铸造工艺流程.docx
《铸造工艺流程.docx》由会员分享,可在线阅读,更多相关《铸造工艺流程.docx(15页珍藏版)》请在冰豆网上搜索。
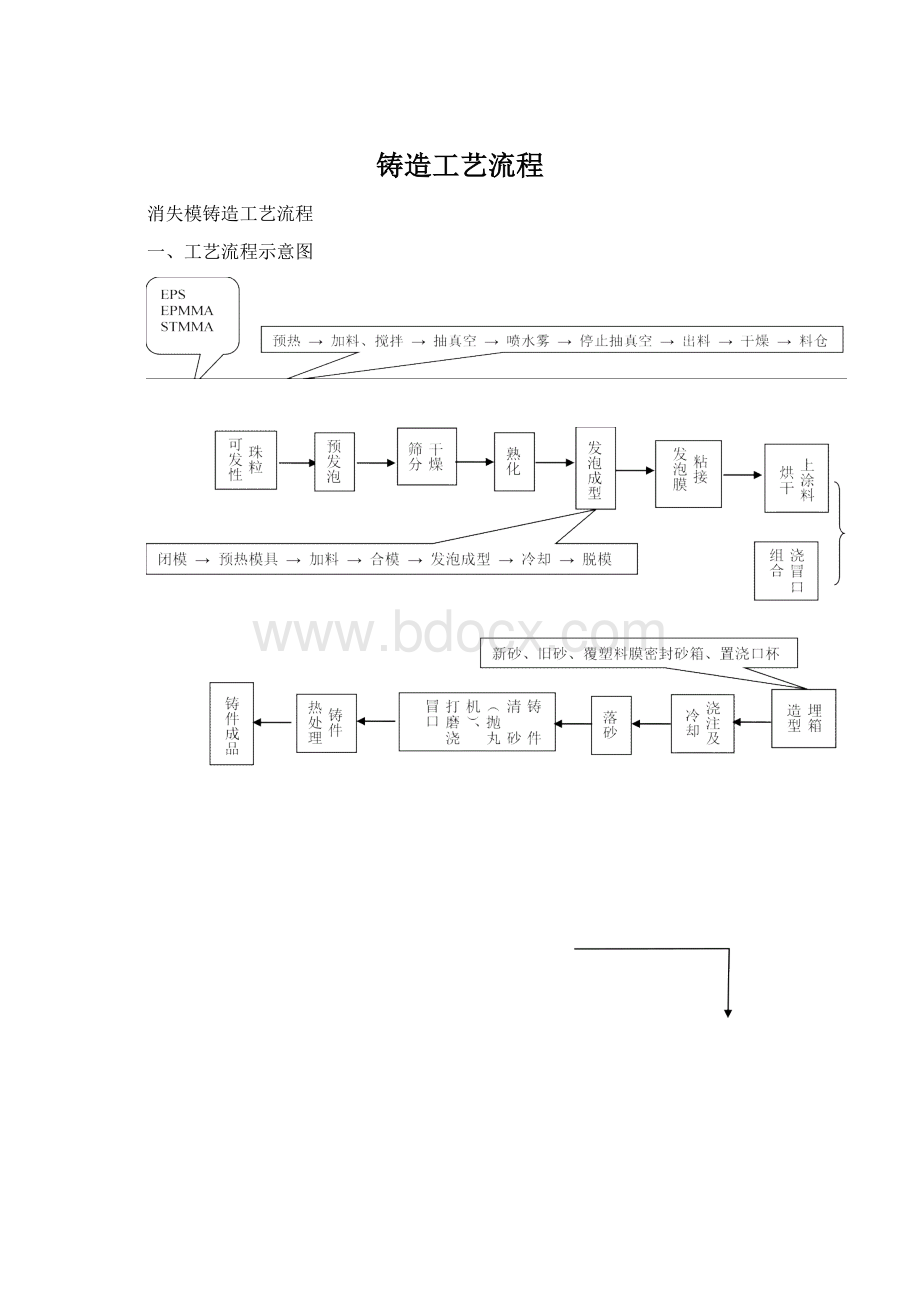
铸造工艺流程
消失模铸造工艺流程
一、工艺流程示意图
二、工艺流程
模样生产工艺流程图
(一)预发泡:
预发泡目的:
为了获得低密度、表面光洁、质量优良的泡沫模样。
流程:
预热→加料、搅拌→抽真空→喷水雾→停止抽真空→出料→干燥→料仓、熟化
EPS预发温度100~105℃;STMMA预发温度105~115℃;EPMMA预发温度120~130℃.进入预发机的加热蒸汽压力在0.15~0.20MPa范围调节。
说明:
1 间歇式蒸汽预发泡机必须满足加热均匀(蒸汽与珠粒接触)筒体内温度在90~130℃范围容易调节和控制。
搅拌要充分、均匀,筒体底部和侧壁要有刮板,防止珠粒因过热而粘壁,搅拌速度可调.筒体底部冷凝水的排除要畅通,否则影响预发泡效果。
2 加热蒸汽压力可调并稳定,且蒸汽中不能夹带水分.
3 出料要干净,每批发泡后,筒体内残留的料要吹扫干净。
熟化:
把预发泡珠放置几小时以上,让空气进入珠粒内,使珠粒变得干燥有弹性,变形后又能复原的过程。
熟化时间一般为10~24h,熟化时间不能太长否则发泡剂损失太多影响发泡成型质量。
(二)成形发泡的工艺过程为:
闭模→预热模具→加料→合模→发泡成型→冷却→脱模→模样熟化
要点:
珠粒均匀填满模具,模具必须预热到100℃,水蒸气温度一般在120℃左右,压力为0。
15MPa.
模样熟化:
将模样置入50~70℃的烘干室强制干燥5~6h,可达到在室温下自然熟化2天的效果。
(三)模样的粘合
对复杂的模样往往不能整体发泡成形,而分块制造,最后需要将各块粘合成整体。
另外,模样与浇冒口系统组成模样组,也需要粘合工序。
粘合工序一般是采用粘结剂来完成的。
