学年第二学期机械制造技术基础作业.docx
《学年第二学期机械制造技术基础作业.docx》由会员分享,可在线阅读,更多相关《学年第二学期机械制造技术基础作业.docx(22页珍藏版)》请在冰豆网上搜索。
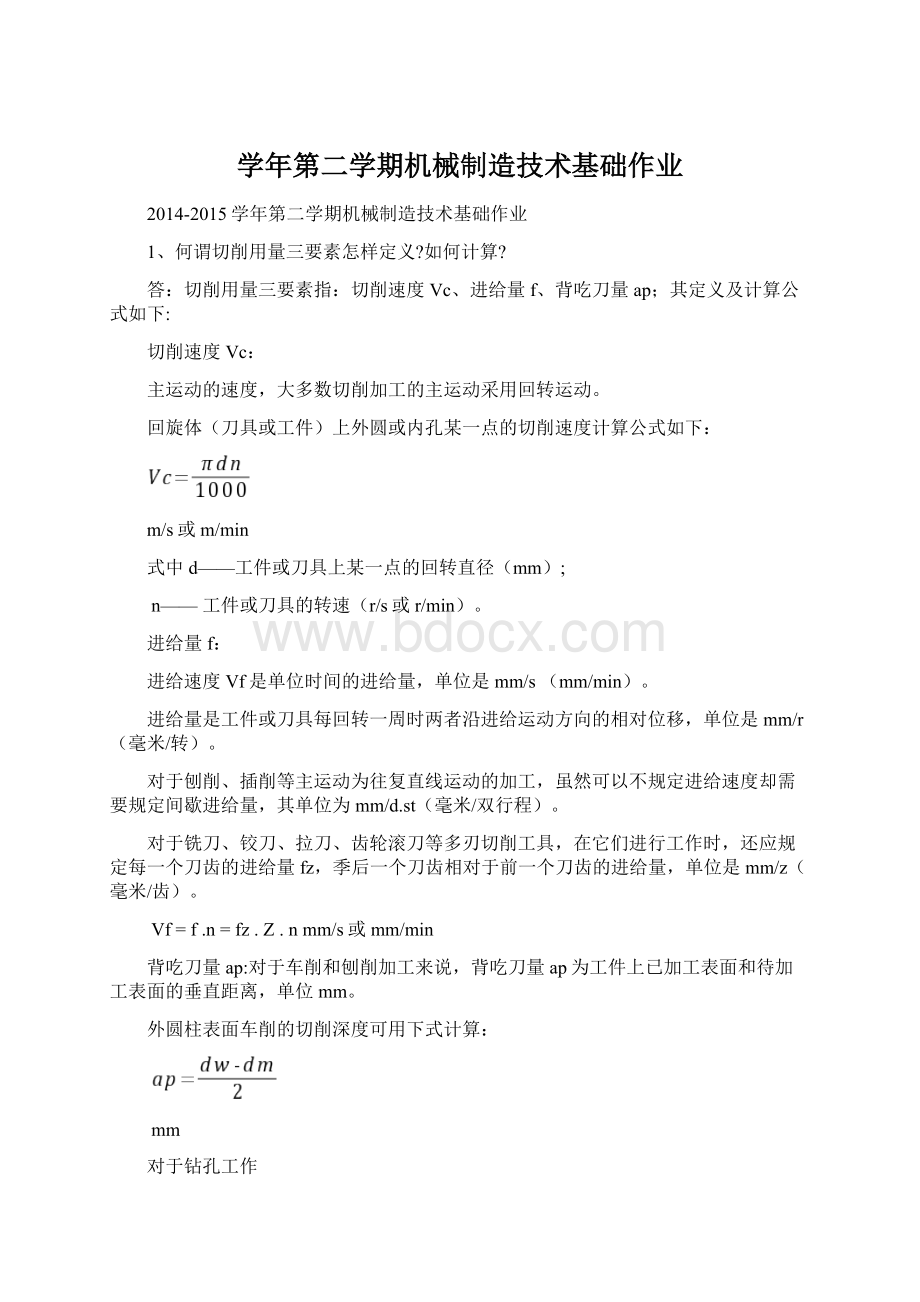
学年第二学期机械制造技术基础作业
2014-2015学年第二学期机械制造技术基础作业
1、何谓切削用量三要素怎样定义?
