QD型起重机制造工艺规程DOC 50页.docx
《QD型起重机制造工艺规程DOC 50页.docx》由会员分享,可在线阅读,更多相关《QD型起重机制造工艺规程DOC 50页.docx(51页珍藏版)》请在冰豆网上搜索。
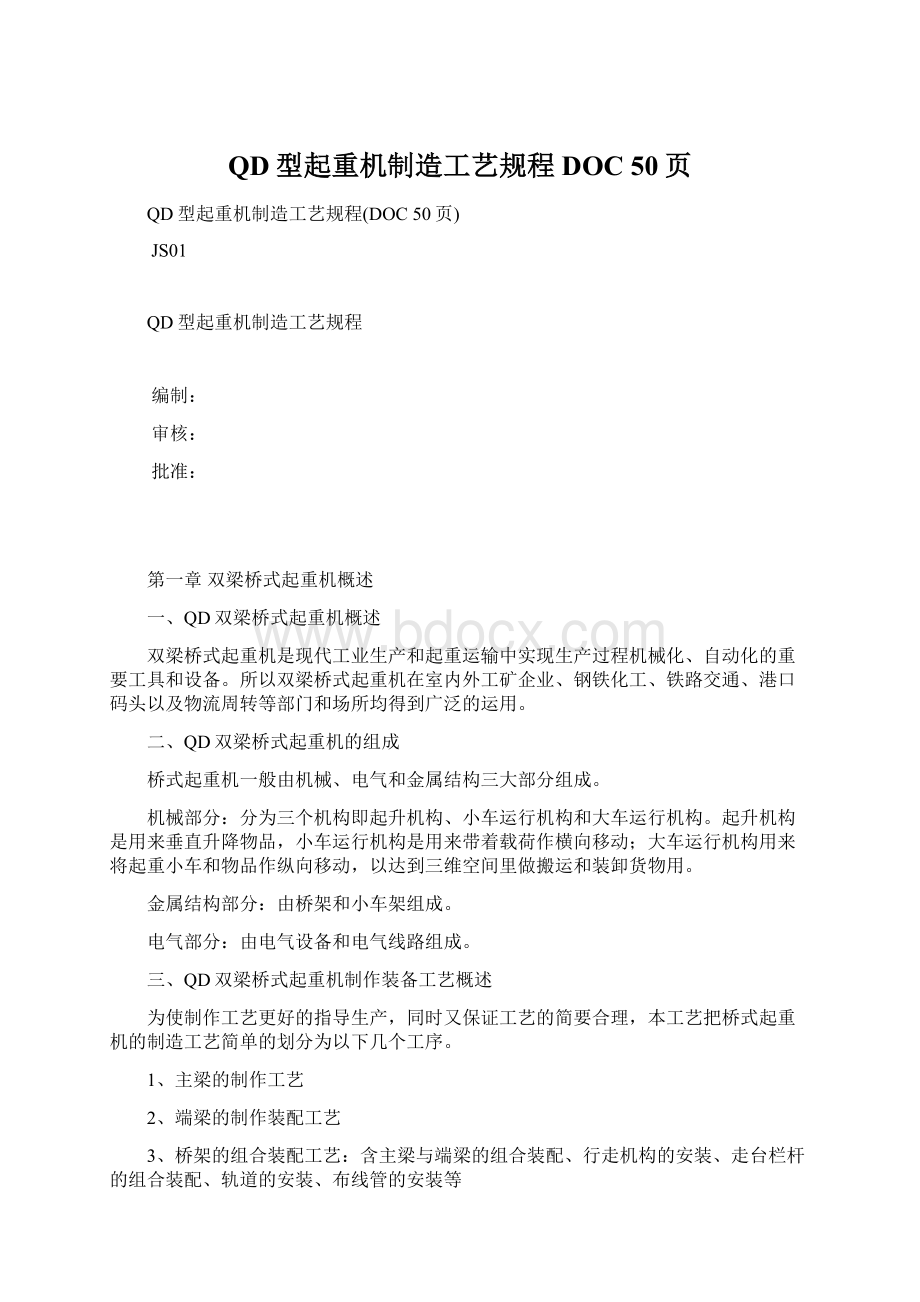
QD型起重机制造工艺规程DOC50页
QD型起重机制造工艺规程(DOC50页)
JS01
QD型起重机制造工艺规程
编制:
审核:
批准:
第一章双梁桥式起重机概述
一、QD双梁桥式起重机概述
双梁桥式起重机是现代工业生产和起重运输中实现生产过程机械化、自动化的重要工具和设备。
所以双梁桥式起重机在室内外工矿企业、钢铁化工、铁路交通、港口码头以及物流周转等部门和场所均得到广泛的运用。
二、QD双梁桥式起重机的组成
桥式起重机一般由机械、电气和金属结构三大部分组成。
机械部分:
分为三个机构即起升机构、小车运行机构和大车运行机构。
起升机构是用来垂直升降物品,小车运行机构是用来带着载荷作横向移动;大车运行机构用来将起重小车和物品作纵向移动,以达到三维空间里做搬运和装卸货物用。
金属结构部分:
由桥架和小车架组成。
电气部分:
由电气设备和电气线路组成。
三、QD双梁桥式起重机制作装备工艺概述
为使制作工艺更好的指导生产,同时又保证工艺的简要合理,本工艺把桥式起重机的制造工艺简单的划分为以下几个工序。
1、主梁的制作工艺
2、端梁的制作装配工艺
3、桥架的组合装配工艺:
含主梁与端梁的组合装配、行走机构的安装、走台栏杆的组合装配、轨道的安装、布线管的安装等
4、小车的制作工艺:
含小车架的制作、小车行走及起升机构的安装
四、编制依据
GB3811--2008《起重机设计规范》
GB/T14405-2011《通用桥式起重机》
JB/T53442—94《通用桥式起重机产品质量分等》
GB6067-2010《起重机安全规程》
GB/T985.1-2008《气焊、手工电弧焊及气体保护焊坡口基本形式和尺寸》
GB986-88《埋弧焊坡口的基本形式和尺寸》
GB10854-89《钢结构焊缝外形尺寸》
GB/T12467.1-2009《焊接质量要求》
JB/T5000.3-2007《重型机械通用技术条件焊接件》
JB/T5000.2-2007《重型机械通用技术条件火焰切割件》
五、总体要求
1、起重机金属结构制造过程中的冷作、焊接、检测工序,从下料到完工、检测,皆需遵守本《规程》制造生产。
2、本《规程》未涉及的内容,在编制《起重机制作工艺装配卡》、《起重机械焊接工艺卡》
时应补充完善明确。
3、起重机械制造除符合本《规程》的规定外,还应符合相应图纸、工艺文件的要求。
本《规程》若与图纸、工艺文件有矛盾,应报请工艺责任工程师或质保工程师处理。
4、制作过程中除要遵守本《规程》外,还应严格执行相关工种的《安全技术操作规程》。
5、各种材料的使用严格按照要求执行。
六、本公司生产的LH型葫芦双梁桥式起重机及箱型单梁起重机的工艺参照此工艺及本工艺相对应的制造装配工艺卡。
第二章主梁的制作工艺
一、主梁的结构
桥式起重机主梁为箱型梁结构,如下图,由上下盖板、腹板、大小筋板、工艺加强角钢和扁钢组成对称的箱梁结构。
