fe0的扩散转移均吸热,所以脱碳反应的总过程是吸热。
钢液的加矿脱碳开始时必须要有足够高的温度,一般应大于1530℃。
为了避免熔池急剧降温,矿石应分批加入,每批的加入量约为钢液重量的1.0%~l.5%,而在前一批矿石反应开始减弱时,再加下一批矿石,间隔时间为5~7min。
熔池的均匀激烈沸腾主要通过对矿石的加入速度和保持合适的间隔时间来控制,当熔池温度较高时,矿石的加入速度也不能太快,如在炉门及电极孔冒出猛烈的火焰,则应停止加矿,以避免发生喷溅或跑钢事故。
钢液的加矿脱碳原则上是在高温、薄渣下进行。
但考虑到钢液的继续脱磷与升温,温度控制是先慢后快,渣量是先大后薄,且还要有足够的碱度及良好的流动性。
粘稠的熔渣不仅不利于脱磷,也不利于(FeO)的扩散及CO气泡的排除,特别是在钢液温度不太高的情况下,熔池容易出现“寂静”的现象,加矿后熔池不沸腾,这时应立即停止加矿,而要用萤石调整熔渣的流动性并升温。
2.钢液的吹氧脱碳
吹氧脱碳最大的特点是脱碳速度快,一般约为(0.03~0.05)%/min,而且钢液温度越高、供氧量越大、钢中的碳含量越高,脱碳速度越快。
在冶炼低碳或超低碳钢时,吹氧容易把碳很快降到很低,而且合金元素的氧化损失比矿石氧化要少,这使得利用返吹法冶炼高合金钢并回收炉料中的贵重合金元素成为可能。
在其他条件相同的情况下,吹氧脱碳和加矿脱碳相比,渣中(FeO)的含量少,且钢液中[FeO]的最终含量也少,这样可减轻钢液精炼的脱氧负担。
然而脱磷条件却恶化了,所以脱磷任务必须在熔化末期或氧化初期且当钢液的温度处于不太高的情况下就已完成。
3.钢液的矿、氧综合脱碳
这种脱碳方法能使钢液的脱碳速度成倍的高于单独加矿或吹氧的脱碳速度。
在操作过程中,矿石的加入是分批进行,且先多后少,最后全用氧气。
吹氧停止后,再进行清洁沸腾或保持锰等操作。
4.碳含量的经验判断
钢液的碳含量主要依靠化学分析、光谱分析及其他仪器来确定。
但在实际操作中,为了缩短冶炼时间,电炉炼钢工也常用经验进行准确的判断,方法介绍如下:
(1)根据用氧参数来估计钢中的碳含量。
(2)根据吹氧时炉内冒出的黄烟多少来估计钢中的碳含量。
(3)根据吹氧时炉门口喷出的火星估计钢中的碳含量。
(4)根据吹氧时电极孔冒出的火焰状况判断钢中的碳含量。
常用于返吹法冶炼高合金钢上。
一般是碳含量高则火焰长,反之则火焰短。
当棕白色的火焰收缩,且熔渣与渣线接触部分有一沸腾圈,这时的碳含量一般小于0.10%。
在返吹法冶炼铬镍不锈钢时,当棕白色的火焰收缩并带有紫红色火焰冒出且炉膛中烟气不大,可见到渣面沸腾微弱,这时的碳含量约为0.06%~0.08%;如果熔渣突然变稀,这是过吹的象征,碳含量一般小于0.03%。
碳低熔渣变稀,这种现象在冶炼超低碳钢时经常遇到。
(5)根据表面张力的大小进行粗略的判断。
(6)根据试样断口的特征判断钢中的碳含量。
(7)根据钢饼表面特征估计钢中的碳含量。
(8)根据火花的特征鉴别钢中的碳含量。
(9)根据碳花的特征判断钢中的碳含量,该法简称碳花观察法。
由于该法简便、迅速、准确,因此获得普遍的应用。
未经脱氧的钢液在样勺内冷却时,能够继续进行碳氧反应,当气泡逸出时,表面附有一薄层钢液的液衣,宛如空心钢珠,这就是火星。
又因为气泡是连续逸出的,所以迸发出来的火星往往形成火线。
如果钢中的游离碳较多,有时在火星的表面上还附有碳粒。
当气泡的压力较大而珠壁的强度不足时,迸发出来的火星破裂,进而形成所谓的碳花。
然而,CO气泡压力随钢液碳含量的降低而降低,碳花的数目和大小也依次递减,火星的迸发力量也是由强到弱。
有经验的炼钢工可根据火星(碳花)的数量、大小与破裂情况及迸发力量的强弱、火线的断续情况或发出的声音等进行判断,碳含量越低判断得越准确,误差常常只有±0.01%~0.02%,而碳含量越高,碳花越大,分叉越多,跳跃越猛烈,也越缺乏规律性,因此碳含量很高时难以准确的判断。
当碳含量超过0.80%以上时,碳花在跳跃破裂过程中还发出吱吱的响声。
碳花的具体观察方法有两种:
一种是直接观察从勺内迸发出来的火星(碳花)情况;另一种是观察火星(碳花)落地后的破裂情况。
一般碳钢的碳含量与碳花特征的关系见表12—2。
表12-2碳钢的碳含量与碳花特征的关系
碳含量/%
火星或碳花
的颜色
火星与碳花的多少等
迸发力量或破裂的情况
备注
0.O5~0.10
棕白色
全是火星构成的火线无花
迸发无力
火线稀疏时有时无
0.1~0.20
白色
火星构成的火线中略有小花
迸发无力
火线稀疏时有时无
0.3~0.40
带红
火星2/3,小花1/3
迸发稍有力
火线细而稍密
0.50~0.60
红色
火线2/3,小花1/3间带2~3朵大花
迸发有力
火线粗而密
0.70~0.80
红色
火线l/3,小花2/3大花3~5朵
迸发有力,花内分叉,呈现二次破裂
0.90~1.O0
红色
火星少,小花多,