橡胶英才网轮胎胶料配方设计.docx
《橡胶英才网轮胎胶料配方设计.docx》由会员分享,可在线阅读,更多相关《橡胶英才网轮胎胶料配方设计.docx(7页珍藏版)》请在冰豆网上搜索。
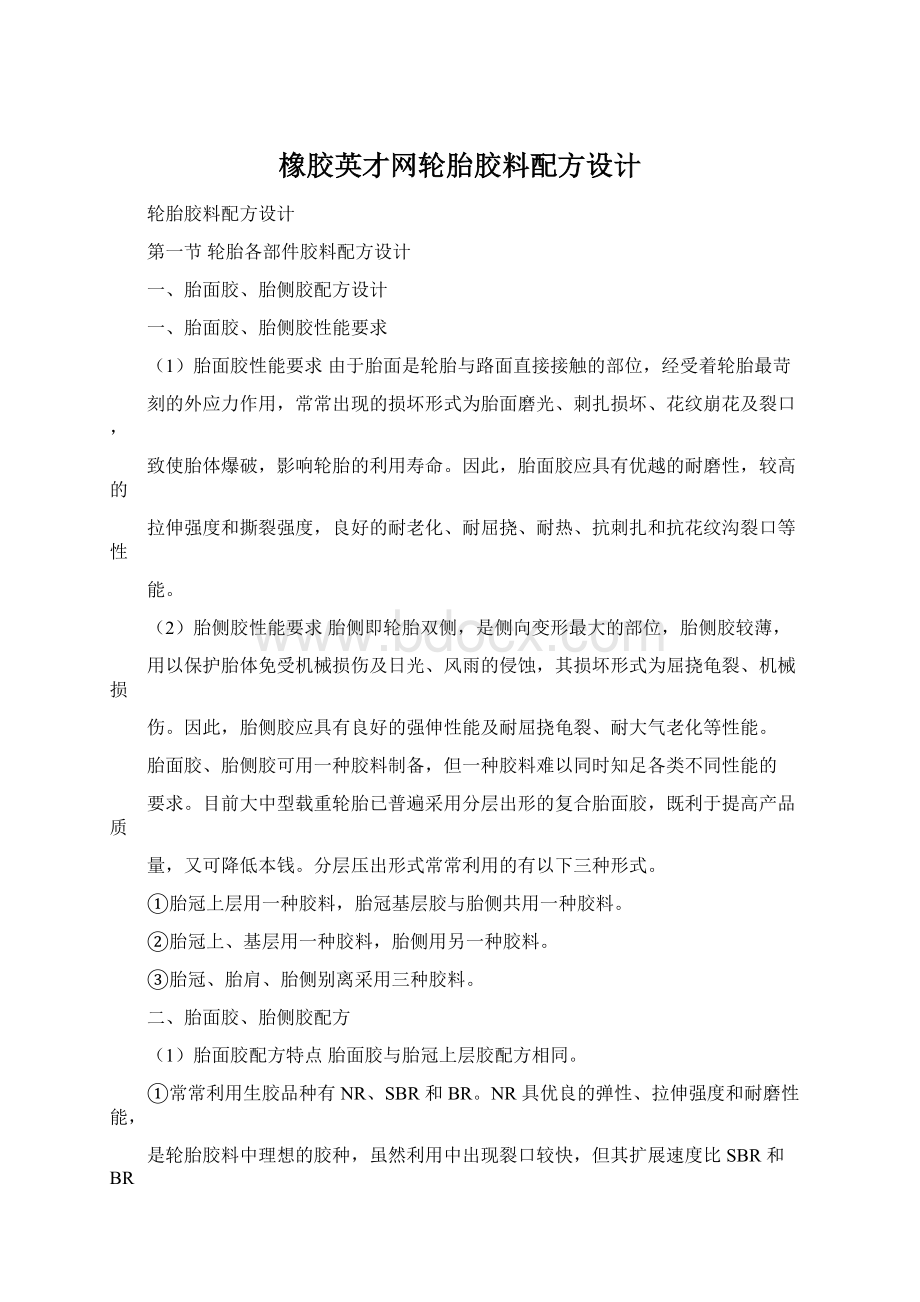
橡胶英才网轮胎胶料配方设计
轮胎胶料配方设计
第一节轮胎各部件胶料配方设计
一、胎面胶、胎侧胶配方设计
一、胎面胶、胎侧胶性能要求
(1)胎面胶性能要求由于胎面是轮胎与路面直接接触的部位,经受着轮胎最苛
刻的外应力作用,常常出现的损坏形式为胎面磨光、刺扎损坏、花纹崩花及裂口,
致使胎体爆破,影响轮胎的利用寿命。
因此,胎面胶应具有优越的耐磨性,较高的
拉伸强度和撕裂强度,良好的耐老化、耐屈挠、耐热、抗刺扎和抗花纹沟裂口等性
能。
(2)胎侧胶性能要求胎侧即轮胎双侧,是侧向变形最大的部位,胎侧胶较薄,
用以保护胎体免受机械损伤及日光、风雨的侵蚀,其损坏形式为屈挠龟裂、机械损
伤。
因此,胎侧胶应具有良好的强伸性能及耐屈挠龟裂、耐大气老化等性能。
胎面胶、胎侧胶可用一种胶料制备,但一种胶料难以同时知足各类不同性能的
要求。
目前大中型载重轮胎已普遍采用分层出形的复合胎面胶,既利于提高产品质
量,又可降低本钱。
分层压出形式常常利用的有以下三种形式。
①胎冠上层用一种胶料,胎冠基层胶与胎侧共用一种胶料。
②胎冠上、基层用一种胶料,胎侧用另一种胶料。
③胎冠、胎肩、胎侧别离采用三种胶料。
二、胎面胶、胎侧胶配方
(1)胎面胶配方特点胎面胶与胎冠上层胶配方相同。
①常常利用生胶品种有NR、SBR和BR。
NR具优良的弹性、拉伸强度和耐磨性能,
是轮胎胶料中理想的胶种,虽然利用中出现裂口较快,但其扩展速度比SBR和BR
慢。
SBR具有优良的耐磨和耐老化性能。
BR的弹性更优于NR并具有良好的耐磨性
和生热低的特点,适宜用于轮胎胎面胶较料中。
通常大型轮胎如工程机械轮胎胎面以NR单用为宜。
中小型轮胎胎面胶则以NR
为主,掺用SBR或BR,拖沓机轮胎胎面也可采用三胶并用的配方。
②主要补强剂是cb,可按照胶料性能要求和生胶类别肯定cb品种及用量。
胎
面胶采用活性cb,一般总用量为45~50质量份。
以下均用“份”代表“质量份”来
表示配合剂用量。
③硫化体系中硫磺用量按照选用胶种而定,全天然橡胶配方硫磺用量为~
份,掺用SBR或BR的配方,以采用低硫高促体系。
一般掺用30%SBR,硫磺用
99
量为~份,掺用30%BR,硫磺用量为~份,若BR用量增至70%时,
硫磺用量只用~份。
增进剂品种及用量与硫磺量应相配合,同时视生胶种
类和cb品种而定。
活性剂一般ZnO3~5份,SA2~3份
④软化剂品种和用量应视生胶及炭黑品种用量而定,同时考虑与生胶有良好的
互溶性。
天然胶胶料可用松焦油,一般为3~8份。
掺用合成橡胶的胶料,宜选用