如何计算?
答:
切削用量三要素指:
切削速度Vc、进给量f、背吃刀量ap;其定义及计算公式如下:
切削速度Vc:
主运动的速度,大多数切削加工的主运动采用回转运动。
回旋体(刀具或工件)上外圆或内孔某一点的切削速度计算公式如下:
m/s或m/min
式中d——工件或刀具上某一点的回转直径(mm);
n——工件或刀具的转速(r/s或r/min)。
进给量f:
进给速度Vf是单位时间的进给量,单位是mm/s(mm/min)。
进给量是工件或刀具每回转一周时两者沿进给运动方向的相对位移,单位是mm/r(毫米/转)。
对于刨削、插削等主运动为往复直线运动的加工,虽然可以不规定进给速度却需要规定间歇进给量,其单位为mm/d.st(毫米/双行程)。
对于铣刀、铰刀、拉刀、齿轮滚刀等多刃切削工具,在它们进行工作时,还应规定每一个刀齿的进给量fz,季后一个刀齿相对于前一个刀齿的进给量,单位是mm/z(毫米/齿)。
Vf=f.n=fz.Z.nmm/s或mm/min
背吃刀量ap:
对于车削和刨削加工来说,背吃刀量ap为工件上已加工表面和待加工表面的垂直距离,单位mm。
外圆柱表面车削的切削深度可用下式计算:
mm
对于钻孔工作
mm
其中,
——为已加工表面直径mm;
——为待加工表面直径mm。
2、刀具标注角度参考系有哪几种?
它们是由哪些参考平面构成?
试给这些参考平面下定义。
答:
刀具标注角度参考系有两类:
一类为刀具角度静止参考系,它是刀具设计时标注、刃磨和测量的基准,用此定义的刀具角度称为刀具标注角度;一类为刀具角度工作参考系,它是确定刀具切削工作时角度的基准,用此定义的刀具角度称为刀具的工作角度。
用于构成刀具角度的参考平面主要有:
基面、切削平面、正交平面、法平面、假定工作平面和背平面。
各参考平面定义如下:
基面Pr:
过切削刃选定点,垂直于主运动方向的平面。
通常,它平行(或垂直)于刀具上的安装面(或轴线)的平面。
例如:
普通车刀的基面Pr,可理解为平行于刀具的底面;
切削平面Ps:
过切削刃选定点,与切削刃相切,并垂直于基面Pr的平面。
它也是切削刃与切削速度方向构成的平面;
正交平面Po:
过切削刃选定点,同时垂直于基面Pr与切削平面Ps的平面;
法平面Pn:
过切削刃选定点,并垂直于切削刃的平面;
假定工作平面Pf:
过切削刃选定点,平行于假定进给运动方向,并垂直于基面Pr的平面;
背平面Pp:
过切削刃选定点,同时垂直于假定工作平面Pf与基面Pr的平面。
3、刀具切削部分材料应具备哪些性能?
为什么?