大体工艺过程为:
备料、组对焊接和校正。
简要的组装焊接工艺过程:
将上盖板吊放在平上,点焊焊接大小筋板,装配腹板并焊接内侧焊缝,装配下盖板,焊接四条主焊缝,校正修整。
二、技术条件
1、为保证桥架具有F=0.9~1.4S/1000上拱度,要求单根主梁应具有的工艺拱度及允差(见附表一)。
主梁工艺拱度是靠腹板下料时的预留拱度保证的。
2、为保证桥吊装配后主梁的直线性,要求单主梁外弯值
(
时只能向走台侧弯曲)
上拱度F外弯值f如图1所示
3、腹板波浪
测量长度为1米,其最大波峰允许偏差。
在离上盖板H/3以上的区域不大于0.7δδ为腹板厚
其余区域不大于1.2δ
如图2所示
4、盖板水平偏斜a〈
如图3所示
腹板垂直偏斜b〈
如图5所示
5、大筋板在沿铅垂面(腹板面)上的倾斜不得大于
。
见图4(a)
大筋板在水平(盖板面)上的偏斜不得大于2mm。
见图4(b)
6、各大筋板间距名义尺寸偏差
mm。
7、上盖板的波浪度
测量肋板间距为1mm,其最大波峰允许偏差:
δ
不大于3mm
δ〉10mm不大于2mmδ为上盖板的厚度
8、同一台的起重机的两根主梁,各截面拱度差不大于3mm。
整个梁的拱度应是圆滑的,基本符合抛物线形状。
注:
主梁的走台斜挂筋在走台上部时,同一台起重机的两根主梁,各截面的拱度差允许不大于5mm。
(拱度偏大的一根作为传动侧)
9、钢板采用自动焊,半自动焊拼接时,应具备有60X60(mm
)厚度与被拼接板等同的工艺板。
10、主梁下盖板的拼接在下列范围内必须成45度斜角。
a.起重机跨度L
25.5m时,主梁跨度中线左右各2m长度内。
b.起重机跨度L>25.5m时,主梁跨度中线左右各3m长度内。
11、腹板的垂直拼接缝,上下盖板的横向拼接缝,以上三者均应相互错开200mm,腹板的垂直拼接缝与大筋板位置应错开不得小于50mm,即同一截面上不允许出现两条焊缝。
12、当腹板高度不够需要拼接时,拼接的宽度不应小于50mm,应避免十字交叉焊缝。
13、单主梁跨度
m,其最大拱度处可以与主梁理论中心偏离500mm,L〉19.5m,允许偏离1000mm。
14、焊接材料,主梁焊缝X光检查的有关规定见本厂双梁吊焊接技术要求,有关焊接规范也见上述要求。
(表一)
δ
6
8
10
a
0.8
0.8
H
2.0
2.5
b
14
16
18
三、主梁制作工艺步骤
根据客户要求及主梁截面大小,确定选用钢板预处理设备对钢材先行除锈、喷漆,或者是在主梁制作完成后经过通过式抛丸机进行除锈。
1、腹板备料下料
当钢板长度、宽度满足要求时,可直接下料,否则按要求拼板备料下料。
腹板的下料可在数控等离子切割机上进行,也可人工下料,但务必注意保证腹板的拱度、长度、高度。
1.1.按跨度L+100mm的长度拼接钢板,焊缝拼接口必须进行剪切,清除焊缝两侧各20mm内(包括反面)的铁锈和污物,接口间隙不大于0.8mm。
如图6。
注:
如腹板高H
板料宽度,焊缝两端须加工艺板。
1.2.如果腹板在高度方向也需拼接时,应先拼好高度方向,再在长度方向上拼接。
1.3.进行点焊肉高不大于3mm,焊段长为20~30mm,严禁用大直径的焊条点焊。