目前国内使用的消失模铸造用的粘结剂可分为热熔胶型、水溶型和有机溶剂型粘胶。
粘接剂要求:
1 足够的粘接强度,大于100MPa。
2 快干性好,最好能在1h内干燥,并具有一定的粘接强度,不致在加工或搬运过程中损坏模样。
3 软化和气化点低:
气化完全,残留物少.
4 干燥后应呈柔软的,而不是脆硬性的薄层,以免在加工时损伤刀刃。
5 无毒和对泡沫塑料无腐蚀作用。
6 成本低、货源广、操作方便。
(四)涂料
1、涂料的作用
1 防止液体金属侵入铸型,特别在负压浇注时,防止出现粘砂和毛刺,促使获得表面光洁的铸件;
2 提高模样束的强度和刚度,防止填砂振动造型及负压定型时模样的变形,保证了铸件的尺寸精度;
3 提高了模样表面抗型砂冲刷能力,防止加砂过程模样表面破损;
2、对涂料的要求
1 要有一定强度、刚度及耐磨性;
2 要有好的透气性,有助于热解气体或液体产物的逸出;
3 能很好地涂挂在泡沫模样表面,形成均匀的涂层,涂层内表面无气孔、微孔;
4 涂层有一定的耐火度;
5 涂层容易从铸件上剥落;
6 对特殊铸件如薄壁铝铸件要有一定的绝热性。
3、涂料的组成
消失模铸造涂料一般由耐火骨料、粘结剂、载体(溶剂)、表面活性剂、悬浮剂、触变剂、氧化剂以及其他附加物组成。
(1)耐火骨料。
常用的耐火骨料有刚玉、锆英石、石英、铝矾土、镁橄榄石、硅藻土、高岭土类熟料.铸铁(包括灰铁、球铁、可锻铁等)选择石英粉、铝矾土、高岭土熟料、棕刚玉等耐火骨料,粒度为270~300目;普碳钢、合金钢选择石英粉、刚玉、锆英石等耐火骨料,粒度为240~270目;高锰钢、耐热钢选择镁橄榄石、锆英石等耐火骨料,粒度为240~270目;铜、铝及铜铝合金选择硅藻土、滑石粉等耐火骨料,粒度为270~300目。
(2)粘结剂。
无机粘结剂有膨润土、水玻璃、硅溶胶;有机粘结剂有糖浆、树脂、淀粉、糊精、白乳胶和By粘结剂等。
常使用的粘结剂:
膨润土、白乳胶和By粘结剂.