答:
刀具材料应满足一下基本性能要求:
较高的硬度和耐磨性;足够的强度和韧性;较高的耐热性和化学稳定性;良好的工艺性;良好的经济性。
主要原因有:
刀具切削部分在强烈摩擦、高压、高温下工作,应具备如下的基本要求。
高硬度和高耐磨性:
刀具材料的硬度必须高于被加工材料的硬度才能切下金属,这是刀具材料必备的基本要求,现有刀具材料硬度都在60HRC以上。
刀具材料越硬,其耐磨性越好,但由于切削条件较复杂,材料的耐磨性还决定于它的化学成分和金相组织的稳定性。
足够的强度与冲击韧性:
强度是指抵抗切削力的作用而不致于刀刃崩碎与刀杆折断所应具备的性能。
一般用抗弯强度来表示。
冲击韧性是指刀具材料在间断切削或有冲击的工作条件下保证不崩刃的能力,一般地,硬度越高,冲击韧性越低,材料越脆。
硬度和韧性是一对矛盾,也是刀具材料所应克服的一个关键。
高耐热性 :
耐热性又称红硬性,是衡量刀具材料性能的主要指标。
它综合反映了刀具材料在高温下保持硬度、耐磨性、强度、抗氧化、抗粘结和抗扩散的能力。
良好的工艺性和经济性:
为了便于制造,刀具材料应有良好的工艺性,如锻造、热处理及磨削加工性能。
当然在制造和选用时应综合考虑经济性。
当前超硬材料及涂层刀具材料费用
4、刀具材料与被加工材料应如何匹配?
怎样根据工件材料的性质和切削条件正确选择刀具材料?
答:
切削刀具与加工对象的匹配主要指二者的力学、物理和化学性能相互匹配,以获得最长的刀具寿命和最大的切削加工生产率。
切削刀具与加工对象的物理性能匹配主要是指刀具与工件材料的熔点、弹性模量、导热系数、热膨胀系数、抗热冲击性能等物理性能参数应相互匹配。
切削刀具与加工对象的化学性能匹配主要是指刀具与工件材料化学亲和性、化学反应、扩散、粘结和溶解等化学性能参数应相互匹配。
在实际应用中,应根据所加工的工件材料选择相互匹配的刀具材料。
刀具材料是指刀具切削部分的材料。
合理选择刀具材料影响到切削加工生产率、刀具耐用度、刀具消耗和加工成本、加工精度和表面质量。
根据工件材料的切削特点,同时考虑其切削的特殊性,选择刀具材料时应考虑以下性能:
高的硬度和耐磨性、高的耐热性、足够的强度和韧性。
5、阐明金属切削形成过程的实质?
哪些指标用来衡量切削层金属的变形程度?
它们之间的相互关系如何?
它们是否真实的反映了切屑形成过程的物理本质?
为什么?
答:
金属切削形成过程的实质是工件材料的切削层在刀具的刀刃和前刀面作用下受到挤压,沿剪切面产生剪切滑移变形,而转变为切屑,同时形成已加工表面的过程。
衡量切削变形的程度的指标:
变形系数、相对滑移和剪切角三个指标。
衡量切削变形的程度的指标的相互关系:
剪切角、相对滑移和变形系数是通常用以表示切屑变形程度的三种方法。
它们是根据纯剪切的观点提出的。
但切削过程是复杂的,它既有剪切,又有前刀面对切屑的挤压和摩擦作用(第二变形区),用这些简单的方式不能反映变形的实质。
它们不能真实的反映了切屑形成过程的物理本质。
原因为切削过程是复杂的,它既有剪切,又有前刀面对切屑的挤压和摩擦作用(第二变形区),用这些简单的方式不能反映变形的实质。
切屑的变形和形成过程实际上经历了弹性变形、塑性变形、挤裂、切离四个阶段。
6、试描述积屑瘤现象及成因。
积屑瘤对切削过程有哪些影响?
答:
(1)积屑瘤是切削过程中产生的一种物理现象,在切削速度不高而又能形成连续带状切屑的情况下,加工一般钢料或其它塑性材料时,刀具前角很小或为负值时,工件、切屑的一部分金属冷焊在刀具的刀尖和前刀面上代替刀具进行切削的硬块称积屑瘤。
积屑瘤的形成与切削速度、工件材料及产生粘结现象的条件有关。
(2)积屑瘤对切削过程的影响有:
增大实际前角。
减少切屑变形,降低切削力。
增大切削厚度。
积屑瘤延伸到刃外,使得实际切削厚度增大,影响尺寸准确性。
增大已加工表面粗糙度。
积屑瘤周期性增大脱落,可随切屑排出或残留在已加工面形成鳞片状毛刺。
、
代替刀刃切削,提高刀具耐用度。
积屑瘤未脱落时,起保护刀刃和减小前刀面磨损的作用,脱落时可能粘连刀具材料一起剥落而加快刀具失效。
7、分别说明切削速度、进给量及背吃刀量的改变对切削温度的影响?
