铣削机械加工外文翻译中英文翻译机械类外文文献翻译.docx
《铣削机械加工外文翻译中英文翻译机械类外文文献翻译.docx》由会员分享,可在线阅读,更多相关《铣削机械加工外文翻译中英文翻译机械类外文文献翻译.docx(44页珍藏版)》请在冰豆网上搜索。
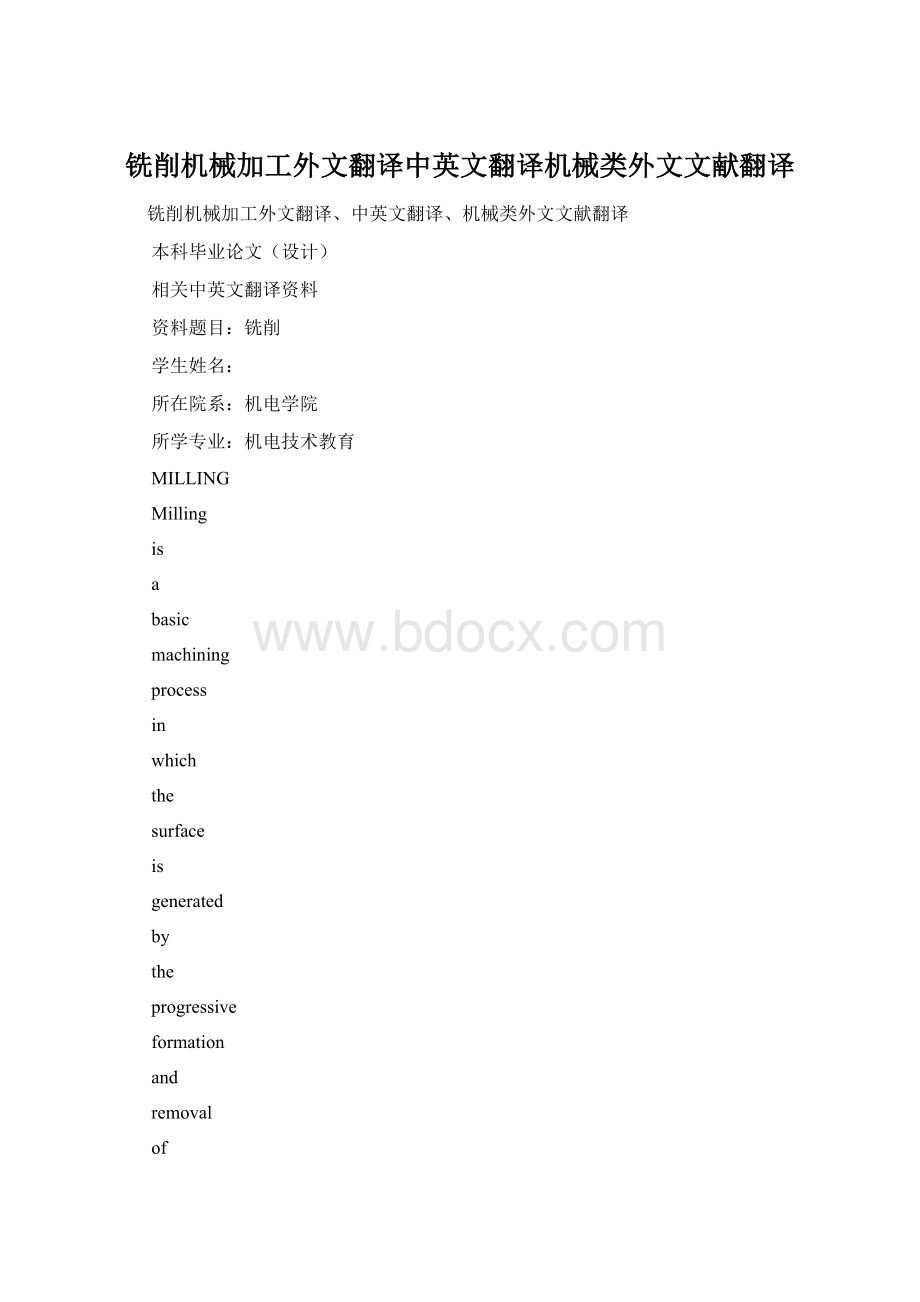
铣削机械加工外文翻译中英文翻译机械类外文文献翻译
铣削机械加工外文翻译、中英文翻译、机械类外文文献翻译
本科毕业论文(设计)
相关中英文翻译资料
资料题目:
铣削
学生姓名:
所在院系:
机电学院
所学专业:
机电技术教育
MILLING
Milling
is
a
basic
machining
process
in
which
the
surface
is
generated
by
the
progressive
formation
and
removal
of
chips
of
material
from
the
workpiece
as
it
is
fed
to
a
rotating
cutter
in
a
direction
perpendicular
to
the
axis
of
the
cutter.