(3)载体(溶剂)消失模铸造涂料从经济及安全的角度来考虑,大多数工厂在实际生产中使用水基涂料较多。
醇基涂料只用来埋箱时临时阻缝和修补.
(4)悬浮剂、触变剂为使涂料中耐火粉料与粘结剂充分混合并处于悬浮状态,使涂料搅拌好成为膏状,需加入悬浮剂.尽管膨润土也是很好的悬浮剂,还必须加入羧甲基纤维素(CMC)、By粘结剂,它们也是很好的触变剂。
4、涂料配制
水基涂料配制过程:
先将耐火材料、膨润土、无水碳酸钠等干料加入混砂机干混10min左右→加入粘接剂溶液和少许水,湿混20~30min→湿料出碾后倒入桶里,加入适量水后进行搅拌.搅拌中加入聚醋酸乙烯乳液等添加物。
搅拌器转速大于1380r/min,搅拌时间大于1h。
采用球磨机配制涂料配制工艺:
先将耐火材料、活化膨润土和少许水配制成膏状涂料(水分占粉料质量的25%~30%)一起加入球磨机,然后加入适量的水搅拌成涂料,球磨时间7~8h,加入配好的粘接剂和聚醋酸乙烯乳液后再球磨1h,将涂料倒入或用压缩空气压入涂料桶充分搅拌。
5、涂挂方法
刷涂、淋凃、浸涂法和喷涂。
浸凃时应注意:
1 涂料应处于连续搅拌状态下,并控制其温度。
2 涂料搅拌应慢速,注意防止卷气.
3 浸凃时应选择模样浸入涂料的方向、部位,有利于防止模样变形。
4 模样涂覆的涂料要全面均匀,不得有未上涂料模样暴露部位。
5 模样从涂料中取出、运送、放置均要考虑防止模样变形问题.
6、涂料的烘干
涂料烘干受泡沫塑料软化温度的限制,所以一般在以下的气氛中烘干2~10h。
烘干时注意空气的流动,以降低湿度,提高烘干效率。
还必须注意模样的合理放置或支撑,防止变形。
(五)造型工艺
消失模铸造使用的一般是硅砂,要求其二氧化硅量在85%~90%以上。
从透气性和耐火度方面考虑,铸钢、铸铁件一般选用粒径0。
850~0。
300mm的硅砂.
先在砂箱底布上一层厚度约100mm的干砂,然后将刷有涂料的EPS模及浇冒口放置在砂箱中央,边填砂边震实,直到干砂离砂箱顶面50mm左右时停止加砂,在干砂上面覆盖塑料薄膜,然后将浇口杯置于直浇口顶端,并在薄膜上撤上一层散砂,以防止浇注时铁水溅落,烧穿薄膜导致漏气塌箱.