答:
(1)切削速度的改变对切削温度的影响:
切削速度对切削温度影响最大,随切削速度的提高,切削温度迅速上升;
(2)进给量的改变对切削温度的影响:
对切削温度影响较切削速度小。
(3)背吃刀量的改变对切削温度的影响:
背吃刀量变化时,散热面积和产生的热量亦作相应变化,对切削温度的影响最小。
8、说明高速钢刀具在低速、中速产生磨损的原因,硬质合金刀具在中速、高速时产生磨损的原因?
答:
(1)高速钢在中速切削是主要产生硬质点磨损(切削温度较低),高速时由于切削温度过高,主要产生塑性变形破坏。
(2)硬质合金车刀高速切削时,主要以扩散磨损为主;中速切削主要以粘结磨损为主。
9、什么叫工件材料的切削加工性?
评定材料切削加工性有哪些指标?
如何改善材料的切削加工性?
答:
(1)工件材料切削加工性:
是指在一定的条件下,工件材料切削加工的难易程度。
由于切削加工的条件和要求不同,材料的切削加工性有不同的内容和指标
(2)评定材料切削加工性有指标有:
以表面加工质量衡量切削加工性。
以刀具耐用度衡量切削加工性。
以单位切削力、切削温度衡量切削加工性。
以断屑性能衡量切削加工性。
(3)改善材料的切削加工性应从这两方面采取措施:
调整材料的化学成分。
在不影响材料使用性能的前提下,可在钢中适当添加一种或几种元素,如S、Pb、Se、P等,可获得易切钢。
易切钢切削力小,易断屑,刀具耐用度高,加工表面质量好。
通过热处理改变金相组织。
金相组织不同,材料的物理机械性能差异很大。
通过热处理,使材料的组织发生改变,使其有利于切削加工。
当材料的切削加工性无法改善时,应考虑选择合适的刀具材料、几何参数、冷却液,有条件可采用加热切削、振动切削等。
10、什么是机械加工工艺过程?
什么叫机械加工工艺规程?
工艺规程在生产中起什么作用?
答:
(1)机械加工工艺过程是指在生产过程中,是对零件采用各种加工方法,直接用于改变生产对象的形状、尺寸、表面粗糙度以及力学物理性能、相对位置和性质等,使之成为合格零件的全部劳动过程。
(2)机械加工工艺规程是指规定零件机械加工工艺过程和操作方法等的工艺文件。
(3)工艺规程在生产中的作用主要有:
是机械加工工艺过程的主要技术文件,是指挥现场生产的依据;是新产品投产前,进行有关的技术准备和生产准备的依据;是新建、扩建或改建厂房(车间)的依据。
11、加工阶梯轴如下图,试列表制订加工工艺过程(包括定位)。
单件小批生产。
答:
加工工艺过程如下:
工序号
工序内容
设备
1
车端面、打顶尖孔、车全部外圆、切槽与倒角
车床
2
铣键槽、去毛刺
铣床
3
磨外圆
外圆磨床
12、下图示柱塞杆零件,如何选择其粗基准?