In
some
cases
the
workpiece
is
stationary
and
the
cutter
is
fed
to
the
work.
In
most
instances
a
multiple-tooth
cutter
is
used
so
that
the
metal
removal
rate
is
high,
and
frequently
the
desired
surface
is
obtained
in
a
single
pass
of
the
work.
The
tool
used
in
milling
is
known
as
a
milling
cutter.
It
usually
consists
of
a
cylindrical
body
which
rotates
on
its
axis
and
contains
equally
spaced
peripheral
teeth
that
intermittently
engage
and
cut
the
workpiece.
1
In
some
cases
the
teeth
extend
part
way
across
one
or
both
Ends
of
the
cylinder.
Because
the
milling
principle
provides
rapid
metal
removal
and
can
produce
good
surface
finish,
it
is
particularly
well-suited
for
mass-production
work,
and
excellent
milling
machines
have
been
developed
for
this
purpose.
However,
very
accurate
and
versatile
milling
Machines
of
a
general-purpose
nature
also
have
been
developed
that
are
widely
used
in
jobshop
and
tool
and
die
work.
A
shop
that
is
equipped
with
a
milling
machine
and
an
engine
lathe
can
machine
almost
any
type
of
product
of
suitable
size.
Types
of
Milling
Operations.
Milling
operations
can
be
classified
into
two
broad
categories,
each
of
which
has
several
variations:
1.
In
peripheral
milling
a
surface
is
generated
by
teeth
located
in
the
periphery
of
the
cutter
body;
the
surface
is
parallel
with
the
axis
of
rotation
of
the
cutter.
Both
flat
and
formed
surfaces
can
be
produced
by
this
method.
The
cross
section
of
the
resulting
surface
corresponds
to
the
axial
contour
of
the
cutter.
This
procedure
often
is
called
slab
milling.
2.
In
face
milling
the
generated
flat
surface
is
at
right
angles
to
the
cutter
axis
and
is
the
combined
result
of
the
actions
of
the
portions
of
the
teeth
located
on
both
the
periphery
and
the
face
of
the
cutter.
2
The
major
portion
of
the
cutting
is
done
by
the
peripheral
portions
of
the
teeth
with
the
face
portions
providing
a
finishing
action.
The
basic
concepts
of
peripheral
and
face
milling
are
illustrated
in
Fig.
16-1.
Peripheral
milling
operations
usually
are
performed
on
machines
having
horizontal
spindles,
whereas
face
milling
is
done
on
both
horizontal-
and
vertical-spindle
machines.
Surface
Generation
in
Mimng.
Surfaces
can
be
generated
in
milling
by
two
distinctly
different
methods
depicted
in
Fig.
16-2.
Note
that
in
up
milling
the
cutter
rotates
againsi
the
direction
of
feed
the
workpiece,
whereas
in
down
milling
the
rotation
is
in
the
same
direction
as
the
feed.
As
shown
in
Fig.
16-2,
the
method
of
chip
formation
is
quite
different
in
the
two
cases.
In
up
milling
the
c
hip
is
very
thin
at
the
beginning,
where
the
tooth
first
contacts
the
work,
and
increases
in
thickness,
becoming
a
maximum
where
the
tooth
leaves
the
work.
The
cutter
tends
topush
the
work
along
and
lift
it
upward
from
Tool-work
relationshios
in
peripheral
and
face
milling
the
table.
This
action
tends
to
eliminate
any
effect
of
looseness
in
the
feed
screw
and
nut
of
the
milling
machine
table
and
results
in
a
smooth
cut.
However,
the
action
also
tends
to
loosen
the
work
from
the
clamping
device
so
that
greater
clamping
forcers
must
be
employed.
In
addition,
the
smoothness
of
the
generated
surface
depends
greatly
on
the
sharpness
of
the
cutting
edges.
In
down
milling,
maximum
chip
thickness
cecum
close
to
the
point
at
which
the
tooth
contacts
the
work.
Because
the
relative
motion
tends
to
pull
the
workpiece
into
the
cutter,
all
possibility
of
looseness
in
the
table
feed
screw
must
be
eliminated
if
down
milling
is
to
be
used.