(六)浇注工艺
消失模铸造浇注过程一般采用慢→快→稳的浇注方式.由于消失模铸造是EPS模被液态金属所置换的成形工艺,在浇注过程中,EPS模的分解,气化需要吸收热量,因此浇注温度要比普通砂型铸造的高20~30℃。
浇注速度要快,在整个浇注过程中,浇口杯必须始终充满,不得断流,否则会破坏铸型的密封,使铸型真空度下降,造成铸件缺陷,甚至发生塌箱。
浇注时选择适当的真空度.铸钢0。
03~0.05MPa,铸铁0.02~0.04MPa.停泵时间一般5min左右,浇注100kg以下浇注结束即可停泵,100kg以上薄壁,结构复杂的铸件,特别是框架结构件,也需浇注一结束就停泵.铸件大、壁又厚时浇注结束后继续抽真空一定时间,比如壁厚20~30mm,500kg左右的铸件,浇注结束后5min左右停泵。
(七)砂处理
砂处理浇注以后,回收砂应经处理,其目的有三:
①砂子温度降到50℃以下,砂温高易导致消失模变形;
②除去粉尘,铁豆;
③除去残留的有机物。
工艺流程:
落砂斗→水平振动筛→型砂冷却→提升机→磁选、除尘→储砂斗
粘土砂处理所经过的砂处理设备流程:
液压翻箱机→振动输送落砂机→振动输送筛分机→链式斗提机→风选磁选机→水冷式沸腾冷却床→斗提机→中间砂库→直线振动输送筛→皮带输送机→斗提机→犁式卸料器→日耗砂库→气动雨淋加砂器→特制砂箱→三维振实台→真空系统→浇注
粘土砂水平分型射压自动造型线
一、工艺流程示意图
旧砂磁选、除尘、冷却
造型(上箱)
配料混制型砂
造型(下箱)
下芯
合金熔炼
清理精整
铸件后处理
炉料准备
不合格
二、工艺流程
混砂
型砂要求:
良好的重复使用特性;适当的粘合剂含量;适当的粒度分布;适当的水分含量.
影响砂型表面紧实度的砂型因素主要是含泥量、透气性、紧实率。
在线型砂性能检测控制仪通过检测型砂紧实率控制型砂水分。
主要砂处理工艺设备:
振动输送机、振动落砂机、鳞板输送机、皮带机、废铁电动葫芦、悬挂磁选机、斗提机、缓冲砂斗、双向带式给料机、星型给料器、旋风分离器、气动犁式卸料器、圆盘给料机、新砂螺旋给料机、旧砂破碎机、多角筛、沸腾冷却床、高速转子混砂机、型砂多功能在线控制仪、型砂松砂器、型砂给料机。
混砂流程:
配料→称量斗→高速转子混砂机→控制仪→型砂斗→松砂机→供砂斗
混砂顺序:
加料→干混→预加水→预混→二次加水→湿混→二次检测→混砂结束
混砂加料顺序的合理性分析:
第一阶段首先部分水混匀,一方面可以避免后期加入粉料时扬尘和污染,另一方面分散加水,可以避免后期加入膨润土后形成粘土球,使型砂更易均匀;第二阶段加入粉料的同时加入少量水进行较长时间混制,使型砂均匀;第三阶段根据实际检测的水量,补加水分达到在线检测自动反馈水分量,可以使水分控制更加准确。
旧砂回收流程:
落砂→磁选→预增湿→破碎机→磁选→多角筛→中间沙仓→砂冷却、增湿→砂仓
砂处理工艺流程:
浇注
温测
废砂
旧砂处理
对旧砂处理的要求
1 旧砂温度不高于室温l0℃。
热砂问题是现代化铸造生产遇到的一个难题.砂温提高,最大的危害是使膨润土粘结力大幅度的下降。
生产实践证明,用一般的冷却办法,要将砂温降到室温是很困难的,一般认为高于室温l0℃即可.
2 旧砂含泥量不超过12%~15%。
旧砂含泥量太高,会使型砂透气性下降,耐火度降低,铸件废品率高.
