催化裂化操作规程.docx
《催化裂化操作规程.docx》由会员分享,可在线阅读,更多相关《催化裂化操作规程.docx(150页珍藏版)》请在冰豆网上搜索。
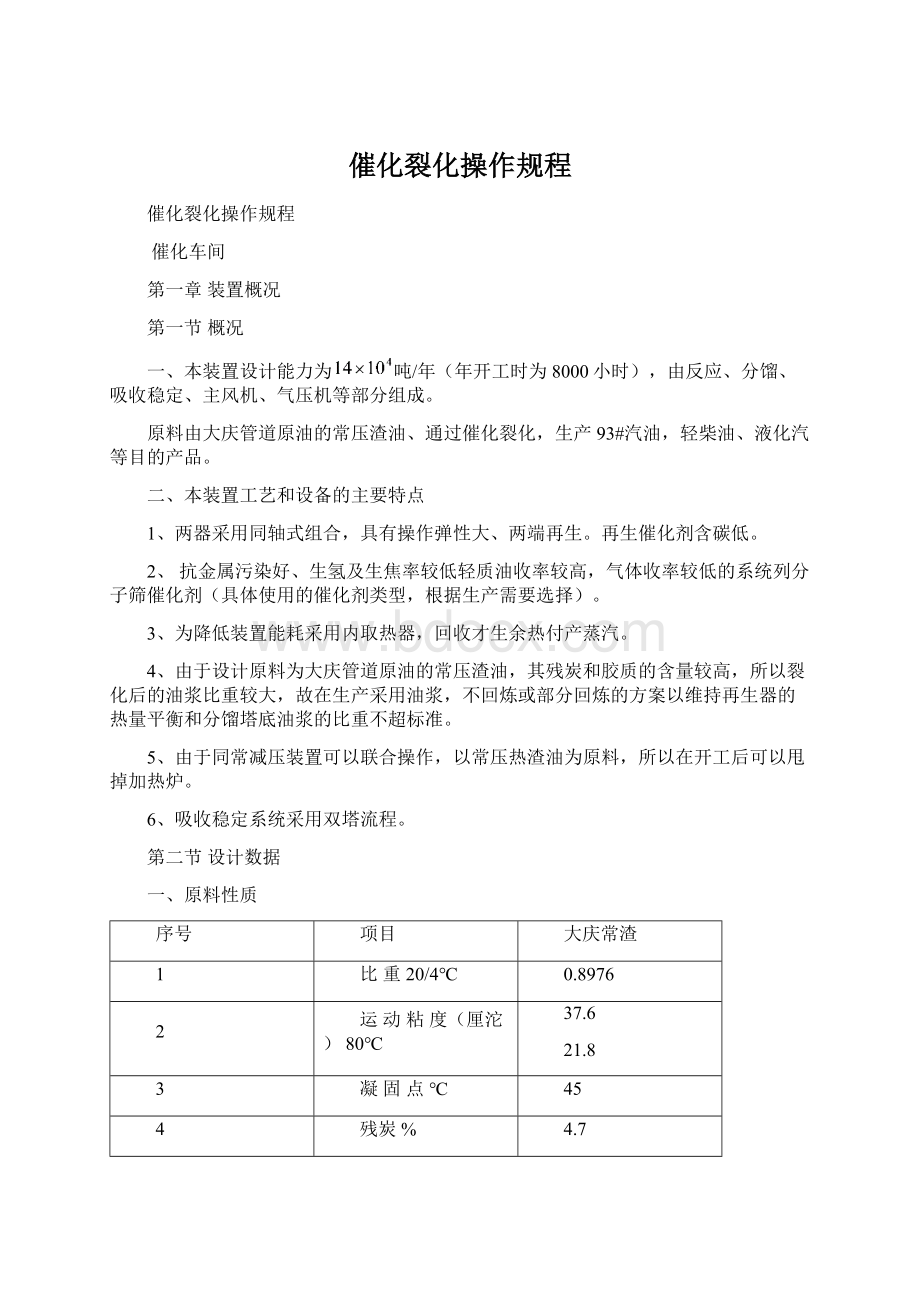
催化裂化操作规程
催化裂化操作规程
催化车间
第一章装置概况
第一节概况
一、本装置设计能力为吨/年(年开工时为8000小时),由反应、分馏、吸收稳定、主风机、气压机等部分组成。
原料由大庆管道原油的常压渣油、通过催化裂化,生产93#汽油,轻柴油、液化汽等目的产品。
二、本装置工艺和设备的主要特点
1、两器采用同轴式组合,具有操作弹性大、两端再生。
再生催化剂含碳低。
2、抗金属污染好、生氢及生焦率较低轻质油收率较高,气体收率较低的系统列分子筛催化剂(具体使用的催化剂类型,根据生产需要选择)。
3、为降低装置能耗采用内取热器,回收才生余热付产蒸汽。
4、由于设计原料为大庆管道原油的常压渣油,其残炭和胶质的含量较高,所以裂化后的油浆比重较大,故在生产采用油浆,不回炼或部分回炼的方案以维持再生器的热量平衡和分馏塔底油浆的比重不超标准。
5、由于同常减压装置可以联合操作,以常压热渣油为原料,所以在开工后可以甩掉加热炉。
6、吸收稳定系统采用双塔流程。
第二节设计数据
一、原料性质
序号
项目
大庆常渣
1
比重20/4℃
0.8976
2
运动粘度(厘沱)80℃
37.6
21.8
3
凝固点℃
45
4
残炭%
4.7
5
闪点(闭口)℃
174
6
硫分量%
0.14
7
馏程℃HK
10%
30%
349
430
492
8
重金属含量PPmFe
Cu
Ni
V
2.9
0.2
4.8
0.1
9
元素分析%C
H
N
S
86.56
12.63.
0.22
0.14
项目
数据
比重20/4℃
运动粘度(厘沱)20℃
凝固度℃
实际胶质mg/100ml
酸度毫克KOH/100ml
铜片腐蚀
10硫分%
闪点(闭口)
馏程℃
50%
90%
95%
十六烷值
0.8460
5.2
—4
合格
0.05
86
273
334
345
40
二、汽油馏分性质三、轻柴油馏分性质
项目
数据
比重20/4℃
实际胶质mg/100ml
酸度毫克KOH/100ml
铜片腐蚀
硫分%
感应度分
馏程℃
10%
50%
KK
辛烷值(马达法)
0.7380
3.4
0.28
合格
0.03
990
60
106
1
96
78
四、装置物料平衡表
出
入
方
物料名称
设计采用数据
重%
公斤/时
万吨/年
原
料
常压渣油
合计
100.00
100.00
9333
9333
7.000
7.000