1.4.如果拼接缝间隙>1mm,应先蹓缝,焊肉高不大于3mm,焊缝不准存在气孔,灰渣等缺陷。
1.5.采用半自动焊接时必须进行焊接规范和焊嘴角度的调试,合适后方可在产品上施焊。
1.6.为保证焊透δ
10mm时反面应清根,采用风铲,气刨等方法均可。
1.7.焊后用样板检查焊缝尺寸。
允许焊肉纵向轴线偏差Δ
1mm,Δ
mm,正反面焊缝两轴线位错(为错为Δ
+Δ
)Δ
1mm,Δ
1mm。
(见图7)
1.8.当腹板长度、高度满足要求后,可在数控等离子切割机上根据套料软件做出的拱度直接下料,也可根据在电脑上放样出的拱度在钢板上划线放样,然后人工下料。
1.9.待料板冷却后,检查并记录下料拱度(每块必检至少测五点),配对并作记号后转交下道工序。
注:
应务必用样冲标示出腹板中心。
2、上下盖板下料
2.1.上盖板加长量为200mm,下盖板加长量不作规定。
当钢板长度满足要求时,可直接按
要求下料,长度达不到要求时,需按要求接板下料。
2.2.6~8mm板厚的上下盖板均按腹板拼接和焊接方法进行,采用自动焊或半自动焊,不开坡口,双面焊接。
焊缝尺寸见表二。
焊接规范见〈焊接技术要求表Π〉。
2.3.δ
mm时,用气割的方法制备V型坡口,反面应清根,封底。
采用φ4mm焊条进行手工电弧焊接,焊缝尺寸见表三。
焊接规范见〈焊接技术要求〉表7。
焊接检查要求见厂标:
Q/YT—105/72。
2.4.数控等离子切割机或半自动切割机下料
上盖板料应与腹板相应组配,使盖板接缝与腹板接缝错开不小于200mm,作出相应的标
记。
注:
焊缝宽度b的公差按如下规定:
δ<10mm时为
1.5mmδ=10~18mm时为
2mm,δ=20~28mm时为
3mm。
2.5.上下板均应进行宽度和厚度的尺寸检查,合格后转下道工序。
(说明:
该工序采用先拼后割,而不是先割后拼)
注:
务必用样冲标示出上下改变中心。
3、大小筋板下料
3.1.大小筋板应保证尺寸要求。
宽度公差不应大于-1.5mm,长度公差应超过
2mm。
3.2.每块大筋板应保证与上盖板焊接的一侧两角为90度(并作出标记),垂直度误差不大于
(H为筋板高)。
3.3.大筋板用板条拼接时按图9进行,必须用定位胎拼装点焊。
采用两面手工焊接,允许不焊透。
当筋板厚度δ
8mm时,反面焊缝应用碳弧气刨清根2~4mm。
3.4.焊后修理变形,不合直角要求者用二次剪切进行矫正。
3.5.检验合格者后转下道工序。
4、箱型梁组对焊接
4.1、上盖板与大小筋板组焊
4.1.1.将上盖板铺在平台上,修理旁弯使盖板平直,清除污绣,铲(磨)平腹板位置处焊肉,以中心为基准打上腹板位置粉线(做好用样冲做标记),偏差不大于1mm。
4.1.2.从跨度中心向两端画筋板位置线(筋板间隔允许偏差
3mm)见图10。
4.1.3.装配,点焊大,小筋板,注意将有90度标记的一端放在上盖板上。
定点时,要求筋板要垂直于盖板而且两端与两腹板粉线的距离相等。
4.1.4.焊接大小筋板焊缝。
注意同一台吊车的两根主梁应向相反方向进行断续焊接,以造成主梁向有走台侧旁弯(见图11),并做出无走台侧标记。
4.1.5.上盖板与筋板的T型焊缝,应在焊前画好焊段位置线,间隔焊的端部正好是非焊段时,应焊上至少50mm长的焊缝。