石油系软化剂,常常利用的有环烷烃油、三线油、六线油、锭子油和机油,用量约6~
12份,顺丁橡胶掺用量增大时,用量适当增大。
⑤防老剂一般采用综合性能较好的对苯二胺类防老剂,如4010、4010NA、4020、
或与BLE、RD、AW并用,总用量为2~4份。
配用物理防老剂石蜡1~2份,可获取
优良的防老化效能并可改善胎面外观质量。
(2)胎侧胶配方特点胎侧胶与胎面胶基层配方相同。
生胶品种可采用全天然
橡胶或以天然橡胶为主,掺用30~50%的丁苯橡胶或顺丁橡胶。
Cb可以补强型炉黑
为主,掺用半补强型炉黑,用量一般约为55份。
防老剂用量可高达3份。
此刻已生产出白色或各类颜色胎侧胶的轮胎。
这种浅色胎侧胶配方宜选用无污
染型的配合剂,如补强剂用改性陶土、白炭黑和钛白粉等,防老剂选用24六、SP或
MB等品种。
相邻胶料不宜选用有迁移性、污染性的配合剂(如软化剂、防老剂等),
浅色胎侧胶配方见表所列
(3)胎面胶、胎侧胶配方举例见表所列
二、胎体胶料配方设计
一、胎体胶料性能要求
胎体胶料包括缓冲层、外帘布层及内帘布层胶料和油皮胶等
(1)缓冲层胶料性能要求缓冲层是胎面胶与帘布层之间的过渡层,在轮胎行驶
进程中,不可是经受剪切应力最大的部位,而且还要缓和和分散外部冲击应力,避
免因局部应力过大造成帘布层初期损坏,因此要求胶料具有较高定伸应力、弹性和
抗剪切性能,同时要求生热低、耐热性好。
(2)帘布层胶料性能要求帘布层因连线密度不同分为外帘布层和内帘布层,外
帘布层位于缓冲层与内帘布层之间,形成过渡层结合。
因此要求胶料与帘线具有良
好的粘合性能,使胎体成为牢固的整体,并要求胶料生热低、耐热及耐屈挠疲劳性
好。
(3)油皮胶料性能要求油皮胶位于外胎的内表面,在内帘布层的里层,起保
护内胎及避免空气和水分侵蚀帘布层的作用。
因此要求胶料有必然的强伸性能和较
好的耐老化性能,而且要求胶料硫化起点较快,可塑性不宜过大,避免在硫化进程
中向帘布层迁移影响帘布层的性能。
二、胎体胶料配方
100
(1)配方特点目前胎体大多数采用尼龙帘线,胶料配方应考虑与帘线的良好粘
合及与外胎各部件的整体配合。
①生胶品种通常可用纯天然橡胶或以天然橡胶为主,掺用部份BR或SBR。
掺用比例
一般按照轮胎品种和规格而定,合成橡胶掺用量以不超过30%为宜,通常大型轮胎
合成橡胶掺用量应少些,外层帘布胶掺用量比内层帘布胶略少。
轮胎胶料含胶率从缓冲层、外帘布层至内帘布层依次逐渐增大,彼此配合,缓
冲层胶一般不低于62%,外层帘布胶不低于63%,内帘布层胶不低于64%。
②补强剂品种及用量应按照不同部位胶料要求而定,cb用量应视帘线种类与合成橡
胶掺用比例定。
③软化剂品种及用量以不影响胶料粘合性及滞后性能为选定原则。
天然橡胶胶料可
单用松焦油和古马隆树脂,用量为3~4份,掺用合成橡胶胶料常常利用芳香烃含量较