产
品
液化石油气
汽油
轻柴油
焦炭
损失
合计
7.0
9.0
48.30
28.7
10.5
1.5
100.00
635
840
4508
2212
980
140
9330
0.490
0.630
3.381
1.659
0.735
0.105
7.000
五、反应再生部分工艺计算汇总
序号
参数名称
单位
提升管反应器
沉降器
汽提段
再生器
1
设备直径×高
Mm
2
温度
℃
上506
中522
下609
495
496
Ⅰ段648
Ⅱ段670
3
MPa
公斤/厘米
0.19
0.18
0.18
0.22
4
藏量
Kg
79
32
1507
Ⅰ段2348
Ⅱ段1250稀相1870
5
空速
165
6
剂油比
5:
1
7
回炼比
0.4
8
催化剂循环量
t/h
66.78
66.78
66.78
83.767
9
原料予热温度
℃
240
10
反应时间
S(min)
原料2.45
回炼油3.46
(1.41)
Ⅰ段2.24
Ⅱ段0.82
11
线速
m/s
上16.53
中7.63
下4.53
0.53
0.19
Ⅰ段0.89Ⅱ段0.54
稀相0.62
12
催化剂密度
上11.7
中26.2
下111
1.1
600
Ⅰ段148.2
Ⅱ段198.2
13
旋风器入口线速
m/s
初旋20
25
一级26.5
二级29.0
14
烧焦量
Kg/h
Ⅰ段810
Ⅱ段170
15
主风量
Ⅰ段123.95
Ⅱ26.05
16
分布管压降
Ⅰ段0.05
Ⅱ段0.05
17
烟气量
162
18
烧焦强度
Kg/t.h
Ⅰ段241.9
Ⅱ段136
六、装置能耗汇总表
设计进料量70000吨/年
装置组成:
反应再生部分,分馏部分,吸收稳定部分,碱洗部分
序号
项目
年消耗量
燃烧低热值或耗能指标
能耗
万大卡/年
单位
数量
单位
数量
1
焦炭
吨
7350
千卡/公斤
9740
2
循环水
吨
千卡/吨
1000
3
脱氧水
吨
千卡/吨
92000
4
污水
吨
千卡/吨
80000
5
电力
度
千卡/度
3000
6
净化压缩空气
千卡/标米
400
7
非净化压缩空气
千卡/标米
300
第三节装置流程简介
一、反应再生部分
原料油自罐区的原料罐来经泵(P201/1.2)加压后送到至2台原料一—轻柴油换热器(E205/1.2)进入原料一—中段换热器(E2060),再进入原料—油浆换热器(E201/1.2.3)换热后,进入加热炉(F201),或直接进入闪蒸罐(V203/1),经过加热炉后的原料沿管排进入闪蒸(V203/1),经过加热炉后的原料油沿管排进入闪蒸罐(V203/1)或直接进料,进入闪蒸罐内的原料(350℃)汽相沿顶部汽返线进入分馏塔(T201)第二层塔盘上部,液相自罐底部抽经泵(P201/2.3)加压后进入提升管反应器。