在画底板焊段位置线的同时将各筋板垂直方向的断续对称焊位置线画好,以备里皮(即里侧)焊接时用。
4.1.6.引弧灭弧时要注意焊肉不能超出大小筋板端部,出现多余焊肉时应铲除,方可装配腹板。
4.1.7.焊工从中心向两侧施焊。
4.2、腹板与上盖板、筋板组焊
4.2.1.在腹板上划出工艺角钢位置线和筋板线。
4.2.2.如主梁有纵向加强角钢时,应将角钢装配焊接于小筋板上并保证角钢外边与大筋板的直线性。
4.2.3.将下料配好对的腹板装配于上盖板上,对好中心后用卡栏将腹板临时固定到大筋板上。
见图12
4.2.4.装配,点焊两腹板时,应从中心向两头两面同时进行。
为保证腹板与筋板间隙较小,用自制液压拼槽机装配点焊。
注意腹板之间,腹板与盖板之间焊缝应相互错开。
点定时不允许在腹板外侧进行。
腹板与盖板间隙不小于1mm。
4.2.5.上盖板与腹板连接焊缝点焊肉高4~5mm,焊段长30mm。
腹板与大小筋板连接焊缝,点焊肉高不大于3mm,大筋板上焊段长80mm为宜,小筋板上焊段长30~50mm为宜。
点焊间距不大于200mm。
筋板,上盖板与腹板三板相交处必须进行点固。
4.2.6.Π型梁腹板两端面处必须焊上100mm长的焊段,焊肉4mm。
4.2.7.Π型梁点定后,要将上盖板腰缝中心处焊上约200mm长的焊段,焊肉3mm。
4.2.8.装配,点焊第二道角钢或工艺扁铁。
4.2.9.焊接前先将Π型梁无走台侧(凹侧)向下放在垫架上,梁的两端及中段均应垫起。
如图13。
4.2.10.焊接采用二氧化碳气体保护焊,焊接腹板和大小筋板,角钢,工艺扁铁间的焊缝。
4.2.11.焊接时焊工应成双对称分布,按预先画好的断续焊缝位置从里向外进行焊接,其顺序见图15。
4.2.12.焊完一面后利用工装翻到另一个面,在Π型梁垫起后,再焊接该面(有走台侧)焊缝。
4.2.13一根Π型梁的两侧焊缝应不间断的一次焊完。
4.2.14.Π型梁焊完后,两端垫起,中间悬空放置好,见图14
4.3、装配下盖板
4.3.1.把焊好里皮的Π型梁两端支起(见图16),检查并记录其上拱度值。
拱度应从中间向两端逐渐减少,基本上保持抛物线型。
如不合要求时,可采用梭子螺丝压紧或采用火焰矫正的方法加以调整。
装配下盖板前,应确保主梁不扭曲,否则务必在此工序校正。
4.3.2.将下盖板上的铁锈及污物去除,铲平腹板处焊肉将下盖板放在垫物上,找好中心。
4.3.3.装配,点焊下盖板:
从中心向端部,两侧同时进行装配焊,腹板与盖板间隙不大于0.8mm,稍度处间隙不大于2mm,点焊肉3mm,焊段长30~40mm,点焊间距小于200mm。
(注意:
装配下盖板时控制腹板波浪以合要求)
4.3.4装配下盖板端部:
a.下盖板厚δ
8mm可冷弯
b.下盖板厚8mm<δ
16mm加热弯曲。
c.下盖板厚δ>16mm,端部加压成型与中部焊成一体再进行装配。
斜稍处点焊采用斜坡点焊法,不允许焊滴下淌。
4.3.5.单主梁点固后两端垫起,检查并记录拱度值(至少测五点。
)并将拱度值标于梁上。
注意:
本工序为主梁制造的重要工序,应严格控制,保证质量。
4.4、主梁头部焊接及修理
4.4.1单主梁点焊后放躺在垫架上,将超过公差的缝隙打严(包括头部斜稍处)。