3 粘土团含量不超过10%。
4 有机物含量不超过5%。
混入粘土砂中的有机物杂质,主要是各种油砂或树脂砂芯子带来的.这些杂质含量太高,使型砂的发气量增大,造成铸件气孔。
5 旧砂水分均匀,均值差不大于5%。
型砂在混制过程中,所谓控制型砂质量,主要是控制水分。
只有旧砂的水分均匀,才能有条件精确地控制型砂水分。
二、铸造工艺方案的确定
(一)浇注位置的确定
铸件的浇注位置是指浇注时铸件在铸型中所处的位置。
正确的浇注位置应能保证获得完整的铸件并使造型、造芯和清理方便。
确定浇注位置的一般原则是:
1)铸件的重要加工面、主要工作面、受力面应尽量放在底部或侧面,以防止这些表面上产生砂眼、气孔、夹渣等铸造缺陷。
2)浇注位置应保证金属液按确定的凝固顺序凝固。
如对收缩较大的合金,浇注位置应有利于顺序凝固,铸件厚大部一般应置于浇注位置的上方,便于设置补缩胃口。
3)浇注位置应有利于型芯的定位、支撑和排气,尽量避免吊芯、悬臂芯。
4)铸件的大平面应置于下部或斜下部以防夹砂等缺陷。
为了方便造型,常采用“横做立浇"、“平做斜浇”等方法。
5)铸件的薄壁部分应置于下部或侧面以防止浇不足、冷隔等铸造缺陷。
6)在大批量生产中应使铸件的毛刺、飞边易于清除。
7)要避免厚大铸件冒口下的主要工作面产生偏析。
(二)分型面的确定
分型面是指铸型组元间的结合面。
分型面选择合理可筒化铸造工艺、提高生产率、降低成本、提高铸件质量.
分型面的确定原则是:
1)尽可能将铸件的全部或大部分放在同一箱内以减少错型.
2)应尽量把铸件的加工定位面和主要加工面放在同一箱内,以使加工定位的尽寸偏差减少.
3)应尽量减少分型面的数量,以减少造型引起的偏差。
4)机器造型一般采用一个分型面,必要时可加型芯以方便造型,免使用活块。
5)尽量减少型芯数量。
6)如有可能,分型面以平面为佳。
7)分型面选在铸件最大截面处可使起模更方便。
8)分型面的选择应有利于清理。
原料质量要求:
原砂:
选用擦洗砂,含泥量〈1.0%,SiO2>85%,原砂粒度70/140目.由于水平分型射压造型属高密度造型,为减少砂型受热膨胀,避免因砂粒受挤压从砂型表面脱落而引起铸造缺陷,粒度要求不宜过于集中,原砂最好采用4筛砂,4筛集中率85%以上,主峰筛(100目)量控制在40%以内。
新砂补加量在5%以下。
煤粉:
含泥量(灰分)〈l0%,煤粉含灰量过高时,使得型砂含泥量增加,影响型砂使用性能。
煤粉含硫分要≤0.5%,煤粉含硫量高时容易使铸件浇出不久便出现锈点。
此外,煤粉不能有大颗粒存在.大颗粒煤粉在浇注过程中遇金属液燃烧时间长,阻止铁液靠近型壁,待铁液凝固后,便会造成铸件表面凹坑,影响铸
件表面光洁度。
因此煤粉粒度必须控制在≥95%通过140目筛.挥发分的高低是衡量煤粉质量好坏的主要指标之一,好的煤粉挥发分含量较高,浇注时,型腔内易形成还原性气体,析出大量的光亮碳,提高铸件的外观质量.但挥发分超过40%,型砂发气量增大,铸件易产生气孔、浇不足等缺陷。
因此,挥发分一般在30%~38%。
淀粉:
我厂在1988年曾生产过一种出口日本的雨漏铸件,该铸件吊砂较大,起模困难,当时加入食用(落地的)淀粉1%,增加了型砂韧性,所以适量加入α淀粉,提高型砂韧性,但湿压强度不能高于1.5MPa,以保证落砂效果。
在型砂中加入淀粉和谷物有利于提高型砂的常温湿拉强度和干压强度,并且有助于型砂保持水分,有效保持膨润土的粘结性,但是却降低了型砂的流动性。
膨润土:
选用钠基膨润土,湿压强度≥120kPa,吸蓝量(g/100g)≥38、粒度过200目≥90%.