(提示:
φA部分余量较φB部分大)
答:
粗基准选择一般应遵循以下原则:
保证相互位置要求原则:
如果首先要求保证工件上加工面与不加工面的相互位置要求,则应以不加工面作为粗基准。
余量均匀分配原则:
如果首先要求保证工件某重要表面加工余量均匀时,应选择该表面的毛坯面作为粗基准。
根据粗基准选择第2条原则,加工时为保证有足够的余量,应选
作为粗基准。
13、选择下图3.36示的摇杆零件的定位基准。
零件材料为HT200,毛坯为铸件,生产批量5000,单位:
件
答:
1.精基准的选择:
该零件的设计基准是
20H7孔及端面A。
根据基准重合原则,应选
20H7孔及端面作定位精基准。
从统一基准的原则出发,以
20H7孔及端面A定位可以方便地加工其他表面,也应选
20H7孔及端面A作统一精基准。
在本例中基准重合与统一基准原则相一致。
2.粗基准的选择:
本例中零件毛坯为一般铸件,
20H7孔及
12H7孔及
12H7孔均较小,一般不铸出,故不存在重要加工面加工余量均匀问题,此时应着索考虑加工面与不加工面的位置要求。
本例中
20H7孔要求与
40外圆同轴,因此在加工
20H7孔时,应以
40外圆作粗基准。
14、试分析钻孔、扩孔和铰孔三种加工方法的工艺特点,并说明这三种孔加工工艺之间的联系。
答:
钻孔是用钻床进行加工的,工艺过程包括:
确定孔位置、样冲做标记、在钻床上装夹、根据要求选钻头。
扩孔就是在前面的工艺基础上增加了一定的孔径,但是扩孔要比钻孔的孔壁表面粗糙度好。
铰孔的作用在于使孔的精度与粗糙度达到生产要求,工艺过程也是在前面的基础之上的。
它们之间有先后,麻花钻先加工出孔,然后再视其要求选择其它工具,再加工扩孔、铰孔。
三种精度要求也是不同的,要求是越来越高。
15、车床结构形式有哪些?
试列举3种车床类型,并说明各自的加工特点。
答:
(1)床结构形式有:
按用途和结构的不同,车床主要分为卧式车床和落地车床、立式车床、转塔车床、单轴自动车床、多轴自动和半自动车床、仿形车床及多刀车床和各种专门化车床,如凸轮轴车床、曲轴车床、车轮车床、铲齿车床。
(2)普通车床:
加工对象广,主轴转速和进给量的调整范围大,能加工工件的内外表面、端面和内外螺纹。
这种车床主要由工人手工操作,生产效率低,适用于单件、小批生产和修配车间。
(3)转塔车床和回转车床:
具有能装多把刀具的转塔刀架或回轮刀架,能在工件的一次装夹中由工人依次使用不同刀具完成多种工序,适用于成批生产。
(4)自动车床:
按一定程序自动完成中小型工件的多工序加工,能自动上下料,重复加工一批同样的工件,适用于大批、大量生产。
16、周铣与端铣、顺铣与逆铣各有什么特点?
如何应用?
答:
(1)周铣与端铣的特点主要有:
周铣是指利用分布在铣刀圆柱面上的切削刃来形成平面(或表面)进行铣削的方式,称为周铣。
端铣是指利用分布在铣刀端面上的端面切削刃来形成平面的进行铣削的方式。
端铣与周铣相比,其优点是:
刀轴比较短,铣刀直径比较大,工作时同时参加切削的刀齿较多,铣削时较平稳,铣削用量可适当增大,切削刃磨损较慢,能一次铣出较宽的平面。
缺点是:
一次的铣削深度一般不及周铣。
在相同的铣削用量条件下,一般端铣比周铣获得的表面粗糙度值要大。
(2)顺铣与逆铣的特点主要有:
逆铣是指铣削时,铣刀每一刀齿在工件切入处的速度方向与工件进给方向相反的铣削方式。