高的石油软化剂如三线油、六线油,用量为3~5份。
④硫化增进体系可按照胎体骨架材料和生胶品种而定,一般人造丝或尼龙帘线胎
体,NR与SBR并用胶料硫磺用量为~份,NR与BR并用胶料硫磺用量为~
份。
钢丝帘线的胎体,为提高胶料与钢丝的粘合性能,硫磺用量较高,为4份
左右。
增进剂品种应选用硫化进程中诱导期较长的后效性增进剂,使胶料有良好的粘
流状态,利于胶与帘线的结合。
(2)配方实例见表4-2所列。
三、胎圈胶料配方设计
一、胎圈胶料性能要求及配方特点胎圈由多部件组成,有钢丝圈、填充胶
条、钢圈包布、胎圈包布和帘布层,要求部件之间胶料有良好的粘合性能,使胎圈
形成一个牢固整体。
①钢丝圈胶料要求与钢丝有良好的粘合性能,胶料硬度较高,不低于70(邵氏A),
胶料强伸性能要求不高,拉伸强度≥,扯断伸长率≥200%,含胶率较低,约
为30%。
因此胶料中宜选用纯天然橡胶与高硫磺量的配合,硫磺用量为7~10份,
乃至高达20份,氧化锌用量可略增加。
钢丝圈胶料为半硬质胶,采用大量的半补
强炉黑和无机添充剂,如碳酸钙、陶土等,还可以掺用少量再生胶,利于改善胶料
的工艺性能,又可降低本钱,软化剂可选用提高胶料粘着性能的松焦油、沥青和松
香等品种。
②填充胶条胶料要求有较高的硬度,不低于70(邵氏A),起填充间隙作用,使
胎圈部轮廓均匀过渡,避免应力集中而损坏。
胶料强伸性能要求不高,拉伸强度
≥,扯断伸长率≥250%,含胶率很低,为15%左右。
因此胶料中除天然橡胶
外可产用再生胶和大量填料,如炭黑、碳酸钙等,也可掺用部份合成橡胶以改善胎
101
圈脱空的毛病。
③钢圈包部胶料和胎圈包布胶料可用同一种配方,便于生产管理。
钢圈包布用以
包裹钢丝圈和填充胶条组成钢圈;胎圈包布是包在胎圈外层,用以保护胎圈的帘布
层免受轮辋磨损。
包布均为挂胶尼龙帆布,因此要求胶料具有良好的粘着性能及耐
老化性能,胶料应有必然的强伸性能,拉伸强度≥,扯断伸长率≥500%,
含胶率一般在50%左右。
生胶品种可选用低级天然橡胶,也可掺用部份丁苯橡胶,
炭黑和无机填充剂并用,软化剂选用增加粘性的品种如松焦油、沥青、松香等,便
于擦胶工艺操作,用量一般较大。
(2)配方实例斜交载重汽车轮胎胎圈各部件胶料配方见表所列。
四、水胎、胶囊、内胎、垫带胶料配方设计
(1)水胎、胶囊胶料配方设计水胎与胶囊作用相同,用以硫化外胎做内模型用,
并需充入过热水或高压蒸汽,在高温下利用,同时要经受上百次反复硫化外胎的装
卸操作,因此水胎和胶囊胶料要求应具有良好的耐热性、耐老化性、耐高温撕裂和
耐屈挠疲劳性能,而且还应有良好的耐水性能。
①水胎、胶囊胶料物理机械性能指标可由生产厂自行控制,见表所列。
②水胎、胶囊胶料配方特点是用于水胎的生胶品种常为天然橡胶,用于胶囊的生
胶品种均为丁基橡胶,国外也有采用丁基胶和三元乙丙胶并用的,因丁基橡胶饱和