型砂配比(%):
新砂:
5~15,旧砂:
85~95,煤粉:
1~3,膨润土:
2~5,α淀粉0。
5。
回用砂的砂温控制及除尘
1 砂铁比不小于1:
4,砂库存放砂量满足2.5~3。
5h使用。
2 洒水冷却,在回用砂运输皮带上进行喷水降温,在旧砂库中加入冷水管进行循环冷却,效果很好。
3 随圆盘给料机加入新砂。
4 采用沸腾冷却床降低砂温。
紧实率、水分、湿压强度控制
透气性:
由于是垂直分型无箱造型,排气好,故透气性可低些.
紧实率、水分:
分别由紧实率监控仪器和水分控制仪测定。
紧实率范围为37±1%,水分控制在4%。
混砂工艺:
经过长期观察发现,型砂经过松砂后总有些像小米粒大小坚硬的砂团存在于型砂中,多的时候,靠多加新砂降低其粘砂团的比倒。
粘砂团的成分实际上就是土和砂子的烧结物和粘士球,这种粘砂团用水一泡就开,所以混砂工艺改为,加砂后先加水化解粘砂团,再加其它粉科,这样混出的型砂中粘土砂团就少了很多.混砂工艺:
旧砂+新砂+水:
湿混15s后,加膨润土+煤粉+添加剂混120~140s.混砂时间不可太长,否则砂子发热影响型砂的流动性,强度反而受影响。
造型工艺
多年实践发现,影响铸件表面光洁度因素除了型砂水分含量外,就是浇口尺寸。
浇注系统要按DISA公司推荐的等流量原则来设计.砂型底部铸件内浇道和横浇道要略小于型腔上部的,浇单件大件还应多开几个内浇道。
对于带字或图案的铸件,在工艺设计时,尽可能把带字或图案的部分放在型腔上半部,内浇口还要躲开字或图案,避免铁液冲坏图案或字体。
模板温度高于型砂5℃为宜,起模时不粘模.也不致表面太干燥。
防止铸件产生变形及裂纹。
对易变形、易裂的铸件适宜放拉筋,拉筋与铸件交接处尽可能薄一些,便于在清整时去掉,也可以利用内浇道做拉筋.
对凸模较大的模板确定利用率>60,砂铁比要高一些。
浇注
浇注时要快速连续浇注,否则易产生串气、冲砂,形成水分迁移(俗称放炮),造成砂型损坏,浇出废品。
快浇还可防止机加工铸件硬度过高,金属液快速充型,并且做到高温出炉、高温浇注,这样的铸
型砂的含泥量和有效膨润土含量
型砂中加入的膨润土、煤粉,经过铁液的高温烧灼后一部分变成死粘土、灰分和煤粉焦化物,另外一部分有效成分保留下来.型砂的含泥量中主要包括有效膨润土、失效膨润土、煤粉、煤粉焦化物和直径小于20μm的砂粒细末.
煤粉的选用
型砂中加入煤粉可防止铸件表面产生粘砂缺陷煤粉的作用在于:
在高温下分解出还原性气体,消耗型腔里的氧气,防止气孔和渣孔的产生,并在高温下燃烧后形成煤焦类酥软物质,为砂粒膨胀提供空间,适时填补砂粒间隙,因此提高铸件的表面光洁度.