难以靠严的采用手工焊进行蹓缝,蹓缝时采用φ4mm焊条,焊肉3mm。
4.4.2.修理单主梁该面波浪变形。
4.4.3翻身后同步骤4.4.1。
4.4.4修理另一面波浪变形。
4.4.5主梁两头部大筋板密封焊缝可在主梁立放检修之前手工焊接。
以上见图17
4.5、主梁四条主焊缝焊接
4.5.1将主梁两端放在焊接平台上如图18,用全自动龙门埋弧焊从两侧同时焊接,焊接次序一般如下:
先焊接焊缝1,2(下盖板与腹板焊缝),后焊接焊缝3,4见图19。
4.5.2.每批首焊件必须在试板上调试规范,合适后方可在产品上施焊,严禁在产品上边焊边调。
4.5.3.用手工二氧化碳气体保护焊时,两台焊机要同时开机,在施焊过程中,两机错开的间距不得超过以下规定:
10.5~13.5m跨,不得超过1/3跨长。
16.5m跨以上,不得超过4m。
不允许单机操作,以免造成旁弯过大。
4.5.4.如果单主梁点固后,拱度过大,焊接次序变为先3.4,后1.2
4.5.5.垫墩位置一般设在距梁端为全长1/4附近的大筋板处。
4.5.6.主梁两端不要把腹板焊到头,留30-50mm,这样便于主梁与端梁的装配。
4.6、主梁的修理与检验
将同一台起重机的两个主梁旁弯向外的放在检验台架上,检查拱度,波浪,扭曲,高低差等,如不符合要求时,可采用火焰矫正压重矫正。
4.6.1拱度矫正
a.整个梁长度方向的拱度都不足时,可先在下盖板(大筋板处)横向布置几处带状加热面,随后在两侧腹板布置三角形加热面。
见图20
b.拱度不足时,可在不足之下盖板和两侧腹板,用上述方法布置加热面进行矫正。
c.拱度过大时,用上述同样方法,但局部加热面布置在主梁上部,可配合加重。
d.两根梁高低差过大(>3mm)时,可按局部或过大拱度进行处理。
4.6.2旁弯的矫正
e.当旁弯不符合要求时(包括S弯)可采用火焰矫正法进行。
f.加热面布置在主梁上部筋板位置处(要求凸弯的反侧)加热尺寸如图21。
g.扭曲可用矫正旁弯和拱度两向矫正方法加以解决。
4.6.3波浪矫正
h.波浪形一般产生在腹板中部和下部,无走台面更严重一些,可采用火焰矫正。
i.凸出处用园点加热法并伴随着园点外围锤击进行矫正。
j.凹处可采用点焊带孔拉板,提起凹处,或配合火焰加热,锤击加以矫正。
k.如波浪形是长方形的,可采用“棱”形加热面进行矫正。
(以上见图22)
附表一:
桥架主梁拱度交检值
拱度
跨度(m)标准
标准
正差
负差
F=
F+0.3F
F-0.1F
7.5
7.5
9.8
6.7
10.5
10.5
13.7
9.4
13.5
13.5
17.6
12.1
16.5
16.5
21.5
14.8
19.5
19.5
25.4
17.5
22.5
22.5
29.3
20.2
25.5
25.5
33.2
22.9
28.5
28.5
37.1
25.6
31.5
31.5
41.0
28.3
拱度
跨度(m)非标准
标准
正差
负差
F=
F+0.3F
F-0.1F
7
7
9.1
6.7
11
11
14.3
9.4
14
14
18.2
12.1
17
17
22.1
14.8
20
20
26.0
17.5
23
23
29.9
20.2
26
26
33.8