回炼油自分馏塔第一层塔盘自流入回炼油罐(V202),经回炼油泵(P206/1.2)加压后,送到提升管反应器下部与分馏塔底油浆经泵(P207/1.2)加压后送至提升管下部的回炼油浆混合一并进入提升管反应器(R101)。
在提升管反应器(R101)内,原料与来自再生器(R103)二段的高温催化剂接触后迅速反应,反应油气与催化剂一并向上流动,从提升管顶部经初级旋风分离器,一级旋风分离器,将油气携带的催化剂除去,反应油气沿Dg350管线进入分馏塔(T201)。
经过旋风分离器分离下来的催化剂在反应沉降器(R102)内靠重力流入汽提段,在汽提蒸汽的作用下,脱除所携带的油气,催化剂沿待生立管,经待生塞阀进入再生器(R301)一段密相床进行烧焦再生,用再生底部送入的主风烧掉吸附在催化剂上焦炭及氢和碳,同时放出大量热量,完成催化剂的再生过程,再生剂自密相床底部经过再生塞阀送回提升管下部,完成催化剂循环过程。
催化剂再生过程所需主风是由主风机(M401/1.2)将空气压缩后,分别经过一、二段主风分布管进入再生器密相床,烧焦过程产生的高温烟气经过再生器内,一、二级旋风分离器,出点携带的催化剂后离开再生器(R103)经双动滑阀和孔板降压器排入大气中。
为了控制再生器能在最佳的热平衡条件下烧焦,再生器(R301)内设置了四组垂直分布的取热盘管。
脱氧水自动力进入水汽分离器(V105),由(V105)下部抽出经泵(P101/1.2)加压后进入给水分器(V107),再生器(R103)内三组垂直取热盘管,然后进入V105中部进行平衡汽化,蒸汽沿V105顶部进入再生器(R103)内一组垂直取热盘管后,并入蒸汽管网。
二、分馏系统
反应油气从沉降器(R102)顶部进入分馏塔(T201)底部,与循环油浆经过八层人字挡板逆流接触,一方面洗涤反应油气携带的催化剂,一方面脱除过剩热量,使反应油气呈“饱和状态”进入第一层塔盘。
分馏塔顶油气经油气—空气冷却器(E203/1.2)、塔顶油气冷凝器(E207/1.2.3),到分馏塔顶油气分离器(V201)进行平衡汽化,气相—富气从油气分离器顶部去气压机(M501/1.2.3.4)加压后送至吸收稳定系统,平衡汽化冷凝下来的脱酸性水集中到V201脱水包中排去。
轻柴油从T201第15、17层塔盘自流入轻柴气提塔(T202)经汽提蒸汽汽提后,轻组份随蒸汽由挥发线返回分馏塔的第18层下部,汽提后的轻柴油自塔底经泵(P204/1.2)抽出后,进入轻柴油—原料换热器(E205/1.2)后,在进入轻柴油空冷器(E209/1.2.3)然后一部分去碱洗并作为产品出装置,另一部分去再吸收塔(T304)作吸收油。