度高,并具有极好的耐热性和气密性。
国内已用420活性剂(烷基苯胺多硫物)硫
化丁基水胎及胶囊,取得良好效果,其利用次数比天然胶水胎可提高倍。
丁基胶水胎及胶囊由于丁基橡胶分子链含少量的双键,其硫化体系可采用硫磺
硫化,也可采用树脂硫化。
补强填充体系,由于丁基橡胶为结晶型橡胶,自身具有较高的强度,补强剂只
有助于提高胶料的撕裂强度和定伸强度,利于改善工艺加工性能,一般补强填充剂
仍以炭黑补强效果最佳,常常利用的有高耐磨炉黑与半补强炉黑、快压出炉黑并用,用
量约为40~60份。
软化增塑体系,由于丁基橡胶为非极性橡胶,易利用与其具有较好相容性的极
性小的软化剂,如机油、石蜡和凡士林等。
也可加入420活化剂,这种多烷基苯酚
二硫化物,可以提高胶料的粘性。
防老剂在丁基橡胶配方中无显高作用,一般可没必要加入。
③水胎、胶囊胶料配方实例见表所列。
(2)内胎胶料配方设计内胎胎壁较薄,充入紧缩空气后,在高温和伸张状态下
利用,并维持稳定的气压。
因此要求胶料具有良好的气密性及低定伸应力,同时要
求弹性高、撕裂强度高、永久变形小、耐热性能好。
①内胎胶料物理机械性能指标按照不同胶种有不同要求,见表所列。
102
②内胎胶料配方特点常常利用生胶品种为纯天然橡胶或掺用30%SBR,由于丁基胶
具有极佳的气密性和耐热性能,而且形变小,已成为制造内胎最适宜的胶种,得以
普遍应用。
天然胶内胎胶料宜选用定伸应力较低的补强剂,如半补强炉黑,快压出炉黑等,
或与碳酸钙并用可减小用就变形,用量约为40份。
内胎壁薄,硫化速度宜快,但
为了提高胶料的耐老化性能及抗撕裂性能,硫磺用量已选用低值,约为份,
因此增进剂品种选用秋兰姆为第一增进剂与噻唑类增进剂并用或与次磺酰胺类促
进剂并用,如DM+TMTD,M+TMTD和DM+CZ(NOBS)等,
丁基橡胶内胎胶料的补强剂一般采用高耐磨炉黑与半补强炉黑,快压出炉黑或通
用炉黑并用,用量为50-70份。
软化剂采用极性极小的饱和烃类如凡士林,锭子油,
蓖麻油等。
硫化体系一般采用秋兰姆为第一增进剂与噻唑类增进剂并用硫磺硫化体
系,可取得较好的工艺加工性能和利用性能。
③内胎胶料配方见表所列
(3)垫带胶料配方设计垫带只起保护内胎免受轮辋磨损的作用。
因此只要求胶
料具有必然的强伸性能,较小的永久变形,还有较好的耐屈挠,耐老化性能。
①垫带胶料物理机械性能指标一般控制拉伸强度为,拉断伸长率为
500%,硬度(邵氏A)为53+3,扯断永久变形为35%。
②垫带胶料配方特点,生胶可利用低级5号烟片胶和大量合成橡胶,为降低
胶料本钱可掺用再生胶,含胶率约为30-40%.
补强剂多采用半补强炉黑与高耐磨炉黑并用,用量为40-50份,并掺用大量无
机填充剂如碳酸钙或陶土等。
软化剂用量大,约为10-16份。
垫带采用模压硫化,
硫化速度快,故可用M+DM+TT或M+DM+D,用量约为份左右。