22.9
28
28
36.4
25.6
32
32
41.6
28.3
附表二:
腹板下料拱度表(夏、秋季)
(mm)
吨位(T)
跨度(m)
5、10
15、20
30、50
10.5
21~23
19~21
21
13.5
28~30
24~26
30
16.5
37~39
32~34
41
19.5
42~44
38~40
48
22.5
53~55
49~51
54
25.5
65~67
56~58
64
28.5
81~83
67~69
77
31.5
89~91
77~80
90
附表三:
腹板下料拱度表(夏、秋季)
(mm)
吨位(T)
跨度(m)
5、10
15、20
30、50
10.5
16~18
13~15
19
1
13.5
20~22
18~20
23
2
16.5
29~31
26~28
29
2
19.5
34~36
30~33
34
2
22.5
43~45
39~41
39
2
25.5
50~52
45~47
44
2
28.5
60~62
52~54
51
2
31.5
70~72
58~60
57
2
附表四:
钢丝自重扣除表(重铊为15公斤,钢丝直径φ0.49~0.52mm)
跨度
10.5
13.5
16.5
19.5
22.5
25.5
28.5
31.5
扣除值
1.5
2.5
3.5
4.5
6
8
10
12
※实际拱度计算:
撑杆高为H,钢尺量得值为h
,相应跨度钢丝的自重扣除值为h
,则实际拱度F=H-(h
+h
)
毛值F
=H-h
第三章端梁的制作工艺
一、端梁工艺概述
箱型双梁吊钩桥式起重机的端梁是起重机的重要部件,制造精度的高低将直接影响桥架的组装精度,因此,必须严格控制。
端梁由上、下盖板、腹板、补强板、隔板、弯堵头板、拉筋板和脚踏板组成对称的两个部分的箱梁结构,中间接头用角钢和钢板通过螺栓紧固联接成为端梁整体(见图一)。
大体工艺过程为:
备料,端梁的组对焊接,接孔的钻铰,装配螺栓和检验。
简要的组装焊接工艺过程:
将上盖板吊放在平上,预制出旁弯画出隔板,腹板和工艺扁铁的位置先组装隔板及工艺扁铁的焊接。
组装一侧两块腹板,定位点焊,再装另一侧两块腹板定位点焊。
焊接梁各部位,焊缝清渣,内部涂防锈底漆,组装下盖板,焊接端梁四条纵向焊缝装配,焊接其它零件,钻铰接头孔和装配螺栓。
重点是:
梁要制造的规矩,旁弯必须达到工艺的要求,扭曲、倾斜、弯板平面差和直角差等,必须保证在允许的偏差范围内,以确保桥架装配和为装配运行机构创造条件。
二、端梁的技术要求
1、端梁上拱度F1≤W/1000(见图二)。
2、端梁向桥架内水平弯曲f=2~5mm。
(见图三)
3、端梁扭曲C≤3mm,其两组弯板扭曲C≤2mm(见图四)。
3、端梁盖板水平倾斜b≤B/250(见图五)。
4、端梁腹板垂直倾斜h≤H/250(见图六)。
5、弯板90度折合间隙d≤1.5mm(见图七)。
6、一组两块弯板不平差g≤2mm,两组弯板高低差g≤4mm(见图八)。
7、两块弯板孔距“A”的允许偏差±3mm(见图九)。
8、两弯板孔距中心线与端梁纵向中心线的偏差e≤4mm(见图八),端梁高度H+0-2
三、端梁制作工艺
1、备料
1.1.腹板备料