分馏塔(T201)多余热量由顶循环回流,中段循环回流和油浆循环回流取走。
顶循环回流,为了控制分馏塔顶温度塔顶设有循环回流,由第25层塔盘用顶循环回流泵(P203/1.2)抽出后,经循环水换热器(E201、E205/3),进入顶循环空冷器(E208/1.2.)后返回分馏塔第29层。
中段循环回流,为了控制轻柴油凝固点,分馏塔(T201)设有中段循环回流,中段循环油自第10、12层塔盘抽出,经泵(P205/1.2)加压后,送到吸收稳定系统,经过稳定塔底部再沸器(E302),给稳定塔(T303)提供热源后进入解吸塔再沸器(E301)向解吸塔(T302)提供热源,在进入中段—原料油换热器(E206)后进入中段—循环水换热器(E201)后,返回分馏塔(T201)第14、16层上。
油浆循环回流:
油浆自塔底部经泵(P207/1.2)抽出后,一部分反应进料,另一部分经过油浆—原料油换热器(E202/1.2.3)后,返回塔底作为循环回流。
三、吸收稳定系统
气压机(M501/1.2.3)压缩后的富气,进入压缩富气—循环水换热器(E305)冷却后,再与来自解吸塔(T302)顶部的解吸气和吸收塔底的富吸收油合并进入压缩富气冷却器(E307/1.2),冷却后进入气压机出口油气分离器(V301)平衡汽化,气相压缩富气进入吸收塔底(T301)与上部的吸收剂—粗汽油、稳定汽油逆流接触,经吸收后的贫气自顶部进入再吸收塔(T304)底部,轻汽油组分解析下来,再吸塔底液压回粗汽油罐(容201)。
干气自再吸收塔(T304)顶部出来去常压作燃料,剩余的低压瓦斯放火炬。
为了取走吸收塔内放出的吸收热,吸收塔设有中段循环回流中段循环在吸收塔(T301)第13层抽出经泵(P303)加压后进入中段—循环水冷却器(E308/1),冷却后返回吸收塔第12层塔盘。
解吸塔(T302)。
凝缩油从气压机出口油气分离器(V301)底部抽出经泵(P301/1.2)加压后,打入解吸塔(T302)第25层,由解吸塔底在为期(E301)提供热源,在塔内脱除凝缩油中轻于的组分,脱乙烷汽油自塔底由稳定他(T303)进料泵(P302/1.2)抽出加压后,经过稳汽—脱乙烷换热器(E302)换热后进入稳定塔(T303)作为进料。
稳定塔(T302)由塔底重沸器(E303)提供热量,在塔内将解吸塔送来的脱乙烷汽油中的组分分离出来,并从塔顶蒸出,经稳定塔(T303)顶空冷器(E309/1.2)和塔顶冷却器(E310)后,进入稳定塔顶回流罐(V302)平衡汽化,液相—液化石油气自底部经泵(