顺铣是指铣削时,铣刀每一刀齿在工件切出处的速度方向与工件进给方向相同的切削方式。
1)从切屑截面形状分析 逆铣时,刀齿的切削厚度由零逐渐增加,刀齿切入工件时切削厚度为零,由于切削刃钝圆半径的影响,刀齿在巳加工表面上滑移一段距离后才能真正切入工件,因而刀齿磨损快。
加工表面质量较差。
顺铣时则无此现象
2)从工件装夹可靠性分析 逆铣时,刀齿对工件的垂直作用力Fv向上,容易使工件的装夹松动:
顺铣时,刀齿对工件的垂直作用力向下,使工件压紧在工作台上,加工比较平稳。
3)从工作台丝杠、螺母间隙分析 逆铣时,工件承受的水平铣削力小与进给速度vf的方向相反,铣床工作台丝杠始终与螺母接触。
顺铣时,工件承受的水平铣削
(3)周铣和端铣:
端铣具有铣削较平稳,加工质量及刀具耐用度均较高的特点,且端铣用的面铣刀易镶硬质合金刀齿,可采用大的切削用量,实现高速切削,生产率高。
端铣适应性差,主要用于平面铣削。
周铣的铣削性能虽然不如端铣,但周铣能用多种铣刀,铣平面、沟槽、齿形和成形表面等,适应范围广,因此生产中应用较多。
17、分析成形式、渐成式、轮切式及综合式拉削方式的各自特点及相应拉刀切削部分的设计特点。
答:
拉削时,从工件上切除加工余量的顺序和方式有成形式、渐成式、轮切式和综合轮切式等。
成形式。
加工精度高,表面粗糙度较小,但效率较低;拉刀长度较长,主要用于加工中小尺寸的圆孔和精度要求高的成形面。
渐成式适用于粗拉削复杂的加工表面,如方孔、多边形孔和花键孔等,这种方式采用的拉刀制造较易,但加工表面质量较差。
轮切式切削效率高,可减小拉刀长度,但加工表面质量差,主要用于加工尺寸较大、加工余量较多、精度要求较低的圆孔。
综合轮切式是用轮切法进行粗拉削,用成形法进行精拉削,兼有两者的优点,广泛用于圆孔拉削。
18、非回转表面加工中所用机床夹具由哪些部分组成?
各组成部分有何功用?
答:
(1)非回转表面加工中所用机床夹具由定位支承元件、夹紧装置、连接定向元件、对刀元件或导向元件、其它装置或元件、夹具体部分组成。
(2)各组成部分功用有:
1)定位支承元件:
确定工件在夹具中的正确位置并支承工件,是夹具的主要功能元件之一。
定位支承元件的定位精度直接影响工件加工的精度。
2)夹紧装置:
将工件压紧夹牢,并保证在加工过程中工件的正确位置不变。
3)连接定向元件:
用于将夹具与机床连接并确定夹具对机床主轴、工作台或导轨的相互位置。
4)对刀元件或导向元件 :
保证工件加工表面与刀具之间的正确位置。
用于确定刀具在加工前正确位置的元件称为对刀元件,
5)其它装置或元件
根据加工需要,有些夹具上还设有分度装置、靠模装置、上下料装置、工件顶出机构、电动扳手和平衡块等,以及标准化了的其它联接元件。
6)夹具体
夹具体是夹具的基体骨架,用来配置、安装各夹具元件使之组成一整体。
常用的夹具体为铸件结构、锻造结构、焊接结构和装配结构,形状有回转体形和底座形等形状。
上述各组成部分中,定位元件、夹紧装置、夹具体是夹具的基本组成部分。
19、加工非回转表面主要有哪些定位方式、常用哪些定位元件?
答:
主要有:
⑴工件以平面定位:
圆柱支承、可调支承、自位支承、辅助支承;
⑵工件以外圆定位:
V形块、定位套、半园套、圆锥套;
⑶工件以圆孔定位:
定位销、圆锥销、定位心轴;
⑷工件以组合表面定位:
一面两销。
20、非回转体加工常用哪些夹紧机构?
各有何特点?