It
should
never
be
attempted
on
machines
that
are
not
designed
for
this
type
of
milling.
Inasmush
as
the
material
yields
in
approximately
a
tangential
direction
at
the
end
of
the
tooth
engagement,
there
is
much
less
tendency
for
the
machined
surface
to
show
tooth
marks
than
when
up
milling
is
used.
Another
considerable
advantage
of
down
milling
is
that
the
cutting
force
tends
to
hold
the
work
against
the
machine
table,
permitting
lower
clamping
force
to
be
employed.
3
This
is
particularly
advantageous
when
milling
thin
workpiece
or
when
taking
heavy
cuts.
Sometimes
a
disadvantage
of
down
milling
is
that
the
cutter
teeth
strike
against
the
surface
of
the
work
at
the
beginning
of
each
chip.
When
the
workpiece
has
a
hard
surface,
such
as
castings
do,
this
may
cause
the
teeth
to
dull
rapidly.
Milling
Cutters.
Milling
cutters
can
be
classified
several
ways.
One
method
is
to
group
them
into
two
broad
classes,
based
on
tooth
relief,
as
follows:
1.Profile-cutters
have
relief
provided
on
each
tooth
by
grinding
a
small
land
back
of
the
cutting
edge.
The
cutting
edge
may
be
straight
or
curved.
2.In
form
or
cam-reheved
cutters
the
cross
section
of
each
tooth
is
an
eccentric
curve
behind
the
cutting
edge,
thus
providing
relief.
All
sections
of
the
eccentric
relief,
parallel
with
the
cutting
edge,
must
have
the
same
contour
as
the
cutting
edge.
Cutters
of
this
type
are
sharpened
by
grinding
only
the
face
of
the
teeth,
with
the
contour
of
the
cutting
edge
thus
remaining
unchanged.
Another
useful
method
of
classification
is
according
to
the
method
of
mounting
the
cutter.
Arbor
cutters
are
those
that
have
a
center
hole
so
they
can
be
mounted
on
an
arbor.
Shank
cutters
have
either
tapered
or
straight
integral
shank.
Those
with
tapered
shanks
can
be
mounted
directly
in
the
milling
machine
spindle,
whereas
straight-shank
cutters
are
held
in
a
chuck.
Facing
cutters
usually
are
bolted
to
the
end
of
a
stub
arbor.
The
common
types
of
milling
cutters,
classified
by
this
system
are
as
follows:
Types
of
Milling
Cutters.
Hain
milling
cutters
are
cylindrical
or
disk-shaped,
having
straight
or
helical
teeth
on
the
periphery.
They
are
used
for
milling
flat
surfaces.
This
type
of
operation
is
called
plai
n
or
slab
milling.
Each
tooth
in
a
helical
cutter
engages
the
work
gradually,
and
usually
more
than
one
tooth
cuts
at
a
given
time.
This
reduces
shock
and
chattering
tendencies
and
promotes
a
smoother
surface.
Consequently,
this
type
of
cutter
usually
is
preferred
over
one
with
straight
teeth.
Side
milling
cutters
are
similar
to
plain
milling
cutters
except
that
the
teeth
extend
radially
part
way
across
one
or
both
ends
of
the
cylinder
toward
the
:
center.
The
teeth
may
be
either
straight
or
helical.
Frequently
these
cutters
are
relatively
narrow,
being
disklike
in
shape.
Two
or
more
side
milling
cutters
often
are
spaced
on
an
arbor
to
make
simultaneous,
parallel
cuts,
in
an
operation
called
straddle
milling.
Interlocking
slotting
cutters
consist
of
two
cutters
similar
to
side
mills,
but
made
to
operate
as
a
unit
for
milling
slots.
The
two
cutters
are
adjusted
to
the
desired
width
by
inserting
shims
between
them.Staggered-tooth
milling
cutters
are
narrow
cylindrical
cutters
having
staggered
teeth,
and
with
alternate
teeth
having
opposite
helix
angles.
They
are
ground
to
cut
only
on
the
periphery,
but
each
tooth
also
has
chip
clearance
ground
on
the
protruding
side.
These
cutters
have
a
free
cutting
action
that
makes
them
particnlarly
effective
in
milling
deep
slots.Metal-slitting
saws
are
thin,
plain
milling
cutters,
usually
from
1/32
to
3/16
inch
thick,
which
have
their
sides
slightly
"dished"
to
provide
clearance
and
prevent
bindin