旧砂温度
自动造型线效率高,旧砂循环快且温度高,旧砂温度的控制非常重要。
旧砂的温度以高于室温5℃小于43℃为宜。
旧砂温度过高对型砂及造型质量的影响主要有以下几方面:
1 型砂温度高使水分蒸发快混砂时难以控制型砂的性能;
2 热型砂在输送的过程中型砂水分损失快,型砂性能变化大,且性能不稳定,给型砂性能控制带来困难;
3 造型时,热型砂的水分容易在模型表面凝结,起模时型砂粘模,导致砂型报废;
4 若旧砂温度过高,在同一型砂混制工艺条件下型砂的强度降低,为满足型砂的性能要求需要消耗更多的膨润土;
5 合箱后,热型砂的水分易蒸发,凝结在冷的芯子上,使芯子的强度降低;
6 热旧砂在砂斗贮存时,由于水分迁移,旧砂容易粘在砂斗壁上造成堆积,减少砂斗贮存体积,导致系统中可循环使用的旧砂量越来越少,砂温进一步提高,导致恶性循环.
旧砂水分
旧砂水分含量对型砂性能有着重要的影响,适当的旧砂水分含量对提高型砂韧性和保证型砂的综合性能有着至关重要的作用。
旧砂水分含量控制在1.5%~2。
5%较为合适,旧砂需要在砂斗中停留2h以上再进入混砂,旧砂斗的储量应超过每小时混砂量的2。
5倍。
粉尘检测与控制
应定时对砂处理系统中的粉尘进行检测,掌握粉尘中有关组分的含量,以了解除尘器的工作状态是否正常,避免由此带来的型砂系统的波动.当粉尘中含泥量>50%时,表明除尘器的风量偏小,须调整增大除尘风量;当粉尘中有效膨润土含量>5%时,表明除尘器的风量过大。
型砂中过多有效成分被排出造成浪费,应调整减小除尘风量。
混砂机工作效率
影响混砂机工作效率主要有以下几个因素:
旧砂温度:
过高的旧砂温度降低混砂机工作效率
旧砂水分:
旧砂水分过低,型砂中的有效膨润土不能充分发挥作用,影响混砂机工作效率。
湿混时间:
型砂必须具备足够的湿混时间,转子式混砂至少保证90s以上的湿混时间,碾轮式混砂机湿混时间要在6min以上。
混砂机状况:
应定期对混砂机进行保养,调整混砂机底盘与刮板的间隙,保证该间隙在设备规定的范围之内,若间隙过大则型砂难以混制均匀。
炉衬:
普通铸铁生产采用酸性材料石英砂、锆砂;合金铸铁,球墨铸铁一般采用碱性材料刚玉砂和铝矾土.
①用于打结炉衬的石英砂SiO2≧99%,FeO≤0。
5%及少量氧化物经破碎、磁选、筛分、烘干(水分≤0.5%).
②正确选择粒度配比.
③适量的助熔剂。
(硼酸H3BO3或硼酐B2O3)
(七)消失模工艺的铸造缺陷及对策
1)塌箱
造成浇注过程塌箱的主要原因有:
(1)塑料薄膜被飞溅的铁水烧穿;
(2)浇注时断流,浇口杯没充满;
(3)真空系统出现故障;
(4)铸型或涂料透气性差或真空泵抽气速度太小;
(5)内浇口尺寸太小,阻碍铁水流动;
(6)涂料强度太低等等。
采取的对策有:
砂箱顶面的薄膜要覆盖严实,薄膜上要铺一层散砂,浇注时确保浇口杯充满,浇冒口均要涂敷铸造涂料,并提高铸型或涂料的透气性。
对于厚壁件要加大内浇口的截面尺寸。
根据铸件大小选择适当的真空泵,确保真空系统稳定。
2)粘砂
产生粘砂(主要是机械粘砂)的主要原因有:
(1)硅砂粒度太大;
(2)真空度偏高;
(3)浇注温度太高;
(4)涂料性能差,涂层厚度太薄等等.
防止措施为:
选择适当粒度的硅砂,在保证获得足够铸型硬度的前提下,尽可能降低真空度,适当降低涂料透气性。
涂层厚度应控制lmm以上,对于铸铁件而言,浇注温度控制在1400℃左右。