答:
(1)常用的夹紧机构有螺旋夹紧机构、偏心压板夹紧机构、定心夹紧机构、多位夹紧机构、液压夹紧机构几种。
(2)各夹紧机构的特点有:
1)螺旋夹紧机构:
靠转动螺杆直接作用于工件上来实现夹紧的一种机构。
其特点是结构简单,夹紧可靠,制造方便,适用于一般手动夹紧。
2)偏心压板夹紧机构:
用偏心件,通过压板将工件夹紧的一种机构。
其特点是夹紧工件迅速,结构紧凑,操作方便,所以在机床夹具中应用极广。
3)定心夹紧机构。
在夹具中,工件的定位与夹紧同时实现的机构称为定心夹紧机构。
其特点是定位和夹紧为同一元件,能同时等距离地移向或退离工件。
因此,不仅定心、夹紧好,而且生产效率高。
4)多位夹紧机构:
指操作一个手柄能在几个夹紧位置上同时夹紧一个工件(单件多位夹紧)或夹紧几个工件(多件多位夹紧)的夹紧机构。
它能同时从几个方向上均匀地夹紧工件,所以既能保证夹紧质量,又能缩短辅助时间。
它广泛应用于成批生产中的夹具上。
5)液压夹紧机构:
利用压力油作为介质来传递动力和运动的一种夹紧机构。
它具有夹紧可靠、工作平稳、操作方便、动作迅速等优点,广泛应用于各种大批量的自动化流水线生产中。
21、举例说明加工精度、加工误差的概念以及两者的区别与关系。
答:
加工精度:
零件加工后的实际几何参数(尺寸、形状和位置)与理想几何参数相符合的程度。
符合程度越高则加工精度就越高。
加工误差:
零件加工后的实际几何参数对理想几何参数的偏离程度称为加工误差。
加工误差的大小表示了加工精度的高低,加工误差是加工精度的度量。
区别与关系:
加工精度和加工误差都是评定零件几何参数准确程度的两种不同概念,从不同的角度在描述误差,但是加工误差的大小由零件的实际测量的偏离量来衡量,而加工精度的高低由公差等级或者公差值来衡量,并由加工误差的大小来控制。
一般来说,只有加工误差小于公差时才能保证加工精度。
22、表面质量的含义包括哪些主要内容?
为什么机械零件的表面质量与加工精度具有同等重要的意义?
答:
(1)表面质量的含义包括:
①加工表面的几何特征[表面粗糙度及波度];
②表面层物理力学性能的变化[表面层因塑性变形引起的冷作硬化;表面层中的残余应力;表面层因切削(力)热引起的金相组织变化。
]
(2)机器零件的加工质量不仅指加工精度,还包括加工表面质量,它是零件加工后表面层状态完整性的表征。
机械加工后的表面,总存在一定的微观几何外形的偏差,表面层的物理力学性能也发生变化。
机械零件加工后表面层的状态会影响零件的使用性能,使用寿命及工作可靠性,从而影响产品的质量。
因此要根据产品的工作要求,订出合格的表面质量与加工精度。
23、何谓工艺系统的刚度、柔度?
它们有何特点?
工艺系统刚度对加工精度有何影响?
怎样提高工艺系统的刚度?
答:
(1)工艺系统刚度:
指工件加工表面在切削力法向分力Fp的作用下,刀具相对工件在该方向上位移y的比值:
k=Fp/y;是等于机床、夹具、刀具及工件刚度的倒数之和的倒数。
工艺系统柔度:
刚度的倒数称为柔度w。
(2)工艺系统的刚度、柔度的特点有:
工艺系统的刚度是由组成工艺系统各部件的刚度决定的,主要取决于薄弱环节的刚度。
(3)工艺系统刚度对加工精度影响有:
1)受力点位置的变化(所引起工件的误差);包括:
机床变形、工件的变形、工艺系统总变形、工件在顶尖上加工后的单边变形等。
2)工件毛坯加工余量和材料硬度的变化(误差复映规律)
3)传动力、惯性力、重力和其它作用力的变化
①由于惯性力和传动力引起的加工误差
②机床部件和工件本身的重量引起的加工误差
③夹紧变形引起的误差
4)当工件的刚性较差时,由于加紧的方法不当,也会引起工件的形状误差。
(4)提高工艺系统的刚度措施主要有:
1)增加机床的床身以及夹具体等支承零件本身的静刚度。
(增加截面积,大的惯性矩)
2)提高接触刚度。
(提高表面粗糙度和形状精度的要求)
3)设置辅助支承,提高部件刚度。
4)采用合理的安装方法和加工方法。
24、何谓误差复映规律?