腹板用数控等离子切割机下料(见图九)。
1.1.1按图纸尺寸切割腹板长宽外形,腹板上装90°弯板的曲线部分和工作孔,割后清理熔渣。
1.1.2切割后的腹板高度H+0-3,腹板应按组装顺序编号。
1.1.3冷态下在辊式矫平机上矫平波浪变形,长度在6米范围内水平弯曲≤3mm,并不得有S弯和两头翘起。
1.2补强板备料
1.2.1按图纸尺寸,切割补强板长宽及装弯板曲线部分等外形尺寸(见图十)。
1.2.2清渣矫平,依图纸要求划出塞焊孔5-φ20。
钻5-φ20塞焊孔。
1.3隔板备料
1.3.1隔板用剪板机剪切下料,剪切下料时,剪切面与轧制面应垂直,其斜度允差不大于1∶10,棱边上的堆积物,毛刺和凸凹不平应铲除,毛刺不大于0.5mm。
刻痕不大于1mm。
1.3.2剪切后的隔板宽度允差±1mm,并保证任意两块隔板之差不大于1mm,四角保证两角要垂直90°(直角应做标记)间隙а≤1mm。
(见图十一)剪切后的隔板高度H+0-3
1.4弯板备料
1.4.1用半自动切割机或数控火焰切割机下料,切割下料,加长余量50mm。
(见图十二)
1.4.2压制成型,弯角不小于90°,即折合间隙b≤1.5mm。
1.4.3划螺孔线2-φ45。
钻孔2-φ45。
1.5、盖板
1.5.1切割下料,依图纸外形尺寸,数控气割机,切割下料长宽及凹进部分。
下料后,清除熔渣及铲平边棱堆积物。
1.5.2矫平,水平弯曲≤L/1000。
(L为盖板长度)
1.6中间接头连接件备料
1.6.1联接角钢、砂轮切割下料,去毛刺、涂刷防腐底漆。
(见图十三)
1.6.2划螺孔线、4-φ21,两件同时钻铰4-φ21的孔、每对拧紧予紧螺栓。
1.7其他件备料下料
1.7.1根据实际情况用相应设备下料
注:
所有零部件下料后均应做尺寸复检。
2、端梁组焊
2.1、π型梁的组装
2.1.1将上盖板放在平台上,两端下面放置厚2-3mm垫板。
调整水平弯曲2-5mm(见图十六)
2.1.2点焊定位工艺板,紧固压板螺栓。
(见图十六)
2.1.3画隔板和腹板两个方向的位置线。
(见图十六)
2.1.4将隔板具有90°的一端与上盖板相接,点焊定位,保证隔板两个方向的垂直性。
(见图十七)
2.1.5组装点焊定位旁弯凹侧两块腹板,保证腹板与盖板的垂直性,保证腹板与隔板和盖板贴紧(见图十八)
2.1.6焊接隔板与上盖板的角焊。
(见图十九)采用φ4.0焊条。
施焊方向均从有腹板侧向另一侧进行。
2.1.7用卡具装配点焊定位另一侧的两块腹板。
腹板必须与隔板和上盖班接触紧密,两侧腹板曲线部分要对齐。
(见图二十)
2.1.8在腹板上装配点焊定位中间接头的联接角钢。
(见图二十)
2.1.9装配点焊定位腹板头部的补强板,保证与腹板接触紧密及曲线部分的吻合。
(此工序用于16t以上起重机)
2.1.10尺寸复检
2.2、弯板的组装
2.2.1检查修理弯板,使弯角不小于90°,即折合间隙b≤1mm。
(见图二十一)
2.2.2将一组,两块弯板放在平台上。
用定位样杆将其一端连成一体。
用直角尺测量垂直与平台的两个弯板平面修理使其间隙b≤1mm。
调整使两块弯板的孔距尺寸达到要求后,将弯板这一端用联接板点焊定位。
(见图二十一)
2.2.3焊接腹