误差复映系数的含义是什么?
它与哪些因素有关?
减小误差复映有哪些工艺措施?
答:
(1)在加工过程中,由于工件毛坯加工余量或材料硬度的变化,引起切削力和工艺系统受力变形的变化,因而产生工件的误差。
(2)误差复映系数:
△工=ε△坯,ε的数量级的含义是表示了加工后工件误差与毛坯误差之间的比例关系,说明了“误差复映”的规律。
(3)影响误差复映系数因素有:
λ-系数,一般为0.4
Cp-反映工件材料和刀具角度的系数
kxt-系统刚度
(4)减小误差复映的工艺措施有:
1)走刀次数(或工步次数)愈多,总的误差愈小,零件的形状精度愈高,对于轴类零件则是径向截面的形状精度愈高。
2)系统刚度愈好,加工精度愈高。
25、磨削加工时,影响加工表面粗糙度的主要因素有哪些?
答:
(1)几何因素(砂轮的磨粒、砂轮修整、磨削用量)
(2)物理因素(磨削用量、磨削速度、工件材料、砂轮粒度与硬度、切削液等)
增加砂轮的转速,降低工件的转速,减少砂轮的纵向进给量,减小砂轮的粒度,增加金刚石笔锋利程度、减少其纵向进给量进行砂轮修整,硬度合适、自励性好,以及合适的砂轮材料都能降低表面粗糙度。
26、什么是磨削“烧伤”?
为什么磨削加工常产生“烧伤”?
为什么磨削高合金钢较普通碳钢更易产生“烧伤”?
磨削“烧伤”对零件的使用性能有何影响?
试举例说明减少磨削烧伤及裂纹的办法有哪些?
答:
(1)磨削烧伤,是指由于磨削时的瞬时高温使工件表层局部组织发生变化,并在工件表面的某些部分出现氧化变色的现象。
(2)磨削加工常产生“烧伤的主要原因有:
磨削加工不仅磨削比压特别大,且磨削速度也特别高,切削单位体积金属的功率消耗远大于其它加工方法,而加工所消耗能量的绝大部分都要转化为热量,这些热量中的大部分将传于被加工表面,使工件具有很高的温度,就会使工件表面层金属的金相组织产生变化,使表层金属硬度下降,使工件表面呈氧化膜颜色,从而出现烧伤现象。
(3)为什么磨削高合金钢较普通碳钢更易产生“烧伤”
磨削加工不仅磨削比压特别大,且磨削速度也特别高,切削单位体积金属的功率消耗远大于其它加工方法,而加工所消耗能量的绝大部分都要转化为热量,这些热量中的大部分将传于被加工表面,使工件具有很高的温度,就会使工件表面层金属的金相组织产生变化,使表层金属硬度下降,使工件表面呈氧化膜颜色,从而出现烧伤现象。
(4)磨削烧伤会降低材料的耐磨性、耐腐蚀性和疲劳强度,烧伤严重时还会出现裂纹。
(5)试举例说明减少磨削烧伤及裂纹的办法有哪些?
1)正确选用砂轮,例如可采用颗粒较粗、较软、组织较疏松的砂轮;砂轮磨损后应及时修整。
若砂轮的粒度越细、硬度越高时自砺性差,则磨削温度也增高。
砂轮组织太紧密时磨屑堵塞砂轮,易出现烧伤。
砂轮钝化时,大多数磨粒只在加工表面挤压和摩擦而不起切削作用,使磨削温度增高,故应及时修整砂轮。
2)改善磨削时的冷却条件,如采用内冷却方法;设法使冷却液渗透到磨削区中。
3)合理选择磨削用量,例如提高